冷轧超深冲钢种系统控氧工艺研究与实践
控扎控冷论文

控扎控冷论文第一篇:控扎控冷论文控轧控冷技术的研究现状及发展摘要:本文介绍了控轧控冷工艺的发展历史、工艺原理以及控轧控冷工艺,叙述了近些年来国内外发展与应用以及今后的展望。
关键词:控扎控冷;TMCP; 超快冷技术;热轧一、概述控扎控冷是一项具有丰富理论内容和较大实用价值的轧钢新技术,其特点是把利用塑性变形得到钢材外部几何形状的热加工成形过程与控制改善钢材的组织状态,提高钢材性能的物理冶金过程有机结合起来,简单地说就是把将钢的热变形与相变有机的结合起来。
其突出的优点是:可大幅度提高低碳钢、低合金钢钢材的强韧性;提高热轧钢材性能合格率;同时可简化工序,节省能耗,节约合金,具有显著地经济效益和社会效益[1]。
控制轧制(CC) 技术的研究始于1890年至二次世界大战期间的德国,当时科研人员对钢铁制品的热加工条件、材质及显微金相组织之间的关系进行了非系统的零散研究,只是定性地揭示了热加工条件和材质间的关系。
到了20世纪60年代初期, 在美国科研人员定性地解释了热轧后的钢材继续发生奥氏体再结晶的动力学变化后, 这才从理论上某种程度地解释了控制轧制技术。
到了20世纪60年代末期, 科研人员通过试验发现, 添加微量元素铌(Nb) 对提高单纯轧制钢。
材的强度有效。
随后进一步的研究表明, 造成铌系钢材高强度的原因,是由于微细铌碳氮化合物的铁素体析出相强化造成的。
同期英国钢铁研究机构对轧制钢材的显微结构和机械性能的1定量关系、铌、钒(V)的强化机理, 控制轧制原理等进行研究, 证实了依靠物理冶金基础, 进行合理的合金成分的设计和轧制条件的设定, 便能达到所期望的钢材目标性能值和显微组织。
到了20世纪70年代,对钢材强度、低温韧性、焊接性能要求更高了,而此时仅仅依靠传统的控制轧制技术远远不够。
于是在奥氏体控制轧制的基础上, 还需要控制冷却速度来控制相变本身, 于是开始了真正意义的控轧控冷技术的应用[2]。
二、控扎控冷的原理控轧控冷技术的基本原理就是控制热轧条件,经过相变过程在奥氏体(γ)的基体上,形成高密度的铁素体(α)晶核,从而在相变后, 达到细化钢材的组织结构[3]。
纯净钢生产技术

≤15
≤10 ≤2
厚 板
低温 9% 抗低 用钢 Nb钢 温脆
抗撕 裂钢 高强 度钢 抗撕 裂性
≤30
≤10≤10 Leabharlann 2纯净钢质量要求及纯净水平要求
产品 用途 钢种
轴承 钢 不锈 钢 轴承 钢
要求
疲劳 寿命 电蚀 性能 疲劳 性能 疲劳 性能 断裂 疲劳
C
N
≤50
T.O
≤10 ≤20 ≤10 ≤15 ≤30
X100 0.02~0.04 1.6~1.8 ≤0.001 ≤0.005 0.05 0.08 0.015 0.15~0.3 任选
国外钢中杂质元素单体控制水平的发展趋势(极限值)
年份 C 1960 1970 1980 1990 1996 2000 200 80 30 10 5 4 S 200 40 10 4 5 0.6 P 200 100 40 10 10 3 元素/10-6 N 40 30 20 10 10 6 H 3 2 1 0.8 <1 0.5 T.O 40 30 10 7 5 2
钢中T[O]量与产品质量关系: (1)轴承钢T[O]由30³10-6降到5³10-6,疲劳寿命提高100倍。 (2)钢中T[O]与冷轧板表面质量存在明显的对应关系。
美国Weirton公司生产0.15mm厚薄板,在DTR生产线上检查120 个板卷发现:
T[O]/10-6 质量指数
15~20
21~25 26~30 >30
66
83-119 82-187
本钢纯净钢的纯净水平
钢种 C/ppm P/ppm S/ppm O/ppm N/ppm ∑/ppm
IF
X70
14-28
30-60
冷轧工艺介绍
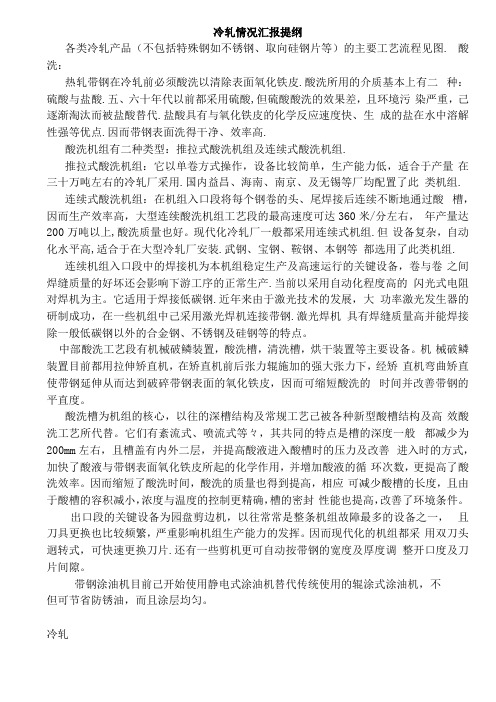
冷轧情况汇报提纲各类冷轧产品(不包括特殊钢如不锈钢、取向硅钢片等)的主要工艺流程见图. 酸洗:热轧带钢在冷轧前必须酸洗以清除表面氧化铁皮.酸洗所用的介质基本上有二种:硫酸与盐酸.五、六十年代以前都采用硫酸,但硫酸酸洗的效果差,且环境污染严重,己逐渐淘汰而被盐酸替代.盐酸具有与氧化铁皮的化学反应速度快、生成的盐在水中溶解性强等优点.因而带钢表面洗得干净、效率高.酸洗机组有二种类型:推拉式酸洗机组及连续式酸洗机组.推拉式酸洗机组:它以单卷方式操作,设备比较简单,生产能力低,适合于产量在三十万吨左右的冷轧厂采用.国内益昌、海南、南京、及无锡等厂均配置了此类机组.连续式酸洗机组:在机组入口段将每个钢卷的头、尾焊接后连续不断地通过酸槽,因而生产效率高,大型连续酸洗机组工艺段的最高速度可达360米/分左右,年产量达200万吨以上,酸洗质量也好。
现代化冷轧厂一般都采用连续式机组.但设备复杂,自动化水平高,适合于在大型冷轧厂安装.武钢、宝钢、鞍钢、本钢等都选用了此类机组.连续机组入口段中的焊接机为本机组稳定生产及高速运行的关键设备,卷与卷之间焊缝质量的好坏还会影响下游工序的正常生产.当前以采用自动化程度高的闪光式电阻对焊机为主。
它适用于焊接低碳钢.近年来由于激光技术的发展,大功率激光发生器的研制成功,在一些机组中己采用激光焊机连接带钢.激光焊机具有焊缝质量高并能焊接除一般低碳钢以外的合金钢、不锈钢及硅钢等的特点。
中部酸洗工艺段有机械破鳞装置,酸洗槽,清洗槽,烘干装置等主要设备。
机械破鳞装置目前都用拉伸矫直机,在矫直机前后张力辊施加的强大张力下,经矫直机弯曲矫直使带钢延伸从而达到破碎带钢表面的氧化铁皮,因而可缩短酸洗的时间并改善带钢的平直度。
酸洗槽为机组的核心,以往的深槽结构及常规工艺己被各种新型酸槽结构及高效酸洗工艺所代替。
它们有紊流式、喷流式等々,其共同的特点是槽的深度一般都减少为200mm左右,且槽盖有内外二层,并提高酸液进入酸槽时的压力及改善进入时的方式,加快了酸液与带钢表面氧化铁皮所起的化学作用,并增加酸液的循环次数,更提高了酸洗效率。
钢中氧的控制

3MnO. Al2O3.3SiO2(锰铝榴石)的作用
• 熔点低,1400℃;球形易于上浮; • 夹杂物可塑性好(800℃~1300℃); • 钢中无Al2O3析出,钢水可浇性好; • 脱氧良好,铸坯无皮下气泡形成。
脱氧及夹杂物的生成控制-铝镇静钢
形成的脱氧产物: Al2O3,其危害:
• 熔点高,2050℃;固态析出与钢水; • 可塑性差,影响钢材性能;
3、 LD-LF-CC 流程氧的控制
高纯净钢缺陷产生的原因调查
钢种
DI罐用镀锡板 ERW管材 镀锡板 深冲用冷轧钢 板 UO管材 UOE管(厚钢 板) 产品缺陷 飞边裂纹 UT缺陷 US缺陷 炉渣分层 冲压缺陷 夹杂 UT缺陷 US缺陷 引起缺陷夹杂物 最小直径
150um 、60um 150um 220um 400um、150um
[C][O]=0.0027, 炉龄<2500(炉) Ⅱ区: a[O] 远离在C-O平衡线; [C][O]:0.0031~0.0037, 炉龄> 2500(炉) Ⅲ区(其它区域): [C][O]:远离C-O平衡线且波动 较大,复吹效果降低。
转炉终点氧的控制-终点温度的控制
转炉终点温度的控制(生产统计):
[C]=0.02%~0.05%,顶吹终点a[O] = 700ppm~900ppm; 复吹终点a[O] = 250ppm~600ppm。
脱氧及夹杂物的生成控制
连铸钢种脱氧的模式 硅镇静钢:-脱氧剂:Si+Mn 硅-铝镇静钢-脱氧剂:Si+Mn+Al(少量) 铝镇静钢--脱氧剂:过剩Al,[Al]>0.01%。
渣相的吸收
夹杂物的排除(钢包精炼)
连铸过程钢中氧的控制-钢水二次污染的防止 连铸过程氧的控制关键 防止钢的二次氧化 进一步利用连铸中间包、结晶器排除夹杂
最全的冷轧知识(材质牌号分类及生产工艺)

冷轧知识一、普通冷轧板材简介是由热轧薄板通过冷压力加工而得到的产品。
由于经过多道次的冷轧,其表面质量优于热轧薄板,经过热处理后,可得到良好的力学性能。
1、普通冷轧板材的用途分类根据生产企业的不同需求,通常将冷轧板分为:一般用冷轧板、冲压级冷轧板、深冲、特深冲及超深冲级冷轧板,一般以卷材和平板交货,厚度以毫米表示,宽度一般为:1000mm和1250mm,长度一般为2000mm和2500mm。
2、普通冷轧板材的牌号常用牌号为:Q195、Q215、Q235、08AL、SPCC、SPCD、SPCE、SPCEN、ST12、ST13、ST14、ST15、ST16、DC01、DC03、DC04、DC05、DC06等;ST12:表示为最普通的钢号,与Q195、SPCC、DC01牌号材质基本相同;ST13/14:表示为冲压级的钢号,与08AL、SPCD、DC03/04牌号材质基本相同;ST15/16:表示为冲压级的钢号,与08AL、SPCE、SPCEN、DC05/06牌号材质基本相同。
3、普通冷轧板材的牌号尺寸表示方法例如鞍钢产ST12,1*1250*2500/C,表示为:牌号ST12普通冷板,厚度为1mm,宽度为1250mm,长度为2500mm或C 卷材。
外观为白铁皮精包装,机械性能为最普通的,最基础的钢号,只能用于折弯成型,不能用于冲压。
使用于机械咬口用,例如冰箱的外壳,车辆油箱等。
ST13以上产品,用在需要深冲的行业,如汽车制造,柴油机的油箱等,具体要用哪一种,看其拉深的要求而定。
ST12与SPCC的差别:其两种产品的机械性能相差无几,只是退货方式不同,ST12材质的产品拉伸性能相对比SPCC 要强。
日本JIS标准材质含义SPCC---S表示为钢(Steel),P表示为板(Plate),C表示冷(Cold),C表示商业(Commercial),为日本JIS 标准。
如需保证抗拉强度,在牌号末尾加T,为:SPCCT。
超深冲钢冶金技术

防止上缘卷 <20μm 边时裂纹
r >1.8-2.0
<100μm
防止光刻蚀 <5μm 边部不良
丸川雄净,大量生產規模にぉける不純物元素の精煉限界への挑戰,日本鉄鋼協會高溫フロ セス部會精煉フォラム,1997年3月,1
44
结晶器卷渣造成的大型非金属夹杂物
No. a b c d
Al2O3 5.42 75.74 19.00 3.59
日本IF钢目标: DP、TRIP高强度钢: 1980s:≤20ppm; 500~900MPa; 1990s:≤15ppm; DP已商业化应用。 2000s:≤10ppm。 超高强度钢:
热冲压成形; 局部热处理等。
9
低温退火用超低碳IF钢板(≤13ppm)
宝钢2#RH2006年12月生产实绩:
满足低温退火工艺要求IF钢板(碳含量<13ppm)的比 率达到了70%。
18 14
[N],ppm
15
13
10
5
0 第 1炉 第 2炉 第 3炉
国内某钢厂生产IF钢中间包钢水[N]含量
37
长水口密封
新日铁君津厂中间包密封结构
38
密封结构设计存在不足
密封垫内径偏小。
上水口插入深度不 足(60mm左右)
钢水“反灌”,造成长水口 结合面结冷钢,再使用前 必须烧氧。
39
合理的长水口密封结构
24
新日铁八幡厂各工序阶段的增碳量
1987 Steelmaking conference Proceedings, p381
25
减少增碳的措施
采用含碳量低的覆盖剂; 采用专用长水口、浸入式 水口; 采用低碳、无碳保护渣。
冷轧带钢组织性能与检测

2 冷轧加工性能与生产条件2.1 加工性能冷轧带钢的主要用途是用于冲压加工领域,冲压加工有剪断、成形两个工序组成,冲压成形是最中心的工序。
近年来,在迅速发展的冲压成型理论的分析方面,对加工性能引入了成形性、磨合性、形状稳定性等概念。
重点放在加工性能上。
当考虑加工性能时,必须考虑成形中的问题(即不发生断裂和裂纹而能成形的问题)和成形后的问题(即正确保持成形件尺寸精度)。
一般认为冷轧带刚在冲压加工性能方面比较优越,这是因为通过控制生产条件,能满足这些要求的各种特性。
对于热轧带钢工艺来说,控制化学成分和热轧温度几乎是控制加工性能的唯一手段。
与此相反,冷轧带钢是通过冷轧和退火、晶粒调整、利用析出相(如AlN)改善各向异性等提高延性,能采用的手段很多,这是冷轧带钢的优点。
当然,对冷轧带钢的质量控制也很难。
2.2 加工性能和生产条件平整冷轧带钢以极软钢为原料,比如S08AL、SPHD等低碳钢,热轧后至少通过压下率40%以上的冷轧,在退火再结晶结束后,经受1%左右的平整轧制。
2.2.1炼钢条件冶炼工艺要点:(1)冶炼①入炉铁水应经过铁水脱硫预处理;②炉前留氧操作,精炼进行铝的合金化。
(2)精炼①经RH真空处理,保证低的、稳定的C含量;②应保证过程温度的稳定性,避免在AHF加升温铝。
(3)连铸①连铸过程应保证保护浇铸,采用无碳和低碳保温材料、保护渣,避免过程回碳;②连铸坯规格为210mm*1100m,控制中间包温度为1550-1565℃℃,拉速为0.4~1.0m/min,依据钢水成分和温度等进行调整;③人工检查连铸坯有无角红裂、结疤等缺陷。
炼钢主要是控制化学成分和纯度,含碳量越低,材料越软,加工性能越好。
碳和磷都是使抗拉强度提高的元素。
为得到好的深冲性能,必须降低含碳量,但是含碳量过低,含氧量增多,屈服点上升,延伸率下降。
含硫量低成形性好,但一般含硫量在0.025%左右时,除浓度严重偏析部位外,对成形性能影响不太大。
南钢E690海洋工程用钢的研制和开发

南钢E690海洋工程用钢的研制与开发刘朝霞崔强李恒坤(南京钢铁股份有限公司,南京 210035)摘 要 南钢炉卷轧机最大咬入坯料厚度为220mm,为了试制80mm低压缩比E690海洋工程用钢板,进行成分设计研究、并在热力模拟实验机Gleeble 3800上对关键工艺参数进行探索,随后进行现场试制验证研究。
结果表明,本研究设定的成分体系下,轧制工艺、冷却工艺窗口较大,便于炉卷轧机上轧制。
成品组织为回火索氏体,沿厚度方向的原奥氏体晶粒细小均匀。
拉伸性能、冲击性能、时效性能、落锤性能(NDT)等优异,满足E690级海洋工程用钢DNV、CCS、ABS等船级社认证要求。
关键词 海洋工程用钢板低压缩比中心偏析 E690Low Compression Ratio E690 Offshore Steel Plate Development in NISCOLiu Zhaoxia Cui Qiang Li Hengkun(Nanjing Iron and Steel United Co.,Ltd., Nanjiang, 210035)Abstract The maximum slab thickness bit by Nanging Iron&Steel Cooperation (NISCO) Steckel mill is 220mm. For the trial production of 80mm low compression ratio E690 offshore steel plate, composition design were investigated. The key process parameters also studied through thermal-simulator Gleeble 3800 followed by the validation field trial study. The results show that rolling process and cooling process windows are big and easy for Steckel mill to roll at the composition system. The trial product microstructure is mainly composed of tempered sorbide. Along the thickness direction, the prior austenite grain is fine and uniform. Tensile properties, impact properties, aging properties, NDT are excellent performed;meet the DNV, CCS, ABS social classification requirements of E690 offshore steel plate.Key words offshore steel plate, low compression ratio, center segregation, E6901 引言人类的不断开发使陆地不可再生资源日趋枯竭,海洋日渐成为满足各国需要的宝藏。
- 1、下载文档前请自行甄别文档内容的完整性,平台不提供额外的编辑、内容补充、找答案等附加服务。
- 2、"仅部分预览"的文档,不可在线预览部分如存在完整性等问题,可反馈申请退款(可完整预览的文档不适用该条件!)。
- 3、如文档侵犯您的权益,请联系客服反馈,我们会尽快为您处理(人工客服工作时间:9:00-18:30)。
3.3.2 ATB工艺 该技术通过向RH熔池表面吹入氧气,使碳 氧反应产生的CO气体二次燃烧生产CO2气体, 提高了转炉出钢过程碳含量,使RH处理前钢水 中的碳含量可以控制在0.04~0.06%之间。同时 RH处理过程中钢水平均温降小于0.35℃/min,可 使转炉出钢温度降低了约10℃,RH处理时间平 均30min左右。RH采用ATB技术,与转炉碳预脱 氧相结合,改变了传统的为了减少RH脱碳时间 和保证极低的碳含量,转炉冶炼终点钢中的碳量 越低越好的操作,降低了钢中多余的氧量和炉渣 的氧化性,提高了钢水的洁净度。
脱氧反应的硅铁的比率%
0.025 0.02
钢水增硅量( % )
1.00 0.85 0.70 0.55 0.40 65 75 85 95 105 RH加入硅铁量(kg) 115 125
0.015 0.01 0.005 0 65 85 105 125 RH硅铁加入量(kg)
图4 RH脱氧硅的加入量与钢水增硅的关系
冷轧超深冲钢种系统控氧工艺研 究与实践
简龙 张越 臧绍双 毛志ቤተ መጻሕፍቲ ባይዱ 郭猛
1、前言 鞍钢2150ASP生产线采用LD-RH-CC工艺路线生产冷轧 超深冲钢种,为了满足钢中碳含量小于0.002%的要求,在实 际生产过程中转炉冶炼终点碳控制在0.02%-0.04%之间,钢 中氧含量控制在0.05%-0.09%之间,在RH-TB精炼过程中, 采用自然脱碳的方式将钢中的碳含量降到0.002%以下,脱碳 结束后钢中氧含量在0.03%-0.06%之间,需要使用大量的铝 合金进行脱氧,增加合金成本的同时其脱氧产物Al2O3如果 不能及时从钢水中排除,还恶化了钢水的洁净度。另外转炉 冶炼终点钢水氧含量过高将导致炉渣中FeO含量较高,增加 了转炉和钢水罐耐材的侵蚀,在钢水罐盛钢期间钢水存在二 次氧化现象,在后续的连铸浇注过程中加重了水口堵塞的程 度,在冷轧板卷表面增加了线状(Sliver)缺陷的机率。针 对此现状,结合2150生产线的现行生产工艺,优化冷轧超深 冲钢种脱氧工艺,从转炉冶炼开始,制定了一系列的精确控 制钢水中氧含量的措施。
0.10 碳高氧高,易喷溅区域 0.08 0.07 0.06 碳氧协调,目标区域
0.04 0.02 0.03 0.04 0.05 RH处理前钢水中[C]含量,% 0.06
图2 RH处理前钢水溶解氧与碳含量的关系
3.2 转炉冶炼终点碳和氧的精确控制
3.2.1转炉出钢过程采用碳预脱氧工艺 为了合理控制钢水中的碳和氧含量,保障RH处理过程碳氧平衡 和提高RH处理后钢水的洁净度,在转炉生产过程中开发了碳预脱氧 工艺。在冶炼终点测定钢水中的溶解氧量,针对钢水中碳含量较低 而氧含量过高的情况,采取在出钢过程向钢水罐内加入焦碳进行预 脱氧处理(依钢水中的溶解氧量分别加入70Kg、90Kg、110Kg)控 制钢水中的氧量,保证RH进站钢中氧量低于700ppm。在碳预脱氧 实验过程中,焦碳脱氧效率为5.32ppm/Kg焦碳,脱氧效果较好,当 焦碳加入量超过90kg时,出现钢水增碳的趋势。另外值得注意的是 在加入焦碳过程中,由于碳氧反应剧烈,存在一定程度的罐内烟尘 较大和炉渣发泡的情况,因此要控制好加入焦碳的时机和数量。 3.2.2转炉出钢过程合金脱氧工艺 为了精确控制钢水中的含氧量,在用焦碳进行预脱氧的基础上, 还可以进行出钢过程合金化脱氧操作和氩站喂铝线脱氧操作,达到 精确调整钢水和炉渣氧化性的目的,同时生成的脱氧产生在进RH处 理前能够有效从钢水中充分上浮排除。
2、钢水中溶解氧对脱碳的影响
采用Mintab统计分析软件针对成品碳含量和RH处理前钢水中溶解的氧含 量进行回归分析(RH脱碳时间为12min-15min),分析成品碳含量与钢水氧含 量的关系如下图1所示:
0.0025
0.0020
成品碳成份,%
0.0015
0.0010
0.03
0.04
0.05 0.06 0.07 RH处理前钢中氧含量,%
3.3 RH-TB处理过程碳和氧的精确控制 3.3.1强制脱碳工艺 针对钢水碳含量偏高而溶解氧含量偏低的情 况,在RH-TB精炼过程开发了强制脱碳工艺,该 技术通过向RH熔池内吹入氧气,增加钢水中溶 解氧的含量,提高了转炉出钢过程中的碳含量, 充分利用碳和氧的双重传质作用,在不延长RH 处理时间的前提下,提高了RH处理的脱碳效率 和真空室温度。
3.3.3 硅预脱氧工艺 先向钢中加入一定量的低碳硅铁进行预脱氧,再向钢水 中加入少量铝粒来进行终脱氧和合金化,低碳硅铁加入 量与其脱氧量的关系如下图3所示:
110 90 70 50 30 65 75 85 95 105 RH硅铁加入量(kg) 115 125
脱氧量(ppm)
图3 不同的低碳硅铁加入量对应的预脱氧量
谢谢大家!
RH-TB精炼处理前钢水中的碳和氧含量控制及其影响分布如下图2 所示:对于冷轧超深冲钢种,RH脱碳处理前碳含量控制在0.03%~ 0.05%,溶解氧控制在0.04%~0.07%,进入碳氧协调区间,在保障脱碳 效率的同时有利于钢水洁净度的提高。
0.12 碳低氧高,过氧化区域
RH处理前钢水中[O]含量,%
0.08
0.09
图1 RH处理前钢水溶解氧对处理后碳含量的影响 从上图1可以看出,RH处理前,钢中溶解氧含量在0.04%-0.09%之间,对成品碳 含量的范围影响不大,溶解氧对成品碳的贡献度R-Sq(调整)仅2.2%,说明在现有 的RH脱碳时期内,受碳传质限制环节的影响,RH处理前钢水中的溶解氧量与成品碳 含量相关性并不强。
4.2系统控氧工艺优化后对铸坯内T[O]的影响 为了考察工艺改进前后钢水洁净度的变化,对采用不同控氧工 艺的铸坯取样进行全氧分析,铸坯中全氧含量变化对比如下图6所示:
0.0035 0.0030 0.0025
0. 002 2
铸坯内T[O]含量,%
0.0020
0.0 017
0.0015 0.0010 传统工艺 优化工艺
随预脱氧低碳硅铁加入量的增加,钢水中硅 含量呈现出增加的趋势,同时参于脱氧反应的硅 铁比率呈现下降的趋势。钢水增硅的主要原因是 在加入硅铁过程中,加入的硅铁除与氧直接反应 外,还要有一部分直接溶入钢水,造成钢水增硅, 另外氧化生成的SiO2又有可能再次被后期加入的 终脱氧和合金化的铝所还原造成钢液增硅。如图 4、图5所示,因此针对低硅钢种,考虑镀锌的需 要,其钢材成品[Si]一般控制在0.05%以下。采用 硅脱氧进行控制钢水中的残氧量时,硅铁的加入 量最好不要超过150Kg,防止钢水增硅或加铝合 金化后出现回硅现象。
图5 RH脱氧硅的加入量与有效硅铁比率的关系
4、系统控氧工艺优化的影响 4.1系统控氧工艺优化后对水口堵塞的影响 RH-TB精炼采用常规高氧低碳的传统方式处 理钢水,在中薄板坯铸机浇注过程中单支浸入式 水口的使用寿命平均为浇注2.3罐,而对RH碳氧 工艺控制优化后,单支浸入式水口的使用寿命达 到3.1罐,相当于每支水口的寿命提高约30分钟, 浸入式水口堵塞现象有所减轻,达到在一个浇次 生产过程中更换一次水口的目的,节约了耐材成 本和提高了铸坯的内在质量。
图6 控氧工艺优化前后铸坯内全氧含量变化
5、结论 (1)RH-TB脱碳时间在12min-15min之间,钢水中的氧含 量在0.04%-0.07%之间已经满足脱碳的需要,脱碳终点钢 水中的碳含量可以稳定地控制在0.002%以下,钢水中多 余的溶解氧对脱碳反应没有实质意义,采取常规低碳高氧 的控制模式弊大于利。 (2)为了保证RH精炼的效果,在RH处理前对钢水中的碳氧进行调整是必要的,采用转炉出钢过程碳预脱氧工艺, 对于稳定钢水中的碳-氧含量和提高钢水的洁净度效果显 著,但其控制碳-氧的精度较低,可以配合铝合金脱氧, 精确控制钢水中的碳-氧含量。 (3)RH采用强制脱碳技术和ATB技术与转炉出钢过程碳预 脱氧工艺相匹配,可以稳定RH操作工艺。 (4)RH采用硅预脱氧工艺,降低合金铝的消耗,有利于减 少脱氧产物Al2O3的生成量,提高钢水的洁净度。 (5)优化冷轧深冲钢种系统控制钢水中的碳-氧工艺,有利 于减少铸机浇注过程中的水口堵塞的机率,提高钢水的洁 净度,从而提高产品的内部质量。