玻璃钢模压成型工艺
玻璃钢模压成型工艺

玻璃钢模压成型工艺概论:玻璃钢是一种以高分子材料和玻璃纤维增强材料为主体组成的复合材料。
同其他常用的材料相比,玻璃钢主要有以下特点:1、玻璃钢兼具轻质高强、绝热、耐热、耐辐射、耐腐蚀、电绝缘、透电磁波、耐超低温等技术特性,从而使共在多种应用环境及领域山有广泛的适应性。
2、一般地说,玻璃钢是一种各向异性材料。
材料的各个方向的性能(如强度等),在较大的程度上可以人为地加以设汁与控制,从而使材料的性能得以充分发挥,为合理地利用材料创造了条件。
3、成型简便,工艺方法种类繁多,适合各地区、单位因地制宜地开拓应用领域。
如果工艺方法及设备选择得当,很容易制造出尺寸准确、结构复杂、外表美观的制品。
由于玻璃钢具备以上特点,因而在汽车、船舶、铁路运输、建筑、日用品、家具、机电、化工、石油等部门获得广泛应用,无疑也会在近代技术(包括能源技术、空间技术、电子技术、激光技术、超导技术等等)的发展中起到一定的作用。
玻璃钢具有优良的成型工艺性,它可以采用多种多样的工艺方法来成型不同结构及性能要求的制品,,据不完全统计,其工艺方法至少有二、三十种,而且也有多种分类方法。
如按增强材料的使用方法分为:层压法(湿法或—r:法)、模压法。
按成型压力大小分接触压法、低压法、高压法。
按成型温度高旺分:室温成型法、高温成型法。
但是最常用的是按:I:艺原理分类,可归纳为手糊法,喷射法,模压成型法,纤维缠绕法和连续成型法等五种。
其中,模压成型工艺是近几年来发展较快、分支较多的一类工艺方法。
模压成型工艺的定义及类型:模压成型工艺一般都涉及成型用模具;但并非所有使用模具成型玻璃钢制品的工艺都称为模压成型工艺。
因为凡是制造玻璃钢制品,总需要各种各样的模具,从最简单的模具——成型板材的模板、到结构复杂的注射成型金属模具。
因此,在国际上有时把各种千差万别的玻璃钢成型工艺统称为模塑成型。
也有人根据成型时模具是否封闭,即制品是否被包容在模具内,而把玻璃钢成型工艺分成两大类型,一是开式或开口模成型法,二是闭式或闭合模成型法。
玻璃钢模压成型工艺综述

玻璃钢模压成型工艺综述一、各种模压成型工艺过程及特点(一)预浸布层压成型工艺1. 概述层压成型工艺是指将浸渍或涂有树脂的片材层叠,组成叠合体,送入层压机,在加热和加压条件下,固化成型复合材料制品的一种成型工艺。
其整个生产工艺流程可用图表示。
层压成型工艺主要是生产各种规格、不同用途的复合材料板材。
它具有机械化、自动化程度高、产品质量稳定等特点,但是设备一次性投资大。
层压成型技术特点是加压方向与制品的板面方向垂直。
层压成型技术包含两方面内容:胶布生产技术和压制成型技术。
2.层压板成型工艺在上述生产工艺中,热压过程的温度、压力和时间是三个最重要的工艺参数。
复合材料的层压工艺的热压过程,一般分为预热预压和热压两个阶段。
热压工艺五段制控制温度曲线,如图所示。
图3.15 热压工艺五段升温曲线示意图(1)第一阶段一预热预压阶段。
此阶段的主要目的是使树脂熔化,去除挥发物、浸渍纤维,并且使树脂逐步固化至凝胶状态。
此阶段的成型压力为全压的1/3-1/2。
几种配方体系的预热预压工艺参数见表。
(2)第二阶段-中间保温阶段这一阶段的作用是使胶布在较低的反应速度下进行固化。
保温过程中应密切注意树脂的流胶情况。
当流出的树脂已经凝胶,不能拉成细丝时,应立即加全压。
(3)第三阶段-升温阶段目的在于提高反应温度,加快固化速度。
此时,升温速度不能过快,否则会引起暴聚,使固化反应放热过于集中,导致材料层间分层。
(4)第四阶段-热压保温阶段目的在于使树脂能够充分固化。
从加全压到整个热压结束,称为热压阶段。
而从达到指定的热压温度到热压结束的时间,称为恒温时间。
热压阶段的温度、压力和恒温时间,也是由配方决定。
几种配方体系的加压工艺参数见表3. 3。
(5)第五阶段-冷却阶段在保压的情况下,采取自然冷却或者强制冷却到室温,然后卸压,取出产品。
冷却时间过短,容易使产品产生翘曲、开裂等现象。
冷却时间过长,对制品质量无明显帮助,但是使生产效率明显降低。
玻璃钢模压成型工艺的优缺点

玻璃钢模压成型工艺的优缺点
玻璃钢模压成型是一种常用于制作轻质复合材料制品的工艺方法,具有一系列独特的优点和缺点。
优点
1. 良好的表面质量
玻璃钢模压成型能够制作出光滑、坚固的表面,具有良好的外观质量,适用于要求较高美观性的制品。
2. 高强度和刚度
玻璃钢模压制品具有高强度和刚度,能够承受较大的荷载,具有较好的耐久性和使用寿命。
3. 良好的耐腐蚀性能
玻璃钢模压制品对酸、碱、盐等腐蚀性较强的介质具有较好的耐腐蚀性能,适用于在恶劣环境条件下的使用。
4. 精密成型
通过模压工艺,可以实现复杂形状和精密尺寸的制造,满足不同工艺要求的制品生产。
缺点
1. 高成本
玻璃钢模压设备投资较大,且原材料成本相对较高,导致制品的生产成本较高。
2. 制造过程复杂
制造玻璃钢模压制品需要经过多道工序,工艺较为复杂,对操作人员技术要求较高。
3. 制品设计受限
由于模具制造成本较高,制品的设计受到模具成本和制造工艺的限制,难以快速调整生产。
4. 模具寿命有限
模具在生产过程中会逐渐磨损,导致模具寿命有限,需要定期更换和维护,增加了生产成本。
总的来说,玻璃钢模压成型工艺具有良好的表面质量、高强度和耐腐蚀性能等优点,但同时也存在较高的生产成本、制造过程复杂、制品设计受限以及模具寿命有限等缺点。
在实际应用中,需要综合考虑优缺点,选择适合自身需求的制造工艺方法。
玻璃钢SMC模压成型工艺流程
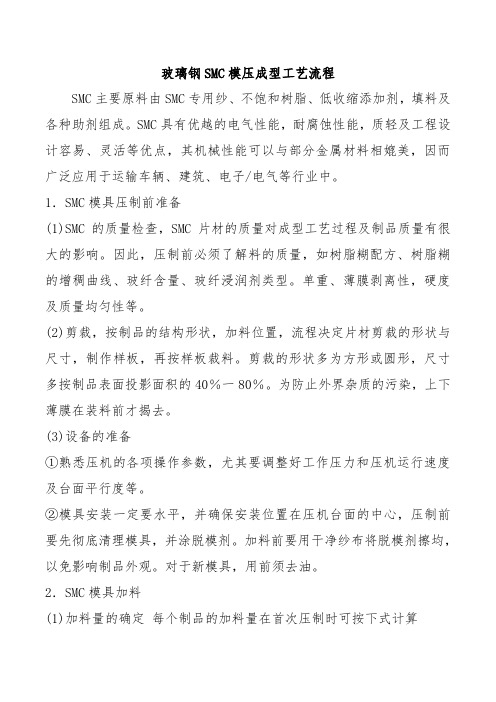
玻璃钢SMC模压成型工艺流程SMC主要原料由SMC专用纱、不饱和树脂、低收缩添加剂,填料及各种助剂组成。
SMC具有优越的电气性能,耐腐蚀性能,质轻及工程设计容易、灵活等优点,其机械性能可以与部分金属材料相媲美,因而广泛应用于运输车辆、建筑、电子/电气等行业中。
1.SMC模具压制前准备(1)SMC的质量检查,SMC片材的质量对成型工艺过程及制品质量有很大的影响。
因此,压制前必须了解料的质量,如树脂糊配方、树脂糊的增稠曲线、玻纤含量、玻纤浸润剂类型。
单重、薄膜剥离性,硬度及质量均匀性等。
(2)剪裁,按制品的结构形状,加料位置,流程决定片材剪裁的形状与尺寸,制作样板,再按样板裁料。
剪裁的形状多为方形或圆形,尺寸多按制品表面投影面积的40%一80%。
为防止外界杂质的污染,上下薄膜在装料前才揭去。
(3)设备的准备①熟悉压机的各项操作参数,尤其要调整好工作压力和压机运行速度及台面平行度等。
②模具安装一定要水平,并确保安装位置在压机台面的中心,压制前要先彻底清理模具,并涂脱模剂。
加料前要用干净纱布将脱模剂擦均,以免影响制品外观。
对于新模具,用前须去油。
2.SMC模具加料(1)加料量的确定每个制品的加料量在首次压制时可按下式计算加料量/g=制品体积/cm3X1.8 /g(2)加料面积的确定加料面积的大小,直接影响到制品的密实程度,料的流动距离和制品表面质量。
它与SMC的流动与固化特性、制品性能要求、模具结构等有关。
一般加料面积为40%-80%,过小会因流程过长而导致玻纤取向。
降低强度,增加波纹度,甚至不能充满模腔。
过大,不利于排气,易产生制品内裂纹。
(3) 加料位置与方式加料位置与方式直接影响到制品的外观,强度与方向性。
通常情况下,料的加料位置应在模腔中部。
对于非对称性复杂制品,加料位置必须确保成型时料流同时到达模具成型内腔各端部。
加料方式必须有利于排气。
多层片材叠合时,将料块按上小下大呈宝塔形叠置。
另外,料块尽量不要分开加,否则会产生空气裹集和熔接区,导致制品强度下降。
玻璃钢模压工艺技术

支链型大分子相对于线型高分子来讲,分子间距离增大,相互作用力减小。如果其支链愈多、愈短,流动的空间位阻愈小,黏度就低,容易流动。
分子量相同,但分子量分布不同的高聚物,其黏度随剪切速率变化的幅度是不同的。当剪切速率变化的幅度是没的。当剪切速率小时,分子量分布宽的融体黏度比分子量分布窄的高。但在剪切速率高时,分子量分布宽的反而比分子量分布窄的小。黏度对温度的敏感性,也随高聚物分子量分布不同而变化。
在模压成型过程中热塑性树脂和热固性塑料的流动性有较大差异。热塑性塑料通过热达到黏流态后开始流动,并在压力作用下充满型腔,成型过程中流动性不发生实质性的变化。对于热固性塑料,通过加热可以使物料熔融降低黏度,在压力作用下发生流动,充模成型。但是与此同时会使塑料分子上的活性基因发生交联反应,导致黏度升高而影响流动性。交联反应放出的热量导致物料温度升高并加速交联固化,从而引起物料黏度急剧增加,流动性迅速下降。
玻璃钢制品模压型
玻璃钢制品模压成型的工艺技术是将热固性塑料的模压料放在已经加热到指定温度的模具中加压,使物料熔融流动并能均匀地充满模腔,经过一定时间固化成型,然后将模压制品取出,再进行必要的辅助加工,即得所需产品。
目前模压的玻璃钢制品,成型前种类有SMC、BMC、DMC、ZMC、IMC、HMC、GMT等多种形态和形式。虽然它们所需要求的性能、类型、模压料组成、形态各不相同,但它们的模压原理和工艺过程是基本相同的。下面对玻璃钢制品模压成型的总体要求;模压料的成型工艺特性;模压成型方法种类;模压成型工艺过程;模压成型工艺条件;模压成型中易出现的问题;及恒力液压机模压成型中的主要解决办法向大家作一简要介绍。
模压成型制作玻璃钢球阀

1. 刖言1.1模压成型工艺模压成型工艺是复合材料生产中最古老而又富有无限活力的一种成型方法。
它是将一定量的预混料或预浸料加入金属对模内,经加热、加压固化成型的方法。
模压成型工艺的主要特点:①生产效率高,便于实现专业化和自动化生产;②产品尺寸精度高,重复性好;③表面光洁,无需二次修饰;④能一次成型结构复杂的制品;⑤因为批量生产,价格相对低廉;⑥加热加压成型,制品结构致密,固化程度高。
模压成型的不足之处在于模具制造复杂,投资较大,加上受压机限制,最适合于批量生产中小型复合材料制品。
随着金属加工技术、压机制造水平及合成树脂工艺性能的不断改进和发展,压机吨位和台面尺寸不断增大,模压料的成型温度和压力也相对降低,使得模压成型制品的尺寸逐步向大型化发展,目前已能生产大型汽车部件、浴盆、整体卫生间组件等。
模压成型工艺按增强材料物态和模压料品种可分为如下几种:①纤维料模压法是将经预混或预浸的纤维状模压料,投入到金属模具内,在一定的温度和压力下成型复合材料制品的方法。
该方法简便易行,用途广泛。
根据具体操作上的不同,有预混料模压和预浸料模压法。
②碎布料模压法将浸过树脂胶液的玻璃纤维布或其它织物,如麻布、有机纤维布、石棉布或棉布等的边角料切成碎块,然后在金属模具中加温加压成型复合材料制品。
③织物模压法将预先织成所需形状的两维或三维织物浸渍树脂胶液,然后放入金属模具中加热加压成型为复合材料制品。
④层压模压法将预浸过树脂胶液的玻璃纤维布或其它织物,裁剪成所需的形状,然后在金属模具中经加温或加压成型复合材料制品。
⑤缠绕模压法将预浸过树脂胶液的连续纤维或布(带),通过专用缠绕机提供一定的张力和温度,缠在芯模上,再放入模具中进行加温加压成型复合材料制品。
⑥片状塑料(SMC)模压法将SMC片材按制品尺寸、形状、厚度等要求裁剪下料,然后将多层片材叠合后放入金属模具中加热加压成型制品。
⑦预成型坯料模压法先将短切纤维制成品形状和尺寸相似的预成型坯料,将其放入金属模具中,然后向模具中注入配制好的粘结剂(树脂混合物),在一定的温度和压力下成型。
玻璃钢模压成型工艺

玻璃钢模压成型工艺模压成型工艺是复合材料生产中最古老而又富有无限活力的一种成型方法。
它是将一定量的预混料或预浸料加入金属对模内,经加热、加压固化成型的方法。
模压成型工艺的主要优点:①生产效率高,便于实现专业化和自动化生产;②产品尺寸精度高,重复性好;③表面光洁,无需二次修饰;④能一次成型结构复杂的制品;⑤因为批量生产,价格相对低廉。
模压成型的不足之处在于模具制造复杂,投资较大,加上受压机限制,最适合于批量生产中小型复合材料制品。
随着金属加工技术、压机制造水平及合成树脂工艺性能的不断改进和发展,压机吨位和台面尺寸不断增大,模压料的成型温度和压力也相对降低,使得模压成型制品的尺寸逐步向大型化发展,目前已能生产大型汽车部件、浴盆、整体卫生间组件等。
模压成型工艺按增强材料物态和模压料品种可分为如下几种:①纤维料模压法是将经预混或预浸的纤维状模压料,投入到金属模具内,在一定的温度和压力下成型复合材料制品的方法。
该方法简便易行,用途广泛。
根据具体操作上的不同,有预混料模压和预浸料模压法。
②碎布料模压法将浸过树脂胶液的玻璃纤维布或其它织物,如麻布、有机纤维布、石棉布或棉布等的边角料切成碎块,然后在金属模具中加温加压成型复合材料制品。
③织物模压法将预先织成所需形状的两维或三维织物浸渍树脂胶液,然后放入金属模具中加热加压成型为复合材料制品。
④层压模压法将预浸过树脂胶液的玻璃纤维布或其它织物,裁剪成所需的形状,然后在金属模具中经加温或加压成型复合材料制品。
⑤缠绕模压法将预浸过树脂胶液的连续纤维或布(带),通过专用缠绕机提供一定的张力和温度,缠在芯模上,再放入模具中进行加温加压成型复合材料制品。
⑥片状塑料(SMC)模压法将SMC片材按制品尺寸、形状、厚度等要求裁剪下料,然后将多层片材叠合后放入金属模具中加热加压成型制品。
⑦预成型坯料模压法先将短切纤维制成品形状和尺寸相似的预成型坯料,将其放入金属模具中,然后向模具中注入配制好的粘结剂(树脂混合物),在一定的温度和压力下成型。
玻璃钢模压制品成型压模设计

玻璃钢模压制品成型压模设计玻璃钢模压制品成型压模成型压模的结构型式,要依据制品的尺寸形状、选取的压制方法,生产批量的大小和所使用的压制设备来确定。
为了对压模有个较系统的了解,可以把玻璃钢的成型压模做如下分类,并简要说明它们的特点。
(一)压模的分类1.按与压机的连接方式分,有移动式压模和固定式压模。
(1)移动式压模产品试制、制品小批量生产及制件上有较多的嵌件和侧向成型杆时广泛使用。
其主要特点是:压模不带加热板,也不带制品自动脱模的顶出装置。
所以压模的结构比较简单,设计和制造周期较短,造价亦较低廉。
移动式压模在生产使用中,压模的分开、装料、闭合和脱模都是间歇地在压机外进行。
一般情况下手工操作频繁。
当压模重量比较大、成型速度较快时,操整理的劳动是相当繁重的。
图7—l所示的为简单结构形状的移动式成型压模。
在压制操作时,向型腔里填充模压料后,要用手工搬动上模,使其与下模装合,然后再把压模放到压机工作台上压制。
制品脱模时,又要把模具放到脱模架上,施加外力,使压模的三个组成零件分开,脱出制品。
因此,不难看出,这种压模在生产使用中,劳动强度大,生产效率也不高。
此外,因为手工操作使上下模对位装合,其配合间隙不可能很均匀,在很多情况下是在压力作用下迫使压模闭合,这样易造成压模配合部位的磨损擦伤,再加上制品脱模时的敲打、磕碰(长期使用的移动式压模、Ul会出现支模板的变形),所以不仅缩短压模的使用寿命,而且制品质量也受到影响。
(2)固定式压模一般在大批量和大型玻璃铜摸制品生产时采用。
固定式压模是把上下模分别固定在压机活动压板台面和弋;工作台上。
操作人员除向压模里填加玻璃钢模压料和制品脱模后对模具的清理外,不需要搬动压模和做其它的繁重劳动。
因为压摸上的顶出装置和压机的顶出机构相联通,所以制品的脱模可以由设备自动来完成。
压模上还可设计有加热系统,确保压制的刁二艺温度。
因而在通常情况下,固定式成型压模自动化程度较高、操作简便、生产效率较高,易于准确执行工艺文倒:所规定的各项操作产品质量易于保证(图7—2)。
- 1、下载文档前请自行甄别文档内容的完整性,平台不提供额外的编辑、内容补充、找答案等附加服务。
- 2、"仅部分预览"的文档,不可在线预览部分如存在完整性等问题,可反馈申请退款(可完整预览的文档不适用该条件!)。
- 3、如文档侵犯您的权益,请联系客服反馈,我们会尽快为您处理(人工客服工作时间:9:00-18:30)。
玻璃钢模压成型工艺概论:玻璃钢是一种以高分子材料和玻璃纤维增强材料为主体组成的复合材料。
同其他常用的材料相比,玻璃钢主要有以下特点:1、玻璃钢兼具轻质高强、绝热、耐热、耐辐射、耐腐蚀、电绝缘、透电磁波、耐超低温等技术特性,从而使共在多种应用环境及领域山有广泛的适应性。
2、一般地说,玻璃钢是一种各向异性材料。
材料的各个方向的性能(如强度等),在较大的程度上可以人为地加以设汁与控制,从而使材料的性能得以充分发挥,为合理地利用材料创造了条件。
3、成型简便,工艺方法种类繁多,适合各地区、单位因地制宜地开拓应用领域。
如果工艺方法及设备选择得当,很容易制造出尺寸准确、结构复杂、外表美观的制品。
由于玻璃钢具备以上特点,因而在汽车、船舶、铁路运输、建筑、日用品、家具、机电、化工、石油等部门获得广泛应用,无疑也会在近代技术(包括能源技术、空间技术、电子技术、激光技术、超导技术等等)的发展中起到一定的作用。
玻璃钢具有优良的成型工艺性,它可以采用多种多样的工艺方法来成型不同结构及性能要求的制品,,据不完全统计,其工艺方法至少有二、三十种,而且也有多种分类方法。
如按增强材料的使用方法分为:层压法(湿法或—r:法)、模压法。
按成型压力大小分接触压法、低压法、高压法。
按成型温度高旺分:室温成型法、高温成型法。
但是最常用的是按:I:艺原理分类,可归纳为手糊法,喷射法,模压成型法,纤维缠绕法和连续成型法等五种。
其中,模压成型工艺是近几年来发展较快、分支较多的一类工艺方法。
模压成型工艺的定义及类型:模压成型工艺一般都涉及成型用模具;但并非所有使用模具成型玻璃钢制品的工艺都称为模压成型工艺。
因为凡是制造玻璃钢制品,总需要各种各样的模具,从最简单的模具——成型板材的模板、到结构复杂的注射成型金属模具。
因此,在国际上有时把各种千差万别的玻璃钢成型工艺统称为模塑成型。
也有人根据成型时模具是否封闭,即制品是否被包容在模具内,而把玻璃钢成型工艺分成两大类型,一是开式或开口模成型法,二是闭式或闭合模成型法。
后者又常称为对模模压法。
这是为了适应大生产而从压力袋法发展起来的一种工艺方法。
在这一类工艺方法中,大多采用结构比较复杂的金属对模,而模压料约束在两半模具成型面之间,在一定温度、压力下固化定型。
尽管它们成型方法很多,伹工艺过程都十分相似。
成型压力的施加,一般都通过液压机来实现。
在对模模压法中,如果树脂在成型时和增强材料几乎同时加入模具内,则属于湿法成型,如果树脂在成型前就预先和增强材料充分的混合,先制成模压料,并且在成型时直接加入到模具内,则属于半干法或干法成型。
按照模压料(即模压用原材料半成品)的制备方法、物理形态及成型时的工艺特点(成型原理),对模模压法可分为吸附预成型坯模压法,预混料或散状模塑料模压法,片状摸塑料模压法,高强度短纤维料模压法,预浸料定向铺设模压法,织物(毡料)—、模压法,碎布料模压法,真空注射模压法,压铸成型法,注射成型法,层压模压法,缠绕模压法,冷模压法和树脂压力注入模压法等等。
那么,在这众多的工艺方法中,究竟什么是模压成型工艺?就我国的具体情况和本书而言,模压成型是指模压料在金属对模中,受高温高压作用成型异形制品的工艺过程。
并且在成型时,模具在模压料完全充满模腔之前,一直处于非闭合状态。
根据这一定义,在上述对模模压分类中,象真空注射模压法、压铸成型法、冷模压法及树脂压力注入模压法等,不属于本书所说的模压成型范畴,但由于其与模压成型有许多共同点,不少学者仍把它们看作是模压工艺的延伸与发展,故本书在“模压工艺的发展”一节中对冷模压法及树脂压力注入模压法作了简单介绍。
在其他的类型中,鉴于在世界各国应用的普遍性,分章重点介绍吸附预成形坯模压法,预混料或散状模塑料模压法,片状模塑料模压法和高强度短纤维料模压法等主要类型。
本节试对各种成型方法及其特点作一比较。
(一)吸附预成型坯模压法这是一种批量生产大型、高强、异型、尤其是深拉制品的工艺方法。
其工艺过程是,先将增强材料——玻璃纤维用吸附法制成与制品结构、形状、尺寸相似的预成型坯,然后再把预成型坯放入模具(一般用金属制成)内,并于其上倒入全配方之树脂,在一定的温度、压力下压制成制品。
预成型坯的制备方法可分为两种,一种是空气吸附预成型法,另一种是湿浆吸附预成型法。
与其它工艺相比,它的主要特点是,制造形状复杂的制品比较经济,材料成本较低,容易实现自动化,制品厚度调节比毡、布对模成型制品容易。
也可埋人装饰材料或连接。
但全工艺过程设备费用较高,对人的操作技能依赖性较强,并且制品厚度一般仅在6毫米以内。
(二)预混料和散状模塑料模压法预混料(Premix)是一种纤维增强热固性模塑料,它是在玻璃纤维无捻粗纱于1949年间问世以后才开始获得应用的。
在50年代获得迅速的发展。
在通常情况下,是由不饱和聚酯树脂、短切纤维、填料、颜料、固化剂等混练而成的—种汕灰状成型材料。
因此,在英国常称其为聚酯料团(DMC)。
在开始发展阶段,由于它成型工艺性十分优良,成本低,性能易调节,因而应用十分广泛。
但是,由于预混料制品强度差,表面往往有严重的收缩波纹,而且处于半湿态的预混料,使操作者深感操作不便。
因此它的进一步发展受到了严重的障碍。
随后,在聚酯树脂的化学增稠及低收缩技术在预混料方面的实用化,就出现了近—卜年来人们常常称之为散状模塑料(BulkMoldingCompound,略称BMC)的新成型材料。
由于在散状模塑料中加入了化学增稠剂和低收缩添加剂,及使用了比预混料更高的玻璃含量,更长的纤维长度.因此敞状模塑料制品比预混科制品有更好的物理性能,具有无波纹、无缩孔的平滑表面,而且不易产生翘曲。
从发展趋势看,散状模塑料正在取代预混料。
预混料成型工艺的特点是制品尺寸、截面形状一般不受限·制,可模制嵌件、连接件、孔洞和螺纹,制品的尺寸精确,材料价格便宜,生产效率高,甚至可成型重达90公斤的制品。
但制品的机械强度不高,表面质量欠佳,加料方法受到一定的限制,很容易出现熔接线等弊病。
这些弊病由于散状模压料(即化学增稠的低收缩型顶混科)的出现,已逐渐得到克服。
聚酯树脂的化学增稠作用使敞状模压料的流动性更好,低收缩添加剂的使用,大大改善了聚酯制品的外观。
与其它工艺方法相比,散状模压科的特点如下:复杂形状可整体成型,成型速度快,适合大批量生产:,能成型嵌件、孔洞、螺纹、筋和凸台等结构,制品的耐热性、耐燃性、耐灿性、耐冲击性好,制品外观、尺寸精度和稳定性奸。
无缩孔、翘曲和表面波纹等弊病,制品电绝缘性优良,耐弧性、耐漏电性能好;价格低廉。
(三)片状模塑料模压成型法。
片状模塑料(SheetMouldingCompo;znd,略称SMC)是在60年代初发展起来的—种“干法”制造聚酯玻璃锏的新型模压用材料。
这种模压片材的组成如图1—1所示。
中间芯材是由经树脂充分浸渍的短印玻璃纤维(或毡)组成,上F两面用聚乙烯薄膜覆盖。
树脂糊里含有聚酯树脂、引发剂、化学增稠剂、低收缩添加剂、填料、脱模剂、颜料等组分。
片状模塑料的模压工艺过程,主要包括片状模塑料的制备和成型两部分。
片状模塑料的制备是在一台专用机组内完成,初期使用玻璃纤维毡,目前多用无捻粗纱。
模压成型过程与一般模压料的模压过程相似,但属于干法成型。
片状漠塑料综合了预混料的优良的成型性和吸附预成型制品的良好强度,而同H寸又克服了上述工艺的弱点。
它的主要特点如下:1.操作处理方便,生产效率高。
生产过程及成型过程容易实现自动化。
2.成型时,由于树脂粘度下降不大,流动性好。
即使是结构复杂的制品,也能实现增强材料的均匀分布,从而获得物理性能优良的制品。
也能实现制品变厚度、带嵌件、孔洞、凸台、筋、螺纹等,尤其适应大面积制品的成型。
3.制品尺寸稳定性好。
表面平滑、光泽好、纤维浮出少。
从而简化了后处理工序。
4.增强材料在模压制造及成型过程中均无损伤,长度均匀,制品强度高。
5.各工序的材料损耗小。
6.成型时,作业环境好,没有湿法作业树脂引起的环境污染和玻璃毛的飞扬。
但是,片状模塑料工艺过程也有它的一定弱点,即设备造价高,设备操作及过程控制比较复杂。
对产品设计,尤其是筋的设计亦有较高的要求。
(四)高强度短纤维料模压成型高强度短纤维料模压成型是一种在我国广泛使用的工艺方法。
它主要用于制备高强度异形制品,也用来制造一些特殊性能要求的制品,如耐腐蚀零件、耐热零件等。
它和其它模压工艺的主要区别,一是具有较高的玻璃含量(一般重量含量在50—60%左右),较长的纤维长度。
(一般长度为30—50毫米)。
二是组成中,一般仅含树脂和增强纤维两种组分。
树脂主要有酚醛、环氧,改性环氧等类型。
混料操作中,为了更好地实现浸渍,多需加入各种非活性溶剂,以调节树脂的浸渍粘度。
这些溶剂在浸渍后期均需大部分除去。
为了获得高性能制品,模具多采用半溢式或不溢式结构。
(五)定向铺设模压成型所谓定向铺设是指玻璃钢制品成型前,使玻璃纤维沿制品主应:力方向取向的铺设过程。
如果把这种定向铺设后之预定形坯进行模压成型制品,则这种成型工艺称之为定向铺设模压成型。
定向铺设模压成型能充分发挥增强材料的强度特性,通过纤维的精确排列与控制可预测制品各向强度及在应力条件下的置信度。
制品性能重复性好。
工艺过程对操作者技能的依赖性小。
并且能提高制品中的纤维含量(增强材料重量含量可达?0%左右)。
但由于增强材料在成型过程中,几乎不发生长程流动。
因此这种工艺最适于制造形状不是十分复杂的大型高强度模压制品。
(六)其它模压成型法除了上述五种国际上通行模压成型法外,随制品结构及性能要求不同还可有其它成型方法。
例如:1、织物模压法系将两向或三向织物(预先织成所需之形状),经预浸渍后,于金属对模内,在高温高压下成型特种制品的—种方法。
2、毡料模压法系将浸毡机组制备之连续玻璃纤维浸渍毡,剪裁成所需的形状,花金属对模中模压成制品的一种方法。
这与片状模压料之主要区别是,多采用酚醛型树脂作粘结剂。
由此也产生了生产设备、工艺及成型方面的许多不同。
3、层压模压法介于层压与模压之间的一种边缘工艺。
系将经预浸渍的玻璃布(或其它织物)裁剪成所需的形状,在金属对模巾层叠铺设模压成型异形制品。
适合于大型薄壁制品或形状简单及有特殊要求之制品。
4、缠绕模压法介于缠绕法与模压法之间的—种边缘工艺。
系将预浸渍的玻璃纤维或布(带)预先缠制在一定的模型上。
再在金属对模中加温加压成型制品。
这种方法适用于有特殊要求之制品及管材等。