Modelling the fatigue crack growth in friction stir welded joint of 2024-T351 Al alloy
《再生钢铁原料》国家标准正式发布

第I期钟治勇等:固溶y时效温度对新型粉末高温合金组织和性能的影响• 63 •度长大,二次f相间距过宽,降低了合金的持久寿 命。
HT1制度试样中二次/相形态失稳,降低了 /相的强化作用。
(3) NPM01 合金经 1190〜1 220 °C 固溶 + 740〜890°C二级时效热处理后,HT2制度试样中二次与三次y相均匀匹配析出,尺寸合理,二次丫'相形状规则,排列整齐。
高温强度和塑性均优于HT0、HT1制度试样,750 °C/750 PMa持久寿命高于HT0试样200 h,高于HT1制度试样145 h,综合力学性能最优异。
参考文献:[1]张义文,刘建涛.粉末高温合金研宄进展[J].中国材料进展,2013, 32(1):1.[2]张义文.俄罗斯粉末高温合金研宄进展[J].粉末冶金工业,2018, 28(6):I.[3 ] Aliniak M O, Bedir F. Modelling of deformation and micro-structural changes in P/M Rene95 under isothermal forging con-ditions[J]. Materials Science and Engineering A, 2006, 429:295.[4] Kruege D D. Kissinger R D, Menzies R G. et al. Development and Introduction of A Damage Tolerant High TemperatureNickel-base Disk Alloy Rene88DT[M]. Superalloy. Warrenda-le:TMS, 1992.[5] Gabb T P, Ellis D L, Kenneth M, et al. NASAA'M-2004-213066[R]. Washington:National Aeronautics and Space Administration. 2004.[6 ]胡本芙,章守华.镍基粉末高温合金FGH95涡轮盘材料研究[J].金属热处理学报,1997,丨8(3): 28.[7 ]刘建涛,张义文,陶宇,等.FGH96合金动态再结晶行为的研究[J].材料热处理学报,2006, 27(5): 46.[8 ]胡连喜,冯小云.粉末冶金高温合金研究及发展现状[J].粉末冶金工业,2018, 28(4): 1.[9 ]陈国良.高温合金学[M].北京:冶金工业出版社,丨988.[10] Radis R. Schaffer M» Albu M, et al. Multimodal size distributions of y'precipitates during continuous cooling of UDIMET720 Li[J].Acta Materialia, 2009, 57:5739.[n]吴凯,刘国权,胡本芙,等.固溶热处理对新型镍基粉末 FGH98I高温合金组织与性能的影响[J].稀有金属材料与工程,2011,40(11): 1966.[12]宁礼奎,郑志,金涛,等.热处理对一种新型镍基单晶高温合金组织与性能的影响[J].金属学报,20丨4,50(8): 1011. [13] Li H Y, Sun J F, Hardy M C, et al. Effects of microstructureon high temperature dwell fatigue crack growth in a coarsegrain PM nickel based superalloy[J]. Acta Materialia. 2015.90:355.[14]马惠萍,颜晓峰,刘万生,等.时效处理对GH648合金析出相和力学性能的影响[J].钢铁研宄学报,2003, 15(7): 123.[15] King A U. Shin D W, Sang X H. et al. Single-step aging treatment for a precipitation-strengthened Ni-based alloy and its influence on high- temperature machanical behavior[J]. ScriptaMaterialia, 2019, 162:416.[16] Baldan A. Effect of grain size and carbides on the creep resistance and rupture properties of a conventionally cast nikel-basesuperalloy[J], Zeitschrift fiir Metallkunde. 1992, 83 (10):750.[17] Kotval P S»Venables J D, Calder R W. The role of hafnium inmodifying the microstructure of cast nickel-base superalloys[J].Metallurgical Transactions, 1972, 3(2):453.[18]杨健,董建新,张麦仓,等.新型镍基粉末高温合金FGH98的高温疲劳裂纹扩展行为研宂[J].金属学报,2013, 49(1):71.[19]秦升学,赵蕊蕊,张弘斌,等.时效处理对GH99中强化相/相的影响[J]•材料热处理学报.2017, 38(2): 55.[20] Jackson M P, Reed R C. Heat treatment of UDIMET 720Li:the effect of microstructure on roperties[J]. Materials Scienceand EngineeringCA), 1999,259:85.[21] Kozar R W, Suzuki A, Milligan W W, et al. Strengthening mechanisms in polycrystalline multimodal nickel-base superalloys[J].Metallurgical and Materials Transactions (A), 2009,40 :1588.•方针跤策•《再生钢铁原料》国家标准正式发布2020年12月丨4日,国家市场监督管理总局(国家标准化管理委员会)批准发布《再生钢铁原料》(GB/T 39733-2020)推荐性国家标准,该标准将于2021年1月1日起正式实施。
疲劳分析软件介绍_DesignLife_9-1_S2098-6_EN_web
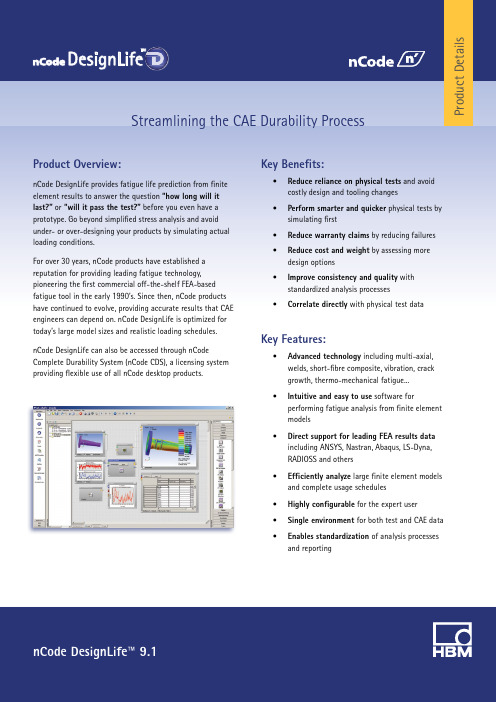
Streamlining the CAE Durability Process
Product Overview:
nCode DesignLife provides fatigue life prediction from finite element results to answer the question “how long will it last?” or “will it pass the test?” before you even have a prototype. Go beyond simplified stress analysis and avoid under- or over-designing your products by simulating actual loading conditions.
• Direct support for leading FEA results data including ANSYS, Nastran, Abaqus, LS-Dyna, RADIOSS and others
• Efficiently analyze large finite element models and complete usage schedules
• Crack Growth – provides a complete fracture mechanics capability using industry standard methodologies for specified locations on FE model. Built-in growth laws include NASGRO, Forman, Paris, Walker and more. Select from a provided library of geometries or supply custom stress intensity factors.
基于Oracle 的高校综合信息分布式管理集成系统
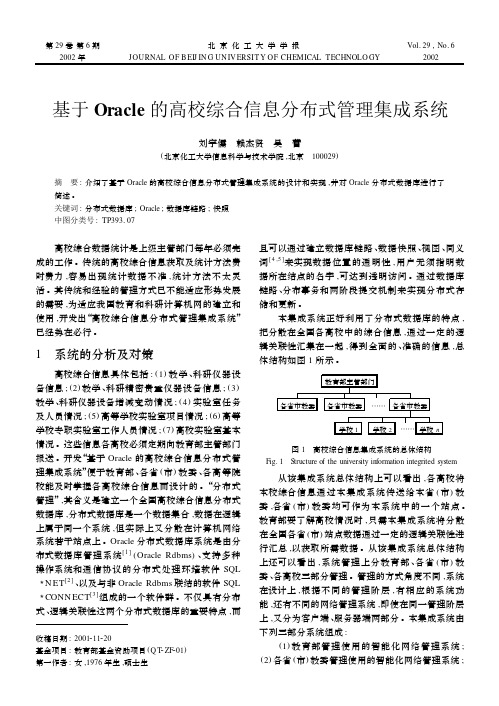
第29卷第6期2002年北京化工大学学报JOURNAL OF BEI J IN G UN IV ERSIT Y OF CHEMICAL TECHNOLO GYVol.29,No.62002基于Oracle 的高校综合信息分布式管理集成系统刘宇儒 赖杰贤 吴 蕾(北京化工大学信息科学与技术学院,北京 100029)摘 要:介绍了基于Oracle 的高校综合信息分布式管理集成系统的设计和实现,并对Oracle 分布式数据库进行了简述。
关键词:分布式数据库;Oracle ;数据库链路;快照中图分类号:TP393107收稿日期:2001211220基金项目:教育部基金资助项目(Q T 2ZF 201)第一作者:女,1976年生,硕士生 高校综合数据统计是上级主管部门每年必须完成的工作。
传统的高校综合信息获取及统计方法费时费力,容易出现统计数据不准,统计方法不太灵活。
其传统和经验的管理方式已不能适应形势发展的需要,为适应我国教育和科研计算机网的建立和使用,开发出“高校综合信息分布式管理集成系统”已经势在必行。
1 系统的分析及对策高校综合信息具体包括:(1)教学、科研仪器设备信息;(2)教学、科研精密贵重仪器设备信息;(3)教学、科研仪器设备增减变动情况;(4)实验室任务及人员情况;(5)高等学校实验室项目情况;(6)高等学校专职实验室工作人员情况;(7)高校实验室基本情况。
这些信息各高校必须定期向教育部主管部门报送。
开发“基于Oracle 的高校综合信息分布式管理集成系统”便于教育部、各省(市)教委、各高等院校能及时掌握各高校综合信息而设计的。
“分布式管理”,其含义是建立一个全国高校综合信息分布式数据库,分布式数据库是一个数据集合,数据在逻辑上属于同一个系统,但实际上又分散在计算机网络系统若干站点上。
Oracle 分布式数据库系统是由分布式数据库管理系统[1](Oracle Rdbms )、支持多种操作系统和通信协议的分布式处理环境软件SQL 3N ET [2]、以及与非Oracle Rdbms 联结的软件SQL 3CONN ECT [3]组成的一个软件群。
Assessment of Fatigue Cracks in Rails
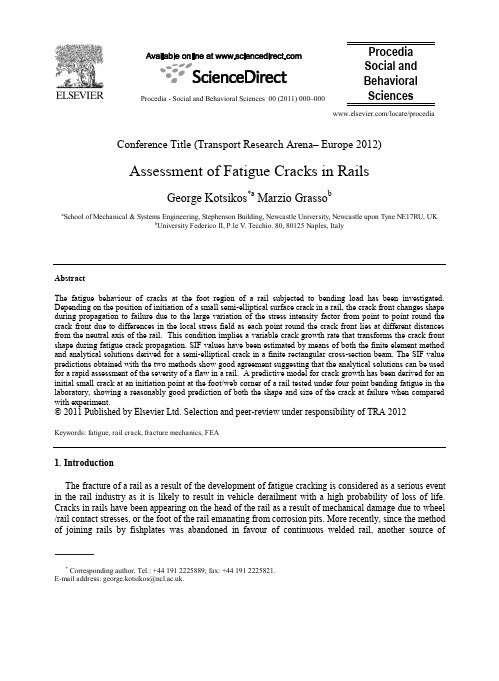
Social and Behavioral Sciences Procedia - Social and Behavioral Sciences 00 (2011) 000–000 /locate/procediaConference Title (Transport Research Arena – Europe 2012)Assessment of Fatigue Cracks in Rails George Kotsikos *a Marzio Grasso ba School of Mechanical & Systems Engineering, Stephenson Building, Newcastle University, Newcastle upon Tyne NE17RU, UKb University Federico II, P.le V. Tecchio. 80, 80125 Naples, ItalyAbstractThe fatigue behaviour of cracks at the foot region of a rail subjected to bending load has been investigated. Depending on the position of initiation of a small semi-elliptical surface crack in a rail, the crack front changes shape during propagation to failure due to the large variation of the stress intensity factor from point to point round the crack front due to differences in the local stress field as each point round the crack front lies at different distances from the neutral axis of the rail. This condition implies a variable crack growth rate that transforms the crack front shape during fatigue crack propagation. SIF values have been estimated by means of both the finite element method and analytical solutions derived for a semi-elliptical crack in a finite rectangular cross-section beam. The SIF value predictions obtained with the two methods show good agreement suggesting that the analytical solutions can be used for a rapid assessment of the severity of a flaw in a rail. A predictive model for crack growth has been derived for an initial small crack at an initiation point at the foot/web corner of a rail tested under four point bending fatigue in the laboratory, showing a reasonably good prediction of both the shape and size of the crack at failure when compared with experiment.© 2011 Published by Elsevier Ltd. Selection and peer-review under responsibility of TRA 2012Keywords: fatigue, rail crack, fracture mechanics, FEA1. IntroductionThe fracture of a rail as a result of the development of fatigue cracking is considered as a serious eventin the rail industry as it is likely to result in vehicle derailment with a high probability of loss of life. Cracks in rails have been appearing on the head of the rail as a result of mechanical damage due to wheel /rail contact stresses, or the foot of the rail emanating from corrosion pits. More recently, since the method of joining rails by fishplates was abandoned in favour of continuous welded rail, another source of*Corresponding author. Tel.: +44 191 2225889; fax: +44 191 2225821.E-mail address : george.kotsikos@.2Author name / Procedia - Social and Behavioral Sciences 00 (2011) 000–000cracking was introduced arising from various weld defects (e.g. porosity, lack of fusion, shrinkage stresses etc.). Infrastructure managers are devoting a large amount of effort to ensure that the integrity of the rail track network is preserved by conducting regular inspections involving up to date NDE techniques. Nevertheless, the development of cracks in rails is unavoidable. The rail damage prediction tools (such as VAMPIRE) currently employed by the industry are based on empirical relations based on the cumulative damage sustained by the axle weight and volume of traffic passing over a rail (J. Evans, 2003). These models do not take into account the development or presence of flaws. It can be stated that decisions on replacement of a rail are not made on the basis of a fracture mechanics based flaw severity assessment (a damage tolerance approach).This work has undertaken the study of fatigue cracks in rails using FEA modeling and analytical solutions to provide a tool to rail NDE inspectors for the quick assessment of the severity of surface breaking and embedded cracks in rails. The work does not investigate crack initiation and propagation phenomena on the heads of rails, but concentrates mainly on cracks initiating and propagating from bending loads in the foot of the rail as a result of passing trains.1.BackgroundThe propagation of a crack is driven by the stress field that develops ahead of the crack tip. In fracture mechanics, the stress and strain fields can be characterized by parameters such as the stress intensity factor, K, under elastic conditions, or the J-integral or crack tip opening displacement(CTOD) under conditions of extended plasticity. Such parameters describe the mechanics of the crack in terms that include the applied load and the length of the crack. The resistance of a material to fast fracture is given by the fracture toughness. Under small scale yielding conditions, to predict crack propagation life and fracture strength, accurate stress-intensity factor solutions are needed both for initial, intermediate and final crack configurations. But, because of the complexities of such problems, exact solutions are not available. Instead, investigators have had to use approximate analytical methods, experimental methods, or engineering estimates to obtain the stress-intensity factors. Closed form solutions for stress intensity factors of elliptical cracks in infinite bodies have been derived by several authors (Green-1950, Irwin-1962, Kassir-1966, Kobayashi-1976, Newman-1979). For finite bodies, all solutions have required approximate analytical methods with the use of finite element analysis (FEA) or boundary element analysis (BEA) methods (Nishioka-1983, Raju-1979, Shah-1971, Smith -1967, Tracey -1973, Vijakumar-1981, Pan -1999).In this paper, a numerical approach that takes into account not only the finite geometry of the defected component but also the real elastoplastic behaviour of the component material has been applied. The implemented numerical model has been validated by means of full scale crack propagation test on defected rails.2.Analytical solutionThe stress intensity factor expression used in this work is given by: K = S F b√(πa/Q)where, S, is the remote applied stress (tensile or bending), a, is the maximum crack depth, Q, is the shape factor for an ellipse given by the square of the complete elliptic integral of the second kind, and F b, is the boundary correction factor which accounts for the influence of the various boundaries. The definition of F b is important and various authors have provided numerous expressions based on FEA parametricAuthor name / Procedia - Social and Behavioral Sciences 00 (2011) 000–000 3 studies. As a starting point the expressions derived by Newman & Raju have been used in this work. A detailed description of these expressions can be found in reference Raju & Newman (1979).3.ExperimentalMechanical property tests were carried out according to BS EN 10002-1:2001 to obtain the rail material mechanical properties for the analysis. Specimens were obtained from the rail head, web andbase along the longitudinal and transverse direction to the rail. There was little variation in the tensile properties between the different regions of the rail. The average yield strength was determined as 540MPaand the ultimate strength 940MPa with an elongation of approximately 12%.Fracture mechanics tests were conducted according to BS7448 Part 2. DCB specimens were extractedfrom the head, web and base of the rail so that the notch (and crack extension path) would lie in the transverse direction to the rail, which is also the direction cracks grow in service.Figure 1. Position of extraction of tensile and fracture mechanics test samples from a UIC60 rail.The fracture toughness K IC of the material could not be determined because the size of the specimensthat could be extracted from the rail would not yield valid results. The K Q value was determined and wasfound to be approximately 27 MN∙m-3/2 (±2 MN∙m-3/2) at all specimen positions in the rail.Constant load amplitude four point bending fatigue tests were carried out on a section of a rail toassess the accuracy of the numerical and analytical solutions. A UIC60 rail section, the most common railprofile in European railways, was used. The rail support span was 750mm and the loading point span190mm. The maximum applied fatigue load was 582kN with a frequency of 1Hz and an R ratio of 0.3(R=P min/P max). The fatigue tests were alloed to continue until complete fracture of the rail took place.Once a crack had initiated, the test was stopped and the crack heat tinted in order to determine the shapeof the crack front just after initiation and how this changes as the crack front propagates to failure.Figure 2. Flaws on fatigued samples, semicircular crack at rail base (left), elliptical crack at bottom web corner (right)4Author name / Procedia - Social and Behavioral Sciences 00 (2011) 000–0004. FEAThe finite element analysis has been carried out using the ANSYS package. Singular quarter-point elements for the small region around the crack front, where the stress field is K-dominated, have been used. The quarter-point elements allow the modelling of singular displacement fields and thus the evaluation of the stress intensity factor (SIF) with great accuracy and a relatively coarse mesh. Several methods are actually available to obtain the SIF values during the post processing of the finite element solution. Among them, the Displacement Correlation Method (DCM) , applicable only when the material has linear elastic isotropic behaviour, makes use of the well-known relations between the SIF’s values and the displacement field around the crack front. Otherwise, knowing the stress and strain field, the J values along the crack front have to be numerically evaluated and from them the SIF values can be derived.The scientific code FRANC3D version 5.0, developed by Cornell University, was used to generate the mesh around the crack front, which allows for both the preprocessing, i.e. it allows the creation of the starter crack in the model, and the postprocessing, i.e. the calculation of the SIF in all the nodes of the crack front created. Starting from these SIF values, a prediction of crack growth has been attempted using Paris’ law which relates the crack growth rate with the stress intensity factor in the form of the expression:da/dN=C K mIn this work, the parameters C and m were obtained by means of crack propagation tests on DCB specimens, extracted from a rail. The values were: C = 3.3×10-13 and m =2.63Figure 3. Outline of fatigue crack fronts at failure.Figure 3 shows a number of crack fronts of fatigue cracks at failure during fatigue testing. The crack geometries were carefully measured and used for comparisoon with the FEA model and the analytical solutions. Comparative results of the FEA and analytical solution for crack 1 and crack 3 are given in Figure 4. It can be seen that there is a good agreement of the SIF values between FEA and analytical solution for both crack fronts. The FEA shows an increase in the SIF values as the crack front ends approach the surface. This is a result of how the FRANC3D code treats the singularity near the free surface of the material. The singularity is described by 1/r0.5and is approximated by the quarter pointAuthor name / Procedia - Social and Behavioral Sciences 00 (2011) 000–000 5 element. This is true along the crack front but not thenpoint where the crack front intersects the externalsurface and the quarter point element does not describe in a proper manner the singularity because thepower of trhe singularity depends on the angle between the front and the external surface and the Poissonratio.Figure 4. Comparison of SIF values from FEA and analytical solution for web corner Crack 1 (left) and crack 3(right).Also, in the present calculation, the M-integral method was used to evaluate stress intensity factors. Therefore, the stress intensity factor calculated for the surface point was in fact an average value over the element size. The stress intensity factor for the surface point of the surface crack should be considered a reasonable physical approximation of the state of affairs at the surface.Figure 5. Semi-circular crack on base of rail 30mm from the CLThe modelling then examined the development of cracks from the foot of the rail, (Figure 2-left). A comparison of the results is shown in Figure 5. In a similar manner to the web corner cracking, the analytical model also adopted the Newman & Raju solutions for bending stress incorporating a bending correction factor, H j, for the component geometry. For the rail geometry the bending factor overestimatedthe stress level and was not appropriate for prediction of SIFs. A better agreement between the FEAmodels and the analytical solution was achieved by considering the loading on the rail as a variabletensile stress the magnitude of which is a function of the distance from the neutral axis according to the equation s=My/I where, M is the bending moment, I the moment of intertia of the rail and y the distancefrom the neutral axis.6Author name / Procedia - Social and Behavioral Sciences 00 (2011) 000–0005.Crack Propagation predictive modelIt was observed that the crack initially has a semi-circular profile which changes to elliptical as the crack propagates. The crack front extends further towards the foot of the rail and less towards the web. This is reasonable as the stress increases the further away from the neutral axis towards the foot of the rail.Figure 6. Fatigue tested rail showing semicircular crack near initiation site (solid line)and semi-elliptical crack atfailure (dotted line).Since the aforementioned practice does not take into account the material ductility, a special code has been implemented in MATLAB, to correct the crack front shape with the plastic radius and evaluate the effective SIF values along the front. By the theoretical SIF values, K I, and the following expression:r p=( /8)(K I/Y)2where, Y is the material yield stress. The plastic radius values, r p, along the front have been evaluated, and a virtual crack front equivalent to the real one, but embedded in an elastic medium, has been generated. The front so created was imported in FRANC3D to evaluate the effective ΔK and the local increment Δa of the crack front, in order to o btain the new “theoretical” crack front corresponding to a given increment of number of cycles.Figure 7. Crack fronts obtained numerically starting from an initial semicircular flaw with radius equal to 2 mm.Author name / Procedia - Social and Behavioral Sciences 00 (2011) 000–000 7 In Figure 7 a series of crack fronts during fatigue crack propagation to failure obtained from an initialflaw of semicircular shape and 2 mm radius are presented. The initial crack is located near the corner between the foot and web of the rail where the center of the semicircle is positioned on the externalsurface and 27 mm distance from the underside of the rail foot. This simulates the fatigue crack of figure6. A comparison of the crack fronts at failure of Figures 6 and 7 shows not a perfect but a reasonablyclose prediction of the fatigue crack final front. This result also confirms the need of take account of theplastic region around the crack tip when the fatigue crack growth phenomenon in a ductile material has tobe simulated.6.ConclusionsAnalytical solutions based on the Newman & Raju equations to obtain the stress intensity factorsround the crack front of cracks in rails have been derived. These were compared with FEA data using ANSYS incorporating the FRANC3D code. The results show a good agreement if a modification is madeto the Newman & Raju equations whereby the applied stress is treated as a variable tensile stress ratherthan bending. The results were validated via experimental four point fatigue tests in rails.A finite element analysis of the fatigue crack growth near the foot of a rail was carried out by means ofa commercial code integrated with an ad hoc macro written to iteratively evaluate the plastic radius, sincethe rail material is ductile, and the eff ective ΔK value that has to be used to evaluate the local growth ofthe crack front.The good agreement between numerical result and experimental data obtained by fatigue testing of aUIC60 rail segment with the same geometry, made of the same material, having the same defect and subjected to same load used in the numerical simulation, confirms the validity of the adopted modeling procedure and the need of directly introduce the effect of the plastic region at the crack tip when the problem of the crack growth in a ductile material has to be faced.7.ReferencesJ. Evans. “Whole life rail model application and development for RSSB- Dynamic modeling of rolling contact fatigue”, AEA Technology Rail report AEATR-VTI-2003-048 Issue 1, , (2003).Green, A. E. and Sneddon, I. N.: The Distribution of Stress in the Neighbourhood of a Flat EllipticalCrack in an Elastic Solid, Proc. Cambridge Phil. Soc., Vol. 47, 1950, pp. 159-164.Irwin, G. R.: The Crack Extension Force for a Part-Through Crack in a Plate, ASME, Journal of Applied Mechanics, Vol. 29, No. 4, 1962, pp. 651-654.Kassir, M. K. and Sih, G. C., Three-Dimensional Stress Distribution Around an Elliptical Crack Under Arbitrary Loadings, Journal of Applied Mechanics, Vol. 88, 1966, pp. 601-611.Kobayashi, A. S.: Crack-Opening Displacement in a Surface Flawed Plate Subjected to Tension or Plate Bending, Proc. Second Intl_Conf. on Mechanical Behaviour of Materials, ASM, 1976, pp. 1073-1077. Newman, J. C., Jr._ and Raju, I. S.: Analyses of Surface Cracks in Finite Plates under Tension or Bending Loads, NASA TP-1578, Dec. 1979.8Author name / Procedia - Social and Behavioral Sciences 00 (2011) 000–000Nishioka, T.; and Atiuri, S. N.: Analytical Solution for Embedded Elliptical Cracks, and Finite Element-Alternating Method for Elliptical Surface Cracks, Subjected to Arbitrary Loadings, Engineering Fracture Mechanics, Vol. 17, 1983, pp. 247-268.Raju, I. S.; and Newman, J. C., Jr.: Stress-Intensity Factors for a Wide Range of Semi-Elliptical Surface Cracks in Finite-Thickness Plates, Engineering Fracture Mechanics J., Vol. ii, No. 4, 1979, pp. 817-829.Shah, R. C.; and Kobayashi, A. S.: Stress-Intensity Factor for an Elliptical Crack Under Arbitrary Normal Loading, Engineering Fracture Mechanics, Vol. 3, 1971, pp. 71-96.Smith, F. W.; Emery, A. F.; and Kobayashi, A. S.: Stress Intensity Factors for Semi-Circular Cracks, Part 2 - Semi-Infinite Solid, Journal of Applied Mechanics, Vol. 34, No. 4, Trans. ASME, Vol. 89, Series E, Dec. 1967, pp. 953-959.Tracey, D. M.,: 3D Elastic Singularity Element for Evaluation of K Along an Arbitrary Crack Front, Int. J. of Fracture, Vol. 9, 1973, pp. 340-343.Vijayakumar, Ko; and Atluri, S. N.: An Embedded Elliptical Flow in an Infinite Solid, Subject to Arbitrary Crack-Face Tractions, Journal of Applied Mechanics, Vol. 48, 1981, pp. 88-96.Pan, E.; Amadei, B.: Boundary Element analysis of fracture mechanics in anisotropic materials, Engineering analysis with Boundary Elements, Vol 23, (1999), pp. 683-691。
机械英语试题及答案详解
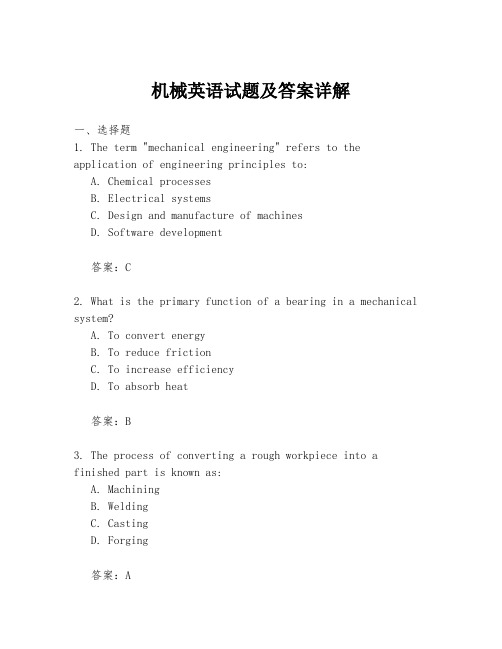
机械英语试题及答案详解一、选择题1. The term "mechanical engineering" refers to the application of engineering principles to:A. Chemical processesB. Electrical systemsC. Design and manufacture of machinesD. Software development答案:C2. What is the primary function of a bearing in a mechanical system?A. To convert energyB. To reduce frictionC. To increase efficiencyD. To absorb heat答案:B3. The process of converting a rough workpiece into a finished part is known as:A. MachiningB. WeldingC. CastingD. Forging答案:A二、填空题4. The formula for calculating the force exerted by a springis known as ________.答案:Hooke's Law5. In mechanical design, the term ________ refers to thestudy of the forces and moments acting on a body.答案:Statics6. The unit of pressure in the International System of Units (SI) is ________.答案:Pascal (Pa)三、简答题7. Explain the difference between static and dynamic friction.答案:Static friction is the force that must be overcometo start moving an object at rest, while dynamic friction is the force that opposes the motion of an object that isalready moving.8. Describe the purpose of a gear in a mechanical system.答案:A gear is used to transmit motion and force from one part of a system to another, often changing the speed and/or direction of the motion.四、计算题9. A hydraulic press has a piston with an area of 0.02 m². If the pressure applied to the piston is 5 MPa, calculate the force exerted by the piston.答案:Force = P ressure × Area = 5 × 10⁶ Pa × 0.02 m²= 100,000 N10. A lever is balanced when the product of the effort force and its distance from the fulcrum is equal to the product of the load force and its distance from the fulcrum. If the effort force is 300 N and the load force is 1200 N, and the effort is applied 2 m from the fulcrum, calculate the distance from the fulcrum to the load.答案:Let the distance from the fulcrum to the load be\( x \). According to the principle of levers, \( 300 N\times 2 m = 1200 N \times x \). Solving for \( x \) gives\( x = \frac{300 N \times 2 m}{1200 N} = 0.5 m \).五、论述题11. Discuss the importance of mechanical vibrations in the context of machinery operation and maintenance.答案:Mechanical vibrations are crucial in machinery for several reasons. They can indicate the health of a machine, with abnormal vibrations often signaling a problem such as imbalance, misalignment, or wear. Monitoring vibrations can help in predictive maintenance, preventing breakdowns and extending the life of machinery.12. Explain the concept of stress concentration in mechanical components and its implications.答案:Stress concentration occurs in mechanical components where the stress is higher than the average stress due to geometrical discontinuities or material defects. This can lead to premature failure of the component under load, as the high-stress areas are more susceptible to fatigue and cracking. Designing to minimize stress concentrations and using materials with good fatigue resistance can mitigate these effects.。
一种预测高低周复合疲劳寿命的新方法
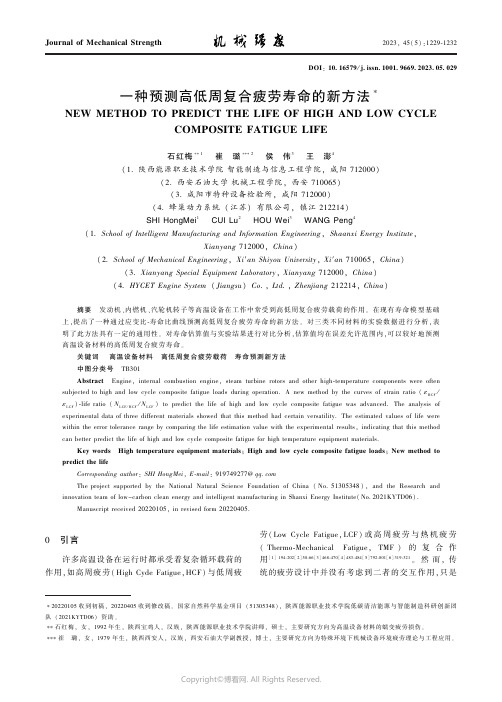
Journal of Mechanical Strength2023,45(5):1229-1232DOI :10.16579/j.issn.1001.9669.2023.05.029∗20220105收到初稿,20220405收到修改稿㊂国家自然科学基金项目(51305348),陕西能源职业技术学院低碳清洁能源与智能制造科研创新团队(2021KYTD06)资助㊂∗∗石红梅,女,1992年生,陕西宝鸡人,汉族,陕西能源职业技术学院讲师,硕士,主要研究方向为高温设备材料的蠕变疲劳损伤㊂∗∗∗崔㊀璐,女,1979年生,陕西西安人,汉族,西安石油大学副教授,博士,主要研究方向为特殊环境下机械设备环境疲劳理论与工程应用㊂一种预测高低周复合疲劳寿命的新方法∗NEW METHOD TO PREDICT THE LIFE OF HIGH AND LOW CYCLECOMPOSITE FATIGUE LIFE石红梅∗∗1㊀崔㊀璐∗∗∗2㊀侯㊀伟3㊀王㊀澎4(1.陕西能源职业技术学院智能制造与信息工程学院,咸阳712000)(2.西安石油大学机械工程学院,西安710065)(3.咸阳市特种设备检验所,咸阳712000)(4.蜂巢动力系统(江苏)有限公司,镇江212214)SHI HongMei 1㊀CUI Lu 2㊀HOU Wei 3㊀WANG Peng 4(1.School of Intelligent Manufacturing and Information Engineering ,Shaanxi Energy Institute ,Xianyang 712000,China )(2.School of Mechanical Engineering ,Xiᶄan Shiyou University ,Xiᶄan 710065,China )(3.Xianyang Special Equipment Laboratory ,Xianyang 712000,China )(4.HYCET Engine System (Jiangsu )Co.,Ltd.,Zhenjiang 212214,China )摘要㊀发动机㊁内燃机㊁汽轮机转子等高温设备在工作中常受到高低周复合疲劳载荷的作用㊂在现有寿命模型基础上,提出了一种通过应变比-寿命比曲线预测高低周复合疲劳寿命的新方法㊂对三类不同材料的实验数据进行分析,表明了此方法具有一定的通用性㊂对寿命估算值与实验结果进行对比分析,估算值均在误差允许范围内,可以较好地预测高温设备材料的高低周复合疲劳寿命㊂关键词㊀高温设备材料㊀高低周复合疲劳载荷㊀寿命预测新方法中图分类号㊀TB301㊀㊀Abstract ㊀Engine,internal combustion engine,steam turbine rotors and other high-temperature components were oftensubjected to high and low cycle composite fatigue loads during operation.A new method by the curves of strain ratio (εHCF /εLCF )-life ratio (N LCF /HCF /N LCF )to predict the life of high and low cycle composite fatigue was advanced.The analysis of experimental data of three different materials showed that this method had certain versatility.The estimated values of life were within the error tolerance range by comparing the life estimation value with the experimental results,indicating that this methodcan better predict the life of high and low cycle composite fatigue for high temperature equipment materials.Key words㊀High temperature equipment materials ;High and low cycle composite fatigue loads ;New method topredict the lifeCorresponding author :SHI HongMei ,E-mail :919749277@The project supported by the National Natural Science Foundation of China (No.51305348),and the Research andinnovation team of low -carbon clean energy and intelligent manufacturing in Shanxi Energy Institute(No.2021KYTD06).Manuscript received 20220105,in revised form 20220405.0㊀引言㊀㊀许多高温设备在运行时都承受着复杂循环载荷的作用,如高周疲劳(High Cyde Fatigue,HCF)与低周疲劳(Low Cycle Fatigue,LCF)或高周疲劳与热机疲劳(Thermo-MechanicalFatigue,TMF )的复合作用[1]194-202[2]58-66[3]468-470[4]483-484[5]792-801[6]319-321㊂然而,传统的疲劳设计中并没有考虑到二者的交互作用,只是㊀1230㊀机㊀㊀械㊀㊀强㊀㊀度2023年㊀单独研究了两种疲劳失效形式㊂随着高温设备运行工况越来越复杂,进一步研究表明很多高温设备的疲劳寿命和高周疲劳载荷的附加有很大关系;随着高周疲劳载荷应变幅的增大,材料的疲劳寿命飞速降低[7-8]㊂因此,研究高温设备材料在高低周复合疲劳载荷下的寿命模型,成为了该领域的研究重点㊂对于高低周复合疲劳寿命模型的研究,较成熟的是裂纹扩展模型和累积损伤模型[9]629-632㊂基于裂纹扩展的机制模型认为叠加的高周疲劳载荷会增加裂纹扩展速率,减少构件的疲劳寿命,经实验验证可以较好地预测材料的疲劳寿命㊂赵振华等[9]629-632提出了线性和非线性疲劳损伤累积模型,其中非线性损伤累积模型研究了高低周复合循环比和应力(应变)幅比的关系,故而估算精度较好㊂这两种模型虽然得到了广泛的应用,但都只是将高低周疲劳载荷对材料寿命的影响进行了纯粹地叠加,而没有考虑二者的交互作用㊂因此,本文分析了高低周疲劳载荷对几种高温设备材料寿命的影响,提出一种预测高低周复合疲劳寿命的新方法㊂1㊀分析方法1.1㊀基础模型㊀㊀SCHWEIZER C等[1]194-202为了描述高低周复合载荷下疲劳裂纹的扩展行为,提出了以裂纹增长速率(d a/d N)和循环裂纹尖端位移(ΔCTOD)的相关性而展开的机制制型:d ad N block=d ad N total+ðblock d a d N HCF式中,d a/d N|block为高低周复合载荷下的裂纹增长速率;d a/d N|total为低周载荷下的裂纹增长速率;ðblock (d a/d N|HCF)为高周载荷下的裂纹增长速率㊂文中以汽轮机转子10%Cr钢为实验材料,分别进行了低周载荷和高低周复合载荷下的疲劳实验,得到了裂纹长度和循环周期的曲线,如图1所示㊂如此,已知裂纹长度,就可预测试件在该载荷下的循环周期(寿命)㊂而且此模型的预测结果和实验结果吻合度较好,可以很好地描述高低周复合载荷下疲劳裂纹的扩展行为㊂1.2㊀演化方法㊀㊀由图1可知,载荷加载初期,裂纹扩展很慢;当循环周期达到1500后,裂纹扩展速率加快,表现为裂纹长度迅速增大,而且高低周复合载荷下裂纹的扩展速率远大于纯低周疲劳载荷;裂纹长度增大到一定值时不再变化,循环周期趋于固定值,说明此时试件已经断图1㊀10%Cr钢在不同载荷下裂纹长度与循环周期的关系Fig.1㊀Relationship between crack length and life cycle of10%Cr steel under different loads裂,相对应的循环周期可以表示为试件的实验寿命㊂㊀㊀因为高周疲劳载荷的附加会大大降低材料的复合疲劳寿命,所以可推算得材料的高低周复合疲劳寿命与纯低周疲劳寿命之比(N LCF/HCF/N LCF)小于1,且大于0㊂受上述基础模型的启发,以10%Cr钢实验数据为例,做出高周应变-寿命比(εHCF-N LCF/HCF/N LCF)和高低周应变比-寿命比(εHCF/εLCF-N LCF/HCF/N LCF)两种曲线[10],如图2所示㊂图2㊀10%Cr钢的应变-寿命比和应变比-寿命比曲线Fig.2㊀Fitting curve that the strain-life ratio and the ratioby strain-life of10%Cr steel经曲线拟合,发现应变比-寿命比曲线的变化趋势更明显,拟合度较高㊂因此,提出可通过应变比-寿命比曲线来预测高温设备材料的复合疲劳寿命㊂此方法计算简单,其是否具有较高的准确度和通用性,需要大量的数据验证㊂㊀第45卷第5期石红梅等:一种预测高低周复合疲劳寿命的新方法1231㊀㊀2㊀方法验证2.1㊀实验数据分析㊀㊀铸造铝合金一般用于汽车发动机的汽缸盖㊁机体和活塞等部件,而这些部件往往遭受着复杂的热疲劳与机械疲劳载荷[3]468-470[4]483-484[5]792-801㊂钴基合金材料一般用于航空发动机或燃气涡轮机的燃烧室,而燃烧室在工作时既承受着由温度变化引起的热机疲劳载荷,也承受着由机械振动引起的高周疲劳载荷[6]319-321㊂球墨铸铁材料常用于内燃机的高温设备,尤其是汽缸盖部件[2]58-66㊂这些高温设备工作时不但遭受着由频繁启停机引起的低周疲劳载荷,而且承受着由点火压力和机械惯性振动引起的高周疲劳载荷㊂本文摘取以上三类材料在复合疲劳载荷下的实验数据,并对这三类不同材料在不同实验条件下的实验数据进行了分析,得到了其应变比-寿命比曲线,如图3所示㊂图3㊀不同材料的应变比-寿命比曲线Fig.3㊀Fitting curve that the ratio by strain-lifeof different materials由图3可知,所有数据的变化趋势一致,都是幂函数关系,且与10%Cr钢材料的应变比-寿命比曲线变化趋势一致㊂2.2㊀论证分析㊀㊀由以上不同材料的数据分析,可以得到如下结论: 1)虽然以上几种材料在组成成分上差别较大,但其大多都用在燃气涡轮机和航空发动机的燃烧室或燃烧器及汽车发动机的汽缸盖㊁机体和活塞等部件上,而这些高温部件在工作时不仅承受着由温度变化引起的热机疲劳载荷或者低周疲劳载荷,还承受着由机械振动及燃烧压力引起的高周疲劳载荷㊂这与10%Cr钢材料工作时的受力情况基本相同,故这几种材料具有可比性和代表性㊂2)同种材料,实验工况(温度㊁频率等)不同,其应变比-寿命比曲线计算值几乎在同一条曲线上,曲线变化趋势一致;不同材料,实验条件各不相同,但其应变比(εHCF/εLCF)-寿命比(N LCF/HCF/N LCF)曲线的变化趋势也相同㊂所有曲线都和10%Cr钢材料的曲线变化趋势一致,材料的应变比-寿命比呈幂函数变化关系㊂3)从数据分析的角度看,应变比-寿命比曲线反映的其实还是应变幅与疲劳寿命之间的关系,只不过将此关系用应变比-寿命比的数学关系反映出来了,更适合表达高周复合疲劳载荷下高低周应变福与疲劳寿命之间的关系㊂在疲劳实验中,当实验温度确定,在同样的应变幅下,同材料的疲劳寿命基本稳定在一定范围数值下,而应变比-寿命比曲线反应的含义与此实验现象是一致的,即应变幅值是决定疲劳寿命的最主要因素㊂因此,通过应变比(εHCF/εLCF)-寿命比(N LCF/HCF/ N LCF)曲线预测高温设备材料的高低周复合疲劳寿命时,具有一定的适用性㊂3㊀寿命估算㊀㊀10%Cr钢的应变比-寿命比计算值和对应的拟合曲线如图2(b)所示㊂图中黑色实心方块是根据实验数据计算的结果,平滑曲线是根据计算值在Origin中非线性拟合得到的曲线㊂在双对数坐标下,应变比与寿命比之间呈幂函数关系,拟合相似度为0.9777㊂得到这条拟合曲线后,已知实验条件(高低周载荷应变幅)和材料在纯低周载荷下的疲劳寿命,就可估算出材料在高低周复合载荷下的疲劳寿命㊂图4所示为通过拟合曲线估算的高低周复合疲劳寿命和实验结果的误差分析㊂由图4可知,此方法的计算精度在两倍误差范围内,且误差分布均匀㊂因此,该方法可以较好地估算高低周复合载荷下高温设备材料的疲劳寿命㊂图4㊀疲劳寿命估算值与实验值的比较Fig.4㊀Comparison of estimated and experimental values of fatigue life 4㊀结论与展望㊀㊀发动机㊁内燃机㊁汽轮机转子等高温部件在工作中常受到高低周复合疲劳载荷的作用,本文在现有寿命模型基础上,提出了一种预测高低周复合疲劳寿命的新方法㊂此方法通过应变比和寿命比反映了高低周疲劳载荷的交互作用,两者在双对数坐标下呈幂函数关系,三类不同材料的应变比-寿命比曲线表明此关系成立㊂文中还通过此关系估算了10%Cr钢的复合疲劳㊀1232㊀机㊀㊀械㊀㊀强㊀㊀度2023年㊀寿命,并与实验结果进行了对比,均在误差允许范围内,进而表明此方法可以估算高温设备材料的复合疲劳寿命㊂高低周复合疲劳参数复杂,影响因素众多,其中,温度和应变幅是最主要的影响因素㊂本文中得到的应变比-寿命比曲线是暂时忽略了温度的影响而得到的,通过实验数据的分析,不同温度下应变比-寿命比曲线的趋势基本是一致的㊂由此说明,此关系具有一定适用性,可以利用此关系估算高低周复合疲劳寿命㊂但为了更精确地预测疲劳寿命,可在后期通过实验及资料收集,得到更多实验数据,进行温度修正,使此关系能更精准地预测高温设备材料的复合疲劳寿命㊂参考文献(References)[1]㊀SCHWEIZER C,SEIFERT T,NIEWEG B,et al.Mechanisms andmodelling of fatigue crack growth under combined low and high cyclefatigue loading[J].International Journal of Fatigue,2011(33):194-202.[2]㊀METZGER M,NIEWEG B,SCHWEIZER C,et al.Lifetimeprediction of cast iron materials under combined thermomechanicalfatigue and high cycle fatigue loading using a mechanism-basedmodel[J].International Journal of Fatigue,2013(53):58-66. [3]㊀BECK T,LOEHE D,LUFT J,et al.Damage mechanisms of cast Al-Si-Mg alloys under superimposed thermal-mechanical fatigue andhigh-cycle fatigue loading[J].Materials Science and Engineering:A,2007,468/469/470:184-192.[4]㊀BECK T,HENNE I,LOEHE D.Lifetime of cast AlSi6Cu4undersuperimposed thermal mechanical fatigue and high-cycle fatigueloading[J].Materials Science and Engineering:A,2008,483/484:382-386.[5]㊀ZHENG X,ENGLER-PINTO C C,SU X,et al.Modeling of fatiguedamage under superimposed high-cycle and low-cycle fatigue loadingfor a cast aluminum alloy[J].Materials Science&Engineering A,2013(560):792-801.[6]㊀MOALLA M,LANG K-H,LOEHE D.Effect of superimposed highcycle fatigue loadings on the out-of-phase thermal-mechanical fatiguebehaviour of CoCr22Ni22W14[J].Materials Science andEngineering:A,2001:319/320/321:647-651.[7]㊀崔㊀璐,康文泉,吴㊀鹏,等.高低周复合疲劳工况下汽轮机转子钢寿命模型[J].科学技术与工程,2021,21(9):3612-3617.CUI Lu,KANG WenQuan,WU Peng,et al.Life model of steamturbine rotor steel under combined high and low cycle fatigueconditions[J].Science Technology and Engineering,2021,21(9):3612-3617(In Chinese).[8]㊀崔㊀璐,石红梅,李㊀臻,等.先进汽轮机转子材料蠕变疲劳损伤研究新进展[J].机械强度,2018,40(2):449-454.CUI Lu,SHI HongMei,LI Zhen,et al.Research on hightemperature and low cycle fatigue performance of ultra-supercriticalsteam turbine high and intermediate pressure rotor steel[A].Journalof Mechanical Strength,2013(7):51-52(In Chinese). [9]㊀赵振华,陈㊀伟,吴铁鹰.高低周复合载荷下的钛合金疲劳寿命估算[J].机械强度,2011,33(4):629-632.ZHAO ZhenHua,CHEN Wei,WU TieYing.Fatigue life estimationof titanium alloys under high and low cycle compound loads[J].Journal of Mechanical Strength,2011,33(4):629-632(InChinese).[10]㊀石红梅.复杂蠕变疲劳载荷对超超临界汽轮机转子钢寿命的影响[D].西安:西安石油大学,2017:42-46.SHI HongMei.The influence of complex creep fatigue loading on lifeof ultra supercritical steam turbine rotor steel[D].Xiᶄan:XiᶄanShiyou University,2017:42-46(In Chinese).。
An engineering model of fatigue crack growth under variable amplitude loading

da/dN DKth0
Kmax
K
OL max
DK DKeq0
DKu
a b,b1 g ry rÀy rmax rOmLax
rimin; rimþi1n
crack growth rate (mm/cycle)
threshold strpesffiffisffiffi intensity factor range at
R ¼ 0 ðMPa mÞ
Received 5 August 2006; received in revised form 1 March 2007; accepted 5 March 2007 Available online 20 March 2007
Abstract
Fatigue crack growth in structure components subjected to variable amplitude loading is a very complex subject. Many models have been proposed, but as yet no universal model exists. In this paper, the concept of an equivalent stress intensity factor (SIF) range corresponding to R = 0 and a modified Wheeler model are introduced. These innovations lead to a fatigue life prediction model that depends mainly on the stress ratio and the plastic zone size ahead of the crack tip. This model also describes the phenomena of retardation and arrest due to overload, and the acceleration due to a state of underload following an overload. The plastic zone size ahead of the crack tip is modeled as a continuous function of the maximum applied SIF, yield strength, and plate thickness, making its calculation precise and easy. The proposed model is validated using experimental fatigue crack growth data in 7075-T6 and 2024-T3 aluminum alloys and 350WT steel under various overload, underload, and spectrum loadings published in the literature. The predicted results are in good agreement with these test data. Ó 2007 Elsevier Ltd. All rights reserved.
《蝶变英语作文》

蝶变英语作文:从蛹到蝶的华丽转身In the world of English writing, the journey of transformation from a caterpillar to a butterfly is as beautiful and captivating as the natural metamorphosis of the insect itself. This process, known as "Butterfly Effect" in the realm of composition, represents a significant leap in the quality and finesse of English essays.The caterpillar stage is marked by the exploration of basic language skills and the establishment of a solid foundation. Just as the caterpillar crawls and feeds on leaves, so does a beginning writer nibble at the leaves of vocabulary and grammar, building a robust foundation for future flights. This phase is crucial, as it lays the groundwork for more complex and nuanced expressions in the later stages.As the caterpillar grows and matures, it begins to spin its cocoon, a protective shell that will enable it to undergo the remarkable transformation into a butterfly. Similarly, as a writer gains confidence and proficiency in the language, he or she starts to craft more intricatesentences and paragraphs, weaving together ideas and arguments in a cohesive and impactful manner. This cocoon stage is marked by experimentation and risk-taking, as writers push the boundaries of their language skills and explore new territories.The emergence of the butterfly from its cocoon is a breathtaking display of beauty and freedom. Similarly, the emergence of a mature English essay from its initial caterpillar stage is a testament to the writer's growth and development. The essay now takes on a new form, with elegant sentences, profound insights, and a captivating flow that takes the reader on a journey. The butterfly essay is not just a product of linguistic mastery; it is also a reflection of the writer's unique perspective and individuality.The "Butterfly Effect" in English writing is not just about the transformation of the essay itself; it is also about the transformation of the writer. As the writer grows and evolves, so does his or her writing. The caterpillar essay may be a humble beginning, but with hard work, dedication, and continuous improvement, it can transforminto a beautiful butterfly essay that soars high in the skies of literary excellence.In conclusion, the journey from caterpillar tobutterfly in English writing is a transformative experience that requires patience, perseverance, and a never-ending quest for improvement. It is a journey that not only enhances the quality of our writing but also transforms us as writers, allowing us to express ourselves more freely and powerfully through the medium of the English language. **蝶变英语作文:从蛹到蝶的华丽转身**在英语写作的世界里,从蛹到蝶的转变就如同昆虫的自然蜕变一样美丽而迷人。
- 1、下载文档前请自行甄别文档内容的完整性,平台不提供额外的编辑、内容补充、找答案等附加服务。
- 2、"仅部分预览"的文档,不可在线预览部分如存在完整性等问题,可反馈申请退款(可完整预览的文档不适用该条件!)。
- 3、如文档侵犯您的权益,请联系客服反馈,我们会尽快为您处理(人工客服工作时间:9:00-18:30)。
Modelling the fatigue crack growth in friction stir welded joint of 2024-T351Al alloyA.F.Golestaneh *,Aidy Ali,M.ZadehDepartment of Mechanical and Manufacturing Engineering,University Putra Malaysia,43400UPM Serdang,Selangor,Malaysiaa r t i c l e i n f o Article history:Received 31October 2008Accepted 7January 2009Available online 11January 2009Keywords:Failure analysis (H)Fatigue (E)Welding (D)a b s t r a c tIn this work the fatigue crack propagation within the friction stir welded (FSW)joint of 2024-T351Al alloy is studied as well as fatigue lifetime of the joint using Walker and Nicholls models.The FSW joint is characterised in terms of the residual stress (using the hole drilling technique),material,and cyclic properties.The material surface is polished in order to avoid any surface irregularities.The crack initia-tion is detected applying scanning electron microscopy (SEM),however plastic replication technique is used to monitor the crack propagation.The concepts of crack closure,residual stress and stress relaxation are incorporated into both models.Finally the results are validated and compared together regarding to the experiments.Ó2009Elsevier Ltd.All rights reserved.1.IntroductionFriction stir welding (FSW)is a type of solid state welding,in-vented in 1991by The Welding Institute (TWI)in Cambridge UK [1,2].This type of welding involves in joining structures with no fu-sion and filler substance.A threaded or non-threaded pin which is installed on a cylindrical tool,translates along the plane joint line (PJL)of two butted plates,rotating fast as shown in Fig.1.FSW joint macrostructure consists of five different zones called:(1)nugget zone (NZ),(2)flow arm zone (FAZ),(3)thermomechan-ically affected zone (TMAZ),(4)heat affected zone and (5)parent plate zone (PZ).Fig.2illustrates the various zones along the cross section of a joint.According to the previous studies,fatigue crack propagation through the FSW joints is intensely affected by (1)microstructure [2–6],(2)hardness [2–5,7],and (3)residual stress [1,5,7–9]where these characteristics depend on the joined material types and the welding process.Any changes in the parameters of the welding process,such as tool geometry,feeding speed,and tool material,cause different properties of the welded zones [10–15].The hard-ness is not uniform along the thickness of FSW joint and it changes through the thickness especially within the nugget zone.In fact material microstructure varies obviously from top surface to the bottom within the NZ which influences the hardness characteristic through the thickness [3,7,16–18].Hardness variation along the zones is not usually negligible.The series of 2xxx and 7xxx Al alloy show maximum hardness at the HAZ and the minimum value at the TMAZ [7,18–20].Previous research on the distribution of resid-ual stress along the FSW zones presents that residual stress is notuniform and varies from one zone to another as well as along the specimen thickness [1,7,8,21,22].Fatigue crack behavior of a T-joint under mixed-model loading was successfully simulated by Xiang et al.[23]based on Paris mod-el.They considered several various models in order to incorporate the mixed-mode condition into the Paris model and define the effective stress intensity factor.Yongshou et al.[24]has applied Paris model to the crack propagation along polyethylene methac-rylate and investigated the effect of temperature on the crack growth rate.The effect of various stress ranges on the fatigue crack growth rate within a nickel alloy was studied by Zheng et al.[25]based on Walker model for two different conditions:(1)constant applied load range (D P )and (2)constant stress intensity factor (SIF).In other work Al-Rubaie et al.[26]applied two types of fati-gue growth models to predict the fatigue of 7475-T7351Al alloy under constant amplitude and stress range of R =0.5.The results showed better prediction using Priddle model compared with Col-lipriest.However modified Forman model presented the best agreement with experiments.Forman–Newman–de Koning model in the work space of FRANC3D was used by Barlow et al.[27]in or-der to simulate the crack propagation along the attachment of mil-itary aircraft engine blade in three dimensions.A mixed-mode fracture condition was considered due to complicated geometry of blade attachment and loading condition.Previous research on fatigue crack growth has focused on crack behavior within one material,with homogeneous properties.How-ever in this study the fatigue crack behavior within the FSW joint of 2024-T351Al alloy was investigated through different welding zones using two types of crack growth models:(1)Walker and (2)Nicholls models.Fatigue lifetime of the FSW joint was deter-mined based on both models and compared with experiments for validation.0261-3069/$-see front matter Ó2009Elsevier Ltd.All rights reserved.doi:10.1016/j.matdes.2009.01.006*Corresponding author.Tel.:+60122749592;fax:+60386567122.E-mail address:gs16938@.my (A.F.Golestaneh).Materials and Design 30(2009)2928–2937Contents lists available at ScienceDirectMaterials and Designj o u r n a l h o m e p a g e :w w w.e l s e vier.c om/loc ate/matdes2.Experiment2.1.Macrostructure and specimenThe experimental tests were performed on the FSW plates with the size of 80Â60Â13mm,provided by Airbus UK Ltd.The plates were welded along the long edge in longitudinal direction and mechanically polished to a 1/4l m for optical observation pur-poses.Finally it was lightly etched in Keller’s reagent in accordance with ASTM E340-00in order to avoid any surface irregularities,which hides the small surface cracks from detection.The specimen was subjected to the four-point bending test using an Instron dig-itally controlled test machine of 100KN capacity as shown in Fig.3.Loading was under constant amplitude with the frequency of 20Hz and load ratio of R =0.1.The fatigue endurance tests were carried out on the specimens in accordance with ASTM D6272(1998).Fig.4represents the extension of different FSW zones away from PJL and through the thickness on a cross section of a as a symmetrical circular area located at the center of the weld,extended to 5–6mm away from PJL,when FAZ,between the NZ and the welded surface spread to 9mm.The size of TMAZ was wide up to 4mm,on the top welding surface however it narrowedNomenclature a half of the internal crack length a c critical crack lengtha H crack length at the HAZ–PZ boundary a i initial crack lengtha Tcrack length at the TMAZ–HAZ boundary da dNcrack growth rateC coefficient of Paris modelC H coefficient of Paris model at HAZ C o coefficient of Walker modelC oH coefficient of Walker model at HAZ C oP coefficient of Walker model at PZ C oT coefficient of Walker model at TMAZ C P coefficient of Paris model at PZ C T coefficient of Paris model at TMAZCT compact tension specimenE modulus of elasticity (Young modulus)FAZ flow arm zoneFSW friction stir weldingH strain hardening coefficient HAZ heat affected zone HCF high cycle fatigue K c fracture toughnessK c ,H fracture toughness of HAZ K c ,P fracture toughness of PZ K c ,T fracture toughness of TMAZ LCF low cycle fatigueLEFM linear elastic fracture mechanics m exponent of Paris model m 1exponent of Walker modelm 1H exponent of Walker model at HAZ m 1Pexponent of Walker model at PZm 1T exponent of Walker model at TMAZ m H exponent of Paris model at HAZ m P exponent of Paris model at PZ m Texponent of Paris model at TMAZ Max r rex maximum stress after relaxation Min r rex minimum stress after relaxation n strain hardening exponent N f fatigue lifeN p number of propagation cycles NZ nugget zone PZ parent zone Rstress ratioTMAZ thermomechanically affected zone D K stress intensity factor rangeD K effective stress intensity factor range D r stress rangeD r effeffective stress range c Walker constantc H Walker constant at HAZ c P Walker constant at PZ c T Walker constant at TMAZ r maxmaximum applied stressr max+res maximum stress after incorporating residual stress r minminimum applied stressr min+res minimum stress after incorporating residual stress r op crack-opening stress r res residual stress r Y yield strengthr Y,H yield strength of HAZ r Y,P yield strength of PZ r Y,Tyield strength of TMAZFig.1.Schematic illustration of FSW butt joint.Fig.2.Various zones along the cross section of FSW joint.A.F.Golestaneh et al./Materials and Design 30(2009)2928–29372929and vanished through out the thickness of10.5mm from the plate surface.HAZ widened through the thickness from the5mm on the top surface to the14mm at the bottom.The coordinate of the mac-rostructural boundaries was mapped by using optical PolyVarMet microscopy as shown in Fig.4.2.2.Hardness and residual stressHardness measurement was carried out according to the stan-dard test method for Vickers hardness test ASTM E92-82(1989). Hardness was measured on top and bottom of the specimen and at the different distances from the PJL with various microstructural types.Fig.5a shows six different positions to measure the hardness where the profiles1and2were located in the NZ,profile3was in the FAZ,TMAZ and HAZ,profiles4and5were in HAZ and profile6 was in the PZ.In order to investigate the hardness variation through the specimen depth,microhardness test was performed by a digitally controlled hardness test machine applying1.0kg force for15s.Fig.5b illustrates the measured hardness variation along the FSW zones at top and bottom surfaces.Residual stress was measured using hole drilling technique,in accordance to the ASTM E837-99(2000).A1.6mm nominal diam-eter holes were drilled at several locations in welding zones,on both sides of the specimen(see Fig.6a).Three equiangular strain rosettes(CEA-06-062UL-120)were positioned at the drilled holes to measure the principle strains.Finally the principle residual stresses and consequently the longitudinal and latitudinal residual stresses were calculated using the obtained strains.Fig.6b shows the residual stress distribution along the FSW zones at the top and bottom surfaces of the specimen.2.3.Crack initiation and propagationScanning electron microscopy(SEM)analysis was used on the fracture surface of the failed specimens from different stress ranges in order to analyze the defect level,initiation site and to mark any possible crack coalescence and failure mechanism in FSW speci-mens.The results showed the high influence of applied loading on the crack initiation site and size,where a higher applied stress will increase the length of the initiated crack and change the crack site further along the PJL.Quantitative microanalysis of initiation areas on the surface was carried out using the Energy Dispersive X-ray analysis(EDX)method.Fig.7shows the crack initiation sites observed by SEM for high cycle fatigue(HCF)of161MPa maxi-mum applied stress and low cycle fatigue(LCF)of300MPa.The positions of the initiation sites,for both161MPa applied stress 300MPa,have been plotted on the hardness–distance diagram in Fig.5b.As it is observed there is a good consistency between crack initiation sites and hardness distribution in the FSW joint for both loadings where the crack initiations were observed at the positions with low hardness characteristic.Fig.6b represents the correlation between residual stress distribution and the position of the fatigue initiation sites observed by SEM in Fig.7.The residual stress distri-bution and initiation sites are consistent where the initiations oc-cur at the points with high residual stress(points A,B and E in Fig.6b).However the residual stress distribution does not show a strong correlation with the initiation sites where the defects exist (points C and D in Fig.6b).In the present work the crack propaga-tion was monitored using surface replication technique as repre-sented in Fig.8.3.Specimen geometry and materials propertiesIn four-point bending test the moment is uniformly distributed between two top spans(see Fig.3)where bending stress distribu-tion is a linear gradient through the thickness with the maximum magnitude on the surface.Therefore the maximum crack growth rate occurs on the surface.In the current modelling a rectangular plate with a size of60Â20mm was considered to model the sur-face of the specimen between two spans.Fig.9shows the FSW zones modelled along the geometry in accordance with the size of zones measured in experiment(Fig.4).4.LoadingAccording to the previous studies[2,5,6,27]on intense influence of residual stress on crack propagation,here different values of residual stress was considered for each welding zone regarding to Fig.6b.Note that residual stress through the PZ is negligible due to this region does not experience any mechanical and heattreatment.Fig.3.FSW specimen under bending fatiguetest.Fig.4.The transverse cross section in an FSW2024-T351Al Alloy joint mapping the boundaries of the macro structural zones. 2930 A.F.Golestaneh et al./Materials and Design30(2009)2928–2937Elber [28,29]showed,the existence of residual stress within the plastic wake along the crack faces keeps the crack faces close for the significant portion of the cycles.Based on the strong effect of crack closure on the stress intensity factor range [30–32],here the effective stress range (D r eff )was calculated,accounting for the residual stress and crack closure:D r eff ¼r max þr res Àr opifr min þr res r op ;ð1ÞotherwiseD r eff ¼ðr max Àr min Þ;ð2Þwhere r max is the maximum applied stress,r min is the minimum ap-plied stress,r res denotes residual stress,and r op represents opening stress value.It is worth noting that whenever the applied stress ex-ceeds the material yield strength,some amount of residual stress is released as the result of plastic deformation.For the loading condi-tion of 270MPa maximum stress and R =0.1,the maximum and minimum stresses after incorporating the residual stress (r max+res ,r min+res )were:r max þres ¼r max þr res ¼270þ96¼366MPa ;r min þres ¼r max R þr res ¼27þ96¼123MPa :ð3ÞDue to the maximum stress exceeded the yield strength of TMAZ (272MPa),the residual stress relaxation was incorporated as follows:366¼Max r rex þðMax r rex Þn )366¼Max r rex 68;000þðMax r rex 800Þ0:1266)Max r rex ¼318MPa ;ð4Þwhere E is the modulus of elasticity,H and n are the strain harden-ing coefficient and exponent presented in Table 1respectively,Max r rex is the maximum stress after incorporating the residual stress relaxation.Therefore the new value of minimum stress can be calculated as Min r rex ¼r min þres Àð366À318Þ¼75MPa.Accord-ing to Eq.(1)and r op ¼110MPa,the effective stress range is D r eff ¼Max r rex Àr op ¼208MPa.5.Crack initiationThe initial crack detection in Fig.7determined a crack initiation site at the TMAZ for HCF.However the initiation site was observed at the end of TMAZ,adjacent to the HAZ for LCF.Therefore in the current work crack growth was modelled for initial crack within TMAZ with the lowest hardness and highest residual stress.The smallest initial crack size identified by the replication work,for the stress condition of 270MPa maximum stress,was about 0.112mm where this value escalated to 0.62mm for the 300MPa maximum stress.Therefore the initial crack with the length of 0.2mm was considered for HCF (loading conditions be-low 300MPa maximum stress)to predict the fatigue life.The length of initial crack increased to 1mm for LCF (loadings beyond 300MPa maximumstress).Fig.5.(a)The hardness measurement at six positions and (b)the hardness variation along the FSW zones of 2024-T351Al Alloy joint.A.F.Golestaneh et al./Materials and Design 30(2009)2928–293729316.Crack growth models 6.1.Walker modelAlthough Walker [33]established his model based on Paris equation [2,16,23],this model was developed so that the coeffi-cient and exponent of the equation do not depend on load ratio and are only influenced by material characteristics.Walker modelexpresses a linear relationship between the crack growth rate (da )and effective stress intensity factor range (D K )in a logarithmic scale.This model predicts the growth rate during the stable prop-agation through the region II as follows:dadN¼C o ðD K Þm 1;ð5Þwhere C o is the Walker coefficient,m 1denotes the Walker exponent and D K is defined by stress intensity factor range (D K ),load ratioand Walker constant (c )as:D ¼D Kð1ÀR Þ1Àc.c is a constant in the range of 0.4–0.9.Therefore Walker model can be rearranged as:da dN ¼C oð1ÀR Þm 1ð1Àc ÞðD K Þm 1;ð6Þwhich is the same with Paris model if C oð1ÀR Þm 1ð1Àc Þis replaced with Paris coefficient (C ).The number of cycles (N p )for a crack propagation from an initial length of a i to the arbitrary length of a can be determined by inte-grating the Eq.(6)with respect to the crack size as presented in Eq.(7).It is worth noting that the fatigue life N f is estimated by substi-tuting the critical crack length a c for the upper limit of the integral in Eq.(7)ZN pdN ¼ð1ÀR Þm 1ð1Àc ÞC oZaa ida½D K ða Þ m 1:ð7ÞHowever for the case of FSW joint consisting of various zones,Eq.(7)was presented as some sub-integrals in order to cover the crack propagation through each zone.In the present work with an initial crack detected within the TMAZ,fatigue life can be calcu-lated by Eq.(8)Fig.6.(a)The residual stress measurement at several positions and (b)the residual stress variation along the FSW zones of 2024-T351Al Alloy joint.2932 A.F.Golestaneh et al./Materials and Design 30(2009)2928–2937ZN fdN ¼ð1ÀR Þm 1T ð1Àc T ÞC oTZa Ta ida ½D K ða Þ m 1T þð1ÀR Þm 1H ð1Àc H ÞC oH ÂZa Ha Tda ½D K ða Þ m 1H þð1ÀR Þm 1P ð1Àc P ÞC oP Za c a H da ½D K ða Þm 1P ;ð8Þwhere subscripts T,H and P represent the values of C o ,m 1and c for TMAZ,HAZ and PZ,respectively.a T and a H denote the crack lengths at the end of TMAZ (TMAZ–HAZ boundary)and at the end of HAZ (HAZ–PZ boundary).6.2.Nicholls modelNicholls law presents another model for stable crack propaga-tion,which defines that the propagation rate depends on D K andmaterial properties as below:da dN ¼14E Y K cD K 4;ð9Þwhere r Y is material yield strength and K c denotes the fracture toughness presented in Table 1.Integration of Nicholls modelalongFig.7.SEM fractograph images of crack initiation in a FSW joint of 2024-T351Al alloy for (a)161MPa maximum applied stress and (b)300MPa.A.F.Golestaneh et al./Materials and Design 30(2009)2928–29372933FSW zones yields the number of cycles during the crack propaga-tion.Fatigue life can be calculated by Nicholls model as follows:ZN pdN ¼4ErY ;T K 2c ;TZa Ta idaD K 4ða Þþr Y ;H K 2c ;HZa Ha TdaD K 4ða Þ"þrY ;P K 2c ;PZa ca HdaD K ða Þ#:ð10Þ7.Adaptation of the Walker and Nicholls modelsIn order to adapt the Walker and Nicholls models the mecha-nism of the fatigue crack propagation within the FSW joint was analyzed.The sizes of the initial cracks detected by replication work were higher than 0.1mm for HCF and higher than 0.5mm for LCF,therefore in the current work the initial cracks were con-sidered as the long cracks compared to the short cracks in stage I with the size order of 20l m.In other words in these tests the cracks grew from defects in stage II where the propagation could be modelled using Walker and Nicholls equations.Note that although the applied equations in the present modelling do not cover the fast propagation phe-nomenon through the stage III,the obtained fatigue lifetimes pro-vided good accuracies.In fact crack growth rate is high along the stage III where the crack propagation does not affect the predicted fatiguelife.Fig.8.Replica images of the FSW of 2024-T351Al alloy for (a)270MPa applied stress and (b)300MPa.Fig.9.The specimen geometry subjected to the distributing loading.Table 1Material properties of FSW zones in 2024-T351Al Alloy.FSW regimesNZ TMAZ HAZ PZ ExperimentalYield stress (MPa)350272448370Modulus of elasticity (GPa)68686868Hardening coefficient (H)–800719770Hardening exponent (n )–0.12660.05540.0860Fracture toughness (MPa ffiffiffiffiffim p )544961322934 A.F.Golestaneh et al./Materials and Design 30(2009)2928–2937The Walker and Nicholls equations are empirical models which are based on experimental data.The parameters in Nicholls model (r Y ,K c ,and E )were measured directly through the experiments on material characteristics as presented in Table.In order to deter-mine the crack behavior by Walker model,the parameters of this equation (C o ,m 1,and c )were calculated fitting a curve through the test data.7.1.Determining m 1The Walker exponent can be considered as the average of the Paris exponent (m )for several load ratios as well as the same value with Paris exponent.In the present modelling the Walker expo-nents for FSW zones were determined the same with Paris expo-nents as presented in Table 2.7.2.Determining C o ,and cConsidering the m ¼m 1and taking the logarithms of Eq.(6)yield:log ðda =dN ÞÀm log ðD K Þ¼log C o Àm ð1Àc Þlog ð1ÀR Þ:ð11ÞSince the left side of Eq.(11)is equal to the Paris coefficient it can be rearranged as log C ¼log C o Àm ð1Àc Þlog ð1ÀR Þ.Therefore C o ,and c can be determined by regressing three or more numbers of C and (1ÀR )while they are plotted in the logarithmic scale.In fact C o is the Paris exponent for R =0and c can be extracted easily from the slope of the plotted line as shown in Fig.10.Table 2represents Walker coefficients and exponents for differ-ent FSW zones where Paris constants have been mentioned for comparison purpose.8.Results and discussionFig.11shows the fatigue crack propagation within the different zones of FSW joint predicted by Walker and Nicholls models in addition to the experimental results.As it is observed the crack propagation process accelerates along the welding zones and the slope of the curve decreases.The crack behavior is intensely af-fected by the variation of hardness and residual stress along the zones.Increase in hardness from the TMAZ (118Hv1)to the high-est value of 167(Hv1)at the next zone (HAZ)supports higher crack growth rate (decrease in the slope of the curve)from TMAZ to HAZ.However due to the decrease in hardness after HAZ,the hardness characteristic contrasts with the observed increase in the crack propagation rate along PZ.The increase in crack growth rate within the PZ compared with the HAZ is attributed to the lower residual stress (negative residual stress)within the HAZ.During crack prop-agation phenomenon the crack length increases which causes higher crack growth rate according to Eqs.(6),(9),and (11):D K /D r ffiffiffiffiffiffip a p ;ð12Þwhere D r is stress range.Therefore,hardness variation and the crack growth phenomenon both have the positive impact on the in-crease in crack growth rate,within the HAZ compared with the TMAZ.Although hardness has a negative effect on the increase ofcrack growth rate along PZ,residual stress and crack growth phe-nomenon support higher growth rate through PZ compared with the HAZ.It is interesting that Walker predictions show more agree-ment with the experiment compared to the Nicholls results,how-ever both of the models calculate the crack growth rate less than the experiment.The number of cycles at the end of each FSW zone was pre-sented for various loading conditions,based on Walker and Nicho-lls models,in Table 3.Final numbers of cycles before fatigue failure (fatigue lifetime),extracted from Table 3,were plotted in the form of S–N curves in Fig.12for Walker and Nicholls models.The exper-imental lifetimes obtained from fatigue crack tests were illustrated in the same figure for validation purpose.Fig.12represents higher agreement of Walker model with experiments compared with Nicholls model especially for the high cycle fatigue.In fact the pre-diction of fatigue crack behavior in Walker model is under theinfluence of coefficient C oð1ÀR Þm 1ð1Àc Þand exponent ðm 1Þ.These fac-tors are both affected by material characteristics like microstruc-Table 2Walker and Paris constants for FSW zones of 2024-T351Al alloy.FSW zones Paris C ðCycle ÞÀ1Walker C o ðCycle ÞÀ1Paris–Walker m ¼m 1Walker cNZ 2.8338Â10À122.53Â10À123.800.72TMAZ 5:5837Â10À124.86Â10À12 2.760.52HAZ 1:1778Â10À12 1.03Â10À12 2.790.53PZ2:8500Â10À122.49Â10À122.940.56Fig.10.Schematic representation of Walker model in logarithmicscale.Fig.11.Fatigue crack propagation within FSW zones under 270MPa applied stress.A.F.Golestaneh et al./Materials and Design 30(2009)2928–29372935ture,hardness and residual stress and vary from one welding zone to another.On the other hand Nicholls model is only a function ofone coefficient 14E r Y K 2cwhere the exponent of D K is identical for allthe zones.Therefore Walker equation shows more reliable model for the case of crack propagation in FSW joints than Nicholls equa-tion.However by increasing the applied loading,Nicholls model represented higher agreement with those two other models and experiments,where for the LCF conditions all three models yielded the same results close to experiments.9.Conclusions1.Fatigue crack propagation through FSW joint consisting of four different zones with various characteristics was modelled using Walker and Nicholls fatigue models incorporating the effects of residual stress,stress relaxation,and crack closure.The results showed good agreement with experiments.However Walker model presented more accuracy on crack growth prediction compared with the Nicholls model.2.Fatigue lifetimes of the FSW joint of 2024-T351Al alloy were predicted based on two models and presented in the form of a S–N curve which showed a good consistent with test results.3.Although both of the models presented acceptable predictions,Walker equation yielded higher accuracy compared to the Nich-olls equation,especially for the HCF.However Nicholls model showed higher agreement for higher values of applied loadings in LCF conditions.AcknowledgementThe authors would like to appreciate University Putra Malay-sia (UPM)for awarding fellowships to two of the authors (A.F.Golestaneh and M.Zadeh Mohammadi)and for supporting this research.References[1]Fratinia L,Zuccarellob B.An analysis of through-thickness residual stresses inaluminium FSW butt joints.Int J Mach Tool Manufac 2006;46:611–9.[2]Scialpi A,de Filippis LAC,Cavaliere P.Influence of shoulder geometry onmicrostructure and mechanical properties of friction stir welded 6082aluminium alloy.Mater Design 2007;28:1124–9.[3]Ali A,Brown MW,Rodopoulos CA,Gardiner S.Characterization of 2024-T351friction stir welding joints.J Fail Anal Prev 2006;6:41–53.[4]Cavaliere P,Nobilea R,Panellaa FW,Squillaceb A.Mechanical andmicrostructural behaviour of 2024-7075aluminium alloy sheets joined by friction stir welding.Int J Mach Tool Manufac 2006;46:588–94.[5]Ceschini L,Boromei I,Minak G,Morri A,Tarterini F.Effect of friction stirwelding on microstructure,tensile and fatigue properties of the AA7005/10vol.%Al2O3p pos Sci Technol 2007;67:605–15.[6]Lomolinoa S,Tovob R,Dos Santos J.On the fatigue behavior and design curvesof friction stir butt-welded Al alloys.Int J Fatigue 2005;27:305–16.[7]Bussu G,Irving PE.The role of residual stress and heat affected zone propertieson fatigue crack propagation in friction stir welded 2024-T351aluminium joints.Int J Fatigue 2003;25:77–88.[8]Prime MB,Gnaupel-Herold T,Baumann JA,Lederich RJ,Bowden DM,SebringRJ.Residual stress measurements in a thick,dissimilar aluminium alloy friction stir weld.Acta Mater 2006;54:4013–21.[9]Staron P,Kocak M,Williams S,Wescott A.Residual stress in friction stir-welded Al sheets.Physica B 2004;350:e491–3.[10]Lombard H,Hattingh DG,Steuwer A,James MN.Optimising FSW processparameters to minimise defects and maximise fatigue life in 5083-H321aluminium alloy.Eng Fract Mech 2008;75:341–54.[11]Elangovan K,Balasubramanian V.Influences of pin profile and rotational speedof the tool on the formation of friction stir processing zone in AA2219aluminium alloy.Mater Sci Eng A 2007;459:7–18.[12]Hattingh DG,Blignault C,Van Niekerk TI,James MN.Characterization of theinfluences of FSW tool geometry on welding forces and weld tensile strength using an instrumented tool.J Mater Process Technol 2008;203:46–57.[13]Kim YG,Fujii H,Tsumura T,Komazaki T,Nakata K.Effect of weldingparameters on microstructure in the stir zone of FSW joints of aluminium die casting alloy.Mater Lett 2006;60:3830–7.[14]Cavaliere P,Panella F.Effect of tool position on the fatigue properties ofdissimilar 2024-7075sheets joined by friction stir welding.J Mater Process Technol 2008;206:249–55.[15]Elangovan K,Balasubramanian V.Influences of tool pin profile and toolshoulder diameter on the formation of friction stir processing zone in AA6061aluminium alloy.Mater Design 2008;29:362–73.[16]Ahmad Khodir S,Shibayanagi T.Friction stir welding of dissimilar AA2024andAA7075aluminum alloy.Mater Sci Eng B 2008;148:82–7.[17]Ceschini L,Boromei I,Minak G,Morri A,Tarterini F.Microstructure,tensile andfatigue properties of AA6061/20vol.%Al2O3p friction stir welded posites:Part A 2007;38:1200–10.[18]Jata KV,Sankaran KK,Ruschau JJ.Friction stir welding effects onmicrostructure and fatigue of aluminium alloy 7050-T7451.MMTA 2000;31:2181–92.[19]Booth D,Sinclair I.Fatigue of friction stir welded 2024-T351aluminium alloy.Mater Sci Forum 2002:1671–6.Table 3Number of cycles at the end of each FSW zone for various stress conditions predicted by Walker and Nicholls models.Max stress (MPa)At TMAZ–HAZ boundary (Cycles)At HAZ–PZ boundary (Cycles)Last propagation step (Cycles)WalkerNicholls Walker Nicholls Walker Nicholls 2701750,00188,000365,000388,000370,000388,0002741550,00175,000300,000315,000304,000316,0002851190,00155,000249,000269,000253,000271,00029592,000140,000212,000227,000216,000228,00030580,000110,000186,000205,000189,000207,00031067,00085,000161,000167,000162,500168,50033057,00073,000116,500129,500124,000131,00035346,00056,00094,000111,00096,000112,00037537,50038,00086,00088,00087,50088,50040031,50033,50066,50069,50068,50071,00044427,00027,50055,00055,50056,00061,00046024,00026,50052,00052,00053,00054,100Fig.12.Fatigue life predictions of FSW joint in 2024-T351Al alloy by Walker and Nicholls models.2936 A.F.Golestaneh et al./Materials and Design 30(2009)2928–2937。