参考自动化组合机床的plc控制系统设计.doc
四工位组合机床PLC设计说明书
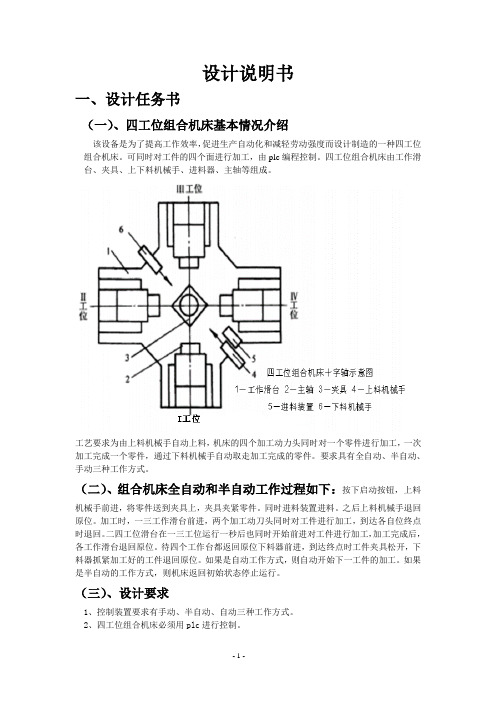
设计说明书一、设计任务书(一)、四工位组合机床基本情况介绍该设备是为了提高工作效率,促进生产自动化和减轻劳动强度而设计制造的一种四工位组合机床。
可同时对工件的四个面进行加工,由plc编程控制。
四工位组合机床由工作滑台、夹具、上下料机械手、进料器、主轴等组成。
工艺要求为由上料机械手自动上料,机床的四个加工动力头同时对一个零件进行加工,一次加工完成一个零件,通过下料机械手自动取走加工完成的零件。
要求具有全自动、半自动、手动三种工作方式。
(二)、组合机床全自动和半自动工作过程如下:按下启动按钮,上料机械手前进,将零件送到夹具上,夹具夹紧零件。
同时进料装置进料。
之后上料机械手退回原位。
加工时,一三工作滑台前进,两个加工动刀头同时对工件进行加工,到达各自位终点时退回。
二四工位滑台在一三工位运行一秒后也同时开始前进对工件进行加工,加工完成后,各工作滑台退回原位。
待四个工作台都返回原位下料器前进,到达终点时工件夹具松开,下料器抓紧加工好的工件退回原位。
如果是自动工作方式,则自动开始下一工件的加工。
如果是半自动的工作方式,则机床返回初始状态停止运行。
(三)、设计要求1、控制装置要求有手动、半自动、自动三种工作方式。
2、四工位组合机床必须用plc进行控制。
3、有急停、预停两种停止按钮。
4、滑台的进退,夹具的夹紧、松开以及上下料之间都进行互锁保护。
5、绘制电器原理图、选择电器元件、编制元件目录表。
6、绘制总接线图、控制面板布置图与接线图等工艺图样。
7、编制设计使用说明书。
8、设计用户程序,编写设计报告。
二、设计过程(一)、总体方案选择说明1、四工位组合机床四个主轴转动分别用M1~M4电机作为动力源。
2、四个滑台的进退以及夹具、上下料机械手和进料装置有一个液压系统进行控制,只需选用一个液压泵。
而冷却装置单独用一个液压系统进行控制。
3、四个滑台上都设有行程开关,来保证主轴与工件的相对位置的准确性。
4、M1~M4为自动控制连续运转,采用热继电器实现过载保护5、滑台的进退,夹具的夹紧、松开以及上下料之间都进行互锁保护。
plc第3章 组合钻床控制系统(电子书)

第3章组合钻床控制系统本章以组合钻床控制系统为例,先通过三台电机的启动、停止学习多台电机的控制方法,为组合钻床系统中电机的控制做基础,然后延续上一章的顺序控制设计法,学习使用SCR指令编写梯形图程序,掌握较全面的编程方法,最终使学生有应对一些复杂项目的能力。
教学导航教知识重点(1)多台电机的启动、停止控制。
(2)使用SCR指令设计顺序功能图。
(3)使用SCR指令编写梯形图程序。
知识难点使用SCR指令编写梯形图程序。
推荐教学方法本章的知识链接部分用讲授法和引导文法;初步训练部分使用案例教学法;强化训练、拓展训练部分使用项目教学法。
学推荐学习方法动手完成多台电机的启动、停止控制,进一步掌握编程中常用的经验设计法;通过组合钻床控制系统的完成,掌握使用SCR指令设计顺序功能图,并编写梯形图程序的方法,并在实施过程中深入理解S7-200的编程指令真正含义。
必须掌握的理论知识(1)使用SCR指令设计顺序功能图。
(2)使用SCR指令编写梯形图程序。
必须掌握的技能(1)S7-200外围电路的接线连接。
(2)S7-200编程控制多台电机的启停。
3.1 组合钻床系统介绍钻床指主要用钻头在工件上加工孔的机床。
通常钻头旋转为主运动,钻头轴向移动为进给运动。
钻床结构简单,加工精度相对较低,可钻通孔、盲孔,更换特殊刀具,可扩、锪孔,铰孔或进行攻丝等加工。
加工过程中工件不动,让刀具移动,将刀具中心对正孔中心,并使刀具转动(主运动)。
钻床的特点是工件固定不动,刀具做旋转运动。
根据钻床的用途和结构主要分为以下几类:1、立式工作台和主轴箱可以在立柱上垂直移动,用于加工中小型工件。
2、台式简称台钻。
一种小型立式钻床,最大钻孔直径为12~15毫米,安装在钳工台上使用,多为手动进钻,常用来加工小型工件的小孔等。
3、摇臂式主轴箱能在摇臂上移动,摇臂能回转和升降,工件固定不动,适用于加工大而重和多孔的工件,广泛应用于机械制造中。
4、深孔钻床用深孔钻钻削深度比直径大得多的孔(如枪管、炮筒和机床主轴等零件的深孔)的专门化机床,为便于除切屑及避免机床过于高大,一般为卧式布局,常备有冷却液输送装置(由刀具内部输入冷却液至切削部位)及周期退刀排屑装置等。
PLC在组合机床控制中的应用

1工作原理和要求
现有一个 回转式 8工位组合机床,用于加工某工件
一
个 侧面的 出油孔 ,主要 加工动作有钻孔 、扩 孔 、铰
图 1 系统框图
孔 、倒角等,加工时进刀量和精度 由液压系统及机械机 构 控 制 。 机 床 上 共 有 8个 工 位 , 2工 位 之 间 的 夹 角为 4 。, I 5 工位用于装卸工件,其余 7 工位均 由 F 个 C控
般档次的带有移位寄存器和移位指令编程的 P C L ,也 可用带有步进指令编程的 P C L 。信号输入通过行程开 关 控制; 手动、自动的工作方式和手动进给部件选择用转换 开 关选择 。控制系统的执行元件用 电磁阀;动力头 电机 正、反转用接触器。根据动作要求,系统 中的输入部分
一
32 回转 台调整 .
可靠性 差等缺点 。特别是在更换 产品而改变动作 循环 时,需重 新设 计 、安装 、调试,不能适 应现代生产 要
求 ,若将 原 系 统 改装 为 P C 控 制 系统 ,利 用 P C 对 组 L L 合 机床 进行 控 制改 造 ,则 能克 服 上述 不 足 ,较 好 地 提 高 了其 可 靠性和 灵 活性 。
左 辉 (9 9 ) 女 , 1 6 一 , 本科 , 师 。 讲
5 I WW.hn e.e 电工技术 O W c ia t t n I
维普资讯
数控 技 术
前位 ,它 们 作为 P C 的输入 信 号量 , 以改 变机 床工 作 状 L 态 。 由于这 3个 行程 开 关 指示 机 床 的 3个 不 同位置 , 因 此 在 任何 情 况 下 ,它 们 中 的任 何 两 个 都 不 能 同时 闭 合 , 若有 两 个 同 时闭 合 ,只 能 说 明行 程 开 关 出 了故 障 。当 各
基于PLC的组合机床控制系统设计
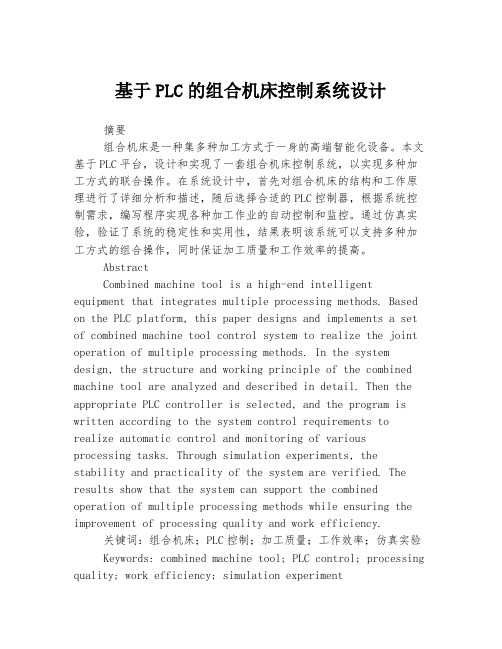
基于PLC的组合机床控制系统设计摘要组合机床是一种集多种加工方式于一身的高端智能化设备。
本文基于PLC平台,设计和实现了一套组合机床控制系统,以实现多种加工方式的联合操作。
在系统设计中,首先对组合机床的结构和工作原理进行了详细分析和描述,随后选择合适的PLC控制器,根据系统控制需求,编写程序实现各种加工作业的自动控制和监控。
通过仿真实验,验证了系统的稳定性和实用性,结果表明该系统可以支持多种加工方式的组合操作,同时保证加工质量和工作效率的提高。
AbstractCombined machine tool is a high-end intelligent equipment that integrates multiple processing methods. Based on the PLC platform, this paper designs and implements a set of combined machine tool control system to realize the joint operation of multiple processing methods. In the system design, the structure and working principle of the combined machine tool are analyzed and described in detail. Then the appropriate PLC controller is selected, and the program is written according to the system control requirements to realize automatic control and monitoring of various processing tasks. Through simulation experiments, thestability and practicality of the system are verified. The results show that the system can support the combined operation of multiple processing methods while ensuring the improvement of processing quality and work efficiency.关键词:组合机床;PLC控制;加工质量;工作效率;仿真实验Keywords: combined machine tool; PLC control; processing quality; work efficiency; simulation experiment一、研究背景随着工业技术的快速发展,组合机床逐渐成为了制造业领域中的重要设备。
plc 毕业设计(完好篇)

多工步组合机床的PLC控制系统设计摘要工业机床的控制在工业生产自动化控制中占有重要的位置。
在机床行业中,多工步动作多机床由于其工步及,控制较为复杂。
采用传统的继电器控制时,需要的继电器多,接线复杂,因此故障多,维修困难、费时费力。
采用PLC控制,可是接线大为简化,不但安装十分方便,而且保证了可靠性,减少了维修量,提高了功效。
制造业是一个国家或地区经济发展的重要支柱,其发展水平标志着该国家或地区的经实力、科技水平、生活水准和国防实力。
而制造业的生产能力蛀牙取决于执照设备——机床的先进程度。
多工步机床用于加工棉纺锭子锭脚的一种加工机床,某锭脚加工工艺比较复杂,零件加工前为实心毛坯件,整个机械加工由7个刀具分分别按照7个工步要求依次进行切削。
7个工步依次为:钻孔、车平面、钻深孔、车外圆及钻孔、粗绞双节孔及倒角、精绞双节孔、绞锥孔的工步要求。
关键词:制造业,多工步机床,PLC控制,梯形图Design of combination machine tools control system of PLCABSTRACTThe control of industrial automation control in industrial production occupies an important position. The machine tool industry , multi-stage machine and work because of its action,control is more complicated. Using traditional relay control, need complex, the relay, fault than wiring, maintenance difficulties, Feigong time-consuming. PLC control, but not only greatly simplified wiring, installation is very convenient, and ensure the reliability, reduce the maintenance and increase the efficiency.Manufacturing is one country or region development of the important pillars, its development level mark the country or region`s economic strength and technology level, the living standards and national defence capabilities. While manufacturing production capacity depends on the advanced manufacturing equipment, machine tool. Many workers step for processing cotton spinning ingots machine a processing machine a feet, a spindle feet processing technology is more complex, parts processing for solid blank piece before, the whole mechanical processing by seven tool points respectively according to seven workers were cutting step requirements. Seven work step is as follows: the drilling, car plane, drill deep holes, outside, round and drilling, coarse twisted double festival hole and chamfering and fine twisted double festival, twisted tapered bore holes work step requirements.KEY WORDS: Manufacturing,Multi-stage machine, PLC control,Iadder-iagram目录前言 (1)第1章多工步组合机床与PLC (2)1.1 课题研究的背景 (2)1.1.1 我国工业电气控制技术的发展状况 (2)1.2可编程控制器的简介 (3)1.2.1可编程控制的定义 (3)1.2.2 PLC的特点 (4)1.3 课题的提出 (5)1.4 课题研究的意义,价值和技术可行性 (5)1.4.1 PLC控制与继电器控制的比较 (5)1.4.2 PLC控制与单片机控制的比较 (7)1.5 小结 (7)第2章硬件设计 (8)2.1 PLC选型设计 (8)2.2 PLC的I/O编址 (9)2.2.1 PLC的I/O具体分配表 (9)2.3 PLC的I/O电路设计 (10)2.4 元件明细表 (11)2.5 小结 (14)第3章软件设计 (16)3.1软件开发平台和编程语言的选择 (16)3.1.1软件开发平台 (16)3.1.2编程语言的选择 (16)3.2多工步机床电气控制系统的流程图设计 (18)3.3 多工步机床电气控制系统梯形图设计 (19)3.4 小结 (24)第4章组态设计 (26)4.1 人机界面(HMI)设计 (27)4.2 定义设备和连接变量 (29)4.3 数据变量定义 (29)4.4 动画连接与命令语言 (30)4.5 组态图 (33)结论 (35)谢辞 (36)参考文献 (37)外文资料翻译 (38)前言工业机床的控制在工业生产自动化控制中占有重要的位置。
基于PLC的组合机床控制系统设计
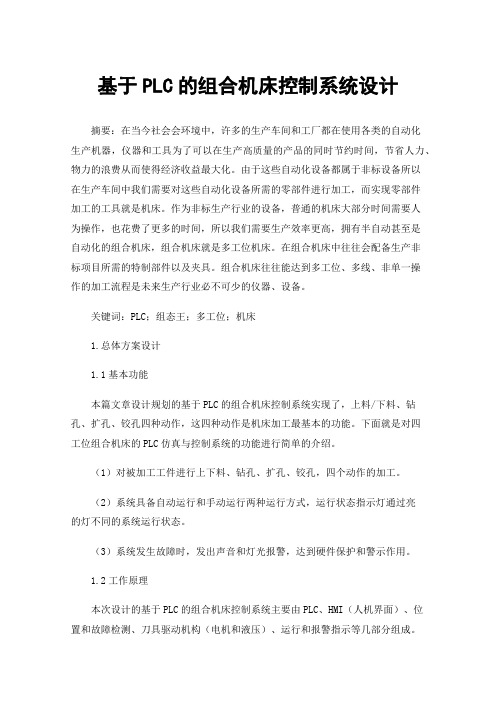
基于PLC的组合机床控制系统设计摘要:在当今社会会环境中,许多的生产车间和工厂都在使用各类的自动化生产机器,仪器和工具为了可以在生产高质量的产品的同时节约时间,节省人力、物力的浪费从而使得经济收益最大化。
由于这些自动化设备都属于非标设备所以在生产车间中我们需要对这些自动化设备所需的零部件进行加工,而实现零部件加工的工具就是机床。
作为非标生产行业的设备,普通的机床大部分时间需要人为操作,也花费了更多的时间,所以我们需要生产效率更高,拥有半自动甚至是自动化的组合机床,组合机床就是多工位机床。
在组合机床中往往会配备生产非标项目所需的特制部件以及夹具。
组合机床往往能达到多工位、多线、非单一操作的加工流程是未来生产行业必不可少的仪器、设备。
关键词:PLC;组态王;多工位;机床1.总体方案设计1.1基本功能本篇文章设计规划的基于PLC的组合机床控制系统实现了,上料/下料、钻孔、扩孔、铰孔四种动作,这四种动作是机床加工最基本的功能。
下面就是对四工位组合机床的PLC仿真与控制系统的功能进行简单的介绍。
(1)对被加工工件进行上下料、钻孔、扩孔、铰孔,四个动作的加工。
(2)系统具备自动运行和手动运行两种运行方式,运行状态指示灯通过亮的灯不同的系统运行状态。
(3)系统发生故障时,发出声音和灯光报警,达到硬件保护和警示作用。
1.2工作原理本次设计的基于PLC的组合机床控制系统主要由PLC、HMI(人机界面)、位置和故障检测、刀具驱动机构(电机和液压)、运行和报警指示等几部分组成。
当PLC检测到机加工位有元工件时,然后钻孔工位、扩孔工位、铰孔工位对工件进行加工,加工完成再回到原始工位,取走工件,然后等待下一个工件的到来。
如果PLC检测到系统故障,系统会启动自我保护功能(自动运行将不能运行或启动),同时发出报警以引起工作人员的注意。
在整个运行过程中,系统执行件的每个状态都会显示在触摸屏(HMI)上,进行人机交互。
2.设计方案2.1控制系统电源的设计本设计系统中供电电源为交流380V,PLC的供电电源为交流220V,使用隔离变压器为其供电,PLC输入/输出回路的电源为直流24V,选用交流220V/直流24V直流稳压电源。
机电一体化PLC毕业设计
第二章 自动化组合机床的硬件
PLC输入地址编号
第二章 自动化组合机床的硬件
PLC输出地址编号
第二章 自动化组合机床的硬件
根据输入/输出点分配,画出PLC的外部接 线图
Hebei Institute of Machine and Electrical Technology
第二章 自动化组合机床的硬件
液动回转台工作控制过程
自锁销脱开及回转台抬起 按回回转转台按钮回S转B4及,缓电冲磁铁YA5通电(动力头在原位 时回,转限台位开反关靠SQ1被压动,回转台才能转位)。将
电磁阀YV1的阀杆推向右端,将液压泵的压力油送
到回夹转紧台液压夹缸紧1G,使其活塞上移抬起回转台。同时 经使离阀自合Y锁V器销1的脱脱压开开力。后油的也状送到态自锁液压缸2G,活塞下移
动作,接通信号,使滑台快 速返回。达到原始位置时, 便停止转动,完成一个工作 循环
第二章 自动化组合机床的硬件
输入设备与输出设备
输入设备器件:启动/停止按钮8个、限位开关8个 压力继电器1个
输出设备器件:交流接触器3个、电磁铁10个、隔 离开关1个、熔断器9个、热继电 器3个
第二章 自动化组合机床的硬件
第二章 自动化组合机床的硬件
主回路
1、 M1主电动机用来控制工 件的进退。只需单方向起动, 要求有短路及过载保护。 2、M2液压泵电动机用来提供 液压。也只需单方向起动, 要求有短路及过载保护 3、M3冷却泵功率较小,单方 向运转,要求有短路及过载 保护。 4、M1和M2可以同时起停,也 可单独起停。 5、要求在动力头工作时,即 M2起动后,M3才接通,但也 可以随时调整。
我的毕业设计介绍完毕 谢谢各位老师
四工位组合机床的plc控制系统设计 正文
正文第一章绪论一、组合机床概述组合机床是针对特定工件,进行特定加工而设计的一种高效率自动化专用加工设备,这类设备大多能多刀同时工作,并且具有自动循环的功能。
组合机床是随着机械工业的不断发展,由通用机床、专用机床发展起来的。
通用机床一般用一把刀具进行加工,自动化程度低、辅助时间长、生产效率低,但通用机床能够重新调整,以适应加工对象的变化。
专用机床可以实现的多刀切削,自动化程度较高,结构较简单,生产效率也较高。
但是,专用机床的设计,制造周期长,造价高,工作可靠性也较差。
专用机床是针对某工件的一定工序设计的,当产品进行改进,工件的结构,尺寸稍有变化时,它就不能继续使用。
在综合了通用机床、专用机床优点的基础上产生了组合机床。
组合机床通常由标准通用部件和加工专用部件组合构成,动力部件采用电动机驱动或采用液压系统驱动,由电气系统进行工作自动循环的控制,是典型的机电或机电液一体化的自动加工设备。
常见的组合机床,标准通用部件有动力滑台各种加工动力头以及回转工作台等,可用电动机驱动,也可用液压驱动。
各标准通用动力部件组合构成一台组合机床时,该机床的控制电路可由各动力部件的控制电路通过一定的连接电路组合构成。
多动力部件构成的组合机床,其控制通常有三方面的工作要求:第一方面是动力部件的点动和复位控制。
第二方面是动力部件的半自动循环控制。
第三方面是整批全自动工作循环控制。
组合机床具有生产率高、加工精度稳定的优点。
因而,在汽车、柴油机、电机、机床等一些具有一定生产批量的企业中得到了广泛应用。
目前,组合机床的研制正向高效、高精度、高自动化和柔和性化方向发展。
本文所用组合机床为四工位组合机床,该机床由四个滑台,各载一个加工动力头,组成四个加工工位,除了四个加工工位外,还有夹具,上下料机械手和进料器,四个辅助装置以及冷却和液压系统共14个部分。
机床的四个加工动力头同时对一个零件的四个端面以及中心孔进行加工,一次加工完成一个零件,由上料机械手自动上料,下料机械手自动取走加工完成的零件,零件每小时可加工80件。
基于PLC的组合机床控制系统设计
基于PLC的组合机床控制系统设计摘要组合机床是高度机电一体化的产品,是现代机床技术水平的重要标志,是现代机械制造业重要标志,是现代制造业的基础装备,尤其是在加工产品更换频繁、零件形状复杂、精度要求较高的工件时,不但可以节省大量的时间和资源,而且还能够确保工件的质量与产量,进而提高生产效率,具有良好的经济性。
传统的机床主要采用继电器--接触器进行控制,其缺点是故障率高、可靠性差、维修工作量大等,而采用PLC组成的控制系统可以很好地解决上述问题。
本文在基于可编程控制器(PLC)的结构和工作原理的基础上,介绍了基于PLC的加工中心控制系统的总体方案设计,重点介绍了加工中心控制系统中的硬件选择方法、软件的设计过程,并给出了系统组成框图和程序流程图,提出了西门子PLC 的编程方法,列出了具体的主要硬件电路、加工中心的控制梯形图及指令表,解决了继电器——接触器故障率高、可靠性差、安装调试周期长、维修工作量大、接线复杂等缺点。
关键词:组合机床,继电器—接触器,PLC,控制系统Based on a combination of the plc toolsto monitor system designABSTRACTBuilding-block machine is a highly integrated mechanical and electrical products, is an important indicator of the level of modern technology ,is an important symbol of modern machinery manufacturing industry ,is the basis of modern manufacturing equipment, especially in the frequent replacement of processed products, spare parts of complex shape, the accuracy requirements are more stringent than work piece high, not only can save a lot of time and resources, but also to ensure the quality and output of the work piece, thus improving production efficiency, has a good economy.The main use of the traditional machine tool relay - contactor control, the drawback is the high failure rate, poor reliability,heavy workload of maintenance, consisting of the use of PLC control system can solve these problems. In this paper, based on the programmable logic controller (PLC) of the structure and working principle, based on the introduction of the PLC-based control system for machining center's overall program design, focuses on the machining center control system hardware selection, software design process and gives the system flow chart diagram and procedures, put forward a Siemens PLC programming methods, a list of specific hardware circuit, the control processing center table ladder and instructions to solve the relay - contacts high failure rate, reliability, poor long-term installation, maintenance workload and the complexity of wiring and other shortcomings.KEY WORDS: Building-block machine, the relay - contactor, PLC, control system目录前言 (1)第1章组合机床的概述 (3)1.1组合机床的发展史 (3)1.2 组合机床的加工方式 (4)1.3 组合机床的特点与未来发展 (4)1.3.1 组合机床的特点 (4)1.3.2组合机床的未来发展 (4)第2章可编程序控制器 (6)2.1 PLC的应用与特点 (6)2.1.1 PLC的应用 (6)2.2.2 PLC的特点 (7)2.2 PLC的工作原理 (8)第3章控制系统的方案设计 (10)3.1组合机床控制系统的工艺流程图及设计要求 (10)3.2根据工艺过程分析控制要求 (11)3.2.1加工过程分析: (11)3.2.2操作方式 (12)第4章控制系统硬件设计 (13)4.1选择PLC机型 (13)4.2 S7-200 PLC的简要介绍 (14)4.3控制系统PLC的输入/输出分配表 (16)4.4PLC硬件连接图 (19)第5章控制系统软件设计 (20)5.1控制流程图设计 (20)5.2梯形图的分解阐述 (22)第6章仿真模拟 (28)结论 (29)谢辞 (30)参考文献 (31)附录 (32)外文资料翻译 (39)前言随着科学技术的发展,近年来我国的机械生产技术得到飞速的发展,一些机械设备制造厂商也在不断地改进设计,修改工艺,生产新型的机械制造设备,组合机床就是其中之一。
组合机床的电气与PLC控制系统设计
组合机床的电气与PLC控制系统设计摘要可编程控制器(plc)是以微处理机为基础,综合了计算机技术、自动控制技术和通信技术等现代科技而发展起来的一种新型工业自动控制装置,其具有逻辑控制、计时、计数、数据处理、联网与通信等强大功能,同时,由于plc具有很高的可靠性和极大的应用灵活性,用它来替代传统的继电接触控制系统巳成为必然。
大量采用传统继电一接触控制系统的设备通过改造更新,成为plc控制的自动化系统,而且具有改造成本低、周期短和可靠性高等特点。
本文介绍双面钻孔组合机床的电气控制系统设计与应用。
双面钻孔组合机床是在工件两相对表面上钻孔的一种高效率自动化专用加工设备。
本次课程设计的内容是对双面钻孔组合机床电气控制系统的设计。
在机床电气控制系统中既有自动控制又有手动控制方式因此在本次设计中对控制系统既有自动控制方式的设计也有手动方式的设计。
本次设计采用PCL控制系统来实现双面钻孔组合机床的电气系统控制,包含控制系统的硬件电路设计和软件电路设计两个部分,本设计以PCL控制系统为核心列出了PCL的输入输出点分配表,绘制了PCL的输入输出点接线图和控制状态转移图,编写了PCL控制程序的梯形图和指令表。
关键字:双面钻孔组合机床;PCL;可编程控制器;目录第1章设计目的要求和概述 (3)1.1 设计目的 (3)1.2 双面钻孔组合机床的概述 (3)1.3设计要求与任务分配 (3)第2章双面钻孔组合机床的控制要求 (5)2.1 双面钻孔组合机床的工作流程 (5)2.2电动机控制要求 (5)2.3 机床动力滑台、工件定位装置、夹紧装置控制要求 (6)第 3 章 PLC的简介与选择 (8)3.1 PLC (8)3.2 PLC简介 (8)3.3 PLC的结构及基本配置 (8)3.4 PLC选择 (9)第4章双面钻孔机床左机钻孔顺序动作PLC控制 (10)4.1 双面钻孔组合机床的左机钻孔自动控制PLC输入输出点分配 (10)4.2状态继电器的分配 (10)第5章双面钻孔组合机床的PLC控制实现 (14)5.1 并行分支状态转移 (14)5.2 PLC控制考虑上双面钻孔组合机床的手动方式控制 (14)第6章总结 (21)参考文献 (22)第1章设计目的要求和概述1.1 设计目的1、培养学生综合分析和解决本专业的一般工程技术问题的独立工作能力,拓宽和深化学生的知识。
- 1、下载文档前请自行甄别文档内容的完整性,平台不提供额外的编辑、内容补充、找答案等附加服务。
- 2、"仅部分预览"的文档,不可在线预览部分如存在完整性等问题,可反馈申请退款(可完整预览的文档不适用该条件!)。
- 3、如文档侵犯您的权益,请联系客服反馈,我们会尽快为您处理(人工客服工作时间:9:00-18:30)。
设计项目名称自动化组合机床的PLC控制系统设计AbstractThis article introduced that the PLC control system design of Automatic combined machine tool, this system has a high degree of automation and precision, and also be widely used in industrial production and other fields. The traditional combined machine tool uses the relays generally, the precision is low, the reliability is not high, did not meet the social development need. Along with the PLC control technology's rapidly expand, as the core combined machine tool has highlighted its superiority take PLC.This paper first introduced that PLC and the history and development of the combined machine tools, and emphatically expounds the structure, movement and the control mode of combined machine tools, then the composition of PLC is analyzed, besides these, the general arrangement of PLC control system and the presentation of program are also given an overview, then we confirm PLC's type, distribute I/O address and external wiring. According to the related content we draw sequential function chart and use FXGPWIN software to draw PLC ladder diagram. At the end of the article we also introduced Fault diagnosis and exclusion of PLC control system and further summary fo the article.【Key words】: PLC 、Mitsubishi FX series、combined machine tools摘要本文介绍自动化组合机床的PLC控制系统设计,该系统具有自动化程度高,精度高等特点,在工业生产等领域有广泛应用。
传统的组合机床采用继电器,精度低,可靠性不高,已不适合社会发展需要。
随着PLC控制技术的迅速发展,以PLC为核心的组合机床控制系统已凸显出其优势。
本文首先介绍PLC和组合机床的历史与发展,并论述了组合机床的运动形式以及控制方式,接着对PLC控制系统的总体设计和程序的表达方式做了概述,然后确定PLC型号、分配I/O地址和外部配线,接着根据相关内容画出顺序功能图并利用FXGPWIN软件画出PLC梯形图。
在文章的最后还介绍了PLC控制系统的故障诊断和排除以及对论文的进一步总结。
【关键字】PLC,三菱FX系列,组合机床目录Abstract (1)摘要…………………………………………………………………………………………………………….2第1章概述………………………………………………….………………………………………41.1 机械自动化发展史 (4)1.2 自动化组合机床的特点及应用……………………………………………………… 6. 第2章自动化组合机床的硬件……………………………………………………82.1 课题要求……………………………………………………………………………………………82.2 确定输入设备与输出设备………………………………………………………………102.3 I/O点分配……………………………………………………………………………………….112.4 PLC类型选择…………………………………………………………………………………122.5 PLC外围硬件电路图……………………………………………………………………15第3章自动化组合机床的PLC控制系统软件 (16)3.1根据系统的控制要求设计程序…………………………………………………….163.2 模拟调试及优化…………………………………………………………………………….213.3 联机调试……..……………..………………………………………………………………….23第4章PLC控制系统故障诊断与排除……………………………………25心得体会 (28)致谢 (29)参考文献 (30)附录1 操作说明书 (31)附录2 PLC外围硬件电路图…………………………………………………………………..32附录3 PLC外部接线图..................................................................................... 34 附录4 梯形图 (36)第1章概述1.1 机械自动化发展史自动化技术是本世纪以来发展机迅速和影响极大的科学技术之一。
现代自动化技术是一种完全新型的生产力,是直接创造社会财富的主要手段之一,对人类的生产活动和物质文明起着极大的推动作用。
机械自动化,主要指在机械制造业中应用自动化技术,实现加工对象的连续自动生产,实现优化有效的自动生产过程,加快生产投入物的加工变换和流动速度。
机械自动化技术的应用与发展,是机械制造业技术改造、技术进步的动速度。
机械自动化技术的应用与发展,是机械制造业技术改造、技术进步的制造业的发展,而且对国民经济各部门的技术进步有很大的直接影响。
1、机械自动化技术机械自动化是一个由低级到高级、由简单到复杂、由不完善到完善的发展过程。
当机器的操作采用自动控制器后,生产方式才从机械化逐步过渡到机械控制(传统)自动化、数字控制自动化、计算机控制自动化。
只有建立了自动化工厂后,生产过程才能全盘自动化,才能使生产率全面提高,达到自动化的高级理想阶段。
机械自动化技术从本世纪20年代首先在机械制造冷加工大批量生产过程中开始发展应用,60年代后为适应市场的需求和变化,为增强机械制造业对市场灵活快速反应的能力,开始建立可变性自动化生产系统,即围绕计算机技术的柔性自动化。
它是在制造系统不变或变化较小的情况下,机器设备或生产管理过程通过自动检测、信息处理、分析判断自动地实现预期的操作或某种过程,并能够自动地从制造一种零件转换到制造另一种不同的零件。
70~80年代国际上出现了开始采用计算机集成制造系统CIMS(Computer Integrated Manufacturing),柔性自动化生产模式也有这种情况。
初期犆犐犕犛以信息集成为重点,以较高的自动化程度为特征,但在实现过程中遇到了困难。
鉴于实现计算机集成制造系统的全盘自动化所需的巨额投入(一个全盘自动化工厂耗资数百亿美元,柔性制造系统一般价格为600~2500万美元),所承担的巨大风险,加之技术上的难度与可靠性等问题,世界工业发达国家已开始“碰壁转产”,转而注重信息集成的效果,追求低成本自动化LCA(Low Cost Automation)的企业组织结构和运行方式。
目前,世界各国的机械自动化水准除少数工业发达国家的某些生产部门外,大多数还处于操作阶段的自动化。
我国也不例外,需要循序渐进,不断努力,创造条件,向自动化的高级理想阶段迈进。
实现我国机械自动化技术是一个长期的过程,不可能一蹴而就。
应该发展工艺成熟的大批量生产的自动化技术。
大批量生产的产品品种单一,结构稳定,产量很大,具有连续流水作业和综合机械化的良好条件。
应发展生产效率高和技术经济效果良好的生产自动线,并在自动线的基础上按先进的工艺方案建立综合自动化车间和全盘自动化工厂。
组合机床自动线和专用机床自动线成本低,应优先发展。
我国现阶段,在产品数量较大的同类产品连续流水作业的切削加工生产中,自动化设备仍然是半自动机床、自动机床、组合机床及其组成的自动线、回转体零件加工自动线等。
2、发展机械自动化技术发展机械自动化技术,应以企业的生产和技术发展的实际需要及具体条件为导向。
只有对合适的产品采用与之相适应的自动化方式进行生产,才能收到良好的技术经济效益和社会经济效益。
70~80年代初期,我国发展数控机床缺乏明确的战略思想,究竟解决我国制造技术中哪些主要技术问题,似乎并不十分明确,带有浓厚的就技术论技术色彩,偏重速度,忽视效益,造成了不少数控机床只出样品、展品,不能提供商品,用于生产实际。
70年代中期研制成功的数控机床,除数控非圆插齿机、数控劈锥铣床等能提供商品用于生产外,相当多的数控机床未能正常提供商品,甚至有的数控机床最终还是报废。
80年代后期乃至“八五”计划期间,我国数控机床自动化技术发展是快速的,但却是在曲折中前进。
造成这种状况的原因是多方面的,但主要是在发展策略上有失误:主机攻关有背当时国内的主要市场,没有适应生产需要发展数控机床自动化技术,结果是数控机床品种虽不少,而结构性能重复的较多,影响了自动化数控机床的实际应用。
在已有的数控机床中,能正常使用、不能正常使用和不能使用的各占三分之一。
而正常和稳定运行的数控机床的利用率也很低。
我国的铸造造型线品种不少,引进的多达一百几十条,从紧实原理、PC机控制到布线方式都是先进的,可以说当今世界上几乎所有的各类先进造型线都引进了,但能在生产中长期服役的生产线很少,相当数量的引进造型线长期闲置,没有发挥实效。
3、自动化技术发展低成本自动化技术,潜力大,前景广,投资省,见效快,提高自动化程度,可以收到事半功倍的经济效果,适合我国现阶段的发展需要和国情。
90年代美国麻省理工学院提出的精节生产LP(Lean Production)模式,就是以最小的投入,取得最大的产出的具体表现。
我国机械制造业各企业有大量的通用设备,在发展现代机械自动化技术时,若以原有的设备为主,合理调整机床布局,添加少量的数控设备,引入PLC技术,充分发挥计算机自动化管理的优势和人的创造性,共同构成一个以人为中心、以信息自动化为先导、树立自主的单元化生产系统,为我国机械制造业自动化技术发展应用提供了一条投资少、见效快、效益高、机械自动化技术发展应用新途径。