一、切削原理
《金属切削原理与刀具》知识点总结
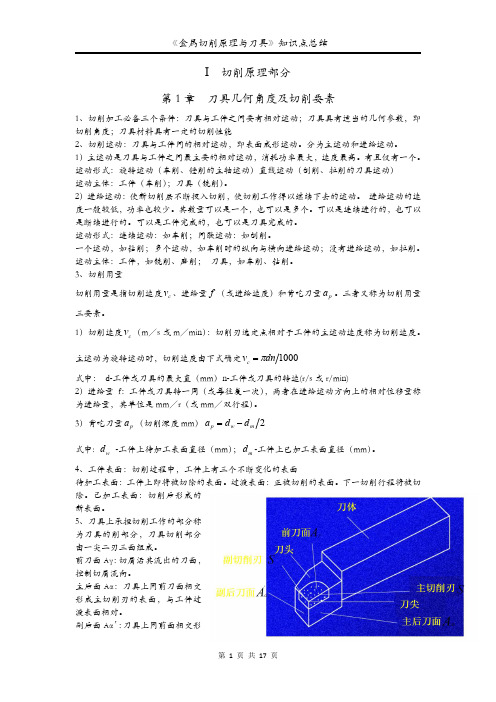
I 切削原理部分第1章刀具几何角度及切削要素1、切削加工必备三个条件:刀具与工件之间要有相对运动;刀具具有适当的几何参数,即切削角度;刀具材料具有一定的切削性能2、切削运动:刀具与工件间的相对运动,即表面成形运动。
分为主运动和进给运动。
1)主运动是刀具与工件之间最主要的相对运动,消耗功率最大,速度最高。
有且仅有一个。
运动形式:旋转运动(车削、镗削的主轴运动)直线运动(刨削、拉削的刀具运动)运动主体:工件(车削);刀具(铣削)。
2)进给运动:使新切削层不断投入切削,使切削工作得以继续下去的运动。
进给运动的速度一般较低,功率也较少。
其数量可以是一个,也可以是多个。
可以是连续进行的,也可以是断续进行的。
可以是工件完成的,也可以是刀具完成的。
运动形式:连续运动:如车削;间歇运动:如刨削。
一个运动,如钻削;多个运动,如车削时的纵向与横向进给运动;没有进给运动,如拉削。
运动主体:工件,如铣削、磨削;刀具,如车削、钻削。
3、切削用量切削用量是指切削速度c v 、进给量f (或进给速度)和背吃刀量p a 。
三者又称为切削用量三要素。
1)切削速度c v (m/s 或m/min):切削刃选定点相对于工件的主运动速度称为切削速度。
主运动为旋转运动时,切削速度由下式确定1000dn v c π=式中:d-工件或刀具的最大直(mm)n-工件或刀具的转速(r/s 或r/min)2)进给量f:工件或刀具转一周(或每往复一次),两者在进给运动方向上的相对位移量称为进给量,其单位是mm/r(或mm/双行程)。
3)背吃刀量p a (切削深度mm)2m w p d d a -=式中:w d -工件上待加工表面直径(mm);m d -工件上已加工表面直径(mm)。
4、工件表面:切削过程中,工件上有三个不断变化的表面待加工表面:工件上即将被切除的表面。
过渡表面:正被切削的表面。
下一切削行程将被切除。
己加工表面:切削后形成的新表面。
5、刀具上承担切削工作的部分称为刀具的削部分,刀具切削部分由一尖二刃三面组成。
机械加工的工艺原理是

机械加工的工艺原理是
机械加工是利用机械设备对工件进行切削、磨削、拔拉、钻削等加工过程的技术。
其工艺原理主要包括以下几个方面:
1. 切削原理:利用刀具与工件之间的相对运动,以切削刃对工件进行削除材料的操作。
刀具通过推刀进给或工件旋转提供所需的运动,切削刃将工件上的材料削除,形成所需的形状和尺寸。
2. 磨削原理:利用磨料颗粒在工件表面的相对运动,将磨削粒子对工件材料的切削和磨擦作用,使工件表面达到所要求的精度和光洁度。
3. 拔拉原理:通过拔拉设备,将工件在规定的力下进行拉伸,使其形成所需的形状,如拉制金属线材和伸长钢材等。
4. 钻削原理:通过旋转运动和向前进给的力,通过刀具的刃部对工件进行孔洞加工,同时将削屑排除。
总的来说,机械加工的工艺原理是通过机械设备对工件进行切削、磨削、拔拉、钻削等操作,以实现工件形状、尺寸和表面质量的加工要求。
整个过程依靠机械设备提供运动和力量,通过切削或磨削等方式将工件的材料削除或变形,从而得到所需的产品或工件。
车铣刨磨钻的原理

车铣刨磨钻的原理
车铣刨磨钻都是基于金属切削原理工作的机械加工工具,其原理可概括为: 1. 切削原理
工具的切削刃将加工材料切削下来,逐步形成所需的形状和尺寸。
2. 主运动和切削运动
车床主轴转动提供主运动,切削刀具相对工件作切削运动。
3. 控制切屑
切屑槽引导和排出切屑,防止切屑堵塞影响切削。
4. 切削力平衡
合理的刀具结构和加工参数,平衡切削力,保证切削稳定。
5. 刃尖强度
选用合适的刀具材料,使刃尖保持高强度和硬度,提高刀具寿命。
6. 制动和火花防护
车铣等高速旋转时需要安装制动装置;钻孔时需防护火花。
7. 冷却和润滑
切削部位的冷却和润滑,主要通过切削液实现。
8. 优化切削参数
合理选择切削速度、进给量等参数,优化切削过程,提高效率。
9. 精确定位系统
严格定位系统保证加工精度,如丝杠传动定位等。
10. 刀架和刀体系设计
合理刀架结构设计实现刀具快换;刀体系选用匹配不同加工需求。
综上,这些机械加工工具都遵循切削原理,但根据具体用途有不同结构设计。
1-1切削概念解析

图1.1-13 外圆纵车时的切削层参数
20
1.1.4 切削层参数
(1)切削层
在切削加工中,刀具相对于工件沿进给方向每移动 f 或 fz 之后,正在 切削的金属层称为切削层。
(2)切削厚度hD
垂直于过渡表面来度量的切削层尺寸,称为切削厚度,以hD表示。 在外圆纵车时 hD = f sinkr
(3)切削宽度bD
沿过渡表面度量的切削层尺寸,称为切削宽度,以bD表示。 在外圆纵车时 bD = ap/sinkr 可见,在f 、ap一定的条件下,主偏角增大,切削厚度也增大,但切 削宽度减小,当kr=90o时,hD=f。
图1.1-3 a)刨削
6
例2 分析铣削的切削运动、加工表面 和切削用量。
图1.1-3 b)铣削
7
1.1.2 切削用量(cutting conditions)
(1)切削速度vc (cutting speed)
切削刃的选定点相对于工件的主运动的瞬时速度,单位为m/min(切削) 或 m/s (磨削)。一般计算最大的切削速度。 回转主运动的计算公式如下:vc=πdn/1000
工件上已加工表面和待加工表面间的垂直距离,单位为mm。
ap =(dw - dm)/2
8
1.1.3 刀具切削部分的几何参数
(1)刀具切削部分结构要素
夹持部分已经标准化,一般称刀柄或刀体。 切削部分由刀面、刀刃和刀尖组成。 ① 前刀面:切屑流过的刀面。 后刀面:与工件上新形成的过渡表面相对的刀面。 副后刀面:与工件上已加工表面相对的刀面。 ②主切削刃:前刀面和后刀面交线,主要切削, 形成过渡表面。 副切削刃:前刀面和副后刀面交线,参与部分切削, 影响已加工表面粗糙度。 过渡刃:连接主、副切削刃之间的一小段切削刃, 可以是直线或圆弧。 ③刀尖:主、副切削刃连接处相当短的那部分切削刃, 常用交点、圆弧和倒棱刀尖。
切削加工概论
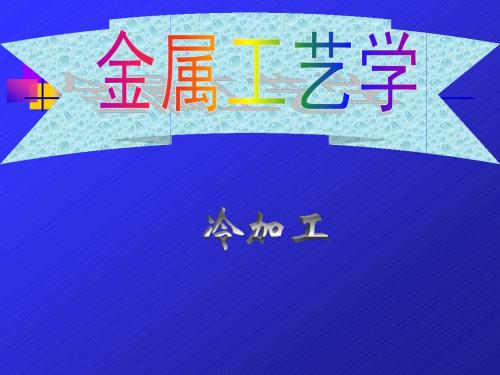
三、机床的切削运动
1、机床的切削运动
主运动:切除工件上的切削层,使之成为切屑,形成工件新表 面的运动。 进给运动:使切削层不断投入切削的运动。
a)车削 b)钻削 c) 铣削 d)刨削 e)磨削 f)滚齿 图1.2 切削运动简图
几种典型机床的切削运动见表1.1。 表1.1 几种典型机床的切削运动
(二)、切削加工的特点和作用
切削加工的精度和表面粗糙度范围广泛。 切削加工零件的材料、形状、尺寸和重量范围较大。 切削加工的生产率较高。 切削加工存在切削力,刀具和工件均需具有一定刚度 和强度,且刀具材料的硬度必须大于工件材料的硬度
(三)、切削加工的发展方向
随着科学技术和现代工业日新月异的飞速发展,切削 加工也正朝着高精度、高效率、自动化、柔性化和智能化 方向发展,体现在以下三方面:
切削用量三要素:切削速度、进给量、吃刀量(背吃刀量、侧吃刀 量、进给吃刀量) (1)切削速度 ①主运动为回转运动: c v
c(切削刃选定点相对于工件的主运动的瞬时速度)
(m s) v c dn (m min ) 1000 60 1000
dn
d-切削刃选定点处工件或刀具直径,mm。 n-工件或刀具的转速,r/min。
退火或正火 调质 淬火 磨削加工
毛坯
粗加工
半精加工 刀具精加工 时效
精密加工
超精密加工
二、零件的种类及组成
1、零件的种类 按结构可分类6类(1)轴类(2)盘套类(3)支架箱体类 (4)六面体类(5)机身机座类(6 )特殊类零件 2、组成零件的表面 组成零件常见的表面有外圆、内圆、锥面、平面、螺纹、 齿形、成形面及各种沟槽等。
圆柱面
圆锥面
回转体成形表面 平面
金属切削原理
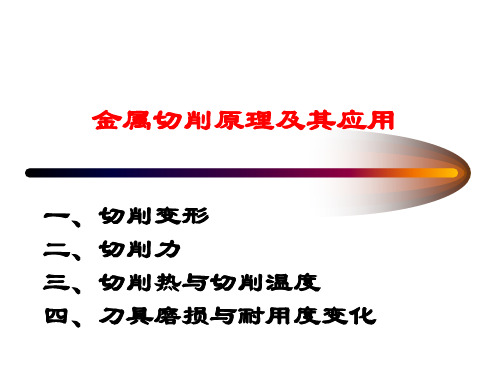
切削时消耗的功率
金属切削原理及其应用
一、切削变形 二、切削力 三、切削热与切削温度 四、刀具磨损与耐用度变化
1.1 金属切削过程的基本规律
一、切削变形 变形Ⅰ,Ⅱ,Ⅲ区, 剪切面间距0.02-0.2mm。
1. 切屑的形成
图为金属切削过程中的滑移线
1.1 金属切削过程的基本规律.
• (1)第一变形区 从OA线开始发生塑性变形,到 OM线金属晶粒的剪切滑移基本完成。OA线和OM 线之间的区域(图中Ⅰ区)称为第一变形区。
碳素钢,合金钢,铜 铝合金; 黄铜,低速切削钢; 铝; 铸鉄,黄铜
图为切屑类型
2. 积屑瘤
图为积屑瘤与切削刃的金 相显微照片
2. 积屑瘤
积屑瘤高度及其实际工作前角
2. 积屑瘤
(1)积屑瘤对切削过程的影响: 1) 积屑瘤包围着切削刃,可以代替前面、后面和切
削刃进行切削,从而保护了刀刃,减少了刀具的磨 损。 2) 积屑瘤使刀具的实际工作前角增大,而且,积屑 瘤越高,实际工作前角越大,刀具越锋利。 3) 积屑瘤前端伸出切削刃外,直接影响加工尺寸精 度。 4) 积屑瘤直接影响工件加工表面的形状精度和表面 粗糙度。
Fx Fxy sin r
3. 影响切削力的因素
3)刀具几何参数对切削力的影响。
c)刃倾角ls 对切削力的影响; ls↑ 背前角gp↑ 侧前角gf↓
Fp↓ Ff↑
3. 影响切削力的因素
3)刀具几何参数对切削力的影响。
d)刀尖圆弧半径r 对切削力的影响;
3. 影响切削力的因素
3)刀具几何参数对切削力的影响。 e)使用切削液 对切削力的影响;
v a 273
f 0.26 0.07
c
0.01
金属切削的基本原理
金属切削的基本原理金属切削的基本原理1. 引言金属切削作为一种重要的制造工艺,在现代工业中得到广泛应用。
了解金属切削的基本原理对于提高生产效率和产品质量至关重要。
本文将深入探讨金属切削的原理和相关概念。
2. 金属切削的定义和概述金属切削是指通过工具在金属材料上切削形成所需形状的制造过程。
这种切削通过将刀具与金属工件相对移动来去除材料,从而实现目标形状。
金属切削常用于车削、铣削、钻削等加工过程中。
3. 切削过程的基本元素金属切削包括以下基本元素:3.1 切削工具切削过程中使用的工具通常由坚固的材料制成,如高速钢、硬质合金等。
切削工具的类型和几何形状根据切削操作的需求而变化,比如刀片、铣刀、钻头等。
3.2 金属工件金属工件是经过切削加工的目标。
它可以是圆柱形、平面形或复杂形状的。
不同材料的切削特性也会影响切削过程的选择和参数设定。
3.3 切削速度切削速度是指工具切削过程中与工件接触部分的相对速度。
合适的切削速度可以提高加工效率和工件表面质量,但过高的切削速度可能导致工具磨损和加工表面粗糙度增加。
3.4 进给速度进给速度是指工具与工件相对运动的速度。
适当的进给速度可以控制切削过程中材料的去除率,同时避免过度磨损和切削力过大。
3.5 切削深度切削深度是指工具进入工件的深度,即每次切削过程中所移除的金属厚度。
切削深度的选择应根据工件的要求、切削力和工具稳定性等因素考虑。
4. 金属切削的力学原理金属切削的力学原理主要涉及三个力:切削力、切向力和主动力。
4.1 切削力切削力是指在金属切削过程中作用在切削工具上的力。
它由切削材料的去除、摩擦和变形引起。
切削力的大小和方向取决于切削工艺参数、切削材料和刀具等。
4.2 切向力切向力是指垂直于切削方向的力。
它使工件保持在切削位置,并防止工件偏离切削方向。
切向力的大小和方向直接影响切削的稳定性和表面质量。
4.3 主动力主动力是指在金属切削过程中将工具向工件施加的力。
它与切削深度和切削速度等直接相关。
金属切削原理及刀具
金属切削原理及刀具§1切削运动和切削用量刀具从毛坯上切除多余金属,从而获得在行状上、尺寸精度上和表面质量都合乎预定要求的加工,称为金属切削加工。
在切削加工过程中,刀具与工件相互接触且存在着相互运动,这种相互运动的过程称为金属切削过程。
在切削过程中,将产生各种物理现象及其变化,这些都是金属加工原理所要研究的内容。
一.切削运动1)主运动切削时直接切除工件上的金属层,使之转变为切屑的运动,称为主运动。
通常,主运动的速度最高,消耗的功率最大。
主运动可以由工件完成,也可以由刀具完成。
车削时工件的旋转运动是主运动。
一种切削加工方法其主运动只有一个。
2)进给运动不断地将多余金属投入切削,以保证切削连续进行的运动,称为进给运动。
进给运动的速度较低,消耗的功率较小。
车削的时候,车刀的纵向移动和横向移动都属于进给运动。
一种切削加工方法其进给运动不限于一个。
在切削过程中,被切金属层不断地被切削而转变为切屑,从而加工出所需要地工件表面。
在工件表面形成的过程中,工件上有三个不断变化着的表面。
(1)已加工表面切削后在工件上形成的新表面。
(2)待加工表面即将被切除的表面。
(3)加工表面切削刃正在切削着的表面。
二.切削用量切削用量是衡量切削运动和切削力大小的参数。
它包括三个要素:切削速度、进给量、切削深度。
切削用量的大小,反映单位时间内的金属切除量。
它是衡量生产率的重要参数之一。
1.切削速度即主运动的线速度,即m/s。
其中,为工件待加工表面直径,n为工件转速;由于刀刃上各点相对于工件的旋转半径不同,因而刀刃上各点的切削速度也不相同。
计算时,应以最大速度为准。
2.进给量当主运动旋转一周时,刀具(或工件)沿进给方向上的位移量。
车削时,工件旋转一周,刀具沿进给方向的位移量。
显然,进给量的大小反映着进给速度的大小关系为:3.切削深度工件上已加工表面与待加工表面之间的垂直距离。
车削时,车削深度是待加工表面直径与已加工表面直径差的一半,即,其中,为工件已加工表面直径。
机械制造技术基础知识点
机械制造技术基础知识点壹金属切削原理一、切削运动:使刀具和工件产生相对运动以进行切削的运动,通常速度最大。
二、切削中的工件表面:1、待加工面:加工时即将被切除的表面。
2、已加工面:已被切除多余金属的工件新表面。
3、过渡表面:刀具正在切除的工件表面。
三、切削用量(三要素):1、切削速度V c:V c=2、进给量f(进给速度V f):V f=fn3、背吃刀量(切削深度)a p:a p=四、刀具切削部分的结构三要素1、前刀面Aγ:切屑流出的表面。
2、主后刀面Aα:刀具上与工件过渡表面相对的表面。
3、副后刀面A’α:刀具上与已加工表面相对的表面。
4、主切削刃S:前刀面与主后刀面的交线,完成主要的切削工作。
5、副切削刃S’:前刀面与副后刀面的交线,配合主切削刃并完成已加工面五、刀具标注角1、参考系(1)基面p r通过切削刃某一指定点,并与该点切削速度相垂直的平面。
(2)切削平面p s通过主切削刃某一指定点,与主切削刃相切并垂直于基面。
(3)正交平面p o 通过主切削刃某一指定点,同时垂直于基面和切削平面。
2、标注角(1)前角γo正交平面内测量的前刀面与基面的夹角(2) 后角αo正交平面内测量的主后刀面与切削平面的夹角(3) 刃倾角λs切削平面内测量的主切削刃与基面的夹角(4) 主偏角κr基面内测量的主切削刃在基面上的投影与进给运动方向的夹角(5) 副偏角κ’r基面内测量的副切削刃在基面上的投影与进给运动反方向的夹角六、金属切削变形区及特点1、第一变形区: 从OA线开始发生塑性变形,到OM线剪切滑移结束2、第二变形区: 前刀面排出时受到挤压和摩擦,靠近前刀面处金属纤维化3、第三变形区: 已加工表面受挤压和摩擦,产生变形和回弹,造成表层金属纤维化与加工硬化七、积屑瘤1、现象:在切削速度不高又可以产生连续性切屑,加工钢等塑性材料。
(即低速切削塑性材料产生连续性切屑时)。
2、产生原因:切屑与前刀面发生强烈摩擦形成新鲜表面接触,在适当温度及较高压力下产生粘结(冷焊)。
02.切削原理概念与刀具
基本规律:是工具
1次课
• 切削变形
• 切削力
• 切削温度
• 刀具磨损 刀具角度、切削用量对切削过程的影响(重点)
规律的应用:是目的
1次课
• 合理选择刀具材料
• 合理选择刀具几何参数(重点)
• 合理选择切削用量(重点)
• 合理选择切削液
第3页
浙江大学现代制造工程研究所
基本概念
• 切削过程是工件和刀具相互作用的过程,为了能使刀 具从工件毛坯上切除多余金属,必须具备三个条件:
• 这三个表面是针对某一瞬时而言的,它们在不断地变 化
第6页
浙江大学现代制造工程研究所
概念三:切削用量
• 切削用量是切削速度、进给量和切削深度三者的总称, 称为切削用量三要素。
• 切削速度V:刀刃上某一点相对于工件的主运动速度。 主运动的方向即为切削速度的方向。单位:m/s,m/min。 刀刃上各点的速度可能不同,如V=π *d *n/1000
第28页
浙江大学现代制造工程研究所
内冷却式麻花钻
第29页
浙江大学现代制造工程研究所
内冷却式麻花钻结构
第30页
浙江大学现代制造工程研究所
各种刀具
第31页
浙江大学现代制造工程研究所
各种刀具
第32页
浙江大学现代制造工程研究所
自驱式中心钻
第33页
浙江大学现代制造工程研究所
专用刀具
第34页
浙江大学现代制造工程研究所
标注角度中的参考系以主运动,而工作角度是以主运动的合 成运动来确定参考系的,即需要考虑进给速度的大小
考虑刀具的安装位置
第23页
浙江大学现代制造工程研究所
刀具材料
- 1、下载文档前请自行甄别文档内容的完整性,平台不提供额外的编辑、内容补充、找答案等附加服务。
- 2、"仅部分预览"的文档,不可在线预览部分如存在完整性等问题,可反馈申请退款(可完整预览的文档不适用该条件!)。
- 3、如文档侵犯您的权益,请联系客服反馈,我们会尽快为您处理(人工客服工作时间:9:00-18:30)。
A、刀具切削部分的组成
1、前刀面 2、主后刀面 3、副后刀面 4、主切削刃 5、副切削刃 6、刀尖
目录
B、刀具的几何角度
1、前角—前刀面与Pr之 间的夹角
2、后角—主后刀面与 切削平面Ps之间的夹角
3、刃倾角——切削刃 与基面Pr间的夹角,在 切削平面Ps内度量
d
A、可转位外圆车刀的型号表示
ISO标准和我国标准规定了外圆车刀型号的 含义。现对十个号位具体内容作说明。 PWLNR2525M08
目录
目录
目录
目录
目录
ISO刀片编号:
B、刀片目编录 号
目录
C、 ISO铣ISO铣刀刀片片编号编: 号
D、可转位车目刀录 示意图
E、钻头基础知识
三、加工程式设计
1、准备知识
A、形状位置公差 基本概念 B、表面粗糙度 C、常用三角函数
2、程式结构 3、坐标系 4、决对值和增量值 5、辅助功能 6、刀具功能 7、G代码 8、综合练习 (车床以FANUC Series Oi-TB,加工中心以FANUC Series 16i-MB为例)
切削三要素之二
目录
进给量(铣削)
N: 转速(rpm) F:每分钟进给量(mm/min) fz:每齿进给量(mm/teeth) Z:齿数
切削三要素之三
切深(车削)
目录
Doc=(D-d)/2
Фd Doc:切深(mm) D:加工前直径(mm) d:加工后直径(mm)
切削三要素之三
切深d(铣削)
目录
C、丝锥的基本知识
丝锥公差带代 适用内螺纹公差带
号
等级
H1
4H、5H
H2
5G、6H
H3
6G、7H、7G
H4
6H、7H
目录
目录
DG、切削的类型及控制
带状切屑
挤裂切屑
单元切屑
崩碎切屑
G、切削的类型及控制 目录
1. 带状切屑 它的内表面光滑,外表面毛茸。加工塑性金 属材料,当切削厚度较小、切削速度较高、 刀具前角较大时,一般常得到这类切屑。它 的切削过程平衡,切削力波动较小,已加工 表面粗糙度较小。
High高
切削三要素之一
目录
切削速度(车削)
N: 转速(rpm) D:直径(mm) V:切削速度(m/min)
切削三要素之一
目录
切削速度(铣削)
N: 转速(rpm) D:直径(mm) V:切削速度(m/min)
切削三要素之二
进给量(车削)
目录
N: 转速(rpm) F:每分钟进给量(mm/min) f:每转进给量(mm/rev)
F、丝锥的基本知识 目录
丝锥各部的名称见图一
C、丝锥的基本知识 目录
直槽、挤压、螺尖、螺旋槽丝锥
F、丝锥的基本知识
目录
国产机用丝锥都标志中径公差带代号:H1、 H2、H3分别表示公差带不同的位置,但公 差值是相等的。手用丝锥的公差带代号为 H4,公差值、螺距及角度误差比机用丝锥 大,材质、热处理、生产工艺也不如机用 丝锥。H4按规定可以不标志。丝锥中径公 差带所能加工的内螺纹公差带等级如下:
4、主偏角——切削平 面Ps与进给剖面Pf的夹 角,在基面Pr内度量
目录
碳素工具钢与合金工具钢
切削米数为8-10M/MIN,主要用于 手动工具。价格低廉,耐热性差
目录
高速钢价格适宜,应用很广
目录
硬质合金
耐磨性好,耐热性高,抗冲击性差, 应用范围广
目录
PCD(金刚石)
切削米数200-1000M/MIN, 主要用于有色金属及非金属
目录
刀具材质硬度与刚性表
High
PCD 类金刚石
高
CBN 立方氮化硼
Ceramic 陶瓷
Cermet 金属陶瓷
Coated 涂层 Uncoated 不涂层
Hardness 硬度
HSS 高速钢
适于所有加工T方o案ughness 韧性
目录
目录
涂层刀具材料
涂层刀具是在刀具材料 的基础上涂上几微米厚 的高硬度、高耐磨性的 金属化合物而构成的。 韧性好、硬度高,性能 优异
陶瓷
目录
切削米数200-600M/MIN很高的硬度 及耐热性,抗黏结摩擦,抗扩散摩擦 的能力很强。主要缺点抗冲击性差
目录
CBN(六方氮化硼)
切削米数200-1000M/MIN,仅次于金刚 石,化学惰性差与铁族金属在1200°1300 °也不发生化学反应
二、刀具的基本知识
A、可转位外圆车刀的型号表示 B、刀片编号* C、ISO铣刀片编号* D、可转位车刀示意图* E、钻头基础知识 F、丝锥的基本知识 G、切削的类型及控制 H、拉削冷却液* I、工件材质* J、刀具磨损状况* K、刀具选择* L、练习*
2. 挤裂切屑 这类切屑与带状切屑不同之处在外表面呈锯 齿形,内表面有时有裂纹。这种切屑大多在 切削速度较低、切削厚度较大、刀具前角较 小时产生。
目录
G、切削的类型及控制
3. 单元切屑 如果在挤裂切屑的剪切面上,裂纹扩展到整个面上, 则整个单元被切离,成为梯形的单元切屑,如图c所示。 以上三种切屑只有在加工塑性材料时才可能得到。其 中,带状切屑的切削过程最平稳,单元切屑的切削力 波动最大。在生产中最常见的是带状切屑,有时得到 挤裂切屑,单元切屑则很少见。假如改变挤裂切屑的 条件,如进一步减小刀具前角,减低切削速度,或加 大切削厚度,就可以得到单元切屑。反之,则可以得 到带状切屑。这说明切屑的形态是可以随切削条件而 转化的。掌握了它的变化规律,就可以控制切屑的变 形、形态和尺寸,以达到卷屑和断屑的目的。
目录
一、金属切削原理
A、刀具切削部分的组成 B、刀具的几何角度 C、刀具材料
1、碳素工具钢与合金工具钢
2、高速钢 3、硬质合金 4、涂层刀具材料 5、陶瓷 6、CBN(六方氮化硼) 7、PCD(金刚石) 8、刀具材质硬度与刚性表
D、切削三要素
1、切削速度 2、进给量 3、切深
目录
横刃
刃背
40°-60°
副切削刃
前刀面 主切削刃
118°
棱边
后刀面
E、钻头基础知识
目录
可转位浅孔钻介绍
E、钻头基础知识
目录
特点
1.高速切削,切削速度在80m/min以上,生产效率比麻花钻高3~5倍。 2.加工质量好,表面粗糙度值为Ra3.2~6.3µm。 3.刀片可转位使用,节约辅助时间。 4.断屑好,切屑易排除。 5.不仅能钻孔,还可用做镗、锪孔用