钢材锻造工艺
精致钢工艺流程

精致钢工艺流程全文共四篇示例,供读者参考第一篇示例:精致钢工艺流程是一种高度精密的加工技术,主要应用于不锈钢、铝合金、铜等金属材料的加工过程中。
该工艺流程不仅可以提升产品的质量和精度,还可以实现一体化生产,提高生产效率。
下面将介绍一下精致钢工艺流程的具体步骤:一、材料准备与裁剪在精致钢工艺流程中,首先需要准备好所需的原材料,包括不锈钢、铝合金、铜等金属材料。
然后根据产品设计的要求,进行材料的裁剪工作,通常采用剪板机、激光切割机等设备进行裁剪,确保材料的尺寸和形状符合要求。
二、粗加工与成型在材料裁剪完成之后,接下来就是粗加工与成型的步骤。
在这一步中,通常会采用车床、铣床、钻床等设备进行加工,将金属材料进行成型,形成产品的基本轮廓和结构。
三、精密加工与修整在完成粗加工与成型后,进入到精密加工与修整的阶段。
在这一步中,需要使用磨床、电火花加工机等高精度设备,对产品进行精密加工和修整,确保产品的尺寸精度和表面光洁度达到设计要求。
四、打磨与抛光完成精密加工与修整之后,产品通常需要进行打磨与抛光的处理,以提高产品的表面光洁度和光泽度。
在这一步中,通常会采用抛光机、砂带机等设备进行处理,使产品表面光滑、亮丽。
五、清洗与除油为了确保产品表面的清洁度和无油污,通常在打磨与抛光完成后,需要对产品进行清洗与除油处理。
在清洗过程中,通常采用电解清洗、超声波清洗等设备,彻底清除表面的油污和污垢。
六、质量检测与包装最后一步是质量检测与包装。
在这一步中,通常会对产品进行质量检测,包括尺寸检测、表面质量检测等,确保产品符合设计要求。
然后将产品进行包装,以防止在运输和储存过程中出现损坏。
精致钢工艺流程是一种高度精密的加工技术,具有高效、精准、高质的特点。
通过对原材料的准备、裁剪、粗加工、精密加工、打磨抛光、清洗除油、质量检测包装等一系列工序的处理,可以生产出质量优良、精美细致的金属制品。
在未来的发展中,精致钢工艺流程将会继续不断完善和发展,以满足市场对高品质产品的需求。
第10章锻造(自由锻造工艺规程的编制及举例)

第十章锻压章节重点本章重点介绍了锻压的分类、特点、应用塑性变形对金属组织和性能的影响自由锻的主要工序及工艺要点锻压件的特点及应用。
学习目标1了解锻压的分类、特点、应用。
2理解塑性变形对金属组织和性能的影响常用金属的锻压性能。
3了解自由锻的主要工序及工艺要点识读锻件图、坯料的质量和尺寸、锻造工序、加热和冷却规范、锻造设备等会画简单锻件图。
4了解其他常用锻压方法的特点及应用、锻压技术发展趋势。
5初步具备合理选择典型零件的锻压方法、分析锻件结构工艺性具有锻件质量与成本分析的初步能力。
第一节锻压的基本知识一、锻压的概述【锻压】是指对坯料施加压力使其产生塑性变形改变尺寸、形状及改善性能用以制造机械零件、工件或毛坯的成形加工方法。
它是锻造和冲压的总称。
锻压包括轧制、挤压、拉拨、自由锻造、模型锻造、冲压等加工方法其典型工序实例如图所示。
常用的锻压加工方法锻压加工是以金属的塑性变形为基础的各种钢和大多数非铁金属及其合金都具有不同程度的塑性因此它们可在冷态或热态下进行锻压加工而脆性材料如灰铸铁、铸造铜合金、铸造铝合金等则不能进行锻压加工。
金属锻压加工的主要特点: 优点1 能改善金属内部组织提高金属的力学性能。
2 节省金属材料。
与直接切削钢材的成形相比还可以节省金属材料的消耗而且也节省加工工时。
3 生产效率较高。
如齿轮轧制、滚轮轧制等制造方法均比机械加工的生产率高出几倍甚至几十倍以上。
缺点: 1 不能获得形状很复杂的制件其制件的尺寸精度、形状精度和表面质量还不够高 2 加工设备比较昂贵制件的成本比铸件高。
二、金属的塑性变形金属在外力作用下将产生变形其变形过程包括弹性变形和塑性变形两个阶段。
【弹性变形】是指除去外力后物体完全恢复原状的变形。
【塑性变形】是指作用在物体上的外力取消后物体的变形不完全恢复而产生的永久变形。
塑性变形不仅能用于成形加工还会对金属的组织和性能产生很大影响。
一塑性变形的实质1 单晶体的塑性变形单晶体的变形方式有滑移和孪生两种。
锻造工艺学(完整版)课件

控制锻造工艺参数
如温度、压力、时间等,以获 得最佳的锻造效果。
制定检验标准
对锻造产品进行严格的质量检 验,确保产品符合标准。
持续改进
根据质量反馈,不断优化锻造 工艺和质量控制措施。
质量检测方法
目视检测
通过肉眼或低倍放大镜观察产品表面和内部 质量。
无损检测
利用X射线、超声波等无损检测技术对产品 内部进行检测。
有色金属
复合材料
如铜、铝、锌等,具有良好的导热性和塑 性,适用于制造要求轻量化和美观的零件 。
由两种或多种材料组成,具有优异的性能 ,如高强度、高刚性和轻量化,适用于航 空、航天等高科技领域。
锻造工具
锻锤
是最常用的锻造工具之 一,通过敲击使材料变 形,达到锻造的目的。
压力机
通过施加压力使材料变 形,适用于大型和重型
提高材料利用率和降低成本
通过合理的锻造工艺,可以减少材料浪费,降低生产成本。
锻造工艺的历史与发展
古代锻造工艺
现代锻造工艺
人类早期的锻造工艺主要采用简单的 锤击和砧打方式,用于制作工具和武 器。
随着科技的不断进步,锻造工艺在材 料、设备、工艺控制等方面取得了重 大突破,广泛应用于航空、航天、汽 车、能源等领域。
分类
锻造工艺学根据不同的分类标准可以 分为多种类型,如按变形温度可分为 热锻、温锻和冷锻;按变形程度可分 为自由锻、模锻和精密锻造等。
锻造工艺的重要性
提高金属材料的力学性能
通过塑性变形消除金属内部的缺陷,提高其力学性能,如强度、 韧性等。
实现复杂形状零件的成形
锻造工艺能够将金属材料加工成具有复杂形状和尺寸要求的零件, 满足各种工程应用需求。
金属材料成形与加工_锻压工艺之板料成形

肘杆式:
5 冲压设备
摩擦压力机
肘杆式压力机
5 冲压设备
➢按床身结构形式可分为:
开式压力机:床身为C型,工作台三面敞 开,便于前后、左右送料. 刚性较差,用于1000KN以下的 小型压力机.
闭式压力机:床身左右封闭,只有前后 两面敞开,刚度好,精度 高,1000KN以上的大、中 型压力机多采用.
二 冲压工艺力学基础
2.1 金属材料的塑性与变形抗力
1.塑性 塑性是指固体材料在外力作用下发生永久变形而不破坏其完整性 的能力. 常用的塑性指标:伸长率δ 和断面收缩率ψ . 材料的塑性是塑性加工的依据,冲压成形时总希望被冲压的材料 具有良好的塑性.
同一变形条件下不同的材料具有不同的塑性,同一种材料在不同 的变形条件下又会出现不同的塑性.
影响金属材料塑性变形的因素 金属材料本身的性质:化学成分、金相组织; 外部条件:如变形温度、变形速度和应力状态等.
2.1 金属材料的塑性与变形抗力
2.变形抗力
塑性变形时,使金属产生塑性变形的外力称为变形力,金 属抵抗变形的力称为变形抗力.变形抗力反映了使材料 产生塑性变形的难易程度. 在冲压生产中常用真实应力-应变曲线来表示材料变形抗 力与变形程度的关系:
rB lnB/B0 t lnt/t0
rB t (BB l)(ln B l/nB B0/ Bl0nl/l0)llnn B B B /0lB 00l
2.3拉伸试验
r 值的大小,表明板材在单向拉应力作用下,板平面方向 和板厚方向上变形难易程度的比较.
当 r>1 时,板材厚度方向上的变形比宽度方向上的变 形困难,起皱趋向性降低,利于拉深成形.r值与拉深系数密切 相关〔如图.
锻造工艺学重点知识点

1.大型钢锭的内部结构:1、细晶粒层2、柱状晶区3、倾斜树枝晶区4、粗大等轴晶区5、沉积锥6、冒口区2.钢锭是由冒口、锭身和底部组成。
两种钢锭规格一种普通锻件4%锥度、高径比1.8~2.3、冒口比例17%.....一种优质锻件 11%~12%的锥度、高径比1.5左右、冒口比例20%~24%3.大型钢锭内部缺陷:①偏析。
【可减少、不可消除】钢锭内部化学成分和杂质分布不均匀性称为偏析。
偏析是钢液凝固时选择结晶的产物,钢锭俞大偏析越严重。
分为树枝状偏析(显微偏析)和区域偏析(低倍偏析)树枝状偏析是指钢锭在晶体范围内化学成分的不均匀性。
A晶内偏析B晶间偏析通过锻造和锻后热处理消除。
区域偏析是指钢锭在宏观范围内的不均匀性A∨型偏析区B过度偏析区C∧型偏析区D负偏析区②夹杂。
钢锭内部不溶解于基体金属的非金属化合物,经过加热、冷却热处理仍不能消失,称为非金属夹杂物,统称夹杂。
通常存在的非金属夹杂有:硅酸盐(多脆)、硫化物(热脆+Mn)、氧化物(+Si)③气体。
在冶炼过程中氮、氢、氧等气体通过炉料和炉气熔入钢液。
钢液凝固时,这些气体虽然析出一部分,但在固态钢锭内仍有残余。
氧和氮在钢锭中以氧化物和氮化物出现,氢则以原子状态存在,也可能形成一部分分子状态氢和氢化物。
④、缩孔(大)和疏松(小)缩孔:冒口区形成,从钢液冷凝成钢锭时发生物理收缩现象,如果没有钢液补充,钢锭内部某些地方形成空洞。
疏松:由于晶间钢液最后凝固收缩造成的晶间空隙和钢液凝固过程析出气体构成的显微孔隙。
4.常用的下料的方法:剪切、冷析、锯割、车断、砂轮切割、刴断及特殊精密下料等。
5.锻前加热目的:提高金属塑性、降低变形抗力、使之易于流动成型并获得良好的锻后组织。
6.锻前加热方法:火焰加热、电加热。
火焰加热:利用燃料在火焰加热炉内燃烧产生含有大量热能的高温气体,通过对流、辐射把热能传给坯料表面,再由表面向中心热传导而使金属坯料加热。
对流传热(600~700℃):通过火焰在坯料周围不断流动,借助高温气体与坯料表面的热交换,把热能传递给金属坯料。
自由锻造工艺规程
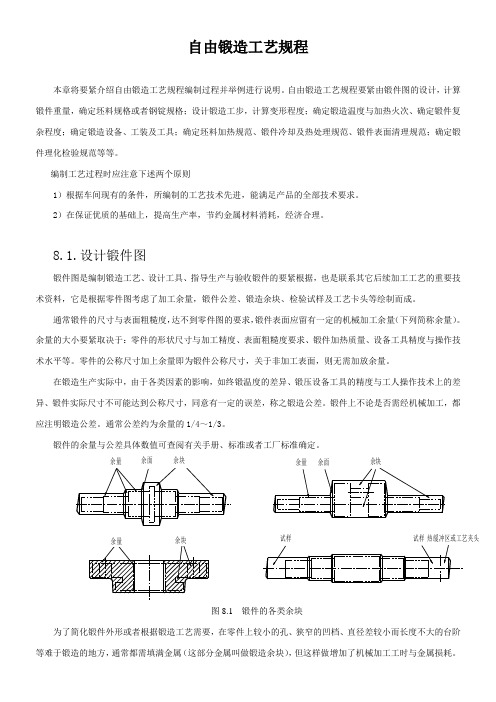
自由锻造工艺规程本章将要紧介绍自由锻造工艺规程编制过程并举例进行说明。
自由锻造工艺规程要紧由锻件图的设计,计算锻件重量,确定坯料规格或者钢锭规格;设计锻造工步,计算变形程度;确定锻造温度与加热火次、确定锻件复杂程度;确定锻造设备、工装及工具;确定坯料加热规范、锻件冷却及热处理规范、锻件表面清理规范;确定锻件理化检验规范等等。
编制工艺过程时应注意下述两个原则1)根据车间现有的条件,所编制的工艺技术先进,能满足产品的全部技术要求。
2)在保证优质的基础上,提高生产率,节约金属材料消耗,经济合理。
8.1.设计锻件图锻件图是编制锻造工艺、设计工具、指导生产与验收锻件的要紧根据,也是联系其它后续加工工艺的重要技术资料,它是根据零件图考虑了加工余量,锻件公差、锻造余块、检验试样及工艺卡头等绘制而成。
通常锻件的尺寸与表面粗糙度,达不到零件图的要求,锻件表面应留有一定的机械加工余量(下列简称余量)。
余量的大小要紧取决于:零件的形状尺寸与加工精度、表面粗糙度要求、锻件加热质量、设备工具精度与操作技术水平等。
零件的公称尺寸加上余量即为锻件公称尺寸,关于非加工表面,则无需加放余量。
在锻造生产实际中,由于各类因素的影响,如终锻温度的差异、锻压设备工具的精度与工人操作技术上的差异、锻件实际尺寸不可能达到公称尺寸,同意有一定的误差,称之锻造公差。
锻件上不论是否需经机械加工,都应注明锻造公差。
通常公差约为余量的1/4~1/3。
锻件的余量与公差具体数值可查阅有关手册、标准或者工厂标准确定。
图8.1 锻件的各类余块为了简化锻件外形或者根据锻造工艺需要,在零件上较小的孔、狭窄的凹档、直径差较小而长度不大的台阶等难于锻造的地方,通常都需填满金属(这部分金属叫做锻造余块),但这样做增加了机械加工工时与金属损耗。
因此,是否加放余块,应根据零件形状、锻造技术水平、加工成本等综合考虑确定。
除了锻造工艺要求加放余块之外,关于有特殊要求的锻件,尚需在锻件的适当位置添加试样余块(供检验锻件内部组织与力学性能试验用等)、热处理或者机械加工用夹头等。
锻造工艺与模具设计
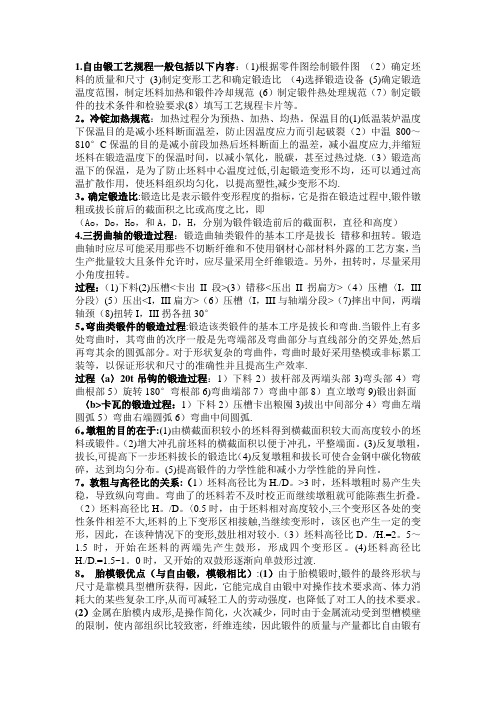
1.自由锻工艺规程一般包括以下内容:(1)根据零件图绘制锻件图(2)确定坯料的质量和尺寸(3)制定变形工艺和确定锻造比(4)选择锻造设备(5)确定锻造温度范围,制定坯料加热和锻件冷却规范(6)制定锻件热处理规范(7)制定锻件的技术条件和检验要求(8)填写工艺规程卡片等。
2。
冷锭加热规范:加热过程分为预热、加热、均热。
保温目的(1)低温装炉温度下保温目的是减小坯料断面温差,防止因温度应力而引起破裂(2)中温800~810°C保温的目的是减小前段加热后坯料断面上的温差,减小温度应力,并缩短坯料在锻造温度下的保温时间,以减小氧化,脱碳,甚至过热过烧.(3)锻造高温下的保温,是为了防止坯料中心温度过低,引起锻造变形不均,还可以通过高温扩散作用,使坯料组织均匀化,以提高塑性,减少变形不均.3。
确定锻造比:锻造比是表示锻件变形程度的指标,它是指在锻造过程中,锻件镦粗或拔长前后的截面积之比或高度之比,即(Ao,Do,Ho,和A,D,H,分别为锻件锻造前后的截面积,直径和高度)4.三拐曲轴的锻造过程:锻造曲轴类锻件的基本工序是拔长错移和扭转。
锻造曲轴时应尽可能采用那些不切断纤维和不使用钢材心部材料外露的工艺方案,当生产批量较大且条件允许时,应尽量采用全纤维锻造。
另外,扭转时,尽量采用小角度扭转。
过程:(1)下料(2)压槽<卡出II段>(3)错移<压出II拐扁方>(4)压槽〈I,III 分段〉(5)压出<I,III扁方>(6)压槽〈I,III与轴端分段>(7)摔出中间,两端轴颈(8)扭转I,III拐各扭30°5。
弯曲类锻件的锻造过程:锻造该类锻件的基本工序是拔长和弯曲.当锻件上有多处弯曲时,其弯曲的次序一般是先弯端部及弯曲部分与直线部分的交界处,然后再弯其余的圆弧部分。
对于形状复杂的弯曲件,弯曲时最好采用垫模或非标累工装等,以保证形状和尺寸的准确性并且提高生产效率.过程〈a〉20t吊钩的锻造过程:1)下料2)拔杆部及两端头部3)弯头部4)弯曲根部5)旋转180°弯根部6)弯曲端部7)弯曲中部8)直立墩弯9)锻出斜面〈b>卡瓦的锻造过程:1)下料2)压槽卡出粮囤3)拔出中间部分4)弯曲左端圆弧5)弯曲右端圆弧6)弯曲中间圆弧.6。
锻造和冷拔

钢材的锻造与冷拉、冷拔天津鹏程煤矿设备有限公司锻造:在生产中,采用合理的工艺和工艺参数,可以通过下列几方面来改善原材料的组织和性能:1)打碎柱状晶,改善宏观偏析,把铸态组织变为锻态组织,并在合适的温度和应力条件下,焊合内部孔隙,提高材料的致密度;2)铸锭经过锻造形成纤维组织,进一步通过轧制、挤压、模锻,使锻件得到合理的纤维方向分布;3)控制晶粒的大小和均匀度;4)改善第二相(例如:莱氏体钢中的合金碳化物)的分布;5)使组织得到形变强化或形变——相变强化等。
由于上述组织的改善,使锻件的塑性、冲击韧度、疲劳强度及持久性能等也随之得到了提高,然后通过零件的最后热处理就能得到零件所要求的硬度、强度和塑性等良好的综合性能。
锻造工艺能很好的减少材料浪费,从而降低成本。
宏观上讲锻造对材料基本无影响就像合面团一样合完还是面团。
微观上讲锻造加热可能会使碳元素进入材料,在受冷却温度速度的影响会使材料硬度增加。
事实也正是如此锻造的材料比原材料要稍硬。
但不影响材料整体性能。
冷拉:钢筋冷拉是在常温条件下,以超过原来钢筋屈服点强度的拉应力,强行拉伸钢筋,使钢筋产生一塑性变形达到提高钢筋屈服点强度和节约钢材的目的。
此处常温为平均室外温度大于5℃。
冷拔:钢筋同时经受张拉和挤压而发生塑性变形,拔出的钢筋截面积减小,产生冷作强化,抗拉强度可提高40~90%。
冷拉和冷拔是金属冷加工的两种不同的方法,两者并非一个概念。
冷拉指在金属材料的两端施加拉力,使材料产生拉伸变形的方法;冷拔是指在材料的一端施加拔力,使材料通过一个模具孔而拔出的方法,模具的孔径要较材料的直径小些。
冷拔加工使材料除了有拉伸变形外还有挤压变形,冷拔加工一般要在专门的冷拔机上进行。
经冷拔加工的材料要比经冷拉加工的材料性能更好些;冷拔钢筋是将钢筋用强力拔过比它本身直径还小的硬质合金拔丝模,这是钢筋同时受到纵向拉力和横向压力的作用,截面变小,长度变长,钢丝的强度大大提高,但塑性降低很多。
- 1、下载文档前请自行甄别文档内容的完整性,平台不提供额外的编辑、内容补充、找答案等附加服务。
- 2、"仅部分预览"的文档,不可在线预览部分如存在完整性等问题,可反馈申请退款(可完整预览的文档不适用该条件!)。
- 3、如文档侵犯您的权益,请联系客服反馈,我们会尽快为您处理(人工客服工作时间:9:00-18:30)。
钢材锻造是一种常见的金属加工工艺,通过对钢材进行加热和机械力的作用,改变其形状和性能。
下面是一般钢材锻造的工艺流程:
钢材选材:选择适合锻造的钢材,通常选择具有良好锻造性能和适当强度的材料。
加热:将选好的钢材加热至适当温度,使其达到良好的可塑性。
加热温度根据钢材的成分和要求来确定。
锻造准备:将加热好的钢坯放置在锻造设备上,并调整设备的工作参数,如锻造力、锻击次数等。
锻造操作:在加热好的钢坯上施加压力,通过锤击、挤压或压力机等方式,使钢材发生塑性变形,改变其形状。
锤击力和次数根据锻件形状和要求来确定。
退火处理:锻造后的钢件通常会存在一定的残余应力和组织不均匀性,通过热处理,将其加热至适当温度再缓慢冷却,以减少应力和改善组织性能。
后续处理:根据产品要求,可能需要进行后续加工工艺,如切割、修整、热处理、表面处理等。
以上是钢材锻造的一般工艺流程,具体的工艺操作和参数会根据锻件的形状、尺寸和要求而有所不同。
钢材锻造是一项复杂的技术工艺,需要经验丰富的操作人员和先进的设备来保证产品的质量和性能。