甲醇走壳程
制氢物料平衡计算

甲醇制氢物料平衡计算甲醇制氢的物料流程如图1-2。
流程包括以下步骤:甲醇与水按配比1:1.5进入原料液储罐,通过计算泵进入换热器(E0101)预热,然后在汽化塔(T0101)汽化,在经过换热器(E0102)过热到反应温度进入转化器(R0101),转化反应生成H2、CO2的以及未反应的甲醇和水蒸气等首先与原料液换热(E0101)冷却,然后经水冷器(E0103)冷凝分离水和甲醇,这部分水和甲醇可以进入原料液储罐,水冷分离后的气体进入吸收塔,经碳酸丙烯脂吸收分离CO2,吸收饱和的吸收液进入解析塔降压解析后循环使用,最后进入PSA装置进一步脱除分离残余的CO2、CO及其它杂质,得到一定纯度要求的氢气。
图1-2 甲醇制氢的物料流程图及各节点物料量1 物料衡算1、依据甲醇蒸气转化反应方程式:CH3OH→CO↑+2H2↑(1-1)CO+H2O→CO2↑+ H2↑(1-2)CH3OH分解为CO转化率99%,反应温度280℃,反应压力1.5MPa,醇水投料比1:1.5(mol).2、投料计算量代入转化率数据,式(1-3)和式(1-4)变为:CH 3OH →0.99CO ↑+1.98H 2↑+0.01 CH 3OHCO+0.99H 2O →0.99CO 2↑+ 1.99H 2+0.01CO合并式(1-5),式(1-6)得到:CH 3OH+0.981 H 2O →0.981 CO 2↑+0.961 H 2↑+0.01 CH 3OH+0.0099 CO ↑ 氢气产量为: 1200m 3/h=53.571 kmol/h甲醇投料量为: 53.571/2.9601ⅹ32=579.126 kg/h水投料量为: 579.126/32ⅹ1.5ⅹ18=488.638 kg/h3、原料液储槽(V0101)进: 甲醇 579.126 kg/h , 水 488.638 kg/h出: 甲醇 579.126 kg/h , 水 488.638 kg/h4、换热器 (E0101),汽化塔(T0101),过热器(E0103)没有物流变化.5、转化器 (R0101)进 : 甲醇 579.126kg/h , 水488.638 kg/h , 总计1067.764 kg/h出 : 生成 CO 2 579.126/32ⅹ0.9801ⅹ44 =780.452 kg/hH 2 579.126/32ⅹ2.9601ⅹ2 =107.142 kg/hCO 579.126/32ⅹ0.0099ⅹ28 =5.017 kg/h剩余甲醇 579.126/32ⅹ0.01ⅹ32 =5.791 kg/h剩余水 488.638-579.126/32ⅹ0.9801ⅹ18=169.362 kg/h总计 1067.764 kg/h6、吸收塔和解析塔吸收塔的总压为1.5MPa,其中CO 2的分压为0.38 MPa ,操作温度为常温(25℃). 此时,每m 3 吸收液可溶解CO 211.77 m 3.此数据可以在一般化工基础数据手册中找到,二氯 化碳在碳酸丙烯酯中的溶解度数据见表1一l 及表1—2。
甲醇生产工艺(2)

作业
1、写出CO与H2合成甲醇的主副反应方程式,对其进 行热力学分析,分析合成甲醇的最佳工艺条件。 2、低压法合成甲醇的原料气组成中,为何选择氢过量? 3、低压法合成甲醇的原料气组成中,惰性气体主要有 哪些?它们的存在对反应体系有哪些影响?生产中如 何减小惰性气体的影响? 4、简述MTO/OCP一体化工艺原理。
ATOFINA/UOP烯烃裂解工艺流程
来自MTO工段
反应釜工段
C2=、C3=
脱丙烷塔 脱丁烷塔
MTO/OCP一体化工艺
甲醇制烯烃
增加20%轻烯烃产 率; 降低约80%C4+副 产物;
C2=、C3=
丙烯/乙烯产品比例 可高达1.75; 优良的整合潜力。
烯烃裂解
H2
CO
CH4
抗氢蚀
抗一氧化碳腐蚀
F 耐腐蚀的特种不锈钢
第四节 甲醇下游产品的开发与应用
MTO/OCP一体化工艺
UOP/Hydro
MTO工艺
甲醇制烯烃工艺,由美国的UOP公司和挪威 的Hydro公司共同开发的工艺。 UOP/Total
MTO工艺主要副产物组成
MTO C4
1,3-丁二烯 丁烷 丁烯 线性烯烃 二烯烃
MTO C5
支化烯烃
环状化合物 烷烃
0.13-0.21/吨轻烯烃
0.06-0.07/吨轻烯烃
OCP工艺原理
OCP: 烯烃裂解工艺
乙烯
丙烯
吸热
UOP/Hydro MTO工艺流程
反应釜 再生器 急冷塔 洗涤器 碱洗塔 脱C2 脱C1 C2分离器 脱C3 C3分离器 脱C4
尾气 再生气
C1~C2
干燥器
甲醇合成的工艺流程
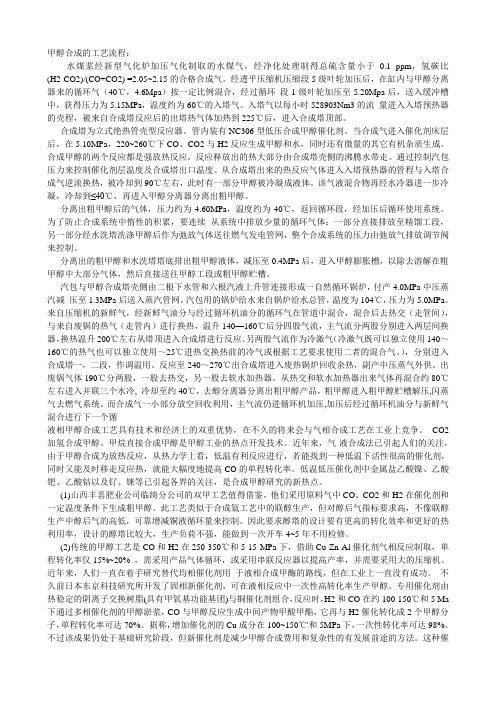
甲醇合成的工艺流程:水煤浆经新型气化炉加压气化制取的水煤气,经净化处理制得总硫含量小于0.1 ppm,氢碳比(H2-CO2)/(CO+CO2) =2.05~2.15的合格合成气。
经透平压缩机压缩段5级叶轮加压后,在缸内与甲醇分离器来的循环气(40℃,4.6Mpa)按一定比例混合,经过循环段1级叶轮加压至5.20Mpa后,送入缓冲槽中,获得压力为5.15MPa,温度约为60℃的入塔气。
入塔气以每小时528903Nm3的流量进入入塔预热器的壳程,被来自合成塔反应后的出塔热气体加热到225℃后,进入合成塔顶部。
合成塔为立式绝热管壳型反应器。
管内装有NC306型低压合成甲醇催化剂。
当合成气进入催化剂床层后,在5.10MPa,220~260℃下CO、CO2与H2反应生成甲醇和水,同时还有微量的其它有机杂质生成。
合成甲醇的两个反应都是强放热反应,反应释放出的热大部分由合成塔壳侧的沸腾水带走。
通过控制汽包压力来控制催化剂层温度及合成塔出口温度。
从合成塔出来的热反应气体进入入塔预热器的管程与入塔合成气逆流换热,被冷却到90℃左右,此时有一部分甲醇被冷凝成液体。
该气液混合物再经水冷器进一步冷凝,冷却到≤40℃,再进入甲醇分离器分离出粗甲醇。
分离出粗甲醇后的气体,压力约为4.60MPa,温度约为40℃,返回循环段,经加压后循环使用系统。
为了防止合成系统中惰性的积累,要连续从系统中排放少量的循环气体:一部分直接排放至精馏工段,另一部分经水洗塔洗涤甲醇后作为弛放气体送往燃气发电管网,整个合成系统的压力由弛放气排放调节阀来控制。
分离出的粗甲醇和水洗塔塔底排出粗甲醇液体,减压至0.4MPa后,进入甲醇膨胀槽,以除去溶解在粗甲醇中大部分气体,然后直接送往甲醇工段或粗甲醇贮槽。
汽包与甲醇合成塔壳侧由二根下水管和六根汽液上升管连接形成一自然循环锅炉,付产4.0MPa中压蒸汽减压至1.3MPa后送入蒸汽管网。
汽包用的锅炉给水来自锅炉给水总管,温度为104℃,压力为5.0MPa。
甲醇工艺路线

甲醇工艺流程本装置是以焦炉气为原料,低压合成甲醇的工业装置。
主工艺路线包括焦炉气气柜、焦炉气粗脱硫、焦炉气精脱硫、纯氧转化、压缩、甲醇合成、甲醇精馏、甲醇罐区等。
工艺流程简述如下:1、气柜、焦炉气压缩首先来自焦化系统压力~7kPa的焦炉气进入脱油脱萘器,除去焦炉气中含的焦油和萘等后送入气柜缓冲后,压力~0.7kPa、温度40℃,进入焦炉气压缩机,经四级压缩压力升至2.3MPa送至精脱硫系统。
2、精脱硫、转化经综合加热炉加热至250℃进入一级加氢预转化器(一开一备)、一级加氢转化器,气体中97%的有机硫在此转化成无机硫,不饱和烃加氢成为饱和烃。
进入中温氧化锌脱硫槽(两开一备),脱去绝大部分的无机硫。
再经二级加氢转化器将残余的有机硫进行转化,最后经过中温氧化锌脱硫槽(两台)把关,使气体中的总硫达到0.1ppm以下。
出氧化锌脱硫槽的气体压力约为 2.3Mpa,温度约为380℃送往转化。
与转化余热锅炉出来的部分饱和蒸汽混合,进入综合加热炉的蒸焦预热段和蒸焦加热段加热至~650℃,然后进入纯氧转化炉上部。
来自空分的氧气温度约为100℃,压力为2.5mpa与余热锅炉过热后420℃蒸汽混合,再进入蒸氧加热段加热~300℃,最后经纯氧转化炉上部中心管烧嘴进入纯氧转化炉内与蒸焦混合气发生燃烧反应,约1400℃的高温气体进入催化剂床层进行烃类的催化蒸汽转化反应,生成主要含CO、CO2、H2的转化气。
纯氧转化炉出来的转化气温度~980℃,经转化余热锅炉产生3.9MPa中压蒸汽回收主要热量,降温至~360℃进入中压锅炉给水加热器回收热量。
然后送至甲醇精馏工序作为甲醇精馏的热源,进一步回收热量后转化气温度降至~120℃,再由脱盐水加热器回收其低位热能,最后由空冷器冷却到40℃以下,经气液分离器进一步分离冷凝液后经常温氧化锌脱硫槽脱除气体中残余的硫,为甲醇合成作最后把关。
出脱硫槽的转化气温度40℃,压力约 2.0Mpa的转化气送往合成气压缩工段。
甲醇合成的工艺流程
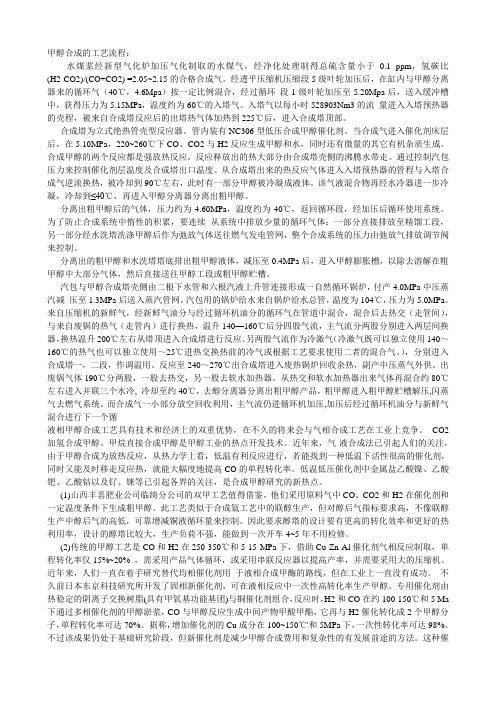
甲醇合成的工艺流程:水煤浆经新型气化炉加压气化制取的水煤气,经净化处理制得总硫含量小于0.1 ppm,氢碳比(H2-CO2)/(CO+CO2) =2.05~2.15的合格合成气。
经透平压缩机压缩段5级叶轮加压后,在缸内与甲醇分离器来的循环气(40℃,4.6Mpa)按一定比例混合,经过循环段1级叶轮加压至5.20Mpa后,送入缓冲槽中,获得压力为5.15MPa,温度约为60℃的入塔气。
入塔气以每小时528903Nm3的流量进入入塔预热器的壳程,被来自合成塔反应后的出塔热气体加热到225℃后,进入合成塔顶部。
合成塔为立式绝热管壳型反应器。
管内装有NC306型低压合成甲醇催化剂。
当合成气进入催化剂床层后,在5.10MPa,220~260℃下CO、CO2与H2反应生成甲醇和水,同时还有微量的其它有机杂质生成。
合成甲醇的两个反应都是强放热反应,反应释放出的热大部分由合成塔壳侧的沸腾水带走。
通过控制汽包压力来控制催化剂层温度及合成塔出口温度。
从合成塔出来的热反应气体进入入塔预热器的管程与入塔合成气逆流换热,被冷却到90℃左右,此时有一部分甲醇被冷凝成液体。
该气液混合物再经水冷器进一步冷凝,冷却到≤40℃,再进入甲醇分离器分离出粗甲醇。
分离出粗甲醇后的气体,压力约为4.60MPa,温度约为40℃,返回循环段,经加压后循环使用系统。
为了防止合成系统中惰性的积累,要连续从系统中排放少量的循环气体:一部分直接排放至精馏工段,另一部分经水洗塔洗涤甲醇后作为弛放气体送往燃气发电管网,整个合成系统的压力由弛放气排放调节阀来控制。
分离出的粗甲醇和水洗塔塔底排出粗甲醇液体,减压至0.4MPa后,进入甲醇膨胀槽,以除去溶解在粗甲醇中大部分气体,然后直接送往甲醇工段或粗甲醇贮槽。
汽包与甲醇合成塔壳侧由二根下水管和六根汽液上升管连接形成一自然循环锅炉,付产4.0MPa中压蒸汽减压至1.3MPa后送入蒸汽管网。
汽包用的锅炉给水来自锅炉给水总管,温度为104℃,压力为5.0MPa。
甲醇回收操作规程
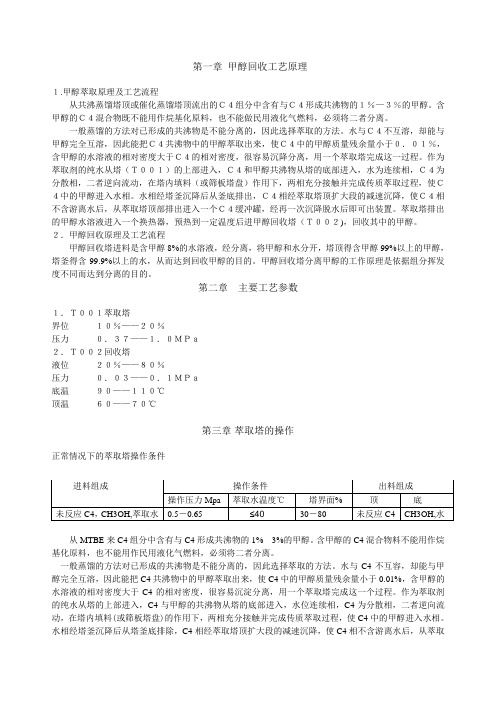
第一章甲醇回收工艺原理1.甲醇萃取原理及工艺流程从共沸蒸馏塔顶或催化蒸馏塔顶流出的C4组分中含有与C4形成共沸物的1%—3%的甲醇。
含甲醇的C4混合物既不能用作烷基化原料,也不能做民用液化气燃料,必须将二者分离。
一般蒸馏的方法对已形成的共沸物是不能分离的,因此选择萃取的方法。
水与C4不互溶,却能与甲醇完全互溶,因此能把C4共沸物中的甲醇萃取出来,使C4中的甲醇质量残余量小于0.01%,含甲醇的水溶液的相对密度大于C4的相对密度,很容易沉降分离,用一个萃取塔完成这一过程。
作为萃取剂的纯水从塔(T001)的上部进入,C4和甲醇共沸物从塔的底部进入,水为连续相,C4为分散相,二者逆向流动,在塔内填料(或筛板塔盘)作用下,两相充分接触并完成传质萃取过程,使C4中的甲醇进入水相。
水相经塔釜沉降后从釜底排出,C4相经萃取塔顶扩大段的减速沉降,使C4相不含游离水后,从萃取塔顶部排出进入一个C4缓冲罐,经再一次沉降脱水后即可出装置。
萃取塔排出的甲醇水溶液进入一个换热器,预热到一定温度后进甲醇回收塔(T002),回收其中的甲醇。
2.甲醇回收原理及工艺流程甲醇回收塔进料是含甲醇8%的水溶液,经分离,将甲醇和水分开,塔顶得含甲醇99%以上的甲醇,塔釜得含99.9%以上的水,从而达到回收甲醇的目的。
甲醇回收塔分离甲醇的工作原理是依据组分挥发度不同而达到分离的目的。
第二章主要工艺参数1.T001萃取塔界位10%——20%压力0.37——1.0MPa2.T002回收塔液位20%——80%压力0.03——0.1MPa底温90——110℃顶温60——70℃第三章萃取塔的操作正常情况下的萃取塔操作条件从MTBE来C4组分中含有与C4形成共沸物的1%---3%的甲醇。
含甲醇的C4混合物料不能用作烷基化原料,也不能用作民用液化气燃料,必须将二者分离。
一般蒸馏的方法对已形成的共沸物是不能分离的,因此选择萃取的方法。
水与C4不互容,却能与甲醇完全互溶,因此能把C4共沸物中的甲醇萃取出来,使C4中的甲醇质量残余量小于0.01%,含甲醇的水溶液的相对密度大于C4的相对密度,很容易沉淀分离,用一个萃取塔完成这一个过程。
甲醇生产工艺流程概况

工艺流程简述1、转化工艺流程概述界区外来的天然气,分成两路,一路原料气通过原料气分离器V-0101分离出其中水、石脑油等冷凝物后,送至燃料气脱硫槽R-0101A/B/C/D脱硫后作为转化炉和开工锅炉的燃料天然气。
另一路原料气通过原料气分离器BS-101分离出其中水、石脑油等冷凝物后,补入一定量从氢回收装置送来的氢气后进入原料气预热器加热,依次通过常温脱硫槽(BR-0101A/B)、高温钴钼加氢脱硫槽(BR-102)、高温氧化锌脱硫槽(R-101 A/B)脱硫,使原料天然气中的总硫含量降到0.1ppm 以下,脱硫后的天然气作为甲醇生产装置的工艺天然气送至原料混合器MIXER中。
在原料混合器MIXER中工艺天然气、1. 9Mpa的工艺蒸汽、CO2,按H2O/C (2.95—3.05):1的比例混合后,通过混合气预热器E-104,加热到500℃,在1.6Mpa的压力下进入一段转化炉。
一段转化炉用天然气、合成驰放气、合成闪蒸气作为燃料为反应提供热量。
混合原料气在850℃温度下通过转化管中触媒层,从一段转化炉出来的转化气,温度760℃,压力1.2MPa 残留甲烷≤10%。
由一段转化炉下部集气总管输至二段转化炉顶混合烧咀,用于优化调节的部分工艺天然气和回收的氢气在集气总管上加入,来自博源联化公司的氧气1.5Mpa、120℃与部分工艺蒸汽混合后从混合烧咀顶部加入;在混合烧咀出口处的转化气与氧气混合在高温下自燃,进行部分燃烧反应放出热量,使入二段转化炉的混合气体温度升至1100℃再次进入二段转化催化剂床层,对残余甲烷进行转化,出二段转化炉的高温转化气1.15Mpa、950℃进入废热锅炉产生高压蒸汽,回收部分热量,并经其它换热器利用余热后,转化气一分为二,一部分进入原甲醇装置天然气预热器出口总管,并经原甲醇装置回收利用余热,最终冷却至40℃分离后入原甲醇装置合成气压缩机压缩入合成。
另一部分通过调节阀控制进入新增的转化B系列后工序,最终冷却至40℃分离后入新增合成气压缩机压缩入合成。
甲醇合成操作规程
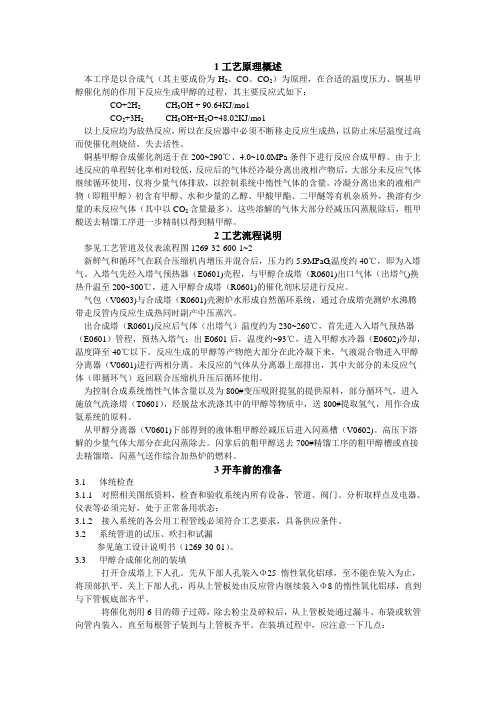
1工艺原理概述本工序是以合成气(其主要成份为H2、CO、CO2)为原理,在合适的温度压力、铜基甲醇催化剂的作用下反应生成甲醇的过程,其主要反应式如下:CO+2H2 CH3OH + 90.64KJ/mo1CO2+3H2CH3OH+H2O+48.02KJ/mo1以上反应均为放热反应,所以在反应器中必须不断移走反应生成热,以防止床层温度过高而使催化剂烧结,失去活性。
铜基甲醇合成催化剂适于在200~290℃、4.0~10.0MPa条件下进行反应合成甲醇。
由于上述反应的单程转化率相对较低,反应后的气体经冷凝分离出液相产物后,大部分未反应气体继续循环使用,仅将少量气体排放,以控制系统中惰性气体的含量。
冷凝分离出来的液相产物(即粗甲醇)初含有甲醇、水和少量的乙醇、甲酸甲酯、二甲醚等有机杂质外,换溶有少量的未反应气体(其中以CO2含量最多)。
这些溶解的气体大部分经减压闪蒸脱除后,粗甲酸送去精馏工序进一步精制以得到精甲醇。
2工艺流程说明参见工艺管道及仪表流程图1269-32-600-1~2新鲜气和循环气在联合压缩机内增压并混合后,压力约5.9MPaG,温度约40℃,即为入塔气。
入塔气先经入塔气预热器(E0601)壳程,与甲醇合成塔(R0601)出口气体(出塔气)换热升温至200~300℃,进入甲醇合成塔(R0601)的催化剂床层进行反应。
气包(V0603)与合成塔(R0601)壳测炉水形成自然循环系统,通过合成塔壳测炉水沸腾带走反管内反应生成热同时副产中压蒸汽。
出合成塔(R0601)反应后气体(出塔气)温度约为230~260℃,首先进入入塔气预热器(E0601)管程,预热入塔气;出E0601后,温度约~93℃,进入甲醇水冷器(E0602)冷却,温度降至40℃以下。
反应生成的甲醇等产物绝大部分在此冷凝下来,气液混合物进入甲醇分离器(V0601)进行两相分离。
未反应的气体从分离器上部排出,其中大部分的未反应气体(即循环气)返回联合压缩机升压后循环使用。
- 1、下载文档前请自行甄别文档内容的完整性,平台不提供额外的编辑、内容补充、找答案等附加服务。
- 2、"仅部分预览"的文档,不可在线预览部分如存在完整性等问题,可反馈申请退款(可完整预览的文档不适用该条件!)。
- 3、如文档侵犯您的权益,请联系客服反馈,我们会尽快为您处理(人工客服工作时间:9:00-18:30)。
(一)确定物性数据热流体进口温度:337.85K,出口温度:337.85K 冷流体进口温度:300.15K,出口温度:317.15K定性温度:可取流体进口温度的平均值。
壳程甲醇蒸气的定性温度为T =337.85K ,2T =337.85K ,1T = 337.85K 管程冷却水的定性温度为1t =300.15K ,2t =317.15 , t=(300.15+317.15)/2=308.15K根据定性温度,分别查取壳程和管程流体的有关物性数据 甲醇蒸气在337.15K 下的物性数据: 密度 ρ1=1.193/Kg m定压比热容 p1c=1.620/()KJ Kg K •热导率 λ1=0.013/()W m K •粘度μ1=0.011mPa s •汽化潜热 γ =1100/KJ Kg 冷却水在308.15K 下的有关物性数据: 密度 ρ0=994.063/Kg m定压比热容 p0c=4.165/()KJ Kg K •热导率 λ=0.623/()W m K • 粘度μ=0.7245mPa s •(二)估算总传热系数1.热流量甲醇质量流量:s1W =1.2×3600×1.19=5140.8/h Kg =1.428/s Kg 甲醇热负荷:1Q =5140.8×1100=5.655×610/KJ h =1570.8KW2.平均传热温差t Δm=tt t 2121ln -ΔΔΔΔt =5.1317-5.83375.1300-85.337ln 5.1317-5.8337-5.1300-85.337)()(K 628.3 ≈其中t 1Δ=t 11-T ,t Δ2=t 22-T ,T 1=T 2=337.85K 3. 冷却水用量 s0W =)(t Q Δ0c =5.655×610/[4.165×(317.15-300.15)]=79867.2/h Kg =22.2/s Kg 4.传热面积初值估算:取总传热系数K =7002/()W m K •估算传热面积:A估=)(tK Q Δm=1570.8×310/(700×28.36)=79.1262m (三)工艺结构尺寸1.管径和管内流速 选用Φ19mm ×2mm 的碳钢管,取管内流速ui=0.5m/s ,其内径m i015.0d=,外径m d o 019.0=2.计算管程数和传热管数 根据传热管内径和流速确定单程传热管数u d n iV 2i e 4π==.5085.706.099422.215.002××=252.88≈253(根)按单管程计算,所需传热管长度为L =n d eo π26.179=25319.004.1379.126××=5.24m根据传统换热器管长可取6米单程换热器,则传热管总根数NT=253(根)3.平均传热温差校正及壳程数 平均传热温差校正系数R=5.1300-5.13175.8337-5.8337=0P=5.1300-5.83375.1300-5.1317=0.45按单壳程温差校正系数应查有关图表。
可得ΦtΔ=1平均传热温差'mt Δ=t Δ•m t ΔΦ=1×28.36=28.36℃4.传热管排列和分程方法采用组合排列法,即每程内均按正三角形排列。
取管心距t=1.25 d,则t=1.25×19=23.75≈25(mm)对于单管程换热器,横过管束中心线的管数81≈50.172531.1==n c 根 管束的分程方法:采用单管程共有传热管253根, 5.壳体内径本设计采用单管程结构正三角形排列,壳体内径可用下式计算: D=t (1-n c )+b 2‘,管束中心线上最外层管的中心至壳体内径的距离.5mm 2819.51.51'=×==d b o则壳体内径为:D=19.511-1825×+)(=453.5mm圆整后取壳体直径为D=500mm6.折流板采用弓形折流板,取弓形折流板圆缺高度为壳体内径的25%,则切去的圆缺高度为 'h =0.25×500=125mm 两相邻折流挡板的距离(板间距)为:h=D .80=0.8×500=400mm ,故可取h=400mm. 允许的折流板最小间距为h m in =0.2D=0.2×500=100mm, 折流板数目:1-折流板间距传热管长=N B =4006000-1=14(块)折流板圆缺面水平装配。
(四)核算总传热系数K1.污垢热阻和管壁热阻 管程冷却水的污垢热阻R di =0.00034W K m •2壳程纯净甲醇气体的污垢热阻 Rdo=0管壁热阻 R w =λwb,其中b 为传热管壁厚,m ;λw 为管壁热导率,/()W m K •碳钢在308.15K 下的热导率为51.10/()W m K •,所以R w =.15102.00=0.000039W K m •22.管程给热系数 管内流通面积A i =n ei d 24π=4π×015.02×253=0.04472m 管内流速AW u is i ρ00= =0447.006.9942.22×=0.4996m/s管内雷诺系数 Re i =μρ0u d i i=103-7245.006.9944996.0015.0×××=10282.24(湍流)管内普朗特数 Pr i=λμ0c p =326.07245.04165103-××=4.844对流传热系数44.844.210282Pr Re λα.408.04.08.00015.0623.0023.023.00×××=••=i i ii d =29102/()W K m •3.壳程给热系数壳程对流传热系数)Δμγλρ(α3232725.041td n g o o=式中,γ为比汽化热,g K J ρ为冷凝液的密度,3/Kg mλ为冷凝液的热导率,/()W m K • μ为冷凝液的黏度,mPa s •t Δ为饱和温度T s 与外壁温度T w 之差,n 为水平管束在垂直列上的管排数,该换热器为单管程单壳程共253跟管子,管子按照三角形排列,则有 n ≈20定性温度取膜温,即2T T T ws+=定现假设管外壁温K T w 330=,则 K t T T w s 15.7330-15.337-===ΔK T T Tws755.33323305.13372=+=+=定,在该定性温度下:m 3kg.6760ρ=,s Pa •=m 342.0μ,)m 8.197λK m W•=)(15.719.001042.3020101100978.101.89.6760)Δμγλρ(α3-3233225.703232725.04141×××××××××==td n g o o=24992/()W K m • 4.壁温核算热流体在管内流动,Ts=337.15K ,则单根水平管的传热量W QQ0.76208253W.815702531031=×==单,根据壁温公式有AR t At T AR T Qidi imodo ot b T 1)1(--1)1(-αλαw ww w w+==+=单式中,T w 为管外壁温,t w 为管内壁温,R di 为管程冷却水污垢热阻,R do 为壳程纯净甲醇气体的污垢热阻,b 为管厚度,A i 为单根换热管的内表面积,A o 为单根换热管外表面积,A m 为单根换热管平均表面积,λw 为碳钢热导率。
619.004.13124991-15.337×××=T Qw单,求得 T w =330.21K ,这与假设相差不大,可以接受。
4.计算总传热系数KK=dd d d R dd R ioiio di modo ob •+•+++αλα111w式中d i为管子内径,do为管子外径,d m 为管子平均直径,αi 为管程传热系数,αo 为壳程传热系数。
R di 为管程污垢热阻,R do 壳程污垢热阻,λW 为碳钢热导率将已知数据代入上式,得 K=015.0019.029101015.0019.00034.0017.0019.000.15102.000249911×+×+×++=763.452/()W m K •5.计算传热面积裕度传热面积49.5726.32845.763.8157010Δ31=××==tQ A mcK 2m实际传热面积A p =N d To l π=3.14×0.019×6×253=90.5642m该换热器的面积裕度为.83%24549.7249.572-64.590-===AA A ccpH传热面积裕度合适,该换热器能够完成生产任务。
(五)核算压力降1.管程压降P i ΣΔNN F P P P psti)(ΔΔΣΔ21+=式中,F t 为结垢校正系数;N s 壳程数;N p 为管程数;P Δ1为直管阻力压强降,Pa ;P Δ2为回弯管压强降,Pa ;取碳钢的管壁粗糙度为0.1mm,则00667.0151.0==die,而24.10282Re =i ,于是037.01.01.0)24.102826800667.0()Re 68(λ23.023.0===++ii d e i 26.099415.00637.002Δ996.40ρλ2201×××==udiiilP =1836.07Pa 206.9943234996.02202××=×=Δu Piρ=372.18Pa 对三角形排列F t =1.4,且N s =1,N p =1,则11.418.13727.01836)(ΔΔΣΔ21×××+=+=)(NN F P P P psti=3091.55Pa2.壳程压降()s t o N F P P P 'Δ'ΔΣΔ21+= 其中1=s N ,1=t F 流体流经管束的阻力()2ρ1Δ2'1oBc o u N n Ff P +==×=253228.0-5fo已知: 14=B N ,5.0=F ,根18=n c()2ρ1Δ2'1oBc o u N n Ff P +=2ρ25.3Δ2'2oB u D B N P =。