单壳程双管程管壳式换热器设计
孙兰义教授新作《换热器工艺设计》第3章 管壳式换热器ppt

特性
适用范围
ϕ25×2.5
325~1Байду номын сангаас00
2,4
3,6
ϕ19×2 ϕ25×2.5
△
浮头 式
GB/T 28712.1 —2012
325~1900
2,4, 3, 4.5, 6, ϕ19×2 6 9
◇
ϕ25×2.5
3.1 管壳式换热器的特点
管壳式换热器的主要组合部件
TEMA标准中规定的管壳式换热器的主要组合
图3-3 GB/T 151-1999 管壳式 换热器中的主要部件和部件代号图
⑤ F型壳体用于需要多壳体的工况,它可起到两台或多 台串联换热器的作用,并允许换热器温度交叉的出现。
3.1 管壳式换热器的特点
前端管箱和后端管箱
前端管箱有封头管箱和平盖管箱两种基本型式。封头管箱(B)最常用,一 般是在管侧流体较清洁的情况下使用。平盖管箱可以是可拆式(A)也可以与 管板做成一个整体(C)。对于水冷却器,当管侧需要定期清洗且管侧设计压 力小于1 MPa时,前封头可选A型,对于高压换热器前封头宜选择D型。各管箱 详细介绍见书p6~p7。 可参考的一般选型指导:
(a)竖缺形折流板
(b)横缺形折流板
图3-11 折流板缺口方向
3.2 管壳式换热器结构参数选择
折流板换热器间隙 折流板管孔与管壁之间的间隙 根据TEMA标准,对于未受支承的管子的最大长度为36 in(914.4 mm)
或更小,或者对于外径大于1.25 in(31.8 mm)的管子,该孔隙为1/32 in (0.80 mm);对于未受支承的长度超过36 in,外径为1.25 in或更小的 管子,该孔隙为1/62 in(0.40 mm)。
管壳式换热器换热面积-换热器设计手册
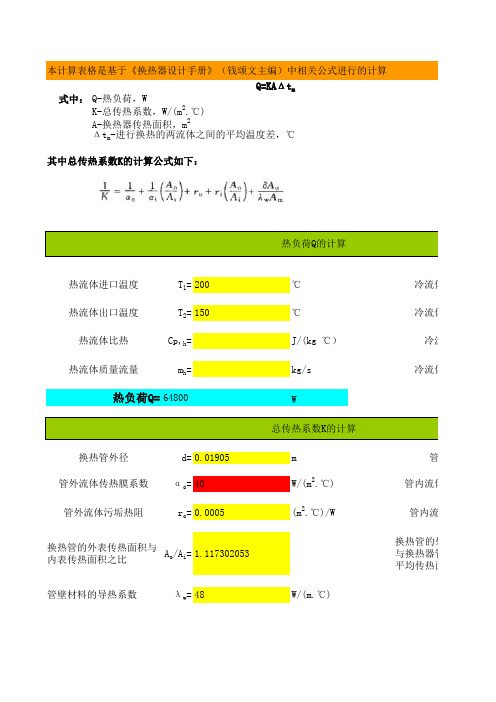
式中:T 1=200℃T 2=150℃Cp,h =J/(kg ℃)m h =kg/sWd=0.01905m αo =40W/(m 2.℃)r o =0.0005(m 2.℃)/W A o /A i =1.117302053λw =48W/(m .℃)本计算表格是基于《换热器设计手册》(钱颂文主编)中相关公式进行的计算Q=KA Δt mQ-热负荷,WK-总传热系数,W/(m 2.℃)A-换热器传热面积,m 2Δt m -进行换热的两流体之间的平均温度差,℃其中总传热系数K的计算公式如下:热负荷Q的计算热流体进口温度冷流体进热流体出口温度冷流体出热流体比热冷流体热流体质量流量冷流体质热负荷Q=64800总传热系数K的计算换热管外径管壁管外流体传热膜系数管内流体传管外流体污垢热阻管内流体换热管的外表传热面积与内表传热面积之比换热管的外表与换热器管内和管外的平均传热面积之比管壁材料的导热系数7.885W/(m 2.℃)Δt 2=150℃Δt 1=125℃0.833Δt 2=175℃Δt 1=100℃0.571Δt m =137.5Δt m =137.5Δt m =137.1203737Δt m =134.020522总传热系数K=1、当换热器冷热流体逆向流动时较大端温差较小端温差Δt 1/Δt 2=2、当换热器冷热流体并向流动时较大端温差较小端温差Δt 1/Δt 2=3、确定平均温度差(1)当Δt 1/Δt 2 <2 时且逆向流动时(2)当Δt 1/Δt 2 <2 时且并向流动时(3)当Δt 1/Δt 2 >2 时且逆向流动时(4)当Δt 1/Δt 2 >2 时且并向流动时4、确定温度修正系数(1)对于单壳程、双管程或者2n管程的管壳式换热器P=0.171428571R=1.6666666670.9861.15m 2换热面积A=5、根据P、R值查图,确定对应温度修正系数温度修正系数 F T =t 1=25℃t 2=55℃Cp,c =1200J/(kg ℃)m c =1.8kg/s δ=0.002m αi =45W/(m 2.℃)r i =0.0005(m 2.℃)/W A o /A m =1.055402流体进口温度流体出口温度冷流体比热流体质量流量管壁厚度流体传热膜系数内流体污垢热阻的外表传热面积与换热器管内和管外的平均传热面积之比算。
管壳式换热器工艺设计说明书
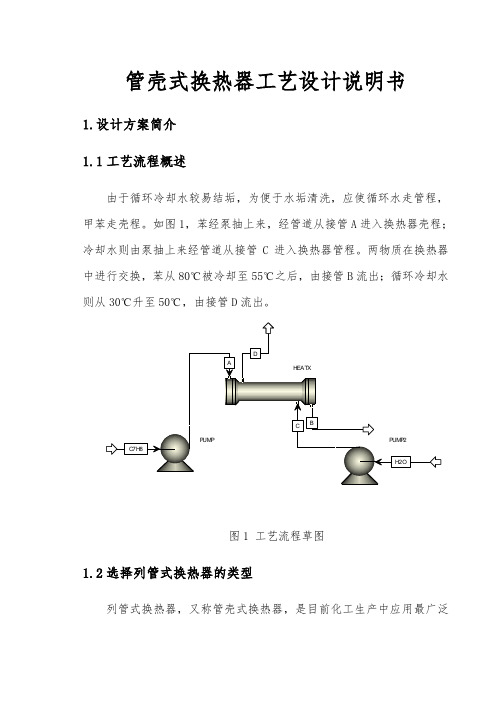
管壳式换热器工艺设计说明书1.设计方案简介1.1工艺流程概述由于循环冷却水较易结垢,为便于水垢清洗,应使循环水走管程,甲苯走壳程。
如图1,苯经泵抽上来,经管道从接管A进入换热器壳程;冷却水则由泵抽上来经管道从接管C进入换热器管程。
两物质在换热器中进行交换,苯从80℃被冷却至55℃之后,由接管B流出;循环冷却水则从30℃升至50℃,由接管D流出。
图1 工艺流程草图1.2选择列管式换热器的类型列管式换热器,又称管壳式换热器,是目前化工生产中应用最广泛的传热设备。
其主要优点是:单位体积所具有的传热面积大以及窜热效果较好;此外,结构简单,制造的材料范围广,操作弹性也较大等。
因此在高温、高压和大型装置上多采用列壳式换热器。
如下图所示。
1.2.1列管式换热器的分类根据列管式换热器结构特点的不同,主要分为以下几种:⑴固定管板式换热器固定管板式换热器,结构比较简单,造价较低。
两管板由管子互相支承,因而在各种列管式换热器中,其管板最薄。
其缺点是管外清洗困难,管壳间有温差应力存在,当两种介质温差较大时,必须设置膨胀节。
固定管板式换热器适用于壳程介质清洁,不易结垢,管程需清洗及温差不大或温差虽大但壳程压力不高的场合。
固定板式换热器⑵浮头式换热器浮头式换热器,一端管板式固定的,另一端管板可在壳体内移动,因而管、壳间不产生温差应力。
管束可以抽出,便于清洗。
但这类换热器结构较复杂,金属耗量较大;浮头处发生内漏时不便检查;管束与壳体间隙较大,影响传热。
浮头式换热器适用于管、壳温差较大及介质易结垢的场合。
⑶填料函式换热器填料函式换热器,管束一端可以自由膨胀,造价也比浮头式换热器低,检修、清洗容易,填函处泄漏能及时发现。
但壳程内介质有外漏的可能,壳程中不宜处理易挥发、易燃、易爆、有毒的介质。
⑷U形管式换热器U形管式换热器,只有一个管板,管程至少为两程,管束可以抽出清洗,管子可以自由膨胀。
其缺点是管内不便清洗,管板上布管少,结垢不紧凑,管外介质易短路,影响传热效果,内层管子损坏后不易更换。
热交换器原理与设计第2章 管壳式热交换器
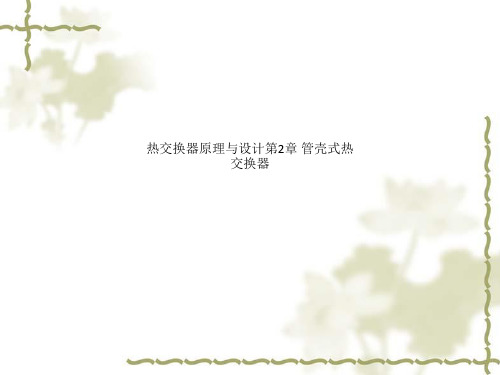
☆挡管是两端堵死的管子,安置在相应于分程隔板槽后面的 位置上,每根挡管占据一根换热管的位置,但不穿过管板, 用点焊的方法固定于折流板上。通常每隔3~4排管子安排一 根挡管,但不应设置在折流板缺口处,也可用带定距管的拉 杆来代替挡管。
优点:结构简单,制造成本低,规格范围广,工程中应用广泛。 缺点:壳侧不便清洗,只能采用化学方法清洗,检修困难,对较脏
或有腐蚀性介质不能走壳程。当壳体与换热管温差很大时, 可设置单波或多波膨胀节减小温差应力。
管壳式换热器结构名称
单程管壳式换热器
1 —外壳,2—管束,3、4—接管,5—封头 6—管板,7—折流板
图2.25 折流板的几何关系
2.2.4 进出口连接管直径的计算
进出口连接管直径的计算仍用连续性方程, 经简化后计算公式为:
D 4M1.13M
πρw
ρw
2.3 管壳式热交换器的传热计算
1) 选用经验数据:根据经验或参考资料选用工艺条 件相仿、设备类型类似的传热系数作为设计依据。 如附录 A。 2) 实验测定:实验测定传热系数比较可靠,不但可 为设计提供依据,而且可以了解设备的性能。但实 验数值一般只能在与使用条件相同的情况下应用。
焊在换热管上)。
图2.23 防冲板的形式
a) 内导流筒 图2.24 导流筒的结构
b) 外导流筒
★导流筒
❖ 在立式换热器壳程中,为使气、液介质更均匀地流入管间, 防止流体对进口处管束段的冲刷,而采用导流筒结构。
化工原理课程设计——换热器
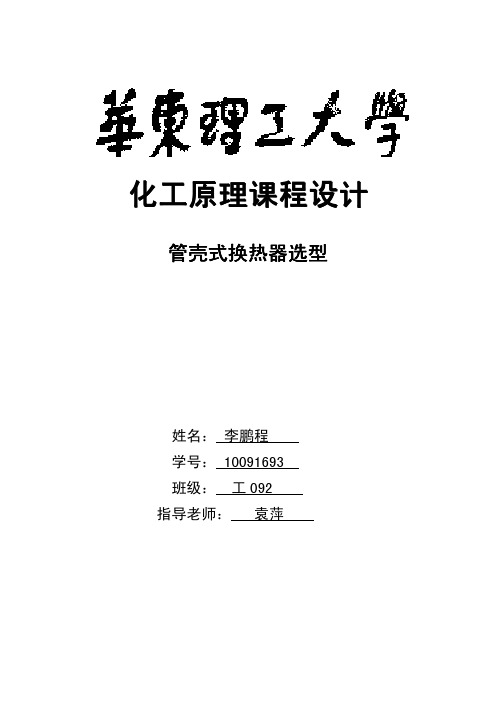
化工原理课程设计管壳式换热器选型姓名:学号:10091693班级:工092指导老师:袁萍前言1.换热器的设备简介传热是热能从热流体间接或直接传向冷流体的过程。
其性质复杂,不但要考虑经过间壁的热传导,而且要考虑到间壁两边流体的对流传热,有时还须考虑到辐射传热。
在化学工业中常遇到的热交换问题,根据冷、热流体热量交换的原理和方式基本上可分三大类即:间壁式、混合式和蓄热式。
其中间壁式换热器詹用量最大,据统计,这类换热器占总用量的99%。
间壁式换热器又可分为管壳式和板壳式换热器两类,其中管壳式换热器以其高度的可靠性和广泛的适应性,在长期的操作过程中积累了丰富的经验,其设计资料基本齐全,在许多国家都有了系列化的标准。
因此,作为广泛应用于各个领域的工业设备,它在国民经济中具有非常重要的作用。
换热器(英语翻译:heat exchanger),是将热流体的部分热量传递给冷流体的设备,又称热交换器。
管壳式换热器按结构特点分为固定管板式换热器、浮头式换热器、U型管式换热器、双重管式换热器、填料函式换热器和双管板换热器等。
前3种应用比较普遍。
固定管板式换热器的结构:主要有外壳、管板、管束、顶盖(又称封头)等部件构成。
它的特点是结构简单,没有壳侧密封连接,相同的壳体内径排管最多,在有折流板的流动中旁路最小,管程可以分成任何管程数,因两个管板由管子互相支撑,故在各种管壳式换热器中它的管板最薄,造价最低,因而得到广泛应用。
这种换热器的缺点是:壳程清洗困难,有温差应力存在。
这种换热器适用于两种介质温差不大,或温差较大但壳程压力不高及壳程介质清洁,不易结垢的场合。
在满足工艺过程要求的前提下,换热器应达到安全与经济的目标。
换热器设计的主要任务是参数选择和结构设计、传热计算及压降计算等。
设计主要包括壳体形式、管程数、换热管类型、管长、管子排列、管子支承结构、冷热流体的流动通道等工艺设计和封头、壳体、管板等零部件的结构、强度设计计算。
化工原理课程设计管壳式换热器的设计
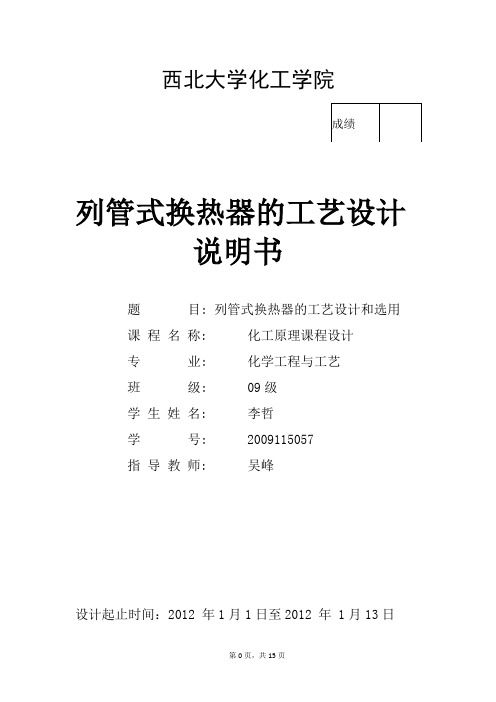
西北大学化工学院列管式换热器的工艺设计说明书题目: 列管式换热器的工艺设计和选用课程名称: 化工原理课程设计专业: 化学工程与工艺班级: 09级学生姓名: 李哲学号: 2009115057指导教师: 吴峰设计起止时间:2012 年1月1日至2012 年 1月13日设计题目:列管式换热器的工艺设计和选用一、设计条件炼油厂用循环水将煤油油从230℃冷却到120℃。
柴油流量位28700kg/h;循环水初温为22℃,经换热后升温到46℃。
换热器的热损失可忽略。
管、壳程阻力压降不大于100kPa。
试设计能完成上述任务的列管式换换热器。
二、设计说明书的内容1、设计题目及原始数据;2、目录;3、设计方案的确定;4、工艺计算及主体设备设计;5、辅助设备的计算及选型;(主要设备尺寸、衡算结果等);6、设计结果概要或设计结果汇总表;7、参考资料、参考文献;目录一.设计任务及设计条件 (3)二.设计方案 (3)1.换热器类型选择 (3)2.流程选择 (3)3.流向选择 (3)三.确定物性数据 (3)四.估算传热面积 (3)五.工艺结构尺寸计算 (3)1.管径及管内流速选择 (3)2.传热管数和传热管程数 (4)3.平均传热温差校正及壳程数 (5)4.传热管排列和分程方法 (5)5.壳体内径 (5)6.折流板 (5)7.其他主要附件 (6)8.接管 (6)9.壁厚的确定、封头 (7)六.换热器核算 (7)(一).热流量核算 (7)1.壳程表面传热系数核算 (8)2.管程表面传热系数核算 (8)3.污垢热阻 (9)4.传热面裕度 (9)(二)传热管壁温及壳体壁温计算 (9)(三)阻力计算 (10)1.管程流体阻力计算 (10)2.壳程流体阻力计算 (10)七.换热器主要计算结果汇表 (11)八.主要符号说明 (11)九.换热器主要结构尺寸图和管子布置图 (12)十.参考文献 (15)一.设计任务及设计条件:用循环冷却水将流量为28700Kg/h 的煤油从230℃降至120℃,冷却水为清净河水,进口温度22℃,选定冷却水出口温度46℃,设计一台列管换热器完成冷却任务。
管壳式换热器谁走管程谁走壳程是怎么定的?
混和气体在℃下地有关物性数据如下(来自生产中地实测值):
密度
定压比热容℃
热导率
粘度
循环水在℃下地物性数据:
密度㎏
定压比热容℃
热导率℃
粘度
二.确定设计方案
.选择换热器地类型
两流体温地变化情况:热流体进口温度℃出口温度℃;冷流体进口温度℃,出口温度为℃,该换热器用循环冷却水冷却,冬季操作时,其进口温度会降低,考虑到这一因素,估计该换热器地管壁温度和壳体温度之差较大,因此初步确定选用浮头式换热器.文档来自于网络搜索
管子在管板上排列地间距(指相邻两根管子地中心距),随管子与管板地连接方法不同而异.通常,胀管法取(~),且相邻两管外壁间距不应小于,即≥().焊接法取.文档来自于网络搜索
.管程和壳程数地确定当流体地流量较小或传热面积较大而需管数很多时,有时会使管内流速较低,因而对流传热系数较小.为了提高管内流速,可采用多管程.但是程数过多,导致管程流体阻力加大,增加动力费用;同时多程会使平均温度差下降;此外多程隔板使管板上可利用地面积减少,设计时应考虑这些问题.列管式换热器地系列标准中管程数有、、和程等四种.采用多程时,通常应使每程地管子数大致相等.文档来自于网络搜索
.计算管、壳程压强降根据初定地设备规格,计算管、壳程流体地流速和压强降.检查计算结果是否合理或满足工艺要求.若压强降不符合要求,要调整流速,再确定管程数或折流板间距,或选择另一规格地设备,重新计算压强降直至满足要求为止.文档来自于网络搜索
.核算总传热系数计算管、壳程对流传热系数α和α,确定污垢热阻和,再计算总传热系数',比较得初始值和计算值,若'=~,则初选地设备合适.否则需另设选值,重复以上计算步骤.文档来自于网络搜索
.流体流动阻力(压强降)地计算
换热器课程设计2011
④ 饱和蒸汽宜走管间-便于及时排除冷凝液及不凝性气体
⑤ 有毒流体宜走管内,使泄露机会较少 ⑥ 被冷却的流体宜走管间-可利用外壳向外的散热作用
⑦ 流量小或粘度大的液体,宜走管间-提高对流传热系数
⑧ 若两流体的温差较大,对流传热系数较大者宜走管间-减少热 应力
上述各点若不能同时兼顾,应视具体情况抓主要矛盾。
2.管长
以清洗方便及合理使用管材为原则
合理的换热器管长:1.5m、2m、3m、6m等 管子长度与公称直径之比,一般为l/d=4~6 ,对直 径小的换热器可取大些。
3.管子排列方法
正三角形、转角正三角形、正方形、转角正方形等
管板强度高;流体走短路 机会少,且扰动较大,因 而对流传热系数较高;相 同壳程内排更多管子。
膨胀节结构
• 管壳式换热器型号与系列标准
• 1)基本参数和型号 • (1)基本参数
• 公称换热面积SN • 公称直径DN • 公称压强PN • 换热器管长度L • 换热管规格和排列 • 管程数NP (2)型号表示方法 例G800II-1.0-110
1 2 3 4 5
二、化工原理课程设计任务
• 五、设计要求:
1、选定管壳式换热器的种类和工艺流程。 2、管壳式换热器的工艺计算和主要工艺尺寸 的设计。 3、设计结果概要或设计结果一览表。 4、设备简图。(要求在坐标纸上按比例画出 主要结构及尺寸和布管图) 5、对本设计的评述及有关问题的讨论。
二、化工原理课程设计任务
五、管程和壳程数的确定
1.管程数
当流体的流量较小或传热面积较大而需管数很多时, 有时会使管内流速较低,对流系数较小。 为提高管内流速,可采用多管程。 但管程数过多,管程流动阻力加大,增加动力费用;多程 会使平均温度差下降;多程隔板使管板上可利用面积减少 标准中管程数有:1、2、4和6程,多程时应使每程管子数 大致相等。 管程数m计算:
管壳式换热器设计参数的选择
管壳式换热器设计参数的选择摘要:文章探讨了管壳式换热器设计过程中管箱、壳体、管束、折流板和防冲板等参数的选择,提出了对设计过程中常见问题的解决方案,可以为此类换热器的设计提供参考。
关键词:管壳式换热器,管箱,壳体,管束,折流板,防冲板,设计Parameters Determine in Shell-Tube Heat Exchanger DesigningZhou Hai-ge*, SUN Ai-jun(China Textile Industry Engineering Institute, Beijing 100037)Abstract: Parameters determine of tube box, shell, bundle, baffle and impingement in shell-tube heat exchanger designing is discussed in this article. Propose the solution to ordinary question in designing. It is can be the reference for this type exchanger designing.Keywords: shell-tube heat exchanger, tube box, shell, bundle, baffle, impingement, design引言管壳式换热器是石化行业中应用最广泛的间壁式传热型换热器,适用范围从真空到超高压(超过100MPa),从低温到高温(超过1100℃),约占市场多于65%的份额[1],因此对于工程设计人员来说,管壳式换热器的设计十分重要。
管壳式换热器的主要组合部件包括壳体、前端管箱和后端结构(含管束)三部分。
管箱、壳体、管束、折流板、防冲板等设计参数决定了换热器的类型、规格及性能特点。
1. 管箱1.1 前端管箱的选择原则GB151中分别列出了A、B、C、N、D五种前端管箱型式[2]。
《热交换器原理与设计》管壳式热交换器设计22-23解析
13
式中:
ls——折流板间距; d0——管子外径; s——管间距;
sn——与流向垂直的管间距。 As,Ab,Ac之间的关系
As AbAc
As——为保证流速所需要的流通截面积
Ab——流体在缺口处的流通截面积
AC—两折流板间错流的流通截面积
38
Thank you for attention!
39
1、由理想管束的传热因子图查出柯尔本传热因子jH
假定 壳程流体全部错流流过管束
jHG sc0PP2/r3w0.1 4
2、查取折流板的校正因子jc, 缺口处不排管的结构jc=1 36
3、查取折流板泄漏影响的校正因子j1(A和E流路), 4、查取旁通影响的校正因子jb 5、折流板间距不等时的校正因子 js
壳体的外径
强度
钢制压力容器标准的规定加以确定 7
公称直径小于或等于400mm的热交换器,可以采用无缝钢管 制作圆筒,卷制圆筒的公称直径以400mm为基础,以100mm, 为进级档,必要的时候允许以50mm为进级档。
三、壳程流通截面积的计算
内容: 确定纵向隔板或折流板的数目与尺寸。
纵向隔板
AsM s/sws
二、壳体直径的确定
内径 作图(可靠,准确)
方法
估算 D s b 1 s 2 b
6
式中:
b′——管束中心线上最外层管中心至壳体内壁距离, b′=(1~1.5)d0(d0为管外径)。
b ——沿六边形对角线上的管数。
估算 当管子按照等边三角形排列时,b1.1 nt ;
当管子接正方形排列时 b1.19nt
9
弓形折流板 缺口高度
- 1、下载文档前请自行甄别文档内容的完整性,平台不提供额外的编辑、内容补充、找答案等附加服务。
- 2、"仅部分预览"的文档,不可在线预览部分如存在完整性等问题,可反馈申请退款(可完整预览的文档不适用该条件!)。
- 3、如文档侵犯您的权益,请联系客服反馈,我们会尽快为您处理(人工客服工作时间:9:00-18:30)。
本科生通用题目:单壳程双管程管壳式换热器设计(立式)专业:应用化学班级:0703班姓名:肖黎鸿成绩:导师签字:2010年7月11日题目:单壳程双管程管壳式换热器设计(立式)参数:要求要求每位学生在设计的过程中,充分发挥自己的独立工作能力及创造能力,在设计过程中必须做到:(1)及时了解有关资料,做好准备工作,充分发挥自己的主观能动性和创造性。
(2)认真计算和制图,保证计算正确和图纸质量。
(3)按预定计划循序完成任务。
日程安排:1.准备阶段(1天)2.设计计算阶段(3天)3.绘图阶段(4天)4.编写设计说明书(2天)目录1.绪论 02.设计计算 (1)2.1管子数n的计算 (1)2.2管子排列方式,管间距的确定 (1)2.3壳体直径的确定 (2)2.4壳体厚度的计算 (2)2.5壳体液压试验应力校核 (2)2.6分程隔板的选择 (2)2.7封头的选择 (3)2.8法兰,管板的选择 (3)2.9垫片尺寸的确定 (4)2.10管子拉脱力的计算 (4)2.11是否安装膨胀节的计算 (6)2.12折流板设计 (7)2.13拉杆设计 (7)2.14开孔补强 (8)2.15支座 (8)3.设计评述 (9)4.参考文献 (10)附:设计结果一览表 (11)1.绪论热交换器,通常又称作换热器,是化工﹑炼油和食品及其他工业部门的通用设备,在生产中占有重要作用。
化工生产中,换热器可作为加热器、冷却器、冷凝器、蒸发器和再沸器等,应用甚为广泛。
换热器种类很多,但根据冷、热流体热量交换的原理和方式基本上可以分为三大类,及间壁式、混合式和蓄热式。
三类换热器中,间壁式换热器应用最多。
本次设计的管壳式换热器就属于间壁式换热器的一种。
立式固定管板式换热器示意图2.设计计算2.1管子数n 的计算选25 ×2.5的无缝钢管,材质20号钢,管长1.5m 。
因为F =πd 均Ln ,所以根均1045.10225.011=⨯⨯==ππL d F n2.2管子排列方式,管间距的确定本设计物料:管程氮气,壳程水,循环水工作温度90℃较高,不易结垢。
可暂不考虑机械清洗水垢的问题,故排列方式采用结构紧凑、传热系数较高的正三角形排列。
由《化工设备与仪表自动化》中表6-4得六角形层数为6,对角线上的管数为13,管子根数为127其中因安排拉杆需减少6根(参见2.12拉杆设计),实际管数121根。
查表6-5,由管子外径25mm,可得管间距α=32mm 。
管子排列方式如右图:2.3壳体直径的确定D i =a(b-1)+2l式中 D i —换热器内径,mmb —正六角形对角线上的管子数,查表6-4,取b=13 l —最外层管子的中心到壳壁边缘的距离,取l =2d.mmD i 4852522)113(32=⨯⨯+-⨯=查《仪表设备及仪器自动化》P58表2-5,并结合壳体直径的计算,确定D i =500mm2.4壳体厚度的计算p c —计算压力,取p c =0.8MPa ;D i =500mm; 焊接系数φ=0.85; 材料选用Q235-B 钢,[σ]95℃=113Mpa 。
计算壁厚为mm p D p s c i c 09.28.085.011325008.0]2[t =-⨯⨯⨯=-=ϕσ取 c 2=1mm,由书中表4-7得c 1 =0.3mm圆整后实取S n =4mm 。
DN500,δ=4每米钢板质量为50kg 。
2.5壳体液压试验应力校核试验压力MPa p p tT 0.11131138.025.1][][25.1=⨯⨯==σσ故:()()MPa S S D p e e i T T 1.93)3.14(2)3.14(5000.12=-⨯-+⨯=+=σQ235-B 在常温时MPa s 235=σ,MPa s 78.17923585.09.09.0=⨯⨯=ϕσ,sT ϕσσ9.0<, 故液压试验应力校核合格。
2.6分程隔板的选择分程隔板应采用与封头、管箱短节相同材料,故材料选用Q235-B 。
要求隔板的密封面与壳体法兰密封面,管板密封面与分程槽面须处于同一基面。
分程隔板槽深度为4mm ,槽宽12mm 。
其结构相见装配图。
查《化工单元过程及设备课程设计》表4-1得分程隔板的最小厚度为8mm2.7封头的选择上下封头均选用EHA椭圆封头,其厚度与壳体厚度相同,材料选用Q235-B 钢。
上封头的主要尺寸如下表:公称直径DN (mm) 曲面高度h1 (mm) 直边高度h2 (mm) 碳钢厚度δ(mm) 500 125 40 4 下封头的主要尺寸如下表:公称直径DN (mm) 曲面高度h1 (mm) 直边高度h2 (mm) 碳钢厚度δ(mm) 500 125 50 4 查《过程设备机械设计》P106标2 JB/T4746-2002得:公称直径DN (mm) 总深度H(mm)内表面积A (m2)容积V (m3)质量M (kg)500 150 0.3103 0.0213 9.6 如下图所示:2.8法兰,管板的选择容器法兰材料选16MnR。
根据JB4701—2000标准,选用DN500,PN1.6(MPa)的甲型平密封面法兰。
DN25(100)PN<4MPa管法兰的接管伸出长度为150mm。
容器法兰的主要尺寸如下表:公称直径DN,mm法兰,mm 螺柱D D1D2D3D4δ d 规格数量500 630 590 555 545 542 44 23 M20 28选用固定式换热器管板,不兼做法兰,换热管与管板的连接采用先焊后强度胀的连接形式,考虑到胀接结构要求,此次管板的厚度取30mm。
实际上,管板的厚度应按GB151-1991进行强度计算,但由于计算复杂,在此不进行具体的校核。
2.9垫片尺寸的确定由于与壳体接触的介质仅为冷却水,对密封的要求一般,因此密封垫片选用价格相对较低的石棉橡胶片。
根据JB/T4704—1992及所选的DN500,PN1.6(MPa)甲型平焊法兰。
垫片尺寸如下表:(单位:mm)公称直径DN 垫片内径d i垫片外径D0垫片厚度t 500 504 544 32.10管子拉脱力的计算计算数据如下表p ld pfq p 0π= 式中)(39625432866.04866.022202mm d a f =⨯-⨯=-=ππp =1.1(MPa); l =40mmMPa q p 14.040253961.1=⨯⨯⨯=πB.温差应力导致的每平方米胀接周边上的拉脱力l d d d q i t t 02204)(-=σ式中st s l t A A t t aE +-=1)(σ2n 24.633042508500S mm D A s =⨯+⨯=⨯=ππ中 222220625.21371)6127()2025(4)(4mm n d d A it =-⨯-⨯=-=ππ则)(47.4224.6330625.213711751021.0108.1166MPa t =+⨯⨯⨯⨯=-σ )(91.150254)2025(47.4222MPa q t =⨯⨯-⨯=由已知条件可知,q p 与q t 的作用方向相同,都使管子受压,则合拉脱力为MPa q q q t p 05.291.114.0=+=+= q <[q ]=4.0(MPa) 因此,拉脱力在许用范围内。
2.11是否安装膨胀节的计算 管,壳壁所产生的轴向力:)(1008.9625.2137124.6330625.2137124.6330751021.0108.11)(5661N A A A A t t aE F t s t s s l ⨯=⨯⨯+⨯⨯⨯⨯=⋅⋅+-=-压力作用于壳体上的轴向力:t s sA A QA F +=2其中lt t s i p S d n p nd D Q ])2()[(420202⋅-+⋅-=π)(1038.1]1.1)5.2225(1217.0)25121500[(45222N Q ⨯=⨯⨯-⨯+⨯⨯-=π则N F 55210315.0625.2137124.633024.63301038.1⨯=+⨯⨯=压力作用于管子上的轴向力:N A A QA F t s t 55310065.1625.2137124.6330625.213711038.1⨯=+⨯⨯=+=)(41.14824.633010315.01008.95521Mpa A F F s s =⨯+⨯=+=σ)(50.37625.2137110065.11008.95531MPa A F F t t -=⨯+⨯-=+-=σ根据《钢制管壳式换热器设计规定》:)(180][241.148MPa MPa t s s =〈=σφσ)(206][250.37Mpa MPa l t t =〈=σσq <[q ]=4.0(MPa)条件成立,故本换热器不必设置膨胀节。
2.12折流板设计折流板为单弓形,切缺率(切掉圆弧的高度与壳体内径百分比)为20%~49%,通常为20%~25%,最佳大小一般为20%,此时单位压降下的传热膜系数最高。
切掉圆弧的高度mmD h i 1002.0500%20=⨯=⨯=实际应用中,单弓形折流板间距B=(0.2-1.0)D i ,以0.4~0.5最优。
取B=0.5D i=250mm 。
折流板数5125015001=-=-=折流板间距传热管长B N折流板最小厚度与壳体直径、换管无支承板有关,由书中表6—6查得为3mm 。
由表6—8查得折流板外径496.5mm,材料为Q235—B 钢。
按GB151规定,I 级换热器由于d<32mm,l =1500>900mm,故折流板管孔直径与允许偏差分别为25.4mm 和0.3mm 。
弓形缺口为上下布置,以造成流体剧烈扰动,增大传热系数。
2.13拉杆设计由于换热管外径大于19mm ,故拉杆采用拉杆定距管的形式。
根据《过程设备机械设计》中表5-6,拉杆选用Φ10,共6根,材料为Q235—B 钢,如图所示:由GB151-1999表45查得,拉杆的主要尺寸如下表: 拉杆螺纹公称直径 d n /mm 数量 基本尺寸拉杆直径d/mm L a /mm L b /mm b /mm 1061013≥401.5拉杆孔见上图:d n=10mm, L2=1.5×d n=15mm2.14开孔补强换热器壳体和封头的接管处开孔需要补强,常用的结构是在开孔外面焊上一块与容器的材料和厚度相同,即4mm厚的Q235—B钢板。
开孔补强如下图。
2.15支座采用裙座,裙座厚度取S c=8mm,基础环厚度取10mm。
设计结果,见所绘的换热器装配图。
3.设计评述本次设计的单壳程双管程管壳式换热器,其两端与壳体连为一体,管子则固定于管板上,其结构简单;在相同的壳体直径内,排管最多,比较紧凑。