转炉炼钢的基本任务及原理共46页
转炉炼钢
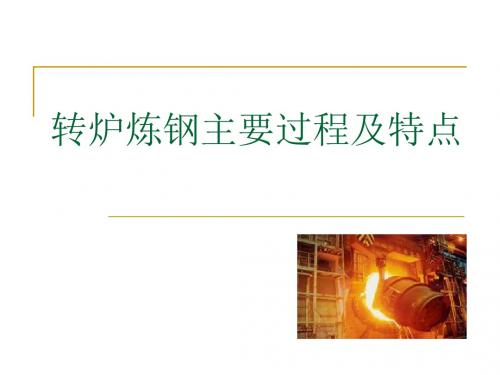
造渣制度
在生产中,一般根据铁水成分和所炼钢种来 确定造渣方法,包括单渣法、双渣法和双渣留渣 法。 氧气转炉的冶炼周期短,必须做到快速成渣, 使炉渣尽快具有适当的碱度、氧化性和流动性, 以便迅速把金属中的杂质去除。 渣料的加入通常根据铁水条件和石灰质量而 定,当铁水温度高和石灰质量好时,渣料可在兑 铁水前一次性加入炉内,以早化渣,化好渣。
转炉炼钢主要过程及特点
转炉炼钢在钢铁生产中的地位
转炉炼钢是介于炼铁和轧钢之间的中间环节
高 炉 炼 铁
连 铸
出 铁 水
转炉炼钢
轧 钢
转炉炼钢的基本任务
脱碳、脱磷、脱硫、脱氧; 去除有害气体和夹杂; 提高温度; 调整成分;
炼钢过程通过供氧、造渣、加合金、搅拌、 升温等手段完成炼钢基本任务。
转炉炼钢的基本原理
根据所炼钢种的要求 把生铁中的含碳量去除到 规定范围,并使其它元素 的含量减少或增加到规定 范围的过程。简单地说, 是对生铁降碳、去硫磷、 调硅锰含量的过程。这一 过程基本上是一个氧化过 程,是用不同来源的氧(如 空气中的氧、纯氧气、铁 矿石中的氧)来氧化铁水中 的碳、硅、锰等元素。
转炉炼钢的特点
完全依靠铁水氧化带来的化学热及物理热;
生产率高(冶炼时间在20分钟以内); 质量好,气体含量少:(因为CO的反应搅拌,将N、 H除去)可以生产超纯净钢,有害成份(S、P、N、 H、O)〈80ppm; 冶炼成本低,耐火材料用量比平炉及电炉用量低; 原材料适应性强,高P、低P都可以。
在转炉炼钢中,到达吹炼终点时,钢水含氧量 一般比较高为了保证钢的质量和顺利ቤተ መጻሕፍቲ ባይዱ注,必须对 钢水进行脱氧。 为了使钢达到性能要求,还需向钢水中加入 合金元素,即所谓合金化操作。 采用复吹工艺后,钢中[O]含量平均比顶吹转炉 降低104×10-6。合金收得率有所提高,不仅可减 少脱氧铁合金消耗,而且大幅度降低脱氧生成的夹 杂物,为提高钢材洁净度创造了有利的条件。
转炉炼钢的冶炼原理

转炉炼钢的冶炼原理
转炉炼钢法:这种炼钢法使用的氧化剂是氧气。
把空气鼓入熔融的生铁里,使杂质硅、锰等氧化。
在氧化的过程中放出大量的热量(含1%的硅可使生铁的温度升高200摄氏度),可使炉内达到足够高的温度。
因此转炉炼钢不需要另外使用燃料。
转炉炼钢是在转炉里进行。
转炉的外形就像个梨,内壁有耐火砖,炉侧有许多小孔(风口),压缩空气从这些小孔里吹炉内,又叫做侧吹转炉。
开始时,转炉处于水平,向内注入1300摄氏度的液态生铁,并加入一定量的生石灰,然后鼓入空气并转动转炉使它直立起来。
这时液态生铁表面剧烈的反应,使铁、硅、锰氧化(FeO,SiO2 , MnO,) 生成炉渣,利用熔化的钢铁和炉渣的对流作用,使反应遍及整个炉内。
几分钟后,当钢液中只剩下少量的硅与锰时,碳开始氧化,生成一氧化碳(放热)使钢液剧烈沸腾。
炉口由于溢出的一氧化炭的燃烧而出现巨大的火焰。
最后,磷也发生氧化并进一步生成磷酸亚铁。
磷酸亚铁再跟生石灰反应生成稳定的磷酸钙和硫化钙,一起成为炉渣。
转炉 原理

转炉原理
转炉是一种用来炼钢的设备,其原理是利用高温将原料中的杂质和不纯物质去除,从而得到高纯度的钢材。
转炉的操作过程可以大致分为两个阶段:吹炼和出钢。
在吹炼阶段,首先将底吹氧气和喷吹煤气混合物以高速吹入转炉中。
煤气在高温下燃烧,产生的热量使转炉内部的温度升高。
吹入的氧气则与煤气中的一部分碳反应生成一氧化碳和二氧化碳,同时释放出大量的热量。
这些燃烧和反应过程会形成一个高温高碳的还原区,也称为“焦墨区”。
焦墨区内的高温和高碳环境有助于将原料中的杂质和不纯物质还原为气体或脆性的固体物质,从而实现了炉内的净化作用。
炉内的搅拌装置会将炉内的材料搅拌均匀,促进反应的进行。
吹炼过程中,转炉的操作工人会根据炉内的温度和氧气供应量等参数进行调节,以控制反应的速度和程度。
一般来说,吹炼时间为20-30分钟左右。
吹炼结束后,开始进行出钢操作。
操作工人会逐渐停止底吹和喷吹,采取顶吹的方式将氩气或氮气吹入炉内,以稳定温度,并形成一个保护层,防止钢液的再次氧化。
在出钢过程中,操作工人会打开底部的钢水口,将炉内的钢液流出,并通过连铸设备进行凝固和成型。
同时,还会对钢液进
行取样分析,以确保钢材的质量达到要求。
总的来说,转炉通过高温和高碳环境以及氧气的吹入,实现了对原料中的杂质和不纯物质的去除,从而得到高纯度的钢材。
这种炼钢方式具有高效、灵活和环保等特点,广泛应用于钢铁行业。
转炉炼钢工艺简介
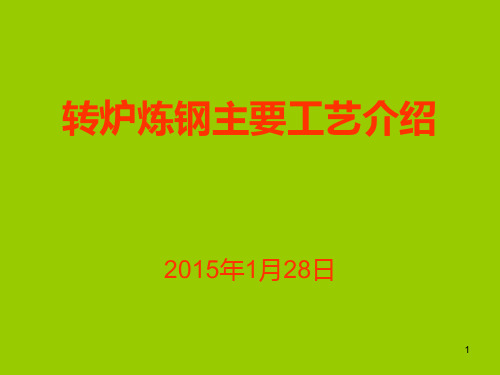
2015年1月28日
1
主要内容
一 炼钢的基本任务 二 转炉炼钢特点及工艺流程 三 炼钢用主要原材料 四 转炉炼钢主要工艺制度
2
一 、炼钢的基本任务
1.脱碳、脱磷、脱硫、脱氧; 2.去除有害气体和夹杂; 3.调整温度; 4.调整成分。
炼钢过程通过供氧、造渣、加合金、搅拌、 升温等手段完成炼钢基本任务。 氧气顶吹转炉炼 钢过程,主要是脱碳、升温、脱磷、脱硫以及脱 氧和合金化等高温物理化学反应的过程,其工艺 操作则是控制供氧、造渣、温度及加入合金材料 等,以获得所要求的钢液,并浇成合格钢钢锭或 铸坯。
归纳:四脱、二去、两调整
3
二、转炉炼钢特点及工艺流程
转炉炼钢特点: 1.生产率高(吹氧时间在20分钟以内); 2.质量好:气体含量少(因为CO的反应强搅拌,将N、
H除去)可以生产超纯净钢; 3.有害成份(S、P、N、H、O)〈100PPm; 4.冶炼成本低,耐火材料用量比平炉电炉用量低; 5.原材料适应性强,高P、低P都可以; 6.设备少,投资节省。
• S的影响
除了含硫易切钢(要求ωS=0.08%~0.30%)以外, 绝大多数钢中硫是有害元素。 转炉中硫主要来自金属料和熔剂材料等,而其中 铁水的硫是主要来源。在转炉内氧化性气氛中脱 硫是有限的,脱硫率只有20%~40%。由于低硫 [s]<0.010%的优质钢需求量增长,因此用于转炉 炼钢的铁水要求[s] <0.010%。这种铁水很少, 为此必须进行预处理,降低入炉铁水硫含量。
12
2)废钢
废钢是电弧炉炼钢的基本原料,用量约 40~100%;对氧气顶吹转炉炼钢,既是主 原料之一,也是冷却效果稳定的冷却剂。 通常占装入量的30%以下,适当地增加废 钢比,可以降低能源消耗。
冶金安全生产技术(转炉炼钢)

转炉炼钢安全生产技术
操作流程:装料时,把炉体倾斜,先装入称量好 的废钢,接着装入铁水。然后使炉体直立,一边喷吹 氧气一边投入轧钢铁皮、石灰等辅助原料。用氧气喷 枪进行喷吹出现着火现象。后期,降下副枪测定铁水 中的碳浓度和温度,预测达到目标的时间,最后上升 氧枪,把炉体倒向装料侧,从炉口进行测温和取样, 再把炉体倒向出钢侧出钢。出钢后再把炉体倒向装料 侧排出渣。
转炉炼钢安全生产技术
(2)兑铁、加废钢时发生大喷的原因—— 均发生在 留渣作业
留渣操作中,若兑入铁水,炉内条件发生根本变 化,一方面铁水带来大量碳,另一方面铁水温度较低, 使炉内残留炉渣及钢水温度骤然下降,促进碳氧反应 的剧烈进行,就会发生“爆炸”性大喷。
转炉炼钢安全生产技术
(3)终点倾炉大喷原因 后吹时间长或由于操作不当,炉内尚在剧烈反应, 使大量钢渣外涌,形成喷溅。 补炉料粘结不牢,倾炉时突然塌落,造成钢渣猛烈 外涌性喷溅。 出钢或兑铁过程中炉衬大面积塌落。
转炉炼钢安全生产技术
三、重点危险因素的分析及对策 1、转炉氧枪坠落爆炸
转炉冶炼过程中C-O反应所需的氧气由氧枪提供, 反应过程中高温高达1700℃以上,为了防止氧枪烧坏, 氧枪均采取高压水冷却,但如果氧枪直接与高温液面接 触,即使有在冷却系统完好的情况下,氧枪也会被烧坏, 高压水击入高温液面下,形成爆炸。
转炉炼钢安全生产技术
预防转炉喷溅伤害的对策: ③吹炼中途加料,尽量采用小批次的办法,以避免熔 池温度明显降低,抑制碳氧反应而使渣中氧化铁升高。 ④炉渣不化,提枪化渣时,不能长时间高枪位吹氧, 否则,氧化铁大量增加,引起喷溅。一旦发生喷溅, 不能立即降枪,若此时降枪,脱碳反应更加激烈,反 会加剧喷溅。此时可适当提枪,一方面减缓脱碳反应, 另一方面借助氧气流股的机械冲击力冲击炉渣,使气 体排出,减轻炉渣发泡程度。如果是金属喷溅,可适 当提枪增加渣中氧化铁,另外加适量萤石,使炉渣快 速熔化覆盖钢液面。
转炉炼钢原理及工艺

转炉炼钢原理及工艺
转炉炼钢是通过加热合金材料,然后将其在氧气中抽出到转炉,形成一个旋转坩埚里,再使材料在转炉内不断熔化、混合、渣滓沉淀,达到钢的熔化和净化,最后冷却固化,即可获得均匀的高质量的钢的过程。
转炉炼钢的工艺路径主要包括:原料进炉、熔炼、净化、合金添加、出炉等步骤。
1、原料进炉:将碳钢和合金料装入转炉,加热至溶化温度,开始熔融。
2、熔炼:转炉内熔融的温度受多种因素的影响,如加料量、加料温度、炉气系统的平衡性、熔炼时间等。
3、净化:即清洁熔化渣滓,消除杂质,把金属液中的杂质置于渣滓中,让金属液纯度升高。
4、合金添加:将净化后的钢液入合金添加系统,加入合金钢料,使钢液按照要求的成分,营造钢种具有相应的技术性能。
5、出炉:金属液改变形态,冷却成指定的形状和尺寸,经过纯化后形成高质量钢。
转炉工作原理

转炉工作原理
转炉是一种用于钢铁冶炼的设备,其工作原理主要包括以下几个步骤。
首先,转炉会预热并预处理废钢。
废钢通常包括废旧钢材、废钢屑等。
这些废钢会被切碎并清理,然后送入转炉。
预热的目的是提高废钢的温度,以加快冶炼过程。
接下来,废钢被加入到转炉中,并加入适量的石灰石和焦炭。
石灰石的作用是与废钢中的杂质反应,形成熔渣,将杂质分离出去。
而焦炭则为提供还原剂,帮助将铁氧化物还原为金属铁。
在高温下,转炉内部的氧气被吹入,氧气与废钢中的碳反应,产生大量的热量。
这样的高温环境下,废钢中的铁和其他成分开始熔化并混合在一起。
熔融的废钢逐渐转变为炉渣和钢水。
炉渣是由废钢中的氧化物、碱金属和杂质等组成,可通过与废钢的比重差异,从钢水中分离出来。
而钢水则是由熔化的废钢中的金属铁和其他合金元素组成,钢水会流出转炉底部的铁口。
最后,钢水被收集并送往连铸机进行连铸成型。
连铸机会将钢水注入到多个铸模中,使其快速冷却并形成连铸坯。
这些连铸坯可进一步加工成不同形状和尺寸的钢材。
总的来说,转炉的工作原理是通过在高温、高氧气环境下,利用石灰石和焦炭的反应产生的热量和还原剂的作用,使废钢熔
化,并将其中的杂质分离出去,最终得到熔融的钢水,再通过连铸工艺将其加工成为实际应用的钢材。
转炉炼钢基础知识
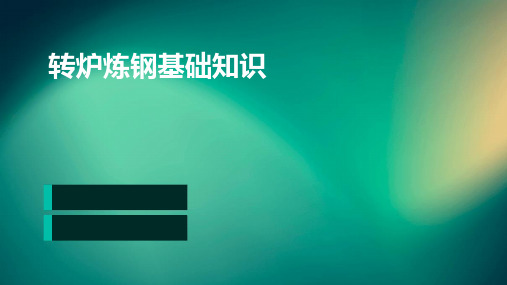
04 转炉炼钢操作技术
装料技术
装入炉料
根据炼钢工艺要求,将所需原材料装入转炉中。
合理配比
根据钢种要求,合理配比铁水、废钢、生铁等炉 料。
装料顺序
按照一定顺序装入炉料,以保证炼钢过程顺利进 行。
熔化技术
熔化温度控制
控制熔化温度,确保炉料完全熔 化。
熔化速过慢影响生产效率。
转炉炼钢是现代钢铁生产中最为重要的工艺之一,具有高效、低耗、环保等优点。
转炉炼钢的工艺流程
铁水预处理
去除铁水中的杂质和有 害元素,提高铁水的纯
净度。
转炉吹氧
通过向炉内吹入氧气,使铁 水中的杂质和碳元素氧化,
生成气体和炉渣排出。
钢水成分调整
通过加入合金元素,调 整钢水的化学成分,以 满足不同用途的要求。
钢水浇注
将合格的钢水注入钢锭 模或连铸机中,形成钢
锭或连铸坯。
转炉炼钢的优缺点
优点
生产效率高、成本低、环保性好 、产品品种多等。
缺点
对原料质量要求高、能耗较大、 操作技术要求高等。
02 转炉炼钢原料
铁水
铁水是转炉炼钢的主要原料之一,含 有大量的铁元素和少量的碳、硅、锰 等元素。
铁水预处理技术,如脱硫、脱磷等, 可以提高转炉炼钢效率和产品质量。
烟气处理系统的设计需考虑能耗、处理效果和设 备寿命等方面的因素。
06 转炉炼钢环境保护与节能 减排
烟尘治理
烟尘来源
转炉炼钢过程中产生的烟尘主要来源于原料的破碎、配料、装料、 熔炼、出钢等环节。
烟尘治理措施
采用高效除尘器,如电除尘器、袋式除尘器等,对烟尘进行收集和 处理,降低烟尘排放浓度。
烟尘治理效果
余热利用