铝板带加工过程中的织构问题
铝板加工现状分析报告
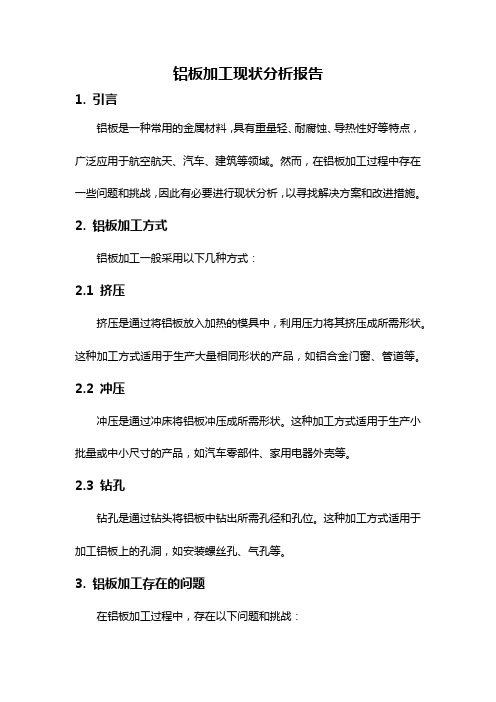
铝板加工现状分析报告1. 引言铝板是一种常用的金属材料,具有重量轻、耐腐蚀、导热性好等特点,广泛应用于航空航天、汽车、建筑等领域。
然而,在铝板加工过程中存在一些问题和挑战,因此有必要进行现状分析,以寻找解决方案和改进措施。
2. 铝板加工方式铝板加工一般采用以下几种方式:2.1 挤压挤压是通过将铝板放入加热的模具中,利用压力将其挤压成所需形状。
这种加工方式适用于生产大量相同形状的产品,如铝合金门窗、管道等。
2.2 冲压冲压是通过冲床将铝板冲压成所需形状。
这种加工方式适用于生产小批量或中小尺寸的产品,如汽车零部件、家用电器外壳等。
2.3 钻孔钻孔是通过钻头将铝板中钻出所需孔径和孔位。
这种加工方式适用于加工铝板上的孔洞,如安装螺丝孔、气孔等。
3. 铝板加工存在的问题在铝板加工过程中,存在以下问题和挑战:3.1 刀具磨损由于铝板的物理性质,加工过程中刀具容易磨损,导致加工效率低下。
特别是在冲压和钻孔过程中,刀具容易因铝板的硬度较低而受损。
3.2 加工精度铝板加工精度要求较高,特别是在航空航天领域需要达到更高的精度要求。
然而,由于铝板的软性,容易产生变形和翘曲现象,影响加工精度。
3.3 加工表面质量铝板的加工表面质量对于产品的外观和性能有重要影响。
然而,因为铝板的软性,容易出现表面瑕疵、划痕等问题,使得加工表面质量难以满足要求。
4. 改进和解决方案为解决上述问题和挑战,可以采取以下改进措施:4.1 刀具选择和涂层技术选择合适的刀具材质和涂层技术,提高刀具的硬度和抗磨损性能,延长刀具寿命,提高加工效率。
4.2 规范加工工艺制定严谨的加工工艺流程,确保每个环节的操作规范。
同时,通过合理的加工参数设置和控制,减少变形和翘曲现象,提高加工精度。
4.3 加工表面处理增加铝板的表面处理环节,如喷涂、阳极氧化等,改善加工表面质量,提高产品的外观和性能。
4.4 自动化加工引入自动化加工设备和机器人技术,提高加工的自动化水平,减少人为因素对加工质量的影响,提高生产效率和产品质量。
深冲用铝板的织构和各向异性
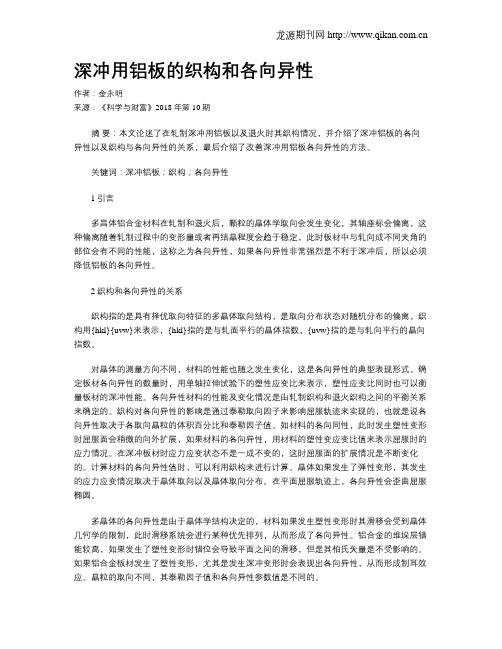
深冲用铝板的织构和各向异性作者:金永明来源:《科学与财富》2018年第10期摘要:本文论述了在轧制深冲用铝板以及退火时其织构情况,并介绍了深冲铝板的各向异性以及织构与各向异性的关系,最后介绍了改善深冲用铝板各向异性的方法。
关键词:深冲铝板;织构;各向异性1引言多昌体铝合金材料在轧制和退火后,颗粒的晶体学取向会发生变化,其轴座标会偏离,这种偏离随着轧制过程中的变形量或者再结晶程度会趋于稳定,此时板材中与轧向成不同夹角的部位会有不同的性能,这称之为各向异性,如果各向异性非常强烈是不利于深冲后,所以必须降低铝板的各向异性。
2织构和各向异性的关系织构指的是具有择优取向特征的多晶体取向结构,是取向分布状态对随机分布的偏离,织构用{hkl}{uvw}来表示,{hkl}指的是与轧面平行的晶体指数,{uvw}指的是与轧向平行的晶向指数。
对晶体的测量方向不同,材料的性能也随之发生变化,这是各向异性的典型表现形式,确定板材各向异性的数量时,用单轴拉伸试验下的塑性应变比来表示,塑性应变比同时也可以衡量板材的深冲性能。
各向异性材料的性能及变化情况是由轧制织构和退火织构之间的平衡关系来确定的。
织构对各向异性的影响是通过泰勒取向因子来影响屈服轨迹来实现的,也就是说各向异性取决于各取向晶粒的体积百分比和泰勒因子值。
如材料的各向同性,此时发生塑性变形时屈服面会稍微的向外扩展,如果材料的各向异性,用材料的塑性变应变比值来表示屈服时的应力情况。
在深冲板材时应力应变状态不是一成不变的,这时屈服面的扩展情况是不断变化的。
计算材料的各向异性值时,可以利用织构来进行计算。
晶体如果发生了弹性变形,其发生的应力应变情况取决于晶体取向以及晶体取向分布。
在平面屈服轨迹上,各向异性会歪曲屈服椭圆。
多晶体的各向异性是由于晶体学结构决定的,材料如果发生塑性变形时其滑移会受到晶体几何学的限制,此时滑移系统会进行某种优先排列,从而形成了各向异性。
铝合金的堆垛层错能较高,如果发生了塑性变形时错位会导致平面之间的滑移,但是其柏氏矢量是不受影响的。
铝材轧制过程中常见问题的解决方法

铝材轧制过程中常见问题的解决方法技术工作总结——铝材轧制过程中常见问题的解决方法铝原料轧制过程中的质量控制技术对现行的的生产型企业来讲是十分重要的。
我们现在所采用的原料轧制技术是沿用上世纪七十年代中期上海铝材厂传授下来的成熟的轧制技术(当时这种技术属国内比较先进的生产技术),从铝锭和角料进炉开始到成品铝带出厂,系列铝加工轧制技术均能够得到充分运用和发挥,通过三十多年来的生产实践和运用,在不更换现有生产设备的情况下,改良轧制过程中的工艺技术,发现和解决生产中常见问题十分关键。
按照现时确定的轧制原料工工序,应包含熔炼、浇铸、热轧、冷通及精轧。
1熔炼方面我公司所熔炼的原料是铝锭加角料,在原料的进炉前,我认为必须对角料进行检验,主要是检查角料中的包杂情况进行抽检,其次是对角料中是否含水份情况进行一一巡视,决不能向炉膛内投进一块含有水分的角料块,经过多年来的问题排查发现,角料含水是造成后道产品气泡等质量问题的原因之一。
实践中,我认识到在熔炼过程中,必须注意的是除气、排渣问题,如果除气、排渣处理不好,产品到了后道,或者成品到用户以后,就会出现后续产品有气泡、亮点、白丝等诸多质量问题。
我采用的解决的方法是通过空心管向铝液中吹入氮气,这样处理得比较好的话,气泡、亮点、白丝等质量问题就会消除。
为了提高出水率,在铝液达到一定温度后,继续向铝液中投放一定数量的角料块,在温度允许的前提下,角料会在铝液中迅速融化成铝液,既省时有省料,还没有烧损,是一个提高经济效益的好方法,但是,要重视的问题就是,同样要做好除气排渣的工作,否则会出现产品起皮现象。
熔炼方面按照技术要求去做,产品质量问题就会随之消灭。
2浇铸方面铝液经过一定时间的静止后,就可以浇铸。
此时的模具一定要经过安全检查,按照操作规程操作,将模具倾斜到一定角度,铝液慢慢的向模具内倒入,不可太快。
太快易造成铝液中夹杂的气体不能排出,引起坯块密度小于2.7×103Kg/m3(结构疏松),其强度低于sb=80~100MPa,轧制后尤其是到了后续加工制品时会出现各种质量等问题。
《冷轧AA6061铝合金的织构、微米压痕与腐蚀性能研究》
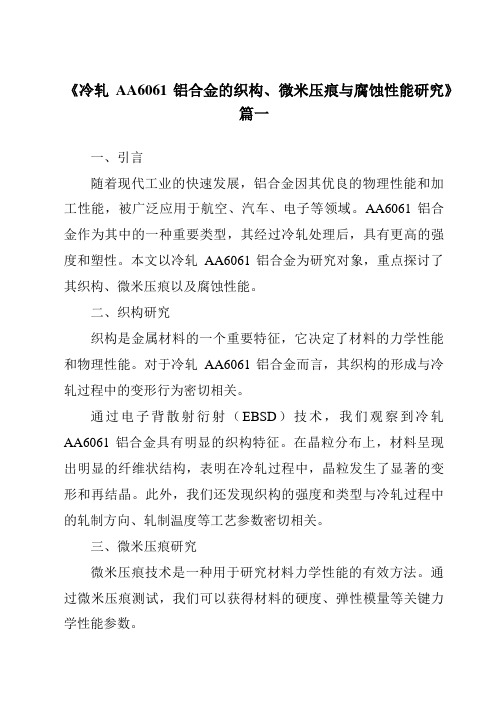
《冷轧AA6061铝合金的织构、微米压痕与腐蚀性能研究》篇一一、引言随着现代工业的快速发展,铝合金因其优良的物理性能和加工性能,被广泛应用于航空、汽车、电子等领域。
AA6061铝合金作为其中的一种重要类型,其经过冷轧处理后,具有更高的强度和塑性。
本文以冷轧AA6061铝合金为研究对象,重点探讨了其织构、微米压痕以及腐蚀性能。
二、织构研究织构是金属材料的一个重要特征,它决定了材料的力学性能和物理性能。
对于冷轧AA6061铝合金而言,其织构的形成与冷轧过程中的变形行为密切相关。
通过电子背散射衍射(EBSD)技术,我们观察到冷轧AA6061铝合金具有明显的织构特征。
在晶粒分布上,材料呈现出明显的纤维状结构,表明在冷轧过程中,晶粒发生了显著的变形和再结晶。
此外,我们还发现织构的强度和类型与冷轧过程中的轧制方向、轧制温度等工艺参数密切相关。
三、微米压痕研究微米压痕技术是一种用于研究材料力学性能的有效方法。
通过微米压痕测试,我们可以获得材料的硬度、弹性模量等关键力学性能参数。
在冷轧AA6061铝合金的微米压痕测试中,我们发现材料的硬度随着压痕深度的增加而逐渐降低。
这表明材料在受到外力作用时,表层具有较高的硬度和较强的抵抗变形的能力。
此外,我们还发现材料的弹性模量也具有显著的方向性特征,与材料的织构特征密切相关。
四、腐蚀性能研究腐蚀是金属材料在特定环境下的一种常见失效形式。
对于冷轧AA6061铝合金而言,其腐蚀性能与其表面状态、内部组织以及外部环境等因素密切相关。
通过电化学腐蚀测试,我们发现冷轧AA6061铝合金在特定环境下具有较好的耐腐蚀性能。
这主要归因于其致密的氧化膜层和稳定的内部组织。
然而,在不同环境下,材料的腐蚀行为可能存在差异,因此在实际应用中需要充分考虑环境因素的影响。
五、结论通过对冷轧AA6061铝合金的织构、微米压痕和腐蚀性能的研究,我们得出以下结论:1. 冷轧处理可以显著改变AA6061铝合金的织构特征,使其具有更高的强度和塑性。
Al-Zn-Mg-Cu系铝合金厚板冷轧过程中的织构演变
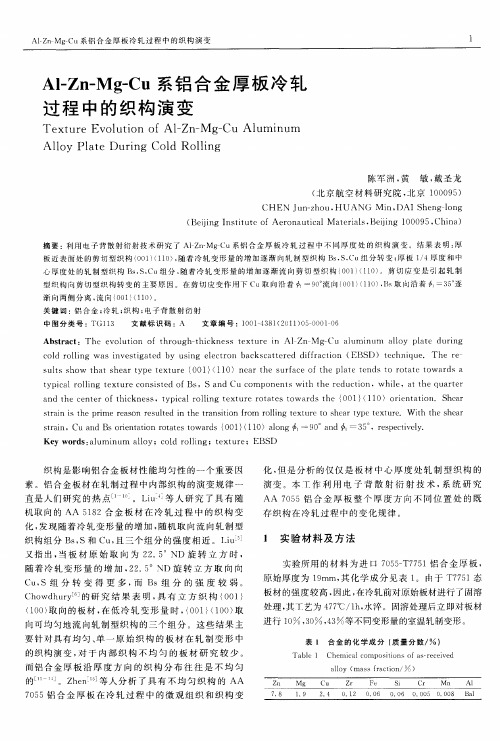
心厚 度 处 的 轧制 型 织 构 B , , u组 分 . 着 冷 轧变 形 量 的 增 加逐 渐 流 向剪 切 型织 构 { 0 } 1 0 。剪 切 应 变 是 引 起 轧 制 ss C 随 0 1 ( 1) 型织 构 向剪切 型织 构 转 变 的 主要 原 因 。在剪 切 应 变 作 用下 C u取 向沿 着 ≠ 一9 。 向 { 0 l 1 0 . s 向 沿着 一3 0流 0 1 ( 1) B 取 5逐
s i h w h ts e rt p e t r { 0 } 1 0 e rt es ra eo h lt e d O r tt o r sa u t s o t a h a y etx u e 0 1 ( 1 >n a h u fc ft ep aet n st o aet wad s
a d t ec n e ft ik e s y ia ol g tx u er ttst wa d h { 0 } 1 0 n h e t ro hc n s ,t p c l l n e t r o ae o r st e 0 1 ( >o in a in S e r r i 1 re tt . h a o
( ej g I si t fAe o a t a Ma eil。 ejn 0 0 5, ia B in n t u eo r n u i l i t c tras B i g 1 0 9 Ch n ) i
摘 要 : 用 电子 背散 射 衍 射 技 术研 究 了 Al n MgC 利 — — u系铝 合 金 厚 板 冷 轧 过 程 中不 厚 度 处 的织 构 演 变 。结 果 表 明 : Z 厚
铸造铝合金的织构
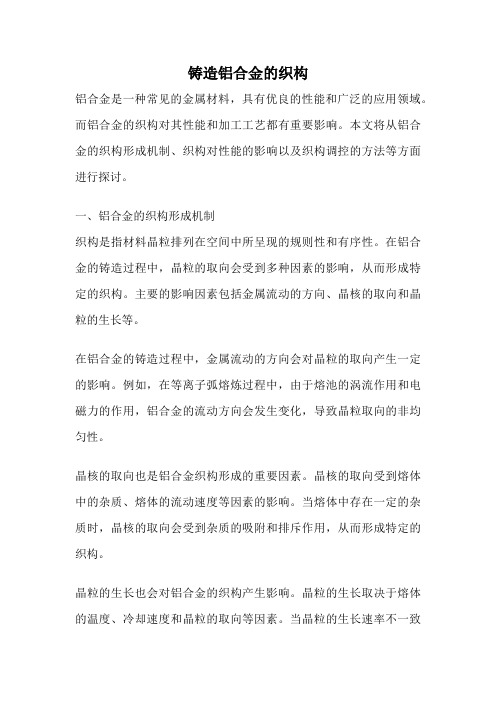
铸造铝合金的织构铝合金是一种常见的金属材料,具有优良的性能和广泛的应用领域。
而铝合金的织构对其性能和加工工艺都有重要影响。
本文将从铝合金的织构形成机制、织构对性能的影响以及织构调控的方法等方面进行探讨。
一、铝合金的织构形成机制织构是指材料晶粒排列在空间中所呈现的规则性和有序性。
在铝合金的铸造过程中,晶粒的取向会受到多种因素的影响,从而形成特定的织构。
主要的影响因素包括金属流动的方向、晶核的取向和晶粒的生长等。
在铝合金的铸造过程中,金属流动的方向会对晶粒的取向产生一定的影响。
例如,在等离子弧熔炼过程中,由于熔池的涡流作用和电磁力的作用,铝合金的流动方向会发生变化,导致晶粒取向的非均匀性。
晶核的取向也是铝合金织构形成的重要因素。
晶核的取向受到熔体中的杂质、熔体的流动速度等因素的影响。
当熔体中存在一定的杂质时,晶核的取向会受到杂质的吸附和排斥作用,从而形成特定的织构。
晶粒的生长也会对铝合金的织构产生影响。
晶粒的生长取决于熔体的温度、冷却速度和晶粒的取向等因素。
当晶粒的生长速率不一致时,会导致晶粒取向的不均匀性,从而形成特定的织构。
二、织构对性能的影响铝合金的织构对其力学性能、塑性变形行为和热处理效果等方面都有重要影响。
织构对铝合金的力学性能有显著影响。
不同的织构会导致铝合金的力学性能发生变化。
例如,具有纤维状织构的铝合金在拉伸过程中具有较高的强度和较低的延伸性,而具有等轴织构的铝合金则具有较高的延伸性和较低的强度。
织构对铝合金的塑性变形行为也有显著影响。
不同的织构会导致铝合金在塑性变形过程中的应变硬化行为发生变化。
例如,具有纤维状织构的铝合金在塑性变形过程中容易出现异性变形,而具有等轴织构的铝合金则容易出现各向同性变形。
织构对铝合金的热处理效果也有重要影响。
不同的织构会导致铝合金在热处理过程中晶粒尺寸和晶粒取向的变化。
例如,具有等轴织构的铝合金在热处理过程中容易形成较细小的晶粒,而具有纤维状织构的铝合金则容易形成较大的晶粒。
冷轧CC5052铝合金板表层至中心层织构变化的X射线衍射分析
冷轧 C C 5 0 5 2铝 合金 板 表层 至 中心层 织构 变化 的 X射线 衍 射分 析
陈明彪 , 刘文 昌 , 马 晓艺 , 李 戬 , 杨庆 祥 , 王 珊 , 马 曼 , 刘 畅 , Z h a o Y M。
1 .青海大学机械学院 , 青海 西宁 8 1 0 0 1 6 0 6 6 0 0 4
中图分类号 : TG1 3
引 言
对于热轧后冷轧 的铝合金板 , 其 厚度 方 向织构 分布的差 异影响工艺性能及使用性能 。 刘 文 昌等【 l 1 研究 5 0 5 2双履带 连续冷却铸造铝合金 板 ( C C 5 0 5 2 铝 合金板 ) 热 轧及 随后 再结
晶退火后 的织构 变化 发现 :C C 5 0 5 2铝合 金板 经过 热轧 后 , 其轧制织构主要 由 B织构 、 G o s s 织构组 成 ; 随着 轧制道次 由 1增加到 3 , 其不 同深度层 的轧制织构强度增加 ,自心部 向表 层 的织构增 强梯 度 显著 减 小 。经 过再 结 晶退 火 后 ,得 到 的 C u b e等再结 晶织构 的强度及 其沿 厚度方 向 的分布保 留 了轧 制织构 的梯度分布特点 ,但是梯度有 所增大 ; 经 3道次轧 制 后 的试样 ,再结晶退火后沿厚度方 向仍然存 在织构梯 度 ;随
铸造方法对铝合金零件织构与力学性能的影响
铸造方法对铝合金零件织构与力学性能的影响铝合金是一种广泛应用于航空、汽车、船舶等工业领域的重要结构材料。
在制造铝合金零件时,铸造方法起着至关重要的作用,对零件的织构和力学性能产生着深远的影响。
本文将探讨几种常见的铸造方法,并讨论它们对铝合金零件织构和力学性能的影响。
一、压力铸造压力铸造是一种常用的铸造方法,通过将熔化的铝合金注入金属型腔中,并施加高压力,使得铝合金迫使进入模具的细小孔隙中,从而得到具有较高密度和织构均匀的零件。
相比其他铸造方法,压力铸造能够有效降低铝合金零件的气孔率和缩松缺陷,提高其力学性能。
然而,压力铸造过程中高温、高压力的作用也会对铝合金零件的织构产生一定的影响。
研究表明,压力铸造往往会导致铝合金零件中存在沿织构流线方向形成的有序区域,这些区域的晶粒组织比较致密,强度较高;而在该方向的垂直方向上,晶粒组织则较为松散,强度较低。
因此,在设计和应用压力铸造的铝合金零件时,需要充分考虑织构对力学性能的影响,避免在强度要求较高的方向上使用零件。
二、重力铸造重力铸造是一种将熔化的铝合金通过重力力场填充到金属型腔中的铸造方法。
相比压力铸造,重力铸造的操作简单,成本较低,广泛应用于大型铝合金零件的制造。
然而,由于没有施加额外的压力,重力铸造容易产生气孔率较高的铝合金零件,这对织构和力学性能产生一定的不利影响。
为了改善重力铸造的铝合金零件织构和力学性能,研究者不断进行着努力。
例如,采用精细化的熔化处理和特殊的浇注系统,能够有效降低铝合金零件的气孔率。
同时,在铝合金的配方设计和处理工艺上,也可以通过添加特定的合金元素或者合理选择热处理条件,来调控铝合金的织构和力学性能。
三、连续铸造连续铸造是一种将熔化的铝合金通过连续浇注的方式,制造出长条状的铝合金材料或型材的铸造方法。
相比其他铸造方法,连续铸造具有生产效率高、材料利用率高等特点,广泛应用于铝合金材料的生产。
然而,连续铸造对铝合金零件的织构和力学性能还存在一定的挑战。
汽车用6111铝合金板材力学性能和织构研究
汽车用6111铝合金板材力学性能和织构研究近年来,随着汽车制造技术的进步,汽车制造的重点逐渐从传统的机械制造转向了高强度、低成本、轻量化和无损金属材料的利用,6111铝合金因其具有优异的力学性能等众多优点而被广泛应用于汽车制造行业。
因此,本文旨在通过对6111铝合金板材的力学性能和织构研究,以探讨汽车行业中6111铝合金板材的应用前景。
1、6111铝合金板材的结构与力学性能6111铝合金板材是一种合金铝板材,由铝、镁、硅、铬和其它微量元素组成,具有优异的力学性能。
它具有良好的塑性和延展性,在低温时可以抵抗腐蚀,耐用,耐高温,耐腐蚀和经久耐用。
此外,6111铝合金板材的抗拉强度和屈服强度比传统的6061铝合金板材更高,其延展率更高。
2、6111铝合金板材的制备工艺6111铝合金板材可以通过压延法、变形法和冶炼法等多种方法制备,其制备方法有些许不同。
一般来说,以6111铝合金为原料的板材,其制备方法主要有铸造法、压延法和变形法。
(1)铸造法:铸造法是以6111铝合金坯料为原料,经熔炼和浇注成型,最后经冷却、退火等工艺加工而成的变形加工方法,可以有效地制备高密度的6111铝合金板材。
(2)压延法:压延法是以6111铝合金坯料作为原料,经热处理、扩口、压延、退火等工序进行制备,可以有效地制备低厚度6111铝合金板材。
(3)变形法:变形法是以6111铝合金坯料为原料,经热处理、定量变形、退火等工艺进行制备,能够制备出较厚的6111铝合金板材。
3、6111铝合金板材的应用6111铝合金板材通过其优良的力学性能,应用于汽车制造行业十分广泛,其中最常见的应用有汽车车身、汽车引擎盖、汽车轮毂、汽车车身支架等,并广泛应用于汽车内轮廓及外观设计,可以满足汽车制造行业的加工要求。
4、总结本文通过对6111铝合金板材的力学性能和织构研究,发现其具有优异的力学性能和良好的塑性与延展性,能够满足汽车制造行业的需求,且在汽车制造行业中有着广泛的应用。
现代化背景下不同润滑条件下高纯铝的冷轧织构及组织分析
现代化背景下不同润滑条件下高纯铝的冷轧织构及组织分析摘要该文实现了TEM法与晶体取向分布函数法的结合,进行了不同润滑条件下高纯铝冷轧织构及组织状况的分析。
在冷軋变形基础上进行机油润滑模式的分析,冷轧织构由B- 、Cu及S-织构组分构成,这三者取向分布的密度峰值均处于S-取向位置。
其冷轧箔组织结构呈现均匀性的特点,不存在立方取向亚晶问题。
在煤油润滑环境下,其轧制织构比较薄弱,出现了{001}剪切织构,在煤油润滑冷轧箔过程中,不存在立方取向亚晶及剪切带状况。
关键词润滑条件;高纯铝冷轧织构及组织;TEM法前言立方织构的比例、立方织构含量等因素决定了电熔铝箔的质量,如果前两者的比例及含量较大,电熔铝箔会得到较大的比电容。
在这个过程中,立方织构的比例受到铝中微量杂质含量、铝箔生产工艺参数等的影响。
冷轧润滑直接影响着铝箔轧制的织构及相关组织,从而影响到成品的立方织构水平。
在不同润滑条件下高纯铝的冷轧织构及组织亦存在相应的变化情况。
1 实验方法下文研究了煤油、机油对高纯铝冷轧组织及织构的影响。
为了明确不同润滑环境下冷轧过程中织构及组织的形成及发展状况,必须进行金属宏观变形特点及晶体取向状况的分析,这需要将高纯原铝放在真空高频感应炉中进行熔炼。
在氧化锌涂层铁模中铸成一定长度、宽度、高度的长方体锭[1],其具体的化学成分状况如下表1。
在实验研究过程中,为了进行TEM组织分析及ODF技术检测,需要将0.11mm厚的冷轧箔作为样品。
在试验环节中,需要用腐蚀法去除冷轧箔试样的表面层,从而实现极图检测工作的开展。
为了进行鬼峰效应的消除,需要利用高斯正态分布函数模型,进行级数奇数项的计算,得出真ODF。
2 实验结果分析图1为0.11mm厚冷轧铝箔的α-取向线、β-取向线、CubeND取向线分析图,图中的字母A代表机油润滑条件下f(g)即晶粒取向密度沿三取向线的分布状况,字母B代表煤油润滑条件下f(g)沿三取向线的分布状况,从下图1中看出,样品经过润滑冷轧变形后,{011}B-、{112}Cu-及{123}S-取向密度值都很高,S-位置存在f (g)的最大值,{011} G-组分的f (g)值很低,Rot. Cube-组分的f(g)值几乎为零。
- 1、下载文档前请自行甄别文档内容的完整性,平台不提供额外的编辑、内容补充、找答案等附加服务。
- 2、"仅部分预览"的文档,不可在线预览部分如存在完整性等问题,可反馈申请退款(可完整预览的文档不适用该条件!)。
- 3、如文档侵犯您的权益,请联系客服反馈,我们会尽快为您处理(人工客服工作时间:9:00-18:30)。
1.1 晶体取向与织构——晶体取向
➢晶体取向
➢晶体取向
1.1 晶体取向与织构——晶体取向
➢晶体取向
1.1 晶体取向与织构——晶体取向
➢晶体取向
1.1 晶体取向与织构——晶体取向
➢晶体取向
1.1 晶体取向与织构——晶体取向
➢晶体取向:从样品(参考坐标系)到晶体坐标系的旋转。
✓样品/参考坐标系的坐 标轴一般为样品对称轴( 轧向RD、横向TD和板 法向ND);
S3 C3
C3
S3
gij ci s j
✓晶体坐标系坐标轴一 般为低指数晶向(立方
晶胞中共顶点的三条棱 边[100]、[010]和[001])
ND s3 001 c3 s1RD
C1 c2 010
S2 C2
M l
1 2l
1
ml
Cl
1.1 晶体取向与织构——多晶体材料织构
➢ 金属材料的加工过程中都有可能会影响织构的形成和演变。
✓铸造织构:传热最快的晶体学方向与结晶器散热最快的方向一致形成特 定的晶体学织构,定向凝固。
定向凝固组织
定向凝固涡扇发动机叶片
1.1 晶体取向与织构——多晶体材料织构
σc gσsgT
1.1 晶体取向与织构——晶体取向
➢米勒指数表示晶体取向(hkl)[uvw]。 (hkl)晶体学面平行轧制面,[uvw]晶体学方向平行轧制方向。
[uvw]RD TD ND(hkl)
g11 g12
g21
g22
g31 g32
归一化处理: H2+K2+L2=M2, U2+V2+W2=N2 S1┴S3: H*U+K*V+L*W=0 6个参数中有冗余参数(不需要6个参数就可以表示取向)
001 c3
c2
s1RD
010
TD s2
100 c1
R1S R2S
g11 g21
g12 g22
g13 g23
R1C R2C
R3S g31 g32 g33 R3C
RS g RC
c ij
gik
s kl
g
jl
[010]
2nd position
ycrystal=e2’’’ 1st position
e”2
e’2 e2=Ysample=TD
xcrystal=e1’’’ [100]
TD
F e’1=e”1
Sample Axes
e1=Xsample=RD
1.1 晶体取向与织构——多晶体材料织构
➢ 多晶体材料晶体取向分布偏离随机分布(经常是择优取向) 的状态称为晶体学织构。
取向分布函数(Orientation Distribution Function,ODF)定量描述织构。
dV f(g)dg V
单晶体各向异性:
M g mlT&&&l g l
f g ClT&&&l g l
多晶体材料性能:
1
培训主要内容
一、织构基础知识(6学时)
1.1 晶体取向与织构 1.2 织构的测算与表征 1.3典型铝板带产品对织构的要求
二、铝合金织构的形成与演变(6学时)
2.1 形变织构及其演变 2.2 再结晶织构及其演变 2.3 铝合金织构调控的技术途径
三、典型铝合金织构调控实例(4学时)
第一讲 织构基础知识
g13
g
23
g33
1.1 晶体取向与织构——晶体取向
➢Bunge欧拉角(φ1,Φ,φ2)表示晶体取向。 通过3个连续的旋转实现从样品坐标系到晶体坐标系的旋转。
[001]
e’3= e3=Zsample=ND
zcrystal=e3’’’ e”3 =
f1
f2
Crystal RD
3rd position (final)
S1
C2 g11
S2
g
21
C1
g31
g12 g22 g32
g13
g23
g33
c1 c2 c3
s1 s2 s3
TD s2
100 c1
➢晶体取向:晶 胞堆砌成晶体/晶
粒的方式。
1.1 晶体取向与织构——晶体取向
➢晶体取向矩阵把晶体各向异性与样品各向异性关联起来。
ND s3
• 极射赤面投影图(简称为极图)。
ND
100 001
010
ND
RD
βi
100
001
αi
001
1.2 织构的测算与表征
• 极射赤面投影图。
1.2 织构的测算与表征
• 极射赤面投影图可以表示晶体取向。
1.2 织构的测算与表征
• 采用织构多晶体衍射仪测试的多晶体材料极密度分布函数图 (简称为极图)经常被用来表征织构。
j2 j1
F
在二维的纸平面无法精确表示三维取向分布函数(ODF)。
铝合金织构通常采用φ2截 面图来表征取向分布函 数(ODF)。
1.2 织构的测算与表征
1: ϕ1 59° φ 37° ϕ2 63° 2: ϕ1 26° φ 58° ϕ2 19° 3: ϕ1 53° φ 74° ϕ2 34°
1.2 织构的测算与表征
✓形变织构:大变形造成的晶体转动,与纤维组织(由于晶粒形状导致各 向异性)不同。
冷变形纤维组织:晶 粒被拉长成长条状
取向A
取向B
取向C
取向D
冷变形织构:较多的晶粒内单胞采用特定方式堆砌。
✓再结晶织构:择优形核和择优长大。
1.2 织构的测算与表征
• 织构通常采用三维取向分布函数(ODF,f(g)=f(φ1,Φ,φ2)) 的图形来描述。
n 2d sin
a dhkl h 2 k2 l2
[100]//RD
b.作直线OP平行与待标志 的晶向或待标定晶向的直 线通过坐标原点
c.确定通过原点直线上任 一点的坐标值
d.将坐标值化为最小整数 并加上方括号[UVW]
1.1 晶体取向与织构——晶体学基础
➢晶体学面与晶面指数
① 建立坐标系 ② 确定晶面在各坐标轴上的 截距 ③ 取截距的倒数,并通分, 化为最小的简单整数 (hkl)
1.1 晶体取向与织构——晶体学基础
➢晶体是由具有特定晶体结构的单胞堆砌而成。
➢铝单胞晶体结构是面 心立方(FCC)结构。 ➢不同方向、不同面上 的原子排列不一样, 表现各向异性。
1.1 晶体取向与织构——晶体学基础
➢晶体学方向与晶向指数
a.建立坐标系,以某一阵点 为原点O,以三个基矢为坐 标轴,以晶胞边长作为坐标 轴的长度单位