高速旋转轮盘模态分析
高速旋转轴系的扭振模态实验研究

高速旋转轴系的扭振模态实验研究1 引言对于旋转机械,扭转振动是广泛存在的,而对高速旋转机械来说,这种现象也更加明显。
现在广泛使用的扭振测量方法有相位差法、激光多普勒测扭法以及脉冲时序法,这些方法有一个共同点,就是要求待测轴上已经安装有分度结构或者有足够空间用于安装测量齿盘[1]。
而在高速旋转机械中,旋转轴往往在非常复杂的工况下运行,例如充满润滑油的变速齿轮箱,在这种高温复杂并且充满干扰的环境下是不可能用传统方法进行测量的,无论是定位元件的安装以及传感器的抗干扰性都很难保障。
虽然脉冲时序法克服了齿盘分度不均匀的影响,测量精度也较高,但是这种方法对待测轴系有严格的要求:轴的长度必须具有一定跨度来安装多个传感器;并且轴上必须安装有轮盘或者有足够的空间可以安装轮盘[2]。
对于本论文中待测的传动轴来说,大部分轴段是在密封环境中使用的,而暴露在外的轴段没有足够空间安装分度轮盘,这个时候就需要改进测试方法,选用更加节省空间的测试方法。
结合上文的介绍,本论文采用了试验台对旋转轴的扭振特性进行研究,在传感器方面,选用了美国ATI 公司的2000 系列遥测扭振传感器,一方面考虑到它的无线信号传送的优点,既传感器测得的信号不需要线材就可以很好的被接收器接收。
这样不仅很好的解决了测量高速旋转轴扭振时信号线难的问题,同时也避免了传统脉冲时序法对轴系形式有特定要求的弊端。
另一方面,因为该传感器采用了对称布置的双加速度传感器结构,所以很好消除了重力以及径向加速度的影响。
在试验中,利用现有高速旋转试验平台,用试验的方法得到了待测轴的扭振一阶固有频率,同时,利用Ansys 仿真软件计算出待测轴的模态参数,通过和实验数据的对比,证明了扭振测试系统的准确性和可靠性。
2 扭转振动测试系统扭振测试部分主要对被测旋转轴的扭转振动加速度参数进行测量。
示的是ATI 扭振传感器安装实物图:为保证扭振测试装置能够方便的安装、调整,整个测试装置设置在具有T 型滑动槽的工作平台上,同时,各传感器组件以及支架都可以方便的进行横向和纵向的位置调整,已获得更大的灵活性并满足不同传感器的安装位置要求。
高速动车组车轴的轮轴系统动力学建模

高速动车组车轴的轮轴系统动力学建模随着交通运输业的发展,高速动车组的运营和使用已经成为现代城市化的重要组成部分。
在高速动车组中,车轴的轮轴系统是非常重要的组件之一,它承载了整个车辆的重量,同时还需要满足高速行驶的稳定性和安全性要求。
因此,对于高速动车组车轴的轮轴系统动力学进行建模和分析是非常必要的。
在建立高速动车组车轴的轮轴系统动力学模型时,需要考虑以下几个方面的因素。
首先,需要考虑车轴的运动学特性。
车轴一般由多个车轮组成,车轮在车轴上的安装位置和转动轴心位置是影响车轴整体运动学特性的重要因素。
通过测量和计算车轮的位置和转动轴心的位置,可以得到车轴的运动学特性。
其次,需要考虑车轴的弯曲变形和振动特性。
在高速行驶过程中,车轮承受着来自地面的垂直载荷和横向载荷,这些载荷会导致车轴发生弯曲变形和振动。
为了准确描述车轴的弯曲变形和振动特性,可以使用弹性力学理论进行建模,并结合实测数据进行校准。
另外,还需要考虑车轴的轮轴系统动力学特性。
车轴的运动和振动是由诸多因素共同决定的,包括轮轴的刚度、阻尼特性和质量分布等。
在建立轮轴系统模型时,可以将轮轴视为弹簧-阻尼系统,通过将车轴的弯曲变形和振动特性与轮轴的动力学特性相耦合,可以得到完整的轮轴系统动力学模型。
此外,还需要考虑动车组的整车动力学特性对车轴的影响。
动车组在高速行驶过程中产生的横向力、纵向力和附着力等载荷都会影响车轴的运动和振动特性。
因此,在建立车轴的轮轴系统动力学模型时,需要结合动车组的整车动力学模型,将动车组的运动和振动特性与轮轴的动力学特性相耦合,得到全面的车轴系统动力学模型。
综上所述,对于高速动车组车轴的轮轴系统动力学建模,需要考虑车轴的运动学特性、弯曲变形和振动特性、轮轴系统的动力学特性,以及动车组的整车动力学特性。
通过建立准确的动力学模型,可以对高速动车组车轴的工作状态进行分析,为车辆的设计和运营提供科学依据。
然而,其他因素如车轨异物检测、防破坏措施和系统安全参数设置也需要进行进一步研究,以提高高速动车组车轴的轮轴系统的稳定性和安全性。
高速旋转机械系统动力学特性分析与改进

高速旋转机械系统动力学特性分析与改进一、引言随着工业化进程的不断推进,高速旋转机械系统在现代工程中发挥着越来越重要的作用。
然而,高速旋转机械系统的动力学特性对系统的性能和稳定性有着重要影响。
因此,对高速旋转机械系统的动力学特性进行分析和改进是非常必要的。
二、动力学特性分析高速旋转机械系统的动力学特性主要包括振动现象、稳定性以及共振等问题。
1. 振动现象高速旋转机械系统在运行过程中会出现不可避免的振动现象。
这种振动不仅会降低系统的工作效率,还会对机械部件造成损伤。
因此,对振动进行分析和控制是非常重要的。
2. 稳定性高速旋转机械系统的稳定性是指系统在工作过程中是否能保持平衡状态。
若系统不稳定,会导致系统振荡甚至失衡,进而使整个系统运行不正常。
因此,对稳定性进行分析和改进对于系统的正常运行具有重要意义。
3. 共振共振是指机械系统在某个或某些特定频率下发生振动时,受到的外界激励与机械系统自身固有频率产生共振现象。
共振现象会加剧机械系统的振动幅度,甚至造成系统的破坏。
因此,对共振进行分析和控制是必不可少的。
三、改进方法针对高速旋转机械系统的动力学特性问题,可以采取以下改进方法。
1. 结构设计改进通过优化结构设计,可以降低振动噪声和提高系统稳定性。
例如,增加机械部件的刚度、减小质量偏心和采用阻尼材料等方式可以有效改善系统的动力学特性。
2. 润滑改进适当的润滑可以减少机械系统的摩擦和磨损,降低振动噪声和能量损失。
选择合适的润滑方式和润滑剂,优化润滑系统的设计,可以有效改善机械系统的动力学特性。
3. 控制系统改进优化控制系统的设计,如采用反馈控制、模糊控制和自适应控制等方法,可以提高系统的稳定性和抗干扰能力。
同时,合理设置控制参数和控制模式,可以减小系统的共振现象,降低振动的影响。
4. 材料选用改进选择合适的材料可以改善机械系统的动力学特性。
例如,选用高强度、高硬度和低密度的材料,可以提高系统的刚度和耐磨性,减小振动和疲劳损伤。
旋转机械的固有振动模态分析

旋转机械的固有振动模态分析旋转机械是指转子在运行过程中产生旋转运动的机械设备,如发动机、泵、电机等。
由于旋转机械的工作环境和工作方式的不同,其内部会存在各种振动模式,这些振动模态的研究对于机械的设计和维护至关重要。
首先,我们需要了解什么是固有振动模态。
固有振动模态指的是物体在没有受到外力作用时,仅由于其结构形状和材料特性而产生的自由振动形式。
旋转机械的固有振动模态分析可以帮助我们了解机械的振动特性,进而判断机械是否存在结构强度不足、材料疲劳等问题。
旋转机械的固有振动模态分析通常通过模态分析方法来进行。
模态分析是指通过求解机械系统的动力学方程,得到机械系统的固有频率和振型。
常用的模态分析方法有有限元法、边界元法等。
在进行固有振动模态分析之前,我们首先需要建立旋转机械的运动模型。
对于简单的旋转机械,可以将其简化为质点和弹簧系统。
通过建立旋转机械的动力学方程,可以得到机械系统的固有频率和振型。
在实际的固有振动模态分析中,我们需要进行数值计算。
通过将机械系统建立为有限元模型,利用有限元分析软件进行计算,可以得到机械系统的固有频率和振型。
在进行有限元计算时,需要注意选择合适的网格划分和元素类型,以保证计算结果的准确性。
通过固有振动模态分析,我们可以得到机械系统的固有频率和振型。
固有频率是指机械系统在自由振动时的振动频率,其大小与机械系统结构和材料特性有关。
振型则是机械系统在自由振动时的形变形式,可以揭示机械系统的振动分布情况。
对于旋转机械而言,其固有振动模态分析还可以帮助我们了解机械系统在不同转速下的振动特性。
通过改变转速,我们可以观察机械系统固有频率的变化。
如果存在与机械系统转速相匹配的固有频率,则可能产生共振现象,导致机械系统的振动增大,甚至引发破坏。
除了固有振动模态分析,我们还可以通过实验手段来研究旋转机械的振动特性。
利用振动传感器和数据采集系统,我们可以获取机械系统的振动数据,并对其进行分析。
通过实验和分析,可以验证模态分析的结果,并进一步了解机械系统的振动特性。
高速动车组车轴的模态分析与优化设计
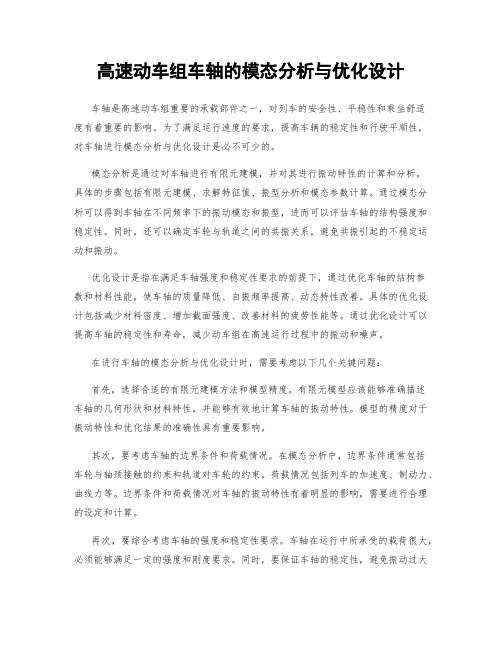
高速动车组车轴的模态分析与优化设计车轴是高速动车组重要的承载部件之一,对列车的安全性、平稳性和乘坐舒适度有着重要的影响。
为了满足运行速度的要求,提高车辆的稳定性和行驶平顺性,对车轴进行模态分析与优化设计是必不可少的。
模态分析是通过对车轴进行有限元建模,并对其进行振动特性的计算和分析。
具体的步骤包括有限元建模、求解特征值、振型分析和模态参数计算。
通过模态分析可以得到车轴在不同频率下的振动模态和振型,进而可以评估车轴的结构强度和稳定性。
同时,还可以确定车轮与轨道之间的共振关系,避免共振引起的不稳定运动和振动。
优化设计是指在满足车轴强度和稳定性要求的前提下,通过优化车轴的结构参数和材料性能,使车轴的质量降低、自振频率提高、动态特性改善。
具体的优化设计包括减少材料密度、增加截面强度、改善材料的疲劳性能等。
通过优化设计可以提高车轴的稳定性和寿命,减少动车组在高速运行过程中的振动和噪声。
在进行车轴的模态分析与优化设计时,需要考虑以下几个关键问题:首先,选择合适的有限元建模方法和模型精度。
有限元模型应该能够准确描述车轴的几何形状和材料特性,并能够有效地计算车轴的振动特性。
模型的精度对于振动特性和优化结果的准确性具有重要影响。
其次,要考虑车轴的边界条件和荷载情况。
在模态分析中,边界条件通常包括车轮与轴颈接触的约束和轨道对车轮的约束。
荷载情况包括列车的加速度、制动力、曲线力等。
边界条件和荷载情况对车轴的振动特性有着明显的影响,需要进行合理的设定和计算。
再次,要综合考虑车轴的强度和稳定性要求。
车轴在运行中所承受的载荷很大,必须能够满足一定的强度和刚度要求。
同时,要保证车轴的稳定性,避免振动过大和失稳引起的事故。
在进行优化设计时,要权衡车轴的强度和稳定性,保证两者的兼顾。
最后,要考虑车轴的制造和维修工艺。
车轴作为高速动车组的重要组成部分,其制造工艺和维修工艺对于车轴的质量和寿命具有重要影响。
在进行优化设计时,要考虑工艺的可行性,确保设计方案可以被有效地制造和维修。
高速卷绕机卡盘轴模态分析

高速卷绕机卡盘轴模态分析以高速卷绕机卡盘轴为研究对象,利用SoildWorks建立卡盘轴三维模型,对卡盘轴进行试验模态分析和利用workbench理论模态分析,得到卡盘轴固有频率和模态振型结果,两者对比验证,误差在允许范围内,验证建立三维模型正确。
然后对卡盘轴主要构件套筒、传动轴、支撑套筒利用workbench进行模态分析,得出它们固有频率对卡盘轴的影响,为提高卡盘轴工作效率和优化结构提供理论依据。
标签:模态分析;卡盘轴;模态频率;模态振型0 引言高速卷绕机是生产化纤核心设备,随着科技进步和化纤需求增加,高速卷绕机向高速化方向发展[1]。
卡盘轴作为高速卷绕机重要部件直接影响着卷绕质量和效率。
据统计,转子故障在旋转机械故障中占总数的70%以上[2]。
为降低故障发生可能性,研究卡盘轴及其各个构件的动力学特性,对卡盘轴结构优化和性能提高具有重要意义。
董少伟在对卡盘轴模态分析时,得到卡盘轴振动最大在悬臂端[3];赵军等研究了卡盘轴自由状态和约束状态下的盘轴动态特性[4]。
目前还没有对主要构件模态分析研究卡盘轴动力学特性。
本文对高速卷绕机卡盘轴进行实验模态分析和利用ANSYS workbench进行理论模态分析,对两者得到的固有频率和模态振型进行对比验证,证明建立模型的正确性,然后进行套筒、传动轴、支撑套筒模态分析,得出套筒、传动轴、支撑套筒固有频率对卡盘轴的影响,为优化卡盘轴结构参数提供理论依据。
1 模态分析理论模态分析是以振动理论为基础,以模态参数(固有频率、模态振型、阻尼比)为目标的分析方法。
模态分析方法分为理论模态分析法和实验模态分析法[5]。
其运动微分方程为:式中求得和。
是特征值代表第i阶所求的的固有频率,它是由质量矩阵和刚度矩阵决定。
是特征向量表示构建的模态振型[6]。
2 Workbench模态分析2.1 模型建立高速卷绕机卡盘轴主要由传动轴结合件、支撑套筒结合件、套筒组成如a图,利用SolidWorks建立卡盘轴装配体模型。
高速旋转状态下齿轮轴系耦合的模态分析
结构或机械传动部件 的固有频率 , 使设计人员可以避
开这些频率或最大限度减少对这些频率 的激励 , 从而 消除过度振 动或 噪声 , 提高齿 轮箱 的寿命 和工 作 环 境 。 目前大多数学者 主要 研 究 了齿 轮装 配 体模 态 l
每一 时步 , 比 Q 对 面 上物 体 A、 B的坐 标或 对 比速 率来 实 现 位 移
协调 条件 。 U 一
=
式 中 : , 分别 为齿轮 系统 质 量矩 阵 、 C, 阻尼 矩 阵和 刚度 矩阵 ;X , X 分 别 为齿 轮 系统 振 动 加 速 度 向 X,
半 收稿 日期 :O 2 o — O 2 1 一 7 1
作者简 介 : 胡瑞 帆 (9 9 ) 男 , 18 一 , 江西 鄱 阳人 , 在读硕 士 , 研究方 向 : 轮 齿
・
8 ・ 2
・
机 械 研 究 与 应 用 ・ 0 年 期( 第1 期) 2 2 第4 总 2 1 0
nQ。 由 于 两 物 体 不 ,
动 时轮齿 之 间相互 接 触 , 即为 一 种 约束 关 系 , 且这 而 种 约束关 系 随时 间变 化 , 这是 由于啮合 部位 和接触 面
积 是 随时 问 变化 所造 成 的 , 即 K为 时变 , 就是说 也 也
图 4 ቤተ መጻሕፍቲ ባይዱ 触 算 法 示 意 图
齿 轮传 动 系统并 不存 在一个 确定 的固有频率 , 与传 这 统 的线 性模 态分 析 理 论 相悖 。装 配体 的模态 分 析 是
() 5
其 对应 的特征值 方程 为 :
( 一 )iO X= () 4 式 中 : ∞ 为第 i 阶模 态 的 固有 频 率 i , … , 。这 =12, n
高速旋转状态下汽车弧齿锥齿轮的动力学模态分析
高速旋转状态下汽车弧齿锥齿轮的动力学模态分析王犇;华林【摘要】在Pro/E和ANSYS软件环境下,分别建立了汽车主减速器弧齿锥齿轮的三维几何模型和动力学模态分析有限元模型,进而对静止状态和高速旋转状态下的齿轮进行了模态分析,得到了各阶固有频率和振型.结果表明,在高速旋转状态下,齿轮由于离心弹性变形而产生"离心刚化效应",从而改变了齿轮的模态特性:随着转速的增加,轮齿离心弹性变形量和各阶固有频率均增大,且某些振型也与静止状态下的不同.%The 3D geometric model and FE model for dynamic modal analysis of automotive spiral bevel gears are established with software Pro/E and ANSYS respectively.Then modal analyses on gears in both static state and high-speed rotation state are performed and the natural frequencies and the mode shapes in different orders are obtained.The results show that in high-speed rotation state, the centrifugal stiffening effect occurs due to the centrifugal elastic deformation of gear teeth, leading to the change in modal characteristics of gears.With the rise of rotational speed, the centrifugal elastic deformation of gear teeth and the natural frequency of gears in different orders increase and some of the mode shapes differ from that in static state.【期刊名称】《汽车工程》【年(卷),期】2011(033)005【总页数】5页(P447-451)【关键词】弧齿锥齿轮;高速旋转;模态特性;固有频率;振型【作者】王犇;华林【作者单位】武汉理工大学材料科学与工程学院,武汉,430070;武汉理工大学材料科学与工程学院,武汉,430070【正文语种】中文前言弧齿锥齿轮因具有传动平稳、效率高、承载能力强和噪声低等优点,已在汽车、航空航天、石油和化工等诸多领域中代替直齿锥齿轮实现相交轴间的运动传递。
基于高速旋转齿轮的有限元分析论文
基于高速旋转齿轮的有限元分析引言:齿轮泵是工程中较为常见的一种泵,在高速运转时齿轮受到多种力的作用,包括齿面受到的压力,啮合时的接触应力以及自身离心力。
在此过程中,齿轮将发生形变,为此我们需要对其进行分析,确保其结构的稳定性,这对于齿轮泵安全有效地运行具有很重要的意义。
关键词:高速齿轮、平面静力分析、接触应力分析、离心力分析一、分析对象这里我们分析的对象是齿轮泵中高速运转的齿轮,在ANSY防我们建立了标准齿轮模型,其各项数据如下表所示表齿轮泵咼速齿轮参数二、平面静力分析1、分析问题为了考查齿轮泵在高速运转时,齿轮发生多大的径向位移,从而判断其变形情况,以及齿轮运转过程齿面受到的压力作用。
在这里我们将齿轮的空间结构简化为平面模型,并分析其平面应力情况。
此处的静力分析为线性静力分析,求解步骤分为建模、施加载荷和边界条件并求解、结果分析和评价三个步骤,下面依序进行。
2、建立模型2.1 定义单元类型根据齿轮的平面几何对称性和此处分析类型,我们选择四节点矩形单元PLANE42 PLANE42不仅可以用于计算平面应力问题,还可以用于分析平面应变和轴对称问题。
每个节点2个自由度:x,y方向。
具有塑性,徐变,膨胀,应力强化,大变形,大应变能力。
设定好单元类型后,对选择的PLANE42^元进行设置,在Element behavior (单元行为方式)选择Pla ne stress w/wk 。
2.2 定义实常数本处选用带有厚度的平面应力行为方式的PLANE 42单元,需要设置器厚度实常数,只需在“ Type1 PLANE 42中将厚度设为4即可。
2.3 定义材料属性考虑惯性力的静力分析中必须定义材料的弹性模量和密度。
2.4 建立齿轮面模型,如下图所示图2建立齿轮面模型2.5对盘面划分网格选择Main Menu: Preprocessor>Meshing>Meshing Tool(网格工具)命令, 然后单击Line域选择所有线条(Pick All), 之后用线控制单元网格划分,在No.of element division(划分单元的份数)中输入10,表示所有线条被划分为10 份。
高速长轴转子振动的模态分析
高速长轴转子振动的模态分析程道来;高相龙;纪林章;仪垂杰【摘要】When debugging the high speed test bench, it is found that the rotor reaches the first critical speed, there is a problem that the vibration is too large to risespeed.After consulting the relevant literature at home and abroad,the idea and scheme of reducing abnormal vibration based on ANSYS finite element method and experimental method are proposed. First use ANSYS to test rig rotor modeling to get the first, second, third modes in different eccentric; and the experimental debugging, vibration testing, test rotor in eccentric, first-order critical speed and 10000r/min three different conditions vibration amplitude and spectrum. After two methods comparative analysis obtained: the amplitude of the rotor surgein the critical speed,amplitude retention after the critical speedand when rotor drop speed in the critical speed,the critical speed value offset.the three issue in the main reason for the experimental platform with the supporting table and installation caused, security problem been solved in the experimental bench rotor test will be due to excessive vibration may bring to the students.%在调试高速实验台时发现:当转子达到第一阶临界转速时出现振动过大导致转速升不上去等问题.经过查阅国内外相关文献,提出了基于ANSYS有限元法和实验法的减少异常振动的思路和方案.首先利用ANSYS软件对实验台转子建模,获得在偏心不同情况下的一、二、三阶模态;再对实验台调试、振动测试,得到实验台转子在偏心、一阶临界转速和10000r/min三种不同工况下振动幅值和频谱.经过两种方法比较分析得出:出现实验台过临界转速时转子振幅激增、过临界转速后振幅滞留和转子降速过临界转速时临界转速值偏移这三大问题的主要原因是转子上的圆盘偏心过大所引起的,解决了在实验台转子试验时会因振动过大可能会对学生带来的安全问题.【期刊名称】《机械设计与制造》【年(卷),期】2018(000)005【总页数】3页(P229-231)【关键词】ANSYS;高速长轴;模态分析;偏心【作者】程道来;高相龙;纪林章;仪垂杰【作者单位】上海应用技术大学轨道交通学院,上海201418;上海应用技术大学机械工程学院,上海201418;上海应用技术大学机械工程学院,上海201418;青岛理工大学能源与动力装备研究发展中心,山东青岛266033【正文语种】中文【中图分类】TH161 引言对购买的某转速高达10000r/min转子实验台在给学生做试验前进行了升、降速完整振动特性调试出现在逐渐升速过程中,实验台及转子振动越来越大,当转子转速接近临界转速时,振动非常剧烈,过第一阶临界转速时,振动依然非常剧烈,直到转子超过临界转速600r/min后,振动骤然下降为正常的振动;继续升速,当转子升速到10000r/min接近电机最高转速时,振动明显加,然后降速,振动逐渐恢复到正常状态。
- 1、下载文档前请自行甄别文档内容的完整性,平台不提供额外的编辑、内容补充、找答案等附加服务。
- 2、"仅部分预览"的文档,不可在线预览部分如存在完整性等问题,可反馈申请退款(可完整预览的文档不适用该条件!)。
- 3、如文档侵犯您的权益,请联系客服反馈,我们会尽快为您处理(人工客服工作时间:9:00-18:30)。
高速旋转轮盘模态分析在进行高速旋转机械的转子系统动力设计时,需要对转动部件进行模态分析,求解出其固有频率和相应的模态振型。
通过合理的设计使其工作转速尽量远离转子系统的固有频率。
而对于高速部件,工作时由于受到离心力的影响,其固有频率跟静止时相比会有一定的变化。
为此,在进行模态分析时需要考虑离心力的影响。
通过该实验掌握如何用ANSYS进行有预应力的结构的模态分析。
一.问题描述本实验是对某高速旋转轮盘进行考虑离心载荷引起的预应力的模态分析,求解出该轮盘的前5阶固有频率及其对应的模态振型。
轮盘截面形状如图所示,该轮盘安装在某转轴上以12000转/分的速度高速旋转。
相关参数为:弹性模量EX=2.1E5Mpa,泊松比PRXY=0.3,密度DENS=7.8E-9Tn/mm 3。
1-5关键点坐标:1(-10, 150, 0)2(-10, 140, 0)3(-3, 140, 0)4(-4, 55, 0)5(-15, 40, 0)L=10+(学号×0.1)RS=5二.分析具体步骤1.定义工作名、工作标题、过滤参数①定义工作名:Utility menu > File > Jobname②工作标题:Utility menu > File > Change Title(个人学号)2.选择单元类型本实验将选用六面体结构实体单元来分析,但在建模过程中需要使用四边形平面单元,所有需要定义两种单元类型:PLANE42和SOLID45,具体操作如下:Main Menu >Preprocessor > Element Type > Add/Edit/Delete①“ Structural Solid”→“ Quad 4node 42” →Apply(添加PLANE42为1号单元)②“ Structural Solid”→“brick 8node 45” →ok(添加六面体单元SOLID45为2号单元)在Element Types (单元类型定义)对话框的列表框中将会列出刚定义的两种单元类型:PLANE42、SOLID45,关闭Element Types (单元类型定义)对话框,完成单元类型的定义。
3.设置材料属性由于要进行的是考虑离心力引起的预应力作用下的轮盘的模态分析,材料的弹性模量EX 和密度DENS必须定义。
①定义材料的弹性模量EXMain Menu >Preprocessor > Material Props > Material Models> Structural > Linear >Elastic >Isotropic弹性模量EX=2.1E5泊松比PRXY=0.3②定义材料的密度DENSMain Menu >Preprocessor > Material Props > Material Models>densityDENS =7.8E-94.实体建模对于本实例的有限元模型,首先需要建立轮盘的截面几何模型,然后对其进行网格划分,最后通过截面的有限元网格扫描出整个轮盘的有限元模型。
具体的操作过程如下。
①创建关键点操作:Main Menu > Preprocessor > Modeling > Create > Keypoints > In Active CS 列出各点坐标值Utility menu >List > Keypoints >Coordinate only②由关键点生成线的操作:Main Menu > Preprocessor > Modeling > Create > Lines > Lines > In Active Coord③建立圆角:Preprocessor > Modeling > Create > Lines > Lines > Lines Fillet④生成面:Main Menu > Preprocessor > Modeling > Create >Areas >Arbitrary >By Lines(逆时针选线)1 2 3 4 5 13 14 15 168910 11 12 Y5.划分网络Main Menu >Preprocessor >Meshing >MeshTool①对全局进行设置。
单击Size Controls (尺寸控制区)全局设置项(Global)的Set 按钮,将弹出Global Element Sizes 单元尺寸全局设置对话框在对话框中输入Element edge Length (单元边长度)为6。
②单击Size Controls (尺寸控制区) Lines (线设置项)的按钮,将弹出Element Size on Picked Lines (在所选线上定义单元尺寸)的拾取对话框。
用鼠标左键在图形输出窗口中拾取圆角对应的线。
单击ok 按钮,将弹出Element Size on Picked Lines (在所选线上定义单元尺寸)对话框,在对话框中输入No. of element divisions (每条线将要分成的单元数)为1,设定圆角处对应的线只分一个单元。
(由于是模态分析,只要能反应出需要知道的前几阶模态就行,而不需要知道具体的应力值,所以不需要对此处进行单元细化。
)③对分网进行控制。
在分网控制区的Mesh 下拉框中选定分网类型为Area (面),Shape (网格形状)设置为Quad (四边形),分网方式设置为Free (自由分网)。
④对面进行分网。
在MeshTool (分网工具)对话框中单击Mesh 按钮,将弹出Mesh Aeras (对面划分网格)拾取对话框。
从图形输出窗口中拾取创建的面,单击ok 按钮。
完成网格划分。
XYZ6. 出整个轮盘的有限元模型通过将面绕轴旋转成有限元实体模型的功能,将前面建立的轮盘截面有限元网格,围绕定义的旋转轴扫掠成整个轮盘的实体有限元模型。
具体的操作过程如下。
① 定义旋转轴。
可以通过定义旋转轴所在轴线上的两个关键点来,指定旋转轴的位置。
Main Menu >Preprocessor >Modeling >Create >Key points >In Active CS生成两个关键点20、21。
关键点20:X,Y ,Z 位置分别为-10,0,0关键点21:X,Y ,Z 位置分别为10,0,0②设置单元生成选项Main Menu >Preprocessor >Modeling >Operate >Extrude >Elem Ext Opts,弹出Element Extrusion Options (单元挤出选项)对话框,在对话框中的Element type number (单元类型序号)下拉框中选择2号单元SOLID45。
单元尺寸选项中的分割单元数(V AL1 NO. Elem Divs)设置为18,即在挤压出的每个体上将沿周向被分成18份。
拉伸比例为0,保持等截面拉伸。
将Clear area(s) after ext (删除原始面)设置为Yes,在挤压的单元完成之后将删除原来的面以及其上的单元。
单击ok按钮,完成对单元选项的设置。
③绕轴旋转截面Main Menu >Preprocessor >Modeling >Operate >Extrude >Areas >About Axis,将弹出Sweep Areas about Axis (绕轴扫描面)的拾取对话框。
从图形输出窗口中选择创建好的平面网格,单击拾取对话框中的按钮。
然后从图形窗口中选取定义旋转轴的关键点20,21,单击ok按钮,将弹出Sweep Areas about Axis对话框,在对话框中输入旋转角度为(Arc length in degrees)360,No. of volume segments(一周创建体的数目)为4,单击ok按钮。
创建如图所示的整个盘的有限元模型。
XYZ ④ 观察创建的网格形式。
Utility Menu >Plot >Element ,图形窗口中将会显示出由平面网格扫掠而成的实体单元网格情况。
存盘,SAVE_DB 。
至此,完成了创建轮盘有限元模型的所有工作。
XYZ 7. 节点的坐标变换根据轮盘的工作情况其约束条件为盘心轴向和周向约束,这种约束条件在直角坐标系下无法定义,而柱坐标下可以非常方便地定义。
根据ANSYS 程序中坐标系的定义规则,需要将柱坐标系的Z 轴和旋转轴重合,Y 轴表示转角,X 轴表示径向。
ANSYS 程序提供的全局柱坐标系不满足要求。
通常可以有两种办法来解决这个问题:a.将所建有限元模型进行旋转使其轴向和柱坐标Z 轴方向一致。
b.重新建立一个柱坐标系使其的Z 向和旋转轴一致。
本实例采用第二种方法。
具体操作过程如下:① Utility Menu >WorkPlane >Offset WP by Increments ,弹出Offset WP (工作平面偏移)菜单,拖动Degrees 滑动条,将Degrees (旋转角度)值设置为90。
单击按钮,使工作平面绕Y 轴正向旋转90度,单击ok 按钮,将工作平面的WZ 轴和总体坐标系的X 轴方向重合,。
② 在工作平面原点创建柱坐标系。
Utility Menu >WorkPlane >Local Coordinate Systems >Create Local CS >At WP Origin ,将弹出Create Local CS at WP Origin (在工作平面原点创建本地坐标系)对话框,Ref number of newcoord sys (新坐标系的参考序号)缺省值为11,一般就使用缺省值,也可自己设定。
在Type of coordinate system(坐标系类型)下拉框中选取Cylindrical 1 (柱坐标系),其它设置为缺省值。
单击ok按钮。
将完成要求的柱坐标系的创建,并且将新建坐标系定义为当前激活坐标系。
③将所有节点移到当前柱坐标系中。
Main Menu >Preprocessor >Modeling >Create >Nodes >Rotate Node CS >To Active CS将弹出Rotate Nodes into CS菜单。