浅析石油化工装置检修过程中硫化亚
硫化亚铁清洗技术概论

炼油装置设备清洗技术(发表)概述二、炼油设备工艺物料侧污垢特点三、硫化亚铁清洗技术四、重油垢清洗技术五、本公司产品性能介绍八、木公司产品的应用实践概述炼油装置经过一个周期(2〜3年)的运行后,大量硫化亚铁及油泥油垢等污垢沉积在塔、换热器、容器、管线等设备的表面。
这些污垢的存在主要带来以下问题:①FeS遇空气自燃,损坏设备,引发安全事故;②换热器抽芯困难,有的其至无法抽出;③设备打开后大量的油垢难以清除干净;④H2S含量较高的部位在进行吹扫时大量的H2S散布在空气中严重影响环境,危害健康。
我公司开发的新型硫化亚铁清洗技术,不但能完全清除硫化亚铁和硫化氢,而且能清除大部分油泥油垢,确保了检修安全,大大提升了检修进度。
QL-1026硫化亚铁清洗剂技术特点1、药剂高效、无毒、不损害设备,不造成二次污染,对系统内的硫化亚铁和硫化氢可100%清除。
2、具有良好的除油效果,轻油乳化能力大于50g/L,解决了普通硫化亚铁(硫化氢)清洗剂不能清除油垢的难题。
3、使用方便:使用时可根据装置工艺条件不需要改动工艺流程即可以进行单台设备清洗或系统清洗。
4、腐蚀率小:使用时对碳钢腐蚀率^2g/m\h:对不锈钢、铜设备无腐蚀。
5、清洗液无毒害成分,不存在杀生性物质,采用的清洗药剂易于生物降解(>95%),清洗液对活性污泥安全,对环境无污染,可以直接排放。
效果清洗后打开设备不发生自燃,设备内H2S含量为0,塔盘、换热器等设备表面无油泥油垢。
左:清洗前,右:清洗后市场应用重质油垢化学清洗技术简介炼油厂和化工厂的塔盘、换热器、罐及管线表面,运行中由于各种原因会积聚大量重质油垢,这些油垢炭化程度高,清除困难。
我公司研制的重质油垢清洗剂,利用特殊的清洗技术和清洗工艺,对其进行化学转型后可有效清除。
该技术不需拆除设备和机械除垢,可大大降低检修难度和加快检修进度。
技术特点1 •清洗工艺简单,不需对流程作调整,不需拆除设备;2•清洗液具有极强的渗透能力,能穿过污垢表面的微小间隙进入污垢内部;3•当清洗液进入污垢内部后,与之发生反应,使分子量较大的重质油垢,转型成为分子量较小的物质而被乳化分散到清洗液中;效果1•重质油垢清除率:>90%;2•清洗后可直接密封进入投运状态。
储油罐清洗中硫化亚铁自燃事件原因分析及处置
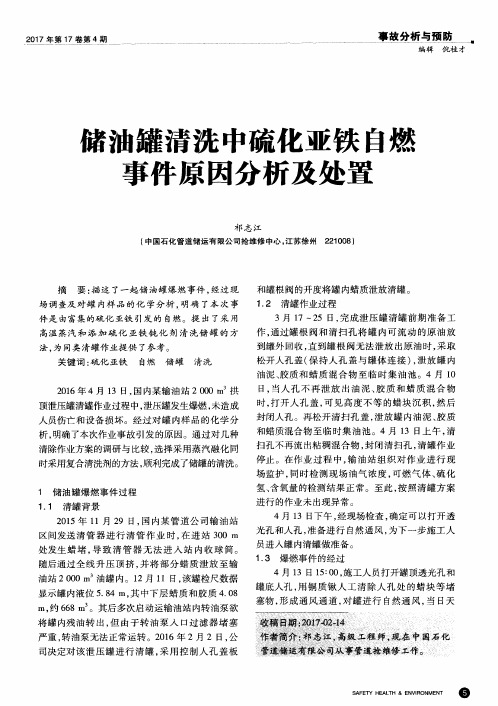
区间 发送 清 管 器 进 行 清 管 作 业 时 , 在进 站 3 0 0 1 3 1
处发生蜡堵 , 导致 清管 器无法 进入 站 内收球筒 。 随后通 过 全 线 升 压 顶 挤 , 并 将 部 分 蜡 质 泄 放 至 输
立 即启 动应 急 预案 , 启 动 消 防泵 , 并 组 织 人 员 到 罐 区实施 灭火 , 至当 日 1 9 : 0 0 , 应 急 处置 结束 。
通 过 样 品 的化 学 分 析 , 表 明残 油 中存 在 较 多 的F e S 、 F e S等 微 晶 固 体 。正 是 这 些 微 晶 形 态 的 F e S和 F e S , 加上 油 气 和油 泥 的易 燃 性 , 暴 露 在 空
时, 打 开人 孔 盖 , 可 见 高 度 不 等 的蜡 块 沉 积 , 然 后
封 闭人 孔 。再松 开 清 扫孔 盖 , 泄 放 罐 内油泥 、 胶 质 和蜡 质混合 物 至 临 时集 油 池 。4月 1 3 日上 午 , 清
清除作业方 案 的调 研 与 比较 , 选 择 采用 蒸 汽融 化 同 时采用复合 清洗剂 的方法 , 顺利 完成 了储 罐 的清洗 。
将 罐 内残 油转 出 , 但 由 于转 油 泵 人 口过 滤 器 堵 塞 严重 , 转 油泵 无 法正 常 运转 。2 0 1 6年 2月 2 日, 公
罐底 人孔 , 用 铜 质锹 人 工 清 除人 孔 处 的蜡 块 等 堵
塞物 , 形 成 通 风通 道 , 对 罐 进 行 自然 通 风 , 当 日天
石油化工储运系统中硫化亚铁自然风险分析及防范措施
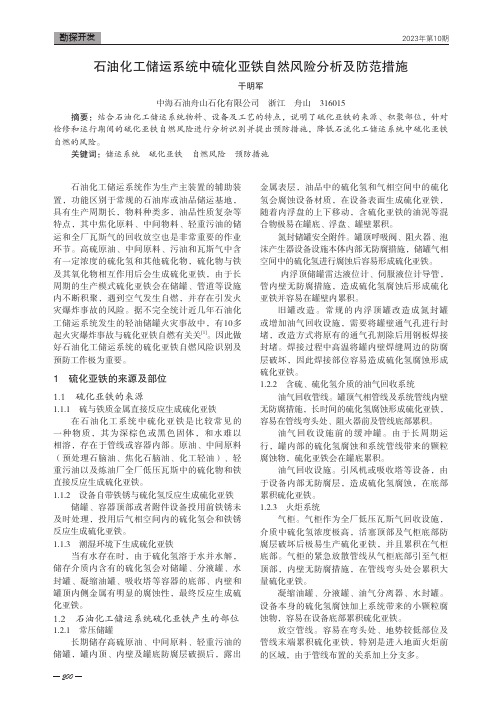
200石油化工储运系统作为生产主装置的辅助装置,功能区别于常规的石油库或油品储运基地,具有生产周期长,物料种类多,油品性质复杂等特点,其中焦化原料、中间物料、轻重污油的储运和全厂瓦斯气的回收放空也是非常重要的作业环节。
高硫原油、中间原料、污油和瓦斯气中含有一定浓度的硫化氢和其他硫化物,硫化物与铁及其氧化物相互作用后会生成硫化亚铁,由于长周期的生产模式硫化亚铁会在储罐、管道等设施内不断积聚,遇到空气发生自燃,并存在引发火灾爆炸事故的风险。
据不完全统计近几年石油化工储运系统发生的轻油储罐火灾事故中,有10多起火灾爆炸事故与硫化亚铁自燃有关关[1]。
因此做好石油化工储运系统的硫化亚铁自燃风险识别及预防工作极为重要。
1 硫化亚铁的来源及部位1.1 硫化亚铁的来源1.1.1 硫与铁质金属直接反应生成硫化亚铁在石油化工系统中硫化亚铁是比较常见的一种物质,其为深棕色或黑色固体,和水难以相溶,存在于管线或容器内部。
原油、中间原料(预处理石脑油、焦化石脑油、化工轻油)、轻重污油以及炼油厂全厂低压瓦斯中的硫化物和铁直接反应生成硫化亚铁。
1.1.2 设备自带铁锈与硫化氢反应生成硫化亚铁储罐、容器顶部或者附件设备投用前铁锈未及时处理,投用后气相空间内的硫化氢会和铁锈反应生成硫化亚铁。
1.1.3 潮湿环境下生成硫化亚铁当有水存在时,由于硫化氢溶于水并水解,储存介质内含有的硫化氢会对储罐、分液罐、水封罐、凝缩油罐、吸收塔等容器的底部、内壁和罐顶内侧金属有明显的腐蚀性,最终反应生成硫化亚铁。
1.2 石油化工储运系统硫化亚铁产生的部位1.2.1 常压储罐长期储存高硫原油、中间原料、轻重污油的储罐,罐内顶、内壁及罐底防腐层破损后,露出金属表层,油品中的硫化氢和气相空间中的硫化氢会腐蚀设备材质,在设备表面生成硫化亚铁,随着内浮盘的上下移动,含硫化亚铁的油泥等混合物极易在罐底、浮盘、罐壁累积。
氮封储罐安全附件。
罐顶呼吸阀、阻火器、泡沫产生器设备设施本体内部无防腐措施,储罐气相空间中的硫化氢进行腐蚀后容易形成硫化亚铁。
硫化亚铁自燃危害与防范技术研究进展

质量和热流的同步分析实验所得 TG-DSC 曲线进
第4期
高建村等. 硫化亚铁自燃危害与防范技术研究进展
行分析,较系统地研 究 了 FeS 氧 化 自 燃 的 热 效 应 及
动力学,计 算 了 反 应 的 活 化 能 平 均 值;通 过 Ma
l
ek
法 y(
α)-α 曲线得到 FeS 最概然机理函数为 f(
一是高温条件下(
240℃ 以上)重 质 原 油 所 含 单
质硫、硫化氢和硫醇与金属直接发生化学腐蚀,这是
性有重 要 影 响,当 水 分 适 量、气 流 量 较 大 且 FeS 粒
形式 [7]:
最常见的硫腐蚀形式。
H2S+Fe=FeS+ H2 ↑
S+Fe=FeS(高温)
RCH2CH2SH +Fe=RCHCH2 +FeS+ H2 ↑
有国外学者认 为,储 罐 壳 层 材 料 在 有 水 存 在 条
件下可腐蚀生成 α
-FeO(
OH),之后与酸性气体硫化
氢反应生成 FeS,其他介 质(
CO2 、溶 解 氧 等)的 存 在
加速了整个化学腐蚀过程
。
[
12]
二是低温条件下的电化学腐蚀。在潮湿环境下
或溶液中,储罐 内 极 易 发 生 严 重 的 电 化 学 腐 蚀。 硫
收稿日期:
2020
08
07;修回日期:
2020
09
24
基金项目:中国博士后科学基金资助项目(
2020M670202);国家级大学 生 创 新 创 业 计 划(URT)项 目(
2020J
00082);北 京 高 等 学 校 高 水 平 人 才
硫化亚铁在原油储运过程中的危害及防治措施

硫化亚铁在原油储运过程中的危害及防治措施胡广杰;邹韬;张志宏【摘要】阐明了原油储罐中硫化亚铁主要来源于硫化氢等腐蚀性气体直接与金属作用,产生的腐蚀产物及硫化氢与铁锈的反应产物。
硫化亚铁最主要的危害是其自燃引起火灾,呼吸阀外腔内的硫化亚铁危害最大。
分析了原油储罐中硫化亚铁的自燃过程,提出了硫化亚铁自燃事故的预防措施。
%It is pointed out that iron sulfide in the crude oil storage tanks is proclueed by directly interaction hydrogen sulfide and other corrosive gases with the metal and reaction between hydrogen sulfide and rust. The greatest hazard of ferrous sulfide is its spontaneous combustion resulting in fire, and ferrous sulfide in the external cavity of breathing valves has the greatest harmfulness. The process of the spontaneous combustion of ferrous sulfide in oil tanks is analyzed, and some prevention measures are proposed.【期刊名称】《腐蚀与防护》【年(卷),期】2012(033)004【总页数】3页(P342-344)【关键词】硫化亚铁;原油储运;危害;腐蚀;自燃【作者】胡广杰;邹韬;张志宏【作者单位】中国石油化工股份有限公司西北油田分公司,乌鲁木齐830011;中国石油化工股份有限公司西北油田分公司,乌鲁木齐830011;中国石油化工股份有限公司西北油田分公司,乌鲁木齐830011【正文语种】中文【中图分类】TE988.2随着石油工业的发展,高含硫原油的产量日益增加,我国塔里木盆地、四川盆地的油气田生产的原油以及从中东地区进口的原油中均大量存在硫化氢气体和单质硫,这些原油中的活性硫对石油加工和储运设备的腐蚀日益严重,其中比较常见的腐蚀产物硫化亚铁危害最大,因其具有很高的自然氧化性,已经引发多起油品储罐着火和爆炸等恶性事故[1-6],严重影响石油化工企业的正常安全生产。
应用钝化清洗消除硫化亚铁隐患

应用钝化清洗消除硫化亚铁隐患作者:付玉军来源:《中国化工贸易·下旬刊》2019年第04期摘要:笔者所在的公司二套催化装置年加工能力60万吨,现在采用减压渣油原料(常减压装置主要加工大庆原油掺炼少部分俄油)。
在装置检修期间经常发生因硫化亚铁自燃造成设备冒烟现象,如果不及时发现和处理会造成火灾事故。
车间以往做法是人工除锈、定点存放、按时浇水,塔器和设备通过公司的消防车定期浇水保持湿润和冷却,固废由公司集中处置。
在应用钝化清洗后,能够及时有效地清除设备上的锈垢,消除硫化亚铁隐患。
关键词:硫化亚铁;钝化清洗;安全管控在停工检修时,设备管线铁锈中硫化亚铁与空气接触会出现冒烟、产生自燃现象,危及装置的顺利停工、检修。
通过装置停工检修时应用了硫化亚铁钝化清洗技术,有效地消除了硫化物,在塔器内部形成了一层钝化膜,消除了硫化亚铁自燃的隐患,消除了为处置硫化亚铁固废带来的麻烦。
钝化清洗工作可以进一步发展成为工艺全流程的清洗,取代或部分取代炼油化工装置的检修工作,真正做到“气不上天、油不落地、声不扰民”。
1 硫化亚铁在设备中的形成机理FeS的颜色多为黑或棕两种,难溶于水,密度4.74g/cm3,熔点1193℃。
硫有两种主要形式存在于油品中:活性硫、非活性硫。
活性硫在石油及其馏分中的有单质活性硫(S)和硫化氢(H2S)及硫醇(RSH)。
其突出表现是在与金属相遇后产生金属硫化物。
超过200℃,硫化氢遇上铁立即产生FeS。
在360至390℃产生率尤为突出,到450℃上下变化逐渐缓慢且趋近于变化消失。
到350至400℃左右,单质硫会轻松和铁化合产生硫化亚铁(FeS)。
而此刻的温度,H2S出现分解:H2S→S+H2产生活性硫与铁的效果最激烈。
超过200℃,硫醇也与铁产生变化:RCH2CH2SH + Fe → RCHCH2 + FeS + H2石油及其馏分中的非活性硫含量较低,包括多硫化物、环硫醚等。
它们的特点为不可以和铁直接产生反应,却在受热之后产生分解为活性硫,产生的活性硫以前述规则与铁产生变化。
加氢装置检修期间硫化亚铁自燃预防与对策
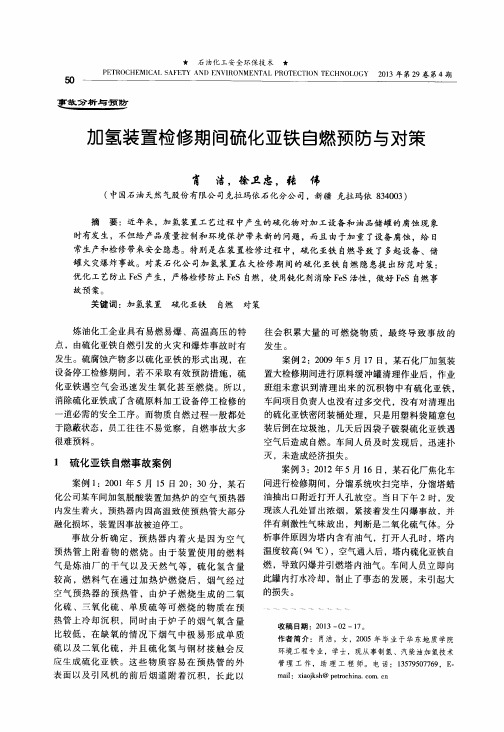
加氢精制反应过程中的硫分布情况如表2 所示:
产品名称 产量/( t ·月一) 硫化 物含 量/ ( mg·L。 1)
原料
<O.1%
表2加氢精制反应过程中的硫分布
精制 柴 油
冷高 分 底 含硫污水
冷低分底 含硫污水
74×109 <0.1%
4 95往会积 累大量的可 燃烧物质, 最终导致事 故的 发生 。
案例2:2009年5月17 Et ,某石化厂加氢装 置大检修期间进行原料缓冲罐清理作业后,作业 班组未意识到清理出来的沉积物中有硫化亚铁, 车间项目负责人也没有过多交代,没有对清理出 的硫化亚铁密闭装桶处理,只是用塑料袋随意包 装后倒在垃圾池,几天后因袋子破裂硫化亚铁遇 空气后造成自燃。车间人员及时发现后,迅速扑 灭,未造成经济损失。
表1加氢精制装置原料油性质
项目 处理量/( t ·a 。1) 混合比例,m% 油品性质
焦化石脑油
27. 29 30.07
焦 化柴油
63. 45 69. 93
混合原料
90. 74
1∞.0
密度( 20℃) / ( g·e m一3)
0.7 38
0.855
O. 816
馏程,( ASTM D86) ℃ I BP/l O% 30 %/5 0% 70 %/9 0%
1硫化亚铁自燃事故案例
案例1:2001年5月15日20:30分,某石 化公司某车间加氢脱酸装置加热炉的空气预热器 内发生着火,预热器内因高温致使预热管大部分 融化损坏,装置因 事故被迫停工。
事故 分析确定 ,预热 器内着火 是因为空 气 预热管 上附着物的 燃烧。由于 装置使用的 燃料 气是炼 油厂的干气 以及天然气 等,硫化氢 含量 较高, 燃料气在通 过加热炉燃 烧后,烟气 经过 空气预 热器的预热 管,由炉子 燃烧生成的 二氧 化硫、 三氧化硫、 单质硫等可 燃烧的物质 在预 热管上 冷却沉积, 同时由于炉 子的烟气氧 含量 比较低, 在缺氧的情况下 烟气中极易形 成单质 硫以及 二氧化硫, 并且硫化氢 与钢材接触 会反 应生成 硫化亚铁。 这些物质容 易在预热管 的外 表面以及 引风机的前后 烟道附着沉积, 长此以
浅析石油化工装置检修过程中硫化亚铁自燃事故及对策
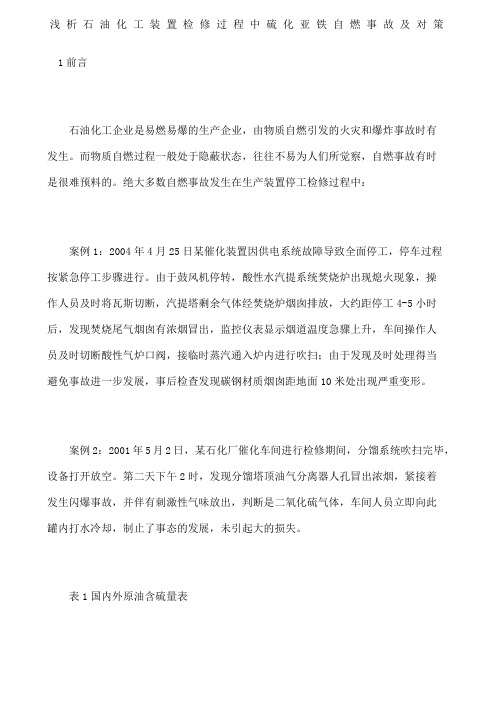
浅析石油化工装置检修过程中硫化亚铁自燃事故及对策1前言石油化工企业是易燃易爆的生产企业,由物质自燃引发的火灾和爆炸事故时有发生。
而物质自燃过程一般处于隐蔽状态,往往不易为人们所觉察,自燃事故有时是很难预料的。
绝大多数自燃事故发生在生产装置停工检修过程中:案例1:2004年4月25日某催化装置因供电系统故障导致全面停工,停车过程按紧急停工步骤进行。
由于鼓风机停转,酸性水汽提系统焚烧炉出现熄火现象,操作人员及时将瓦斯切断,汽提塔剩余气体经焚烧炉烟囱排放,大约距停工4-5小时后,发现焚烧尾气烟囱有浓烟冒出,监控仪表显示烟道温度急骤上升,车间操作人员及时切断酸性气炉口阀,接临时蒸汽通入炉内进行吹扫;由于发现及时处理得当避免事故进一步发展,事后检查发现碳钢材质烟囱距地面10米处出现严重变形。
案例2:2001年5月2日,某石化厂催化车间进行检修期间,分馏系统吹扫完毕,设备打开放空。
第二天下午2时,发现分馏塔顶油气分离器人孔冒出浓烟,紧接着发生闪爆事故,并伴有刺激性气味放出,判断是二氧化硫气体,车间人员立即向此罐内打水冷却,制止了事态的发展,未引起大的损失。
表1国内外原油含硫量表原油名称含硫量% 时间大庆原油0.097 1996.8 胜利原油0.77 1996.11 惠州原油0.03 1991.2 辽河原油0.1736 1984.5 陆丰原油0.1127 1998.7阿曼原油1.08961997.10伊朗轻原油1.631998.4伊拉克巴士拉原油2.111997.12沙特轻质原油2.031998.3沙特中质原油2.561994.5沙特重质原油3.091994.8迪拜原油1.661994.2据有关资料统计,目前我国石油消费量的年增长率为4%,而国内原油量的年产量增长率低于1%,不足的部分要靠进口原油来补充。
从表1中可以看出外国进口原油含硫量较高,特别是中东原油,均大于1%,最高可达3.09%。
加工高硫原油不但给产品质量控制和环境保护带来新的问题,而且由于加重了设备腐蚀,为日常生产和检修过程带来安全隐患,特别是装置检修过程中的硫化亚铁自燃事故,令人防不胜防,发生率较高,如何避免和正确处理硫化亚铁自燃,对安全生产是十分重要的。
- 1、下载文档前请自行甄别文档内容的完整性,平台不提供额外的编辑、内容补充、找答案等附加服务。
- 2、"仅部分预览"的文档,不可在线预览部分如存在完整性等问题,可反馈申请退款(可完整预览的文档不适用该条件!)。
- 3、如文档侵犯您的权益,请联系客服反馈,我们会尽快为您处理(人工客服工作时间:9:00-18:30)。
浅析石油化工装置检修过程中硫化亚铁自燃事故及对策1前言石油化工企业是易燃易爆的生产企业,由物质自燃引发的火灾和爆炸事故时有发生。
而物质自燃过程一般处于隐蔽状态,往往不易为人们所觉察,自燃事故有时是很难预料的。
绝大多数自燃事故发生在生产装置停工检修过程中:案例1:2004年4月25日某催化装置因供电系统故障导致全面停工,停车过程按紧急停工步骤进行。
由于鼓风机停转,酸性水汽提系统焚烧炉出现熄火现象,操作人员及时将瓦斯切断,汽提塔剩余气体经焚烧炉烟囱排放,大约距停工4-5小时后,发现焚烧尾气烟囱有浓烟冒出,监控仪表显示烟道温度急骤上升,车间操作人员及时切断酸性气炉口阀,接临时蒸汽通入炉内进行吹扫;由于发现及时处理得当避免事故进一步发展,事后检查发现碳钢材质烟囱距地面10米处出现严重变形。
案例2:2001年5月2日,某石化厂催化车间进行检修期间,分馏系统吹扫完毕,设备打开放空。
第二天下午2时,发现分馏塔顶油气分离器人孔冒出浓烟,紧接着发生闪爆事故,并伴有刺激性气味放出,判断是二氧化硫气体,车间人员立即向此罐内打水冷却,制止了事态的发展,未引起大的损失。
表1国内外原油含硫量表据有关资料统计,目前我国石油消费量的年增长率为4%,而国内原油量的年产量增长率低于1%,不足的部分要*进口原油来补充。
从表1中可以看出外国进口原油含硫量较高,特别是中东原油,均大于1%,最高可达3.09%。
加工高硫原油不但给产品质量控制和环境保护带来新的问题,而且由于加重了设备腐蚀,为日常生产和检修过程带来安全隐患,特别是装置检修过程中的硫化亚铁自燃事故,令人防不胜防,发生率较高,如何避免和正确处理硫化亚铁自燃,对安全生产是十分重要的。
2硫化亚铁的产生原因及自燃机理2.1硫化亚铁的产生原因(1)电化学腐蚀反应生成硫化亚铁原油中80%以上的硫集中在常压渣油中,这些硫化物的结构比较复杂,在高温条件特别是在催化剂的作用下,极易分解生成硫化氢和较小分子硫醇。
当有水存在时,这些硫化氢和硫醇对铁质设备具有明显的腐蚀作用,反应过程为:H2S=H++HS-HS-=H++S2-这是一种电化学腐蚀过程:阳极反应:Fe→Fe2++2e阴极反应:2H++2e→H2(渗透钢中)Fe2+与S2-及HS-反应:Fe2++S2-=FeS↓Fe2++HS-=FeS↓+H+另外,硫与铁可直接作用生成硫化亚铁:Fe+S=FeS↓生成的硫化亚铁结构比较疏松,均匀地附着在设备及管道内壁。
(2)大气腐蚀反应生成硫化亚铁装置由于长期停工,设备内构件长时间暴露在空气中,会造成大气腐蚀,而生成铁锈。
铁锈由于不易彻底清除,在生产过程中就会与硫化氢作用生成硫化亚铁。
反应式如下:Fe+O2+H2O→Fe2O3•H2OFe2O3•H2O+H2S→FeS↓+H2O此反应较易进行,由于长期停工,防腐不善的装置更具有生产硫化亚铁的趋势。
2.2硫化亚铁自燃的机理及现象(1)硫化亚铁自燃的机理硫化亚铁及铁的其它硫化物在空气中受热或光照时,会发生如下反应:FeS+3/2O2=FeO+SO2+49KJ2FeO+1/2O2=Fe2O3+271KJFeS2+O2=FeS+SO2+222KJFe2S3+3/2O2=Fe2O3+3S+586KJ(2)硫化亚铁自燃的现象硫化亚铁自燃的过程中如没有一定的可燃物支持,将产生白色的SO2气体,常被误认为水蒸汽,伴有刺激性气味;同时放出大量的热。
当周围有其它可燃物(如油品)存在时,会冒出浓烟,并引发火灾和爆炸。
3影响硫化亚铁生成速度因素从硫化亚铁的生成机理可知,在日常生产中,硫化亚铁的生成过程就是铁在活性硫化物作用下而进行的化学腐蚀反应过程。
因此,控制化学腐蚀反应是限制硫化亚铁生成的关键手段。
只要我们找出生产装置易发生硫腐蚀的部位,根据各部位特点采取有效措施,就可减小硫化亚铁生成量,进而从根本上避免硫化亚铁自燃事故的发生。
油品的含硫量、温度、水及Cl-的存在等因素是影响此电化学腐蚀反应进行速度的重要因素。
3.1原油加工过程中的硫分布规律只要有硫存在的情况下,才会发生硫化学腐蚀;油品含硫量高的部位是最易发生腐蚀的地点。
因此,分析原油在加工过程的硫分布对于控制硫化亚铁的生成具有指导意义。
表2常压蒸馏后馏分的硫分布(1)从表2可以看出,原油经常压蒸馏后85%的硫都集中在350℃以上的馏分即常压渣油中,因此常压渣油流经的设备受硫腐蚀的倾向较大;在实际生产中,减压塔塔内构件及减压单元换热器是硫化亚铁最易生成的部位。
(2)从表3可以看出,约70%的硫随反应油气进入分馏、吸收稳定系统;近30%的硫存在于焦炭中随再生烟气排掉。
因此,分馏塔顶冷凝系统、吸收稳定系统的凝缩油灌及再沸器、柴油抽出系统是硫化亚铁易产生的部位。
(3)硫含量较高的酸性水处理系统及酸性水流经的设备也是易发生硫腐蚀的地点。
3.2高温硫腐蚀硫腐蚀反应为化学腐蚀反应,温度升高可加快反应速度。
因此,对于物流温度较高的常压塔底及常渣换热单元、减压单元、催化裂化柴油抽出系统比较容易发生高温硫腐蚀。
3.3水及Cl-存在可促进设备硫腐蚀从硫化亚铁生成反应机理可知有水存在可促进化学腐蚀的进行而当有Cl-存在即使温度较低时也会发生如下反应:Fe+2HCl→FeCl2+H2↑FeCl2+H2S→FeS↓+2HClFe+H2S→FeS↓+H2↑FeS+2HCl→FeCl2+H2S对于常压塔顶冷凝系统,即塔顶、油气挥发线、水冷器及回流罐等部位,易发生低温H2H-HCl-H2O腐蚀。
4案例分析案例1事故分析:○1由于长时间停电使风机停转,造成其焚烧炉熄火,而H2S浓度较高的酸性气通过烟囱排放;由于炉膛温度(900℃左右)仍然较高,酸性气中硫化氢预热升温后与碳钢作用生成硫化亚铁。
○2由于当时风较大,加速了空气进入炉膛及烟囱的速度,随着酸性气体的减少,氧含量的提高,硫化亚铁与氧气发生自燃反应,放出大量热,最后将铁制烟囱烘得严重变形。
○3检修中发现烟囱变形部位周围较大面积变薄,已严重腐蚀,经分析可能是在开停工及平时操作波动过程中,焚烧烟气中含有未转化成SO2的硫化氢气体,促使硫化亚铁不断生成。
另外,变形部位未进行保温,可能发生露点腐蚀,使管道变薄。
○4吸取了本次事故的教训后,车间将烟囱由碳钢改为耐腐蚀性好的钢材,并加强了烟囱的保温状况。
另外,在风机出口管线上加设蒸汽线,当焚烧炉熄灭时,可用来吹扫未反应的气体,减少硫化亚铁的生成几率。
案例2事故分析:○1进入罐内检查发现,罐底沉积较厚一层类似铁锈的物质,经化验发现硫化亚铁含量很高。
②由于停工时间较长,设备内部构件长期暴露在空气中,会造成大气腐蚀,生成铁锈;开工前的清理不易将其除去,在生产过程中铁锈和硫化氢作用生成硫化亚铁,下次停工吹扫时由于吹扫使硫化亚铁层脱落,随气流进入油水分离罐,沉积下来。
③由于天气炎热,气温达30℃,随着热量的积累,使“铁锈”表面油膜及水分蒸发掉,与空气直接接触,最后引起干燥的硫化亚铁发生自燃,并引燃油气发生闪爆。
5硫化亚铁自燃事故的防治对策5.1 从根源上控制硫化亚铁生成硫化亚铁的产生过程是设备的腐蚀过程,有必要从多个方面采取措施,减少对设备的硫腐蚀。
(1)从工艺方面入手,减少设备硫腐蚀,控制硫化亚铁的产生。
○1加强常压装置“一脱四注”抑制腐蚀。
根据原油的实际状况,选择效果好的破乳剂,优化电脱盐工艺,加大无机盐(例如MgCl2、CaCl2 )脱除率,从而减小塔顶Cl-含量。
使用适合于高硫原料的缓蚀剂,降低腐蚀速度。
适当加大注氨量,减轻硫腐蚀。
○2采用渣油加氢转化工艺降低常压渣油的硫含量。
催化裂化装置对常渣的硫含量要求较高,在加工高含硫原油的情况下,可采用渣油加氢转化技术,降低渣油中的硫、胶质、氮等物质的含量,可以减轻催化设备腐蚀,同时生产出高品质的产品。
○3在分馏塔顶试添加缓蚀剂,使钢材表面形成保护膜,起阻蚀作用。
(2)从设备方面采取措施,阻止硫化亚铁产生。
○1易被硫腐蚀的部位,更换成耐腐蚀的钢材。
兼顾成本,选择性价比较高的耐腐蚀钢材,例如选择价格合理而防腐性能与昂贵的316L钢相当的渗铝钢。
○2采用喷镀隔离技术在易腐蚀设备内表面采用喷镀耐腐蚀金属或涂镀耐腐蚀材料等技术实现隔离防腐目的。
但生产过程中如果流经设备及管线的油品的流速较大或设备中的易磨损部位不宜采用喷镀隔离技术。
○3加强停工期间的防腐保护。
对于长期停工的装置,应采用加盲板密闭,注入氮气置换空气等措施,防止大气腐蚀。
(3)加强日常操作管理加强有关岗位的操作管理,防止因操作不当造成硫化亚铁的不断生成。
5.2采用化学处理方法消除硫化亚铁。
对于像减压塔填料,酸性水汽提塔板极易产生硫化亚铁部位,可采用化学方法处理。
(1)酸洗:可用稀盐酸清洗来消除硫化亚铁存在,但会释放出硫化氢气体,需加额外硫化氢抑制剂,以转化并消除硫化氢气体。
(2)螯合物处理:特制的高酸性螯合物在溶解硫化物沉淀时非常有效,不会产生硫化氢气体,但实际价格较昂贵。
(3)氧化处理:可用氧化剂高锰酸钾氧化硫化物,具有使用安全,容易实施的优点。
5.3 停工检修过程中应注意的事项(1)停工前做好预防硫化亚铁自燃事故预案。
停车前根据装置自身特点及以往的实践经验,做好硫化亚铁自燃预案,一量发生自燃事故,立即采取措施,防止事故范围扩大,减小经济损失。
(2)设备吹扫清洗时,对于弯头、拐角等死区要特别处理,并注意低点排凝,确保吹扫质量,防止残油及剩余油气的存在。
从而避免硫化亚铁自燃引发爆炸和火灾扩大。
(3)设备降至常温方可打开,进入前用清水冲洗,保证内部构件湿润,清除的硫化亚铁应装入袋中浇湿后运出设备外,并尽快采取深埋处理。
(4)加强巡检。
检修期间,特别是在气温较高的环境下,必须加强检查,及时发现,及时处理。
参考文献1杨书显.原油加工过程中硫分布规律分析与控制.中国石油化工科技指南,2003上卷2黄靖国等.常减压蒸馏装置的腐蚀及控制.石油化工,2002.3(5)3黄鹄催化装置冷换设备的腐蚀现状与防腐对策.石油安全,2002.3(6)。