第4章 带长管道负载敏感系统的试验研究
负载敏感技术在甘蔗联合收割机上的应用_付玉林

负载敏感技术在甘蔗联合收割机上的应用付玉林1,2,陈远玲1,程志青3,施江天2,徐 杰2(1.广西大学机械工程学院,南宁 530004;2.装甲兵技术学院,长春 130117;3.上海师范大学天华学院,上海 201815)摘 要:甘蔗联合收割机由于执行元件的复杂性及液压系统负载的多变性,在作业过程中造成了大量的液压能损失现象。
为改善收割机的节能性,在对负载敏感系统的工作原理进行分析的基础上首次提出了将负载敏感技术应用于甘蔗联合收割机的节能观点,并为其负载敏感系统匹配了相关参数。
基于A M E S i m平台的静、动态仿真结果表明,在系统压力达到调压阀设定压力之前,系统的流量仅取决于流量阀的开口而与负载无关,负载敏感阀将根据流量阀的开口自动调节变量泵的排量。
在系统压力达到调压阀设定压力之后,系统压力仅取决于调压阀的设定值,而与负载无关,此时负载敏感阀将自动调节变量泵的排量使其恰好与负载的需要相适应,控制过程的压力损失小于1M P a,从而大大减小了甘蔗联合收割机的液压能损失。
关键词:负载敏感;甘蔗联合收割机;节能中图分类号:T H137.52;S225.5+3 文献标识码:A文章编号:1003-188X(2009)03-0014-040 引言自20世纪50年代全球性的能源危机爆发以来,节能问题越来越受到国际社会的关注。
作为大型农业机械,甘蔗联合收割机在作业过程中要一次性完成切割、断尾、输送、剥叶及集蔗等工序,执行元件庞杂且各执行元件之间必须保持一定的转速比以协调工作[1],而蔗田内不同区段蔗株疏密程度及秆径变化各异。
因此,液压系统负载变化频繁,整个液压系统的压力、流量也会不断变化,溢流、节流损失严重。
另外,为减少甘蔗收割过程中的破头率,应尽量避免执行元件转速的频繁波动。
现有的4G Z-180等系列的甘蔗收割机由于在设计之初很少考虑节能问题,因而液压能量损失严重,经济效益差,而且由于采用了开中心多路阀,在大负载情况下阀杆的操纵性能很差,调速性能不稳定。
(完整版)负载敏感
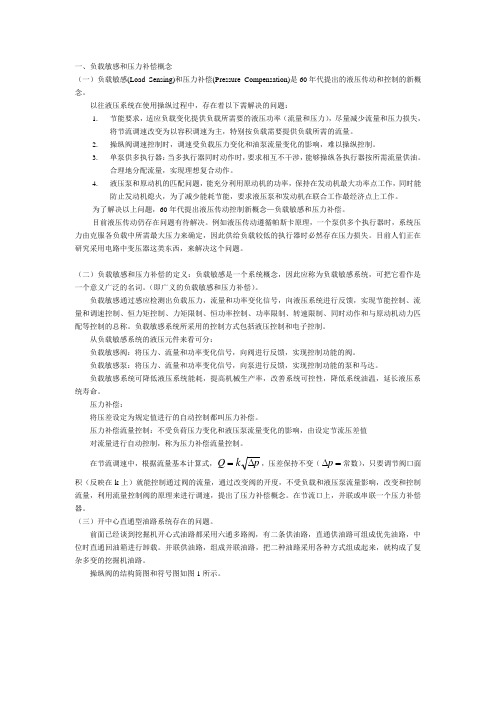
一、负载敏感和压力补偿概念(一)负载敏感(Load Sensing)和压力补偿(Pressure Compensation)是60年代提出的液压传动和控制的新概念。
以往液压系统在使用操纵过程中,存在着以下需解决的问题:1.节能要求,适应负载变化提供负载所需要的液压功率(流量和压力),尽量减少流量和压力损失,将节流调速改变为以容积调速为主,特别按负载需要提供负载所需的流量。
2.操纵阀调速控制时,调速受负载压力变化和油泵流量变化的影响,难以操纵控制。
3.单泵供多执行器:当多执行器同时动作时,要求相互不干涉,能够操纵各执行器按所需流量供油。
合理地分配流量,实现理想复合动作。
4. 液压泵和原动机的匹配问题,能充分利用原动机的功率,保持在发动机最大功率点工作,同时能防止发动机熄火,为了减少能耗节能,要求液压泵和发动机在联合工作最经济点上工作。
为了解决以上问题,60年代提出液压传动控制新概念—负载敏感和压力补偿。
目前液压传动仍存在问题有待解决。
例如液压传动遵循帕斯卡原理,一个泵供多个执行器时,系统压力由克服各负载中所需最大压力来确定,因此供给负载较低的执行器时必然存在压力损失。
目前人们正在研究采用电路中变压器这类东西,来解决这个问题。
(二)负载敏感和压力补偿的定义:负载敏感是一个系统概念,因此应称为负载敏感系统,可把它看作是一个意义广泛的名词。
(即广义的负载敏感和压力补偿)。
负载敏感通过感应检测出负载压力,流量和功率变化信号,向液压系统进行反馈,实现节能控制、流量和调速控制、恒力矩控制、力矩限制、恒功率控制、功率限制、转速限制、同时动作和与原动机动力匹配等控制的总称。
负载敏感系统所采用的控制方式包括液压控制和电子控制。
从负载敏感系统的液压元件来看可分:负载敏感阀:将压力、流量和功率变化信号,向阀进行反馈,实现控制功能的阀。
负载敏感泵:将压力、流量和功率变化信号,向泵进行反馈,实现控制功能的泵和马达。
负载敏感系统可降低液压系统能耗,提高机械生产率,改善系统可控性,降低系统油温,延长液压系统寿命。
长输管道的试压

国外在进行管段划分时比较灵活 。参考规范要 求 ,结合具体情况 ,可以适当延长或缩短试压管段长 度 。苏丹输油管道〔7〕起自南部黑哥林格油区首站 , 经过奥贝伊德 、喀土穆 ,穿越尼罗河 、阿特巴拉河 ,翻 越红海山区 ,终止于苏丹港末站 。管道全长为 1 504 km ,管径为 711. 2 mm ,材质为 A PI 5L X60 ,钢管的 壁厚为 10. 72 mm 和 16. 36 mm ,设计压力分别为 9. 722 M Pa 和 14. 844 M Pa 。按照常规的试压分段 方法 ,1 504 km 的管道就需要分八十多段 ,这对于 部分地区严重缺水 、环境条件恶劣的苏丹而言施工 难度很大 。通过查阅国外的有关标准和规范 ,将试 压管段最长延长至 60 km ,管段数量比常规划分减 少了 1/ 3 。延长试压分段长度明显减少了工作量 , 但缺点是因管道过长 ,出现缺陷或泄漏的概率增加 。 总体试压时间有的长达几个月 ,多次升压 、降压 ,不 仅延误工期 ,也对管道造成了损伤〔8〕。
这些重大的长输管道 ,需要更加安全和有效的施工 工艺 。在长输管道工程中 ,试压是其中的一个重要 工序 ,是对管道施工质量 、材料性能 、管道整体性的 一次综合检验 。目前国际上普遍使用压力2容积曲 线法进行水压试验 ,将水压试验的压力提高至管材 最小屈服强度值的 1. 0~1. 1 倍 ,而国内还未应用此 方法 ,不少新建管道仍用空气做管道的强度试压介 质 ,落后当代水压试验技术 40 年〔1〕。结合现有的国 家规范和近几年国内外的施工情况 ,从管段划分 、试 压介质选择 、试验压力三个方面进行综述 。
负载敏感技术原理
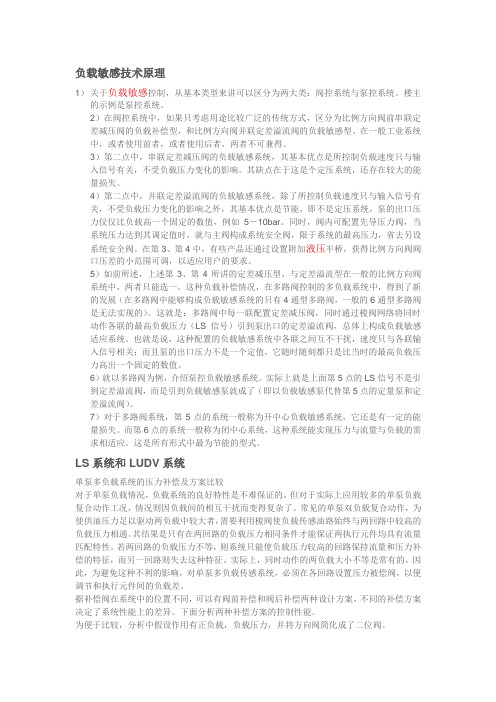
负载敏感技术原理1)关于负载敏感控制,从基本类型来讲可以区分为两大类:阀控系统与泵控系统。
楼主的示例是泵控系统。
2)在阀控系统中,如果只考虑用途比较广泛的传统方式,区分为比例方向阀前串联定差减压阀的负载补偿型,和比例方向阀并联定差溢流阀的负载敏感型。
在一般工业系统中,或者使用前者,或者使用后者,两者不可兼得。
3)第二点中,串联定差减压阀的负载敏感系统,其基本优点是所控制负载速度只与输入信号有关,不受负载压力变化的影响。
其缺点在于这是个定压系统,还存在较大的能量损失。
4)第二点中,并联定差溢流阀的负载敏感系统,除了所控制负载速度只与输入信号有关,不受负载压力变化的影响之外,其基本优点是节能,即不是定压系统,泵的出口压力仅仅比负载高一个固定的数值,例如5-10bar。
同时,阀内可配置先导压力阀,当系统压力达到其调定值时,就与主阀构成系统安全阀,限于系统的最高压力,省去另设系统安全阀。
在第3、第4中,有些产品还通过设置附加液压半桥,获得比例方向阀阀口压差的小范围可调,以适应用户的要求。
5)如前所述,上述第3、第4所讲的定差减压型,与定差溢流型在一般的比例方向阀系统中,两者只能选一。
这种负载补偿情况,在多路阀控制的多负载系统中,得到了新的发展(在多路阀中能够构成负载敏感系统的只有4通型多路阀,一般的6通型多路阀是无法实现的)。
这就是:多路阀中每一联配置定差减压阀,同时通过梭阀网络将同时动作各联的最高负载压力(LS信号)引到泵出口的定差溢流阀,总体上构成负载敏感适应系统。
也就是说,这种配置的负载敏感系统中各联之间互不干扰,速度只与各联输入信号相关;而且泵的出口压力不是一个定值,它随时随刻都只是比当时的最高负载压力高出一个固定的数值。
6)就以多路阀为例,介绍泵控负载敏感系统。
实际上就是上面第5点的LS信号不是引到定差溢流阀,而是引到负载敏感泵就成了(即以负载敏感泵代替第5点的定量泵和定差溢流阀)。
7)对于多路阀系统,第5点的系统一般称为开中心负载敏感系统,它还是有一定的能量损失。
负载敏感液压系统典型工况原理分析
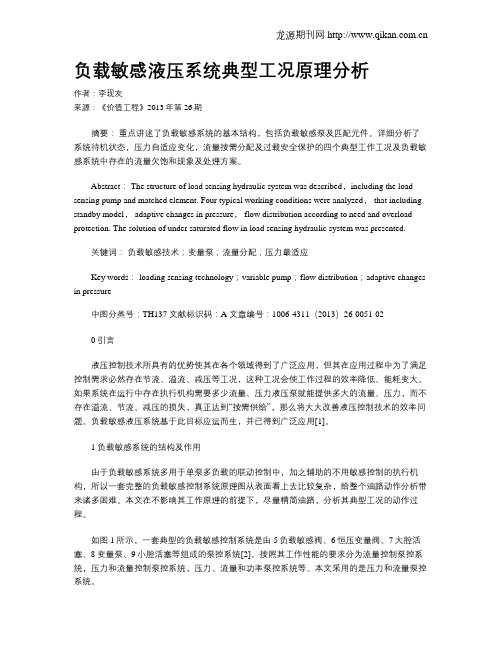
负载敏感液压系统典型工况原理分析作者:李现友来源:《价值工程》2013年第26期摘要:重点讲述了负载敏感系统的基本结构,包括负载敏感泵及匹配元件。
详细分析了系统待机状态,压力自适应变化,流量按需分配及过载安全保护的四个典型工作工况及负载敏感系统中存在的流量欠饱和现象及处理方案。
Abstract: The structure of load sensing hydraulic system was described,including the load sensing pump and matched element. Four typical working conditions were analyzed, that including standby model, adaptive changes in pressure, flow distribution according to need and overload protection. The solution of under saturated flow in load sensing hydraulic system was presented.关键词:负载敏感技术;变量泵;流量分配;压力最适应Key words: loading sensing technology;variable pump;flow distribution;adaptive changes in pressure中图分类号:TH137 文献标识码:A 文章编号:1006-4311(2013)26-0051-020 引言液压控制技术所具有的优势使其在各个领域得到了广泛应用,但其在应用过程中为了满足控制需求必然存在节流、溢流、减压等工况,这种工况会使工作过程的效率降低、能耗变大。
如果系统在运行中存在执行机构需要多少流量、压力液压泵就能提供多大的流量、压力,而不存在溢流、节流、减压的损失,真正达到“按需供给”,那么将大大改善液压控制技术的效率问题。
海洋立管的模态及参数敏感性分析

。0 x 2
m
一 E
6 (
。
¨
式 中: r —— 张力 因子 ;
— —
单位 长度 的表 观重力 。
0[ I 2]x E X6 O
i o L
( 4 )
若考 虑表 观重 力 的影 响 , 张力 沿 立 管 高 度 则
为线性 变化 , 任意 高度 z 的张 力可表 示 为 处
海 洋 立 管 的模 态 及 参 数 敏 感 性 分 析
雷 松, 张文 首 。 林家浩 。 岳前 进
( 大连理工大 学 运载工程与力学学部 , 宁 大连 16 2 ) 辽 10 3 摘 要: 为分析海洋立管受不 同形式 的轴 向张力作用时 的模态求解问题 , 哈密 尔顿原理建立理论模型 , 用
计 算 方法 , 究 相关 参 数 对 立 管振 动 频 率 和振 型 研
的影 响 。
1 微 分 方 程 的推 导
海洋立 管 通常 可 以 看作 弹 性 梁 , 可运 用 基 于 小变形 假设 的 欧拉坝 努利 梁模 型 , 即假 设微 元 的转 动量 可以 忽略 , 只关注水 平位 移 ; 和弯 曲变 形 相 比, 因剪切 力 引起 的 角 变形 是 微 阶小 量 。如 图
0 2 0x 2
一
 ̄( t )一 - ( )+m )
o
d
= () o 9
下面 重点讨 论立 管 自由振动 的模 态 问题 。
2 自由振 动 方程 的 求解
号 出 叫
( 2. 2 1 )
基本 参数 的计算 在实 际工 程 中 , 根立 管直 径相 同 , 略连接 单 忽
微元上外力所作 的虚功 为 : 出。沿 z 廊 方 向积分可得 到整个系统 的应 变能 、 动能和总 虚功。 对于整个 系统 , 运用哈密顿原理 可表达为
负载敏感泵的变量响应特性对挖掘机性能的影响

关键 词 : 负载敏 感 ; 态 测 试 ; 动 变量 特 性 ; 阻尼 ; 空 吸
中图分类号 : nB
文献标识码 : A
文章编号 :06 4 1 (0 1 0 - 0 6 0 10 - 44 2 1 )3 09 - 3
M o Yo —y u— u
’ 1 mpa to a i b e r s n e c I ei 1 c fv r a l e po s har c e sis o o d e stv m p on e c a or p r o m a e a t r tc fl a s n i e pu i i x av t e f r nc
( y rui t hooyi tu G ag i uhi ev d syC . D Yl u nx 5 7 0 ,C i ) H dal c nl stt ce g nie unx ca hayi ut o , A, u nG ag i 3 05 h a Y n r i n
t n a d t e l e o u . F o la e st e t e r i n l f mp o h f p rm o d s n i v h oy,t e fco s w ih i a m o ai l s o s h r c eit s o a i h a tr h c mp e n v r e r p n e c a a t r i fl d b a e sc o s n i v u p a d t e k y is e e d t e n t e r n lz d c r fl .I p o i e rc c ls p o t oe c v t rh d a - e s ep i t m n e su s n e b oi d a ea ay e aeul h o c y t r vd sp a t a u p r t x a ao y r i n
深水钢制悬链线立管疲劳敏感性分析研究

- 31 -第3期图1 气田总体布置及钢悬链立管布置图深水钢制悬链线立管疲劳敏感性分析研究杨伟,李旭,任翠青,苑健康,张薇(海洋石油工程股份有限公司, 天津 300452)[摘 要] 南海某深水项目是国内首个采用钢悬链线立管的深水工程项目。
本文以该气田10寸钢悬链立管(SCR)为例,结合工程经验确定了影响疲劳的主要因素,利用Flexcom软件建立了疲劳分析模型并进行了敏感性分析。
通过对比所有敏感性分析结果可知,立管重量制造公差、系泊锚链预张紧力对立管触底区域的疲劳有明显影响。
通过本文的研究,为项目及后期类似项目的钢悬链立管分析设计提供了参考和借鉴。
[关键词] 钢悬链线立管;敏感性分析;疲劳分析作者简介:杨伟(1983—),男,河北人,硕士研究生,高级工程师,海洋石油工程股份有限公司立管结构工程师。
近年来,深海开发中的油气勘探和生产活动大大增加,与几年前相比水深增加了一倍[1]。
钢制悬链线立管(SCR )由于其成本低、对浮体运动有较大的适应性,且适用高温高压工作环境,因此逐渐成为深水开发的首选立管形式,被誉为深水开发的成本有效解决方案[2]。
南海某深水项目是国内首个采用深水钢质悬链线立管的深水工程项目,因此从立管构型设计、关键部件选择、立管计算分析,管土作用评估、安装分析、管材确定都面临挑战。
本文从南海某深水项目实际工程出发,针对实施中遇到的影响SCR 疲劳分析的不确定因素开展敏感性分析,给出了在南海特有环境条件下的立管动力分析结果,为其他南海类似工程的SCR 分析设计提供了参考和借鉴。
1 项目概述南海某深水油气田是我国首个自营开发的深水气田。
气田水深范围1220~1560m ,其中SCR 应用水深范围1430~1470m 。
该气田开发示意图如图1所示,由一座深水半潜平台(SEMI )、水下生产系统、SCR 和海底管道组成。
该工程共有6根SCR ,分别为一根18寸外输天然气SCR (GE ),两根12寸生产SCR (P1和P2),两根10寸生产SCR (P3和P4),以及一根6寸MEG 注入SCR (MEG1)。
- 1、下载文档前请自行甄别文档内容的完整性,平台不提供额外的编辑、内容补充、找答案等附加服务。
- 2、"仅部分预览"的文档,不可在线预览部分如存在完整性等问题,可反馈申请退款(可完整预览的文档不适用该条件!)。
- 3、如文档侵犯您的权益,请联系客服反馈,我们会尽快为您处理(人工客服工作时间:9:00-18:30)。
第四章带长管道负载敏感系统的试验研究4.1 引言科学研究的起点是科学问题,本章试图通过进行部分的实验,对负载敏感系统中存在的管道效应获得一些初步的感性认识。
并从中发现问题,以确定今后理论研究的方向。
本章首先介绍了试验系统的构成,并确定试验方案,明确试验目的。
在此基础上进行对负载敏感系统中的管道问题做了初步的试验研究。
4.2 试验系统介绍本课题的所有试验都是在“负载敏感及功率回馈试验台”上完成的,此台架为一模拟工程机械液压系统的综合性试验平台。
利用此试验平台,能够实现阀控缸、阀控马达、泵控缸、泵控马达,原动机的变频控制以及负载敏感多路控制系统的试验研究。
试验台原理图及操作面板见附录1及附录2。
此系统的构成比较复杂,以下是对其液压回路和测控系统的简单介绍。
4.2.1 液压回路1). 组成部分此试验台的油源部分由控制泵装置、循环泵装置、各泵压力控制块、冷却器、加热器、滤油器以及高位油箱组成的。
液压动力源由两部分构成,第一部分为由带电子油门控制的柴油机及电动机作为原动机、以变量泵为主泵的液压动力源,第二部分为由变频电动机作为原动机、以定量泵为主泵的液压动力源。
控制部分由比例伺服阀、电液比例多路阀以及进行油路切换用二通球阀、三通球阀组成的。
管道部分分为四组。
每组由六根长度为6米内径12毫米的钢管组成,由置于管道两端的连接块将其连接为一根长度为36米的管道。
其中两组位于多路阀与液压缸之间,另外两组位于多路阀与变量泵之间。
此试验台有三套执行机构,其中两个为直线运动的单出杆液压缸,其行程为1.5米,每只液压缸内安装一根磁致伸缩线性位移传感器。
此传感器既可提供位移输出亦可提供速度输出。
另一个为回转运动的定量马达。
与执行机构相对应,加载系统也由三部分构成。
第一部分为由双向定量泵、回转惯量组以及电液比例加载阀块组成的回转运动加载机构部分。
第二部分为由加载液压缸、分片重块、滑轮机构以及电液比例加载阀块组成的直线运动加载部分,其中分片重块为圆形重块,总重量为1吨,分成15片,其中100kg5块,50kg10块。
第三部分为由加载液压缸、惯性块以及与两个动力源相连接的电液比例伺服阀构成。
构成惯性块的条形重块总重量为1吨,分成一块底座重200kg,32块分片重块,每块重25kg。
前两个加载系统为被动加载方式,最后一个加载系统为主动加载方式,其加载特性由程序灵活决定。
2)可实现的基本回路通过切换二通、三通球阀,此试验台可以由上述部分组合为不同试验回路,具体有以下的几种组合情况:1.变量泵、多路阀、马达2.变量泵、多路阀、液压缸A3.变量泵、多路阀、液压缸B4.定量泵、伺服阀A、液压缸A5.定量泵、伺服阀B、液压缸B6.定量泵、伺服阀A、马达对前三种由变量泵作为油源的情况而言,根据连接油源、多路阀、执行机构之间的管道长短,每种回路又存在以下四种情况。
1.变量泵与多路阀之间、多路阀与执行机构之间均为短管道。
2. 变量泵与多路阀之间为长管道,多路阀与执行机构之间为短管道。
3. 变量泵与多路阀之间为短管道,多路阀与执行机构之间为长管道。
4. 变量泵与多路阀之间、多路阀与执行机构之间均为长管道。
4.2.2 测控系统试验装置测试系统为用户提供了用于电压测量、压力测量、流量测量、液压缸位移测量、扭矩测量的A/D输入通道和用于系统控制的D/A输出通道。
试验系统的各个被测压力、变量泵输出流量、液压缸位移、变量泵输入扭矩、转速、惯性轴负载扭矩、转速等参数可在仪表面板上实时显示,各比例多路阀、比例伺服阀、液压缸和马达加载阀、变量泵排量、等可由D/A输出信号控制。
测试系统的硬件包括工业控制计算机、测量传感器、数字显示仪表、输入信号隔离与处理、A/D转换器、D/A转换器、输出信号隔离与调理等功能单元。
本实验中需要采集压力、流量、位移信号,下面详细介绍这三个量的测量与显示原理及数据采集系统。
1) 压力测量与显示测试系统有9个压力测量点,用来测量被试液压系统中各相应油口的压力,各压力测量通道的结构相同,见图4-1。
图4-1 压力测量与显示压力传感器将被测压力变换成电压信号,分两路送至数字电压表和信号处理与隔离电路。
数字电压表用于实时显示被测压力值,其读数由读数校准电位器调整。
信号处理与隔离电路的输出与数据采集系统的A/D转换器相连。
本试验台采用的压力传感器为压阻式压力传感器,其量程为30 MPa ,线性度误差为0.3%FSR,频宽为1KHz,输出电压范围为1~5 V。
2)流量测量与显示变量泵输出流量的测量与显示通道如图4-2所示,齿轮马达流量传感器将被测流量转换成脉冲信号,该脉冲信号经流量计算议运算后显示流量值,同时,流量积算仪通过模拟输出端口将电压信号送至信号处理与隔离电路,与数据采集系统的A/D转换器相连。
其量程为:0.1~150 L/min,测量精度为<±0.3%,耐40MPa 高压,动态响应: 50ms图4-2 流量测量与显示3)位移测量与显示液压缸位移由内置式磁致伸缩位移传感器进行测量,其结构见图4-3。
图4-3 位移测量与显示磁致伸缩位移传感器和信号处理电路将被测液压缸活塞杆的位移变换成电压信号,分两路送至数字电压表和信号处理与隔离电路。
数字电压表用于实时显示被测位移值,其读数由读数校准电位器调整。
信号处理与隔离电路的输出与数据采集系统的A/D转换器相连。
其量程为0~1500 mm,测量精度为<±0.05%FSR,频宽为100 Hz,模拟输出电压为0~10 V。
4) 电压测量电压输入通道将被测电压信号直接送至信号处理与隔离电路,与数据采集系统的A/D转换器相连。
本系统设有两路电压输入通道U1、U2,可用于测量其他形式的输入电压信号。
电压输入技术指标:输入量程:±10V 频宽:2.4KHz输入阻抗: 2 MΩ信号处理与隔离技术指标:输出电压范围:±10V 隔离电压:1000VDC精度:±0.1%FRS 频宽: 2.4KHz压力、位移、流量、电压输入量程:±10V转速输入量程:±5V5)D/A输出D/A输出由数据采集系统中的D/A转换器产生电压信号,经信号处理与隔离电路送至各比例多路阀放大器、比例伺服阀放大器、液压缸和马达加载阀放大器、变量泵排量控制放大器、柴油机转速控制器、变频器的输入端。
当上述放大器或控制器的调节模式通过旋钮设定为电调模式时,可以通过D/A输出来控制各相应的执行器工作。
其输出电压为±10V,输出阻抗<50Ω,最大驱动电流为10mA,频宽为2.4KHz。
6)数据采集系统数据采集系统由AXIOM公司AX6156工控机和研华公司PCL-818HG A/D卡、PCLD-8115端子板、PCL-727D/A卡、PCLD-880端子板组成,用于被测信号的采集、处理和测试过程控制。
4.2.3 试验系统的改造由于本课题所采用的试验台架-“负载敏感及功率回馈试验台”,为一通用试验台。
在某些细节上不能满足本课题的试验要求。
因此,作者对其进行了如下改造:1)原回路中所提供的负载敏感反馈管道为钢管,而工程机械中,常常采用高压软管作为反馈管道。
另外,只提供了一种管道内径,一种管道长度,不利于考察管道长度和内径的变化带来的影响。
因此,作者为其增置了一套软管作为压力反馈管道,可以十分方便地修改管道的长度。
软管通径有6毫米和12毫米两种。
2)原回路中所提供的变量泵具有恒功率、恒压力和比例变排量功能,没有负载敏感功能。
无法进行机液反馈负载敏感系统试验。
因此,作者为此变量泵增加了一负载敏感模块,使变量泵的输出流量和输出压力均能适应负载的要求变化而变化。
3)原回路中所提供的多路阀接口模块中具有一个三通流量调节阀,此阀适用于与定量泵组成开式负载敏感回路。
而本课题研究的主要对象是闭中心负载敏感回路,必须使此阀无效。
作者通过加工一顶杆替代阀中弹簧,使此阀的阀口始终处于关闭状,丛而使此阀处于无效状态,解决了多路阀的负载敏感问题。
4)原回路中所提供的部分压力传感器安装位置与测压点之间通过一条细长管道相连,这样就降低了压力传感器所能感受到的压力变化频率范围,不利于本课题对流体管道内高频脉动流信号进行测量。
作者通过加工过渡接头,使压力传感器安装位置与测压点之间距离缩短到最小,提高了压力测量的准确性和可靠性。
4.2.4 数据采集及处理程序试验系统中所有来自传感器的信号都通过隔离放大器接至研华公司PCL-818HG A/D卡的输入接口上,而所有电-机械转换器的控制信号均来自于系统中配置的输出控制模块PCL-727D/A卡。
这样就可以通过编制程序采集到系统各处压力、流量的变化曲线。
同时,采用适当的控制算法根据系统目前状态计算控制量,并通过D/A卡控制电液控制系统的行为方式。
作者编制了两套程序分别用于研究基于液压管道反馈的负载敏感系统以及基于电反馈的负载敏感系统。
图4-4和图4-5给出了其程序流程。
基于液压管道反馈的负载敏感系统中,反馈信号的传递是采用液压管道实现的,相应的程序仅对系统中各处11个通道的压力及流量信号进行采样,为了保证采样的实时性和准确性,程序利用了采集模块所提供DMA传输功能,这样数据的采集、存储和显示就能同时进行。
基于电反馈的负载敏感系统中,首先由传感器获得负载及管内压力变化的信息,然后通过一定的控制算法计算出控制液压源行为的负载敏感信号。
可见,为了研究电液负载敏感系统,程序在原有功能的基础上要增加根据系统当前状态变量计算控制变量的子程序以及输出控制量的子程序。
4.3 试验方案4.3.1 试验目的考察不同的管道参数下,负载敏感系统静动态特性的变化。
4.3.2 激励信号为了考察负载敏感系统的动态特性,必须给处于某一稳定状态下的系统施加一个激励信号。
激励信号通常有三种:脉冲信号、阶跃信号及正弦波。
本试验采用阶跃信号作为激励信号。
图4-4 机液负载敏感系统测试程序流程图图4-5 电液负载敏感系统测试程序流程图4.3.3 试验回路本试验将采用前面所介绍的试验系统中的变量泵、多路阀、液压缸A及长(短)管道构成单路负载敏感系统。
试验时可以通过切换截止阀的导通状态改变主油路管道长度,在两种主油路长度情况下,可以接入不同长度、不同内径的反馈油管来考察反馈管路的影响。
试验时所采用的回路简化原理图如图4-6所示。
图4-6 试验原理图4.3.4 试验时可改变的系统参数为了全面考察参数变化给负载敏感系统带来的影响,试验时尽可能的采用了多种不同管道参数及其他系统参数。
本试验系统中可改变的参数有:1)阶跃激励信号的初始状态及幅值;2)重力负载及恒力负载的大小;3)反馈管道的长度及内径;4)主油路(进油管路及回油管路)的长度;5)负载敏感模块中弹簧的预紧力,即稳定状态下,泵出口压力与负载压力的差值;6)变量泵上的可调阻尼,改变负载敏感泵的响应速度;4.4 试验结果与分析作者按以上所制定的试验方案,改变各种系统参数,对传统的机液负载敏感系统做了详细的试验研究,本小节给出所有的试验结果,并对其进行了初步的分析,得到一些结论,对进一步的理论研究和实践有着重要的指导意义。