模具设计之零件准备阶段(doc 10页)(正式版)
APQP阶段的资料准备
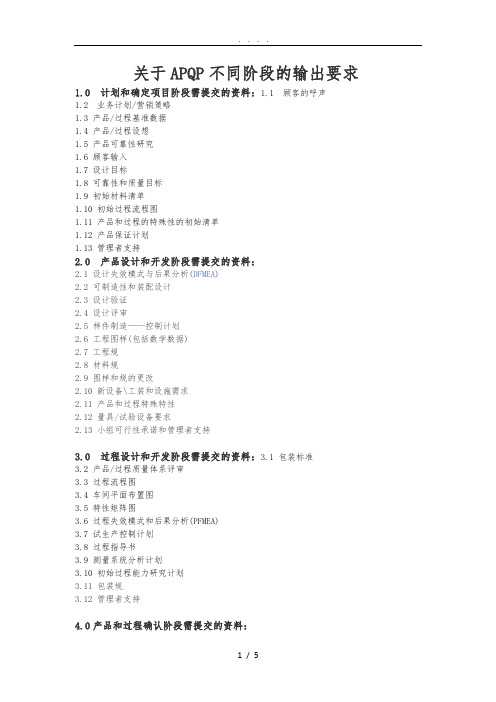
关于APQP不同阶段的输出要求1.0 计划和确定项目阶段需提交的资料:1.1 顾客的呼声1.2 业务计划/营销策略1.3 产品/过程基准数据1.4 产品/过程设想1.5 产品可靠性研究1.6 顾客输入1.7 设计目标1.8 可靠性和质量目标1.9 初始材料清单1.10 初始过程流程图1.11 产品和过程的特殊性的初始清单1.12 产品保证计划1.13 管理者支持2.0 产品设计和开发阶段需提交的资料:2.1 设计失效模式与后果分析(DFMEA)2.2 可制造性和装配设计2.3 设计验证2.4 设计评审2.5 样件制造——控制计划2.6 工程图样(包括数学数据)2.7 工程规2.8 材料规2.9 图样和规的更改2.10 新设备\工装和设施需求2.11 产品和过程特殊特性2.12 量具/试验设备要求2.13 小组可行性承诺和管理者支持3.0 过程设计和开发阶段需提交的资料:3.1 包装标准3.2 产品/过程质量体系评审3.3 过程流程图3.4 车间平面布置图3.5 特性矩阵图3.6 过程失效模式和后果分析(PFMEA)3.7 试生产控制计划3.8 过程指导书3.9 测量系统分析计划3.10 初始过程能力研究计划3.11 包装规3.12 管理者支持4.0产品和过程确认阶段需提交的资料:4.1 试生产4.2 测量系统评价4.3 初始过程能力研究4.4 生产件批准4.5 生产确认试验4.6 包装评价4.7 生产控制计划4.8 质量策划认定和管理者支持5.0 反馈、评定和纠正措施阶段需提交的资料:5.1 减少变差5.2 顾客满意5.3 交付和服务在前面补充一下,很多朋友提到SQE除了PPAP,其他就是简单参与参与,但是我多年的经验告诉我,光是打酱油是不行滴,参与时SQE更要擦亮自己的双眼,紧盯团队是否能有质量的输出一些东西给供应商。
更要在供应商和项目团队之间起到润滑剂和协调沟通者的作用,具体听我一一道来:第一阶段:计划和项目确定1.1)和研发人员一起做质量功能展开,顾客图纸评审如果前期就能知道哪些东西要给供应商做,那么SQE的意见是很重要的,比如某个零件没有现有适宜供应,或是国供应商根本没法达到那样的技术要求,一起评审顾客给的图纸,那么就要反馈顾客的图纸是不合理的!公差太紧之类的1.2)重要零件和质量特性确认SQE第一阶段就应该知道哪些是产品的重要零件!有什么重要质量特性!前期和研发和部项目经理沟通的越多,后期就越能避免被动,因为你们的客户也是希望你们尽早沟通,不懂就问!1.3)整体进展如果感觉有搞不定的供应商,会影响整个项目进度的,或是模具比较复杂,要试模多次的,都要提前把时间预留好,不然整个团队都会炮轰SQE开发供应商和开发新零件太慢!1.4)决定第一阶段里程碑是否可以完毕客户图纸还有疑惑的和错误的,业供应商都达不到的质量要求,你这时候不跳出来说不,那就死了第二阶段:产品设计和开发2.1)零件设计出来的图纸部审核研发画出来的图纸,理论上SQE要审核的,不然没有可制造性!或是没有重点!没有可靠性要求!没有外观要求!等等等2.2)选择最适宜的供应商!SQE要一定能够深入参与并决策的!如果选了不适宜的供应商,后期的痛苦。
模具的机械加工-课件 (一)

模具的机械加工-课件 (一)模具的机械加工-课件模具是用于制造工业产品所需的模板或模具,在现代生产中已成为重要的工具。
模具的制作过程需要高精度和高品质的加工,因此机械加工是模具制造的重要环节之一。
本文将介绍模具的机械加工,其步骤和技术要点。
一、机械加工步骤模具的机械加工一般需要经过以下五个步骤:1.零件的装夹和定位。
在加工之前需要将零件进行良好的固定,以保证在加工过程中不会出现偏差,损坏或误差。
2.粗加工。
在确定了零件的位置之后,需要采取粗加工操作,以确定模具的基本形状和尺寸。
3.中加工。
在完成粗加工之后,在零件上添加必要的尺寸和形状,从而得到所需的元件。
4.精加工。
在中加工后,继续对零件进行精加工操作,以达到更高的精度和更好的表面质量。
5.尺寸检测。
零件加工完成后,需要对其尺寸进行检测,以保证其满足要求。
二、机械加工技术要点在模具的机械加工过程中,需要掌握以下几个关键技术点:1.加工设备的选择和调节。
机械加工需要使用到不同的机器和设备(例如车床、镗床、铣床等),在加工之前需要对这些设备进行调整以满足加工需求。
2.零件的定位和装夹。
精确的定位和装夹是模具加工的关键环节。
需要采取适当的夹具来保证工件的稳定性和准确性。
3.工艺路线的设计和计算。
机械加工需要进行合理的工艺路线设计和计算,以确定加工的刀具,切割深度和切削速度,从而实现加工的高效和质量。
4.刀具的选择和刀具路径的设计。
在加工过程中,需要使用不同类型的刀具进行加工,例如铣刀、钻头和切削刃等。
选择合适的刀具和设计合理的刀具路径可以提高加工质量和精度,减少浪费和成本。
结语在模具制造过程中,机械加工是重要的环节之一。
准确和高效的机械加工可以保证模具的品质和生产效率,因此需要制定合理的工艺路线,精心设计工序和选用合适的设备和工具。
模具的机械加工涉及诸多知识和技巧,需要工程技术人员具备丰富的经验和专业的知识。
模具设计规范标准规范标准

模具设计标准规范1、目的:确保模具设计规范化,统一化.能将设计意图正确的传达给制造部门•避免或减少失误。
2、范围:工程部设计组接收工程部产品组转交的图文件、样品等资料到图纸发行为止之阶段均属之。
3、权责:3.1工程部设计组:负责模具开发设计及设计变更、2D/3D产品图面设计、3D建模、设计模具的组立图、3D拆模与拆电极、绘制零件图.3.2现场加工各组:加工各组的组长,在加工前需先审视加工图,若发现与原先检讨的不符合或有误,甚至不合理,需立即反应工程部检讨查核后,方可继续加工。
4、名词释义:无5、作图环境标准:5.1文字标准5.1.1字体。
数字及英文使用“ Arial ”字体,中文使用“标楷体”。
5.1.2文字大小。
为了使整套图面文字视觉效果一致,在标准图框(即1:1图框,A4为297*210)中,设定字高为3.0,宽0.85。
5.2图面标准5.2.1图框:为了便于查阅,装订,保存,图框统一标准如下:A0图框:841*1189 横印(附件一)A1图框:594*841 横印(附件二)A2图框:420*594 横印(附件三)A3图框:420*297 横印(附件四)A4图框:297*210 直印(附件五)5.2.2 图面要求5.2.2.1零件图面按照其在模具当中的位置分类摆放,以便于查找。
5.2.2.2尺寸标注方式。
除了圆以外,所有模板、模仁之尺寸均采用坐标标注方式5.2.2.3 视图投影关系:第三视角法。
5.2.3图档版本版本编号采用大写字母“ A”加上一位数字序号,数字序号按照图文件完成的时间先后顺序进行排列。
例如A1、A2、A3等。
524图层与线型:为了便于图形与尺寸的识别,图层与线型统一标准如下:5.3编码原则531模具结构和主要零件名称如下:5.3.2零件名称与对应的编号如下:5.3.2.1模胚部分编号 零件名称 编号 零件名称 A01 上固定板 A09 脱料板 A02 下固定板 A10 推板 A03 母模板A11 上流道板A04 公模板 A12 电热板 A05 母模承板 A13 脚垫 A06 公模承板 A14浇道脚垫A07 上顶针板A08下顶针板C&v:ly Plate C&v:ly PlateCere PlataSu.p?a r t Plate曲墊Stncer Block上頂針扳ijeclor fetoimer下嘩+板ijetior Plate下固疋扳Clwiw 囚定周廉Locitiina tins A Typ*Hf Laie浣口襯左c 书Spcue B UM I I CTypeGjuds 氏归11 AType :導拄Glide Pin冋曲ReburTt Pi in」带十西瞬三跖pKjectoi 3a ile Piri S T/JE如主SuiHDrl PilUi阖扳聲套Ejector Suide Elu^h停止誚Stop ?in丄回定扳7cpPUte5.3.3编码方式5.3.3.1模具编码方式。
模具设计之零件准备阶段

模具设计之零件准备阶段随着现代制造业的快速发展,模具设计作为其中重要的环节也逐渐被广泛应用和重视。
在模具设计的整个流程中,零件准备阶段被认为是至关重要的一步。
本文将从以下几个方面详细介绍模具设计之零件准备阶段的重要性和注意事项。
一、明确设计要求和标准在进行模具设计零件准备的前期,我们需要做的第一件事是明确设计要求和标准。
设计要求包括功能要求、技术要求、外观要求等,而标准则包括国际标准、国家标准和企业标准等。
明确这些要求和标准,可以为后续的设计工作提供清晰的方向和目标。
二、分析零件的结构和特点零件的结构和特点是决定模具设计方案的基础,因此在零件准备阶段必须对零件进行仔细的分析。
包括零件的形状、尺寸、质量要求、材料等。
同时,需要考虑零件的使用环境和使用寿命等因素。
了解这些特点可以更准确地确定模具的材料、结构和加工工艺等。
三、确定模具类型和结构在分析完零件的结构和特点后,需要根据具体情况来确定适合的模具类型和结构。
一般有冲压模具、注塑模具、压铸模具、拉伸模具等。
不同类型的模具需要采用不同的结构设计方案。
在此基础上,需要进一步优化模具结构以提高模具的使用寿命和生产效率。
四、制作零件立体模型和尺寸绘图制作零件的立体模型和尺寸绘图是模具设计中必不可少的一环。
这一步是为了更加准确地呈现零件的形状和尺寸,以便于后续根据绘图制作模具。
立体模型可以辅助设计人员更加清晰的了解零件形状和细节,尺寸绘图则是保证模具精度和制作准确度的关键因素。
五、作出根据具体情况调整在进行模具设计零件准备的阶段中,也需要根据具体情况进行不断的调整和优化。
可能会出现一些设计问题,或者是新的材料和工艺的应用,需要更加符合实际生产要求的模具设计方案。
因此,设计人员需要随时作出相应的调整,确保设计方案符合实际需求。
总之,模具设计之零件准备阶段是非常关键的一步,对于整个模具设计方案的成败起着决定性的作用。
只有在合理分析、明确设计要求、充分了解零件的特点、采用合适的模具类型和结构、制作准确的模型和绘图,并细致地进行调整和改进,才能设计出高质量的模具,满足生产需求,提高生产效率。
APQP各个阶段

APQP各个阶段第一篇:APQP各个阶段1.APQP有哪几个阶段?共分为五个阶段:第一阶段:计划和确定项目(立项)第二阶段:产品的设计和开发(样件试制)第三阶段:过程的设计和开发(试生产策划)第四阶段:产品和过程的确认(试生产)第五阶段:反馈评定和纠正措施(量产及持续改进)没有产品设计责任时:第一阶段:计划和确定项目第二阶段:样品试制第三阶段:试生产准备第四阶段:小批量试生产第五阶段:批量生产2.APQP与几大工具的关系以及导入时间.3.APQP与工具4.QPN 阶段顺序图5.QPN相关概念序号缩写英文原文解释OTSOFF TOOL SAMPLE用批量生产的工模器具制造出的样件 2PVSProduktions – Versuchs-Serie批量试生产 3TMATrial Manufacturing Agreement试制协议QSVQualitaes-Sicherungs-Vereinbarung质量保证协议 5BMGBau-Muster-Genehmigung产品工程样件性能检验认可 6 B-Freigabe采购认可D-Freigabe试制/0批量的认可 8P-Freigabe计划认可 9TL技术资料汇编LHLastenHeft要求汇总书记 11Pflichtenheft责任汇总书记MEMarkt-Einfuehrung市场导入MISManagement Informations-System管理信息系统 14Nullserie零批量QPNQualifizierungs-Programm Neuteile新零件质量提高计划 16SOPStart-Of-Production批量生产启动Standard Operating Procedure标准操作程序 17QSR质量体系要求APQPAdavanced part quality plan高级产品质量计划 19PPAPproduct part approval procedure生产件批准程序 20QSA质量体系评审MSAmeasurement system analysis测量系统分析 22FMEA失效模式及结果分析 23SPC统计过程控制第二篇:APQP各阶段清单APQP各阶段清单第一阶段:计划和确定项目序号表单责任部门市场调查分析表业务计划/营销策略产品/过程基准数据顾客要求可行性报告、风险评估报价单合同评审新产品开发申请表多方论证小组成员和职责表新产品开发进度计划表设计任务书产品质量保证计划设计目标确定产品可靠性和质量目标初始材料清单(产品明细表)初始过程流程图设备、工装、量具、试验装置初始清单产品和过程特殊特性初始清单产品保证计划阶段总结第二阶段:产品设计和开发序号表单责任部门DFMEA设计FMEA检查表产品可制造性和装配设计设计验证设计评审样件控制计划样件控制计划检查表工程图样工程规范材料规范图样和规范的更改新设备、工装和设施要求新设备、工装和设施采购产品和过程特殊特性清单量具和试验设备要求量具和试验设备采购生产率过程能力、成本指标新设备、工装和试验设备检查表小组可行性承诺和管理者支持第三阶段:过程设计和开发序号表单责任部门包装标准产品/过程质量体系检查表过程流程图过程流程图检查表车间平面布置图车间平面布置检查表特性矩阵图过程FMEA过程FMEA检查表试生产控制计划控制计划检查表作业指导书接收准则可追溯性预期设计质量、可靠性、可测量性数据测量系统分析计划(MSA)初始过程能力研究计划样件制造与测试包装规范阶段总结和管理者支持第四阶段:产品和过程确认序号表单责任部门试生产测量系统分析评价初始过程能力研究生产件批准生产确认试验试验报告包装评价生产控制计划生产控制计划检查表过程审核质量策划认定和管理者支持第五阶段:反馈、评定和纠正措施序号表单责任部门生产计划减少变差(X-R控制图)质量成本分析报告顾客满意度调查表顾客信息反馈更改或更新P、DFMEA和控制计划编制产品审核计划和性能检测计划项目经验教训总结第三篇:APQP的五个阶段APQP的五个阶段第一阶段:计划和确定项目第二阶段:产品设计和开发第三阶段:样件试制及过程设计开发第四阶段:产品和过程确认第五阶段:反馈评定和纠正措施(量产)没有产品设计责任时:第一阶段:计划和确定项目第二阶段:样品试制第三阶段:试生产准备第四阶段:小批量试生产第五阶段:批量生产APQP是五大手册之一,共分为五个阶段:第一阶段:计划和确定项目(立项)第二阶段:产品的设计和开发(样件试制)第三阶段:过程的设计和开发(试生产策划)第四阶段:产品和过程的确认(试生产)第五阶段:反馈评定和纠正措施(量产及持续改进)五大工具中APQP为产品质量先期策划,在策划的不同阶段,先后会用到其他几种参考手册介绍的方法.换句话说:“APQP是个筐,其他工具筐里装”.第四篇:APQP五大阶段APQP五大阶段,SQE需要做什么?问题背景:我司是发动机主机厂,在开发一款新发动机,我司实施APQP,某供方在为我司供活塞,也在实施活塞新项目APQP 问题:一、我司APQP五大阶段,各阶段主机厂SQE需要做什么?二、供方APQP五大阶段,各阶段主机厂SQE又需要做什么?该问题时国内某知名主机厂和外资某前三甲一级供方的面试题目,比较典型,请各位按照APQP五大阶段分阶段回答,感激不尽,共勉!附:APQP五阶段如下:第一阶段:计划和项目确定第二阶段:产品设计和开发第三阶段:过程设计和开发第四阶段:产品和过程确认第五阶段:反馈,评定和纠正措施回答在前面补充一下,很多朋友提到SQE除了PPAP,其他就是简单参与参与,但是我多年的经验告诉我,光是打酱油是不行滴,参与时SQE更要擦亮自己的双眼,紧盯团队是否能有质量的输出一些东西给供应商。
五金模具组立顺序
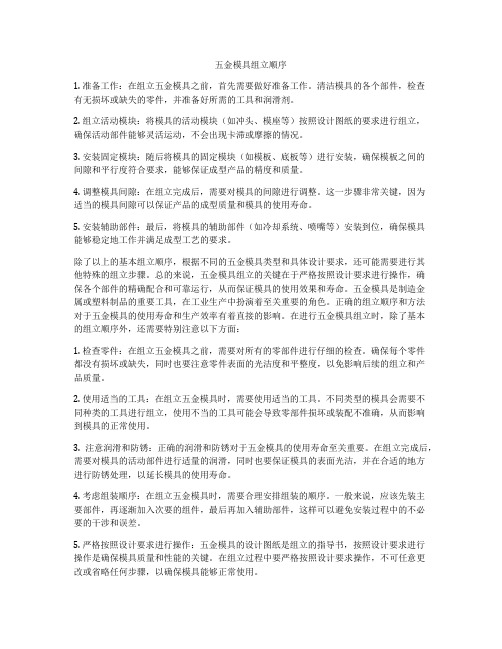
五金模具组立顺序1. 准备工作:在组立五金模具之前,首先需要做好准备工作。
清洁模具的各个部件,检查有无损坏或缺失的零件,并准备好所需的工具和润滑剂。
2. 组立活动模块:将模具的活动模块(如冲头、模座等)按照设计图纸的要求进行组立,确保活动部件能够灵活运动,不会出现卡滞或摩擦的情况。
3. 安装固定模块:随后将模具的固定模块(如模板、底板等)进行安装,确保模板之间的间隙和平行度符合要求,能够保证成型产品的精度和质量。
4. 调整模具间隙:在组立完成后,需要对模具的间隙进行调整。
这一步骤非常关键,因为适当的模具间隙可以保证产品的成型质量和模具的使用寿命。
5. 安装辅助部件:最后,将模具的辅助部件(如冷却系统、喷嘴等)安装到位,确保模具能够稳定地工作并满足成型工艺的要求。
除了以上的基本组立顺序,根据不同的五金模具类型和具体设计要求,还可能需要进行其他特殊的组立步骤。
总的来说,五金模具组立的关键在于严格按照设计要求进行操作,确保各个部件的精确配合和可靠运行,从而保证模具的使用效果和寿命。
五金模具是制造金属或塑料制品的重要工具,在工业生产中扮演着至关重要的角色。
正确的组立顺序和方法对于五金模具的使用寿命和生产效率有着直接的影响。
在进行五金模具组立时,除了基本的组立顺序外,还需要特别注意以下方面:1. 检查零件:在组立五金模具之前,需要对所有的零部件进行仔细的检查。
确保每个零件都没有损坏或缺失,同时也要注意零件表面的光洁度和平整度,以免影响后续的组立和产品质量。
2. 使用适当的工具:在组立五金模具时,需要使用适当的工具。
不同类型的模具会需要不同种类的工具进行组立,使用不当的工具可能会导致零部件损坏或装配不准确,从而影响到模具的正常使用。
3. 注意润滑和防锈:正确的润滑和防锈对于五金模具的使用寿命至关重要。
在组立完成后,需要对模具的活动部件进行适量的润滑,同时也要保证模具的表面光洁,并在合适的地方进行防锈处理,以延长模具的使用寿命。
冲压模具课程设计零件

冲压模具课程设计零件一、教学目标本课程的学习目标包括知识目标、技能目标和情感态度价值观目标。
知识目标要求学生掌握冲压模具的基本原理、类型及应用;技能目标要求学生能够运用冲压模具设计软件进行简单的模具设计;情感态度价值观目标要求学生培养创新意识、团队合作精神及良好的职业操守。
通过对本章的学习,学生应能够:1.描述冲压模具的基本原理和类型;2.解释冲压模具在制造业中的应用;3.使用冲压模具设计软件进行简单模具设计;4.展现创新意识、团队合作精神及良好的职业操守。
二、教学内容本课程的教学内容主要包括冲压模具的基本原理、类型及应用,冲压模具设计软件的使用,以及创新设计方法和团队合作实践。
具体教学内容安排如下:1.冲压模具的基本原理和类型:介绍冲压模具的工作原理、结构特点及分类;2.冲压模具在制造业中的应用:分析冲压模具在各行业中的应用案例;3.冲压模具设计软件的使用:教授如何运用冲压模具设计软件进行模具设计;4.创新设计方法和团队合作实践:引导学生进行创新设计,培养团队合作精神。
三、教学方法本课程将采用讲授法、讨论法、案例分析法和实验法等多种教学方法。
1.讲授法:用于讲解冲压模具的基本原理、类型及应用;2.讨论法:学生讨论冲压模具设计中的问题,促进学生思考;3.案例分析法:分析冲压模具在实际应用中的案例,帮助学生理解;4.实验法:让学生动手操作,实际体验冲压模具的设计和制作过程。
四、教学资源本课程的教学资源包括教材、参考书、多媒体资料和实验设备。
1.教材:选用权威、实用的教材,为学生提供系统、全面的学习资源;2.参考书:提供相关领域的参考书籍,丰富学生的知识体系;3.多媒体资料:制作精美的PPT、视频等多媒体资料,提高学生的学习兴趣;4.实验设备:配置完善的实验设备,让学生能够亲自动手实践。
五、教学评估本课程的教学评估将采用多元化的评估方式,包括平时表现、作业、考试等,以确保评估的客观性和公正性,并全面反映学生的学习成果。
模具设计准备过程

模具设计准备过程概述模具设计是制造行业中重要的一环,它涉及到产品的生产过程中使用的各种模具的设计和制造。
在开始进行模具设计之前,我们需要进行一系列的准备工作,以确保设计的顺利进行和最终的模具质量。
步骤1. 研究产品需求在进行模具设计之前,我们首先需要了解产品的需求和要求。
这包括产品的尺寸要求、功能需求、批量要求等等。
通过与产品开发团队的沟通和交流,我们可以获得所需的技术规范和要求。
2. 收集设计所需资料在进行模具设计之前,我们需要收集一些设计所需的资料。
这包括产品的图纸、CAD文件、材料规格以及相关的技术要求和标准等。
这些资料将为我们提供设计过程中的基础信息,并指导我们进行后续的设计工作。
3. 确定模具类型根据产品的需求和要求,我们需要确定所需要的模具类型。
常见的模具类型包括注塑模具、压铸模具、冲压模具等等。
不同的模具类型有不同的设计和制造要求,因此在确定模具类型后,我们可以对设计进行进一步细化。
4. 进行产品分析在进行模具设计之前,我们需要对产品进行分析。
这包括产品的结构分析、功能分析以及工艺分析等。
通过对产品的分析,我们可以确定所需要的模具结构和设计要求,并为后续的设计提供参考依据。
5. 进行模具设计在进行模具设计之前,我们需要通过CAD软件创建模具的三维模型。
根据产品的需求和要求,我们可以进行模具的结构设计、零件设计以及装配设计等。
在设计过程中,我们需要遵循一系列的设计原则和规范,以确保设计的合理性和可行性。
6. 模拟分析和优化设计在完成模具的初步设计后,我们可以进行模拟分析和优化设计。
通过模拟分析,我们可以评估模具的性能和工艺性,并根据评估结果进行相应的优化设计。
这有助于提高模具的生产效率和质量。
7. 制造工艺规划在完成模具设计后,我们需要进行制造工艺规划。
这包括模具的加工工艺、零件加工工艺以及组装工艺等。
通过制定详细的工艺规划,可以确保模具的高效制造和装配。
8. 制造模具在进行制造工艺规划后,我们可以开始制造模具。
- 1、下载文档前请自行甄别文档内容的完整性,平台不提供额外的编辑、内容补充、找答案等附加服务。
- 2、"仅部分预览"的文档,不可在线预览部分如存在完整性等问题,可反馈申请退款(可完整预览的文档不适用该条件!)。
- 3、如文档侵犯您的权益,请联系客服反馈,我们会尽快为您处理(人工客服工作时间:9:00-18:30)。
零件准备阶段
1. 打开零件
单击SolidWorks中的文件→打开菜单命令,在弹出的打开文件对话框中设置文件类型为Parasolid实体格式文件,通过浏览功能选中Switch Cover文件,单击打开按钮,将模型文件调入,如图1所示,使用文件→另存为菜单命令将其保存为同名的Sldprt格式文件。
图1
提示:在新版SolidWorks中,所有的转换程序插件均已集成到SolidWorks 软件中,并且在主菜单的打开和另存为对话框中始终是可用的文件类型。
这些转换程序可根据需要动态加载和卸载。
它们不再需要激活,也不再会显示为工具、插件下的插件。
2. 数据准备
这个零件是通过输入输出接口转入的,它将需要重新调整方向和位置,以适应为模具设计而建立的装配体。
从SolidWorks主菜单中单击IMOLD→Data Preparation菜单命令或直接从IMOLD工具条中单击工具图标,弹出数据准备的对话框。
在其中Host assembly name输入框中输入主装配体的名称1000 Host Assembly,然后单击Browse按钮,从弹出的浏览对话框中选中刚才另存的文件,在Derived part name中自动出现转出的文件名,如图2所示,同时系统创建1000 Host Assembly装配体,并将Switch Cover模型文件置入。
图2
3. 零件定位
的表面,将其加入到图15的列表中,表面的颜色也随之而改变。
图16
4. 选择型腔面
在图15中左侧Cavity框中
5. 搜寻型芯和型腔表面
单击图17中的Search功能按钮,屏幕出现一个状态显示窗口提示系统在进行计算,完成后模型表面的所有面以分模线为界都将被指定为型芯表面或型腔表面,同时被赋以颜色,它们的名称也将加入到各自的曲面组中,如图18所示。
图18
6. 交换曲面
放大零件侧壁上的一个通槽,右键单击槽中的一个直面,如图19所示,从弹出的快捷菜单中单击选择相切命令,选中槽中相切的所有面,然后单击图18中的按钮,将这些选中的曲面加入到型腔曲面组中。
图19
按同样的方法将其余两个通槽的面也加入到Cavity曲面组中。
7. 提取型腔表面
单击图14中的Extract功能按钮,出现图20所示的提取功能界面,设置提取面为Cavity,在Name for the knitted中输入型腔曲面名称为Cavity Surface,然后单击Extract!功能按钮。
图20
8. 提取型芯表面
型腔表面提取后图20中Extract faces for选项自动变为Core,设置型芯表面的名称为Core Surface,然后单击Extract!功能按钮,提取型芯表面。
完成后单击Done!按钮。
单击图14中示。
图26
在特征管理设计树中将新创建的放射曲面命名为Parting Surface。
9. 编辑型腔
单击图21所示的型芯/型腔创建对话框中Utilities标签,进入应用功能界面中。
从零件编辑打开窗口中选中1000_cavity零件,然后单击Edit-in-context功能按钮在装配体环境中编辑零件,如图27所示。
图27
拷贝型
图31
10. 编辑型芯
从图27中选择1000_Core零件然后单击Edit-in-context功能按钮在装配体环境中编辑零件。
11. 拷贝型芯曲面
单击图27中的Cop
12. 完成分模过程
在Switch Cover_top装配体中,从特征管理设计树中将Switch Cover Derived零件中的所有曲面隐藏。
整体装配体显示如图52所示。
(使用了透明属性)
保存并关闭所有的文件。
图52
布局和浇注系统
13. 调用设计方案
使用IMOLD工具条中的图标工具,调出图8所示的方案对话框,单击Browse功能按钮,找到Switch
Cover_top文件并打开,将设计方案调入。
14. 启动布局设计师
从
15. 加入一个侧浇口
在图56中设置浇口创建类型为Edge方式,根据图57所示设置浇口参数。
图57
16. 浇口定位
现在将在模型上创建一个点用来对浇口定位。
单击图56中的Create point。
,将弹出Smart point智能点创建对话框。
选择前视图方向上的左边一个装配结构上的分模线处的一条边,并设置Edge control中的选项为Closest,如图58所示。
单击Create按钮,创建一个点。
图58
提示:在1000_feed 文件中创建了一个点特征:SmartPoint 。
17. 浇口方向
从图56中单击
Point
垂直约束
图72
18. 确定流道参数
从IMOLD 工具条
图79
注意:这里创建了一个非平衡式的分流道,用来表示它是如何实现的。
单击Cancel 按钮退出Feed Design 对话框。
19. 完成浇注系统设计
保存并关闭所有文件,完成浇注系统的设计过程。
模架设计
20. 调用设计方案
从IMOLD主菜单中单击图标,在弹出的方案控制界面中单击Browse,从打开文件对话框中浏览
到IMOLD的顶层装配
21. 完成模架设计
从图98中单击Cancel退出螺钉设置界面。
模架图形显示如图99所示。
图99
从IMOL工具条中单击保存所有文件,然后关闭所有文件。
滑块和顶块设计
22. 调入方案
单
完成后如图139所示。
图139
退出装配体编辑模式,返回到顶层装配体中。
23. 完成滑块顶块创建
保存并关闭所有文件。
顶出系统设计
重完成后的顶杆如图150所示。
图150 在特征管理设计树中将1000_ejector的显示改为查看特征方式。
24. 完成顶杆设计
单击Cancel退出顶杆设计对话框。
保存并关闭所有文件。
冷却水道设计
25. 打开设计方案并隐藏组件
通过IMOLD工具条中的打开设计方案。
将
图174
26. 继续
重的前视图基准面为反向重合。
27. 完成
恢复显示所有的组件。
保存关闭所有文件。