超经典的精馏塔资料
精馏塔基础知识

塔基础知识1:化工生产过程中,是如何对塔设备进行定义的?答:化工生产过程中可提供气(或汽)液或液液两相之间进行直接接触机会,达到相际传质及传热目的,又能使接触之后的两相及时分开,互不夹带的设备称之为塔。
塔设备是化工、炼油生产中最重要的设备之一。
常见的、可在塔设备中完成单元操作的有精馏、吸收、解吸和萃取等,因此,塔设备又分为精馏塔、吸收塔、解吸塔和萃取塔等。
2:塔设备是如何分类的?答:按塔的内部构件结构形式,可将塔设备分为两大类:板式塔和填料塔。
按化工操作单元的特性(功能),可将塔设备分为:精馏塔、吸收塔、解吸塔、反应塔(合成塔)、萃取塔、再生塔、干燥塔。
按操作压力可将塔设备分为:加压塔、常压塔和减压塔。
按形成相际接触界面的方式,可将塔设备分为:具有固定相界面的塔和流动相界面的塔。
3:什么是塔板效率?其影响因素有哪些?答:理论塔板数与实际塔板数之比叫塔板效率,它的数值总是小于1。
在实际运行中,由于气液相传质阻力、混合、雾沫夹带等原因,气液相的组成与平衡状态有所偏离,所以在确定实际塔板数量时,应考虑塔板效率。
系统物性、流体力学、操作条件和塔板结构参数等都对塔板效率有影响,目前塔板效率还不能精确地预测。
4:塔的安装对精馏操作有何影响?答::(1)塔身垂直.倾斜度不得超过1/1000,否则会在塔板上造成死区,使塔的精馏效率下降;(2)塔板水平.水平度不超过正负2mm,塔板水平度如果达不到要求,则会造成液层高度不均匀,使塔内上升的气相易从液层高度小的区域穿过,使气液两相不能在塔板上达到预期的传热,传质要求.使塔板效率降低。
筛板塔尤其要注意塔板的水平要求。
对于舌形塔板,浮动喷射塔板,斜孔塔板等还需注意塔板的安装位置,保持开口方向与该层塔板上液体的流动方向一致。
(3)溢流口与下层塔板的距离应根据生产能力和下层塔板溢流堰的高度而定。
但必须满足溢流堰板能插入下层受液盘的液体之中,以保持上层液相下流时有足够的通道和封住下层上升蒸汽必须的液封,避免气相走短路。
精馏塔设备概述
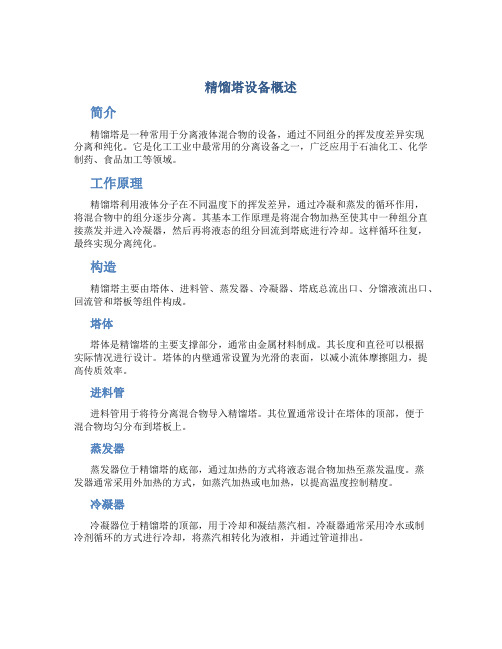
精馏塔设备概述简介精馏塔是一种常用于分离液体混合物的设备,通过不同组分的挥发度差异实现分离和纯化。
它是化工工业中最常用的分离设备之一,广泛应用于石油化工、化学制药、食品加工等领域。
工作原理精馏塔利用液体分子在不同温度下的挥发差异,通过冷凝和蒸发的循环作用,将混合物中的组分逐步分离。
其基本工作原理是将混合物加热至使其中一种组分直接蒸发并进入冷凝器,然后再将液态的组分回流到塔底进行冷却。
这样循环往复,最终实现分离纯化。
构造精馏塔主要由塔体、进料管、蒸发器、冷凝器、塔底总流出口、分馏液流出口、回流管和塔板等组件构成。
塔体塔体是精馏塔的主要支撑部分,通常由金属材料制成。
其长度和直径可以根据实际情况进行设计。
塔体的内壁通常设置为光滑的表面,以减小流体摩擦阻力,提高传质效率。
进料管进料管用于将待分离混合物导入精馏塔。
其位置通常设计在塔体的顶部,便于混合物均匀分布到塔板上。
蒸发器蒸发器位于精馏塔的底部,通过加热的方式将液态混合物加热至蒸发温度。
蒸发器通常采用外加热的方式,如蒸汽加热或电加热,以提高温度控制精度。
冷凝器冷凝器位于精馏塔的顶部,用于冷却和凝结蒸汽相。
冷凝器通常采用冷水或制冷剂循环的方式进行冷却,将蒸汽相转化为液相,并通过管道排出。
塔底总流出口塔底总流出口是精馏塔的最底部出口,用于排出未蒸发的液态组分。
通常通过阀门控制流量和压力。
分馏液流出口分馏液流出口位于精馏塔的中间位置,用于排除已经分离纯化的组分。
也通过阀门进行流量和压力的调控。
回流管回流管从冷凝器中将冷凝的液相通过管道回流到塔底,作为冷却液。
回流液的流量和塔底总流出口的控制可以实现进一步的分离纯化。
塔板塔板是精馏塔内组织分离过程的关键部分,用于实现质量和传质的分离。
塔板通常为水平平板状,上面设置气体和液体的流通孔,以及液体收集槽等构造。
应用领域精馏塔在化工工业中有着广泛的应用,常见的应用领域包括:•石油化工:用于原油的分离和石油产品的精制,如汽油、柴油、润滑油等的提纯。
精馏塔的结构和工作原理(简版专享)

气体出 液体进
气体进
液体出
简约版
3
填料塔
在圆柱形壳体内装填一定高度的填 料,液体经塔顶喷淋装置均匀分布 于填料层顶部上,依靠重力作用沿 填料表面自上而下流经填料层后自 塔底排出;气体则在压强差推动下 穿过填料层的空隙,由塔的一端流 向另一端。气液在填料表面接触进 行质、热交换,两相的组成沿塔高 连续变化。
气体出 液体进
气体进
填料层
液体出
简约版
4
填料塔和板式塔的对比
11
压降 空塔气速 塔效率
板式塔 较大 较大 较稳定,效率较高
填料塔 小尺寸填料较大;大尺寸填料及规整填料较小 小尺寸填料较小;大尺寸填料及规整填料较大 传统填料低;新型乱堆及规整填料高
持液量 液气比 安装检修 材质 造价
较大 适应范围较大 较易 常用金属材料 大直径时较低
精馏塔的结构和 工作原理
简约版
1
精馏塔的功能和分类
基本功能:形成气液两相充分接触的相界面,使质、热的传递快速有效 地进行,接触混合与传质后的气、液两相能及时分开,互不夹带。
精馏塔分类:精馏塔的种类很多,按接触方式可分为连续接触式(填料 塔)和逐级接触式(板式塔)两大类,在吸收和蒸馏操作中应用极广 。
较小 对液量有一定要求 较难 金属及非金属材料均可 新型填料投资较大
简约版
5
板式塔塔板类型
溢流
板式塔
无溢流
降液管
液
相
堰
液相
气相
气相
错流式:泡罩、浮阀、筛板
穿流塔板、逆流塔板
喷射式:舌型、浮舌、浮动喷射式
简约版
6
板式塔塔板类型
溢流塔板 :塔板间有专供液体溢流的降液管 (溢流管),横向流过塔板的 流体与由下而上穿过塔板的气体呈错流或并流流动。 板上液体的流径与液层的高度可通过适当安排降液管的位置及堰的高度 给予控制,从而可获得较高的板效率,但降液管将占去塔板的传质有效 面积,影响塔的生产能力。
精馏塔

精馏塔单元一、工作原理简述二、典型精馏塔动画演示三、工艺流程简介四、组态画面及设备说明一、工作原理简述精馏是化工生产中分离互溶液体混合物的典型单元操作,其实质是多级蒸馏,即在一定压力下,利用互溶液体混合物各组分的沸点或饱和蒸汽压不同,使轻组分(沸点较低或饱和蒸汽压较高的组分)汽化,经多次部分液相汽化和部分气相冷凝,使气相中的轻组分和液相中的重组分浓度逐渐升高,从而实现分离。
精馏过程的主要设备有:精馏塔、再沸器、冷凝器、回流罐和输送设备等。
精馏塔以进料板为界,上部为精馏段,下部为提留段。
一定温度和压力的料液进入精馏塔后,轻组分在精馏段逐渐浓缩,离开塔顶后全部冷凝进入回流罐,一部分作为塔顶产品(也叫馏出液),另一部分被送入塔内作为回流液。
回流液的目的是补充塔板上的轻组分,使塔板上的液体组成保持稳定,保证精馏操作连续稳定地进行。
而重组分在提留段中浓缩后,一部分作为塔釜产品(也叫残液),一部分则经再沸器加热后送回塔中,为精馏操作提供一定量连续上升的蒸气气流。
二、精馏塔动画演示1.板式塔结构2.板式塔工作原理3.精馏塔实观4.精馏塔剖面图5.板式精馏塔1.板式塔结构2.板式塔工作原理3精馏塔实观4精馏塔剖面图5.板式精馏塔三、工艺流程简介本单元是一种加压精馏操作,原料液为脱丙烷塔塔釜的混合液,分离后馏出液为高纯度的C4产品,残液要是C5以上组分。
67.80C的原料液经流量调节器FIC101控制流量(14056Kg/h)后,从精馏塔DA405的第16块塔板(全塔共32块塔版)进料。
塔顶蒸气经全凝器EA419冷凝为液体后进入回流罐FA408;回流罐FA408的液体由泵GA412A/B抽出,一部分作为回流液由调节器FC104控制流量(9664KG/H)送回DA405第32层塔板;另一部分则作为产品,其流量由调节器FC103控制(6707Kg/h)。
回流罐的液位由调节器LC103与FC103构成的串级控制回路控制。
3 精馏塔简介
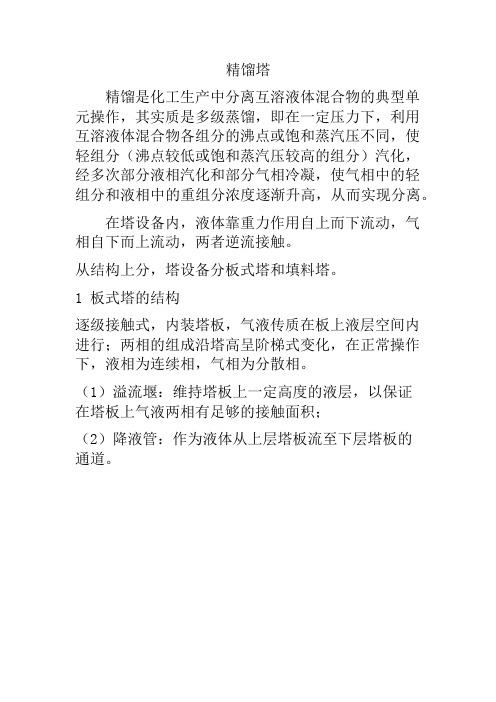
精馏塔精馏是化工生产中分离互溶液体混合物的典型单元操作,其实质是多级蒸馏,即在一定压力下,利用互溶液体混合物各组分的沸点或饱和蒸汽压不同,使轻组分(沸点较低或饱和蒸汽压较高的组分)汽化,经多次部分液相汽化和部分气相冷凝,使气相中的轻组分和液相中的重组分浓度逐渐升高,从而实现分离。
在塔设备内,液体靠重力作用自上而下流动,气相自下而上流动,两者逆流接触。
从结构上分,塔设备分板式塔和填料塔。
1 板式塔的结构逐级接触式,内装塔板,气液传质在板上液层空间内进行;两相的组成沿塔高呈阶梯式变化,在正常操作下,液相为连续相,气相为分散相。
(1)溢流堰:维持塔板上一定高度的液层,以保证在塔板上气液两相有足够的接触面积;(2)降液管:作为液体从上层塔板流至下层塔板的通道。
板式塔特点:生产能力大,塔板效率稳定,操作弹性大,造价低,检修、清洗方便。
2 填料塔的结构(1)填料层:提供气液接触的场所。
(2)液体分布器:均匀分布液体,以避免发生沟流现象。
(3)液体再分布器:避免壁流现象发生。
(4)支撑板:支撑填料层,使气体均匀分布。
(5)除沫器:防止塔顶气体出口处夹带液体。
优点:(1)生产能力大。
填料塔内件开孔率大,空隙率大,液泛点高。
(2)分离效率高。
填料塔每米理论级远大于板式塔,尤其在减压及常压条件下。
(3)压降小。
空隙率高,阻力小。
(4)持液量小。
(5)操作弹性大。
缺点:填料造价高;当液体负荷较小时不能有效地润湿填料表面,使传质效率降低;不能直接用于有悬浮物或容易聚合的物料;对侧线进料和出料等复杂精馏不太适合等。
填料作用(1)提供气液接触面积;(2)强化气体湍动,降低气相传质阻力;(3)更新液膜表面,降低液相传质阻力。
填料塔与板式塔的比较对于许多逆流气液接触过程,填料塔和板式塔都是可以适用的,设计者必须根据具体情况进行选用。
填料塔和板式塔有许多不同点,了解这些不同点对于合理选用塔设备是有帮助的。
①填料塔操作范围较小,特别是对于液体负荷变化更为敏感。
精馏塔课件
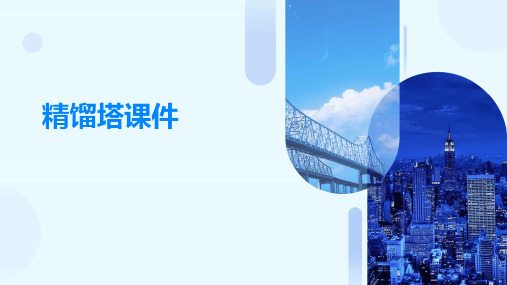
精馏塔的能耗降低
节能型再沸器
采用高效换热器,如板式换热器、翅 片管式换热器等,降低再沸器的能耗 。
优化操作压力
能量回收
利用冷凝器、再沸器的余热进行回收 利用,减少额外能耗。
适当降低操作压力,减小气体压缩机 的能耗。
精馏塔的环保改进
减少挥发性有机物排放
采用高效密封技术,减少精馏过程中的挥发性有机物泄漏。
THANKS
感谢观看
供决策支持。
在线监测与故障诊断
03
开发在线监测系统和故障诊断技术,实时监测精馏塔运行状态
,预测和预防故障发生。
绿色环保的精馏塔发展
1 2
节能减排技术
研究节能减排技术,降低精馏过程的能耗和物耗 ,减少污染物排放。
环保型填料和溶剂
开发环保型填料和溶剂,减少对环境的污染和破 坏。
3
资源回收利用
研究精馏塔副产物的回收利用技术,实现资源的 高效利用。
进料
将原料送入进料口,控制 流量和温度等参数。
加热
通过加热器将原料加热至 所需温度,使液体汽化。
精馏塔的操作流程
分馏
蒸汽在塔内上升过程中与液体 进行多次逆流接触,实现组分
分离。
冷凝
蒸汽在塔顶冷凝器中冷凝成液 体,收集产品。
回流
部分液体回流至塔内,增加分 离效果。
采出
将合格产品从塔底采出,并控 制流量和温度等参数。
精馏塔课件
目录
• 精馏塔简介 • 精馏塔的设计与操作 • 精馏塔的优化与改进 • 精馏塔的应用与案例分析 • 精馏塔的发展趋势与展望
01
CATALOGUE
精馏塔简介
精馏塔的定义
01
精馏塔是一种用于分离液体混合 物的塔式设备,通过加热和冷凝 的方式实现不同成分的分离。
精馏塔的介绍

无论是平衡蒸馏还是简单蒸馏,虽然可以起到一定的分离作用,但是并不能将混合物分离为具有一定量的高纯度产品。
在石油化工生产中常常要求获得纯度很高的产品,通过精馏过程可以获得这种高纯度的产品。
精馏过程所用的设备称为精馏塔,大体上可以分为两大类:①板式塔,气液两相总体上作多次逆流接触,每层板上气液两相一般作交叉流。
②填料塔,气液两相作连续逆流接触。
一般的精馏装置由精馏塔塔身、冷凝器、回流罐,以及再沸器等设备组成。
进料从精馏塔中某段塔板上进人塔内,这块塔板称为进料板。
进料板将精馏塔分为上下两段,进料板以上部分称为精馏段,进料板以下部分称为提馏段。
塔板的分类板式塔是一种应用极为广泛的气液传质设备,它由一个通常呈圆柱形的壳体及其中按一定间距水平设置的若干塔板所组成。
板式塔正常工作时,液体在重力作用下自上而下通过各层塔板后由塔底排出;气体在压差推动下,经均布在塔板上的开孔由下而上穿过各层塔板后由塔顶排出,在每块塔板上皆储有一定的液体,气体穿过板上液层时,两相接触进行传质。
板式塔种类繁多,通常可分类如下:按塔板结构分,有泡罩板、筛板、浮阀板、网孔板、舌形板等等。
历史上应用最早的有泡罩塔及筛板塔,20世纪50年代前后,开发了浮阀塔板。
现应用最广的是筛饭和浮阀塔板,其他不同型式的塔板也有应用。
一些新型塔板或传统塔板的改进型也在陆续开发和研究中。
按气液两相的流动方式分,有错流式塔板和逆流式塔板,或称有降液管塔板和无降液管塔板。
有降液管塔板应用极广,它们具有较高的传质效率和较宽的操作范围;无降液管的逆流式塔板也常称为穿流式塔板,气液两相均由塔板上的孔道通过。
塔板结构简单,整个塔板面积利用较充分。
常用的有穿流式筛板、穿流式栅板、穿流式波纹板等。
按液体流动型式分,有单流形、双流形、U形流形及其他流形(如四流形、阶梯形、环流形等)。
单流形塔板应用最为广泛,它结构简单,液流行程长,有利于提高塔板效率。
但当塔径或液量过大时,塔板上液面梯度会较大,导致气液分布不均,或造成降液管过载,影响塔板效率和正常操作。
精馏塔介绍

一、精馏塔原理
精馏塔是进行精馏的一种塔式气液接 触装置。利用混合物中各组分具有不 同的挥发度,即在同一温度下各组分 的蒸气压不同这一性质,使液相中的 轻组分(低沸物)转移到气相中,而气 相中的重组分(高沸物)转移到液相中, 从而实现分离的目的。
气液分离
塔设备
精馏塔的分类
板式塔:气液两相总体上作多 次逆流接触,每层板上气液两 相一般作交叉流。
再沸器的分类
虹吸式再沸器
优点: 结构紧凑、占地面积小、传热系数高; 壳程不能机械清洗,不适宜高粘度、或脏的传热介质; 塔釜提供气液分离空间和缓冲区; 设备被直接安装在塔旁由于管线系统简单,故设备造价低。 缺点: 管长通常受塔裙高度、传热面积的限制; 维修和清洗困难。
精馏塔的工艺流程
填料塔:气液两相作连续逆流 接触。
精馏塔的基本设备组成
精馏塔塔身
回流罐
冷凝器
再沸器
精馏塔效率的关键
一、气相与液相的接触面积 接触面积越大,越利于热量交换,越利于物料分离,分离效果越好。 二、塔板或填料可通过性 气相可通过性越好,精馏过程的压力降越小,越利于精馏。
第一条和第二条相悖!!
填料塔的介绍
填料的分类
填料是填料塔的核心部件,主要分为:散装填料和规整填料两大类。
散装填料
拉西环
鲍尔环
阶梯环
弧鞍环
矩鞍环
金属intalox
填料的分类
规整填料
不锈钢波纹板填料
丝网波纹填料
陶瓷波纹板填料
格栅填料
液体分布器ห้องสมุดไป่ตู้
槽式液体分布器
列管式分布器
盘式分布器
再沸器的分类
釜式再沸器
优点: 性能可靠,受水动力的影响很小; 在高真空条件下,也能很好运行; 增加管间节距,可获得很高的热流密度; 在小温差的条件下,运行状况良好; 在近临界压力下,性能仍然可靠。 缺点: 釜式再沸器是所有再沸器中最容易结垢的; 壳体较大,造价较高。
- 1、下载文档前请自行甄别文档内容的完整性,平台不提供额外的编辑、内容补充、找答案等附加服务。
- 2、"仅部分预览"的文档,不可在线预览部分如存在完整性等问题,可反馈申请退款(可完整预览的文档不适用该条件!)。
- 3、如文档侵犯您的权益,请联系客服反馈,我们会尽快为您处理(人工客服工作时间:9:00-18:30)。
用到的基本工具是⎪⎩⎪⎨⎧相平衡关系热量衡算物料衡算一、全塔物料衡算(塔顶、塔底产品量的确定)对图l0-20中的虚线圈作全塔物料衡算,可得W D F +=全塔轻组分物料街算WD FWxDxFx+=由于设计时F ,F x ,D x ,W x 均已知,产品量D 和W 可以联解上二式得到。
式中 F ──进料量,kmol/h 或kg/h ;D ──塔顶产品量,kmol/h 或kg/h ;W ──塔底产品量,kmol/h 或kg/h ; Fx ──进料中轻组分的组成,摩尔分率或质量分率;Dx ──塔顶产品中轻组分的组成,摩尔分率或质量分率:W x ──塔底产品中轻组分的组成,摩尔分率或质量分率。
二、理论板数的计算(一)精馏段的物料衡算──精馏段的操作线方程1.精馏段物料衡算相邻两层板间汽液两流组成间(相遇两流)的关系,可通过对塔顶至精馏段任意两层板间截面所作的物料衡算导出。
对图10-2l 中的虚线图作总物料衡算,可得D L V n n +=+1 易挥发组分的物料衡算方程为Dn n n n Dxx L y V +=++11或Dn n n nn x DL D x D L L y +++=+1式(10-55)至(10-57)中n x ──离开n 板液相中轻组分的摩尔分率; 1+n y ──离开n+1板气相中轻组分的摩尔分率; n L ──离开n 板液相摩尔流率,kmol/h ;1+n V ──离开n+1板汽相摩尔流率,kmol/h 。
2.恒摩尔流假定(1)恒摩尔汽化 假定在精馏塔的精馏段内,由每层板上升的汽相摩尔流率都相等,在提馏段也是如此。
即精馏段 V V V V V n n =====+121 (10-58) 提馏段''1''2'1VV V V V n n =====+ (10-59)式中 V ──精馏段每板的汽相摩尔流率,kmol /h ;'V──提馏段每板的汽相摩尔流率,kmol /h 。
应当指出,精馏段和提馏段汽相摩尔流率不一定相等。
(2)恒摩尔溢流 假定在精馏塔的精馏段内,由每层板下降的液相摩尔流率都相等,在提馏段也是如此。
即LL L L L n n =====+121''1''2'1LL L L L n n =====+ 式中 L ──精馏段内液体的摩尔流量,kmol/h ;'L──提馏段内液体的摩尔流量,kmol/h 。
同样,精馏段和提馏段的液相摩尔流率不一定相等。
在恒摩尔流假定下,计算将大为简化,问题是此假定是否合理。
汽、液相在塔板上接触时,如果每有1摩尔蒸气冷凝就相应有1摩尔液体汽化,则汽相相液相在接触后其摩尔流率将保持不变,恒摩尔流假定就可以成立。
要实现上述情况需满足以下两个条件:①组分的摩尔汽化潜热相同。
②汽、液相接触时由于温度不同而传递的显热可以忽略。
③塔的保温良好,热损失可以忽略。
3.精馏段操作线方程在恒摩尔流假定下,式(10-57)可以写成Dn n x V D x V L y +=+1 (10-62)而D L V += (10-63) 将式(10-63)代入式(10-62)并令D L R /=,则可得Dn n x R x R R y 1111+++=+ (10-64)式(10-64)中R 为回流比。
它是精馏的重要参数。
式(10-64)联系了精馏段回流比、产品组成等重要操作参数,故称为精馏段操作线方程。
它表达了在一定的操作条件下,精馏段自第n 层板下降的液相组成n x 和与之相邻的下一层板(即第1+n 层板)上升的汽相组成1+n y 之间的关系。
(二)提馏段的操作线方程──提馏段的物料衡算对图l0-22所示的提馏段由塔底至第m 与1+m 层板间截面分别作总物料衡算和轻组分物料衡算,并应用恒摩尔流假定可得; 总物料衡算:W V L +=''易挥发组分的物料衡算方程为 Wm m Wxy V x L +=+'1''' (10-66)式中 'L ──提馏段各板的液相流率,kmol/h ;'V ──提馏段各板的汽相流率,kmol /h ; 。
'm x ──第m 层板下降液相中轻组分的摩尔分率;'1+m y ──第1+m 层板上升气相中轻组分的摩尔分率。
将式(10-65)代入式(10-66),消去'V ,可得Wm m x WL W x WL L y ---=+'''''1式(10-67)称为提馏段操作线方程。
它表达了在一定操作条件下提馏段内自第m 层板下降的液相组成'm x 与其相邻的下层板上升的汽相组成'1+m y 的关系。
要应用提馏段操作线方程式,必须先计算出'L ,它除了与精馏段回流量L 有关外,还与进料流率及其热状况有关。
(三)进料段的物料衡算精馏段与提馏段的汽相和液相流量是通过进料联系在一起的。
1.汽、液混合物进料,进料的液化分率为q ,10<<q原料进塔后,汽相部分与提馏段上升的汽相汇合进入精馏段,原料中液相部分与精馏段液相汇合进入提馏段。
此时 qF L L +='F q V V )1('-+= 2.饱和液体进料,1=qqF L L +='=F L + ')1('V F q V V =-+= 3.饱和蒸气进料,0=q qF L L +='=LF V F q V V +=-+=')1(' 4.过冷液体进料,1>qqF L L +='F q V V )1('-+=q 值称为进料热状况参数,推导如下: 进料段作总物料衡算可得 ''L V L V F +=++对进料段作热量衡算得: ''''L V L V FHL VHLHHV FH+=++式中 F H ──原料液的焓,J/mol ;',V V H H ──分别为进料板上、下处的饱和汽相的焓,J/mol ; ',L L H H ──分别为进料板上、下处的饱和液相的焓,J/mol 。
由于相邻两层板的温度和浓度变化不大,故可认为 'V VHH ≈,'L L HH ≈于是式(10-69)可以写成LVLVFHL VHLH HV FH''+=++将式(10-68)代入上式消去'V 并整理可得))('()(L VFVH HL L HHF --=-即 LV FVHHH H FLL --=-'令进料的摩尔气化热蒸汽所需热量每摩尔进料气化为饱和≈--=LV FVHHH H qq值称为进料热状况参数。
当进料为汽、液混合物时,设进料的液化分率为q ,对进料作热量衡算可得VLFFHq qFHFH)1(-+=整理得LVFVHHH H q --=可见,当进料为汽、液混合物时,进料热状况参数q即为进料的液化分率。
5.过热蒸气进料,0<qqF L L +='F q V V )1('-+=此种情况恰与过冷液体进料相反,当进料汽相进入精馏段最下一层塔板时,汽相温度必先降至其露点,然后才能与液相进行等摩尔冷凝和汽化,在由进料温度降到露点时,要放出热量,使与之相接触的液相额外汽化一部分。
因此自精馏段最下一块板上升之汽相量包括三个部分,即自提馏段上升之汽相量'V 、原料量以及为将进料温度降至其露点温度所需额外汽化的量V ∆。
由于此额外汽化量,使下降到提馏段的液相量比精馏段的L 少,即L L <'。
(四)逐板计算法求理论板数在导出了精馏段和提馏段的操作线方程以后,可以交替使用操作线方程和相平衡关系来求得所需的理论板数。
若塔顶装设全凝器,则图10-20中D x y =1,由相平衡关系解出1x ,将1x 代入式(10-62)可算出2y ,由2y 通过相平衡关系又可算出2x ,如此重复计算,直到组成与进料组成相近为止。
对于饱和液相进料,如果算得1-<≤n F n x x x ,则说明第n 层理论板是加料板,上述计算共使用过n-1次相平衡关系,因此精馏段需要n-1层理论板。
此后,可改用提馏段操作线,图10-2l 中进入提馏段顶层板的液相组成近似为1-n x ,由式(10-78)可算得'1y ,再利用相平衡关系求出'1x ,由'1x 利用式(10-78)求出'2y ,如此重复计算,直到W m x x <'为止。
由于一般再沸器的分离能力相当于一层理论板,故提馏段所需的理论板层数应为(n-1)。
逐板计算法是求理论板层数的基本方法之一,概念清晰,计算结果较准确,但该法比较繁琐,计算量大。
(五)x y -图解法求理论板数x y -图解法与逐板计算法并无实质性区别,其基本方法也是交替运用操作线方程和相平衡关系。
只是不用数学方法计算,而是x y -图上进行。
1.由x y -图解法求理论板数可按如下步骤进行(1)在直角坐标上给出恒压下的x y -平衡曲线和对角线。
(2)作精馏段操作线。
(3)q 线。
(4)作提馏段操作线。
(5)在平衡线与操作线之间作梯级。
精馏段操作线方程Dx R x R R y 111+++=将其标绘在x y -图上,是一条斜率为1+R R 截距为Dx R 11+的直线。
在x y -图上定出y 轴上的截距和操作线与对角线的交点),(D D x x ,然后连一直线。
提馏段操作线方程Wx W qF L Wx W qF L qFL y -+--++=,由于提馏段操作线截距往往很小,且为负值,作图既不方便又不准确,因而常常取它与精馏段操作线的交点及与对角线的交点),(W W x x 来作图。
两段操作线的交点方程式可由联解两操作线方程式而得。
⎩⎨⎧-=+=WD Wxx L y V Dx Lx Vy ''将上两式相减WDWxDxx L L y V V ++-=-)'()'(由式(10-73)、(10-72)、(10-53)可得 F q V V )1('--=- qF L L -=-' FWDFxWxDx=+FFxqFx Fy q +-=--)1(Fx q x q q y 111---=上式称为q 线方程,在x y -图上代表两段操作线交点的轨迹。
其实质是进料的物料平衡关系,在x y -图上是斜率为1-q q、截距为Fx q 11--的直线。
同样,可以将y =x 代入式(10-84)找到q 线与对角线的交点坐标F x x =,F y y =。