八螺杆挤出的计算公式
螺杆计算

根据经验假设压缩段末H 3=(0.04~0.05)DH 3=6根据经验假设压缩比ε=3H 1=0.5{D-[D 2-4εH 3(D-H 3)]1/2}H 1=20.656mm取H 1=20mm根据经验:螺距S=D=120mm螺旋升角tan θ=S/πDθ=17.665°根据经验:螺棱宽b=(0.08~0.12)Db=10mm螺槽宽B=S-bB=110mm螺槽法向宽度W=B ×cos θW=104.813mm螺楞法向宽度e=b ×cos θe=9.528mm螺杆平均直径D —=D-H 1D —=100mm螺旋根部升角θ1=25.534°螺旋平均升角θ—=20.903°螺杆根径D f =D-2H 1D f=80mm根据经验:摩擦系数f=0.3K=D—/D×(sinθ—+fcosθ—)/(cosθ—-f sinθ—)=100/120×(sin20.903°+0.3×cos20.903°)/(cos20.903-0.3×sin20.903°)∴K=0.642螺旋根部升角θ1=25.534°M=2H1/W×sinθ[K+(D—/D)cotθ—]+ sinθ[K+( D f/D)cotθ1]=2×20/104.813×sin17.665°[0.642+(100/120)cot20.903°]+ sin17.665°[0.642+( 80/120)cot25.534°]∴M=0.945sinθ=[(1+K2-M2)1/2-K×M]/(1+K2)=[(1+0.6422-0.9452)1/2-0.642×0.945]/(1+0.6422)sinθ=0.081θ=4.623°间隙δ=0.15H3δ=1 mmQ/n=π2DH1(D-H1)×tanθ×tanθ/ (tanθ+ tanθ)[W/(W+ε)] =π2×0.12×0.02×(0.12-0.02)×tan17.665×tan4.623/(tan17.665+ tan4.623)[104.813/(104.813+3)]Q/n=1.485×10-4 m3/r密度ρ=1400Kg/ m3质量输送率Q g/n=Q/n×ρQ g/n=1.485×10-4×1400Q g/n=0.208Kg/ rn=20.032r/ min输送段流速V f=G/ρ[π/4(D2- D f2)-eH1/sinθ—]V f=(250/3600)/1400[π/4(0. 122-0.082)-0.009528×0.02/sin20.903] =0.0086m/s假设压缩段密度ρ1=2000Kg/ m3压缩段流速V b= G/ρ1 [π/4(D2- D R2)-eH3/sinθ—]V b=(250/3600)/2000[π/4(0. 122-0.1082)-0.009528×0.006/sin20.903] V b=0.017 m/s假设加料段入口压力P1=0.4MPa压缩段出口压力P2=2.0MPa(P2=1.5, 2.0 ,2.5 ,3.0MPa时,根据公式e w=πNDWZFcosθ(P2-P1)/Ln(P2/P1)计算得19.24 ,23.24 ,26.49,29.83KW,),能量消耗e w=πNDWZFcosθ(P2-P1)/Ln(P2/P1)假设输送长度Z=6me w=3.142×(20.032/60)×0. 12×0.104813×6×0.3×cos4.623(1600000)/Ln5e w=23.533KW螺杆轴向压力P a=(4.3059-3.094Lg△P)△P×AA=πD2/4P a=(4.3059-3.094×Lg2)2×3.142×0.122/4P a=0.076MN螺杆压应力ζy= P a/A rA r=πD f2/4ζy=0.076/(3.142×0.082/4)ζy=15.185 MN/m2M n=9549N max/n max·η=9549×23.533/20.032×0.95M n=10656.988N·m剪应力η= M n/(W n×106)W n=π·D f3/16η=1065.988/[(3.142×0.083/16) ×106]η=105.993MN/m2强度校核(ζy2+4η2)1/2≤[ζ](15.185+4×105.9932)1/2=212.529MN/m2≤[ζ]刚度校核1167M n(1+μ)/ED4≤[1]1167×10656.988×(1+0.3)/200×109×0.124=0.390≤[1]。
第二节 挤出理论

1)螺杆特性线: 挤出机均化段的流率方程如下:
Q
n
f
P
由上式可知:α、β、γ、L3是与螺杆几何参数相关的 常数,η.ηf也是常数。因此上述方程实际上成了Q与 △P的线性方程。
其直线的斜率为:
f
如下图,我们称AB为螺杆的特性线。它是一组相互 平行的直线族,随螺杆n转速的改变而改变。
d. 漏流: 由机筒与螺棱间隙δ处形成的倒流。方向沿螺杆轴 线方向,并由机头向后。流量用QL表示。对提高挤 出机流量起反作用。
实际上螺槽中熔体 的总的流动是这几 种流动的总和。 挤出机的生产能力 即:
Q=Qd-Qp-QL
3.均化段功率消耗于三部分: 螺槽中剪切物料所消耗的功率;
保持螺槽中压力所消耗的功率;
是由物料受机筒的摩擦拖曳引起的,最大处速度为
V1, 起到挤出物料的作用,流量用Qd表示。
b、倒流(压力流)
由机头、口型等阻力 元件产生的压力引起
Vb Vb
机筒表面
的回流。方向与正流
y
方向相反,流量为QP
正流
xz 螺杆表面
倒流
c.横流(环流):
由垂直于螺棱方向的分速度V2引起(如图), 使物料 在螺槽内产生翻转运动。方向与V2方向相同,对生 产能力没有影响,但能促进物料的混合、搅拌和热 交换,流量Qc=0
这就是说,人们还没有完全认识挤出过程。关于挤 出过程的理论正在发展中。
目前常用的关于挤出过程的理论,是在常规全螺纹 螺杆中建立起来的。
根据实验,物料自料斗加入到由机头挤出,要通过 几个职能区:固体输送区、熔融区和熔体输送区。
固体输送区,通常限定在自加料斗开始算起的几个 螺距中,在该区,物料向前输送并被压实,但仍以 固体状存在。
挤出量计算方式
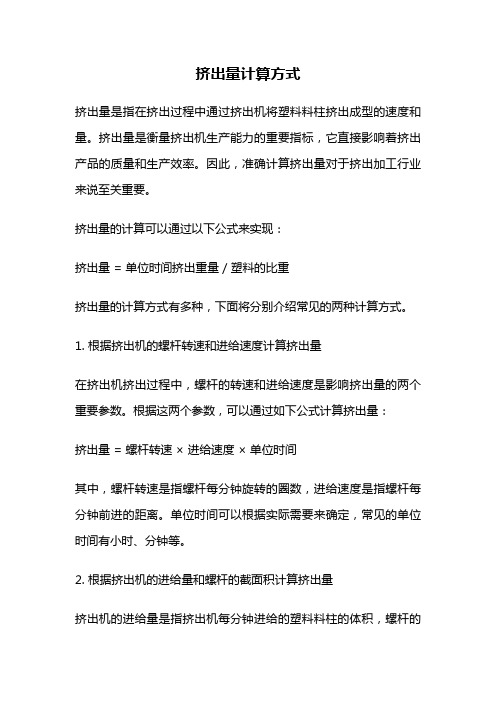
挤出量计算方式挤出量是指在挤出过程中通过挤出机将塑料料柱挤出成型的速度和量。
挤出量是衡量挤出机生产能力的重要指标,它直接影响着挤出产品的质量和生产效率。
因此,准确计算挤出量对于挤出加工行业来说至关重要。
挤出量的计算可以通过以下公式来实现:挤出量 = 单位时间挤出重量 / 塑料的比重挤出量的计算方式有多种,下面将分别介绍常见的两种计算方式。
1. 根据挤出机的螺杆转速和进给速度计算挤出量在挤出机挤出过程中,螺杆的转速和进给速度是影响挤出量的两个重要参数。
根据这两个参数,可以通过如下公式计算挤出量:挤出量 = 螺杆转速× 进给速度× 单位时间其中,螺杆转速是指螺杆每分钟旋转的圈数,进给速度是指螺杆每分钟前进的距离。
单位时间可以根据实际需要来确定,常见的单位时间有小时、分钟等。
2. 根据挤出机的进给量和螺杆的截面积计算挤出量挤出机的进给量是指挤出机每分钟进给的塑料料柱的体积,螺杆的截面积是指螺杆槽横截面的面积。
根据这两个参数,可以通过如下公式计算挤出量:挤出量 = 进给量 / 螺杆截面积进给量可以通过测量料筒进给的长度来确定,螺杆截面积可以通过测量螺杆槽的宽度和深度来计算。
在实际应用中,根据不同的生产情况和需求,可以选择适合的挤出量计算方式。
同时,还需要注意以下几点:1. 在进行挤出量计算时,需要准确测量和记录相关参数,以确保计算结果的准确性。
2. 挤出量的计算结果应该与实际生产情况相符合,如果存在较大的偏差,可能需要检查和调整挤出机的工作参数。
3. 挤出量的大小会直接影响挤出产品的质量和生产效率。
合理控制挤出量可以提高产品的均匀性和一致性,降低生产成本。
4. 挤出量的计算对于挤出加工行业来说非常重要,它不仅可以用于生产计划和生产效率评估,还可以作为产品质量控制的依据。
挤出量的准确计算对于挤出加工行业来说至关重要。
通过选择合适的计算方式,并严格控制相关参数,可以提高产品的质量和生产效率,进而提升企业的竞争力和盈利能力。
挤出机螺杆压缩比计算公式
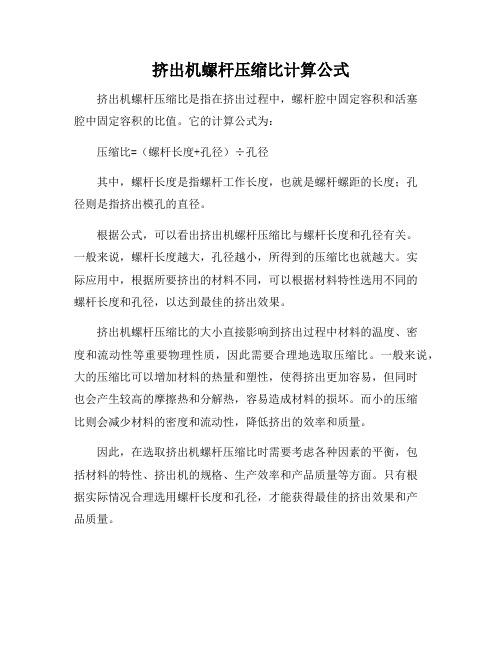
挤出机螺杆压缩比计算公式
挤出机螺杆压缩比是指在挤出过程中,螺杆腔中固定容积和活塞
腔中固定容积的比值。
它的计算公式为:
压缩比=(螺杆长度+孔径)÷孔径
其中,螺杆长度是指螺杆工作长度,也就是螺杆螺距的长度;孔
径则是指挤出模孔的直径。
根据公式,可以看出挤出机螺杆压缩比与螺杆长度和孔径有关。
一般来说,螺杆长度越大,孔径越小,所得到的压缩比也就越大。
实
际应用中,根据所要挤出的材料不同,可以根据材料特性选用不同的
螺杆长度和孔径,以达到最佳的挤出效果。
挤出机螺杆压缩比的大小直接影响到挤出过程中材料的温度、密
度和流动性等重要物理性质,因此需要合理地选取压缩比。
一般来说,大的压缩比可以增加材料的热量和塑性,使得挤出更加容易,但同时
也会产生较高的摩擦热和分解热,容易造成材料的损坏。
而小的压缩
比则会减少材料的密度和流动性,降低挤出的效率和质量。
因此,在选取挤出机螺杆压缩比时需要考虑各种因素的平衡,包
括材料的特性、挤出机的规格、生产效率和产品质量等方面。
只有根
据实际情况合理选用螺杆长度和孔径,才能获得最佳的挤出效果和产
品质量。
螺杆长径比计算公式
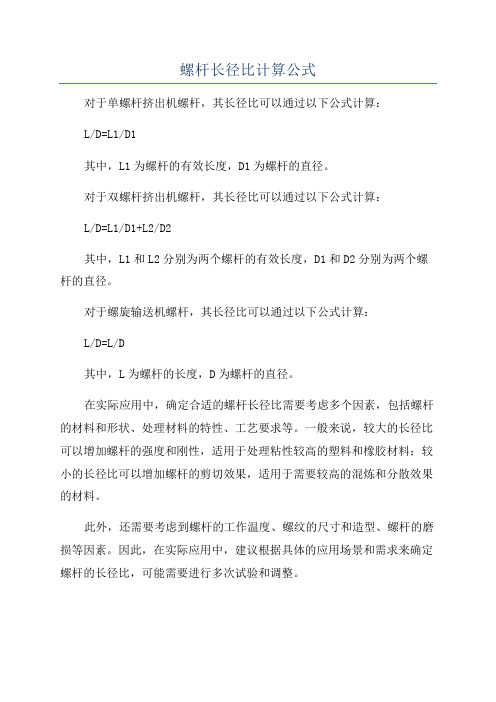
螺杆长径比计算公式
对于单螺杆挤出机螺杆,其长径比可以通过以下公式计算:
L/D=L1/D1
其中,L1为螺杆的有效长度,D1为螺杆的直径。
对于双螺杆挤出机螺杆,其长径比可以通过以下公式计算:
L/D=L1/D1+L2/D2
其中,L1和L2分别为两个螺杆的有效长度,D1和D2分别为两个螺杆的直径。
对于螺旋输送机螺杆,其长径比可以通过以下公式计算:
L/D=L/D
其中,L为螺杆的长度,D为螺杆的直径。
在实际应用中,确定合适的螺杆长径比需要考虑多个因素,包括螺杆的材料和形状、处理材料的特性、工艺要求等。
一般来说,较大的长径比可以增加螺杆的强度和刚性,适用于处理粘性较高的塑料和橡胶材料;较小的长径比可以增加螺杆的剪切效果,适用于需要较高的混炼和分散效果的材料。
此外,还需要考虑到螺杆的工作温度、螺纹的尺寸和造型、螺杆的磨损等因素。
因此,在实际应用中,建议根据具体的应用场景和需求来确定螺杆的长径比,可能需要进行多次试验和调整。
螺纹类各种计算
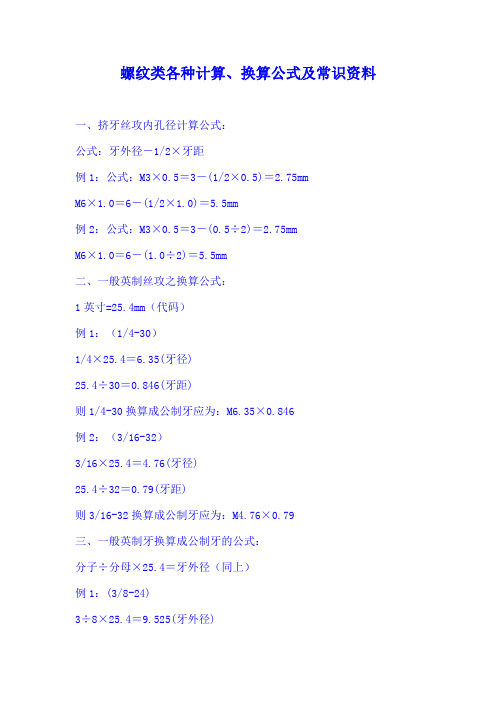
螺纹类各种计算、换算公式及常识资料一、挤牙丝攻内孔径计算公式:公式:牙外径-1/2×牙距例1:公式:M3×0.5=3-(1/2×0.5)=2.75mmM6×1.0=6-(1/2×1.0)=5.5mm例2:公式:M3×0.5=3-(0.5÷2)=2.75mmM6×1.0=6-(1.0÷2)=5.5mm二、一般英制丝攻之换算公式:1英寸=25.4mm(代码)例1:(1/4-30)1/4×25.4=6.35(牙径)25.4÷30=0.846(牙距)则1/4-30换算成公制牙应为:M6.35×0.846例2:(3/16-32)3/16×25.4=4.76(牙径)25.4÷32=0.79(牙距)则3/16-32换算成公制牙应为:M4.76×0.79三、一般英制牙换算成公制牙的公式:分子÷分母×25.4=牙外径(同上)例1:(3/8-24)3÷8×25.4=9.525(牙外径)25.4÷24=1.058(公制牙距)则3/8-24换算成公制牙应为:M9.525×1.058四、美制牙换算公制牙公式:例:6-326-32 (0.06+0.013)/代码×6=0.1380.138×25.4=3.505(牙外径)25.4÷32=0.635(牙距)那么6-32换算成公制牙应为:M3.505×0.635 1、孔内径计算公式:牙外径-1/2×牙距则应为:M3.505-1/2×0.635=3.19那么6-32他内孔径应为3.192、挤压丝攻内孔算法:下孔径简易计算公式1:牙外径-(牙距×0.4250.475)/代码=下孔径例1:M6×1.0M6-(1.0×0.425)=5.575(最大下孔径)M6-(1.0×0.475)=5.525(最小)例2:切削丝攻下孔内径简易计算公式:M6-(1.0×0.85)=5.15(最大)M6-(1.0×0.95)=5.05(最小)M6-(牙距×0.860.96)/代码=下孔径例3:M6×1.0=6-1.0=5.0+0.05=5.05五、压牙外径计算简易公式:1.直径-0.01×0.645×牙距(需通规通止规止)例1:M3×0.5=3-0.01×0.645×0.5=2.58(外径)例2:M6×1.0=6-0.1×0.645×1.0=5.25(外径)六、公制牙滚造径计算公式:(饱牙计算)例1:M3×0.5=3-0.6495×0.5=2.68(车削前外径)例2:M6×1.0=6-0.6495×1.0=5.35(车削前外径)七、压花外径深度(外径)外径÷25.4×花齿距=压花前外径例:4.1÷25.4×0.8(花距)=0.13 压花深度应为0.13八、多边形材料之对角换算公式:1.四角形:对边径×1.414=对角径2.五角形:对边径×1.2361=对角径3.六角形:对边直径×1.1547=对角直径公式2: 1.四角:对边径÷0.71=对角径2.六角:对边径÷0.866=对角径九、刀具厚度(切刀):材料外径÷10+0.7参考值十、锥度的计算公式:公式1:(大头直径-小头直径)÷(2×锥度的总长)=度数等于查三角函数值公式2:简易(大头直径-小头直径)÷28.7÷总长=度数滚牙径计算公式一、60°牙型的外螺纹中径计算及公差(国标GB 197/196)a. 中径基本尺寸计算:螺纹中径的基本尺寸=螺纹大径-螺距×系数值公式表示:d/D-P×0.6495例:外螺纹M8螺纹中径的计算8-1.25×0.6495=8-0.8119≈7.188b.常用的6h外螺纹中径公差(以螺距为基准)上限值为”0”下限值为P0.8-0.095 P1.00-0.112 P1.25-0.118P1.5-0.132 P1.75-0.150 P2.0-0.16P2.5-0.17上限计算公式即基本尺寸,下限值计算公式d2-hes-Td2即中径基本尺寸-偏差-公差M8的6h级中径公差值:上限值7.188 下限值:7.188-0.118=7.07C常用的6g级外螺纹中径基本偏差: (以螺距为基准)P 0.80-0.024 P 1.00-0.026 P1.25-0.028 P1.5-0.032P1.75-0.034 P2-0.038 P2.5-0.042上限值计算公式d2-ges即基本尺寸-偏差下限值计算公式d2-ges-Td2即基本尺寸-偏差-公差例M8的6g级中径公差值:上限值7.188-0.028=7.16 下限值:7.188-0.028-0.118=7.042注:①以上的螺纹公差是以粗牙为准,对细牙的螺纹公差相应有些变化,但均只是公差变大,所以按此控制不会越出规范界限,故在上述中未一一标出.②螺纹的光杆坯径尺寸在生产实际中根据设计要求的精度和螺纹加工设备的挤压力的不同而相应比设计螺纹中径尺寸加大0.04—0.08之间,为螺纹光杆坯径值,例我们公司的M8外螺纹6g级的螺纹光杆坯径实在7.08—7.13即在此范围.③考虑到生产过程的需要外螺纹在实际生产的未进行热处理和表面处理的中径控制下限应尽量保持在6h级为准二、60°内螺纹中径计算及公差(GB 197 /196)a. 6H级螺纹中径公差(以螺距为基准)上限值:P0.8+0.125 P1.00+0.150 P1.25+0.16 P1.5+0.180P1.25+0.00 P2.0+0.212 P2.5+0.224下限值为”0”,上限值计算公式2+TD2即基本尺寸+公差例M8-6H内螺纹中径为:7.188+0.160=7.348 上限值:7.188为下限值b. 内螺纹的中径基本尺寸计算公式与外螺纹相同即D2=D-P×0.6495即内螺纹中径螺纹大径-螺距×系数值c. 6G级螺纹中径基本偏差E1(以螺距为基准)P0.8+0.024 P1.00+0.026 P1.25+0.028 P1.5+0.032P1.75+0.034 P1.00+0.026 P2.5+0.042例:M8 6G级内螺纹中径上限值:7.188+0.026+0.16=7.374下限值:7.188+0.026=7.214上限值公式2+GE1+TD2即中径基本尺寸+偏差+公差下限值公式2+GE1即中径尺寸+偏差三、外螺纹大径的计算及公差(GB 197/196)a. 外螺纹的6h大径上限值即螺纹直径值例M8为φ8.00上限值公差为”0”b. 外螺纹的6h级大径下限值公差(以螺距为基准)P0.8-0.15 P1.00-0.18 P1.25-0.212 P1.5-0.236 P1.75-0.265P2.0-0.28 P2.5-0.335大径下限计算公式:d-Td 即螺纹大径基本尺寸-公差例:M8外螺纹6h大径尺寸:上限为φ8,下限为φ8-0.212=φ7.788c. 外螺纹6g级大径的计算与公差6g级外螺纹的基准偏差(以螺距为基准)P0.8-0.024 P1.00-0.026 P1.25-0.028 P1.5-0.032 P1.25-0.024 P1.75 –0.034P2.0-0.038 P2.5-0.042上限计算公式 d-ges 即螺纹大径基本尺寸-基准偏差下限计算公式 d-ges-Td 即螺纹大径基本尺寸-基准偏差-公差例: M8 外螺纹6g级大径上限值φ8-0.028=φ7.972下限值φ8-0.028-0.212=φ7.76注:①螺纹的大径是由螺纹光杆坯径及搓丝板/滚丝轮的牙型磨损程度来决定的,而且其数值在同样毛坯及螺纹加工工具的基础上与螺纹中径成反比出现即中径小则大径大,反之中径大则大径小.②对需进行热处理和表面处理等加工的零件,考虑到加工过程的关系实际生产时应将螺纹大径控制在6h级的下限值加0.04mm以上,如M8的外螺纹在搓(滚)丝的大径应保证在φ7.83以上和7.95以下为宜.四、内螺纹小径的计算与公差a. 内螺纹小径的基本尺寸计算(D1)螺纹小径基本尺寸=内螺纹基本尺寸-螺距×系数例:内螺纹M8的小径基本尺寸 8-1.25×1.0825=6.646875≈6.647b. 内螺纹6H级的小径公差(以螺距为基准)及小径值计算P0.8 +0. 2 P1.0 +0. 236 P1.25 +0.265 P1.5 +0.3 P1.75 +0.335P2.0 +0.375 P2.5 +0.48内螺纹6H级的下限偏差公式D1+HE1即内螺纹小径基本尺寸+偏差注:6H级的下偏值为“0”内螺纹6H级的上限值计算公式=D1+HE1+TD1即内螺纹小径基本尺寸+偏差+公差例:6H级M8内螺纹小径的上限值 6.647+0=6.6476H级M8内螺纹小径的下限值 6.647+0+0.265=6.912c. 内螺纹6G级的小径基本偏差(以螺距为基准)及小径值计算P0.8 +0.024 P1.0 +0.026 P1.25 +0.028 P1.5 +0.032 P1.75 +0.034P2.0 +0.038 P2.5 +0.042内螺纹6G级的小径下限值公式=D1+GE1即内螺纹基本尺寸+偏差例: 6G级M8内螺纹小径的下限值 6.647+0.028=6.6756G级M8内螺纹小径的上限值公式D1+GE1+TD1即内螺纹基本尺寸+偏差+公差例: 6G级M8内螺纹小径的上限值是6.647+0.028+0.265=6.94注:①内螺纹的牙高直接关系到内螺纹的承载力矩的大小,故在毛坯生产中应尽量在其6H级上限值以内②在内螺纹的加工过程中,内螺纹小径越小会给加工具——丝锥的使用效益有所影响.从使用的角度讲是小径越小越好,但综合考虑时一般采用小径的在中限至上限值之间,如果是铸铁或铝件时应采用小径的下限值至中限值之间③内螺纹6G级的小径在毛坯生产中可按6H级执行,其精度等级主要考虑螺纹中径的镀层,故只在螺纹加工时考虑丝锥的中径尺寸而不必考虑光孔的小径。
螺杆容积计算公式
螺杆容积计算公式注塑机计算公式一.理论出容积π/4=0.785)(1)螺杆直径²*0.785*射出行程=理论射出容积(cm³);(2)理论射出容积/0.785/螺杆直径=射出行程(cm).二.射出重量:理论射出容积*塑料比重*射出常数(0.95)理想=射出重量(gr);三.射出压力:(1)射出缸面积²/螺杆面积²*系统最大压力(140kg/cm²)²=射出压力(kg/cm²);(2)射出缸直径²/螺杆直径²*系统最大压力(140kg/cm²)=射出压力(kg/cm²);(3)料管组合最大射出压力*实际使用压力(kg/cm²)/系统最大压力(140kg/cm²)=射出压力(kg/cm²).四.射出速率:(1)螺杆面积(cm²)*射出速度(cm/sec)=射出速率(cm³/sec);(2)螺杆直径(cm²)*0.785*射出速度(cm/sec)=射出速度(cm³/sec).五.射出速度:(1)射出速率(cm³/sec)/螺杆面积(cm²)=射出速度(cm/sec);(2)泵浦单转容积(cc/rev)*马达转速(rev/sec)/60(秒)/射出面积(cm²)=射出速度(cm/sec).(马达转速RPM:60HZ------1150,50HZ-----958)六.射出缸面积;射出压力(kg/cm²)/系统最大压力(140kg/cm²)*料管面积(cm²)=射出缸面积(cm²);单缸---(射缸直径²-柱塞直径²)*0.785=射出缸面积(cm²);双缸---(射缸直径²-柱塞直径²)*0.785*2=射出缸面积(cm²).七.泵浦单转容积:射出缸面积(cm²)*射出速度(cm/sec)*60秒/马达转速=泵浦单转容积(cc/sec).(马达转速RPM: 60HZ------1150,50HZ-----958)八.螺杆转速及油压马达单转容积:泵浦单转容积(cc/rec)*马达转速(RPM)/油压马达单转容积=螺杆转速;。
挤出机螺杆压强计算公式
挤出机螺杆压强计算公式
压强的计算公式是p=F/S,压强的单位是帕斯卡,符号是Pa。
物体所受的压力与受力面积之比叫做压强,压强用来比较压力产生的效果,压强越大,压力的作用效果越明显。
液体对容器内部的侧壁和底部都有压强,压强随液体深度增加而增大。
液体内部压强的特点是液体由内部向各个方向都有压强;压强随深度的增加而增加;在同一深度,液体向各个方向的压强相等;液体压强还跟液体的密度有关,液体密度越大,压强也越大。
液体内部压强的大小可以用压强计来测量。
挤出机无论是单螺杆还是双螺杆,提到挤出量就必须要说明两个概念,一是理论极限挤出量,二是实际挤出量。
理论极限挤出量的算法是:通过螺杆几何学计算(机筒内部空间的横截面积-螺杆横截面积=流道横截面积)乘以加料段大导程螺纹元件的导程再乘以主机转速,都用标准单位,得到的就是在这个转速下的理论极限挤出量。
实际挤出量是不需要计算的,一般来说都是计量喂料,挤出量就是你设置的喂料量。
挤出机的加卸载压力有一个上下限值,即加载压力和卸载压力范围不能小于0.08mpa,小过这个范围你是无法调节的。
对于定频空压机的加卸载压力最好保持在0.1mpa的范围。
如果你需要的压力为0.7mpa,那么你的加载压力可以设定为0.7mpa而卸载压力最好是0.8mpa,这样你的用气压力最低就是0.7mpa了,从而也不会使机器频繁的加卸载了。
注塑机计算公式
注塑机计算公式一、注塑机相关公式1.理论射出容积(Cm3)=螺杆直径2×0.785x射出行程=螺杆截面积X射出行程2.射出重量(gr)=理论射出容积x0.85×比重3•射出缸有效截面积(Cm2)=(射出缸直径2-活塞杆直径2)×0.785x射出缸个数4.射出压力(kgf/Cm3)=射出缸有效截面积+螺杆截面积(或射出缸直径2÷螺杆直径2)×系统压力5射出速度(Cm/Sec)=泵浦单转容积(cc/rev)x电机转速(RPM)÷60÷射出缸有效截面积(cm2)6•射出效率(Cm3/sec)=螺杆截面积(Cm2)x射出速度(Cm/See)7•螺杆转速(RPM)=泵浦单转容积(cc/rev)x电机转速(RPM)÷液压马达单转容转(cc/rev)8•可塑化能力(Kg/Hr)=(螺杆直径2-螺杆计量段牙底直径2)x0.785X螺杆槽宽X螺杆转速x60X比重X塑化效率常数0.45二、锁模力相关公式1.以油压计算:(1)曲肘式:=锁模缸截面积(Cm2)x系统压力(kgf/Cm2)x曲手放大率(20~50倍)÷1000 (2)单缸直压式:=锁模缸截面积(Cm2)x系统压力(kgf∕Cm2)÷1000(3)四缸直压式:=锁模缸截面积(Cm2)x系统压力(kgf∕Cm2)x4÷10002•以哥林柱大小计算最大锁模力:(1)最大锁模力:=哥林柱直径2(Cm)Xo∙785x材料杨氏系数x4(SCM4红+字钢杨氏系数为lT∕cm3)(2)托模力(Ton)=托模缸截面积(Cm2)x系统核压力(kgf/Cm2)÷1000三、成品投影面积和所需锁模力:所需锁模力=成品投影面积(英寸2)x标准厚度L5(mm)÷成品厚度(mm)x塑料常数1.投影面积以成品对角线为直径计算。
2、与射出方向平行的纵面,约以三分之一计算为平面度。
注塑常用计算公式
怎樣計算料斗加料量 ? 以注塑機、模具搭配進行注塑時,必須計算出料斗所須的 加料量,目的是避免過多塑膠長期儲於料斗內。所用的料斗通 常是加熱式的,而塑膠於料斗內的放時間不可超過1小時。
舉例說明:某注塑機在24秒週期內可生產6件注塑件,每件注 塑件及進料流道的重量分別為14克及12克,因此射料量是 (6*14)+12=96克,然後利用下列公式計算出加料量(Q), 即每小時的塑膠消耗量(kg/h)為
5.射出速度S CM/SEC S=Q/A S:射出速度cm/sec Qr:泵浦吐出量(每回轉/cc)cc/rev A:射出油缸有效面積cm² Q=Qr*RPM/60 (每分鐘/L) Q:泵浦吐出量RPM: 馬達回轉數/每分鐘 例:馬達轉速1000RPM泵浦吐出量85 CC/REV 射出油缸有效面積140 cm² S=85*1000/60/140=10.1 cm/sec
2.射出壓力Pi kg/cm² 公式Pi=P*A/Ao Pi:射出壓力P;泵浦壓力A;射出油缸有效面積 Ao:螺杆截面積. A= π*D2/4 D;直徑 π:圓周率3.14159 例1:已知泵浦壓力 求射出壓力? 泵浦壓力=75 kg/cm² 射出油缸有效面積=150cm² 螺杆截面積=15.9cm² (∮45) Pi=75*150/15.9=707 kg/cm²
Q=總射料量g×3600)÷(1000×週期時間S) Q=(96×3600)÷(1000×24)=14.4kg/h
射料缸滯留時間
t=(射料缸額定料量g×週期時間S)÷(射料量g×300)
6.射出率Sv G/SEC Sv=S*Ao Sv:射出率g/sec S:射出速度cm/sec Ao:螺杆截面積 例:射出速度=10cm/sec螺杆直徑∮42
面積=3.14159*4.2*4.2/4=13.85cm² Sv=13.85*10=138.5g/sec
- 1、下载文档前请自行甄别文档内容的完整性,平台不提供额外的编辑、内容补充、找答案等附加服务。
- 2、"仅部分预览"的文档,不可在线预览部分如存在完整性等问题,可反馈申请退款(可完整预览的文档不适用该条件!)。
- 3、如文档侵犯您的权益,请联系客服反馈,我们会尽快为您处理(人工客服工作时间:9:00-18:30)。
ഥ ್
ܿ݃ݐഥቁ
ௐೞ ௐ್
݊݅ݏ
ቀܭ௦
್
ܿ݃ݐ௦ቁ
ൌ
2 ൈ 12 55.9
ൈ
sin17°39ᇱቀ.ଷାହଷହൈୡ୲ଶଵ°ଵଽᇲቁ
52 55.9
ൈ
sin17°39ᇱ
ൈ
൬0.637
41 65
ൈ
ctg26°46ᇱ൰
ൌ
0.887
计算固体塞移动角
ܵ݅݊ߠ
ܦഥ ൌ ൫ܦ ܦ൯/2 Db —螺杆机筒内直径,m,Db=D; D —螺杆公称直径,m;
(2—8—5)
Df —螺杆进料段根径,m;
H1 —螺杆进料段螺槽深度,m;
ഥ —螺旋角平均值,deg.;
tanഥ
ൌ
ௌ గഥ
—机筒内表面处螺旋角,deg.;
tanୠ
化纤纺丝机械工程计算公式集锦
起点处,X1/W=0.914 熔融系数:
భ
ߖൌ
ఃௐమ
భ
ൌ 6.30 ൈ 10ିଷ
ቀೈభቁమಹಸభ
无因次量,AT/Ψ=0.963
压缩段固相分布函数:
ଶ
ܺ ܹ
ൌ
ܺଵ ܹ
ۍ
ێ ێ
ߖ
்ܣێ
ێ
ۏ
െ
ඨ1
െ
ቀ ்ߖܣെ 1ቁ
ܮ୮ ܮ௭௧
·
்ܣ ߖ
(2—8—2)
ܭ௦
ൌ
ഥ ್
·
௦ഥାೞ௦ഥ ௦ഥି್௦ഥ
ܯ
ൌ
ଶுభ ௐ್
݊݅ݏ
ቀܭ௦
ഥ ್
ܿ݃ݐഥቁ
ௐೞ ௐ್
݊݅ݏ
ቀܭ௦
್
ܿ݃ݐ௦ቁ
ܦഥ —螺杆平均直径,m;
(2—8—3) (2—8—4)
ܹ ൌ ܵcosୠ െ ݁ ൌ 65 ൈ cos 17°39′ െ 6 ൌ 55.9 mm 螺杆根径处螺槽宽度
ܹ௦ ൌ ܵcosୱ െ ݁ ൌ 65 ൈ cos 26°46′ െ 6 ൌ 52 mm
3
【下】功能 元件篇
化纤纺丝机械工程计算公式集锦
计算螺杆平均直径
ܦഥ ൌ ൫್ା൯ ൌ ሺହାସଵሻ ൌ 53 mm
擦系数相同, 且 fb= fs=0.3。求固体输送速率。
求机筒处螺旋角
ୠ
ൌ
tanିଵ
ቀௌቁ
గ್
ൌ
tanିଵ
ቀ ହ ቁ=17°39′
ൈହ
求螺杆根径处螺旋角
ୱ
ൌ
tanିଵ
൬ௌ൰
గ
ൌ
tanିଵ
ቀ ହ ቁ=26°46′
ൈସଵ
求螺旋角平均值
ഥ ൌ tanିଵ ቀగௌഥቁ ൌ tanିଵ ቀൈହହଷቁ=21°19′ 求机筒处螺槽宽度
Φ—系数, kg/s·m3/2;
భ
ߔ ൌ ൜್ೣఘଶሾൣೞሺ்ሺ்ି್்ିೞ்ሻ ା∆ሻାுఎሿೕమ/ଶ൧ൠమ
(2—8—13)
式中,Vbx —机筒内表面圆周速度的 x 方向分速度, m/s;
Vbx= Vb sinφb
Vb —机筒内表面圆周速度,m/s; φb —机筒处螺旋角,deg.; ρm —熔体密度, kg/m3;
0.203m/turn
计算压缩段总长度和渐变度
Lzp=7.5zp=1.41m
8
【下】功能 元件篇
化纤纺丝机械工程计算公式集锦
்ܣ
ൌ
ுభିுయ ௭
ൌ
6.07
ൈ
10ିଷ
计算螺槽宽度
ܹ ൌ ܵcos െ ݁ ൌ 0.056 ݉ 计算机筒内表面圆周速度
Vb=πDn=20.4×10-2 m/s Vbx= Vb sinφb=6.18×10-2 m/s Vbz= Vb cosφb=19.4×10-2 m/s 计算物料质量流动速率
km—熔体热导率, W/m·K; Tb —机筒内表面温度,deg.;
Tm —聚合物熔点,deg.; Ts —聚合物切片温度,deg.; Cs —聚合物固体比热,J/kg·K; ⊿Hm —聚合物熔融热,J/kg; η —聚合物熔体粘度,Pa·s.;
Vj —机筒内表面处熔体的移动速度,m/s;
ܸ ൌ ඥܸଶ ܸ௦ଶ௭ െ 2ܸܸ௦௭ܿݏ
D —螺杆公称直径,m;
H1 —螺杆进料段螺槽深度,m; n —螺杆转数,r/s;
θ—固体塞移动角,deg.;
φ—螺旋角,deg.。
(2) 固体塞移动角的计算
1
(2—8—1)
【下】功能 元件篇
化纤纺丝机械工程计算公式集锦
ܵ݅݊ߠ
ൌ
ඥଵାೞమିெమିೞெ ଵାೞమ
式中,θ —固体塞移动角,deg.;
భ
ቀೈభቁమಹಸభ
(6) 平均螺旋线长度
进料段平均螺旋线长度, m/turn(螺节):
6
(2—8—17) (2—8—18)
【下】功能 元件篇
化纤纺丝机械工程计算公式集锦
ݖ
ൌ
గሺିுభሻ ௦್
压缩段平均螺旋线长度, m/turn(螺节):
ݖ
ൌ
గሾሺିுభሻାሺିுయሻሿ ଶ௦್
ଶ
ଶ
计算 Ks
ܭ௦
ൌ
ܦഥ ܦ
·
݊݅ݏഥ ܿݏഥ
െ
݂௦ܿݏഥ ݂݊݅ݏഥ
ൌ
53 65
ൈ
sin21°19ᇱ 0.3 ൈ cos21°19ᇱ cos21°19ᇱ െ 0.3 ൈ sin21°19ᇱ
ൌ
0.637
计算 M
ܯ
ൌ
ଶுభ ௐ್
݊݅ݏ
ቀܭ௦
物料参数:聚酯方切片固体密度ρs=1.455×103 kg/m3, 熔体密度ρm=1.172× 103 kg/m3, 固体比热 Cs=1.103×103J/kg▪K,熔体热导率 km=0.084W/m▪K,聚酯熔融热△ Hm=129×103J/kg,熔点 Tm=255℃。
操作参数:螺杆转速 n=60r/min,挤出量 G=50kg/h,固体切片温度 Ts=55℃, 机筒加热温度 Tb=295℃。
ఋ
由聚酯流动曲线查取粘度值:η=145Pa·s
试算:
9
【下】功能 元件篇
化纤纺丝机械工程计算公式集锦
ߜ
ൌ
ඨ ቂଶሺ்್ି்ሻାఎೕమቃ
್ೣఘሾೞሺ்ି்ೞሻା∆ுሿ
ൌ
6.91
ൈ
10ିସ√X
当 X=W 时,
δmax=1.634×10-4m δ=δmax/2=8.17×10-5m 计算值与假定值相差 1.83×10-5m,比许用误差值 2×10-4 小,可不再
宽度 X1=W
ௐ
ൌ
భ ௐ
ቀ1
െ
అ ଶுభ
ଶ
ܼቁ
ൌ
ሺ1
െ
0.251zሻଶ
计算压缩段固相分布函数
因为进料段一个螺距的螺旋线长为 zf=0.175 m/turn,所以进料段终点处:
ௐ
ൌ
ሺ1
െ
0.251zሻଶ
ൌ
0.914
进料段终点的固体床宽度即为压缩段计算起点的固体床宽度,所以压缩段
10
【下】功能 元件篇
(3) 熔体移动速度
ܸ ൌ ඥܸଶ ܸ௦ଶ௭ െ 2ܸܸ௦௭ܿݏ Vj —熔体的移动速度,m/s;
(2—8—16)
Vsz —固体床移动速度,m/s。
(4) 熔膜厚度
ߜ ൌ ඨ ቂଶሺ்್ି்ሻାఎೕమቃ
್ೣఘሾೞሺ்ି்ೞሻା∆ுሿ
(5)熔融系数 Ψ
భ
ߖൌ
ఃௐమ
试算,确定:
δ= 8.17×10-5m
ߛሶ ൌ 2332 sିଵ η=13·5Pa·s
计算系数Φ
భ
ߔ
ൌ
൜್ೣఘଶሾൣೞሺ்ሺ்ି್்ିೞ்ሻା∆ሻାுఎሿೕమ/ଶ൧ൠమ
ൌ
0.0295
kg/s
·
య
mమ
计算进料段固相分布函数
假设开始熔融点在进料段最后一个螺节的起始点,因此计算起点的固体床
G=50kg/h=13.9×10-3 kg/s
计算固体床移动速度
ܸ௦௭
ൌ
ீ ௐுభఘೞ
ൌ
1.42
ൈ
10ିଶ
m/s
计算熔体移动速度
ܸ ൌ ඥܸଶ ܸ௦ଶ௭ െ 2ܸܸ௦௭ܿݏ ൌ 19.05×10-2 m/s 试算熔膜厚度
假定熔膜厚度δ=0.01cm=1×10-4m
确定熔膜平均温度:T=(Tb+Tm)/2=275℃ 计算平均剪切速率:ߛሶ ൌ ೕ ൌ 1905 sିଵ
【下】功能 元件篇
化纤纺丝机械工程计算公式集锦
(9) 固相分布函数计算举例 螺杆参数:螺杆直径 D=65mm,长径比 L/D=25,进料段长度 L1=7.5D,压缩段 长度 L2=7.5D,计量段长度 L3=10D,进料段螺槽深度 Hf=12mm, 计量段螺槽深度 H3=3.4mm, 螺棱宽度 e=6mm,螺距 S=65mm,螺旋角φ=17°39′。
求固相分布函数。
计算步骤:
计算平均螺旋线长度
进料段平均螺旋线长度: