孔类零件加工2
广东省佛山市数控铣工考证理论题库2

B A B A A A B B A B A B B B B A C A A C
29 30 31 32 33 34 35 36 37 38 39 40
序 号
41 42 43 44 45 46
数控铣床中级证(DB-2) 题目
20.工件夹紧要牢固、可靠,并保证工件在加工中( )不变。 (A)尺寸 (B)定位 (C)位置 (D)间隙 23.斜垫铁的斜度为( ),常用于安装尺寸小、要求不高、安装后不需要调整的机 床。 27.采用金刚石涂层的立铣刀不能加工( )零件。 (A)钛合金 (B)黄铜 (C)铝合金 (D)碳素钢 29.用φ 10高速钢键槽铣刀粗加工45钢键槽时,切削深度为3㎜,切宽10㎜,主轴转 速600r/min,选择合适的进给速度( )。 (A)10mm/min (B)20mm/min (C)50mm/min (D)200mm/min 33.标准麻花钻的顶角是( )。 (A)100° (B)118° (C)140° (D)130 38.锥孔的加工方法有( )。 (A)成型刀加工 (B)电火花 (C)仿型加工 (D)成型刀加工,电火花,仿型加 工都对 44.在加工表面、切削刀具、切削用量不变的条件下连续完成的那一部分工序内容称 为( )。 (A)工序 (B)工位 (C)工步 (D)走刀 48.相同条件下,使用立铣刀切削加工,侧壁垂直度最好的刀具齿数应为( )。 (A)2 (B)3 (C)4 (D)6 52.测量精度为0.02mm的游标卡尺,当两测量爪并拢时,尺身上49mm对正游标上的( )格。 (A)20 (B)40 (C)50 (D)49 53.铰刀铰销时切下的切屑一般( )。 (A)很薄 (B)较厚 (C)很厚 (D)既可以薄也可以厚 54.用立铣刀加工键槽,采工件侧面对中心时,则要进行换算才可确定中心所在的位 置,换算时必须知道的尺寸是( )。 (A)工件侧面到槽中心位置的距离 (B)刀具的直径 (C)刀具的长度 (D)工件侧面到槽中心位置的距离和刀具的直径 58.钻头直径为10mm,切削速度是30米/分钟,主轴转速应该是( )。 (A)240r/min (B)1920r/min (C)480r/min (D)960r/min 60.修磨麻花钻横刃的目的是( )。 (A)减小横刃处前角 (B)增加横刃强度 (C)增大横刃处前角、后角 (D)缩短横 刃,降低钻削力 63.主轴转速n(r/min)与切削速度v(m/min)的关系表达式是( )。 (A)n=π vD/1000 (B)n=1000π vD (C)v=π nD/1000 (D)v=1000π nD 64.选用刀具直径为100mm的面铣刀时,切削速度为100m/min,则转速应为( )。 (A)520r/min (B)3180r/min (C)100r/min (D)318r/min 66.用心轴对有较长长度的孔进行定位时,可以限制工件的( )自由度。 (A)两个移动、两个转动 (B)三个移动、一个转动 (C)两个移动、一个转动 (D)一个移动、二个转动 68.一个物体在空间如果不加任何约束限制,应有( )自由度。 (A)三个 (B)四个 (C)六个 (D)八个 70.铣削平面时主运动为( )。 (A)铣刀的旋转运动 (B)工件的纵向移动 (C)工件的横向移动 (D)刀具的上 下运动 71.已知一把直径30mm的4刃铣刀,切削速度Vc=215m/min,每齿切削厚度0.12mm,加 工进给速度F=( )。 (A)1095mm/min (B)274mm/min (C)505mm/min (D)2190mm/min
数控车孔类零件的加工教案
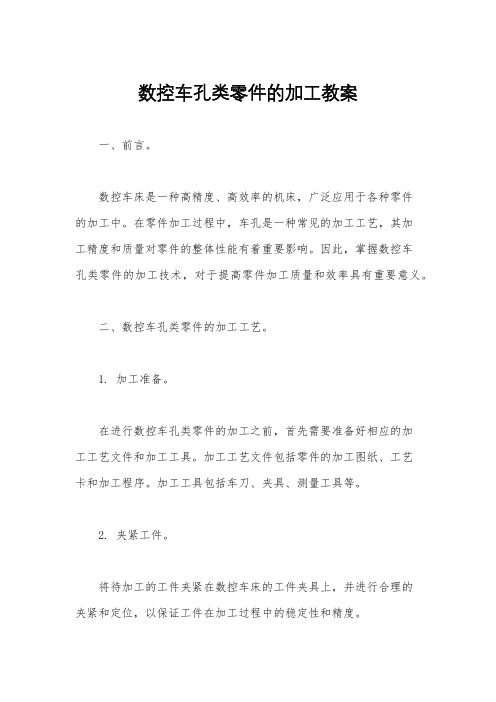
数控车孔类零件的加工教案一、前言。
数控车床是一种高精度、高效率的机床,广泛应用于各种零件的加工中。
在零件加工过程中,车孔是一种常见的加工工艺,其加工精度和质量对零件的整体性能有着重要影响。
因此,掌握数控车孔类零件的加工技术,对于提高零件加工质量和效率具有重要意义。
二、数控车孔类零件的加工工艺。
1. 加工准备。
在进行数控车孔类零件的加工之前,首先需要准备好相应的加工工艺文件和加工工具。
加工工艺文件包括零件的加工图纸、工艺卡和加工程序。
加工工具包括车刀、夹具、测量工具等。
2. 夹紧工件。
将待加工的工件夹紧在数控车床的工件夹具上,并进行合理的夹紧和定位,以保证工件在加工过程中的稳定性和精度。
3. 加工参数设置。
根据零件的加工要求和数控车床的性能特点,设置加工参数,包括主轴转速、进给速度、切削深度、切削速度等。
合理的加工参数设置对于保证零件加工质量和提高加工效率至关重要。
4. 车刀选择和装夹。
根据零件的加工要求和加工特点,选择合适的车刀,并将车刀装夹在数控车床的刀架上。
在装夹过程中,需要保证车刀的正确位置和角度,以保证切削的精度和质量。
5. 加工操作。
根据加工程序和加工要求,进行数控车孔类零件的加工操作。
在加工过程中,需要密切关注加工状态,及时调整加工参数和刀具位置,以保证加工的精度和质量。
6. 质量检验。
在加工完成后,进行零件质量的检验。
主要包括尺寸精度、表面粗糙度和孔的圆度等方面。
对于不合格的零件,需要及时调整加工参数和工艺,以保证零件的质量和性能。
三、数控车孔类零件的加工注意事项。
1. 加工前的准备工作要充分,包括加工工艺文件的准备、加工工具的选择和加工参数的设置等。
2. 在夹紧工件时,需要保证夹紧力的均匀和稳定,以避免在加工过程中出现工件的变形和位移。
3. 在车刀选择和装夹时,需要保证车刀的刃口尖锐和刀具的稳定性,以保证切削的精度和表面质量。
4. 在加工过程中,需要密切关注加工状态,及时调整加工参数和刀具位置,以保证加工的精度和质量。
数控车工中级考证第六单元-零件加工

数控车工中级考证第六单元-零件加工一、单项选择题1.下列各项中,()主要用来支撑传动零部件、传递扭矩和承受载荷。
[单选题] *A.箱体零件B.盘套类零件C.薄壁零件D.轴类零件(正确答案)2.轴类零件是旋转体零件,其长度和直径比小于()的称为短轴。
[单选题] *A.5(正确答案)B.10C.20D.303.轴类零件是旋转体零件,其长度和直径比大于()的称为细长轴 [单选题] *A.10B.20C.25(正确答案)D.304.工带有键槽的传动轴,材料为45钢并需火处理,表面粗糙度要求为Ra0.8um,其加工工艺为() [单选题] *A.粗车一铣一磨一热处理B.粗车一精车一铣一热处理一粗磨一精磨C.车一磨一铣一热处理D车一热处理一磨一铣(正确答案)5.轴类零件加工顺序安排时应按照()的原则。
[单选题] *A先粗车后精车(正确答案)B.先精车后粗车C.先内后外D.先外后内6.轴上的花键槽一般都放在外圆的半精车()进行 [单选题] *A.以前B以后(正确答案)C.同时D.前或后7.下列各项中()适宜于选用锻件和铸件为毛坯材料。
[单选题] *A.轴类零件B.盘类零件(正确答案)C.箱体零件D.薄壁零件8.数控车加工盘类零件时,采用()指令加工可以提高表面精度 [单选题] *A.G96(正确答案)B.G97C.G98D.G99A.G96B.G97C.G98D.G999.下列各项中()的结构特点是直径大、长度短 [单选题] *A.轴类零件B.箱体零件C.薄壁零件D盘类零件(正确答案)10.车削外圆锥时如果车刀不对中心,会产生双曲线误差,双曲线 [单选题] *A.是外凸的B.曲率半径大C.曲率半径小D.是内凹的(正确答案)11.车削圆锥体时,刀尖()工件回转轴线,加工后锥体表面母线将呈曲线。
[单选题] *A.仅高于B.仅低于C.等高于D.高或低于(正确答案)12.车削圆锥体时,刀尖高于工件回转轴线,加工后锥体表面母线将呈() [单选题] *A.直线B曲线(正确答案)C.圆弧D.波浪线13.用一夹一顶或两顶尖装夹轴类零件时,如果后顶尖轴线与主轴轴线不重合,工件会产生()误差 [单选题] *B.圆度C柱度(正确答案)D.同轴度14.主轴加工采用两中心孔定位,能在一次安装中加工大多数表面,符合()原则。
模块五(项目四)孔类零件.
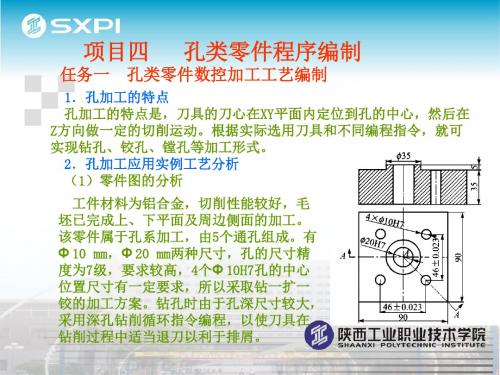
③用Φ 10mm的机用铰刀精铰 4 ×Φ 10 mm的孔至尺寸要求;
④用Φ 13mm的麻花钻将Φ 20mm的孔粗钻至Φ 13mm; ⑤用Φ 19.8mm的麻花钻将Φ 20mm的孔粗钻至Φ 19.8mm;
⑥用Φ 20H7的机用铰刀精铰Φ 20mm的孔至尺寸要求。4个Φ 20 mm孔加工 于XY平面的进给路线,如图所示。
(2)刀具及切削用量的确定 刀具选择:T2:Φ 3 mm的高速钢中心钻,T3:Φ 9.8 mm的高速钢 麻花钻,T4:Φ 10H7的机用铰刀,T5:Φ 13mm高速钢麻花钻,T6: Φ 19.8mm麻花钻,T7:Φ 20H7机用铰刀 (3)工件装夹 选择毛坯底面和两侧面为定位平面,其中底面为主定位面,采用 等高垫铁在平口虎钳口上装夹定位或直接将工件毛坯放在工作台上, 用等高垫铁将工件托起,再用百分表找正工件两侧面进行安装定位, 最后用压板螺母、螺栓、垫圈等元件将工件夹紧。
3.编写加工程序 用 FANUC 0i-MB数控系统的指令及规则编写的加工程序如下:
O3001; N0010 G21; N0020 G17 G40 G49 G69 G80 G90 ; N0030 G54; N0040 T2M6; N0050 S1400 M03; N0060 G00 XO YO ; N0070 G43 G00 Z50 H02; N0080 G00 Z10; N0090 G99 G81 X0 YO Y0 Z-5 R5 F50; N0100 X23 Y23 Z-10 R2; N0110 X-23;N0120 Y-23; N0130 G98 X23; N0140 G80; N0150 GO0 Z50;
N0160 N0170 N0180 N0190 N0200 N0210 N0220 N0230 N0240 N0250 N0260 N0270 N0280 N0290 N0300 N0310 N0320 N0330 N0340 N0350
项目9.3 孔类零件的加工.
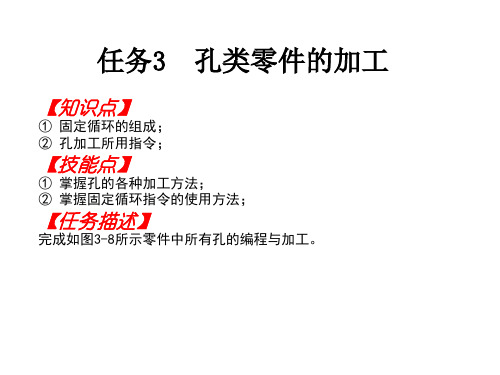
①直径在M6以下的螺纹不适合在立式数控铣床上加工,因为自动攻螺纹不能随机控 制加工状态,且小直径丝锥易折断。 ②攻丝时要求排屑效果好,因此一般应加注切削液。 ③丝锥用钝后应及时更换,不得强行攻制,以免加工时发生折断。 ④立式数控铣床上采用固定循环指令编写攻丝程序,它的6个基本动作类同于孔加工 循环。加工前首先根据图纸要求计算出螺纹底孔的直径,并选择麻花钻加工出底 孔;攻丝加工的进给速度与主轴转速及内螺纹的螺距有关,编程中有的直接给定 螺距,机床可自动计算其进给速度;有的则需将计算出的进给速度()写入程序 中。 表3-9 数控铣床上孔的加工方法
快速移动 快速移动 手动移动 切削进给
2 孔加工固定循环概述
图3-9 固定循环动作及图形符号 (1)孔加工固定循环动作 固定循环通常由六个基本动作构成。(见图3-9) 动作1——X、Y轴定位。刀具快速定位到孔加工的位置(初始点)。 动作2——快进到R点平面。刀具自初始点快速进给到R点平面(准备切削的位 置),在多孔加工时,为了刀具移动的安全,应注意R点平面Z值的选取。 动作3——孔加工。以切削进给方式执行孔加工的动作。 动作4——在孔底的动作。包括暂停、主轴定向停止、刀具移位等动作。 动作5——返回到R点平面。 动作6——快速返回到初始点。 (2)孔加工固定循环的基本格式
粗镗→半精镗→精镗(如仍达不到精度还可进一步采用精细镗)
关于表3-8的说明如下: ①在加工直径小于30mm且没有预孔的毛坯孔时,为了保证钻孔加工的 定位精度,可选择在钻孔前先将孔口端面铣平或采用打中心孔的加工 方法。 ②对于表5-1中的扩孔及粗镗加工,也可采用立铣刀铣孔的加工方法。 ③在加工螺纹孔时,先加工出螺纹底孔,对于直径在M6下的螺纹,通常 不在数控铣床上加工;对于直径在M6~M20的螺纹,通常采用攻螺 纹的加工方法;而对于直径在M20以上的螺纹,可采用螺纹铣刀铣削 加工。
UG NX6 数控编程教程2(孔加工)

第二章点位加工本章要点1.点位加工概述2.点位加工几何体设置3.点位加工循环参数设置4.点位加工一般参数设置2.1 点位加工概述点位加工是一种相当常见的机械加工方法,如图2-1所示的工件。
点位加工包括钻孔、镗孔、扩孔、铰孔、点焊和铆接等,UG NX6可为各种点位加工操作创建刀具路径,如图2-2所示。
点位加工的刀具运动由3部分组成:首先刀具快速定位在加工位置上,然后切入零件,完成切削后退回。
图2-1 点位加工工件图2-2 点位加工刀轨2.1.1 操作安全点在点位加工中,操作安全点是每个切削运动的起点和终点,也是进刀、退刀、避让、快速移刀等辅助运动的起点和终点。
通常,刀具将以快速或进刀进给率向操作安全点运动,刀具从操作安全点向部件表面上的刀位点运动时,以及切削至指定深度的过程将使用切削进给率,如图2-3所示。
但是,如果一个循环处于活动状态,系统将使用“循环参数”菜单中指定的循环进给率。
图2-3 最小安全距离及刀具运动速率2.1.2 加工循环数控系统对典型加工中几个固定或连续动作用同一个指令来指定,完成本来要用多个程序段指令完成的加工动作,这个指令就是加工循环指令。
为了满足不同类型孔的加工要求,UG在点位加工中提供了多种循环类型,控制刀具的切削运动过程。
点位加工操作就是选择合理的加工循环并进行合理的参数设定的过程。
点位加工操作循环也称作固定循环,通常包括的基本动作如下:1.精确定位。
2.以快进或进刀速度移动至操作安全点。
3.以切削速度运动至零件表面上的加工位置点。
4.以切削速度或循环进给率加工至孔最深处。
5.孔底动作(暂停、让刀等)。
6.以退刀速度或快进速度退回操作安全点。
7.快速运行至安全平面(安全平面被激活)。
2.2 点位加工几何体设置为了创建点位加工刀轨,需要定义点位加工几何体。
点位加工几何的设置包括指定孔、部件表面和底面3种加工几何,其中孔为必选项,而部件表面和底面为可选项,如图2-4所示。
图2-4 点位加工几何体2.2.1 指定加工位置在“钻”对话框几何体组中单击“指定孔”图标,系统弹出“点到点几何体”对话框,其中“选择”选项用于选择孔加工的点位几何对象(这些几何对象可以是一般点、圆弧、圆、椭圆以及实心体或片体上的孔),其余选项用于编辑已指定的点位,如图2-5所示。
7、孔加工
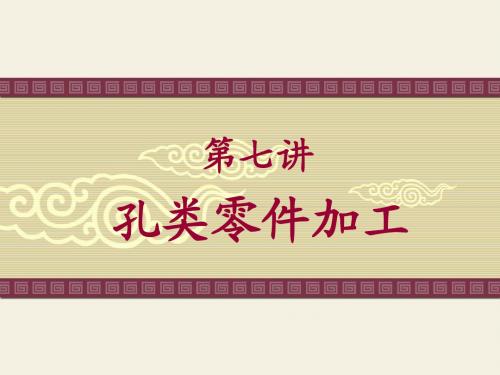
对于直径小于φ30mm无底孔的孔加工,通常采用 锪平端面——打中心孔——钻——扩——孔口倒角——铰加工方案, 对有同轴度要求的小孔,需采用锪平端面——打中心孔——钻——半 精镗——孔口倒角——精镗(或铰)加工方案。
二、孔加工方法的选择原则
内孔表面加工方法选择实例:
Φ40H7内孔可选择钻孔—粗镗(或扩孔)—半精镗—精镗方 案。阶梯孔Φ 13和Φ 22没有尺寸公差要求,因而可选择钻孔—锪 孔方案。
③ 孔加工:以切削进给的方式执行孔加工的动作。
④ 在孔底的动作:包括暂停、主轴准停、刀具位移 等动作。 ⑤ 返回到R点:继续孔的加工而又可以安全移动刀
具时选择R点。
⑥ 返回到初始点:孔加工完成后一般应选择初始点
四、固定循环功能
表1
2、固定循环的代码组成
① 固定循环平面 初始平面 初始平面是为了安全下刀而规定的一个平 面。初始平面到零件表面的距离可以任意设定在一个 安全的高度上 R点平面 R点平面又叫R参考平面,这个平面是刀具 下刀时自快进转为工进的高度平面。距工件表面的距 离主要考虑工件表面尺寸的变化,一般可取2~5mm。 孔底平面 加工盲孔时孔底平面就是孔底的Z轴高度, 加工通孔时一般刀具还要伸出工件底平面一段距离, 主要是保证全部孔深都加工到尺寸,钻削加工时还应 考虑钻头钻尖对孔深的影响。
60 80
40
25
3)高速深孔往复排屑循环G73 指令格式:G73
X_ Y_ Z_ R_ Q_ F_ ;
功能:该循环用于深孔加工。 孔加工动作如图所示,钻头先快速定位至X、Y所指定的坐标 位置,再快速定位至R点,接着以F所指定的进给速度向下钻 削至Q所指定的距离(Q必须为正值,用增量值表示),再快 速回退d 距离(d 是CNC系统内部参数设定的)。依此方式 进刀若干个Q,最后一次进刀量为剩余量(小于或等于q), 到达Z所指的孔底位置。G73指令是在钻孔时间断进给,有利 于断屑、排屑,冷却、润滑效果佳。
数控加工程序编制-加工中心-孔类零件程序编制全解

G88循环
二、相关知识
(二)固定循环功能
(5)精镗循环(G76) 指令格式: G76 X_ Y_ Z_ R_ Q_ F_
精镗时,主轴在孔底定向停止后,向刀尖反方向移 动,然后快速退刀。
这种带有让刀的退刀不会划伤已加工平面,保证了 镗孔精度。
程序格式中,Q 表示刀尖的偏移量,一般为正数, 移动方向由机床参数设定。
1
钻中心孔
2
钻φ5mm通孔
3
攻丝
螺纹孔加工工序卡
刀具规格
类型
材料
A4中心钻
高速钢
Φ4.2mm麻花钻 高速钢
M5mm细牙丝锥 高速钢
主轴转速 (r/min)
1200 600 80
进给速度 (mm/min)
20 30 64
(6)编制零件螺纹孔钻中心孔加工程序
四、拓展知识
用西门子802D孔及螺纹加工循环指令加工图零件。
(二)固定循环功能
(2)带停顿的钻孔循环(G82) 指令格式:
G82 X_Y_Z_P_R_F_
G82循环
该指令除了要在孔底暂停外,其它动作与G81相同。暂 停时间由地址P给出。此指令主要用于加工盲孔,以提 高孔深精度。
二、相关知识
(二)固定循环功能
(3)断屑式深孔加工循环(G73)
指令格式: G73 X_Y_Z_Q_R_F_
三、工作任务的完成
(一)数控加工工艺的制订
4.刀具准备,填写刀具卡
序号
1 2 3
4
5 6 7
刀具号
T05 T06 T07
名称 麻花钻 麻花钻 镗刀
T08 镗刀
T09 中心钻 T10 机用铰刀 T11 麻花钻
刀具规格 直径
- 1、下载文档前请自行甄别文档内容的完整性,平台不提供额外的编辑、内容补充、找答案等附加服务。
- 2、"仅部分预览"的文档,不可在线预览部分如存在完整性等问题,可反馈申请退款(可完整预览的文档不适用该条件!)。
- 3、如文档侵犯您的权益,请联系客服反馈,我们会尽快为您处理(人工客服工作时间:9:00-18:30)。
单项训练-孔加工
一、实训目的与要求
1.能够编制数控加工程序相贯孔加工,并达到如下要求:
(1)尺寸公差等级达IT8级
(2)形位公差等级达IT8级
(3)表面粗糙度达Ra3.2μm
2.能进行调头镗孔,并达到如下要求:
(1)尺寸公差等级达IT7级
(2)形位公差等级达IT8级
(3)表面粗糙度达Ra3.2μm
3.能够编制数控加工程序进行刚性攻丝,并达到如下要求:
(1)尺寸公差等级达IT8级
(2)形位公差等级达IT8级
(3)表面粗糙度达Ra3.2μm
二、训练设备及仪器用具
1、数控铣床及配套的常用工具用具
2、机夹刀具、中心钻、麻花钻、镗刀、铰刀、丝锥
3、45#毛坯
三、孔加工分析
在数控机床上孔加工的方法一般有钻削、扩削、铰削和镗削等。
孔加工方案的确定,应根据加工孔的加工要求,尺寸、具体的生产条件,批量的大小以及毛坯上有无预加孔合理选用。
1)加工精度为IT9级,当孔径小于10mm时,可采用钻→铰加工方案;当孔径小于30mm时,可采用钻→扩加工方案;当孔径大于30mm
时,可采用钻→镗加工方案。
工件材料为淬火钢以外的金属。
2)加工精度为IT8级,当孔径小于20mm时,可采用钻→铰加工方案;
当孔径小于20mm时,可采用钻→扩→铰加工方案,同时也可以采
用最终工序为精镗的方案。
此方案适用于加工除工件材料为淬火
钢以外的金属,
3)加工精度为IT7级,当孔径小于12mm时,可采用钻→粗铰→精铰
加工方案;当孔径在12mm至60mm之间时,可采用钻→扩→粗铰
→精铰加工方案。
对于加工毛坯己铸出或锻出毛坯孔的孔加工,
一般采用粗镗→半精镗→孔口倒角一精镗加工方案。
4)孔精度要求较低且孔径较大时,可采用立铣刀粗铣→精铣加工方案。
有空刀槽时可用锯片铣刀在半精镗之后、精镗之前铣削完成,
也可用镗刀进行单刃螳削,但单刃镗削效率低。
5)有同轴度要求的小孔,须采用饶平端面→打中心孔→钻→半精镗→孔口倒角→精镗(或铰)加工方案。
为提高孔的位置精度,在
钻孔工步前须安排锪平端面和打中心孔工步。
孔口倒角安排在半
精加工之后、精加工之前,以防孔内产生毛刺。
6)螺纹的加工
螺纹的加工根据孔径大小而定,一般情况下,直径在M5mm~
M20mm之间的螺纹,通常采用攻螺纹的方法加工。
直径在M
6mm以下的螺纹,在数控机床上完成底孔加工后,通过其他手
段来完成攻螺纹。
因为在数控机床上攻螺纹不能随机控制加工状
态,小直径丝锥容易拆断。
直径在M25mm以上的螺纹,可采用
镗刀片镗削加工或采用圆弧插补(G02或G03)指令来完成。
四、训练题
题1:
技术要求:
、全部通孔
2、位置公差
3、尺寸公差
、表面粗糙度 3.2题2:
技术要求:
1、尺寸公差
、表面粗糙度 3.2
题3:
技术要求:1、尺寸公差、表面粗糙度 3.2。