典型钢种冶炼工艺共35页
电弧炉炼钢——第六章 电炉典型钢种冶炼

2.轴承钢中的化学成分和主要合金元素的影响 2.1轴承钢中化学成分
表(1-2)(%)
项目
C Mn Si Cr S P Ni Cu
GCr6
1.05/1.1 5
0.20/0.4
0.15/0.3 5
0.40-0.70
≤0.02
≤0.027
≤0.30
≤0.25
GCr9
1.00/1.1 0
0.2/0.40
0.15/0.3 5
(3)目的: 提前造渣,早期去磷,减轻氧化期脱磷 负担 。
(3)炉料熔毕,温度大于1560℃,开始取样;
熔清成分(%)表(1-4)
元素 C Mn Si Cr P S Ni Cu
GCr15S iMn
1.15
0.15
0.05
0.10
0.03 0.025
0.03
0.02
3.4 氧化期
(1)氧化温度在1580℃以上,不准带料氧化; (2)采用氧气、矿石综合脱氧;
表(1-3)
项目 C Mn Si Cr S P Ni Cu
GCr15Si 0.95/1. 0.90/ 0.45- 1.30/ ≤0.02 ≤0.027 ≤0.30 ≤0.25
Mn
05 1.20 0.65 1.65
3.1 冶炼前准备。
(1)轴承钢安排在EAF中期炉龄的炉内冶炼。 (2)炉体、设备良好,无漏水现象。 (3)出钢槽、钢包、铁合金、辅助材料均必须清洁干
0.90-1.20
GCr9SiMn 1.00/1.1 0
0.9/1.20
0.40/0.7 0
0.90-1.20
GCr15
GCr15SiMn
0.95/1.0 5
钢铁行业冶金工艺流程资料
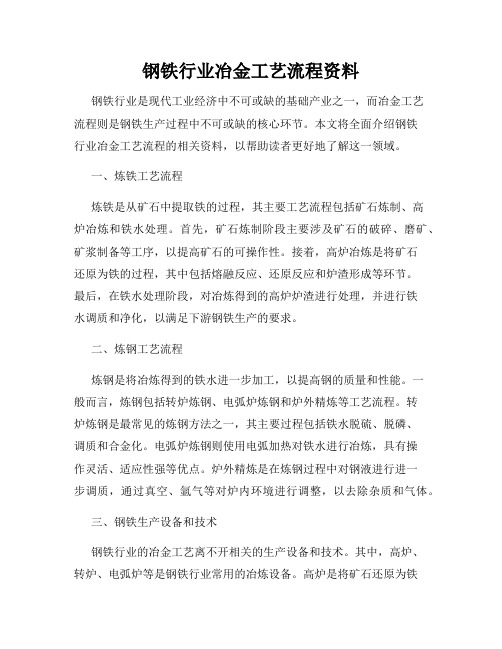
钢铁行业冶金工艺流程资料钢铁行业是现代工业经济中不可或缺的基础产业之一,而冶金工艺流程则是钢铁生产过程中不可或缺的核心环节。
本文将全面介绍钢铁行业冶金工艺流程的相关资料,以帮助读者更好地了解这一领域。
一、炼铁工艺流程炼铁是从矿石中提取铁的过程,其主要工艺流程包括矿石炼制、高炉冶炼和铁水处理。
首先,矿石炼制阶段主要涉及矿石的破碎、磨矿、矿浆制备等工序,以提高矿石的可操作性。
接着,高炉冶炼是将矿石还原为铁的过程,其中包括熔融反应、还原反应和炉渣形成等环节。
最后,在铁水处理阶段,对冶炼得到的高炉炉渣进行处理,并进行铁水调质和净化,以满足下游钢铁生产的要求。
二、炼钢工艺流程炼钢是将冶炼得到的铁水进一步加工,以提高钢的质量和性能。
一般而言,炼钢包括转炉炼钢、电弧炉炼钢和炉外精炼等工艺流程。
转炉炼钢是最常见的炼钢方法之一,其主要过程包括铁水脱硫、脱磷、调质和合金化。
电弧炉炼钢则使用电弧加热对铁水进行冶炼,具有操作灵活、适应性强等优点。
炉外精炼是在炼钢过程中对钢液进行进一步调质,通过真空、氩气等对炉内环境进行调整,以去除杂质和气体。
三、钢铁生产设备和技术钢铁行业的冶金工艺离不开相关的生产设备和技术。
其中,高炉、转炉、电弧炉等是钢铁行业常用的冶炼设备。
高炉是将矿石还原为铁的主要设备,其结构包括炉壳、炉缸、风口、排烟口等。
转炉和电弧炉则是炼钢的主要设备,其结构包括炉体、电极、底吹氧气装置等。
此外,钢铁行业还应用了一些先进的技术,如连铸技术、脱硫技术、脱磷技术等,以提高生产效率和产品质量。
四、钢铁行业的环境保护措施钢铁行业作为传统的重工业部门,其生产活动会对环境造成一定的影响。
为了减少对环境的负面影响,钢铁企业积极采取了一系列的环保措施。
例如,在炼制过程中,利用先进的排放治理设施和技术手段,控制废气、废水和固体废弃物的排放。
此外,钢铁企业还注重资源利用和能源消耗的优化,推广循环经济理念,提高工业绿色化水平。
五、钢铁行业发展趋势与前景随着经济的不断发展和工业结构的升级,钢铁行业也面临诸多挑战和机遇。
钢铁冶炼工艺流程

钢铁冶炼工艺流程钢铁冶炼是将铁矿石经过一系列工艺流程加工成钢铁产品的过程。
这一过程涉及多个步骤和工艺,需要严格控制各个环节,以确保最终产品的质量和性能。
下面我们将详细介绍钢铁冶炼的工艺流程。
首先,钢铁冶炼的第一步是选矿。
在这一阶段,需要对原料进行筛分、破碎和磨矿,以获得适合冶炼的铁矿石。
选矿的目的是提高矿石的品位,减少杂质,为后续的冶炼工艺提供良好的原料。
接下来是炼铁工艺。
在炼铁过程中,将经过选矿处理的铁矿石与焦炭、石灰石等原料一起投入高炉进行冶炼。
在高炉内,矿石在高温下被还原成铁,同时石灰石吸收硅、磷等杂质,焦炭提供热量。
这一过程产生的熔融铁水称为生铁,是钢铁冶炼的重要中间产品。
随后是转炉冶炼。
生铁经过转炉冶炼可以得到钢水。
在转炉内,将生铁与废钢、废铁等原料一起进行冶炼,通过吹氧等工艺,去除熔融铁水中的碳、硅、锰等杂质,调整合金成分,最终得到符合要求的钢水。
接着是连铸工艺。
钢水经过连铸设备进行连铸,将熔融的钢水浇铸成方坯、圆坯等不同形状的铸坯。
连铸是钢铁冶炼的关键环节,直接影响最终产品的质量和形状。
最后是热轧工艺。
铸坯经过热轧设备进行轧制,将其加热至一定温度后进行轧制,得到不同规格和形状的钢材。
热轧是将铸坯加热至一定温度后进行轧制,以改变其形状和尺寸,得到成品钢材的重要工艺。
总的来说,钢铁冶炼工艺流程是一个复杂而又精细的过程,需要各个环节密切配合,确保生产过程的稳定和产品质量的可控。
只有严格按照工艺流程进行操作,才能生产出优质的钢铁产品,满足市场需求。
希望本文的介绍能够对钢铁冶炼工艺有所了解,也希望钢铁行业在未来能够不断创新,提高工艺水平,生产更加优质的钢铁产品。
不锈钢冶炼方法简介

AOD法的基本工艺
AOD 法一般为电炉→AOD 炉双联工艺。不锈钢的冶 炼过程大致分为三个时期:即熔化期、氧化期和还 原精炼期。熔化是在电炉中进行,氧化和精炼在AOD 炉中进行。 熔化:在电炉中装入废不锈钢、合金铁(高碳铬铁、 高碳镍铁、电解镍、NiO等)和造渣材料(石灰等) 进行熔化。炉料成分除了碳、硅、硫外,应接近钢 号标准成分。电炉钢水还原和成分调整后,达到 1500℃左右出钢。 氧化脱碳:电炉钢水倒入AOD炉后首先吹入氩氧混合 气体进行脱碳。脱碳后期为了控制出钢温度并有利 于炉衬寿命,需添加清洁的本钢种废钢冷却钢水。 脱碳终了后根据冶炼钢种不同可以进行扒渣处理。
司与Josly 公司合作于1968 年发明的。AOD 炉二次精炼工艺的诞生为大 量生产高质量的不锈钢开辟了道路。据美国普莱可斯公司统计,2006 年 全球68.7%的不锈钢,是用普莱可斯许可的AOD 生产的。 AOD法的工作原理 AOD 精炼工艺是把电炉粗炼好的钢水倒 入AOD 内,用一定比例的氧和氩的混合 气体从炉体下部侧部吹入炉内, 在O2-Ar 气泡表面进行脱碳反应。 由于Ar 对所生成的CO 的稀释作用 降低了气泡内的CO 分压,因此促成 了脱碳,防止了铬的氧化。
钢铁厂炼钢工艺流程
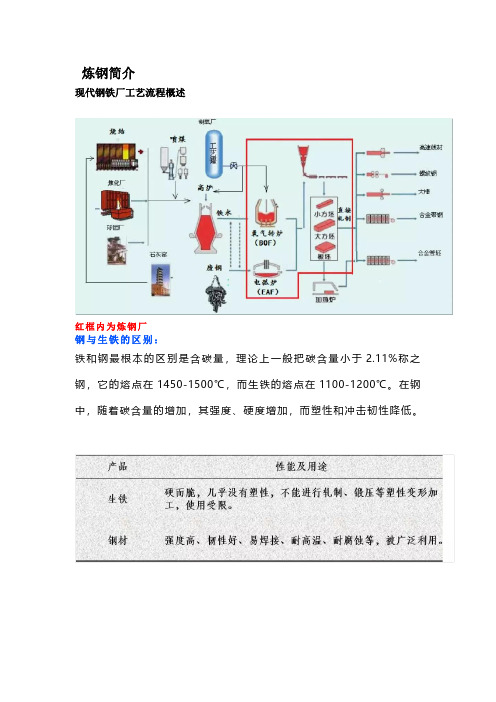
炼钢简介现代钢铁厂工艺流程概述红框内为炼钢厂钢与生铁的区别:铁和钢最根本的区别是含碳量,理论上一般把碳含量小于2.11%称之钢,它的熔点在1450-1500℃,而生铁的熔点在1100-1200℃。
在钢中,随着碳含量的增加,其强度、硬度增加,而塑性和冲击韧性降低。
炼钢的定义:用氧化方法去除生铁和废钢中的杂质,加入适量的合金元素,使之成为具有高的强度、韧性或其他特殊性能的钢,这一工艺过程称为“炼钢”。
含碳量≤2.0%的铁碳合金,铁碳相图中2.0%C的意义。
高温:奥氏体,热加工性能好;常温:以珠光体为主。
为什么炼钢:生铁无法广泛应用。
含碳高:高温下无奥氏体;性能不良:硬脆、韧性差、焊接性能差,不能加工;杂质多:S、P、夹杂物含量高。
钢中常见元素:五大元素:C、Mn、S、P、Si(必须要求)。
其他元素:V、Cr、Ni、Ti、Cu等(根据钢种)。
存在原因:①工艺限制:S、P无法完全脱除;②原料残余:废钢残余Cu、Zn;③改善性能:Mn提高强度Al细化晶粒。
元素含量:①国标要求:GB;②企业标准:企业自定;③其它国家标准:SWRCH82B(日本)。
炼钢工艺流程炼钢“全三脱”工艺流程配有4座300t KR脱硫站、2座300t脱磷转炉、3座300t脱碳转炉;脱磷工位和脱碳工位采用“2+3”双高跨布置,便于“半钢”铁水倒运;精炼配有2座300t双工位RH炉、2座300t CAS炉和1座300t LF炉;连铸采用4台双流板坯连铸机。
工艺特点:采用先进的“一罐到底”、“全三脱”技术,钢水100%精炼工艺处理,铸机高拉速,打造高效快节奏的洁净钢生产平台。
“全三脱”工艺流程如图1所示。
转炉炼钢工艺技术把铁水与废钢混合,倒入转炉中然后吹氧,炉温大约上升到1600℃,炉内反应非常剧烈,象火山爆发一样,将碳与主要杂质迅速烧掉(铁水中的锰和硅被氧化,铁水中的碳也被氧化成二氧化碳)。
整个过程仅约30分钟,而且不再添加任何燃料,就可炼一炉钢,甚至可做到“负能炼钢”用这种方法炼钢,质量可以与平炉炼出的钢相媲美,所需时间却只有平炉的1/10,效率很高。
VD设备及典型钢种的冶炼工艺
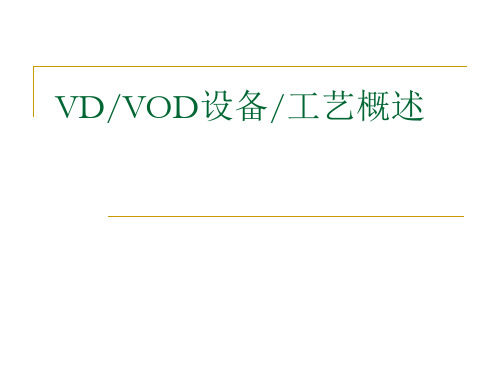
熔池搅拌强度:调整至最大便于有效脱硫去夹杂 脱气时间:在最低压力下根据反应平衡计算所需
的脱气时间;
钢水中氢和氧的平衡
吸氢途径
脱气后水分来源:保温剂;钢包耐火材料;中间包耐材; 气相-渣:
1.在CaO-SiO2系中,单硅酸盐的水蒸气溶解度最低,无论增加CaO还 是SiO2,水蒸气溶解度都增高,特别是呈碱性时显著地增加。
物变性为液态的铝酸钙,并迅速上浮,减少钢 水中的夹杂物和氧含量,纯净钢水。
VD/VOD炉真空精炼能力:
去氢—一般从5ppm脱至<1.5ppm 脱氮—根据不同钢种去除量大于25% 脱碳和升温—超低碳钢和加铝升温 脱氧—根据碳氧平衡而定 脱硫—接近于渣钢的反应平衡值 有害元素去除—去除有较高蒸汽压的元素
发展历史
二十世纪60年代和70年代,炉外精炼技术形成了真空和非真空两大系列。
真空处理: 1965年西德开发的用于超低碳不锈钢生产的真空吹氧脱碳法(VOD)和1967年美国的真空电弧加热去气法
VAD); 1965年瑞典开发用于不锈钢和轴承钢生产的有电弧加热、电磁搅拌和真空脱气的钢包精炼炉法(ASEA-
盖真空罐盖;开启真空泵;调节真空度和吹氩 强度;保持真空;氮气破真空;移走罐盖;测 温取样;喂丝微调成分;停吹氩;吊包出站。
SKF); 1978年日本开发用于提高超低碳钢生产效率的RH吹氧法(RH-OB)。 非真空处理: 1968年美国开发用于低碳不锈钢生产的氩氧脱碳精炼法(AOD); 1971年日本开发配合超高功率电弧炉,代替电炉还原期对钢水进行精炼的钢包炉(LF)以及后来配套真空
脱气(VD)发展起来的LF-VD; 喷射冶金技术如1976年瑞典开发的氏兰法(SL法),1974年前西德开发的蒂森法(TN法),日本开发的川
钢厂各个车间生产工艺(图片)
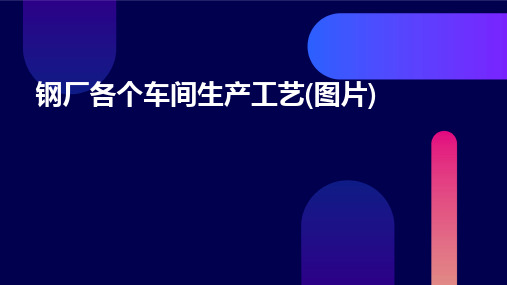
转炉炼钢工艺
总结词
环保、高效、低成本
详细描述
转炉炼钢工艺是一种利用氧气和铁水反应来生产钢的工艺。它具有环保、高效和低成本等优点,是目 前应用最广泛的炼钢工艺之一。转炉炼钢工艺流程包括铁水预处理、转炉炼钢和精炼等环节,最终得 到不同品质和规格的钢材。
电弧炉炼钢工艺
总结词
灵活性、小规模、高合金钢
详细描述
直接还原铁工艺
总结词
直接还原铁工艺是一种将铁矿石直接还原成海绵铁的工艺,通常在较低温度下 进行,以避免产生铁水。
详细描述
直接还原铁工艺通常使用天然气或煤作为还原剂,将铁矿石在较低温度下进行 还原,得到海绵铁。该工艺具有能耗低、污染小等优点,但同时也存在生产效 率较低、成本较高等问题。
熔融还原铁工艺
THANK YOU
球团车间生产工艺
总结词
球团是将细磨物料通过造球机制成球形团块,再经过 高温焙烧,使物料发生固结的工艺过程。
详细描述
球团车间的主要设备包括造球机、焙烧设备、冷却设 备等。造球机用于将细磨物料制成一定粒度和形状的 球形团块,焙烧设备用于提供高温环境,使球团内部 的矿物发生固结。冷却设备用于将焙烧后的球团快速 冷却,以避免其内部的晶体结构发生改变。
炭,以便后续的运输和使用。
烧结车间生产工艺
总结词
烧结是通过加热粉状物料,使其发生物理和化学变化, 最终形成致密块状物料的工艺过程。
详细描述
烧结车间的主要设备包括烧结机、燃烧器、除尘设施等 。烧结机是烧结过程中的核心设备,铁矿粉、溶剂、燃 料等原料在烧结机上经过点火、烧结、冷却等工序,最 终得到烧结矿。燃烧器用于提供烧结所需的热量,除尘 设施用于收集烧结过程中产生的烟尘,以减少对环境的 污染。
典型钢种的生产工艺

典型钢种的生产工艺介绍钢是一种重要的材料,广泛应用于建筑、制造、汽车等各个行业。
不同类型的钢材具有不同的性能和用途,因此在生产过程中需要使用不同的工艺来确保钢材的质量和性能达到要求。
本文将介绍几种典型的钢材生产工艺。
1. 高碳钢的生产工艺高碳钢是一种含碳量较高的钢材,通常含碳量在0.6%至1.5%之间。
高碳钢具有较高的强度和硬度,适用于制作刀具、弹簧和轴承等高强度要求的产品。
高碳钢的生产工艺主要包括以下几个步骤:1.原料准备:选择优质的生铁和合金原料,按照一定的配比进行混合。
2.炼钢:将原料放入炼钢炉中,经过高温熔炼和除杂处理,去除杂质和不良元素。
3.精炼:对炼钢得到的钢液进行精炼处理,包括脱气、脱硫和脱磷等过程,以提高钢液的纯净度和均匀度。
4.进一步加工:将精炼后的钢液进行连铸、轧制、锻造和热处理等工序,使钢材达到所需的形状和性能。
5.检验和包装:对生产出的高碳钢进行严格的检验和品质控制,确保产品符合标准要求,并进行包装和标识。
2. 不锈钢的生产工艺不锈钢是一种具有耐腐蚀性能的钢材,主要由铁、铬、镍和少量的其他元素组成。
不锈钢具有耐高温、耐腐蚀和美观的特点,广泛应用于化工、食品加工和医疗设备等领域。
不锈钢的生产工艺包括以下几个步骤:1.原料准备:选择高质量的生铁和合金原料,根据不锈钢的成分需求进行配比。
2.熔炼:将原料放入电炉或转炉中,通过高温熔炼和精炼处理,去除杂质和不良元素,得到纯净的钢液。
3.进一步加工:将熔炼得到的钢液进行连铸、轧制、退火和冷加工等工序,以获得所需的形状和性能。
4.钢材表面处理:对不锈钢进行酸洗、机械抛光或电解抛光等工艺,使钢材表面平整、光滑和无污染。
5.检验和品质控制:对生产出的不锈钢进行严格的化学成分分析、物理性能检验和表面检查,确保产品符合标准要求。
6.包装和出厂:将符合要求的不锈钢产品进行包装和标识,并进行储存和出厂销售。
3. 高强度钢的生产工艺高强度钢是一种具有更高强度和耐用性的钢材,常用于汽车、航空航天和桥梁等领域。