典型钢种的生产工艺
炼钢生产工艺流程-概述说明以及解释

炼钢生产工艺流程-概述说明以及解释1.引言1.1 概述炼钢生产工艺流程是指钢铁制造过程中的一系列步骤和工艺,旨在将生铁转化为高品质的钢材。
这个过程通常包括炼铁和炼钢两个主要阶段。
炼铁是将铁矿石经过冶炼和还原等多个步骤,从中提取出生铁的过程。
生铁是含有较高碳含量的铁合金,一般还含有一些杂质,需要进行炼钢进一步提纯。
炼钢是在特定条件下,通过控制温度、压力、氧气流量等参数,对生铁进行加工和熔炼,以去除杂质并调整钢材的成分和性能。
炼钢生产工艺流程在各个钢铁企业和工厂可能存在差异,但通常包括以下几个关键步骤:配料、炼钢炉装料、炉前处理、溶解炼炉、精炼、铸钢、连铸以及后续的淬火、热处理和表面处理等工序。
在配料阶段,各种原材料,包括铁矿石、废钢、合金等,按照一定比例混合,以满足最终产品的技术要求。
接下来是炼钢炉装料,将配料装入炼钢炉中,并控制好加热和冶炼条件。
炉前处理是指在进入炼钢炉之前对原料进行预处理,以去除杂质和调整成分。
这一步通常包括破碎、磁选、筛分等物理处理和烧结、还原等化学处理。
溶解炼炉是炼钢的关键过程,原料在高温下熔化,各种杂质被氧化、还原或浮渣分离的方式去除。
精炼是对溶解炼炉的产物进行进一步处理,通过吹氧、渣化反应等技术手段,去除残余杂质,调整成分组成和温度。
接下来是铸钢阶段,将精炼后的钢液倒入连铸机中,通过结晶器冷却凝固,形成连续块或板。
这些块或板可用于制造各种钢材产品,如钢板、钢管、钢坯等。
炼钢生产工艺流程的最后几个过程是后续处理,包括淬火、热处理和表面处理。
通过这些工序,钢材的性能、硬度、韧性、耐腐蚀性等可以得到进一步改善和优化,以满足特定应用需求。
总的来说,炼钢生产工艺流程是一个复杂且关键的过程,需要合理的工序安排、严格的质量控制和先进的技术手段。
它不仅影响到钢材质量和性能,也对钢铁企业的生产效率和经济效益产生重大影响。
1.2 文章结构文章结构部分的内容应该是对整篇文章的组成部分进行简要介绍。
金属工艺学-各种钢的总结
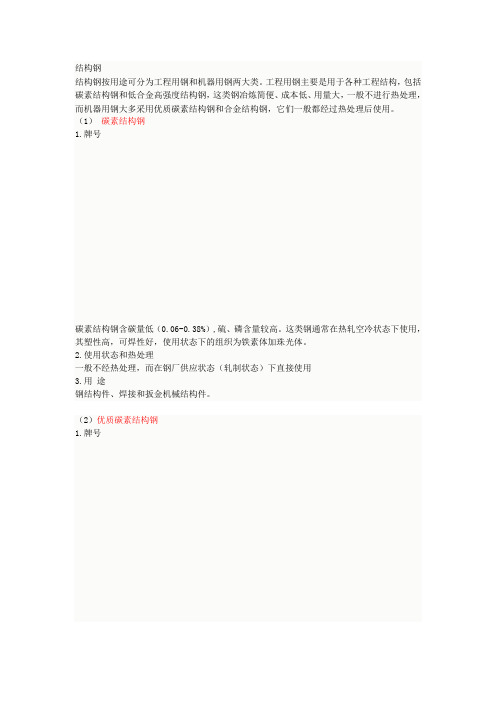
结构钢结构钢按用途可分为工程用钢和机器用钢两大类。
工程用钢主要是用于各种工程结构,包括碳素结构钢和低合金高强度结构钢,这类钢冶炼简便、成本低、用量大,一般不进行热处理,而机器用钢大多采用优质碳素结构钢和合金结构钢,它们一般都经过热处理后使用。
(1)碳素结构钢1.牌号碳素结构钢含碳量低(0.06-0.38%),硫、磷含量较高。
这类钢通常在热轧空冷状态下使用,其塑性高,可焊性好,使用状态下的组织为铁素体加珠光体。
2.使用状态和热处理一般不经热处理,而在钢厂供应状态(轧制状态)下直接使用3.用途钢结构件、焊接和扳金机械结构件。
(2)优质碳素结构钢1.牌号(3)低合金高强度结构钢低合金高强度结构钢是在碳素结构钢的基础上,加入少量的合金元素发展起来的,原称为普通低合金钢。
1.牌号2.性能特点强度高于碳素结构钢,可降低结构自重、节约钢材;具有足够的塑性、韧性及良好的焊接性能;具有良好的耐蚀性和低的冷脆转变温度。
3.成份特点低碳:含碳量≤0.2%低和金:主加元素为锰4.热处理特点在热轧状态下使用,组织为铁素体加珠光体。
5.典型钢种及用途Q345是应用最广、用量最大的低合金高强度结构钢,广泛用于石油化工设备、船舶、桥梁、车辆等大型钢结构中。
(4)渗碳钢1.成分:含碳量0.10-0.25%的合金钢,主要加入能提高淬透性的Mn、Cr、Ni等元素;2.性能特点:经热处理后表硬里韧、耐磨性及抗疲劳性好;3.渗碳件一般的工艺路线:4.用途应用很广,主要用于制造渗碳零件,如变速齿轮、内燃机凸轮轴等各种表面耐磨件。
5.常用的渗碳钢低淬透性渗碳钢:15Cr、20Cr等,心部强度低,尺寸和载荷小的齿轮和滑块;中淬透性渗碳钢:20CrMnTi、20CrMn等,心部强度较高,用于制造中等强度的耐磨零件,如汽车、拖拉机的变速齿轮、齿轮轴等;高淬透性渗碳钢:18Cr2Ni4WA、20Cr2Ni4A等,淬透性很高。
用来制造承受重载荷和强烈磨损的重要零件,如飞机、坦克中的曲轴及重要齿轮等。
冷轧基板SPHC钢转炉直上规模化生产

2020年第2期典型冷轧基板钢种SPHC 钢属低碳、低硅、低硫铝镇静钢,具有较强的延展性及冷加工性能,用途广需求量大。
钢种特性要求决定了其基本的冶炼任务为深脱氧、深脱硫、控铝、控硅、夹杂物控制。
生产实践表明,该类钢种冶炼工艺的复杂性和难点还比较突出,传统工艺为了实现低硫目标往往采用铁水预处理工艺;为实现精确控铝、深脱氧、深脱硫、夹杂物及流动性控制往往必须采用精炼处理工艺,从而形成了铁水预处理→转炉冶炼→LF (RH )精炼→连铸的典型生产工艺流程。
传统工艺流程已经很成熟稳定了,不论在生产的稳定性和连续性、质量控制已经没有太多问题,但存在工艺流程复杂、工序多、生产成本高、效率低等问题。
在行业产能过剩、市场竞争激烈、成本控制压力大的背景下,很多冶金工作者热衷于研究精简化的生产工艺流程。
传统工艺流程中铁水预处理和精炼工序趋于省略。
SPHC 钢转炉直上浇铸的生产工艺,近年来在国内也初步取得了一定的成果,但存在的问题是生产不稳定,钢水流动性不好(絮流)、钢中Al 和S 成分控制不稳定、连浇炉数低等。
笔者在柳州钢铁集团公司柳钢转炉炼钢厂120t 转炉作业区,通过研究摸索优化工艺,解决了上述难题,实现了冷轧基板SPHC 钢转炉直上连续规模化批量生产的目的,生产过程控制稳定、钢的质量控制接近或等同于原走精炼工艺流程的水平。
因简化了生产工序,提升了生产效率,降低了生产成本。
炼钢工序工艺简介柳钢为华南地区特大型钢铁联合企业。
柳钢转炉炼钢厂为柳钢钢铁制造流程上极其重要的工序,近年来通过技术改造,已装备了目前国内主流先进的炼钢工艺装备,在产量、品种、质量上面已达到国内同类企业先进水平。
2019年钢产量达到1367万吨,品种涵盖了建筑、造船、桥梁、汽车、及其他工业用材。
采用SPHC 转炉直上工艺的主要生产现状如下:生产条件柳钢转炉炼钢厂第二作业区装备2套颗粒镁喷吹脱硫装置,3座120t 顶底复吹转炉,2台120t LF 精炼炉,1台120t RH 精炼,3台断面220mm ×(1000~1810)mm 板坯连铸机,2台断面165mm ×165mm7机7流方坯连铸机。
典型钢材的规格与生产

24
轧制钢坯生产工艺过程由哪些基本工序组成,其特点是什么?
轧制钢坯所用轧机的主要形式有初轧机、钢坯连轧机和 三辊开坯机3种。钢坯连轧机直接安装在方坯初轧机或方 一板坯初轧机的后面,连轧钢坯生产仅是初轧生产的一 个环节。三辊开坯生产是老式的开坯方式,有时三辊开 坯机安装在小初轧机的后面,或独立布置。 初轧钢坯生产大多采用钢锭做原料。为了充分利用热 能,初轧厂使用的钢锭大部分是刚脱模的高温热锭.只 有在生产环节受到障碍时才采用冷锭。由于钢锭质量大、 断面大、而高(长)度不大,因而通常采用坑式均热炉进行 加热,只有少量小钢锭及合金钢锭在连续式加热炉中加 热。
26
(8)轻轨,单位长度的质量为11—24kg/m; (9)矿用工字钢,仅有9号、11号两种; (10)矿用u形钢,以每米多少千克表示.中型轧机生产 的u形钢有18u、25u和29UI即18kg/m、25kg/m和 29kg/m的U形钢; (11)H型钢,其规格以腹板高度(腰高)和腿宽(翼缘宽度) 表示,中型万能轧机可生产腹高600mm、翼缘宽 300mm以下的H型钢。
22
常用热轧钢坯有哪些规格?
钢坯是钢锭(也有采用连铸坯)经初轧或开坯得到 的半成品,是各类轧机的原料。钢坯断面有方、 园、扁、矩形和异形等数种,相应称为方坯、圆 坯、扁还、矩形坯和异形坯,表示方法参见前面 表1—2。
23
采用何种钢坯,主要与所要轧制的成品形状有关。轧 制简单断面型钢时,选用与成品断面相近的方坯或矩 形坯。轧制扁钢、角钢等扁形成品时,选用矩形坯或 扁坯。生产工字钢、槽钢时最好用异形坯。圆坯是生 产无缝管的原料,故称作管坯。 在初轧机上可轧出150mmX150mm450mm×450mm的方坯、100mmX300mm500mm×2000mm的板坯和大规格的圆坯及异形坯。 在钢坯这轧机上可得到50mmx 50mm-180mm x180mm的方坯和各种个小规格的扁坯和圆坯。
炼钢车间生产工艺简介

一 级 真 空 泵
二 级 真 空 泵
钢包
炼钢车间生产工艺简介
(2)主要功能:脱碳、脱气、调整钢水成份和温度、 去除夹杂等,尤其是脱[H]效果显著;
(3)冶炼钢种:重轨钢系列、弹簧钢系列、工业纯 铁等。
精诚合作
携手共赢
条材总厂一炼钢分厂炼钢车间
(3)[Mn]的氧化反应 [Mn]的氧化反应
炼钢生铁中含有一定量的[Mn],在炼钢熔池中,有一部分[Mn]会被氧化 炼钢生铁中含有一定量的[Mn],在炼钢熔池中,有一部分[Mn]会被氧化 [Mn] [Mn] 掉。
(4) 脱磷反应
造成钢材冷脆 有利于脱磷的条件—— 三高一低” ——“ 有利于脱磷的条件——“三高一低”: 高碱度、大渣量、 FeO)、 )、低温 高碱度、大渣量、高(FeO)、低温
炼钢车间生产工艺简介
3、炼钢用原材料
炼钢用原材料一般分为主原料、辅原料和各种气体介质。 一、主原料:铁水、废钢 二、辅原料:铁合金、造渣剂 1)铁合金: 吹炼终点脱除钢中多余的氧,并调整成 分达到 钢种规格,需加入铁合金以脱氧合金化 2)造渣剂:石灰、轻烧白云石、萤石等 三、气体介质:氧气、氩气、氮气等
2.2 VD炉简介
炼钢车间VD炉原计划于今年7月份拆除,在其基 础上建设2#RH炉,但在综合权衡其利弊后,拆 除计划暂时取消。 (1)主要设备:真空泵系统、炉盖、双工位地坑、 计测仪表及控制系统; (2)主要功能:真空脱气、去夹杂、均匀成份和 温度等,尤其是脱氮效果较好; (3)冶炼钢种:82B系列、帘线82A等对[N]要 求高的钢种。
炼钢车间生产工艺简介
一、炼钢基本原理与工艺
1、炼钢的基本任务
1).脱碳、脱磷、脱硫、脱氧; 2).去除有害气体和夹杂; 3).调整成分和温度;
钢铁公司全三脱冶炼技术

传统流程存在的上述基本矛盾造成该流程生产 洁净钢存在以下缺点:
1)由于钢水提纯依赖炉外精炼,造成生产批量 小,不能大批量生产洁净钢;
2)由于流程存在回硫、低碳脱磷和钢水过氧化 等问题,造成磷、硫和钢中夹杂物控制不稳定;
3)由于渣量大,不能形成渣循环,造成生产成 本高,生产效率低。
2、“全三脱”新流程
2、关于铁水“全三脱”工艺的价值
1)建立起高效、低成本的洁净钢生产工艺平台, 提高产品竞争力; 2)可以使用较高含P的矿石,铁水含磷可以放到 0.1~0.15%,有利于降低矿石采购成本; 3)有利于脱碳转炉使用锰矿,还原成钢水[Mn], 可以降低合金成本; 4)脱碳转炉渣可为脱磷转炉使用,并少加石灰; 5)加快转炉(大型)冶炼节奏,适合于现代高拉 速板坯铸机匹配运行,提高生产效率; 6)有利于运行过程时间紧凑,实现节能。 不能将其价值局限在冶炼超低磷钢。
3、“全三脱”冶炼工艺技术国内外发展简况
根据所用的不同容器,铁水脱磷可分为两类:一 种是在铁水包或鱼雷车中进行脱磷,另一种就是在 转炉内进行铁水预处理脱磷。与混铁车内或铁水包 中进行的铁水预处理相比,在转炉内进行脱磷预处 理的优点是转炉的容积大、反应速度快、效率高、 可节省造渣剂的用量,吹氧量较大时不易发生严重 的喷溅现象,也不存在鱼雷车和铁水包中脱磷时温 降大、处理时间长等问题,有利于生产超低磷钢, 尤其是中高碳的超低磷钢。因此,近年来在转炉内 进行铁水脱磷的工艺技术得到了较大的发展。
20世纪50年代以前,长期以来总以为一种工艺 、一个装置的功能越多越好,而忽视整个制造流 程生产的总体发展趋势。例如平炉就是一个实例 ,平炉确实有很多功能,一度曾是主要的炼钢方 法,但由于其冶炼周期过长、能耗高,很难与新 兴的连续铸钢工艺经济地匹配起来,因而,随着 全连铸体制钢厂的推行,平炉炼钢工艺趋向萎缩 。
不锈钢生产工艺简介知识讲解
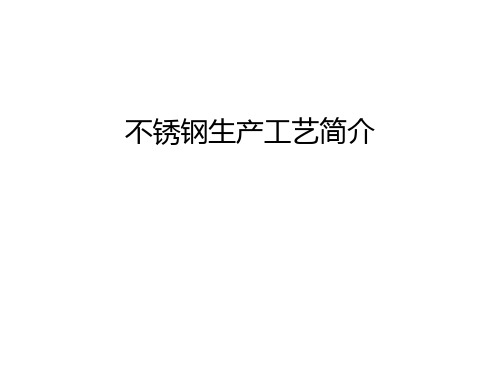
多辊轧机优点
• (1)小直径工作辊; • (2)工作辊硬度高、换辊方便,可生产
高品质带钢; • (3)轧薄能力强; • (4)轧机牌坊刚性大,板形控制手段多,
且采用大张力轧制,板形较好; • (5)设备投资不大。
轧机类型
• DMS二十辊森吉米尔轧机(C为二十辊
辊系配置图)
二中间 工作辊
后支撑
一中间
• 2、酸洗
• 酸洗是冷轧不锈钢的必经工序。现代化 宽带不锈钢生产都是将退火与酸洗设在 同一机组连续作业,称之为连续退火酸 洗机组,如AP(H)、AP(C)等。
• 酸洗的目的:酸洗的目的是去掉热轧及 退火过程中在钢带表面形成的铁鳞,即 氧化层。除此之外,酸洗另一个目的是 对不锈钢表面进行钝化处理,提高钢板 耐蚀性。冷轧成品的酸洗尤为重要。
3、横切
• 当产品以切板状态交货时,带钢要在横 切机组上剪板,一般的横切机组为连续 剪切机组。机组上配置开卷机、圆盘剪、 矫直机、打印装置、垫纸装置、定尺剪、 垛板台等设备,可多功能连续作业。
• 平板板形要求较高,故横切有矫直机
1、平整
• 平整是冷轧不锈钢精整的第一道工序, 也是冷轧的最后一道工序。它不以减小 厚度为目的,而是①改善力学性能,保 证产品的成形加工性;②修正板形,得 到平直的钢板;③根据用户的使用要求, 加工光面或麻面板,并改善表面质量。
平整工艺
• 平整辊 • 干法平整、湿法平整 • 辊型 • 轧制力、张力 • 道次数、延伸率
2、纵切分条
• 当带钢成卷交货时,要在纵切机线上用 圆盘剪切去毛边,为适应来料的宽度变 化,圆盘剪距离可以调整。圆盘剪操作 主要在于适当调整上下剪刃的间隙量和 重合量,间隙量一般随着材料厚度而增 大,一般为材料厚度的7-12%,而重合最 虽与材料厚度有关,但不完全是对应关 系,应结合操作经验确定。
典型钢种炉外精炼
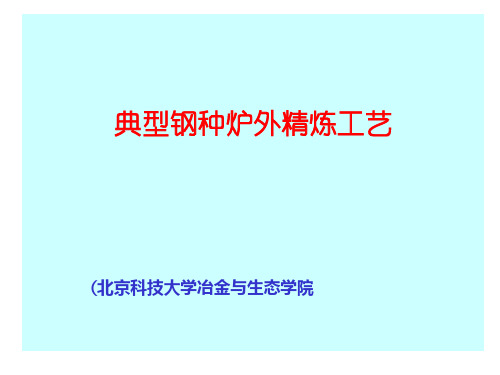
(2)影响钢中铝含量波动的因素。
转炉终点控制:终点碳含量的高低和终点命中
率。
下渣量和终渣的氧化性:不同的炉次,不同的
转炉操作水平差别很大。 6(FeO)+4[Al]=2(Al2O3)+6[Fe] LF炉操作工艺:气氛控制、搅拌剧烈程度、炉 渣流动性、温度高低、精炼时间长短等。
4.连铸容易结瘤,影响连浇。
(1)影响水口结瘤的主要因素之一是钢液中Al2O3夹杂物量的多 少,最大限度去除Al2O3夹杂是最有效的办法,事实也证明大
量的Al镇静钢并不需要用Ca处理。
(2)Ca的加入量主要决定于钢液中Al2O3夹杂物的量,习惯上 用Ca/Al(s), Ca/Al(t), Al(s)/Al(t)来衡量钢液中需要加入的钙量 仅适用在某一特定工况条件下的经验公式,并不十分科学。用 Ca/T[O]可能更为合理一些。
a Al 2O 3 K 2 3 a Al aO
aO a Al 2O 3 /( K a )
3 2 Al
炉渣成分对钢中氧含量的影响
Si脱氧: [Si] + 2[O] = (SiO2)
aSiO2 K Si 2 aSi aO
aO aSiO2 /( K Si aSi )
MnO-Al2O3-SiO2渣系相图
精炼工艺特点:
夹杂物总量要低:夹杂物生成早;容易上浮;容易被顶渣吸 收。采用铝脱氧;高碱度造渣。
D类夹杂物(钙、镁铝酸盐,TiN)几乎没有:极低的钙含量;合 适的镁含量;极低的钛、氮含量;合理的炉渣碱度。 大颗粒夹杂:查明大颗粒夹杂物的性质和类型,分析其来源, 找出去除措施。
(2)高硫易切削非调质钢
CaO-Al2O3-SiO2渣系等硫容量图
2.高洁净度-炉渣吸附Al2O3夹杂物
- 1、下载文档前请自行甄别文档内容的完整性,平台不提供额外的编辑、内容补充、找答案等附加服务。
- 2、"仅部分预览"的文档,不可在线预览部分如存在完整性等问题,可反馈申请退款(可完整预览的文档不适用该条件!)。
- 3、如文档侵犯您的权益,请联系客服反馈,我们会尽快为您处理(人工客服工作时间:9:00-18:30)。
0.15
0.012
0.018 0.005-0.07 0.012 0.03
0.05-0.11 ≤0.007
0.07
≤0.004
SDC05 判定 ≤0.004 0.05 0.11-0.16 0.012 0.013 0.020-0.060 0.05-0.10 ≤0.005
目标 ≤0.003 0.03 0.13
低0.2。 r:塑性应变比,n:加工硬化指数,是评价深冲性能的主要指标 。
首钢-力学性能做拉伸(纵向)和晶粒度试验,结果不做判定,供用户参考。
主要生产工艺
1、生产计划
要求轧制本系列钢种的轧制计划单前全部更换F1-F7精轧工作辊, 在本系列钢种作为烫辊材时,掌握出钢节奏。
2、加热制度
加热时间根据7-9min/cm,230mm坯型加热时间为3.0-4.5小时; 250 mm坯型加热时间为3.5-5.0小时。根据成品钢板厚度、宽度和开轧 温度的设定要求及出钢节奏的快慢,各段温度在上述范围内适当做出 灵活调整。
Si≤
0.03 0.03
0.03 0.03
Mn 0.190.26
0.22 0.190.24
0.22
P≤ 0.01 3
0.01 0.01 2
0.01
S≤ 0.012
Alt
0.0230.050
0.01 0.012
0.03
0.0250.050
0.01 0.03
N
≤0.005 ≤0.004 ≤0.004 2 ≤0.004
牌号
加热温度/℃ 均热温度,℃ 出钢钢坯温度,℃
SDC01/SDC 范围
03
目标
1220-1300 -
1240-1300 -
1230-1290 1250
注:出炉温度的范围为±20℃;各段温度仅为参考值,最终控制出钢温度 在
范围内。
3、温度制度
轧制过程严格控制关键点温度,特别是粗轧出口温度、终 轧温度和卷取温度,轧钢制度温度如下表13所示。
冷轧用钢―SDC系列
常见牌号:SDC01、 SDC03、 SDC04、 SDC05 牌号意义:企标(首钢牌号)
S:Shougang D:Drawn, 表示冷成形用板材产品 C:Cold,表示冷轧产品 01、03、04、05:是钢种序号。
SDC01、SDC03
SDC01:(1)可制作汽车零部件,家具外壳、桶钢制家具等 简单成型、弯曲或焊接加工的产品;
6、精轧
(1) 轧制过程中严格控制除磷水情况,采用双排除鳞,保证除掉精轧过 程中形成的氧化铁皮;
(2) 根据情况,调整机架间水量的大小; (3) 在保证出F7后板形的情况下,尽量较少F7的调平操作并尽量减少带
钢中心线偏差。
7、冷却工艺制度
轧后冷却采用前段层流冷却模式(CTC=0),根据工艺需要可适当 调整冷却模式,工艺设定以保证目标卷取温度为依据。
典型钢种的生产工艺
典型钢种介绍
冷轧用钢:SDC系列;SPHC/D/E 碳素结构钢:Q195;Q235 低合金高强度结构钢:SS400;Q345
管线钢:X42-X100
船板钢:A、B、D、E 、A32-A40;D32-D40 高耐候钢:Q295GNHL、 Q345GNHL、 Q390GNH、SPA-H 汽车结构用钢及IF钢(汽车内、外板) 高强钢:DP、TRIP、超细晶钢
8、卷取工艺
(1) 卷取操作应密切关注卷取温度值和设备运行状况; (2) 换辊期间检查夹送辊、助卷辊等辊的表面质量,不得有影响表面质
量的缺陷存在。
超低碳SDC04、SDC05
化学成分
钢种
C
Si≤ Mn
P≤
S≤ Alt
Ti
N
SDC04 判定 ≤0.006 0.03 目标 ≤0.003 0.01
0.05-0.25 0.017
牌号
粗轧出口,℃ 精轧入口,℃ 终轧,℃ 卷取,℃
SDC0 范围
1
目标
SDC0 范围
3
目标
1040-1100 1030-1090 910-950 710-750
1070
-
930
730
ቤተ መጻሕፍቲ ባይዱ
1040-1100 1030-1090 910-950 730-770
1070
-
930
750
注:(1) 粗轧出口温度的范围为±30℃,其余各温度点的温度范围为±20℃; (2) 根据现场情况可以适当调节各温度点,厚规格温度按照下限控制, 薄规格温度按照上限控制。
270~37 0
30
32
34
35
36
1.3
注:(1) 拉伸试验取横向试样。无明显屈服现象时采用Rp0.2,否则采用下屈服强度ReL。 厚度>0.5mm且≤0.7mm时,屈服强度值可以增加20 MPa;厚度≤0.5mm时,
屈 服强度值可以增加40MPa。
(2) r90值和n90值的要求仅适用于厚度≥0.50mm的产品,当厚度>2.0mm时,r90可 以降
4、粗轧
(1) 粗轧道次设定模式:1+5等模式; (2) 中间坯厚度:中间坯厚度≥3倍成品厚度; (3) 粗轧阶段严格控制除鳞情况,R1第1道次除磷,R2 至少采用1、3、
5道次除鳞,保证除掉粗轧过程中形成的氧化铁皮; (4) 调整粗轧板形,保证带钢对中;要求板形良好。
5、保温罩
为了保证中间坯温度的均匀性,建议使用保温罩。
0.01 0.01 0.025
0.07
≤0.003
力学性能要求-GB
牌号
屈服强度 N/mm2
抗拉强度, Rm, N/mm2
断后伸长率,A80mm,(L0=80mm,b= 20mm),%,≥
<0.4
0.4~ <0.6
0.6~ <1.0
1.0~ <1.6
1.6~ 2.5
r90值 ≥
n90值 ≥
SDC 140~ 04 210
270~ 350
34 36
38
39
40
1.6
0.18
注S0:D5(C 1)11拉2800伸~试验23取73横00~向试样3。6 无明3显8屈服现39象时采4用0Rp0.241,否则采1用.9下屈服0强.2度0 ReL。厚度>0.5mm且≤0.7mm时,屈服强度值可以增加20 N/mm2;厚度
(2)具有一定的强度和好的塑性,一般用于成形汽 车的加强件,内板,后横梁轿车顶盖等一般成形件。
SDC03:可制作变形量小的门板、窗、挡泥板、马达外壳等
冲压成型及较复杂变形加工的零部件。
化学成分
钢种
SDC 01
判定 目标
SDC 03
判定 目标
C
0.015-0.04 0.03 0.0170.035 0.03
力学性能-GB
牌号
屈服强 度/MPa
抗拉强 度 /MPa
断后伸长率,A80mm,(L0=80mm,b=20mm)/%,≥ r90值≥
<0.4 0.4~<0.6 0.6~<1.0 1.0~<1.6 1.6~2.5
SDC01 140~280
270~41 0
26
28
30
32
34
-
SDC03
140~240