外胎硫化工序工艺培训(修改)
硫化岗位培训

防护措施
穿戴防护服: 包括防酸碱服、 化学防护眼镜
等
使用防爆工具: 避免产生火花
和静电
定期检查设备: 确保硫化机等 设备正常运行
培训员工:提 高员工的安全 意识和应急处
硫化岗位的职业素养:具备高度的责任心和质量意识,严谨细致的工作态度,良好 的团队协作和沟通能力
技能要求
熟悉硫化设备和工具的使用 方法
了解硫化材料的性能和特点
掌握硫化原理和硫化工艺流 程
具备一定的安全意识和环保 意识
操作规范
硫化前的准备:检查设备、工具和原材料,确保符合要求。 硫化过程:按照工艺要求,控制温度、压力和时间等参数,确保硫化质量。 硫化后处理:对产品进行质量检查、清洁和包装,确保符合质量标准。 安全注意事项:遵守安全操作规程,确保人身安全和设备安全。
硫化岗位培训
目录
单击此处添加文本 硫化岗位培训的目的和意义 硫化岗位的职责和工作内容 硫化岗位的技能要求和操作规范 硫化岗位的安全知识和防护措施 硫化岗位的培训计划和考核标准
培训目的
提高硫化岗位员 工的专业技能和 操作水平
确保生产过程的 安全、稳定和高 效
增强员工对硫化 岗位的认识和了 解
培养员工的团队 协作和沟通能力
提高员工技能水平,确保生产安全
培训意义
规范操作流程,降低事故风险
添加标题
添加标题
添加标题
添加标题
培养硫化岗位专业人才,提升企业 核心竞争力
增强员工安全意识,促进企业可持 续发展
岗位职责
负责硫化工艺的 执行,确保产品 质量和生产效率
硫化工艺常识

硫化工艺常识1.什么是硫化工艺三卡?三卡的感化是什么?三卡:硫化工艺卡、胎侧标识卡和胎面标识卡。
每个硫化机台必须配齐三卡,同时三卡的规格、斑纹和线条必须一一对应。
三卡用于确保工艺参数设定精确、硫化模具安装精确、胎胚应用精确。
2.什么缘故硫化模具变革时要履行首检轨制?防止工艺参数设定缺点、防止三卡用错、防止模具用错和防止进错胎胚。
3.胶囊软洞对轮胎质量会产生什么阻碍?胶囊软洞是胶囊漏的前期征兆。
硫化时在轮胎表里面会有起鼓胞(实包),阻碍轮胎的应用质量。
4.胶囊常显现的问题有哪些?新胶囊:中间线裂口、膨胀不均和砂眼;胶囊应用过程:胶囊穿、胶囊漏、软洞和老化。
5.什么缘故硫化机预热时必须达到规定的预热温度、预热时刻和合模力?因为预热的温度达不到规定要求会在硫化时导致欠硫;预热时刻不足则硫化设备受热不均导致硫化时升温慢和合模力不足;合模力达不到工艺要求会导致成品胎显现胶边和出台等缺点。
6.什么缘故胶囊应用到规定次数时必须强迫改换?胶囊跟着应用次数增多而老化程度加剧,当应用到必定次数后,胶囊的老化程度严峻阻碍成品胎质量,如胎里别处粗拙。
7.什么缘故要严格操纵硫化吊胎时刻?胎胚在机械手上吊的时刻过长会导致胎胚变形和子口脱空,严峻阻碍轮胎质量。
8.什么缘故进灶前应对胎胚进行检查?幸免烘错胎胚,幸免杂质、气泡等其他胎胚缺点造成废次品。
9.喷隔离剂时什么缘故要清理钢棱圈?钢棱圈上聚积过多隔离剂会产生子口裂口和子口圆角等缺点。
10.什么缘故开灶前必须检查上模,确保前一灶轮胎卸出?幸免显现双胞胎及破坏模具。
11.什么缘故硫化号必须放在指定地位?为了规范性、易查看和幸免毁伤其它标识。
12.什么缘故合模过程中操作人员不克不及分开硫化机台?在主动合模过程中假如操作人员不在硫化机前台,当显现专门时不克不及获得及时的处理会破坏设备、毁伤胎胚,造成成品胎缺点。
13.硫化号有何意义和感化?硫化胎号用于注解轮胎临盆的全然信息(临盆年代日、临盆机台、临盆班组和临盆序号),是产品标准中要求的重要标记之一,同时使每一条胎都具有可追溯性。
轮胎厂硫化成型工艺流程

轮胎厂硫化成型工艺流程英文回答:Tire Manufacturing Vulcanization Process.Vulcanization is a critical process in tire manufacturing that involves heating raw rubber with sulfur and other chemicals under high pressure to create cross-links between the rubber molecules. This process results in a strong, durable, and elastic material that is used to make tires.The vulcanization process typically involves the following steps:1. Preparation: The raw rubber is mixed with sulfur, accelerators, and other chemicals to prepare it for vulcanization.2. Molding: The prepared rubber is placed into a moldthat gives the tire its desired shape and tread pattern.3. Heating: The mold is heated under high pressure to initiate the vulcanization process.4. Curing: The rubber cures or vulcanizes over a period of time, typically several hours to days, depending on the size and thickness of the tire.5. Cooling: Once the vulcanization process is complete, the tire is cooled down slowly to prevent cracking and other defects.The vulcanization process can be carried out using different methods, including:Hot molding: The mold is heated externally using steam or hot oil.Press molding: The mold is heated using pressure applied by a hydraulic press.Autoclave molding: The mold is placed in an autoclave, which is a pressure vessel that uses steam or hot water to heat the rubber.The specific vulcanization process used depends on the type of tire being manufactured, the materials used, and the desired properties of the final product.Factors Affecting Vulcanization.Several factors can affect the outcome of the vulcanization process, including:Temperature: The temperature at which the rubber is heated plays a crucial role in the vulcanization process. Too low a temperature will result in insufficient cross-linking, while too high a temperature can cause the rubber to scorch or burn.Pressure: The pressure applied during vulcanization helps to force the sulfur into the rubber and promotecross-linking.Time: The duration of the vulcanization process is another critical factor that determines the extent ofcross-linking and the properties of the final product.Chemicals: The type and amount of chemicals used in the rubber compound can influence the vulcanization process and the properties of the final product.Quality Control.Quality control is essential in the tire manufacturing process to ensure that tires meet the required performance and safety standards. Various tests are performed on tires throughout the manufacturing process to check their physical properties, such as strength, durability, and elasticity.By carefully controlling the vulcanization process and other aspects of tire manufacturing, manufacturers can produce high-quality tires that meet the demands of the automotive industry.中文回答:轮胎厂硫化成型工艺流程。
硫化机培训计划表

03工段车间
掌握硫化机开合模常见故障的原因查找 及处理方法。
内训
03工段车间
掌握硫化机机械手常见故障的查找原因 和处理方法。 掌握硫化机中心机构的结构和安装,并 能对常见故障进行处理。 掌握硫化机卸胎机构的常见故障的原因 查找及处理方法。
内训
03工段车间
内训
03工段车间
内训
考核方式(开卷/闭卷/现场提 问) 现场提问
硫化机培
班组
2016/3/10
全体维修人员
22
班组
2016/3/31
全维修人员
22
班组
2016/4/14
全体维修人员
22
班组
2016/4/28
全体维修人员
22
工段
硫化机培训计划
培训地点 培训师 培训目标 了解硫化机重点部位的周期性维护保养 知识,并按周期计划实施。 培训性质(内训/外 训) 内训 03工段车间
03工段
培训范围 培训内容 硫化机的周期性检查保养和维护(主 要包括机械手、电机、墙板、减速机 、安全拉杆、安全刹车、中心机构、 固定螺栓、阀门、调模机构等部件) 培训硫化机开合模的故障维修(主要 包括合模接近到位时不合模,手动合 模电流大;合模到位后,运行硫化步 序,无内压内温;合模力不足;蒸锅 式装胎合模后,大量蒸汽从上、下蒸 汽室间泄漏 等故障) 培训硫化机装胎机构的故障维修(主 要包括机械手不转入/转出;机械手不 张开/闭合) 培训硫化机中心机构的故障维修(主 要包括下环不升;上环不能升降或动 作缓慢) 培训硫化机卸胎机构的故障维修(主 要包括卸胎支臂不进/出;卸胎支臂不 升/降) 培训时间 培训对象 培训人数 班组 2016/2/25 全体维修人员 22
半钢硫化基本知识培训
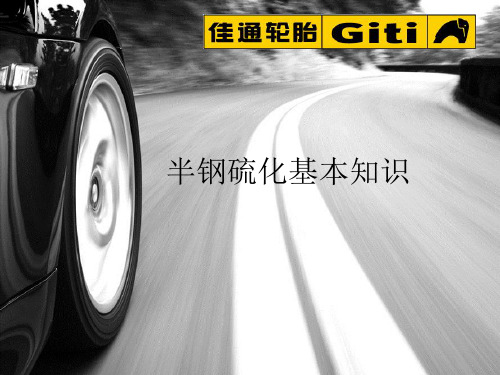
十四、外温不足延硫
外温标准温度为173±3℃
项目 167℃≤外温<170℃ 164℃≤外温<167℃ 外温<164℃ 累计持续时间 <5min ≥5min <2min ≥2min <2min ≥2min 技术要求 不延时,轮胎正常外检 第9步延时1分钟 不延时,轮胎正常外检 第9步延时2分钟 不延时,轮胎正常外检 第9步延时3分钟
八、定型套筒/合模力规定
*定型套筒规定
项目 螺帽高度A (±5mm) 定型套筒高度B (±5mm) 中心机构拉伸高度C (±5mm) 技术要求 50,左右差≤5mm。 依制造标准而定,左右差≤5mm。 依制造标准而定,左右差≤5mm。
*合模力规定
项目 合模力根据轮胎模具J-DIA大小选定 J-DIA≤600 600<J-DIA≤700 700<J-DIA 冷模 (ton) 45±10 60±10 70±10 技术要求 热模 (ton) 70±10 90±10 105±10
备注:对于节假日后生产第一灶,除了在第二步(蒸汽排凝)延时1 分钟外,在第九步(氮气进)还要延时2分钟。
十三、氮气泄露报警规定
项目 一级报警 二级报警 三级报警 技术要求 0.15<第7步始末压力差≤0.30MPa 第7步开始压力必须≥1.80 MPa 0.30<7步始末压力差≤0.45MPa 第7步始末压力差>0.45MPa
半钢硫化基本知识
一、硫化概念
1 概念:使橡胶半成品从塑性状态转变为弹 性状态的工艺过程。 2 实质:硫化的实质是在一定的温度和压力 的条件下,橡胶半成品内部产生化学反应, 使线型的橡胶大分子之间通过交联反应转 变成网状或体型结构,获得需要的物理机 械性能(如弹性、强度、硬度、耐磨性等) 的过程。
(min)
硫化工培训课件

(1)缺胶 ①称胶不准;②模温过高;③ 压力不足; ④胶料流动 性太差,可在胶料表面涂洒硬脂酸锌或提高胶料的塑炼的 程度;⑤胶料早期焦烧(死料)。 (2)窝气 ①排气次数不够,适当对产品进行二次排气;② 模具 不合理,加开排气槽;③喷洒少量水。 (3)裂损 ①模温过高;②脱模剂喷洒过多;③出模方式不正确; ④模具上有模痕,应及时清除;⑤过硫。 (4)气泡 ①模温过高;②硫化时间过长;③压力不足;④硫化 不熟;⑤模内或胶料中有杂质或油污。
耐热老化性能; ③优秀的耐天候性。
(3).优异的电绝缘性能
(4).优秀的耐化学药品性能 (5).卓越的耐水、过热水、水蒸汽性能
1-2-3氯丁胶
(1)不饱和性橡胶,化学性质稳定,耐老化 性能优良。 (2)极性橡胶,耐油耐溶剂性能优良,气密 性、粘着性好,有导电性。 (3)易结晶性(Tg=-43℃),有自补强作用, 有自熄性,阻燃,贮存稳定性差,对温度敏 感,需用金属氧化物(ZnO、MgO)来硫化。 (4)弹性较低,耐寒性较差,低温使用不理 想。(极性橡胶共同点)
1-2-4丁腈胶
(1)非结晶、不饱和的极性橡胶,强度低。 (2)优异的耐油、耐溶剂性。 (3)耐热,耐老化,耐磨性较好。 (4)耐气透性良好(有极性的缘故), (5)但电绝缘性不好,属于半导体。 (6)弹性、耐寒性、耐屈挠性、抗撕裂性较差
1-2-5硅橡胶
(1)非碳链饱和性橡胶,能结晶,弹性、耐寒 性、耐热性、耐老化性及耐腐蚀性好。 硅橡胶是所有橡胶中使用温度范围最宽的。 (2)无毒无味,具有生理惰性,有相当好的稳 定性 (3)强力低,耐酸碱性不好,需用白炭黑补强, 不能用硫黄硫化,而是用过氧化物进行交联。
测量值
174℃ 176℃
360S 18MPa
硫化培训(员工)

硫化培训目的:促使硫化工掌握橡胶材料和硫化的基本知识,提高硫化工专业理论知识和操作技能,更有效地服务与新产品开发试试制工作从而提高硫化工自身的素质,使试制开发产品及时按期交样,并确保新模上线生产的产品合格率和生产效率最大化。
一、应知:1.熟知硫化三要素之间的相互关系及对产品的影响。
2.熟知橡胶产品各工序的生产,及其所使用的设备,设备的操作规程,产品的加工方法。
3.熟知模具、设备工装夹具的操作规程,安全知识及保养知识。
4.了解本公司橡胶产品的使用的胶料代号,胶种及硫化工艺性能,以及主导产品的主要工作部位,外观质量标准。
5.应知硫化时间制定的依据,并能对生产中出现的一般质量缺陷进行分析、解决,并对复杂的问题提出改进意见。
二、应会:1.能够熟练掌握及使用各类结构橡胶模具的试模方法。
2.能鉴别各种胶号、胶料及胶料的外观质量的好坏、并能根据胶料代号准确判定材料的硬度。
3.能看懂各类结构的产品图、模具图及了解模具加工的基本知识。
4.会使用游标卡尺、测厚仪、测温仪,并了解其工作原理。
5.能确定出最佳、最合理的硫化工艺参数、操作技能并应用于生产。
7.能分析试模、试生产过程中出现的质量缺陷的原因,并能提出改进意见。
常见橡胶的基本知识橡胶的分类:天然胶与合成胶两种。
1.天然胶( NR):天然胶的原材料来源于橡胶植物树。
其优点为:弹性好、强度高、绝缘性好、变形小、加工方便。
其缺点为:不耐油、耐温性能差、易老化,一般都是并用掺合使用。
一般生产汽车轮胎和一些减震耐磨的橡胶件。
2.合成胶:合成胶有:丁苯胶(SBR)、丁晴胶( NBR)、顺丁胶( BR)、乙丙胶(EPDM )、丁基胶( IIR )、氯丁胶( CR)、丙烯酸脂胶( ACM )、氢化丁晴(HNBR )、氯磺化聚乙烯( CSM)、氟胶( FKM )、硅橡胶( MVQ )等。
2.1 .乙丙胶( EPDM),本厂代号为(6)1优点:耐老化性能非常优异、耐天候、电绝缘性较好、冲击弹性较好、耐油。
轮胎工安全操作规程培训(3篇)

第1篇一、培训目的为了提高轮胎工的安全意识和操作技能,预防和减少事故的发生,确保员工的生命财产安全,特制定本培训内容。
二、培训对象本培训适用于从事轮胎安装、维修、拆卸等工作的所有员工。
三、培训内容1. 安全意识教育(1)安全意识的重要性:强调安全意识是预防事故的关键,要求员工时刻保持高度警惕,严格遵守安全操作规程。
(2)安全法律法规:介绍相关安全法律法规,使员工了解自己在工作中的权利和义务。
(3)事故案例分析:通过分析典型事故案例,使员工深刻认识到事故的危害,提高安全意识。
2. 安全操作规程(1)上岗要求1)持证上岗,经三级安全教育考试合格。
2)劳保用品穿戴齐全、规范,女工应将发辫塞入帽内。
3)严格执行交接班制度并做记录。
4)不准酒后上岗和班中饮酒。
5)不准疲劳上岗,工作过程要集中精力。
6)保持现场整洁。
(2)岗位操作程序1)准备工作1)工作前,必须检查所用工器具(包括千斤顶、电动工具),保证其完好、牢固、可靠。
2)检查空压机连接部位、润滑系统、冷却系统、安全附件等是否完好、可靠。
3)检查电器及线路是否完好、可靠。
4)检查输气管是否完好、有无漏气现象。
2)操作程序1)空压机在充气时必须保持气压为7kg/cm2(即0.7MPa);空压机运行中每小时点检一次,检查电流、气压、温度是否在允许范围内,冷却、润滑、传动系统、安全防护装置有无故障,并排除油水分离器内的油水;打气完毕,必须排空贮气罐余气。
2)更换轮胎时,车辆必须停放在平坦地面,要用掩木掩好其他轮胎。
如需要顶起货箱时,在货箱顶起后,必须用坚固撑杆在货箱两侧将其支撑稳固或在车厢与底盘间垫上硬木,或在销孔内上销,方准进行拆装轮胎。
3)使用千斤顶顶车时,地面应平整坚实,并用坚硬厚木板垫好;千斤顶与车架或前后桥接触处,同样必须用坚硬厚木板垫好。
4)拆卸轮胎时,应放出轮胎内的压缩空气,后轮双轮应同时放气,轮辋上的限制器有严重损地不时必须更换。
5)装胎时应检查钢圈是否符合要求,对止口磨损过多(厚度小于10mm)有裂纹、面变形的钢圈不应装用。
- 1、下载文档前请自行甄别文档内容的完整性,平台不提供额外的编辑、内容补充、找答案等附加服务。
- 2、"仅部分预览"的文档,不可在线预览部分如存在完整性等问题,可反馈申请退款(可完整预览的文档不适用该条件!)。
- 3、如文档侵犯您的权益,请联系客服反馈,我们会尽快为您处理(人工客服工作时间:9:00-18:30)。
外胎硫化工序工艺培训 把轮胎胎胚装入模型内,经过温度、压力和时间三个相互有关的硫化要素,使各部件密实地成为一体达到设计技术预期要求的物理机械性能和轮廓尺寸,成为有使有价值的产品的加工工艺过程,称为外胎硫化工序。 硫化设备 子午线轮胎硫化采用的是定型硫化机。 定型硫化机有硫化大规格轮胎的单模定型硫化机和硫化中小规格轮胎的双模定型硫化机,定型硫化机使用胶囊而不使用水胎,胶囊呈筒状装在硫化机的中心机构上,外胎胎胚不必预先定型,硫化过程中对装胎、定型、硫化、卸胎等过程可全部实现自动控制。 国内广泛使用的是机械连杆式双模定型硫化机,现新上的工厂都在上液压式定型硫化机。机械连杆式定型硫化机机型按使用的胶囊形式不同有A型(或称AFV型)、B型(或称BOM型)和R型(或称RIB型)三类机型。 A型、B型、R型三种硫化机除中心机构外,其设备主要装置和工作原理基本相同。由于中心机构不同,三种硫化机所使用的胶囊形式也不同。 二.设备主要装置 1.传动装置:用来开启模型和对模型产生足够的合模力。 2.中心机构:主要有动力缸、定型套、调整套、胶囊上下卡盘、进出水管口等,主要用来控制胶囊伸缩膨胀,配合卸胎机构,使轮胎脱离下模,控制一次定型高度,向胶囊提供硫化介质。 3.蒸汽室(现多使用热板):蒸汽室分上、下蒸汽室。下蒸汽室固定在机座上,上蒸汽室可上下移动。 4.装胎机构(机械手):将胎胚从存胎盘上抓取后送到下模定位,充气定型。 5.卸胎机构:在上下卡盘下降动作的配合下,将硫化好的外胎取出送入卸胎辊道。 6.活络模操纵控制机构:控制活络模的收缩和张开。 7.安全装置:安全杆。 8.润滑系统:保证硫化机正常生产延长使用寿命,对主机各润滑点进行润滑加油。 9.管道系统:包括蒸汽热水,动力水和各种阀门。(作用:通过管路给硫化机提供各种硫化介质或进行控制) 10.电气控制系统:包括控制管理,主令控制器、程控器、控制柜及电磁阀、触摸屏等。 三.全钢子午线轮胎的硫化工艺流程 1.硫化工艺流程简述 1.1检查胎胚规格花纹、层级与模具是否相符,同时检查胎胚外观质量; 1.2硫化胶囊微量充压,检查胶囊,并均匀喷刷隔离剂; 1.3启动抓胎器垂直下落,机械手抓起胎胚; 1.4中心机构的卡盘上升达到一定的高度,胶囊抽真空收缩; 1.5抓胎器转入中心机构的上方垂直下落,将胎胚放入模型上; 1.6胎胚下落到设定的高度、胶囊充入设定的一次定型内压; 1.7抓胎器的页片收缩卸下胎胚垂直上升并回转; 1.8启动硫化机的上蒸汽室自动下落到设定的二次定型高度暂停,活络块张开,胶囊内蒸汽压达到二次定型压力; 1.9暂停时间到自动进行合模直至合模完毕; 1.10自动进入胶囊蒸汽达到规定的时间和压力; 1.11自动按规定的时间切换进入一次和二次过热水; 1.12外蒸汽自动进入达到规定的温度和压力; 1.13硫化周期到硫化机自动排放内热水和外蒸汽,胶囊抽真空; 1.14上横梁带动上蒸汽室上升,花纹活络块张开脱离外胎冠部,收缩到上蒸汽室内; 1.15中心机构的上下卡盘同时上升,卸胎器进入,上卡盘上升外胎脱落在卸胎器上; 1.16上下卡盘同时下降,卸胎器上升; 1.17卸胎器返回翻转将胎卸入存胎辊道上。 四. 成品外观质量要求 1.无气泡、脱层: 2.无缺胶、重皮: 3.无子口质量缺陷: 4.无胎里不平: 5.无杂质污染 6.无模缝胶边: 7.无过硫、欠硫: 8.无裂口错模; 9.无变形划伤: 五.硫化工序相关的几个问题 1.全钢硫化为什么要使用活络模? 由上、下侧板、花纹活络块构成活络模是根据子午胎的结构特点和高度均匀性质量要求而发展起来的,全钢子午胎的胎胚形状尺寸接近于成品形状尺寸,由于钢丝帘线的伸长率很小,钢丝带束层把胎体紧紧箍住,周向难以伸张,因此要使用活络模。 使用活络模的优点: (1)胎胚装入模型和胎面压成花纹时,胶料流动小,从而减少了材料的变形。 (2)硫化后带束层角度和宽度变化小,从而提高了产品质量。 (3)子午胎有钢丝带束层,外胎又有花纹,当外胎从两半模脱开时脱落力比斜交胎大得多,这易出花纹块撕裂,胎侧,胎圈变形,而采用活络模就可降低脱模力,避免出现以上所述质量缺陷。 2.为什么要使用硫化定型工艺? 轮胎使用定型硫化机硫化都有一次定型和二次定型两种定型方式。 在装入胎胚未合模之前,分两个阶段往胶囊充入设定的蒸汽压力并保持设定的时间,二次定型还设定高度,从而可使胎胚各部位缓慢均匀的舒张,使胶囊很好的在胎胚胎里滑移舒张,吻贴并排除胶囊与胎里空气。 一次定型的目的: (1)胶囊内充入设定的蒸汽压力负担起胎胚的重量并定位,从而使机械手脱离胎胚胎圈。 (2)胶囊在胎胚胎里均匀对称地膨胀舒展,吻贴胎里并排出胶囊与胎里间空气。 二次定型的目的: (1)胶囊充入比一次定型压力要高的蒸汽压力,使胶囊进一步膨胀舒展和排出胶囊与胎里间空气。 (2)排出胎胚与模型间的空气 二次定型技术上规定了严格的定型高度,定型压力,定型时间 3.为什么要使用胶囊隔离剂和脱模剂? 3.1胶囊隔离剂的作用: (1)有利于胶囊在胎胚里膨胀舒展; (2)有利于排出胶囊与胎里间空气; (3)有利于胶囊从硫化完毕的轮胎胎里脱离出,防止粘囊; (4)有利于延长胶囊的使用寿命。 3.2脱模剂的作用; (1)防止外胎与模具粘连尤其是轮胎的花纹部分,便于硫化出胎和防止外胎损伤; (2)降低胎面胎胚表面胶料在模型内流动,从而获得精确清晰的花纹; 4.为什么要规定胎胚存放时间? 胎胚都规定了一定的存放时间其目的是为了克服易造成成品外观缺陷的因素,保证适量的库存,使硫化生产能够连续进行。 5.硫化过程中的内压起什么作用? 提高胶料的致密性,消除部件间或胶料中的气泡; 促进胶料在模型内的流动,使胶料迅速充满模腔; (3)使胶料与模型内表面紧密贴合,可获得清晰的花纹,图案及光滑的表面; 提高橡胶与骨架材料的密着力和产品的强度及耐屈挠性能; 排出半成品与模型内的空气。 六.常见的质量缺陷、原因分析及解决措施 序号
缺陷名称 产生原因 解决及预防措施
1 胎侧缺胶 ①排气孔堵塞②半成品本身缺胶 ③蒸汽室有水④胶囊上下环泄漏 ⑤二次定型压力太小 ⑥胎胚成型拉破的胎侧修补不平 ⑦胎胚表面有灰尘或油污⑧外喷涂剂不干
①保证排气孔畅通②认真修补缺胶半成品③排净蒸汽室余水④及时更换上下环密封圈⑤二次定型压力按工艺规定执行⑥停用,重新修补后再硫化⑦清除灰尘或油污后硫化⑧待外喷涂剂干后才能装锅。
2 胎里缺胶 ①一次定型压力太大上下环过早封闭,胎里窝气无法排出 ②胶囊隔离剂涂刷过多,遇热后形成气体隔离层 ③二次定型压力过小,胎里空气未排出④内压有波动
①一次定型压力必须适当,但注意不能挤坏胶囊 ②隔离剂涂刷均匀 ③二次定型压力按工艺规定值执行 ④保证内压稳定达到工艺规定值
3 胎圈大边 ①装胎不正 ②定型压力不足 ③胶囊卡盘型号不匹配
①合模前必须保证上环在胎圈的中心无明显偏移 ②二次定型压力按工艺规定值执行 ③调换规格型号相符的胶囊卡盘
4 子口圆角 ①上环泄漏 ②胶囊抽真空不到位,直径大于半成品胎圈③隔离剂流存于下环 ④装胎时胎圈接触模具时间过长,烫伤子口
①及时更换上环密封圈 ②保证胶囊抽真空形状,收缩不少于4瓣③胶囊隔离剂不要流入下卡盘,流入须擦干净 ④按工艺要求装模
5 子口缺胶 ①机械手抓伤②子口处的排气孔堵塞 ③装胎时胎圈接触模具时间过长,烫伤子口
①注意机械手闭合后再上升,一次定型压力不要过大挤住机械手闭合②畅通排气孔 ③按工艺要求装模 6 胶边和压折 ①合模力不足 ②停机时间过长
①调整合模力 ②停机时间过长必须重新预热模具
7 轮胎外部或内部杂物 ①半成品或模具上没有清理干净 ①认真检查半成品胎里或表面 ②清除掉在上模活络块之间残留的胶边③随时注意有无杂物落入下模
8 胎侧气泡 ①半成品没压实或部件中有气泡 ①认真刺扎半成品所有部位的气泡
9 胎侧接头开 ①半成品本身缺陷 ②成型过程胎侧接头未压实
①修补合格后才允许装模
10 子口上抽 ①二次定型压力大或时间长 ②装胎不正 ③胶囊型号不匹配(偏小)
①按工艺规定值执行 ②合模前必须保证上环在胎圈的中心无明显偏移 ③调按规格型号相符的胶囊卡盘
11 胎圈变形 ①抽真空不好 ②开模时活络模未张开 ③开模时轮胎粘连胎圈卡盘
①真空没抽好不准升上环 ②开模时活络模必须张开 ③粘模必须人工撬下后才能继续开模
12 胎冠变形 ①下环升与卸胎支臂时间错误 ①卸胎支臂进必须等下环升到位后方可动作
13 内衬层接头开 ①半成品本身开或成型虚接 ①检查修补半成品及胎胚
14 胶囊破 ①操作人责任心不强或检查不仔细 ①认真检查胶囊损坏程度尤其是接班后第一锅,必须认真彻底检查以做到心中有数
15 装错模 ①责任事故 ①叉车运胎人员应按规格叉送胎胚 ②机台操作人应检查胎胚是否与本机台相符,尤其夜班应注意
16 胎体变形 ①胎胚在机械手上吊胎时间过长 ①胎胚在机械手上吊胎时间不超过5分钟
17 硫化中降压、降温 ①硫化介质达不到工艺要求 ②锅口密封圈损坏
①及时与动力站站联系,采取必要措施,并进行适当延时 ②认真检查密封圈并及时更换
18 胶囊打折 ①用错胶囊 ②胶囊老化严重未及时更换