石油化工讲义节能技术
绿色节能技术在石油化工中的应用

绿色节能技术在石油化工中的应用石油化工是指利用石油、天然气、煤等矿物资源为原料,通过化学反应、物理加工等方法生产化工产品的过程。
作为能源和化工行业的重要组成部分,石油化工产业一直是国民经济发展的支柱产业之一。
随着全球环保意识的不断提升和能源资源的日益枯竭,石油化工企业面临的环保压力和能源消耗问题也变得越来越突出。
绿色节能技术在石油化工中的应用具有重要的意义。
一、绿色节能技术的重要性绿色节能技术是指对环境友好的技术以及能够降低能源消耗、减少污染物排放的技术。
在石油化工生产中,大量的能源消耗和废气排放已经成为环境污染的主要原因之一。
采用绿色节能技术可以有效降低石油化工生产过程中的能源消耗和污染物排放,从而实现可持续发展。
绿色节能技术的应用也可以帮助石油化工企业降低生产成本,提高经济效益,增强企业的可持续竞争力。
绿色节能技术在石油化工中的应用具有重要的意义。
二、绿色节能技术在石油化工中的应用1. 新型催化剂技术在石油化工生产中,催化剂起到了至关重要的作用。
传统的催化剂技术对能源的消耗大,对环境的污染严重。
而采用新型的绿色催化剂技术可以降低反应温度和压力,减少能源消耗,同时降低废气排放,达到节能减排的目的。
采用钝化处理的金属催化剂,能够有效降低催化剂的失活率,延长使用寿命,降低成本。
2. 循环经济技术循环经济是指在资源利用中实现资源的最大化利用和再生利用,减少对自然环境的负荷和污染。
在石油化工生产中,采用循环经济技术可以有效降低原材料的消耗,减少废弃物的排放,降低生产成本。
通过废水处理再利用技术,可以将废水中的有用物质提取出来再次利用,达到能源和物质的循环利用。
3. 绿色能源技术石油化工生产中,使用大量的能源是不可避免的。
而采用绿色能源技术可以减少对传统能源的依赖,降低能源消耗和污染物排放。
采用太阳能、风能等可再生能源替代传统能源,可以有效降低能源成本,减少污染物排放。
4. 低碳技术石油化工生产中,碳排放是无法避免的环境问题。
第五章 炼油化工厂节能技术12 (1)PPT课件
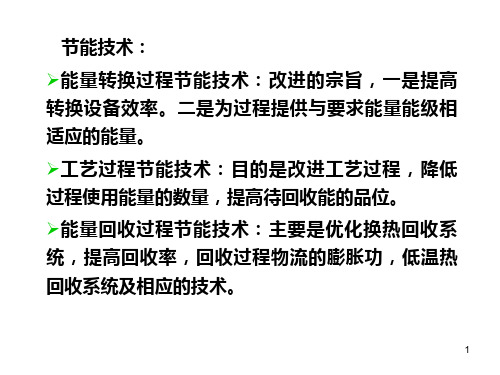
我国岳阳化工厂、兰州化工公司等均有采用。
19
2 、 低 温 朗 肯 循 环 ( LRC—Low temperature
Rankin Cycle)
17
QC+QA=QG+QE
高压
高压 供入热
补充热 低压
解吸器
低压
图5-3 第二类吸收热泵系统
AQHAP温的应度用最,高目,前以QG低和温域QE的的吸温收度制基冷为本多相(同以,溴为化中锂 为温工,质而),Q不C的以温供度热为最目低的。,也常被称为“吸收制冷”。18
吸收式热泵
日本尤尼奇卡公司采用AHP以0.2MPa蒸汽为热源, 将20~25℃低温水升级到70~75℃供热。
1
标题添加
点击此处输入相 关文本内容
前言
点击此处输入 相关文本内容
标题添加
点击此处输入相 关文本内容
点击此处输入 相关文本内容
2
第一节 能量升级利用技术
炼油化工厂中,在装置进行工艺和换热网络优化 后,仍有许多低温热排出系统。这些低温热的回收 利用是石油化工厂深化节能的一个重要方面。
对于炼油厂,空冷、水冷余热大多分布在 90~200℃之间,约占总余热量的55.4%。
过热器
发电
朗肯循环是各种
汽轮机
复杂的蒸汽动力
乏气 循 环 的 基 本 循 环 。
锅炉
冷
凝
它是由锅炉、过
器
热器、汽轮机、
水泵
冷凝器和水泵组
成的。如图
图5-4 朗肯循环图
石油化工中的节能技术

石油化工中的节能技术段占庭教授博士生导师(清华大学)中国老教授协会能源与节能技术咨询中心目录一、精馏技术的节能二、精馏方法的改进与节能三、分离过程的改进与节能四、传质与传热设备的节能一、精馏技术的节能1. 多效蒸馏 多效蒸馏的原理与多效蒸发相同,即将前级塔塔顶蒸气直接作为后级塔塔釜的加热蒸气,这样可以充分利用不同品位的热能。
下图为典型的多效蒸馏流程。
进料分别引入若干塔进行并联操作,各塔操作压力不同,多效蒸馏的关键是选择适宜的各塔操作压力,使高压塔的塔顶蒸气在低压塔的再沸器中冷凝,同时作为低压塔的热源。
只有第一效需要外部加热,末效需要塔顶冷凝。
多效蒸馏受到第一效加热蒸气压力和末效冷却介质温度的限制,常见的是采用双效。
双效蒸馏回收DMF的双效蒸馏普通蒸馏蒸汽用量12100公斤/小时双效蒸馏蒸汽用量5400公斤/小时双效蒸馏可节约大量能量2.热泵精馏间接蒸汽压缩直接蒸汽压缩热泵精馏3. 热耦蒸馏热偶蒸馏用来分离沸点接近的多组元物,可以实现节能。
图为Stupin和Lockhart报道的热偶蒸馏流程分离A、B、C三元混合物。
物料进入第一个顶分馏塔,全部轻组分A和全部重组分C分别由塔底馏出,中间组分B则在塔顶和塔底都有。
将塔顶、塔底产品分别引入第二个分馏塔的合适位置。
这样第二个塔的上部分离A和B,下部分离C,中间产品B则由侧线采出。
由于第一个塔的塔顶冷凝和塔釜加热由两个塔气液直接传热获得,只有第二个塔有冷凝器和再沸器,故减少了能耗,节约了投资。
此概念可以用于分离超过三元的沸点接近物系。
对于N元混合物,采用一般连续蒸馏流程,要用N-1个塔才能把各组分分离,其中每个塔需要一个冷凝器和一个再沸器。
如果采用热偶蒸馏流程,只需要一个冷凝器和一个再沸器。
4.设置中间再沸器,中间冷凝器在普通精馏塔中,热量从温度最高的再沸器加入,从温度最低的塔顶冷凝器移出。
由式可看出,净功消耗大,热力学效率很低。
加热和冷却的费用也随釜温的升高和顶温的降低而升高。
石油化工能量利用及节能

石油化工工业过程节能新技术石油化工行业是能源和材料的生产行业,也是主要的能耗和耗材行业之一,以技术密集和能源消耗集中为特点。
实话行业的能耗在我国行业能耗中排第五位,其取水量占全国工业取水量的5%。
为节省资源、降低成本、保护环境,走可持续发展之路,石化行业在节能方面做出了很大的努力。
从2000年到2005年,中石化集团万元产值综合耗能指标由4.06吨标煤/万元产值降到3.6万元标煤/万元产值;炼油原油综合耗能从76.66千克标油降到68.59千克标油。
但现在石油企业在节能降耗方面仍从在一些不足,与国外存在较大的差距。
石油行业中炼油和乙烯能耗占全国工业总能耗的4%以上,所以炼油和乙烯的节能对全国工业能耗下降具有重要意义。
一、各级炼油装置的节能1. 原油梯级蒸馏节能技术目前原油的常减压蒸馏流程比较成熟,流程的变化很小,存在的主要问题是原油加工过程的能耗高。
其中一个重要原因是蒸馏过程的不可逆加热和冷却造成的。
即:将原油加热到很高的温度进行汽化,然后在不同温度下冷凝获得相关产品。
为解决以上问题,可以将原油加热到接近冷凝的温度下进行汽化,就可以大幅度降低加热和冷却的不可逆性,从而实现节能的目的。
本文的梯级蒸馏节能理论和技术就是在这样的情况下提出的,该技术包含两方面的内容:梯级加热和梯级减压。
一是采用梯级加热技术:采用梯级加热的方法汽化原油,减少不可逆性,及时将汽化后的物料分离出去;二是采用梯级减压技术:由于逐步将轻组分拔出,剩余物料就可以在更低的压力下实现汽化,以降低原料的加热温度。
采用梯级加热技术汽化原油,可以减少不可逆性,及时将汽化后的物料分离出去;同时采用梯级减压技术,逐步将轻组分拔出,通过流程模拟与分析进行合理的匹配与重构,实现压力与温度的耦合,大幅度降低原油加工过程的能耗。
2. 催化裂化吸收稳定系统节能技术目前国内吸收稳定工艺存在干气不干、汽油切割不清晰、稳定塔分离能力不够、稳定汽油烯烃含量高以及能耗高等缺点。
炼油化工厂节能技术
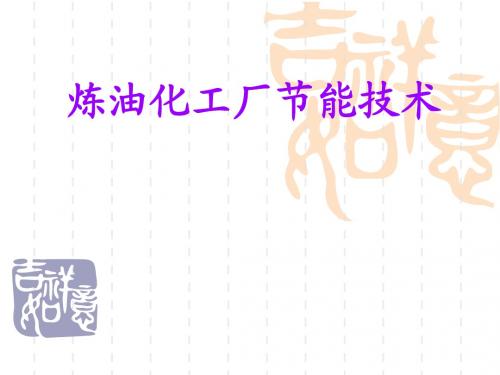
能量升级利用技术
炼油化工厂中,在装置进行工艺和换热网络优化 后,仍有许多低温热排出系统。这些低温热的回收 利用是石油化工厂深化节能的一个重要方面。 对于炼油厂,空冷、水冷余热大多分布在 90~200℃之间,约占总余热量的55.4%。
对于化工厂,空冷、水冷余热大多分布在 60~90℃区间,约占总余热的70%。而这些低温热 量回收利用的好坏对“三环节能量流结构理论”,把整个 系统分为能量转换环节、能量利用环节和能量回收 环节,其中利用环节是核心。工艺总用能是整个过 程系统的核心能量指标
通过优化运行实现炼油厂节能降耗的技术思路:在 四个层面展开:优化工艺装置内部;装置间热联合; 低温热优化利用,优化蒸汽动力系统,火用经济调 优。
三、提高能量回收率,减少排弃能量及火用损
1.减少散热量 2.优化换热系统减少传热 火用损 3.降低冷却排弃能
四、提高能量转换环节效率,减少装置供入能耗
1.停用或合用加热炉 2.提高加热炉效率 3.采用自动调速设施 4.合理选择蒸汽动力的驱动方式 5.催化裂化再生器排烟能量的回收利用
优化运行节能降耗的主要技术
单位:MJ/t原油 (万kcal/t原油)
ηU = 86.91% ;
ηT=9.73% ; ηR =64.5% ;
EN=1178.6MJ/t
图4-5 某炼厂联合装置常减压1980年7月能流图
综上所述,石油化工节能技术改进是有规 律可循的,以用能分析三环节模型为基础的节能 改进方法,反映了这种客观规律及节能改进各用
过程工艺的系统节能思路
工艺装置 装置间热联合 低温热利用 蒸汽动力系统 火用经济学的技术经济分析 实施下一个循环 优化过程完成
2、通过运行优化的节能技术应用
工艺装置内部的运行优化:
炼油节能讲座

直接节能
• 直接节能——通过加强能源的科学管理和 推动技术进步,降低在生产和生活中直接 消耗的能源量。 技术进步是直接节能的主要动力,它主要 是在技术经济全面权衡的基础上,采用先 进合理的节能工艺、技术、设备和材料, 在满足生产要求的条件下,降低单位产品 的能耗。
• 加热炉系统节能
– 提高燃烧温度 – 提高发生蒸汽压力 蒸汽参数达到500℃和15MPa以上时,发电效率可达 40%。但锅炉传热温差仍很大。单纯产热时有效能效 率只有33%,热电联产时有效能效率也只能达到67% – 操作控制优化 控制空气过剩系数、改进喷嘴、加强密封减少散热、 采用高效辐射涂料 – 烟气余热回收 设置热管式空气预热器
1.3 过程单元的节能方向
• 蒸馏过程节能
蒸馏过程的有效能损失: (1)流体流动的压降 (2)不同温度间物流的传热,或不同温度物流 的混合 (3)相浓度不平衡物流间的传质,或不同浓度 物流的混合
1.3 过程单元的节能方向
• 蒸馏节能方法:
– 以热力学第一定律为基础,充分利用过程自身 的热能或冷能,提高蒸馏系统的热效率。如加 强设备保温保冷、强化回收物流的显热或潜热 – 以蒸馏过程原理为基础,减少蒸馏过程本身能 量需求。如减小回流比、采用新型塔板或新型 高效填料以提高分率效率和减小系统压降 – 以热力学第二定律为基础,提高蒸馏系统的效 率。如增设中间再沸器和中间冷凝器、采用多 股进料和侧线进料方式、应用多效蒸馏、热泵 蒸馏以及加预分馏塔等
2.5 5.5 2.0
2.0 2.0 1.5
1.3 过程单元的节能方向
• 热能回收利用系统节能
绿色节能技术在石油化工中的应用

绿色节能技术在石油化工中的应用1. 引言1.1 绿色节能技术的背景绿色节能技术是指在生产和生活中广泛应用的一种节约能源、减少污染的技术系统。
随着环境问题的日益凸显和资源短缺的逐渐加剧,绿色节能技术被越来越多地重视和应用。
石油化工作为能源消耗大、环境污染严重的行业,对绿色节能技术的需求尤为迫切。
绿色节能技术的背景可以追溯至20世纪70年代能源危机以来,各国开始重视节能减排,积极开展节能环保技术研究。
随着科技的不断进步,绿色节能技术也在不断创新和发展。
在石油化工行业,采用绿色节能技术可以有效减少能源消耗,降低生产成本,减少污染排放,提升生产效率和资源利用率,符合可持续发展的要求。
绿色节能技术的背景下,石油化工行业不断探索和应用各种节能技术,努力实现资源的有效利用和环境的保护。
通过引入绿色节能技术,石油化工行业可以实现可持续发展,同时也为未来的发展提供了良好的基础和保障。
【2000字】1.2 石油化工行业的能源消耗问题石油化工行业作为能源消耗大户,其生产过程中对能源的需求量巨大。
石油化工生产包括原油提炼、石油加工、化工制品生产等多个环节,这些环节都需要大量的热力和电力支持。
根据统计数据显示,石油化工行业的能源消耗占全国总能源消耗的比例达到了25%以上,成为我国最大的能源消费行业之一。
由于石化行业的过程复杂,能源利用率较低,产生了大量的能源浪费和环境污染。
炼油过程中炼油炉的热效率较低,化工产品的合成过程中也存在能量损耗等问题。
传统的石化生产模式也对环境带来了巨大的压力,排放的废气、废水、废渣等造成了环境污染和资源浪费。
如何解决石油化工行业的能源消耗问题成为当前亟待解决的难题。
绿色节能技术的应用可以有效地提升石油化工生产的能源利用率,减少能源浪费和减少环境污染。
通过引入绿色节能技术,石化行业可以实现“节能减排”目标,推动产业转型升级,实现可持续发展。
1.3 绿色节能技术在石油化工中的重要性石油化工行业是一个能源密集型行业,其生产过程中消耗大量能源,同时也产生大量的污染物和二氧化碳排放。
石油化工行业节能原理和节能技术讲义

石油化工行业节能原理和节能技术讲义目录目录 (1)前言 (2)第一节节能的基本原理 (100)第二节典型例题分析 (222)第三节节能的基本概念 (32)第四节企业节能的原则和基本途径 (43)第五节企业通用节能技术 (50)第六节石化行业节能技术 (855)前言节能是指在满足相等需要或达到相同目的的条件下,通过加强用能管理,采取技术上可行,经济上合理以及环境和社会可以接受的措施,减少从能源生产到消费各个环节中的损失和浪费,提高能源利用的经济效果。
一、我国的能源发展和供求问题1、能源供应压力大“十五”期间,由于能源需求增长迅速,我国能源市场由“九五”时期的供需基本均衡转向供不应求。
按可比价格计算,这期间我国GDP年均增长率高达9.7%,而相应的能源消费量年均仅增长4.6%,远低于同期经济增长速度,其中1997至1999三年能耗为负增长。
然而,进入21世纪以来,尤其是从2002年开始,我国能源消费增长迅猛,超过了经济发展速度。
我国2005年一次能源生产总量20.6亿吨标准煤。
其中发电量24747亿千瓦小时,比2004年增长12.3%;原煤21.9亿吨,增长9.9%;原油1.81亿吨,增长2.8%。
2005年能源消费总量22.2亿吨标准煤,比2004年增长9.5%。
其中,煤炭消费量21.4亿吨,增长10.6%;原油3.0亿吨,增长2.1%;天然气500亿立方米,增长20.6%;水电4010亿千瓦小时,增长13.4%;核电523亿千瓦小时,增长3.7%。
“十五”期间我国能源消费总量从2001年的13.49亿吨标准煤增长到2005年的22.2亿吨标准煤。
如今我国能源消费总量已经位居世界第二,约占世界能源消费总量的11%。
图1 “十五”期间我国一次能源生产总量和能源消费总量对比表1 “十五”期间我国一次能源生产总量和能源消费总量对比年份一次能源生产总量(亿吨标准煤)能源消费总量(亿吨标准煤)2001 12.1 13.52002 13.8 14.82003 16.0 17.12004 18.5 19.72005 20.6 22.2但我国人均能源消费量较低。