(3)中心复合设计表分析
中心复合试验设计概述

中心复合试验中的立方点、轴向点和中心点
中心复合试验设计由立方点、轴向点和中心点试验三 部分组成,下面以2因子中心复合试验设计为例分别对 三种点加以说明。 立方点 立方点即全因子设计或分部试验设计中的2水平对应的 “-1”和“+1”点,表示如下图:
确定试验因素水平表 水平 A:射出压力 B:保持压力 C:射出时间 1200 700 1.2 + 1400 800 fFactory Pro" 试用版本创建
试验方案确定
改善小组确信三个因素的交互作用对输出有重要影 响,并怀疑非线性影响也是重要影响。因为全因子设 计可测试因素间的相互作用,中心复合设计可以测试 因素的非线性影响,小组决定选择中心复合设计进行 试验。 改善上组确信三个因素的交互作用对输出有重要影 响,并怀疑非线性影响也是重要影响。因为全因子设 计可测试因素间的相互作用,中心复合设计可以测试 因素的非线性影响,小组决定选择中心复合设计进行 试验。
(0,0)
PDF 文件使用 "pdfFactory Pro" 试用版本创建
中心复合设计例
中心复合设计常用于在确信怀疑试验因素对试验指 标存在非线性影响时对因素与指标间的关系进行试验 分析,本节将以3因素中心复合设计为例来讲述中心复 合设计的流程及策略。 某公司生产塑胶零件,长期以来该公司生产的一种 主要产品,销往国外一跨国公司的激光头用滑动底架 的某个关键尺寸难于有效控制,该公司决定成立改善 小组对此进行研究改善。经认真调查分析,小组认为 此尺寸偏差过大的原因是由于零件变形引起,于是小 组将目光聚焦在零件注塑成型工序,经过前期分析和 经验判断,小组确定注塑时引起零件变形的关键因素 为射出压力、保持压力和射出时间。小组决定通过试 验设计来确定以上因素与零件尺寸之间的关系以进行 改善。
探索DOE优化的奥秘
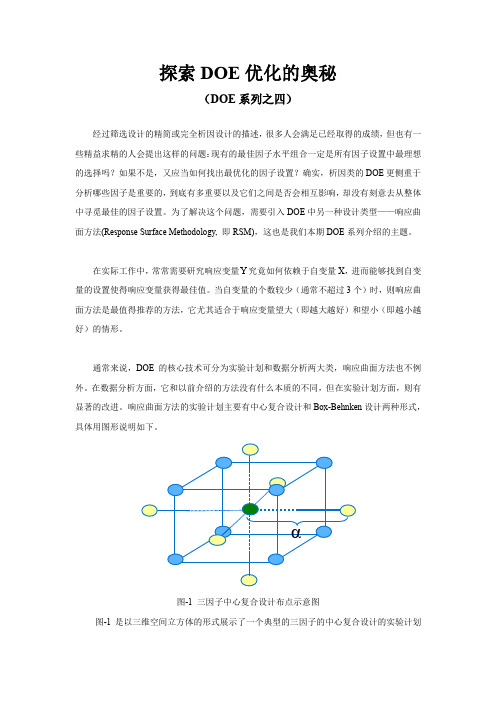
探索DOE优化的奥秘(DOE系列之四)经过筛选设计的精简或完全析因设计的描述,很多人会满足已经取得的成绩,但也有一些精益求精的人会提出这样的问题:现有的最佳因子水平组合一定是所有因子设置中最理想的选择吗?如果不是,又应当如何找出最优化的因子设置?确实,析因类的DOE更侧重于分析哪些因子是重要的,到底有多重要以及它们之间是否会相互影响,却没有刻意去从整体中寻觅最佳的因子设置。
为了解决这个问题,需要引入DOE中另一种设计类型——响应曲面方法(Response Surface Methodology, 即RSM),这也是我们本期DOE系列介绍的主题。
在实际工作中,常常需要研究响应变量Y究竟如何依赖于自变量X,进而能够找到自变量的设置使得响应变量获得最佳值。
当自变量的个数较少(通常不超过3个)时,则响应曲面方法是最值得推荐的方法,它尤其适合于响应变量望大(即越大越好)和望小(即越小越好)的情形。
通常来说,DOE的核心技术可分为实验计划和数据分析两大类,响应曲面方法也不例外。
在数据分析方面,它和以前介绍的方法没有什么本质的不同,但在实验计划方面,则有显著的改进。
响应曲面方法的实验计划主要有中心复合设计和Box-Behnken设计两种形式,具体用图形说明如下。
图-1 三因子中心复合设计布点示意图图-1是以三维空间立方体的形式展示了一个典型的三因子的中心复合设计的实验计划示意图,在以下的叙述中给出的坐标都已将各因子代码化。
整个实验由下面三部分实验点构成。
1.立方体点(Cube Point),用蓝色点表示。
各点坐标皆为1或-1,这是与完全析因设计相同的部分。
2.中心点(Center Point),用绿色点表示。
各点的三维坐标皆为0。
3.轴点(Axial Point),用黄色点表示。
除了一维自变量坐标为±α(旋转性指数)外,其余维度的自变量坐标皆为0。
在三因子情况下,共有6个轴点。
当取k4=2α(k为因子个数)时,该类中心复合设计兼具旋转性和序贯性的优点,是最典型的α值设定情形。
中心复合设计原理

中心复合设计原理
中心复合设计原理(Composite Design Pattern)是一种结构型
设计模式,它允许客户端统一处理单个对象和对象组合。
该模式以一种递归的方式组织对象,使得客户端可以像处理单个对象一样处理对象组合。
这个模式常被用于树状结构的场景。
中心复合设计原理包含以下几个关键角色:
1. 组件(Component):定义对象的一些基本操作,它可以是
接口或抽象类。
这个角色通常包含了对子组件(组合的对象)的操作方法,比如添加、删除、获取子组件等。
2. 叶子组件(Leaf Component):是组合中的具体单个对象,
不能再包含其他对象,实现组件接口。
3. 容器组件(Composite Component):是组合中的具体对象
容器,能够包含其他对象,实现组件接口。
容器组件通常会调用其子组件的操作方法,并进行一些额外的操作。
使用中心复合设计原理的主要优点包括:
1. 客户端统一处理单个对象和对象组合,简化了客户端的代码。
2. 可以递归地组织对象,提供管理复杂对象结构的能力。
3. 可以方便地新增新的组件类型,符合开闭原则。
然而,中心复合设计原理也有一些缺点:
1. 在处理具体组合和单个对象时,需要额外的类型判断,可能会导致代码的复杂性增加。
2. 可能会降低系统的性能,因为递归遍历对象组合可能需要较长的时间。
minitab实验之试验设计(2)解读
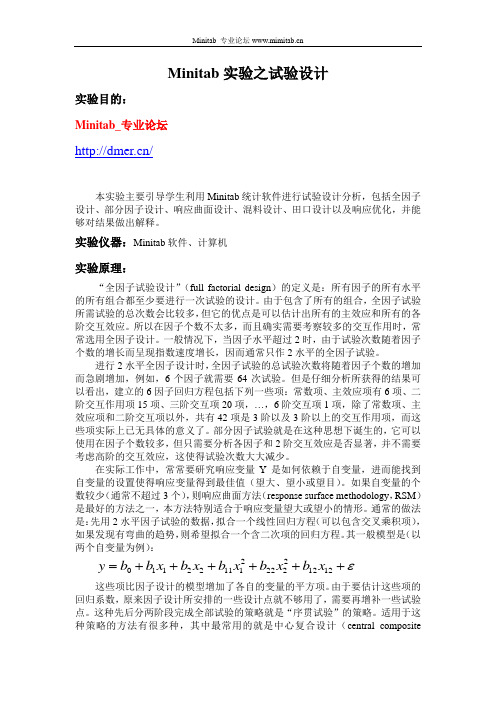
分析要点三:分析评估各项效应的显著性。计算结果显示,4个主效应中,加热温度、加热时间和保温时间是显著的,只有转换时间不显著;6个2因子水平交互效应中,只有加热时间*保温时间是显著的。说明本例中还有不显著的自变量和2因子交互作用,改进模型时应该将这些主效应和交互作用删除。
加热温度*保温时间3.062 1.531 1.500 1.02 0.337
加热时间*转换时间1.263 0.631 1.500 0.42 0.685
加热时间*保温时间7.113 3.556 1.500 2.37 0.045
转换时间*保温时间0.837 0.419 1.500 0.28 0.787
S = 6.00146 PRESS = 1778.45
稳健参数设计(robust parameter design)(也称健壮设计、鲁棒设计,简称参数设计)是工程实际问题中很有价值的统计方法。它通过选择可控因子的水平组合来减少一个系统对噪声变化的敏感性,从而达到减小此系统性能波动的目的。过程的输入变量有两类:可控因子和参数因子。可控因子是指一旦选定就保持不变的变量,它包括产品或生产过程设计中的设计参数,而噪声因子是在正常条件下难以控制的变量。在做参数设计时,就是把可控因子的设计当做研究的主要对象,与此同时让噪声因子按照设定的计划从而系统改变其水平的方法来表示正常条件下的变化,最终按照我们预定的望大、望小或望目地目标选出最佳设置。田口玄一博士在参数设计方法方面贡献非常突出,他在设计中引进信噪比的概念,并以此作为评价参数组合优劣的一种测度,因此很多文献和软件都把稳健参数设计方法称为田口方法(Taguchi design)。
中心复合序贯设计
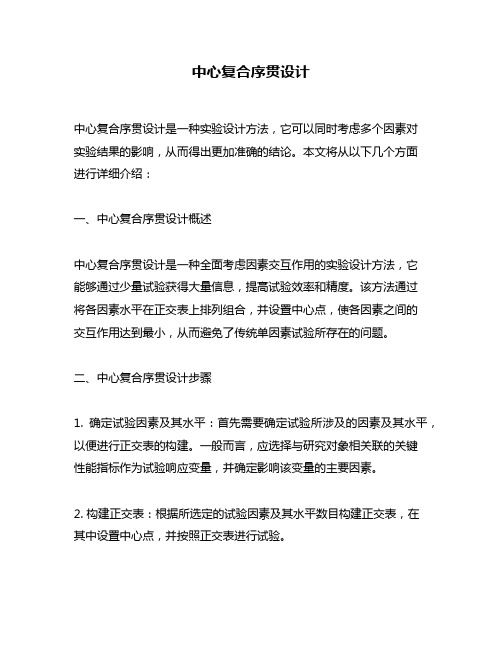
中心复合序贯设计中心复合序贯设计是一种实验设计方法,它可以同时考虑多个因素对实验结果的影响,从而得出更加准确的结论。
本文将从以下几个方面进行详细介绍:一、中心复合序贯设计概述中心复合序贯设计是一种全面考虑因素交互作用的实验设计方法,它能够通过少量试验获得大量信息,提高试验效率和精度。
该方法通过将各因素水平在正交表上排列组合,并设置中心点,使各因素之间的交互作用达到最小,从而避免了传统单因素试验所存在的问题。
二、中心复合序贯设计步骤1. 确定试验因素及其水平:首先需要确定试验所涉及的因素及其水平,以便进行正交表的构建。
一般而言,应选择与研究对象相关联的关键性能指标作为试验响应变量,并确定影响该变量的主要因素。
2. 构建正交表:根据所选定的试验因素及其水平数目构建正交表,在其中设置中心点,并按照正交表进行试验。
3. 进行试验:按照正交表进行试验,并记录各组实验数据。
4. 进行统计分析:根据所得到的实验数据进行统计分析,包括方差分析、回归分析等。
5. 优化设计参数:通过对实验结果的分析,确定最佳组合,并进行优化设计参数。
三、中心复合序贯设计的优点1. 节省试验成本:中心复合序贯设计可以通过少量试验获得大量信息,从而节省试验成本。
2. 提高试验效率和精度:中心复合序贯设计能够全面考虑因素交互作用,从而提高试验效率和精度。
3. 可以同时考虑多个因素对实验结果的影响:传统单因素试验只能考虑一个因素对实验结果的影响,而中心复合序贯设计可以同时考虑多个因素对实验结果的影响。
4. 适用性广泛:中心复合序贯设计适用于各种领域的研究,如材料科学、生物医学、环境科学等。
四、中心复合序贯设计应用案例以某食品企业为例,该企业需要研发一种新型饮料,并确定其最佳配方。
该饮料需要满足以下要求:口感好、色泽艳丽、价格适中。
为了确定最佳配方,该企业采用中心复合序贯设计方法进行试验,试验因素包括三种原料的比例、加热温度、搅拌时间等因素。
在响应曲面方法中三类中心复合设计的比较研究
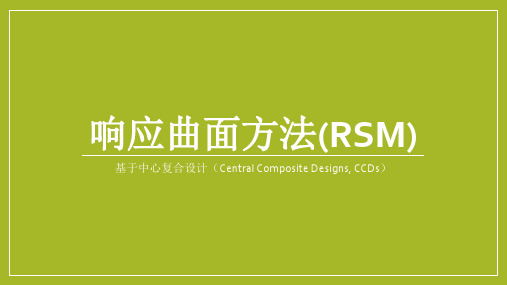
•
从设计域及其复杂性上比较
• •
考虑设计的复杂性: 在应用CCC时,延伸所定义的变量界限得到轴向点,这就需要操作过程中的每个 变量具有五个水平(对于CCI同样)。相反,对于CCF,仅需要每个变量的三个水平, 使之成为一个更简单的设计.实验者应该充分重视由于设计水平的增加而增加 的复杂性,即使一个重新装配过程的成本不高且不费时间,但这会引起更多的实 误差变异来源。根据经验,在应用实验设计时,最常见的失效原因是由于无法预 期的较大的实验误差所引起的,因此选择误差来源少的设计是有道理的,因为在 多数情况下,可旋转性设计的优势不能够补偿所增加的复杂性和相关的风险.
•
k
k
此模型包含1+ 2k+ k(k -1) /2个参数,因此必须至少有1+ 2k+ k(k -1) /2个不同的设 计点,而且至少每个设计变量是三个水平的.
主要的概念
• •
操作域(Operability Region):在安全性允许的条件下,加工设备和生产过程的加工 操作范围所定义的研究变量的上下界限的几何区域。 设计域(Region of Interest):由设计变量的各个水平集合的上下界限所定义的几 何区域,在此区域内,真实的函数关系能够由一个多项式模型很好地近似,每个试 验各自的设计域或相同或不同,但都在操作域之内。
•
案例分析
• • •
从设计点的预测误差来看,CCC、CCI的轴向点和析因点性能相似;CCF轴向点要 显著地好于析因设计点,这说明球形设计的一致精度比立方域要好。 对于被CCI排除但仍然在CCF的操作域之内的各个顶点而言,意味着预测误差增 加了27%(36. 1575435 /28. 3826518 -1)。 从中心点的预测方差来看,CCF具有最高的精度,误差小,这说明CCF设计对中心 点的数目是稳健的.
三类中心复合设计的比较

第三类中心复合设计
设计特点
在中心点、轴向上以及轴向之间的中点上增加试 验点,形成更密集的试验网络。
优点
能够更精确地估计各种线性和非线性效应,提供 更详细的响应面信息。
缺点
试验次数最多,成本最高,但可获得最全面的响 应面信息。
03 三类中心复合设Байду номын сангаас的比较
设计原理比较
01
第一类中心复合设计(CCC)
感谢您的观看
3
促进中心复合设计在各个领域的应用和发展
汇报范围
01 介绍三类中心复合设计的基本概念、原理 和特点
02 比较三类中心复合设计的优缺点和适用范 围
03
分析三类中心复合设计在实际应用中的案 例和效果
04
探讨三类中心复合设计的未来发展趋势和 前景
02 三类中心复合设计概述
第一类中心复合设计
设计特点
在中心点处增加重复试验, 以提高估计精度和检测弯曲 效应。
最优条件确定
通过响应面图形或数值优化方法,确定使得响应变量达到 最优值的因子水平组合。这些最优条件可以为实际生产过 程提供指导。
模型验证
通过额外的实验数据对模型进行验证,评估模型的预测能 力和可靠性。如果模型验证结果良好,则可以将其应用于 实际问题的预测和优化。
05 三类中心复合设计在工业 界的应用案例
案例二:制药工艺改进
药物合成优化
三类中心复合设计可用于优化药 物合成路线中的反应条件、催化 剂选择等关键因素,提高药物合 成的效率和纯度。
制剂工艺改进
通过三类中心复合设计研究药物 制剂中的配方、工艺参数等因素 对药物性能的影响,可以改进制 剂工艺,提高药物的稳定性和生 物利用度。
生产工艺优化
Mintab-DOE操作说明(中心复合设计)
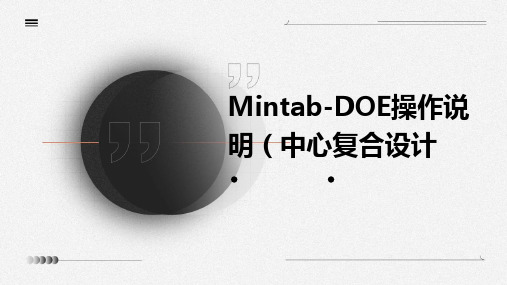
05
结论与展望
中心复合设计在DOE中的优势与局限性
要点一
高效
要点二
全面
中心复合设计能够快速有效地找到关键因素及其交互作用 ,减少实验次数。
能够考虑多个因素及其交互作用,提供更全面的实验设计 。
中心复合设计在DOE中的优势与局限性
• 精确:能够估计因素之间的交互作用,提 高实验的精确度。
因子选择
根据实验目的选择关键因子,并确定其水平范围和变化类型 。
确定实验设计类型与规格
设计类型
根据实验目的和因子数量选择适合的中心复合设计类型,如中心复合面设计、中心复合轴设计等。
设计规格
确定实验设计的具体规格,包括重复实验次数、因子水平数目等。
生成中心复合设计表
设计软件
使用专业的实验设计软件(如Mintab) 生成中心复合设计表。
响应曲面法
响应曲面法是一种通过构建数学模型来描述实验因素与响应变量之间关系的统计方 法。
通过中心复合设计,可以获得多个实验点,并利用这些数据拟合出响应曲面模型。
响应曲面法可以用于预测不同实验因素水平下的响应变量值,并确定最优的实验条 件。
多元线性回归分析
1
多元线性回归分析是一种统计方法,用于研究多 个自变量与因变量之间的线性关系。
感谢观看
THANKS
中心复合设计的概念与应用
概念
中心复合设计是一种实验设计方法,它允许研究者同时研究多个因素及其交互作 用,以确定最佳的参数组合。
应用
中心复合设计广泛应用于各种领域,如化学、生物、工程和制药等,用于优化产 品或过程,提高性能和效率。
02
中心复合设计的基本步骤
- 1、下载文档前请自行甄别文档内容的完整性,平台不提供额外的编辑、内容补充、找答案等附加服务。
- 2、"仅部分预览"的文档,不可在线预览部分如存在完整性等问题,可反馈申请退款(可完整预览的文档不适用该条件!)。
- 3、如文档侵犯您的权益,请联系客服反馈,我们会尽快为您处理(人工客服工作时间:9:00-18:30)。
255
254
253
Y 252
251
2
250
1
0C
-2
-1
-1
B
0
1
-2 2
Hold values: A: 0.0000000000002
第三步: 在
所示:
第四步: 在出现的
第五步: 点击“
选“Target”因为我们希 望输出变量的值在设计中
Surface Plot of Y
Surface Plot of Y
254
253
252
251
Y 250
249
248
2
247
1
0C
-2
-1
-1
A
0
1
-2
2
Hold values: B: 0.0000000000002
从(A、 C从、(YB)、 C(、AY、)B 、中Y,)A因图 素表被 面固图定形 近c:似 参为数平优 化,用优
Linear Square Residual Lack-ofPure Total
分析上表 可知:因
A、B、C均为 显著影响因素 A2项为显著影 响因素
线性项和二 次项为显著 影响因素
显著非线 性影响,
3a::取进得行的 数据如下
b:用 M(a)I:N在ITA MINITA
StdOrder 1 2 3 4 5 6 7 8 9 10 11 12 13 14 15 16 17 18 19 20
C -1 -1 -1 -1 1 1 1 1 0 0 0 0 -1.68179 1.68179 0 0 0 0 0 0
Y 250.98 252.58 252.01 254.46 249.13 251.63 250.51 253.29 249.5 252.71 251.51 253.81 253.64 251.28 252.1 252.74
-2
-1
-1
A
0
1
-2
2
255
254
25249
2
248
1
0B
-2
-1
-1
A
0
1
-2
2
Hold v alues : C: 0.0000000000002
从图中可 以看出, 因素A、 B对Y的 是非线性 的,因为 表面图发 生弯曲。
第五步: 同理可作 出(A、 C、Y) 和(B、 C、Y) 之间的表 面图如 下:
Stat>Fact
orial>Res
RunOrder 1 2 3 4 5 6 7 8 9 10 11 12 13 14 15 16 17 18 19 20
Blocks 1.0 1.0 1.0 1.0 1.0 1.0 1.0 1.0 1.0 1.0 1.0 1.0 1.0 1.0 1.0 1.0 1.0 1.0 1.0 1.0
第1520次试 验,以测 试因素及 其交互作 用对输出 的影响并 判定有无 非线性影 响。再进
行第914部分试 验即对轴 向点进行 试验,以 最终确定 因素与输 出间的关 系模型。
先进行 第1-8次 和15-20 次试验: a:确定各 点代码与 实际水平 设置的对 应关系, 这是试验 的前提条 件,确定 如下表:
存在2 次影响 (非先线 性影响) 。 2:将各 试验因素 设置在如 下水平时 零件尺寸 最优:
3:尺寸 优化值为 252。
因素 射出压力 保持压力 射出时间
最优设置 水平
1092
834
1.26
C -1 -1 -1 -1 1 1 1 1 0 0 0 0 -1.68179 1.68179 0 0 0 0 0 0
Y 250.98 252.58 252.01 254.46 249.13 251.63 250.51 253.29 249.5 252.71 251.51 253.81 253.64 251.28 252.1 252.74
二:试验 实施及分 析: 1:改善 小组按 MINITA B生成的 试验方案 进行试 验,首先 对生成的 试验表进 行分析:
从表中可 以看出: a:第1-8次 试验为3 因素全因 子试验部 分,此部 分试验表 的结构与 3因素全 因子试验 完全相同 。
3因素全因子试 验部分的实验表
轴向点试验部分 的实验表
A -1.000 1.000 -1.000 1.000 -1.000 1.000 -1.000 1.000 -1.682 1.682 0.000 0.000 0.000 0.000 0.000 0.000 0.000 0.000 0.000 0.000
B -1 -1 1 1 -1 -1 1 1 0 0 -1.68179 1.68179 0 0 0 0 0 0 0 0
在
Stat>Fact
orial>Res
A -1.000 1.000 -1.000 1.000 -1.000 1.000 -1.000 1.000 -1.682 1.682 0.000 0.000 0.000 0.000 0.000 0.000 0.000 0.000 0.000 0.000
B -1 -1 1 1 -1 -1 1 1 0 0 -1.68179 1.68179 0 0 0 0 0 0 0 0
(b):在出 现的对话 框选如下 图信息,
(c):选“ Terms”按 钮,输入 下图所示 内容:
(d): MINITA B分析结 果输出如 下:
Response Estimated Term Constant A B C A*A A*B A*C B*C S = 0.3522 Analysis Source Regression
SRES1 -0.73831 -0.56231 -1.2326 0.46092 -1.41819 0.27533 -0.39496 -0.21896 1.64011 -0.39866 0.90914 0.33231 0.70675
0.5347 -1.38162 0.76318 -1.71675 0.52859 0.19347 1.46694
Blocks 1.0 1.0 1.0 1.0 1.0 1.0 1.0 1.0 1.0 1.0 1.0 1.0 1.0 1.0 1.0 1.0 1.0 1.0 1.0 1.0
(h):用表
面图对试
验结果进
行分析,
表面图是
将根据回
归方程确
定Y与其
影响因素
中的两个
之间
的关系
用图形表
示出来的
方法,生
成流程如
下第: 一步:
第二步: 在出现的 对话框选 择下图所 示信息:
第三步: 点“
上图中的 选项表示 在表面图 中Z轴为 输出变量 Y,X轴 为因素 A,Y轴 表示因素 B。
第四步:
表面图 (A、B 、Y)输 出结果如 下:
Surface Plot of Y
255
254
253
252
Y 251
250
249
2
248
1
0B
第六步: 点所击 有“因素 的初始值
本例适用的类别,因为我们 希望零件尺寸为设计中心
MINITA B输出的 R数es据po输nse
Optimizati Parameters
Y Global A B C Predicted Y Composite
图形分析 结果:
Y的最优预测值
各因素最优组合 Y的最优预测值
252 252.67 252.57 252.95
FITS1 251.119 252.686 252.241 254.373 249.396 251.578 250.584 253.331 249.164 252.792 251.324 253.742 253.495 251.17 252.512 252.512 252.512 252.512 252.512 252.512
试验点
立方点
中心点
轴向点
b:首次试 验的数据 如下表:
因素 A B C A B C A B C
代码 -1 -1 -1 0 0 0 -1.682 -1.682 -1.682
实际设置 1200 700 1.2 1300 750 1.4 1132 666 1.1
代码 +1 +1 +1
实际设置 1400 800 1.6
(f): 建立
A、B、C及A2 为显著影响项
线性影响及2次项影 响为显著影响项
根据以
Y=方程
Y=
中:
塑胶零A件=
射出压B力=
保持压A力=
(g):MINI 射出时间
TAB工作
残差
StdOrder 1 2 3 4 5 6 7 8 9 10 11 12 13 14 15 16 17 18 19 20
RunOrder 1 2 3 4 5 6 7 8 9 10 11 12 13 14 15 16 17 18 19 20
+1.682 +1.682 +1.682
1268 834 1.7
尚未试验, 数据为空
c:用 MINITA B对试验 数据进行 分析 (a):在 MINITA B下拉式 菜单选:
Stat>Fact orial>Res ponse Surface> Analysis Response Surfacel Design 如下图
Y的目标达成率:100%
Y的目标达成率:100%
1091.6 34.09 834.09 0.1418 1.2582
Y的最优预测值对 应的各因素组合
三:试验 结论: