高温分离提纯铅过程讲解
炼铅工艺技术
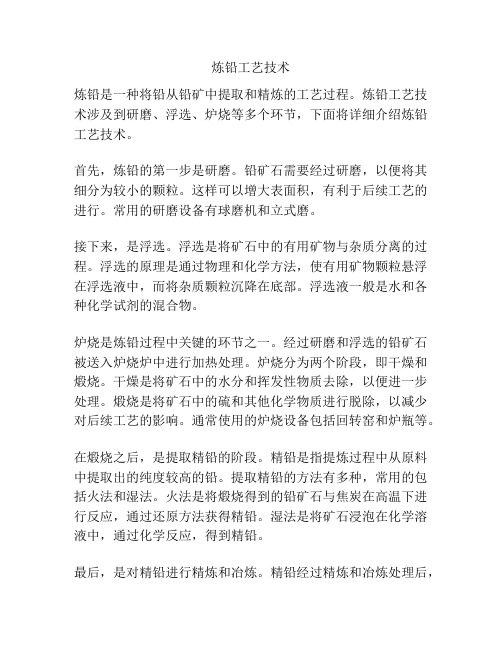
炼铅工艺技术炼铅是一种将铅从铅矿中提取和精炼的工艺过程。
炼铅工艺技术涉及到研磨、浮选、炉烧等多个环节,下面将详细介绍炼铅工艺技术。
首先,炼铅的第一步是研磨。
铅矿石需要经过研磨,以便将其细分为较小的颗粒。
这样可以增大表面积,有利于后续工艺的进行。
常用的研磨设备有球磨机和立式磨。
接下来,是浮选。
浮选是将矿石中的有用矿物与杂质分离的过程。
浮选的原理是通过物理和化学方法,使有用矿物颗粒悬浮在浮选液中,而将杂质颗粒沉降在底部。
浮选液一般是水和各种化学试剂的混合物。
炉烧是炼铅过程中关键的环节之一。
经过研磨和浮选的铅矿石被送入炉烧炉中进行加热处理。
炉烧分为两个阶段,即干燥和煅烧。
干燥是将矿石中的水分和挥发性物质去除,以便进一步处理。
煅烧是将矿石中的硫和其他化学物质进行脱除,以减少对后续工艺的影响。
通常使用的炉烧设备包括回转窑和炉瓶等。
在煅烧之后,是提取精铅的阶段。
精铅是指提炼过程中从原料中提取出的纯度较高的铅。
提取精铅的方法有多种,常用的包括火法和湿法。
火法是将煅烧得到的铅矿石与焦炭在高温下进行反应,通过还原方法获得精铅。
湿法是将矿石浸泡在化学溶液中,通过化学反应,得到精铅。
最后,是对精铅进行精炼和冶炼。
精铅经过精炼和冶炼处理后,可以得到高纯度的铅。
精炼是将精铅与其他杂质进行分离的过程,常用的方法是电解和蒸馏。
电解是将精铅溶解在电解液中,通过电流作用将杂质从铅中分离出来。
蒸馏是将精铅加热蒸馏,使不同沸点的杂质得到分离。
炼铅工艺技术的发展使得铅的提取和精炼变得更加高效和环保。
炼铅过程中严格控制各个环节的操作参数,可以有效降低能耗和减少污染物排放。
同时,炼铅技术还可以通过回收和再利用铅资源,减少矿石开采的需要,达到可持续发展的目标。
总之,炼铅工艺技术涉及到研磨、浮选、炉烧、提取精铅和精炼冶炼等多个环节。
通过优化每个环节的操作和技术手段,可以实现高效、环保的铅炼制过程,为社会经济发展做出贡献。
火法炼铅工艺

火法炼铅工艺火法炼铅工艺是一种常用的金属冶炼工艺,主要用于铅矿石的冶炼。
本文将介绍火法炼铅的工艺流程、设备及对环境的影响。
一、工艺流程:火法炼铅工艺的主要步骤包括碎矿、浮选、烧结、还原、脱硫、炼出等环节。
1. 碎矿:将铅矿石经过破碎和磨矿处理,使其颗粒度适宜进一步处理。
2. 浮选:利用浮选法选别矿石中的杂质,以提高铅的品位。
经过浮选处理,矿石中的硫化铅和杂质被分离,得到精矿。
3. 烧结:将浮选得到的铅精矿与焦炭混合,添加适量的草木灰等助熔剂,经过烧结的高温煅烧处理,使精矿颗粒熔结成为烧结块。
4. 还原:将烧结块放入高温还原炉中,加入石灰和焦炭作为还原剂,将精矿中的氧化铅还原为金属铅。
在还原的过程中,金属铅被蒸发出来,通过冷凝收集。
5. 脱硫:通过向还原炉中加入适量的空气氧化剂,将还原反应中形成的二氧化硫气体进行氧化反应,以除去气体中的硫化物。
6. 炼出:将经过还原和脱硫处理的金属铅熔融炼制,去除其中的杂质和不溶性物质。
经过过滤、离心、冷却等处理,获得纯净的铅液。
二、设备:火法炼铅工艺需要使用的主要设备有碎矿机、浮选机、烧结机、还原炉等。
其中,还原炉是整个工艺中最重要的设备,需要具备高温煅烧和还原铅精矿的能力。
三、环境影响:火法炼铅工艺对环境产生的影响主要有以下几个方面:1. 废气排放:火法炼铅过程中产生大量的废气,主要包括二氧化硫气体。
这些废气中的二氧化硫是一种有害气体,对环境和人体健康都有较大的危害。
2. 废水排放:在火法炼铅过程中,会产生大量的废水,其中含有金属离子和酸性物质。
这些废水需要经过处理后才能排放,否则会对水源和周围的土壤产生污染。
3. 固体废弃物处理:火法炼铅过程中产生的固体废弃物包括矿渣、烟尘等。
这些固体废弃物需要进行妥善处理,以防止对土地和水源造成污染。
为了减少火法炼铅工艺对环境的影响,需要采取相应的环保措施,如加装废气处理设备、建立废水处理系统、合理处置固体废弃物等。
同时,还需要加强监管和管理,确保生产过程中的废物排放符合环境保护要求。
电解铅生产过程
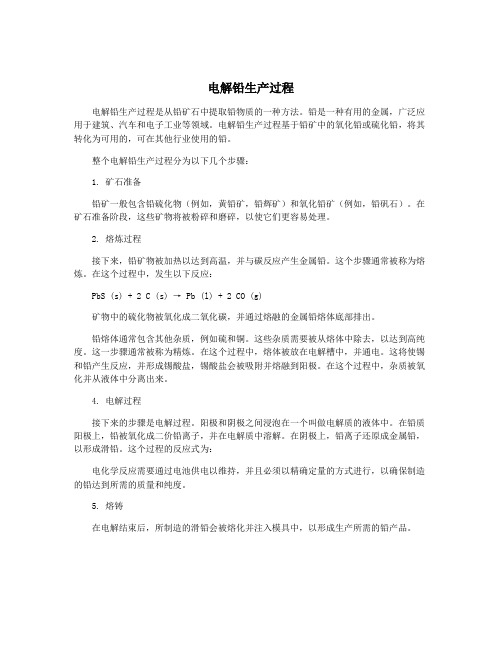
电解铅生产过程电解铅生产过程是从铅矿石中提取铅物质的一种方法。
铅是一种有用的金属,广泛应用于建筑、汽车和电子工业等领域。
电解铅生产过程基于铅矿中的氧化铅或硫化铅,将其转化为可用的,可在其他行业使用的铅。
整个电解铅生产过程分为以下几个步骤:1. 矿石准备铅矿一般包含铅硫化物(例如,黄铅矿,铅辉矿)和氧化铅矿(例如,铅矾石)。
在矿石准备阶段,这些矿物将被粉碎和磨碎,以使它们更容易处理。
2. 熔炼过程接下来,铅矿物被加热以达到高温,并与碳反应产生金属铅。
这个步骤通常被称为熔炼。
在这个过程中,发生以下反应:PbS (s) + 2 C (s) → Pb (l) + 2 CO (g)矿物中的硫化物被氧化成二氧化碳,并通过熔融的金属铅熔体底部排出。
铅熔体通常包含其他杂质,例如硫和铜。
这些杂质需要被从熔体中除去,以达到高纯度。
这一步骤通常被称为精炼。
在这个过程中,熔体被放在电解槽中,并通电。
这将使锡和铅产生反应,并形成锡酸盐,锡酸盐会被吸附并熔融到阳极。
在这个过程中,杂质被氧化并从液体中分离出来。
4. 电解过程接下来的步骤是电解过程。
阳极和阴极之间浸泡在一个叫做电解质的液体中。
在铅质阳极上,铅被氧化成二价铅离子,并在电解质中溶解。
在阴极上,铅离子还原成金属铅,以形成滑铅。
这个过程的反应式为:电化学反应需要通过电池供电以维持,并且必须以精确定量的方式进行,以确保制造的铅达到所需的质量和纯度。
5. 熔铸在电解结束后,所制造的滑铅会被熔化并注入模具中,以形成生产所需的铅产品。
粗铅火法精炼的工艺流程

粗铅火法精炼的工艺流程以粗铅火法精炼的工艺流程为标题,写一篇文章。
粗铅火法精炼是一种常见的铅冶炼工艺,用于提取和精炼铅金属。
下面将介绍粗铅火法精炼的工艺流程。
一、铅矿破碎和磨矿将原料铅矿进行破碎和磨矿处理,将其细化成粉末。
这一步骤旨在增大铅矿的表面积,便于后续的矿石浸取和反应过程。
二、矿石浸取将磨碎后的铅矿与稀硫酸等酸性溶液进行反应浸取。
这一步骤的目的是将铅矿中的铅物质溶解出来,形成铅离子溶液。
三、铅离子还原将铅离子溶液进行还原反应,使铅离子还原为金属铅。
通常采用焙烧法或碳还原法进行。
焙烧法是指将铅离子溶液与还原剂一起加热,使还原剂与铅离子反应生成金属铅。
碳还原法是指将铅离子溶液与炭粉混合后加热,使炭粉与铅离子反应生成金属铅。
四、铅金属精炼经过还原反应后,得到的金属铅中可能还含有杂质。
为了提高铅金属的纯度,需要进行精炼。
精炼通常采用火法精炼或电解精炼。
火法精炼是指将金属铅加热至一定温度,使其中的杂质氧化并形成气体,然后通过冷却和凝固将杂质分离出去。
电解精炼是指将金属铅作为阳极,在电解槽中进行电解,使杂质被电解掉,从而提高铅金属的纯度。
五、铅金属浇铸经过精炼后,得到的铅金属可以进行浇铸成型。
浇铸可以根据需要选择不同的形状和尺寸,用于制造各种铅制品,如铅板、铅管、铅合金等。
六、废渣处理在粗铅火法精炼的过程中,会产生一定的废渣。
这些废渣中可能含有一些有害物质,需要进行安全处理。
废渣处理通常包括固化、中和、焚烧等步骤,以将有害物质固化、中和或破坏,降低对环境的影响。
总结:粗铅火法精炼是一种常见的铅冶炼工艺,通过铅矿破碎和磨矿、矿石浸取、铅离子还原、铅金属精炼、铅金属浇铸和废渣处理等步骤,可以提取和精炼铅金属,并制造各种铅制品。
在整个过程中,需要注意安全环保,对废渣进行正确处理,以减少对环境的污染。
经过粗铅火法精炼,可以获得高纯度的铅金属,为各种应用提供优质的原材料。
铅冶炼中的火法冶炼与电解冶炼

精炼
将粗铅进行精炼处理,去除其中的杂质,得 到纯度较高的精铅。
火法冶炼的特点
01
02
03
生产效率高
火法冶炼具有较高的生产 效率,能够大规模地生产 铅金属。
适用范围广
火法冶炼适用于各种类型 的铅矿石,尤其是低品位 和高难度的矿石。
环境污染大
火法冶炼过程中会产生大 量的废气、废水和废渣, 对环境造成较大的污染。
在资源条件方面,如果铅矿品位较高且矿石中杂质较少,电 解法是更好的选择,因为它可以提供更高纯度的产品。相反 ,如果铅矿品位较低或矿石中杂质较多,火法冶炼可能更适 合,因为它能够更有效地从矿石中提取铅。
根据环保要求选择
火法冶炼过程中会产生大量的废气、废水和固体废弃物, 对环境造成较大的污染。相比之下,电解法在生产过程中 产生的废弃物较少,对环境的影响较小。
03
火法与电解法炼铅的比较
资源利用率比较
火法炼铅
火法炼铅工艺利用了铅锌矿中的有价元素,通过高温熔炼得到粗铅,再经过一 系列的精炼过程得到纯铅。由于火法炼铅过程中无法有效分离锌和铅,因此资 源利用率相对较低。
电解冶炼
电解冶炼工艺通过电解方式将阳极泥中的铅氧化物转化为硫酸铅,再通过还原 熔炼得到纯铅。该工艺能够有效地分离锌和铅,提高了资源利用率。
在能源供应紧张或能源价格较高的地区,电解法则可能成为更经济的选择。此外 ,对于一些可再生能源丰富的地区,如水电丰富的地区,使用电解法进行铅冶炼 可以充分利用可再生能源,降低生产成本。
THANKS
感谢观看
环保友好
为降低生产过程中的环境污染,电解法炼铅技术正不断改进,以减 少废水和废气排放,同时加强对有价金属的回收利用。
多元化产品开发
铅火法精炼工艺流程
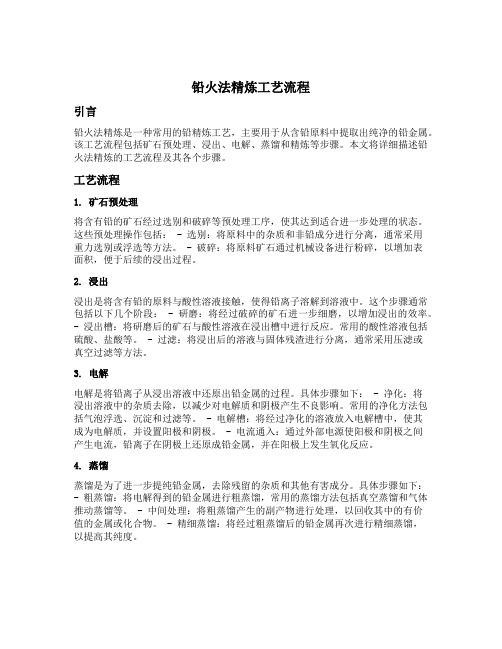
铅火法精炼工艺流程引言铅火法精炼是一种常用的铅精炼工艺,主要用于从含铅原料中提取出纯净的铅金属。
该工艺流程包括矿石预处理、浸出、电解、蒸馏和精炼等步骤。
本文将详细描述铅火法精炼的工艺流程及其各个步骤。
工艺流程1. 矿石预处理将含有铅的矿石经过选别和破碎等预处理工序,使其达到适合进一步处理的状态。
这些预处理操作包括: - 选别:将原料中的杂质和非铅成分进行分离,通常采用重力选别或浮选等方法。
- 破碎:将原料矿石通过机械设备进行粉碎,以增加表面积,便于后续的浸出过程。
2. 浸出浸出是将含有铅的原料与酸性溶液接触,使得铅离子溶解到溶液中。
这个步骤通常包括以下几个阶段: - 研磨:将经过破碎的矿石进一步细磨,以增加浸出的效率。
- 浸出槽:将研磨后的矿石与酸性溶液在浸出槽中进行反应。
常用的酸性溶液包括硫酸、盐酸等。
- 过滤:将浸出后的溶液与固体残渣进行分离,通常采用压滤或真空过滤等方法。
3. 电解电解是将铅离子从浸出溶液中还原出铅金属的过程。
具体步骤如下: - 净化:将浸出溶液中的杂质去除,以减少对电解质和阴极产生不良影响。
常用的净化方法包括气泡浮选、沉淀和过滤等。
- 电解槽:将经过净化的溶液放入电解槽中,使其成为电解质,并设置阳极和阴极。
- 电流通入:通过外部电源使阳极和阴极之间产生电流,铅离子在阴极上还原成铅金属,并在阳极上发生氧化反应。
4. 蒸馏蒸馏是为了进一步提纯铅金属,去除残留的杂质和其他有害成分。
具体步骤如下:- 粗蒸馏:将电解得到的铅金属进行粗蒸馏,常用的蒸馏方法包括真空蒸馏和气体推动蒸馏等。
- 中间处理:将粗蒸馏产生的副产物进行处理,以回收其中的有价值的金属或化合物。
- 精细蒸馏:将经过粗蒸馏后的铅金属再次进行精细蒸馏,以提高其纯度。
5. 精炼精炼是为了进一步提高铅金属的纯度和质量,并去除残留的杂质。
具体步骤如下:- 精炼炉:将经过精细蒸馏后的铅金属放入精炼炉中进行加热。
常用的精炼炉包括反射式电弧炉、感应熔炼炉等。
粗铅火法精炼工艺流程

粗铅火法精炼工艺流程
1.原料准备:将粗铅料经过矿石选矿、破碎等工艺,得到符合要求的
粗铅矿石。
2.熔炼:将粗铅矿石投入到熔炉中,加入一定比例的焙烧矿石(如铅矿)和辅助熔剂(如焦炭),并且加热至高温。
在熔炼过程中,杂质如硫、锑等被氧化生成气体,升腾至熔炉上部,而铅则沉淀在底部。
3.分离和除杂:通过熔炼后的铅浆进一步处理,包括分离和除杂工艺。
首先,将铅浆放入沉降池,让铅沉淀,沉淀后的铅浆称为阳极泥。
其次,
将阳极泥进行干燥和破碎,得到粉末状的阳极泥。
然后,通过浸出工艺,
将阳极泥浸入含硫酸溶液中,硫酸与杂质发生反应生成不溶于溶液的硫酸
盐沉淀。
最后,通过过滤、洗涤和干燥等工艺,得到除杂后的纯净阳极泥。
4.精炼:将纯净阳极泥与碳料(如焦炭)混合,加入电解槽中进行精炼。
电解槽中的阳极为纯净阳极泥和焦炭混合物,阴极为铅板。
通过电流
的作用,阳极上的铅氧化成溶于溶液中的铅离子,然后在电解槽底部的铅
铁板上还原成固态铅,同时有机杂质也被氧化或还原,从而得到纯净的铅。
5.铸锭和精炼再次:精炼后的铅液经过过滤、除杂等工艺,得到纯净
的铅液。
然后,将铅液倒入铸锭模具中,冷却凝固形成铅锭。
铅锭具有高
纯度和规整的形状,并可用于不同领域的应用。
以上就是粗铅火法精炼工艺流程的一般步骤。
需要注意的是,具体每
个工艺环节的操作和工艺参数会因生产工艺、设备和原料的不同而有所差异。
因此,在实际生产过程中,需要根据实际情况进行调整和优化。
铅的湿法冶炼原理

铅的湿法冶炼原理铅的湿法冶炼啊,其实就像是一场在溶液里的奇妙旅行。
你看,铅在自然界里有它自己的存在形式,比如说方铅矿,这里面铅和硫紧紧地抱在一起。
但是我们想要把铅单独弄出来呀,就得想点巧妙的办法。
在湿法冶炼里呢,有个很关键的东西叫浸出剂。
这浸出剂就像是一个超级热心的小助手,它的任务就是把铅从矿石里拽出来。
比如说硫酸就常常被用作浸出剂。
当把含有方铅矿的矿石和硫酸溶液放在一起的时候,就像一场小小的化学派对开始了。
方铅矿(PbS)遇到硫酸(H₂SO₄),它们就开始互相作用啦。
反应式大概是PbS + H ₂SO₄ = PbSO₄+ H₂S。
这个反应就像是铅和硫这对小伙伴被硫酸给搅和了一下,铅就和硫酸根结合成了硫酸铅,而硫呢,变成了硫化氢跑出来了。
不过这硫酸铅还不是我们最终想要的纯铅哦。
那接下来怎么办呢?这时候又有新的角色要登场啦。
我们会用到一种还原剂。
这个还原剂就像是一个救星,它要把硫酸铅里的铅给还原出来。
像铁就可以当这个还原剂。
想象一下,硫酸铅(PbSO₄)正安安稳稳地待着,铁(Fe)就冲过来了,然后发生反应PbSO₄+ Fe = Pb + FeSO₄。
就好像铁把铅从硫酸铅这个小集体里给解救出来了一样,铅就变成了单质铅,而铁自己则变成了硫酸亚铁。
这个过程就像是一场接力赛,浸出剂先把铅从矿石里拉出来一部分,然后还原剂再把铅彻底还原成我们想要的金属铅。
在整个湿法冶炼的过程中啊,还有很多小细节得注意呢。
比如说溶液的浓度、温度这些条件都很重要。
如果溶液浓度不合适,就像做饭的时候调料放错了量一样,反应可能就不能很好地进行。
温度也是,太冷或者太热都不行。
太冷了,那些分子啊、离子啊都懒洋洋的,反应就慢吞吞的;太热了呢,又可能会有一些其他的副反应发生,就像本来好好的一场聚会,突然来了些不速之客捣乱。
而且啊,在冶炼的过程中,我们还得考虑环保的问题呢。
像刚才反应里产生的硫化氢,这可是个有点调皮捣蛋的家伙,它有臭味,还对环境不太友好。
- 1、下载文档前请自行甄别文档内容的完整性,平台不提供额外的编辑、内容补充、找答案等附加服务。
- 2、"仅部分预览"的文档,不可在线预览部分如存在完整性等问题,可反馈申请退款(可完整预览的文档不适用该条件!)。
- 3、如文档侵犯您的权益,请联系客服反馈,我们会尽快为您处理(人工客服工作时间:9:00-18:30)。
第十章高温分离提纯过程10.0 概述一、火法精炼的目的•除去有害杂质,生产出具有一定纯度的金属;→当金属中的杂质含量超过一定限度时,其物理、化学和机械性能会发生变化。
•生产出含有各种规定量的合金元素的金属,使其具有一定的物理、化学和机械性能;如合金钢的生产•回收其中具有很高经济价值的稀贵金属“杂质”。
如:粗铅、粗铜中的金、银及其他稀贵金属。
二、火法精炼的基本原理利用主金属与杂质的物理和化学性质的差异•形成与主金属不同的新相,将杂质富集于其中;•或者:将主金属全部转移至新相,而使杂质残留下来。
三、火法精炼的基本步骤•用多种(化学的或物理的)方法使均匀的粗金属体系变为多相(一般为二相)体系;•用各种方法将不同的相分开,实现主体金属与杂质的分离。
四、火法精炼的基本体系利用主金属与杂质的物理和化学性质的差异•五、火法精炼方法•化学法基于杂质与主金属化学性质的不同,加入某种反应剂使之形成某种难溶于金属的化合物析出或造渣。
•物理法基于在两相平衡时杂质和主金属在两相间分配比的不同。
→利用粗金属凝固或熔化过程中,粗金属中的杂质和主金属在液–固两相间分配比的不同——熔析精炼、区域精炼(区域熔炼)。
→利用杂质和主金属蒸气压的不同,因而粗金属蒸发过程中,其易蒸发的组份将主要进入气相,与难蒸发组分分离——蒸馏精炼、升华精炼。
•10.1 氧化精炼10.1.1 金属熔体中杂质元素[A]氧化反应的机制•1、[A]与空气中的O2直接反应[A] + 0.5O2 = AO(反应10-1)AO为独立的固相或熔于熔渣中。
这种反应机制的机率很小。
•2、主金属Me首先被氧化成MeO,MeO(包括人工加入的MeO)进而与杂质[A]反应(或进入熔渣后与杂质反应):[A] + (MeO) = (AO) + Me(反应10-2)•3、MeO扩散溶解于主金属中并建立平衡,后者再将[A]氧化:2[Me] + 2[O] ←→2(MeO)(反应10-3)[A] + [O] = (AO)(反应10-4)总反应:[A] + (MeO) = (AO) + [Me]10.1.2 金属熔体中元素氧化反应的标准吉布斯自由能变化•在氧化精炼条件下,杂质元素及氧都是作为溶质处于主金属的熔体(溶液)中;•在研究熔体(溶液)中的化学反应时,其溶质的标准态不一定采用纯物质;•为研究熔体中化学反应的热力学,须计算在指定标准状态下溶质氧化反应的标准吉布斯自由能变化?rG□:[A] + [O] = AO[A],[O] ——金属熔体中的A和氧•△rG□与主金属熔体(溶剂)的种类、以及所采用的标准态有关。
铁溶液中杂质的氧化•当A和氧均为处于铁液中的溶质时,其标准态采用符合亨利定律、质量浓度为1%的溶液;假定生成物AOn为纯物质时;•氧化反应的△rG□–T关系(图10-1);→铁液中△rG□与△rG*(图7-2)数值上有很大差异;→但二者存在着类似的规律性;→各元素的顺序亦大体相同。
••在给定的标准状态下,△rG□–T 线位于主金属氧化物的△rG□–T 线以下的元素,都能被主金属氧化物氧化。
如铁液中的杂质Al、Ti、Mn、Si等。
•在生成的氧化物均为纯物质(活度为1)的情况下,铁液中△rG□–T 线位置愈低的元素愈易被氧化除去;→当有多种杂质同时存在时,则位置低者将优先氧化;例如,在铁液中硅将比铬优先氧化。
→某些△rG□–T 线发生交叉。
例如,当温度超过1514K,碳比铬优先氧化——去碳保铬。
•标准状态下,△rG□–T 线位于主金属氧化物△rG□–T 线以上的元素在氧化精炼时将不能除去。
如钢液中Cu、Ni、W、Mo等合金元素不会氧化。
•实践中可采取措施改变反应物或生成物的活度。
→例如,标准状态下,单纯利用(FeO)的氧化作用,不可能去杂质磷。
→若造碱性渣,使生成的P2O5发生反应:P2O5 + CaO = CaO·P2O5降低P2O5的活度,则可在炼钢过程中脱除部分磷。
•粗铜的氧化精炼→能除去Al、Si、Zn、Fe、In、Sn、Co、As、Sb、Co、Pb等;→造碱性渣可除去部分As、Sb等杂质。
•粗铅的氧化精炼→能除去Sn、As、Sb等杂质;→加入NaOH造碱性渣,可大幅度提高除杂效果。
•10.1.3 氧化精炼过程的热力学分析一、生成熔渣或固体产物的氧化精炼过程•当γ0值未知,但已知给定温度下杂质的溶解度时,可求得熔体中杂质平衡浓度的近似结果。
例如,已知1200℃时,铁在铜中溶解度为5%(质量),换算成摩尔分数为0.056。
已知饱和溶液中溶质的活度与其纯物质相同,即在铁饱和的铜液中,aFe = 1,故γ[Fe] = 1/0.056 = 17.8假设在一定的浓度范围内,活度系数不随浓度而变,即在稀溶液中γ[Fe] = = 17.8故平衡时铜液中铁的平衡浓度为:x[Fe] = 1/(17.8*4.57*103) = 1.22*10-5•2、影响氧化精炼过程除杂效果的因素1)温度◆金属中许多杂质的氧化过程为放热过程。
→升高温度对精炼除杂反应不利。
◆炼钢过程中硅、锰、铬、磷氧化反应的平衡常数(表10-2)随温度升高而减小。
→升高温度不利于这些杂质的氧化。
◆杂质锑在铅氧化精炼过程中的行为与此类似(图10-2)。
→渣含锑相同时,随着温度升高,铅中锑含量增加。
2)熔渣的成分◆渣的酸碱度影响渣中氧化物的活度。
◆当生成的杂质氧化物为酸性(如SiO2,P2O5等)时,则在碱性渣中其活度小,有利于其除去。
→例如,粗铅氧化精炼除砷、锑时,加入Na2CO3或硝石,使氧化产物As2O3等进一步反应成砷酸钠以降低其活度。
As2O3 + 3Na2CO3 = 2Na3AsO3 + 3CO2→炼钢过程中,磷在渣相和铁液中的L'P与渣中SiO2含量有关(图10-3)。
降低SiO2、提高CaO 含量,L'P大幅增加。
◆当杂质氧化产物为碱性氧化物时,则炉渣应保持为酸性。
◆渣中主金属氧化物(MeO)的活度对氧化精炼有重大影响。
→如,炼钢时提高铁液中FeO的活度,相应地提高了铁液中氧的活度,故有利于提高L'A 。
→例如炼钢过程中L'P值与渣中FeO含量由关(图10-4)。
→但FeO含量太高时,渣中磷酸盐的稳定性反而降低,不利于脱磷。
3)金属相的成分金属相的成分将影响杂质A的活度系数f[A]。
如铁液中C、Si、P、Al等对硫活度的相互作用系数均为正值。
→它们的存在使铁液中硫的活度系数增大,有利于脱硫。
4)杂质的性质杂质A氧化反应的△fG*或△rGθ值愈负,则K'A值愈大,愈有利于其除去。
二、生成气体产物的氧化精炼过程•1、氧化精炼脱碳(或加碳脱氧)◆典型的脱碳过程——铁液中的脱碳反应:2[C] + O2 = 2CO[C] + (FeO) = CO + Fe[C] + [O] = CO (反应10-6)◆利用反应10-6,可从高氧含量金属中脱氧——加碳脱氧。
◆在钽、铌等金属的高温真空精炼时,利用反应10-6:→加入钽(铌)的氧化物,除去金属中过剩的碳;→当金属中氧过量时,适当加入碳化物除氧。
脱碳(或脱氧)过程中最终产品中残留碳(或氧)量◆金属脱碳反应的平衡常数:◆在PCO一定的情况下,金属中残余氧和碳浓度之积为常数。
——钢液脱碳过程中%[O]与%[C]的关系(图10-5)。
◆残余氧和碳浓度之积与PCO值成正比。
→为降低碳含量,则应降低PCO(如真空脱碳)或适当提高残余氧含量。
→为了降低氧含量,则可适当提高碳含量。
PCO的计算:◆CO气泡的形成应克服气相压力、钢液及熔渣层的静压力以及形成气泡所需的表面能。
◆在钢液与炉底耐火材料界面上,气泡内的CO分压为:PCO ——气泡内的CO分压,Pa;P气——炉气的压力,1.01325×105Pa;ρm、ρs ——分别为钢液及熔渣的密度,kg/m3;Hm、Hs ——分别为钢液层及熔渣层的厚度,m;σ ——钢液的表面张力,N/m;r ——气泡的半径,m;g —— 9.81m/s2,重力加速度。
◆当气泡的半径r≥10-3m时,2σ/r ≤2600Pa;当Hs<0.15m时,Hsρsg<4500Pa;◆相对于大气压力及钢液静压力,可忽略2σ/r和Hsρsg两项。
2)钽、铌真空烧结(或熔炼)的脱碳或脱氧◆钽粉除碳——加入Ta2O5,在高温真空下处理。
钽粉除氧——加入TaC,在高温真空下处理。
◆高温真空处理的基本反应:[O] + [C] = CO(g)◆对于钽(1900~2100℃):(%[C])(%[O])= ( PCO/Pθ)/[2.83*104exp(-3.25*104/T)] (式10-8)对于铌(1600~2000℃):(%[C])(%[O])= ( PCO/Pθ)/[1.1*105exp(-3.35*104/T)] (式10-9)•10.2 硫化精炼•硫化精炼的基本原理与氧化精炼相似。
•常用于铅、锡、锑等粗金属中铜、铁的脱除。
→铜和铁对硫的亲和势较铅、锡、锑等大。
•粗铅、粗锡硫化精炼除铜、铁的基本反应:Pb(l) + S = [PbS][PbS] + 2[Cu] ( 或[Fe]) = Cu2S(s) (或FeS(s)) + Pb(l)Sn(l) + S = [SnS][SnS] + 2[Cu]( 或[Fe]) = Cu2S(s)( 或FeS(s)) + Sn(l) •粗锑硫化精炼除铜、铁的基本反应:2Sb(l) + 3S = [Sb2S3][Sb2S3] + 6[Cu] = 3Cu2S(s) + 2Sb(l)[Sb2S3] + 3[Fe] = 3FeS(s) + 2Sb(l)10.3 熔析与凝析精炼一、基本原理•粗金属在熔化(或凝固)的过程中杂质在固相和液相的平衡浓度不同。
•从均匀的熔体中开始凝固时,首先析出不同组成的固体。
二、熔析精炼的基本步骤•在均匀的合金中产生多相体系(液体+液体、液体+固体);产生多相体系可以用加热、缓冷等方法。
•所产生的两相按比重不同而进行分层。
→如果分层为二液相则分别放出;→如果分层为固体和液体,则利用漏勺、捞渣器等使两相分离;→或者使液体沿着炉底斜坡徘出炉外,而固体则仍留于炉底上,从而使二相分离(如粗锡熔析除铁)。
三、熔析精炼的类型•1、冷却凝析精炼将具有二元共晶型的液态粗金属熔体缓慢冷却到稍高于共晶温度,杂质以固体(或固溶体)析出并浮于金属熔体的表面上,使固相与液相分离。
•2、加热熔析精炼将具有二元共晶型的固态粗金属加热到稍高于共晶温度,杂质含量接近共晶组成的熔体,沿倾斜的炉底流出,而杂质仍留在固相中。
四、熔析精炼的应用•1、熔析精炼对二元系的要求→杂质与主体金属熔点相差较大;→共晶点(三相点)的组成应非常靠近主金属一侧;→共存相应该易于分离。