粗铅的火法精炼技术
粗铅火法精炼工业实践
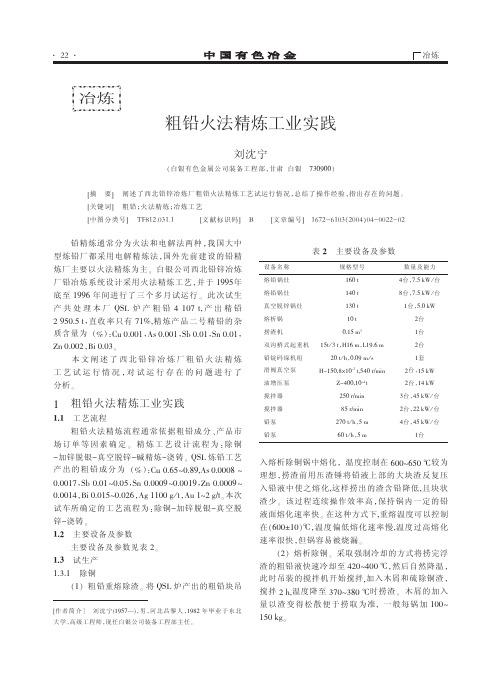
!
"#"
场订单等因素 确定$ 精炼 工艺设计流 程为&除铜
4加锌脱银 4真空脱锌4碱精炼 4浇铸 $ =>0 炼铅工艺 产 出 的 粗 铅 成 分 为 "? %&@A #’"( $#’+15B3 #’###+ $ #’##!&!>C #’#! $#’#(!>9 #’###1 $#’##!1!:9 #’###1 $ #’##!%!D8 #’#!($#’#-" !BE !!## E ! $!BA !$- E7$$ 本次 试车所确定的工艺流程为 & 除铜 4 加锌脱银 4 真空脱
主要设备及参数 主要设备及参数见表 -$
!(# )E$
!!!! 年 " 月第 ! 期
粗铅火法精炼工业实践 ( (( 刘沈宁
! !# !
通常将铅液中的 #$ 除至 %&’" 较为合适 ( 而此 次 试 生 产 #$ 除 到 平 均 %&%")" ( 熔 析 渣 产 出 率 !&*)"( 但含 #$ 较低 ( 只有 *&+)" ! 与国外有关工厂 相比 ( 此次试车熔析渣含 #$ 低 ( 含 ,- 高 ( 产渣率高 ! 待工厂气动吸附装置投入使用后 " 熔析渣含铜将会 大幅度提高 " 产渣率也会相应降低 ! 熔析除铜作业 约需 . /! #+$ 加硫除铜 % 加硫除铜是除铜工序技术性最 强的环节 ( 首 先 是 加 硫 方 式 ( 其 次 是 温 度 点 的 掌 握 ! 将熔析除铜铅泵入硫除铜锅中 ( 快速降温至 ++% # 左 右 ( 进行机械 搅 拌 " 随 之 加 入 硫 磺 ( 硫 磺 的 加 入 量 根据铅液中的含铜量计算确定 ( 一般按 #$$0%’ $’&) 进行控制 ! 硫磺尽量加入旋涡中心( 避免漂浮在铅液 面上氧化燃烧 " 同时硫磺分批加入 ")% 123 加完 ! 加 完硫磺再加 *%! 木屑在 ++% # 恒温 ( 搅拌 )&*&+ /( 吊 开搅拌机升温 " 温度升至 +4% # 时捞渣 ! 在试生产的后期 " 探索出一套较适合的加硫除 铜操作方法 " 除铜效果明显好转 ( 基本能一次将铅液 中的铜除至 %&%’" 以下 " 而且硫渣产率也不高 " 只有
第6章 粗铅精炼
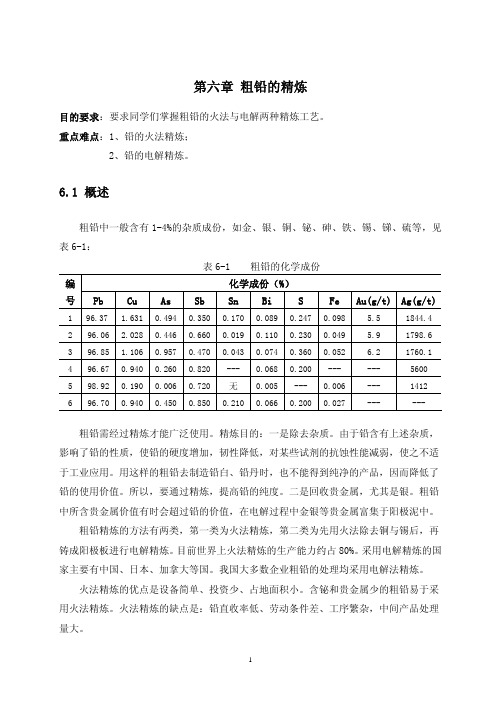
如是电解精炼,阳极板要含 0.3—0.8%锑,此时要对阳极板含锑进行调整。粗铅的火法精
炼工艺流程如图 6-1:
粗铅
粗铅火法精炼工艺流程图
除铜
铜浮渣
已除铜的铅
精炼除砷锑锡
精炼渣
软化铅
加锌除银
银锌壳
除银的铅
精炼除锌
精炼渣
初步精炼的铅
除铋
含铋浮渣
精铅
图 6-1
6.2.2 粗铅除铜精炼
6.2.2.1 除铜精炼的一般原理
2
A、熔析除铜 基本原理:熔析除铜的基本原理是基于铜在铅液中的溶解度随着温度的下降而减少, 当含铜高的铅液冷却时,铜便成固体结晶析出,由于其比重较铅小(约为 9),因而浮至铅 液表面,以铜浮渣的形式除去。又铜在铅液中的溶解度随着温度的变化而变动,温度下 降时,液体合金中的含铜量相应地减少,当温度降至共晶点(326℃)时, 铜在铅中的含 量为 0.06%,这是熔析除铜的理论极限。 当粗铅中含砷锑较高时,由于铜对砷、锑的亲合力大,能生成难溶于铅的砷化铜和 锑化铜,而与铜浮渣一道浮于铅液表面而与铅分离。实践证明,含砷、锑高的粗铅,经 熔析除铜后,其含铜量可降至 0.02~0.03%。粗铅中含砷、锑低时,用熔析除铜很难使铅 液含铜降至 0.06%。这是因为: a、熔析作业温度通常在 340℃以上,铜在铅液中的溶解度大于 0.06%; b、含铜熔析渣的上浮取决于铅液的粘度,铅液温度降低则粘度增大,铜渣细粒不易 上浮。 在熔析过程中,几乎所有的铁、硫(呈铁、铜及铅的硫化物形态)以及难熔的镍、 钴、铜、铁的砷化物及锑化物都被除去;同时贵金属的一部分也进入熔析渣。 熔析操作有两种方法:1.加热熔析法;2.冷却熔析法。二者熔析原理是相同的,前 者是将粗铅锭在反射炉或熔析锅内用低温熔化,使铅与杂质分离;后者是将鼓风炉放出 的铅水铅泵汲送到熔析设备,然后降低温度使杂质从铅水中分凝出来。 B、加硫除铜 理论基础:粗铅经熔析脱铜后,一般含铜仍超过 0.04%, 不能满足电解要求,需再 进行加硫除铜。在熔融粗铅中加入元素硫时,首先形成 PbS,其反应如下:
有色冶金技术专业《火法初步精炼工艺控制》
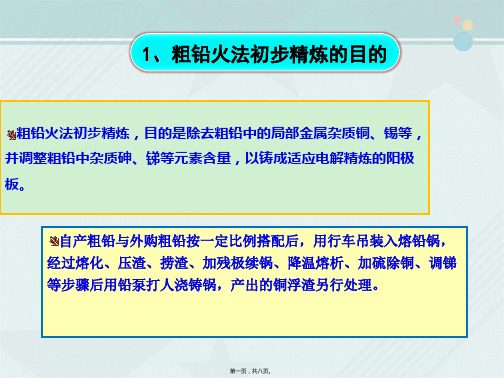
内容总结
粗铅火法初步精炼,目的是除去粗铅中的局部金属杂质铜、锡等,并调整粗铅中杂质 砷、锑等元素含量,以铸成适应电解精炼的阳极板。铜在铅液中的溶解度随着温度的降低 而减少。理论上,当铅液温度为326℃时,含铜量为006%。而含铜高的铅液冷却时铜呈固 熔体状态析出,由于其密度比铅小,浮在铅液外表而被除去。4Sb5O212NaOH ﹦ 4Na3SbO46H2O 4As5O212NaOH = 4Na3AsO46H2O。谢 谢
1、粗铅火法初步精炼的目的
粗铅火法初步精炼,目的是除去粗铅中的局部金属杂质铜、锡等, 并调整粗铅中杂质砷、锑等元素含量,以铸成适应电解精炼的阳极 板。
自产粗铅与外购粗铅按一定比例搭配后,用行车吊装入熔铅锅, 经过熔化、压渣、捞渣、加残极续锅、降温熔析、加硫除铜、调锑 等步骤后用铅泵打人浇铸锅,产出的铜浮渣另行处理。
在铅锅内调锑的根本原理为:锑等杂质氧化与氢氧化钠结合生 成各种钠盐除去或者参加含锑低的粗铅。
4Sb5O212NaOH ﹦ 4Na3SbO46H2O 4As5O212NaOH = 4Na3AsO46H2O
第五页,共八页。
2.粗铅火法初步精炼工艺控制
(4)粗铅火法初步 精炼温度控制
第六页,共八页。
谢 谢!
第二页,共八锡
由于锡对氧的亲和力大于铅与氧的亲和力,故可用氧化铅 作氧化剂,借助机械搅拌参加铅液中锡置换: 2PbOSn = 2PbSnO2 氧化锡不溶于铅且密度小,浮于铅液外表呈稀渣被捞去, 此法暂不用。现工艺过程中锡是在电解后析出铅精炼过程 中除去的。
第三页,共八页。
2、粗铅火法初步精炼工艺控制 (3)调整锑含量
为满足铅电解对阳极含锑的要求,当粗铅含锑低时,需参加局 部含锑高的粗铅、铅锑合金或精锑,使阳极含锑到达04%~07%。 当粗铅含锑过高或过低时,需氧化调锑,使阳极含锑在04%~07%。
火法炼铅工艺

火法炼铅工艺火法炼铅工艺是一种常用的金属冶炼工艺,主要用于铅矿石的冶炼。
本文将介绍火法炼铅的工艺流程、设备及对环境的影响。
一、工艺流程:火法炼铅工艺的主要步骤包括碎矿、浮选、烧结、还原、脱硫、炼出等环节。
1. 碎矿:将铅矿石经过破碎和磨矿处理,使其颗粒度适宜进一步处理。
2. 浮选:利用浮选法选别矿石中的杂质,以提高铅的品位。
经过浮选处理,矿石中的硫化铅和杂质被分离,得到精矿。
3. 烧结:将浮选得到的铅精矿与焦炭混合,添加适量的草木灰等助熔剂,经过烧结的高温煅烧处理,使精矿颗粒熔结成为烧结块。
4. 还原:将烧结块放入高温还原炉中,加入石灰和焦炭作为还原剂,将精矿中的氧化铅还原为金属铅。
在还原的过程中,金属铅被蒸发出来,通过冷凝收集。
5. 脱硫:通过向还原炉中加入适量的空气氧化剂,将还原反应中形成的二氧化硫气体进行氧化反应,以除去气体中的硫化物。
6. 炼出:将经过还原和脱硫处理的金属铅熔融炼制,去除其中的杂质和不溶性物质。
经过过滤、离心、冷却等处理,获得纯净的铅液。
二、设备:火法炼铅工艺需要使用的主要设备有碎矿机、浮选机、烧结机、还原炉等。
其中,还原炉是整个工艺中最重要的设备,需要具备高温煅烧和还原铅精矿的能力。
三、环境影响:火法炼铅工艺对环境产生的影响主要有以下几个方面:1. 废气排放:火法炼铅过程中产生大量的废气,主要包括二氧化硫气体。
这些废气中的二氧化硫是一种有害气体,对环境和人体健康都有较大的危害。
2. 废水排放:在火法炼铅过程中,会产生大量的废水,其中含有金属离子和酸性物质。
这些废水需要经过处理后才能排放,否则会对水源和周围的土壤产生污染。
3. 固体废弃物处理:火法炼铅过程中产生的固体废弃物包括矿渣、烟尘等。
这些固体废弃物需要进行妥善处理,以防止对土地和水源造成污染。
为了减少火法炼铅工艺对环境的影响,需要采取相应的环保措施,如加装废气处理设备、建立废水处理系统、合理处置固体废弃物等。
同时,还需要加强监管和管理,确保生产过程中的废物排放符合环境保护要求。
铅冶炼中的火法冶炼与电解冶炼

精炼
将粗铅进行精炼处理,去除其中的杂质,得 到纯度较高的精铅。
火法冶炼的特点
01
02
03
生产效率高
火法冶炼具有较高的生产 效率,能够大规模地生产 铅金属。
适用范围广
火法冶炼适用于各种类型 的铅矿石,尤其是低品位 和高难度的矿石。
环境污染大
火法冶炼过程中会产生大 量的废气、废水和废渣, 对环境造成较大的污染。
在资源条件方面,如果铅矿品位较高且矿石中杂质较少,电 解法是更好的选择,因为它可以提供更高纯度的产品。相反 ,如果铅矿品位较低或矿石中杂质较多,火法冶炼可能更适 合,因为它能够更有效地从矿石中提取铅。
根据环保要求选择
火法冶炼过程中会产生大量的废气、废水和固体废弃物, 对环境造成较大的污染。相比之下,电解法在生产过程中 产生的废弃物较少,对环境的影响较小。
03
火法与电解法炼铅的比较
资源利用率比较
火法炼铅
火法炼铅工艺利用了铅锌矿中的有价元素,通过高温熔炼得到粗铅,再经过一 系列的精炼过程得到纯铅。由于火法炼铅过程中无法有效分离锌和铅,因此资 源利用率相对较低。
电解冶炼
电解冶炼工艺通过电解方式将阳极泥中的铅氧化物转化为硫酸铅,再通过还原 熔炼得到纯铅。该工艺能够有效地分离锌和铅,提高了资源利用率。
在能源供应紧张或能源价格较高的地区,电解法则可能成为更经济的选择。此外 ,对于一些可再生能源丰富的地区,如水电丰富的地区,使用电解法进行铅冶炼 可以充分利用可再生能源,降低生产成本。
THANKS
感谢观看
环保友好
为降低生产过程中的环境污染,电解法炼铅技术正不断改进,以减 少废水和废气排放,同时加强对有价金属的回收利用。
多元化产品开发
第六章-粗铅精炼

第六章 粗铅精炼1、粗铅精炼方法有 法和 法两种。
目前世界上采用 的厂家较多,我国多采用 。
答案:火法 电解 火法 电解精炼2、火法精炼:火法精炼是利用杂质金属与主金属(铅)在高温熔体中物理性质或化学性质方面的差异,形成与熔融主金属不同的新相(如精炼渣),并将杂质富集其中,从而达到精炼的目的。
3、熔析除铜:根据铜在粗铅中的溶解度随温度下降而减小的原理,当含铜高的铅液冷却时,铜以固溶体的状态析出,由于其密度较铅液小,便以浮渣形式浮在铅液表面而被除去。
4、加硫除铜:根据铜对硫的亲和力比铅大,所以可向铅液中加入硫化剂,硫首先与铅作用生成硫化铅:Pb S PbS +=,由于铜对硫的亲和力大于铅对硫的亲和力,所以硫化铅中的铅很快被铜置换,生成硫化亚铜:22PbS Cu Pb Cu S +=+。
生成的2Cu S 在作业温度下不溶于铅,且密度较小,呈固溶体浮在铅液表面形成硫化渣而被除去。
5、加锌除银、加钙镁除铋的原理:在含杂质金属的粗铅中添加第三种甚至更多种金属,它们与杂质金属形成金属间化合物(合金)的亲和力大于铅,这些化合物密度比铅小,且不溶于铅,呈固溶体浮在铅液表面而被除去。
6、粗铅火法精炼初步除铜用 法,深度除铜用法。
答案:熔析除铜 加硫除铜7、粗铅火法精炼除杂的顺序为先除 ,其方法有和 ,再除砷锑锡,方法有 和 ;接着除银,主要方法有 ,然后除锌,现普遍采用;最后除铋,除铋后进行最终精炼,得到精铅。
答案:铜 熔析除铜 加硫除铜 炼化精炼 碱性精炼 加锌 真空蒸馏法8、碱性精炼:所谓碱性精炼是加碱于熔融粗金属中,使氧化后的杂质与碱给合成盐而除去的火法精炼方法。
9、请指出粗铅电解精炼前都有哪些杂质元素,铅阳极中杂质元素在电解过程中的行为?答案:根据金属的标准电位可把铅中的杂质金属分为三类:1)电位比铅负的金属Zn 、Fe 、Cd 、Co 和Ni 等;2)电位比铅正的Sb 、Bi 、As 、Cu 、Ag 、Au 等;3)电位与铅很相近的Sn ;第一类杂质金属由于它们具有比铅高的析出电位,且浓度极小,因此在阴极不致放电析出。
- 1、下载文档前请自行甄别文档内容的完整性,平台不提供额外的编辑、内容补充、找答案等附加服务。
- 2、"仅部分预览"的文档,不可在线预览部分如存在完整性等问题,可反馈申请退款(可完整预览的文档不适用该条件!)。
- 3、如文档侵犯您的权益,请联系客服反馈,我们会尽快为您处理(人工客服工作时间:9:00-18:30)。
9
粗铅的火法精炼
11.1 概述
生产的粗铅中一般含有1-4%的杂质成份,如金、银、铜、铋、砷、铁、锡、锑、硫等,见表
1-1:
表21-1 粗铅的化学成份(%)
工
厂
化学成份(%)
Pb Cu As Sb Sn Bi S Fe
Au(g/t) Ag(g/t
)
1 96.37 1.631 0.494 0.35 0.17 0.089 0.247 0.098 5.5 1844.4
2 96.06 2.028 0.446 0.66 0.019 0.11 0.23 0.049 5.9 1798.6
3 96.85 1.106 0.957 0.47 0.043 0.074 0.36 0.052 6.2 1760.1
4 96.67 0.94 0.26 0.82 --- 0.068 0.2 --- --- 5600
5 98.92 0.19 0.006 0.72 无 0.005 --- 0.006 --- 1412
6 96.7 0.94 0.45 0.85 0.21 0.066 0.2 0.027 --- ---
粗铅需经过精炼才能广泛使用。精炼目的:一是除去杂质。由于铅含有上述杂质,影响了铅
的性质,使铅的硬度增加,韧性降低,对某些试剂的抗蚀性能减弱,使之不适于工业应用。用这
样的粗铅去制造铅白、铅丹时,也不能得到纯净的产品,因而降低了铅的使用价值。所以,要通
过精炼,提高铅的纯度。二是回收贵金属,尤其是银。粗铅中所含贵金属价值有时会超过铅的价
值,在电解过程中金银等贵金属富集于阳极泥中。
粗铅精炼的方法有两类,第一类为火法精炼,第二类为先用火法除去铜与锡后,再铸成阳极
板进行电解精炼。目前世界上火法精炼的生产能力约占80%。采用电解精炼的国家主要有中国、日
本、加拿大等国。我国大多数企业粗铅的处理均采用电解法精炼。
10
粗铅火法精炼的优点是设备简单、投资少、生产周期短、占地面积小、生产成本较低。含铋
和贵金属少的粗铅易于采用火法精炼。火法精炼的缺点是:铅直收率低、劳动条件差、工序繁
杂,中间产品处理量大。
电解精炼的优点是能使铋及贵金属富集于阳极泥中,有利于综合回收,因此金属回收率高、
劳动条件好,并产出纯度很高的精铅。其缺点是基建投资大,且电解精炼仍需要火法精炼除去铜
锡等杂质。
我分厂采用的火法精炼只是初步精炼,其任务是将粗铅中的铜和砷、锑、锡除至一定程度,
并调整锑含量,浇注成化学质量和物理规格均满足要求的阳极板,为电解精炼做好准备。
11.2 粗铅火法精炼的工艺流程和基本原理
11.2.1 粗铅火法精炼的工艺流程
基夫赛特炉产出的粗铅经排铅口排出,以熔融状态加入连续脱铜炉进行脱铜,脱铜后粗铅含
铜0.07~0.08%,然后加入熔铅锅进一步脱铜精炼,除去粗铅中对电解有害的铜、锡等杂质,调整
锑含量,达到符合电解精炼要求的合格粗铅。工艺流程图见图11-1
11
图11-1 粗铅火法精炼的工艺流程图\
11.2.2 火法精炼的基本原理
11.2.2.1 熔析除铜
熔析除铜的基本原理是基于铜在铅液中的溶解度随着温度的下降而减少,当含铜高的铅液冷
却时,铜便成固体结晶析出,由于其比重较铅小(约为9),因而浮至铅液表面,以铜浮渣的形式除
去。又铜在铅液中的溶解度随着温度的变化而变动,温度下降时,液体合金中的含铜量相应地减
少,当温度降至共晶点(326℃)时, 铜在铅中的含量为0.06%,这是熔析除铜的理论极限。
当粗铅中含砷锑较高时,由于铜对砷、锑的亲合力大,能生成难溶于铅的砷化铜和锑化铜,
而与铜浮渣一道浮于铅液表面而与铅分离。实践证明,含砷、锑高的粗铅,经熔析除铜后,其含
铜量可降至0.02~0.03%。粗铅中含砷、锑低时,用熔析除铜很难使铅液含铜降至0.06%。这是因
为:
a、熔析作业温度通常在340℃以上,铜在铅液中的溶解度大于0.06%;
12
b、含铜熔析渣的上浮取决于铅液的粘度,铅液温度降低则粘度增大,铜渣细粒不易上浮。
在熔析过程中,几乎所有的铁、硫(呈铁、铜及铅的硫化物形态)以及难熔的镍、钴、铜、
铁的砷化物及锑化物都被除去;同时贵金属的一部分也进入熔析渣。
熔析操作有两种方法:1.加热熔析法;2.冷却熔析法。二者熔析原理是相同的,前者是将粗
铅锭在反射炉或熔析锅内用低温熔化,使铅与杂质分离;后者是将鼓风炉放出的铅水铅泵汲送到
熔析设备,然后降低温度使杂质从铅水中分凝出来。
粗铅的连续脱铜是应用熔析除铜的原理。我厂作业在CDF炉内进行,此时,脱铜炉要有足够
深的熔池和其他降温设施,以造成铅熔池自上而下有一定的温度梯度,铜及其化合物从熔池较冷
的底层析出,上浮至高温的上层,被铅液中所含的硫化铅或特意加入的硫化剂(铅精矿或黄铁
矿)所硫化,形成冰铜,其反应式如下:
Pbs(FeS)+2Cu=Cu2S+Pb(Fe)
因此,上部铅液的温度要求较高又要有足够的硫化剂,使上浮的铜不断被硫化,从而又促使
底部的铜上浮。随着这两个过程的进行,底部铅中的铜就越来越少。除硫化剂外,配料时还配入
铁屑、苏打。铁屑与硫化铅发生沉淀反应而降低冰铜中的含铅量,苏打在过程中进行如下反应:
4PbS+4Na2CO3=4Pb+3Na2S+Na2SO4+4CO2
从而降低了冰铜的熔点及含铅量。其余部分则形成砷酸盐,锑酸盐及锡酸盐进入炉渣。
粗铅脱铜程度取决于熔池底层的温度,铅在熔池的停留时间和粗铅中的砷锑含量等因素。产
出的冰铜和炉渣从熔池上部放出,脱铜后的铅液从底部虹吸放出。
在一定意义上说,连续脱铜过程就是把浮渣反射炉处理铜质浮渣的过程于粗铅熔析除铜过程
有机的结合起来,连续脱铜就是把浮渣反射炉置于除铜锅上的联合设备,在这里不断地实现铜的
析出和硫化,使其形成冰铜,消除了中间产物—浮渣。
13
连续脱铜具有的优点是:
a、简化了流程,能在一个炉子内完成多种任务;
b、充分利用铅液的潜热,节约燃料;
c、减轻劳动强度,改善劳动条件,提高劳动生产率,降低了生成成本;
d、便于实践机械化和自动化。
11.2.2.2 加硫除铜
1. 加硫除铜原理
理论基础:粗铅经熔析脱铜后,一般含铜仍在0.1%左右, 不能满足电解要求,需再进行加硫
除铜。在熔融粗铅中加入元素硫时,首先形成PbS,其反应如下:
2[Pb]+ 2S=2[PbS]
由于铜对硫的亲和力大于铅对硫的亲和力,所以硫化铅中的铅被铜置换,继而发生以下反
应:
[PbS]+2[Cu]=[Pb]+Cu2S
Cu2S比铅的比重小,且在作业温度下不溶于铅水,因此,形成的固体硫化渣浮在铅液面上。
最后铅液中残留的铜一般为0.001~0.002%。
加硫除铜的硫化剂一般采用硫磺。加入量按形成Cu2S时所需的硫计算,并过量20-30%。加硫
作业温度对除铜程度有重大影响,铅液温度越低,除铜进行得越完全,一般工厂都是在330-340℃
范围内。加完硫磺后, 应迅速将铅液温度升至450-480℃,大约搅拌40分钟以后,待硫磺渣变得
疏松,呈棕黑色时,表示反应到达终点,则停止搅拌进行捞渣,此种浮渣由于含铜低,只约2-
14
3%,而铅高达95%,因此返回熔析过程。加硫除铜后铅含铜可降至0.001-0.002%,送去下一步电
解精炼。
2.除铜精炼的工艺流程
除铜工艺流程如图11-2。
图11-2 除铜工艺流程
11.3 连续脱铜炉(CDF)本体结构
基夫赛特炉的粗铅经溜子加入到连续脱铜炉(CDF)中。连续脱铜炉的目的是通过冷却粗铅使
铜析出,进入冰铜相,并浮于熔池表面。连续脱铜炉主要由粘土砖和铬镁砖砌筑而成,炉内设3
道高度各不相同的隔墙将熔池分成4部分(原料室、产物室、返回室和循环室),以控制粗铅在