火法精炼ppt
金的火法冶炼.pptx

2
如果金块中含银较多,可按金银 1∶3 比例加入白银于坩锅内升温,熔化后,倒入水中淬成粒 状。加 20%的硝酸煮沸 1~2h 溶解银,溶液反应完全后(无微细泡沫) ,将硝酸银溶液倒入 食盐水中得到氯化银沉淀,滤出沉淀后用水合肼和氨水还原,制得四个上的银。其沉淀物洗涤烘干,于坩锅中加少许硼砂、硝石于1 250℃ 6熔结融,可语提出 999‰以上成色的金。 该炼金工艺经过多年生产应用实践证明,简便快速,损耗小,所用设施及化学试剂仅需要 300 ~500 元,投资少,金回收率高,对新疆阿勒泰地区各中小金矿企业所产的金泥、载金炭灰、 金精矿等冶炼均适用。
1
金泥或载金炭灰时须按一定配比加入熔剂,以除去金银之外的金属和非金属杂质。在金冶炼 过程中,造渣是熔炼的关键,它对冶炼技术及经济指标起决定作用。 (1) 造渣温度需控制在 1 050℃~1 150℃。 (2) 炉渣应具有较小的黏度。黏度小,废渣与金银易分离, 回收率高,损耗小;反之,易导致金 银回收率下降。 (3) 尽可能降低炉渣的相对密度,减少渣量,以提高金银的回收率,降低冶炼成本。 3 金泥的预处理 金泥的预处理实质是初步除去杂质,硫化物氧化和氧化物转化为硫酸盐的过程,为下一步提 炼金创造有利条件,提高金银成色,分离其他贱金属和非金属化合物。预处理过程: 将金泥置 于容器中(搪瓷盆) ,加 15%的稀硫酸文火煮 1h, 冷却过滤, 烘干。含铜、锌高的金泥,可在 稀硫酸介质中加入硝酸铵,加热至 90℃~95℃, 固液比为 1∶6, 煮沸 1~2h, 使铜生成铜 铵络合物进入溶液,过滤,留滤渣烘干后配辅料熔炼。当金泥含铅高时, 可在上述基础上用 15%4的熔N炼aO过H程溶液煮沸 30min 脱铅,过滤烘干后,再加配料熔炼。 称重预处理后的原料,按表 1 配入辅料,装入石墨坩锅。坩锅入炉放置平稳,于底部放木炭粉 末以防止炸裂和黏连。
第二章铜火法精炼的基本原理

第二章铜火法精炼的基本原理第一节铜火法精炼的化学基础粗铜的火法精炼,是在精炼炉中将固体粗铜熔化(或熔体装料),然后向熔体铜中通入空气,使其中对氧亲和力较大的杂质如锌、铁,铅、锡,砷、锑、镍等发生氧化,以氧化物的形态浮于铜液表面形成炉渣,或挥发进入炉气而除去的过程。
残留在铜液中的氧,经还原脱去后,即可浇铸成为电解精炼用的阳极板或火法精炼的精钢锭。
通入铜熔体中的空气,首先与占熔体中绝大多数的铜发生氧化作用,其反应式如下;4Cu +O2 =2Cu2O所生成的氧化亚铜(Cu2O)立即溶解于铜熔体中。
氧化亚铜在铜熔体种的溶解度,随温度的升高而增加,如.温度(℃) 1100 1150 1200溶解度(%) 5 8.3 12,4溶解在铜熔体中的氧化亚铜与铜中呈杂质形态存在的其他金属接触时,出于铜对氧的亲和力比许多金属杂质对氧亲和力小,所以氧化亚铜中的氧,便被这些金属杂质夺去.Cu2O+Me=MeO十2Cu式中Me代表金属杂质.从上式可以看出:当铜熔体中的氧化亚铜浓度愈高时,则与杂质碰撞的机会就愈多,从而使杂质发生氧化而除去的可能件也愈大。
铜精炼作业也就愈完全。
实践证明,为了更迅速彻底地除去铜中杂质,应力求氧化亚铜在铜熔体中的溶解达到饱和程度,并提高炉温。
以增加氧化亚铜在铜熔体中的溶解度。
但铜熔体在高温时饱和氧化亚铜愈多,虽对杂质的除去有利,却在脱氧还原时需要消耗更多的还原剂,延长还原时间,所以对整个作业来说仍然是不利的。
因此,为了避免铜液的过度氧化,要求氧化期铜熔体的温度,以控制在1150~1170℃为宜。
显然,铜熔体表面上的杂质,以及少部分在熔体内的杂质能被炉气或鼓入熔体中的空气泡所直接氧化。
但这种直接的氧化作用,对含量较少的杂质或较难氧化的杂质,毕竟由于反应物质的接触机会少而只有次要的意义。
所以,在粗铜的氧化精炼过程中,杂质的氧化,主要是与溶解在铜中的氧化亚铜的相互反应而实现的,在这种情况下,氧化亚铜起着将空气中的氧输送给杂质的传递作用。
金、银的火法精炼
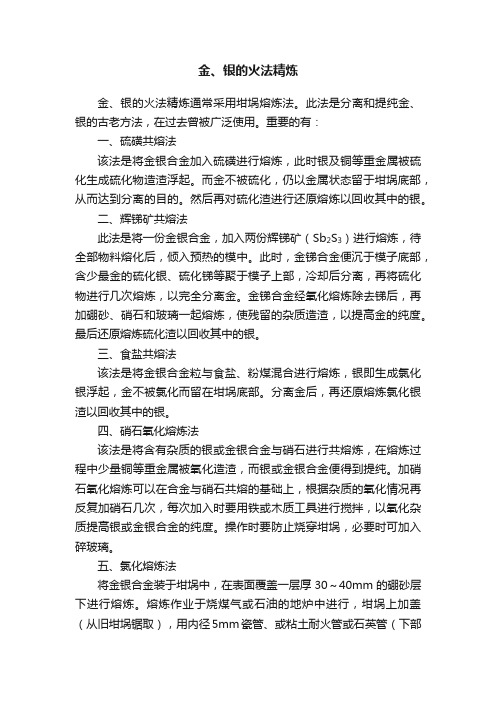
金、银的火法精炼金、银的火法精炼通常采用坩埚熔炼法。
此法是分离和提纯金、银的古老方法,在过去曾被广泛使用。
重要的有:一、硫磺共熔法该法是将金银合金加入硫磺进行熔炼,此时银及铜等重金属被硫化生成硫化物造渣浮起。
而金不被硫化,仍以金属状态留于坩埚底部,从而达到分离的目的。
然后再对硫化渣进行还原熔炼以回收其中的银。
二、辉锑矿共熔法此法是将一份金银合金,加入两份辉锑矿(Sb2S3)进行熔炼,待全部物料熔化后,倾入预热的模中。
此时,金锑合金便沉于模子底部,含少最金的硫化银、硫化锑等聚于模子上部,冷却后分离,再将硫化物进行几次熔炼,以完全分离金。
金锑合金经氧化熔炼除去锑后,再加硼砂、硝石和玻璃一起熔炼,使残留的杂质造渣,以提高金的纯度。
最后还原熔炼硫化渣以回收其中的银。
三、食盐共熔法该法是将金银合金粒与食盐、粉煤混合进行熔炼,银即生成氯化银浮起,金不被氯化而留在坩埚底部。
分离金后,再还原熔炼氯化银渣以回收其中的银。
四、硝石氧化熔炼法该法是将含有杂质的银或金银合金与硝石进行共熔炼,在熔炼过程中少量铜等重金属被氧化造渣,而银或金银合金便得到提纯。
加硝石氧化熔炼可以在合金与硝石共熔的基础上,根据杂质的氧化情况再反复加硝石几次,每次加入时要用铁或木质工具进行搅拌,以氧化杂质提高银或金银合金的纯度。
操作时要防止烧穿坩埚,必要时可加入碎玻璃。
五、氯化熔炼法将金银合金装于坩埚中,在表面覆盖一层厚30~40mm的硼砂层下进行熔炼。
熔炼作业于烧煤气或石油的地炉中进行,坩埚上加盖(从旧坩埚锯取),用内径5mm瓷管、或粘土耐火管或石英管(下部斜口)插入坩埚中通入氯气(图1)。
在熔练过程中,铜、银及其他杂质氯化造渣,其中某些氯化物则挥发除去。
氯化作业一直进行到火焰呈紫红色,用冷金属棒于火焰中能熏上一层黄褐色绒毛状的烟尘时终止。
取出坩埚稍停,待金冷凝后,扒出表面硼砂,将氯化渣铸入模中,倒出金块。
再将金块投入氯化铁溶液中浸泡除去表面氯化物后熔化铸锭,此金的成色可达99%以上。
粗铜的火法精炼技术
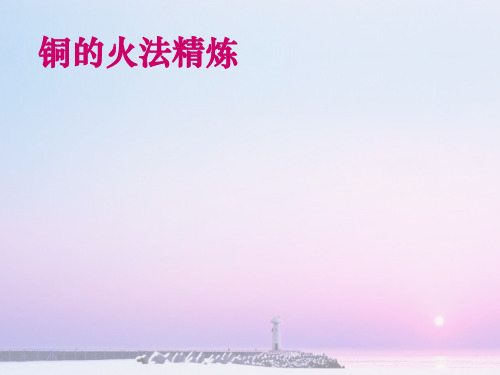
电解对阳极铜的物理外形规格要求,各工厂的控制标准不同,但 要求阳极铜厚度均匀;阳极铜耳部饱满、坚固、不许有明显裂纹, 耳子底部无飞边,耳部顶端对板面的弯曲度不大于10mm;板面平 整、细花纹、不夹渣;飞边、毛刺不超过6mm,板面起泡不超过 6mm;不允许有冷隔层,不允许上薄下厚。
二、铜火法精炼炉的结构
炉顶厚度为 380mm , 村质为镁质 / 镁铬质。
2.2 骨架部分
围板 立柱 拉杆 弹簧 水套构件
2.3 余热回收及烟道部分
反射炉的排烟方式有自然排烟和强制 排烟两种。一般都采用自然排烟方式, 烟气经竖直烟道、斜烟道和余热回收 及烟尘收集系统,由烟囱排出。烟尘 的收集采用重力沉降收尘,无任何的 收尘设备。余热回收采用低压板箱式 汽化水套,中间加对流管束。
三、固定式反射炉
固定式反射炉是传统的火法精炼 设备,是一种表面加热的膛式炉, 结构简单,操作容易,可以处理 冷料,也可以热料,可以烧固体 燃料、液体燃料或气体燃料。炉 子容积可大、可小,波动范围较 大。为了在精炼时使各部分熔体 的温度保持均匀,从而使熔体各 部分的杂质(特别是气体)含量 及浇铸温度均匀,炉子作业空间 不能太长以免发生温度降,为使 熔池温度趋于一致,精炼炉有 1.5~2m的燃烧前室,而且把炉顶 做成下垂式,保证炉尾温度与炉 子中央的温度相近。
倾动式精炼炉是20世纪60年代中期,由 瑞士人研究发明的。它是在反射炉和回 转炉基础上,吸取了两种炉型的长处而 设计的。炉膛形状像反射炉,保持较大 的换热面积,采取了回转炉可转动的方 式,增设了固定风口,取消了插风管和 扒渣作业,减轻了劳动强度,既能处理 热料又能处理冷料。倾动炉由炉基、摇 座、炉体、驱动装置、燃烧器及燃烧室 组成。炉基由耐热钢筋混凝土筑成,在 炉基上装设钢结构摇座,摇座上沿为圆 弧形,装有若干个滚轮。炉体底部也是 圆弧形,座在摇座上。液压缸底部装在 基础上,上部与炉底底部连接。伸缩液 压缸带动炉体倾动,倾动角度为± 30 0 , 有快慢两种倾转速度,氧化、还原、倒
第二篇火法冶金原理第5章粗金属的火法精炼16h
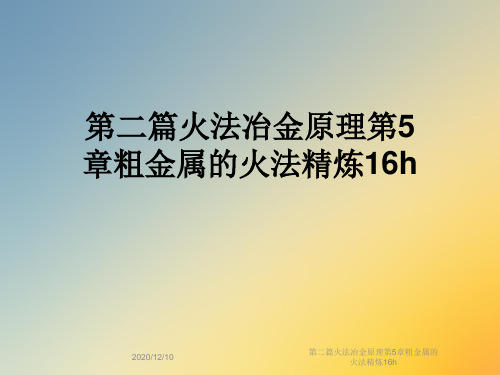
5.2.2 金属熔体中元素氧化反应的标准吉布斯自 由能变化
◆ 在氧化精炼条件下,杂质元素及氧都是作为溶质处于主金 属的熔体(溶液)中;
◆ 在研究熔体(溶液)中的化学反应时,其溶质的标准态不 一定采用纯物质;
◆ 为研究熔体中化学反应的热力学,须计算在指定标准状态 下溶质氧化反应的标准吉布斯自由能变化rGθ: [A] + [O] = AO [A],[O] ——金属熔体中的A和氧
注:表中 [ ] 表示溶于主金属中物质,如 [A] 表示溶于金属中的杂质A; ( ) 表示熔渣形态,如 (AOn) 表示熔渣中的AOn。
第二篇火法冶金原理第5章粗金属的 火法精炼16h
5.2 氧化精炼
5.2.1 金属熔体中杂质元素[A]氧化 反应的机制
5.2.2 金属熔体中元素氧化反应的标 准吉布斯自由能变化
第二篇火法冶金原理第5章粗金属的 火法精炼16h
第二篇火法冶金原理第5章粗金属的 火法精炼16h
◆ 在给定的标准状态下, rGθ–T 线位于主金属氧化物的 rGθ–T 线以下的元素,都能被主金属氧化物氧化。 如铁液中的杂质Al、Ti、Mn、Si等。
◆ 在生成的氧化物均为纯物质(活度为1)的情况下,铁液 中rGθ–T 线位置愈低的元素愈易被氧化除去; ✓ 当有多种杂质同时存在时,则位置低者将优先氧化;
◇ 利用杂质和主金属蒸气压的不同,因而粗金
属蒸发过程中,其易蒸发的组份将主要进入
气相,与难蒸发组分分离——蒸馏精炼。
第二篇火法冶金原理第5章粗金属的 火法精炼16h
精炼方法物理变化
蒸馏精炼
物理变化
氧化、硫化、氯化精炼
化学变化
添加碱金属或碱土金属化合物的精炼
化学变化
利用热离解、歧化反应等特殊高温化学反 应的精炼
粗铅初步火法精炼 ppt课件

粗铅的冶炼方式介绍
—铅冶金—
ห้องสมุดไป่ตู้
粗铅精炼的方法有两类,第一类为火法精炼,第二类为先用火法除去铜
与锡后,再铸成阳极板进行电解精炼。目前世界上火法精炼的生产能力约占 80%。采用电解精炼的国家主要有中国、日本、加拿大等国。我国大多数企 业粗铅的处理均采用电解法精炼。火法精炼是利用杂质金属与主金属(铅) 在高温熔体中物理性质或化学性质方面的差异,形成与熔融主金属不同的新 相(如精炼渣),并将杂质富集于其中,从而达到精炼的目的。
铅冶金就是利用煤气用富氧燃烧在高温下利用无烟煤把金属铅锑从它们的氧化物还原出来其脉石成分与添加的熔剂na2co3造渣从而与还原出来的金属铅锑等分离产出的冰铜中有部分元素以氧化物和硫化物形态存在在高温下配入还原剂熔剂使其中的部分氧化物被还原成金属fe与加入的熔剂组成二元系的渣fe被除去
—铅冶金—
粗铅的火法精炼
a、熔析作业温度通常在340℃以上,铜在铅液中 的溶解度大于0.06%;
b、含铜熔析渣的上浮取决于铅液的粘度,铅液 温度降低则粘度增大,铜渣细粒不易上浮。
在熔析过程中,几乎所有的铁、硫(呈铁、铜及 铅的硫化物形态)以及难熔的镍、钴、铜、铁的砷化 物及锑化物都被除去;同时贵金属的一部分也进入熔 析渣。
而发生以下反应:
[PbS]+2[Cu]=[Pb]+Cu2S Cu2S比铅的比重小,且在作业温度下不溶于铅水,因此,形成的固体硫化渣 浮在铅液面上。最后铅液中残留的铜一般为0.001~0.002%。 加硫除铜的硫化剂一般采用硫磺。加入量按形成Cu2S时所需的硫计算,并过 量20-30%。加硫作业温度对除铜程度有重大影响,铅液温度越低,除铜进行 得越完全,一般工厂都是在330-340℃范围内。加完硫磺后, 应迅速将铅液温 度升至450-480℃,大约搅拌40分钟以后,待硫磺渣变得疏松,呈棕黑色时, 表示反应到达终点,则停止搅拌进行捞渣,此种浮渣由于含铜低,只约2-3%, 而铅高达95%,因此返回熔析过程。加硫除铜后铅含铜可降至0.001-0.002%, 送去下一步电解精炼。
第6章 火法精炼反应

先同铁结合,然后FeO扩散到金属熔池内部。
(FeO)=[O]+[Fe]
C、Si、Mn、P等同[O]反应
[O] + [Mn] = (MnO) 2[O] + [Si] = (SiO2) 5[O] + 2[P] = (P2O5) [O] + [C] = {CO} 2[O] + [C] = {CO2}
[C]
6.2.2 金属熔体中元素氧化反应种类 直接氧化在氧流-金属表面处进行
氧流同熔池作用区的表面; 悬浮于作用区的金属液滴的表面;
作用区周围的氧气泡的表面上;
凡是氧气能直接同金属液接触的表面。 {O2} + 2[Fe] = 2(FeO) {O2} + 2[Mn] = 2(MnO)
{O2} + [Si] = (SiO2)
在这些炼钢方法的工艺中,虽然炼钢的方法和操作在不同程度上
有所区别,但是钢 —渣间平衡的基本原理却是相同的。使用纯氧精 炼不会改变炼钢过程的基本反应和其平衡状态,仅是反应的动力学
上有变化。由于熔池内出现了强烈的搅拌,促使金属—熔渣体系趋
近于平衡状态,这使热力学的平衡计算在炼钢中有重大意义。
6.2.1 氧化精炼介绍
第六章 火法精炼反应
6.1 概述 6.2 氧化精炼 6.3 硫化精炼
6.4 熔析与凝析精炼
6.1 概 述
6.1.1 火法精炼的目的
6.1.2 火法精炼的基本原理
6.1.3 火法精炼的基本步骤
6.1.4 火法精炼的基本体系
6.1.5 火法精炼方法
6.1.1 火法精炼的目的
还原熔炼反应将矿石还原获得粗金属,而粗金属还需要通过进一 步精炼,使其中超过产品金属允许含量的元素及杂质分离除去才能成
炉炼钢是从氧枪或喷嘴吹入的氧气,电炉炼钢则是吸入
有色冶金原理第六章_粗金属火法精炼

熔体中Zn的平衡摩尔分数为:
x Zn 3
3.0 10
2.4 103
4 2
2.3 11
2
3
0.0156
残留Zn量近似为: 0.0156 4.789 65.4 4.886
与Ag发生反应的Zn量为:
0.98 7.775 3 65.4 6.927 2 107 .9
Kg
Kg
消耗的总Zn量为: 4.886 6.927 11.81 Kg 实际生产中,由于达不到平衡以及银锌化 合物活度由于渣壳中铅的存在而小于1, 锌的需要量大于上述计算值。
4 区域精炼
第六章
1 概述
粗金属的火法精炼
2 熔析精炼
3 萃取精炼 4 区域精炼 5 金属的蒸馏过程 6 氧化精炼 7 硫化精炼
1 概述
粗金属火法精炼的目的: ●得到纯金属; ●得到杂质含量在允许范围内的产品; ●提取金属中无害的、但本身具有使用价值的杂质。 步骤: ①使均匀的熔融粗金属中产生多相体系 (如:金属-渣,金属-金属,金属-气体)。 ②将上述产生的各两相体系用物理方法分离。 精炼的产物分为三类: ●金属-渣系; ●金属-金属系; ●金属-气体系。 某些情况下,上述两类可能同时存在。
②结晶。将粗金属缓慢冷却到一定温度,熔体中某成分由 于溶解度减小,而成固相析出,其余熔体仍保持在液态, 从而将金属与杂质分离。 也有这种情况,在冷却粗金属熔体时,并不出现固体,而 是出现另一独立的液相,与原来的熔体分层。
2.4 粗金属熔析精炼的基础
状态图。
例题:铅精炼的撇渣法除铜。 如图所示,体系有一个低熔点共晶,含99%以上的Pb以液 态与固体纯Cu相平衡。富Cu渣浮于Pb水表面被除去。
- 1、下载文档前请自行甄别文档内容的完整性,平台不提供额外的编辑、内容补充、找答案等附加服务。
- 2、"仅部分预览"的文档,不可在线预览部分如存在完整性等问题,可反馈申请退款(可完整预览的文档不适用该条件!)。
- 3、如文档侵犯您的权益,请联系客服反馈,我们会尽快为您处理(人工客服工作时间:9:00-18:30)。
六、熔析过程的主要影响因素 温度 过程温度愈按近共晶温度,提纯效果愈好。 过程温度愈按近共晶温度,提纯效果愈好。 粗金属成份 粗金属中某些其他杂质的存在, 粗金属中某些其他杂质的存在,可能形成溶 解度更小的化合物,提高精炼效果。 解度更小的化合物,提高精炼效果。 粗铅熔析除铜时,铅中的As Sb、Sn能 As、 如:粗铅熔析除铜时,铅中的As、Sb、Sn能 与铜形成难溶化合物, 与铜形成难溶化合物,导致铜在铅的溶解度 降低( 10降低(图10-9)。
K0 可以大于 1, 也可以小于 1;一 20; 般为10 般为10-6~20; 愈接近于1 K0 愈接近于1, 提纯效果愈差; 提纯效果愈差; 对于杂质含量 极小的体系, 极小的体系, K0 可视为常数。 可视为常数。←→ 液相线和固相线均 为直线。 为直线。
三、正常凝固(定向凝固、普通凝固) 正常凝固(定向凝固、普通凝固) 金属锭料全部熔化后, 金属锭料全部熔化后,由一端逐渐向另一 端慢慢凝固的过程。 端慢慢凝固的过程。 应用:从熔体中拉制单晶。 应用:从熔体中拉制单晶。
二、火法精炼的基本原理 利用主金属与杂质的物理和化学性质的差异 形成与主金属不同的新相,将杂质富集于其中; 形成与主金属不同的新相,将杂质富集于其中; 或者:将主金属全部转移至新相, 或者:将主金属全部转移至新相,而使杂质残留 下来。 下来。 三、火法精炼的基本步骤 用多种(化学的或物理的) 用多种(化学的或物理的)方法使均匀的粗金 属体系变为多相(一般为二相)体系; 属体系变为多相(一般为二相)体系; 用各种方法将不同的相分开, 用各种方法将不同的相分开,实现主体金属与 杂质的分离。 杂质的分离。
已知:γ
0 Zn
= 11 γ ,
0 Ag
= 2.3
0 ∆G 773 = −127612
2 Ag ( l ) + 3Zn ( l ) = Ag 2 Zn3
吨粗Pb为计算基础。 以1吨粗Pb为计算基础。 吨粗Pb为计算基础 7 Kmol 初始组成: 初始组成: Ag:.775 =0.072 107.9 992.225 Pb: =4.789 Kmol 207.2
7.3 萃取精炼 7.3.1 概念
萃取精炼:在一定温度下, 萃取精炼:在一定温度下,在熔融粗金属中加入附加 物,附加物与粗金属内杂质生成不溶解于熔体的化合 物而析出,从而达到精炼的目的。 物而析出,从而达到精炼的目的。
7.3.2 例题
铅水加锌除银的帕克斯法。 铅水加锌除银的帕克斯法。 一无Zn粗 水 每吨含7.775Kg的Ag,在773K时加 一无 粗Pb水,每吨含 的 , 时加 Zn除Ag。假设其反应产物是纯 2Zn3,计算除去 计算除去98 除 。假设其反应产物是纯Ag 所需添加的Zn量 %的Ag,每吨粗 所需添加的 量? ,每吨粗Pb所需添加的
三、熔析精炼的类型
1、冷却凝析精炼 将具有二元共晶型的液态粗金属熔体缓慢冷却到稍 高于共晶温度,杂质以固体(或固溶体) 高于共晶温度,杂质以固体(或固溶体)析出并浮 于金属熔体的表面上,使固相与液相分离。 于金属熔体的表面上,使固相与液相分离。 2、加热熔析精炼 将具有二元共晶型的固态粗金属加热到稍高于共晶 温度,杂质含量接近共晶组成的熔体, 温度,杂质含量接近共晶组成的熔体,沿倾斜的炉 底流出,而杂质仍留在固相中。 底流出,而杂质仍留在固相中。
7
7
7.2 熔析与凝析精炼
一、基本原理 粗金属在熔化(或凝固) 粗金属在熔化(或凝固)的过程中杂质在固相和液相的平 衡浓度不同。 衡浓度不同。 从均匀的熔体中开始凝固时,首先析出不同组成的固体。 从均匀的熔体中开始凝固时,首先析出不同组成的固体。
二、熔析精炼的基本步骤
在均匀的合金中产生多相体系(液体+液体、 在均匀的合金中产生多相体系(液体+液体、液 固体); 体+固体); 产生多相体系可以用加热、缓冷等方法。 产生多相体系可以用加热、缓冷等方法。 所产生的两相按比重不同而进行分层。 所产生的两相按比重不同而进行分层。 如果分层为二液相则分别放出; → 如果分层为二液相则分别放出; → 如果分层为固体和液体,则利用漏勺、捞渣 如果分层为固体和液体,则利用漏勺、 器等使两相分离; 器等使两相分离; 或者使液体沿着炉底斜坡徘出炉外, → 或者使液体沿着炉底斜坡徘出炉外,而固体 则仍留于炉底上,从而使二相分离( 则仍留于炉底上,从而使二相分离(如粗锡熔析 除铁)。 除铁)。
五、粗铅熔析除铜
将含铜( 0.06%)的熔融铅缓慢降温, 将含铜(> 0.06%)的熔融铅缓慢降温,并保 K( ℃) 持在稍高于 599 K(326 ℃)的共晶温度 330~ ℃), ),铜以固体浮渣的形式浮于 (330~350 ℃),铜以固体浮渣的形式浮于 铅熔体表面而与之分离; 铅熔体表面而与之分离; 粗铅熔析除铜的理论极限是Pb Cu共晶组成 Pb–Cu共晶组成, 粗铅熔析除铜的理论极限是Pb Cu共晶组成, 0.06%; 即0.06%; 通过共存元素(As、Sb)的作用, 通过共存元素(As、Sb)的作用,实际脱铜 极限可降至0.02 0.03%; 0.02~ 极限可降至0.02~0.03%; Fe、Ni、Co、 等也一并被除去; Fe、Ni、Co、S 等也一并被除去; 熔析除铜设备:铸铁精炼锅。 熔析除铜设备:铸铁精炼锅。
第七章
粗金属的火法精炼
1 概述 2 熔析与凝析精炼 3 萃取精炼 4 区域精炼 5 蒸馏与升华精炼
7.1 概述
一、火法精炼的目的 除去有害杂质,生产出具有一定纯度的金属; 除去有害杂质,生产出具有一定纯度的金属; 当金属中的杂质含量超过一定限度时, → 当金属中的杂质含量超过一定限度时,其物 化学和机械性能会发生变化。 理、化学和机械性能会发生变化。 生产出含有各种规定量的合金元素的金属, 生产出含有各种规定量的合金元素的金属,使 其具有一定的物理、化学和机械性能; 其具有一定的物理、化学和机械性能; 如合金钢的生产。 如合金钢的生产。 回收其中具有很高经济价值的稀贵金属“ 回收其中具有很高经济价值的稀贵金属“杂 质”。 粗铅、粗铜中的金、银及其他稀贵金属。 如:粗铅、粗铜中的金、银及其他稀贵金属。
7.4 区域精炼
一、化学偏析现象 在一个温度分布不均 匀的体系中, 匀的体系中,当连续 降温时, 降温时,先凝固部分 与后凝固部分有不同 的组成。 的组成。 二、平衡分配系数 (分配 分配 分凝比) 比、分凝比 在固–液平衡体系中 液平衡体系中, 在固 液平衡体系中, 溶质(杂质) 溶质(杂质)在固相 的浓度 Cs 与其在液 之比: 相的浓度 Cl 之比:
五、有效分配系数
之间; 有效分配系数 K 界于 K0 和 1 之间; 实际区域精炼的效果低于平衡条件下区域精炼的效果。 实际区域精炼的效果低于平衡条件下区域精炼的效果。
六、区域精炼
图 9-3
图 9-4
区域精炼的锭料分为三个区域: 区域精炼的锭料分为三个区域: 起始区或纯化区; → BE 段:起始区或纯化区; 水平区或致匀区; → EE' 段:水平区或致匀区; → E'g 段:最终区或杂质富集 区。 起始区和水平区的杂质浓度分布由上述方程描述; 起始区和水平区的杂质浓度分布由上述方程描述; 最终区的熔体凝固过程属于正常凝固; 最终区的熔体凝固过程属于正常凝固; 其杂质分布与正常凝固中杂质的分布规律相同。 其杂质分布与正常凝固中杂质的分布规律相同。 区域精炼法的精炼效果不及正常凝固法。 区域精炼法的精炼效果不及正常凝固法。
0 ∆G773 = −127612 = − RT ln K
K = 4.17 × 10 =
8
a Ag 2 Zn3
2 3 a Ag a Zn
2 2 3 3 x Ag γ Ag x Znγ Zn = 2.4 × 10 −9
除去98%的银,则最终残存于精炼铅中的银为: 除去98%的银,则最终残存于精炼铅中的银为: 98 (1 − 0.98) × 0.072 = 1.44 × 10 −3 Kmol 残存银的摩尔分数是: 残存银的摩尔分数是: x Ag 1.44 × 10 −3 = = 3.0 × 10 −4 4.789 + 1.44 × 10 −3
四、熔析精炼的应用
1、熔析精炼对二元系的要求 杂质与主体金属熔点相差较大; → 杂质与主体金属熔点相差较大; → 共晶点(三相点)的组成应非常靠近主金属一侧; 共晶点(三相点)的组成应非常靠近主金属一侧; 共存相应该易于分离。 → 共存相应该易于分离。 固相的比重差应较大, 液–固相的比重差应较大, 固相的比重差应较大 液相的粘度较小。 液相的粘度较小。 2、适宜采用熔析精炼的二元系 Pb-Cu系 粗铅除铜)、Pb-Ag系 粗铅除银)、 )、Pb Pb-Cu系(粗铅除铜)、Pb-Ag系(粗铅除银)、 Sn-Pb系(粗锡除铅)、Sn-Fe系(粗锡除铁)、 Sn-Pb系 粗锡除铅)、Sn-Fe系 粗锡除铁)、 )、Sn Zn-Pb系 粗锌除铅)、Zn-Fe系 粗锌除铁)。 )、Zn Zn-Pb系(粗锌除铅)、Zn-Fe系(粗锌除铁)。
四、火法精炼的基本体系 利用主金属与杂质的物理和化学性质的差异
五、火法精炼方法 基于杂质与主金属化学性质的不同, 化学法 基于杂质与主金属化学性质的不同,加入 某种反应剂使之形成某种难溶于金属的化合物析出 或造渣。 或造渣。 物理法 基于在两相平衡时杂质和主金属在两相间 分配比的不同。 分配比的不同。 利用粗金属凝固或熔化过程中, → 利用粗金属凝固或熔化过程中,粗金属中的杂 质和主金属在液–固两相间分配比的不同 固两相间分配比的不同——熔析 质和主金属在液 固两相间分配比的不同 熔析 精炼、区域精炼(区域熔炼)。 精炼、区域精炼(区域熔炼)。 利用杂质和主金属蒸气压的不同, → 利用杂质和主金属蒸气压的不同,因而粗金属 蒸发过程中,其易蒸发的组份将主要进入气相,与 蒸发过程中,其易蒸发的组份将主要进入气相, 难蒸发组分分离——蒸馏精炼、升华精炼。 蒸馏精炼、 难蒸发组分分离 蒸馏精炼 升华精炼。