第四讲物料循环燃烧系统-循环流化床锅炉
循环流化床锅炉原理
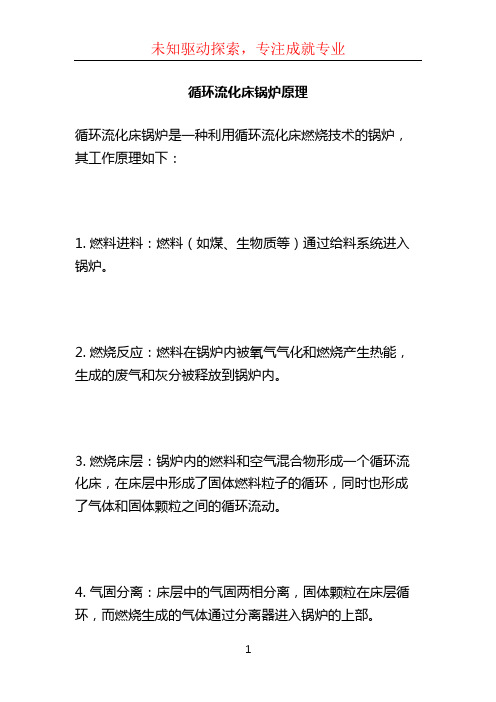
循环流化床锅炉原理
循环流化床锅炉是一种利用循环流化床燃烧技术的锅炉,其工作原理如下:
1. 燃料进料:燃料(如煤、生物质等)通过给料系统进入锅炉。
2. 燃烧反应:燃料在锅炉内被氧气气化和燃烧产生热能,生成的废气和灰分被释放到锅炉内。
3. 燃烧床层:锅炉内的燃料和空气混合物形成一个循环流化床,在床层中形成了固体燃料粒子的循环,同时也形成了气体和固体颗粒之间的循环流动。
4. 气固分离:床层中的气固两相分离,固体颗粒在床层循环,而燃烧生成的气体通过分离器进入锅炉的上部。
5. 固体回流:分离器中的固体颗粒被分离后,一部分被回流到床层继续燃烧,另一部分则通过排渣系统排出锅炉。
6. 热交换:燃烧生成的高温烟气在锅炉的热交换器中与水进行换热,产生蒸汽或热水。
7. 废气处理:通过合适的废气处理系统,对燃烧废气进行脱硫、脱硝和除尘等处理,降低废气对环境的污染。
总体来说,循环流化床锅炉通过循环流化床的形成,实现了燃料和空气的良好混合,提高了燃烧效率;同时通过固体的循环回流,在保持稳定燃烧的同时,降低了燃料的耗损和废渣产生量,提高了锅炉的可持续性和经济性。
循环流化床锅炉物料循环燃烧系统

循环流化床锅炉物料循环燃烧系统引言循环流化床锅炉是一种常见的锅炉类型,其物料循环燃烧系统被广泛应用于工业领域。
该系统的设计和优化对于提高能源利用效率、降低污染物排放以及减少能源消耗具有重要意义。
本文将介绍循环流化床锅炉物料循环燃烧系统的基本原理、组成部分以及工作过程。
系统原理循环流化床锅炉物料循环燃烧系统基于循环流化床技术,其原理是将物料(如煤粉、燃气等)与气体(如空气、蒸汽等)混合进入锅炉炉膛,在一定的温度和压力条件下进行反应燃烧。
循环流化床通过气体的上升和物料的循环降低了燃烧过程中的温度梯度,提高了燃烧效率和热交换效率。
系统组成部分循环流化床锅炉物料循环燃烧系统主要由以下组成部分组成:1.锅炉炉膛:用于燃烧物料的空间。
炉膛通常采用圆形或方形的结构,具有适当的尺寸和容量。
2.循环系统:包括循环器、循环气管和物料循环管。
循环系统中的循环器通过调节循环气流的速度和方向,控制物料在循环管中的循环速度和循环比例。
3.燃烧系统:包括燃料供给系统、燃烧室和燃烧控制系统。
燃料供给系统用于将燃料送入燃烧室,燃烧室通过控制燃烧过程中的气流和温度,实现物料的完全燃烧。
4.热交换系统:包括烟气余热回收器和空气预热器。
烟气余热回收器用于回收燃烧过程中产生的热能,提高能源利用效率。
空气预热器则通过预热进入锅炉的空气,降低了燃料的燃烧温度,减少了污染物的排放。
工作过程循环流化床锅炉物料循环燃烧系统的工作过程可以分为以下几个步骤:1.物料供给:燃料经过处理后,通过燃料供给系统被输送到燃烧室中。
在物料供给的过程中,可以根据需要进行添加辅助燃料或调节燃料的供给量。
2.循环循环:在循环系统的控制下,物料和气体经过循环管进入循环器,形成循环流化床。
在循环过程中,物料在高温下发生燃烧反应,释放出热能。
3.燃烧反应:在循环流化床中,物料与气体发生燃烧反应。
燃料的燃烧过程可以分为物理燃烧和化学燃烧两个阶段,通过控制燃烧过程中的气流和温度,实现物料的完全燃烧。
循环流化床锅炉详细资料

循环流化床锅炉详细资料
包括原理,特点,结构,应用等
一、循环流化床锅炉的原理
1、燃烧:循环流化床锅炉可以使用各种燃料,包括煤、油、核燃料等,由于锅炉的可变燃烧温度,可以在锅炉内部实现完全燃烧,低温燃烧也可以得到满足,从而节约燃料。
2、循环:循环流化床锅炉具有高度动态的热循环。
由于内筒内的安全温度较低,减少了空气中的静电压降,大大降低了热循环的效率,即使在负荷变化很大的情况下也能够稳定地配电。
3、流化,循环流化床锅炉可以将气流化技术应用于锅炉炉膛内的燃烧,其燃烧过程就像一个流化器,可以将气体和固体进行有效的混合,使燃烧更加均匀。
4、辅助:循环流化床锅炉具有良好的低排放和低噪音的特点,并能够根据负荷的变化而改变燃烧温度和锅炉运行模式,最大限度地减少烟气排放,提高热效率,节能降耗。
循环流化床锅炉的工作原理
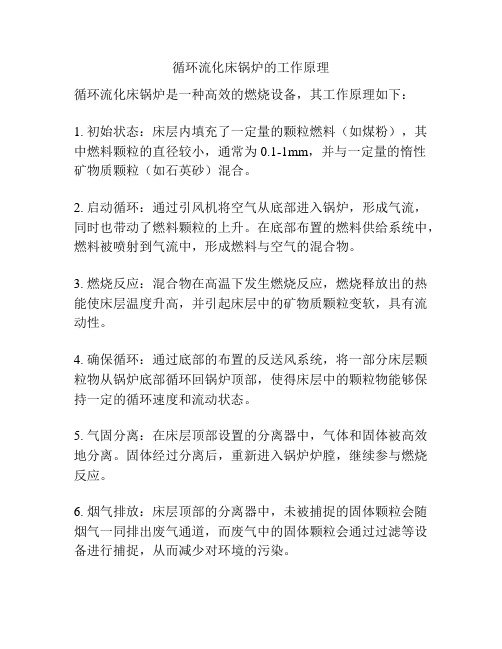
循环流化床锅炉的工作原理
循环流化床锅炉是一种高效的燃烧设备,其工作原理如下:
1. 初始状态:床层内填充了一定量的颗粒燃料(如煤粉),其中燃料颗粒的直径较小,通常为0.1-1mm,并与一定量的惰性矿物质颗粒(如石英砂)混合。
2. 启动循环:通过引风机将空气从底部进入锅炉,形成气流,同时也带动了燃料颗粒的上升。
在底部布置的燃料供给系统中,燃料被喷射到气流中,形成燃料与空气的混合物。
3. 燃烧反应:混合物在高温下发生燃烧反应,燃烧释放出的热能使床层温度升高,并引起床层中的矿物质颗粒变软,具有流动性。
4. 确保循环:通过底部的布置的反送风系统,将一部分床层颗粒物从锅炉底部循环回锅炉顶部,使得床层中的颗粒物能够保持一定的循环速度和流动状态。
5. 气固分离:在床层顶部设置的分离器中,气体和固体被高效地分离。
固体经过分离后,重新进入锅炉炉膛,继续参与燃烧反应。
6. 烟气排放:床层顶部的分离器中,未被捕捉的固体颗粒会随烟气一同排出废气通道,而废气中的固体颗粒会通过过滤等设备进行捕捉,从而减少对环境的污染。
通过上述工作原理,循环流化床锅炉可以实现燃料的高效燃烧和热能的充分利用,同时也能够降低氮氧化物的排放量,保护环境。
循环流化床锅炉设备及系统课件

(1)圆形炉膛 (2)下圆上方形炉膛 结构特点
n 圆形部分不设水冷壁,完全由耐火砖砌成 优点:防磨、压火保温 缺点:启动t长、耐火材料对温升速度要求严格
n 上部炉膛悬吊,下部支承→上下结合处不易密封
2020/5/15
一、燃烧室(炉膛)结构
1. 炉膛结构形式
(3)立式方形炉膛
结构特点:横截面矩形,四周由膜式水 冷壁围成,常与一次风室、布风装置一 体悬吊,可上下自由膨胀
优点:密封好,水冷壁布置方便,锅炉 体积小,启动速度快,工艺制造简单
缺点:水冷壁磨损大→水冷壁内侧衬耐 磨耐火材料
发展趋势:H、L/W↑,A/V↓;考虑给 煤点位置以便给煤分布均匀;经济角度 考量,H受限
(1)制造材料:耐热铸铁、耐热不锈钢(抗磨损性能差)
(2)结构型式(小孔径、大孔径、定向,S,T型)
有帽头特点:阻力大,长期运行后帽沿底易卡杂物, 不易清除、不易排渣,需停炉清理;布风均匀性好
无帽头特点:阻力小,制造简单,气流分配性能差 定向风帽特点:布风均匀,大开孔可防止堵塞,定
1)能均匀、密集分布气流,避免死区 2)出口气流动能大,产生强烈扰动、混合 3)阻力损失小,降低风机能耗 4)有足够强度和刚度,压火时防止布风板
受热变形,风帽不烧损,检修清理方便 5)结构合理,防止床料流入风室
2020/5/15
一、布风装置本体结构
1. 布风板
(1)主要功能
支撑风帽和床料 对气流产生阻力,使流化空气均匀分布,
2020/5/15
2020/5/15
物料循环系统
2020/5/15
二、燃烧室(炉膛)开口
5. 炉膛出口
采用(具有气垫的)直角转弯型式炉膛出口,可增加对固体颗粒的分 离,增加床内εp,发生内循环,增加停留t
循环流化床锅炉工作原理
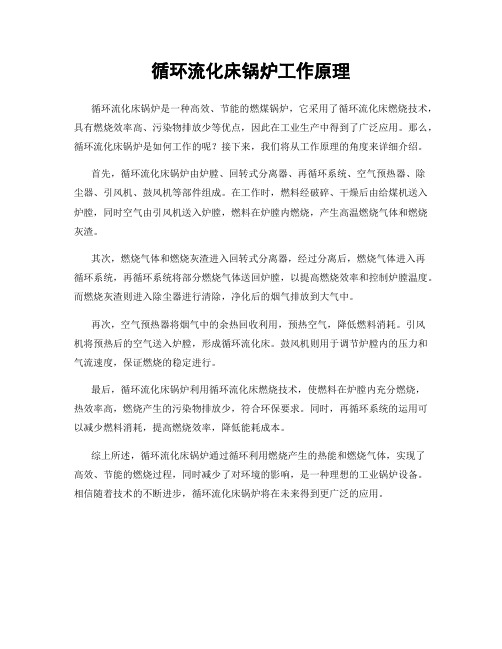
循环流化床锅炉工作原理
循环流化床锅炉是一种高效、节能的燃煤锅炉,它采用了循环流化床燃烧技术,具有燃烧效率高、污染物排放少等优点,因此在工业生产中得到了广泛应用。
那么,循环流化床锅炉是如何工作的呢?接下来,我们将从工作原理的角度来详细介绍。
首先,循环流化床锅炉由炉膛、回转式分离器、再循环系统、空气预热器、除
尘器、引风机、鼓风机等部件组成。
在工作时,燃料经破碎、干燥后由给煤机送入炉膛,同时空气由引风机送入炉膛,燃料在炉膛内燃烧,产生高温燃烧气体和燃烧灰渣。
其次,燃烧气体和燃烧灰渣进入回转式分离器,经过分离后,燃烧气体进入再
循环系统,再循环系统将部分燃烧气体送回炉膛,以提高燃烧效率和控制炉膛温度。
而燃烧灰渣则进入除尘器进行清除,净化后的烟气排放到大气中。
再次,空气预热器将烟气中的余热回收利用,预热空气,降低燃料消耗。
引风
机将预热后的空气送入炉膛,形成循环流化床。
鼓风机则用于调节炉膛内的压力和气流速度,保证燃烧的稳定进行。
最后,循环流化床锅炉利用循环流化床燃烧技术,使燃料在炉膛内充分燃烧,
热效率高,燃烧产生的污染物排放少,符合环保要求。
同时,再循环系统的运用可以减少燃料消耗,提高燃烧效率,降低能耗成本。
综上所述,循环流化床锅炉通过循环利用燃烧产生的热能和燃烧气体,实现了
高效、节能的燃烧过程,同时减少了对环境的影响,是一种理想的工业锅炉设备。
相信随着技术的不断进步,循环流化床锅炉将在未来得到更广泛的应用。
循环流化床锅炉设备及运行物料循环燃烧系统

第四节 固体物料回送装置
重点掌握
• 1.物料循环回路的压力平衡关系 • 2.回料阀的结构、原理 • 3.自平衡回料原理
1.物料循环回路的压力平衡关系
思考:
物料怎样实现 从压力低的分 离器流向压力 高的炉膛?
P=0
P<0
P>0 P>0 循环回路压力关系
哪种方案可行?
1:直接回料
2:密封阀回料
“阀”的概念——回料
1.作用
• 把从炉膛飞出的固体 颗粒从烟气中分离出 来
• 实现了燃料循环燃烧,提 高了燃烧效率
• 实现了脱硫剂循环利用, 节约了脱硫剂用量
• 保留足量的固体颗粒,顺 利完成传热
2.分类
• (1)按分离原理分类
–离心分离 –惯性分离 –组合分离
• (2)按进口温度分类
–高温分离 –中温分离 –低温分离
• 结构、原理与运行
• 重点要掌握:
1. 影响分离效率的因素; 2. 自平衡回料阀的“自平衡”原理。
课后思考题
• 1. 物料为什么能从分离器下部的 低压端流向炉膛的高压端?
• 2. 影响旋风分离器分离效率的因 素有哪些?
• 3. 高温绝热型、水(汽)冷型、 方型分离器各有什么优缺点?
• 4. 锅炉运行时,U型阀的风量要 经常调整吗?为什么?
• 进口速度 • 筒体直径 • 颗粒浓度 • 中心筒插入高度
高温绝热旋风分离器
• 优缺点 • 优点
– 结构简单 – 分离效率高
• 缺点
– 热惯性大,启动时间长 – 易结焦 – 体积庞大,布置困难
为克服上述缺点,冷却型高温旋风 分离器诞生了。
汽(水)冷分离器
• 结构特点
– 汽冷(水冷)
循环流化床锅炉燃烧方式
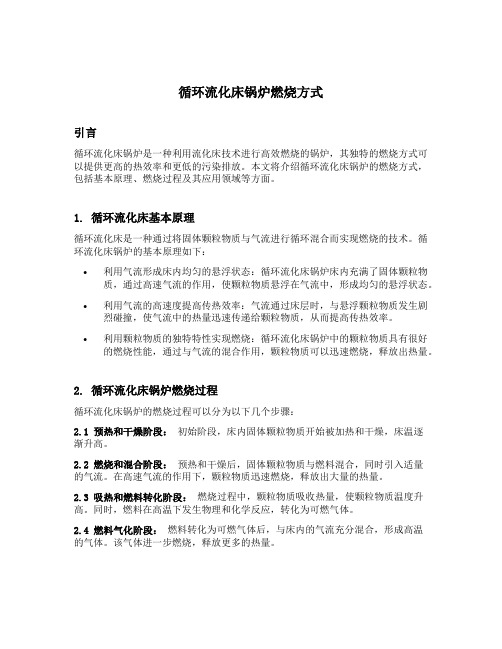
循环流化床锅炉燃烧方式引言循环流化床锅炉是一种利用流化床技术进行高效燃烧的锅炉,其独特的燃烧方式可以提供更高的热效率和更低的污染排放。
本文将介绍循环流化床锅炉的燃烧方式,包括基本原理、燃烧过程及其应用领域等方面。
1. 循环流化床基本原理循环流化床是一种通过将固体颗粒物质与气流进行循环混合而实现燃烧的技术。
循环流化床锅炉的基本原理如下:•利用气流形成床内均匀的悬浮状态:循环流化床锅炉床内充满了固体颗粒物质,通过高速气流的作用,使颗粒物质悬浮在气流中,形成均匀的悬浮状态。
•利用气流的高速度提高传热效率:气流通过床层时,与悬浮颗粒物质发生剧烈碰撞,使气流中的热量迅速传递给颗粒物质,从而提高传热效率。
•利用颗粒物质的独特特性实现燃烧:循环流化床锅炉中的颗粒物质具有很好的燃烧性能,通过与气流的混合作用,颗粒物质可以迅速燃烧,释放出热量。
2. 循环流化床锅炉燃烧过程循环流化床锅炉的燃烧过程可以分为以下几个步骤:2.1 预热和干燥阶段:初始阶段,床内固体颗粒物质开始被加热和干燥,床温逐渐升高。
2.2 燃烧和混合阶段:预热和干燥后,固体颗粒物质与燃料混合,同时引入适量的气流。
在高速气流的作用下,颗粒物质迅速燃烧,释放出大量的热量。
2.3 吸热和燃料转化阶段:燃烧过程中,颗粒物质吸收热量,使颗粒物质温度升高。
同时,燃料在高温下发生物理和化学反应,转化为可燃气体。
2.4 燃料气化阶段:燃料转化为可燃气体后,与床内的气流充分混合,形成高温的气体。
该气体进一步燃烧,释放更多的热量。
2.5 传热和排烟阶段:燃烧产生的热量通过颗粒物质与气流的热交换,传递给锅炉管道中的工质(通常为水蒸气)。
同时,废气中的污染物通过烟气净化设备进行处理,以降低污染物排放。
3. 循环流化床锅炉燃烧方式的优势循环流化床锅炉的燃烧方式具有以下优势:•高热效率:循环流化床锅炉通过气流与颗粒物质的循环混合,使热量更均匀地传递给工质,提高了热效率。
•低排放:循环流化床锅炉通过燃料的充分燃烧和烟气净化设备的处理,减少了二氧化硫、氮氧化物等有害气体的排放。
- 1、下载文档前请自行甄别文档内容的完整性,平台不提供额外的编辑、内容补充、找答案等附加服务。
- 2、"仅部分预览"的文档,不可在线预览部分如存在完整性等问题,可反馈申请退款(可完整预览的文档不适用该条件!)。
- 3、如文档侵犯您的权益,请联系客服反馈,我们会尽快为您处理(人工客服工作时间:9:00-18:30)。
HG风帽介绍
• 物料不会漏进风室; 罩体上孔径大 (22.5mm)使其 不易被颗粒堵塞.
布风板阻力的作用及要求
–布风板阻力越大,布风越 均匀
–布风板阻力应为床层阻力 的25%—30%才可维持床层 稳定运行
第二节 点火装置
一、点火过程
(1)床料加热
固定床点火 流化床点火
(2)试投燃料
间歇给煤
(3)过渡到正常运行
二、点火燃烧器
1.床上点火燃烧器 2.床下点火燃烧器
加热上表面
向下倾斜的启布置
HG点火装置
• 采用“床上+床下” 点火的联合启动 方式。
• 床下启动燃烧器 两只,床上距布 风板约3米处共布 置4只油枪(两侧 墙各2只)。
• 1.炉膛
–炉膛结构(膜式水冷壁、下部敷设耐 磨耐火材料)
图4-2
炉膛形状(矩形截面、下部收缩)
图4-4
锅炉大型化后炉膛的变化
2.布风装置
(1)风室
– 形状 – 等压风室、带均流板风室 – 水冷风室、非水冷风室
风室
(2)布风板及风 帽
–要求:保证床料 流化质量,使之 流化均匀、气泡 小、不留死角
第四讲物料循环燃 烧系统-循环流化床
锅炉
第4讲 物料循环燃烧系统
循环流化床锅炉本体结构(三维动画)
第一节 炉膛及布风装置 第二节 点火装置
• 目的
– 掌握炉膛、布风装置、点火装置的 结构与原理
• 重点
– 布风板、风帽、点火装置的结构和 原理
• 难点
– 布风板开孔率与流化质量的关系 – 床下点火燃烧器的配风
• 布风板型式:
HG水冷布风板
§水冷壁管146根中 的48根管拉稀成膜 式板,折向后墙; §焊接罩式风帽, 共同构成水冷布风 板; §布风板面积: 3160×13160mm2。
Back to 水循环
• 风帽型式
图4-6
图4-7
防止漏床料
方便排大渣
T形风帽
HG风帽介绍
• 直径:159mm • 布置间距: