金属塑性加工——轧制理论与工艺思考题
《材料加工成型原理》思考题参考答案
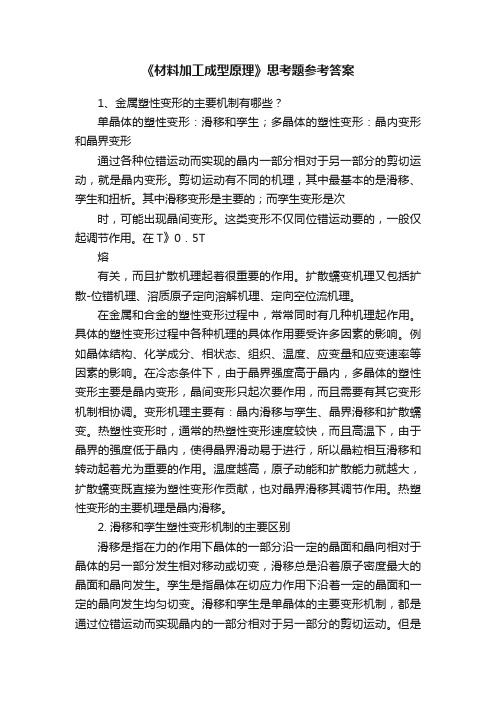
《材料加工成型原理》思考题参考答案1、金属塑性变形的主要机制有哪些?单晶体的塑性变形:滑移和孪生;多晶体的塑性变形:晶内变形和晶界变形通过各种位错运动而实现的晶内一部分相对于另一部分的剪切运动,就是晶内变形。
剪切运动有不同的机理,其中最基本的是滑移、孪生和扭析。
其中滑移变形是主要的;而孪生变形是次时,可能出现晶间变形。
这类变形不仅同位错运动要的,一般仅起调节作用。
在T》0.5T熔有关,而且扩散机理起着很重要的作用。
扩散蠕变机理又包括扩散-位错机理、溶质原子定向溶解机理、定向空位流机理。
在金属和合金的塑性变形过程中,常常同时有几种机理起作用。
具体的塑性变形过程中各种机理的具体作用要受许多因素的影响。
例如晶体结构、化学成分、相状态、组织、温度、应变量和应变速率等因素的影响。
在冷态条件下,由于晶界强度高于晶内,多晶体的塑性变形主要是晶内变形,晶间变形只起次要作用,而且需要有其它变形机制相协调。
变形机理主要有:晶内滑移与孪生、晶界滑移和扩散蠕变。
热塑性变形时,通常的热塑性变形速度较快,而且高温下,由于晶界的强度低于晶内,使得晶界滑动易于进行,所以晶粒相互滑移和转动起着尤为重要的作用。
温度越高,原子动能和扩散能力就越大,扩散蠕变既直接为塑性变形作贡献,也对晶界滑移其调节作用。
热塑性变形的主要机理是晶内滑移。
2. 滑移和孪生塑性变形机制的主要区别滑移是指在力的作用下晶体的一部分沿一定的晶面和晶向相对于晶体的另一部分发生相对移动或切变,滑移总是沿着原子密度最大的晶面和晶向发生。
孪生是指晶体在切应力作用下沿着一定的晶面和一定的晶向发生均匀切变。
滑移和孪生是单晶体的主要变形机制,都是通过位错运动而实现晶内的一部分相对于另一部分的剪切运动。
但是他们也明显的区别,如下:由孪生的变形过程可知,孪生所发生的切变均匀地波及整个孪生变形区,而滑移变形只集中在滑移面上,切变是不均匀的;孪生切变时原子移动的距离不是孪生方向原子间距的整数倍(而是几分之一原子间距),而滑移时原子移动的距离是滑移方向原子间距的整数倍;孪生变形后,孪晶面两边晶体位向不同,成镜像对称;而滑移时,滑移面两边晶体位向不变;由于孪生改变了晶体的取向,因此孪晶经抛光浸蚀后仍可观察到,而滑移所造成的台阶经抛光浸蚀后不会重现;孪生的临界分切应力要比滑移的临界分切应力大得多,常萌发于滑移受阻引起的局部应力集中区;孪生变形的速度极大,常引起冲击波,发出声响;滑移时全位错运动的结果,孪生是不全位错运动。
材料成形技术基础复习思考题-塑性成形部分-题
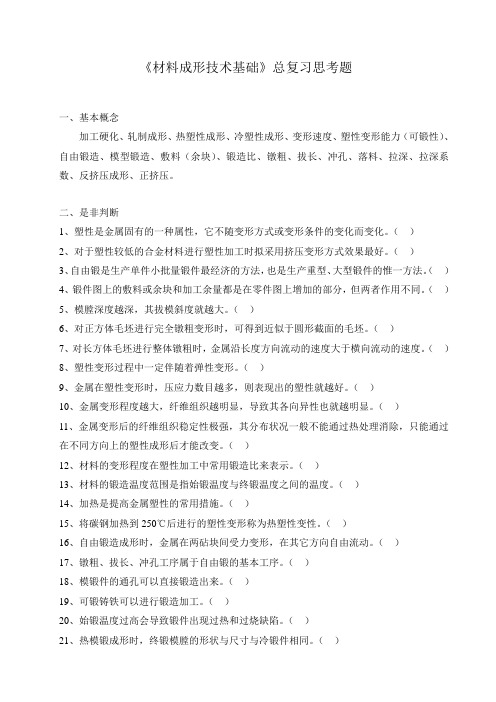
《材料成形技术基础》总复习思考题一、基本概念加工硬化、轧制成形、热塑性成形、冷塑性成形、变形速度、塑性变形能力(可锻性)、自由锻造、模型锻造、敷料(余块)、锻造比、镦粗、拔长、冲孔、落料、拉深、拉深系数、反挤压成形、正挤压。
二、是非判断1、塑性是金属固有的一种属性,它不随变形方式或变形条件的变化而变化。
()2、对于塑性较低的合金材料进行塑性加工时拟采用挤压变形方式效果最好。
()3、自由锻是生产单件小批量锻件最经济的方法,也是生产重型、大型锻件的惟一方法。
()4、锻件图上的敷料或余块和加工余量都是在零件图上增加的部分,但两者作用不同。
()5、模膛深度越深,其拔模斜度就越大。
()6、对正方体毛坯进行完全镦粗变形时,可得到近似于圆形截面的毛坯。
()7、对长方体毛坯进行整体镦粗时,金属沿长度方向流动的速度大于横向流动的速度。
()8、塑性变形过程中一定伴随着弹性变形。
()9、金属在塑性变形时,压应力数目越多,则表现出的塑性就越好。
()10、金属变形程度越大,纤维组织越明显,导致其各向异性也就越明显。
()11、金属变形后的纤维组织稳定性极强,其分布状况一般不能通过热处理消除,只能通过在不同方向上的塑性成形后才能改变。
()12、材料的变形程度在塑性加工中常用锻造比来表示。
()13、材料的锻造温度范围是指始锻温度与终锻温度之间的温度。
()14、加热是提高金属塑性的常用措施。
()15、将碳钢加热到250℃后进行的塑性变形称为热塑性变性。
()16、自由锻造成形时,金属在两砧块间受力变形,在其它方向自由流动。
()17、镦粗、拔长、冲孔工序属于自由锻的基本工序。
()18、模锻件的通孔可以直接锻造出来。
()19、可锻铸铁可以进行锻造加工。
()20、始锻温度过高会导致锻件出现过热和过烧缺陷。
()21、热模锻成形时,终锻模膛的形状与尺寸与冷锻件相同。
()22、金属的锻造性与材料的性能有关,而与变形的方式无关。
()23、模锻件的精度取决于终锻模膛的精度。
“金属塑性加工技术”复习思考题-教师用

《金属塑性加工技术》部分思考题(教师用)2、力学分析:(1)穿孔热挤压铜管的过程中,穿孔针的受力受热分析。
答:穿孔针在每一个挤压周期都要承受一次载荷和温度的剧烈交替。
穿孔时其整体受强烈的压应力作用;而外表与高温铜锭直接接触,温度急剧升高;同时受到金属流动产生的摩擦力作用;稳态挤压过程中,随动穿孔针的移动速度低于铜管轴向流动速度,因此外表面受到很高的轴向摩擦力作用,使整体受拉应力;同时外表温度升高,而内壁受水冷。
一个挤压道次结束后,又采用水冷方式对其外表面进行剧烈冷却。
在这种急冷急热的恶劣工作状态下,穿孔针极容易产生表面龟裂、变形、弯曲、拉毛、变细、断裂等缺陷,使用寿命很短。
可以通过加强穿孔针表面润滑及内孔冷却,缩短挤压锭长度或提高挤压速度,以及采用更耐高温的穿孔针材料等措施来提高穿孔针的使用寿命。
(2)游动芯头拉拔管材时芯头稳定的力学条件。
3、简答简析:(1)举例:复合成形技术(如铸轧、辊锻、铸挤等)(2)举例:短流程生产新技术(如铸轧法生产铜管、连续铸轧法生产铝带坯、铜带“连铸带坯+冷轧开坯”技术等)(3)举例:连续化生产技术(如连铸连轧、盘拉技术、联合拉拔等)(4)简析:反向挤压的特点(变形更均匀;降低挤压力)(11)简析:金属塑性加工的产品质量的内涵。
【(1)化学成分;(2)内部组织结构;(3)材料性能(力学性能、物理性能、腐蚀性能、加工性能等);(4)精度(尺寸精度、形状精度、表面精度)】4、综合分析:(1)对铝型材挤压模具的认识:(答题要点)模具分类:实心平面模、分流组合模、舌型模、叉架模;模具结构:模孔、工作带、分流空、分流桥、焊合室、空刀、导流孔、阻流块等;模具材料及热处理:H13钢;淬火+2-3次回火+氮化处理;模具技术是铝型材生产的核心技术。
挤压模具的结构与尺寸直接决定铝型材的形状与尺寸精度;模具的结构设计直接决定挤压过程的实现与否;模具的使用寿命显著影响生产效率。
挤压模具设计的基本准则是:在保证模具强度和结构刚度的前提下,尽可能使挤出模口的各部分金属纵向流动速度趋于一致。
金属塑性加工学_轧制理论与工艺王廷溥齐克敏主编

1.2.1 沿轧件断面高向上变形的分布
И.Я. Тарновский根据实验研究把轧制变形区绘成 下图,用以描述轧制时整个变形的情况。
1.2.1 沿轧件断面高向上变形的分布
实验研究还表明,沿轧件断面高度方向上的变形不 均匀分布与变形区形状系数(l/h)有很大关系。
1)当l/h >0.5~1.0时,即轧件断面高度相对于接触弧 长度不太大时,压缩变形完全深入到轧件内部,形 成中心层变形比表面层变形大的现象;
沿轧件高度方向金属横向变形的分布也是不均匀的 。
一般情况下接触表面由于摩擦力的阻碍,使表面的宽度 小于中心层,因而轧件侧面呈单鼓形。
当l/h小于0.5时,轧件变形不能渗透到整个断面高度,因 而轧件侧表面呈双鼓形,在初轧机上可以观察到这种现 象。
复习思考题
1 轧制过程基本概念
不均匀变形理论:该理论认为,沿轧件断面高度方 向上的变形、应力和金属流动分布都是不均匀的。
其主要内容为:
(1)沿轧件断面高度方向上的变形、应力和流动速度分布 都不均匀;
(2)几何变形区内, 在轧件与轧辊接 触表面上,不但 有相对滑动,而 且还有粘着,所 谓粘着系指轧件 与轧辊间无相对 滑动;
1.2.1 沿轧件断面高向上变形的分布
为了了解和控制轧制过程,须对轧制过程形成的变 形区及变形区内的金属流动规律有一概括了解。
1.1 变形区主要参数
1.1.0 简单轧制过程 1.1.1 轧制变形区及其主要参数 1.1.2 轧制变形的表示方法
1.1.0 简单轧制过程
简单轧制过程:是指:
1)上下轧辊直径相等,转速相同,且均为主动辊; 2)轧制过程对两个轧辊完全对称; 3)轧辊为刚性; 4)轧件除受轧辊作用外,不受其他任何外力作用; 5)轧件在入辊处和出辊处速度均匀; 6)轧件的机械性质均匀
塑性加工学(轧制)

第三章轧制轧制是最主要的加工方法。
许多有色金属与合金材料也都是靠轧制方法进行生产。
在钢的生产总量中,除少部分采用铸造和锻造等方法直接制成器件以外,其余占90%以上的钢都须经过轧制成材。
由此可见,金属材料的轧制生产在国民经济中占有极其重要的地位。
上世纪六十年代以来,随着冶金和机械电气工业的进步,电子计算机自动控制技术的应用以及社会总体科学技术水平的提高,金属材料的轧制技术,在工艺、设备和理论上也都有着飞跃的发展。
总的看来,金属轧制工业技术发展的主要特点和趋势为:⑴轧制理论由于与实际结合更加紧密而得到迅速发展:板形控制、不对称轧制⑵生产过程日趋连续化,作业速度不断提高连铸一连轧技术⑶生产过程自动化日益完善⑷生产过程日趋大型化、专业化的同时,又转向发展中、小型灵活生产系统,亦即柔性生产系统⑸节约能源和金属消耗以降低生产成本、提高经济效益的新工艺新技术得到大力发展热轧—中温轧制—冷轧⑹采用自动控制及新技术以大大提高产品的尺寸精度及成型质量采用计算机自动控制、板型控制、不对称轧制等新技术和新轧机,都可大大提高板材尺寸、形状和表面质量的控制精度。
⑺发展合金材料与控制轧制工艺以提高材料性能质量生产合金材料,配合控制轧制、控制冷却新工艺,可以显著提高材料使用性能,延长使用寿命。
⑻不断扩大材料品种规格及增加板带材的产品比重第一节简单轧制过程的基本概念轧制过程是靠旋转的轧辊与轧件形成的摩擦力,将轧件拖进辊缝之间,并使之受到压缩产生塑性变形的过程。
平辊轧制:轧件通过两个旋转方向相反的辊身均匀的圆柱体轧辊之间,发生塑性变形的过程,它是生产板、带、条、箔材的主要加工方法。
轧制目的:①使轧件获得一定的形状和尺寸②使轧件具有一定的组织和性能:Y、M、Y2,细晶粒······)一、简单轧制过程及变形参数㈠简单轧制过程轧制过程中,轧件的变形和力的变化是很复杂的,为了讨论问题方便,常把复杂的轧制过程简化成理想的简单轧制过程,简单轧制过程的假设条件:①两轧辊均为主传动辊,辊径相同,转速相等,轧辊为刚性,上下轧辊完全对称;②轧件只受轧辊作用,不受其他外力作用(张力或推力);③轧件的性能均匀(各部分的ζS、ζb、δ等相同);④轧件的变形与金属质点的流动速度沿断面高度和宽度是均匀的。
金属塑性加工——轧制理论与工艺思考题
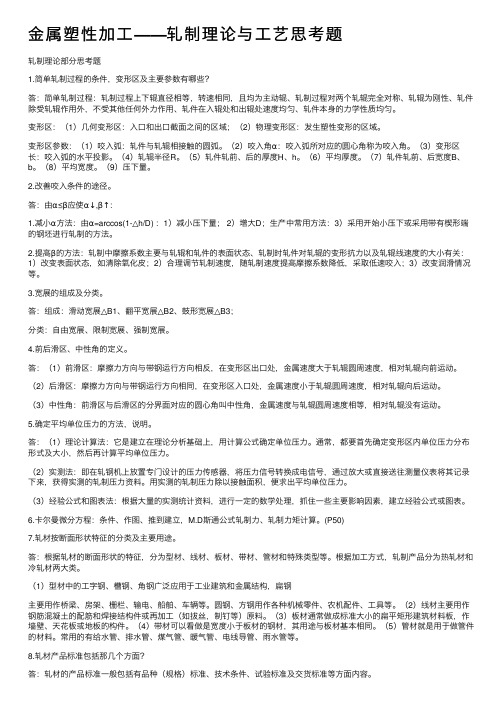
⾦属塑性加⼯——轧制理论与⼯艺思考题轧制理论部分思考题1.简单轧制过程的条件,变形区及主要参数有哪些?答:简单轧制过程:轧制过程上下辊直径相等,转速相同,且均为主动辊、轧制过程对两个轧辊完全对称、轧辊为刚性、轧件除受轧辊作⽤外,不受其他任何外⼒作⽤、轧件在⼊辊处和出辊处速度均匀、轧件本⾝的⼒学性质均匀。
变形区:(1)⼏何变形区:⼊⼝和出⼝截⾯之间的区域;(2)物理变形区:发⽣塑性变形的区域。
变形区参数:(1)咬⼊弧:轧件与轧辊相接触的圆弧。
(2)咬⼊⾓α:咬⼊弧所对应的圆⼼⾓称为咬⼊⾓。
(3)变形区长:咬⼊弧的⽔平投影。
(4)轧辊半径R。
(5)轧件轧前、后的厚度H、h。
(6)平均厚度。
(7)轧件轧前、后宽度B、b。
(8)平均宽度。
(9)压下量。
2.改善咬⼊条件的途径。
答:由α≤β应使α↓,β↑:1.减⼩α⽅法:由α=arccos(1-△h/D) :1)减⼩压下量; 2)增⼤D;⽣产中常⽤⽅法:3)采⽤开始⼩压下或采⽤带有楔形端的钢坯进⾏轧制的⽅法。
2.提⾼β的⽅法:轧制中摩擦系数主要与轧辊和轧件的表⾯状态、轧制时轧件对轧辊的变形抗⼒以及轧辊线速度的⼤⼩有关:1)改变表⾯状态,如清除氧化⽪;2)合理调节轧制速度,随轧制速度提⾼摩擦系数降低,采取低速咬⼊;3)改变润滑情况等。
3.宽展的组成及分类。
答:组成:滑动宽展△B1、翻平宽展△B2、⿎形宽展△B3;分类:⾃由宽展、限制宽展、强制宽展。
4.前后滑区、中性⾓的定义。
答:(1)前滑区:摩擦⼒⽅向与带钢运⾏⽅向相反,在变形区出⼝处,⾦属速度⼤于轧辊圆周速度,相对轧辊向前运动。
(2)后滑区:摩擦⼒⽅向与带钢运⾏⽅向相同,在变形区⼊⼝处,⾦属速度⼩于轧辊圆周速度,相对轧辊向后运动。
(3)中性⾓:前滑区与后滑区的分界⾯对应的圆⼼⾓叫中性⾓,⾦属速度与轧辊圆周速度相等,相对轧辊没有运动。
5.确定平均单位压⼒的⽅法,说明。
答:(1)理论计算法:它是建⽴在理论分析基础上,⽤计算公式确定单位压⼒。
《轧钢机械设计理论》复习思考题及答案
辽宁科技大学机械工程与自动化学院《轧钢机械设计理论》复习思考题2008.12第二章轧制力能参数1.什么是简单轧制过程?1)两辊都驱动2)两辊直径相等3)两辊转速相同4)轧件作等速运动5)轧件只受轧辊作用力6)轧件机械性质是均匀的2.轧制变形的基本参数计算(l、α、ε)和概念。
L接触弧水平投影长度,a咬入角:轧制变形区域内对应的轧辊中心角,ε变形程度:(相对压下量)3.体积不变定律和最小阻力定律的内容和应用。
体积不变定律是指物体的体积在塑性变形中为一常数。
最小阻力定律是指物体在变形过程中当质点有向个方向移动可能时,物体质点向着阻力最小的方向移动。
4.前滑、后滑、中性点、中性角的概念。
在一般的轧制条件下,轧辊圆周速度和轧件速度是不相等的,轧件出口速度比轧辊圆周速度大。
因此,轧件与轧辊在出口处产生相对滑动,称前滑。
而轧件入口速度比轧辊圆周速度低,轧件与轧辊间在入口处也产生相对滑动,但与出口处相对滑动方向相反,称后滑。
在变形区存在一点,这点上的金属移动速度与轧辊圆周速度相等,称中性点。
中性点到轧辊中心之间的连线与两辊中心连线之夹角,称中性角。
5.粘着理论和滑动理论的内容及相应的平均变形速度U m的表达式及适用场合。
粘着理论:轧件与轧辊间没有相对运动。
滑动理论在轧制变形区内轧件和轧辊间有相对运动 p276.轧制过程的咬入条件分为哪两个阶段?咬入条件是什么?开始咬入阶段,已经咬入阶段 p277.塑性方程式的一般式和简化式是什么?p28 p318.金属变形阻力的概念和影响因素是什么?在单向应力状态下,金属材料产生塑性变形时,所需单位面积上的力。
1材料成分2变形速度3变形温度4变形程度5加工历史9.卡尔曼方程建立的假设条件是什么?平面变形假设塑性方程式假设平面断面假设干摩擦理论假设金属变形阻力为常数假设把轧辊是为绝对刚体假设忽略轧件弹性变形轧件材质各项同性假设轧辊圆周速度均匀假设10.影响单位压力的因素有哪些?金属阻力:1材料成分2变形速度3变形温度4变形程度5加工历史应力状态:1外摩擦2张力3外区 p3311.平均单位压力的一般表达式及各符号物理意义。
金属塑性成型原理部分课后习题答案
第一章1.什么是金属的塑性什么是塑性成形塑性成形有何特点塑性----在外力作用下使金属材料发生塑性变形而不破坏其完整性的能力;塑性变形----当作用在物体上的外力取消后;物体的变形不能完全恢复而产生的残余变形;塑性成形----金属材料在一定的外力作用下;利用其塑性而使其成型并获得一定力学性能的加工方法;也称塑性加工或压力加工;塑性成形的特点:①组织、性能好②材料利用率高③尺寸精度高④生产效率高2.试述塑性成形的一般分类..Ⅰ.按成型特点可分为块料成形也称体积成形和板料成型两大类1块料成型是在塑性成形过程中靠体积转移和分配来实现的..可分为一次成型和二次加工..一次加工:①轧制----是将金属坯料通过两个旋转轧辊间的特定空间使其产生塑性变形;以获得一定截面形状材料的塑性成形方法..分纵轧、横轧、斜轧;用于生产型材、板材和管材..②挤压----是在大截面坯料的后端施加一定的压力;将金属坯料通过一定形状和尺寸的模孔使其产生塑性变形;以获得符合模孔截面形状的小截面坯料或零件的塑性成形方法..分正挤压、反挤压和复合挤压;适于低塑性的型材、管材和零件..③拉拔----是在金属坯料的前端施加一定的拉力;将金属坯料通过一定形状、尺寸的模孔使其产生塑性变形;以获得与模孔形状、尺寸相同的小截面坯料的塑性成形方法..生产棒材、管材和线材..二次加工:①自由锻----是在锻锤或水压机上;利用简单的工具将金属锭料或坯料锻成所需的形状和尺寸的加工方法..精度低;生产率不高;用于单件小批量或大锻件..②模锻----是将金属坯料放在与成平形状、尺寸相同的模腔中使其产生塑性变形;从而获得与模腔形状、尺寸相同的坯料或零件的加工方法..分开式模锻和闭式模锻..2板料成型一般称为冲压..分为分离工序和成形工序..分离工序:用于使冲压件与板料沿一定的轮廓线相互分离;如冲裁、剪切等工序;成型工序:用来使坯料在不破坏的条件下发生塑性变形;成为具有要求形状和尺寸的零件;如弯曲、拉深等工序..Ⅱ.按成型时工件的温度可分为热成形、冷成形和温成形..第二章3.试分析多晶体塑性变形的特点..1各晶粒变形的不同时性..不同时性是由多晶体的各个晶粒位向不同引起的..2各晶粒变形的相互协调性..晶粒之间的连续性决定;还要求每个晶粒进行多系滑移;每个晶粒至少要求有 5个独立的滑移系启动才能保证..3晶粒与晶粒之间和晶粒内部与晶界附近区域之间的变形的不均匀性.. Add:4滑移的传递;必须激发相邻晶粒的位错源..5多晶体的变形抗力比单晶体大;变形更不均匀..6塑性变形时;导致一些物理;化学性能的变化..7时间性..hcp系的多晶体金属与单晶体比较;前者具有明显的晶界阻滞效应和极高的加工硬化率;而在立方晶系金属中;多晶和单晶试样的应力—应变曲线就没有那么大的差别..4.试分析晶粒大小对金属塑性和变形抗力的影响..①晶粒越细;变形抗力越大..晶粒的大小决定位错塞积群应力场到晶内位错源的距离;而这个距离又影响位错的数目n..晶粒越大;这个距离就越大;位错开动的时间就越长;n也就越大..n越大;应力场就越强;滑移就越容易从一个晶粒转移到另一个晶粒..②晶粒越细小;金属的塑性就越好..a.一定体积;晶粒越细;晶粒数目越多;塑性变形时位向有利的晶粒也越多;变形能较均匀的分散到各个晶粒上;b.从每个晶粒的应力分布来看;细晶粒是晶界的影响区域相对加大;使得晶粒心部的应变与晶界处的应变差异减小..这种不均匀性减小了;内应力的分布较均匀;因而金属断裂前能承受的塑性变形量就更大..5.什么叫加工硬化产生加工硬化的原因是什么加工硬化对塑性加工生产有何利弊加工硬化----随着金属变形程度的增加;其强度、硬度增加;而塑性、韧性降低的现象..加工硬化的成因与位错的交互作用有关..随着塑性变形的进行;位错密度不断增加;位错反应和相互交割加剧;结果产生固定割阶、位错缠结等障碍;以致形成胞状亚结构;使位错难以越过这些障碍而被限制在一定范围内运动..这样;要是金属继续变形;就需要不断增加外力;才能克服位错间强大的交互作用力..加工硬化对塑性加工生产的利弊:有利的一面:可作为一种强化金属的手段;一些不能用热处理方法强化的金属材料;可应用加工硬化的方法来强化;以提高金属的承载能力..如大型发电机上的护环零件多用高锰奥氏体无磁钢锻制..不利的一面:①由于加工硬化后;金属的屈服强度提高;要求进行塑性加工的设备能力增加;②由于塑性的下降;使得金属继续塑性变形困难;所以不得不增加中间退火工艺;从而降低了生产率;提高了生产成本..6.什么是动态回复为什么说动态回复是热塑性变形的主要软化机制动态回复是在热塑性变形过程中发生的回复自发地向自由能低的方向转变的过程..动态回复是热塑性变形的主要软化机制;是因为:①动态回复是高层错能金属热变形过程中唯一的软化机制..动态回复是主要是通过位错的攀移、交滑移等实现的..对于层错能高的金属;变形时扩展位错的宽度窄;集束容易;位错的交滑移和攀移容易进行;位错容易在滑移面间转移;而使异号位错相互抵消;结果使位错密度下降;畸变能降低;不足以达到动态结晶所需的能量水平..因为这类金属在热塑性变形过程中;即使变形程度很大;变形温度远高于静态再结晶温度;也只发生动态回复;而不发生动态再结晶..②在低层错能的金属热变形过程中;动态回复虽然不充分;但也随时在进行;畸变能也随时在释放;因而只有当变形程度远远高于静态回复所需要的临界变形程度时;畸变能差才能积累到再结晶所需的水平;动态再结晶才能启动;否则也只能发生动态回复..Add:动态再结晶容易发生在层错能较低的金属;且当热加工变形量很大时..这是因为层错能低;其扩展位错宽度就大;集束成特征位错困难;不易进行位错的交滑移和攀移;而已知动态回复主要是通过位错的交滑移和攀移来完成的;这就意味着这类材料动态回复的速率和程度都很低应该说不足;材料中的一些局部区域会积累足够高的位错密度差畸变能差;且由于动态回复的不充分;所形成的胞状亚组织的尺寸小、边界不规整;胞壁还有较多的位错缠结;这种不完整的亚组织正好有利于再结晶形核;所有这些都有利于动态再结晶的发生..需要更大的变形量上面已经提到了..7.什么是动态再结晶影响动态再结晶的主要因素有哪些动态再结晶是在热塑性变形过程中发生的再结晶..动态再结晶和静态再结晶基本一样;也会是通过形核与长大来完成;其机理也是大角度晶界或亚晶界想高位错密度区域的迁移..动态再结晶的能力除了与金属的层错能高低层错能越低;热加工变形量很大时;容易出现动态再结晶有关外;还与晶界的迁移难易有关..金属越存;发生动态再结晶的能力越强..当溶质原子固溶于金属基体中时;会严重阻碍晶界的迁移、从而减慢动态再结晶的德速率..弥散的第二相粒子能阻碍晶界的移动;所以会遏制动态再结晶的进行..9.钢锭经过热加工变形后其组织和性能发生了什么变化参见 P27-31①改善晶粒组织②锻合内部缺陷③破碎并改善碳化物和非金属夹杂物在钢中的分布④形成纤维组织⑤改善偏析10.冷变形金属和热变形金属的纤维组织有何不同冷变形中的纤维组织:轧制变形时;原来等轴的晶粒沿延伸方向伸长..若变形程度很大;则晶粒呈现为一片纤维状的条纹;称为纤维组织..当金属中有夹杂或第二相是;则它们会沿变形方向拉成细带状对塑性杂质而言或粉碎成链状对脆性杂质而言;这时在光学显微镜下会很难分辨出晶粒和杂质..在热塑性变形过程中;随着变形程度的增大;钢锭内部粗大的树枝状晶逐渐沿主变形方向伸长;与此同时;晶间富集的杂质和非金属夹杂物的走向也逐渐与主变形方向一致;其中脆性夹杂物如氧化物;氮化物和部分硅酸盐等被破碎呈链状分布;而苏醒夹杂物如硫化物和多数硅酸盐等则被拉长呈条状、线状或薄片状..于是在磨面腐蚀的试样上便可以看到顺主变形方向上一条条断断续续的细线;称为“流线”;具有流线的组织就称为“纤维组织”..在热塑性加工中;由于再结晶的结果;被拉长的晶粒变成细小的等轴晶;而纤维组织却被很稳定的保留下来直至室温..所以与冷变形时由于晶粒被拉长而形成的纤维组织是不同的..12.什么是细晶超塑性什么是相变超塑性①细晶超塑性它是在一定的恒温下;在应变速率和晶粒度都满足要求的条件下所呈现的超塑性..具体地说;材料的晶粒必须超细化和等轴化;并在在成形期间保持稳定..②相变超塑性要求具有相变或同素异构转变..在一定的外力作用下;使金属或合金在相变温度附近反复加热和冷却;经过一定的循环次数后;就可以获得很大的伸长率..相变超塑性的主要控制因素是温度幅度和温度循环率..15.什么是塑性什么是塑性指标为什么说塑性指标只具有相对意义塑性是指金属在外力作用下;能稳定地发生永久变形而不破坏其完整性的能力;它是金属的一种重要的加工性能..塑性指标;是为了衡量金属材料塑性的好坏而采用的某些试验测得的数量上的指标..常用的试验方法有拉伸试验、压缩试验和扭转试验..由于各种试验方法都是相对于其特定的受力状态和变形条件的;由此所测定的塑性指标或成形性能指标;仅具有相对的和比较的意义..它们说明;在某种受力状况和变形条件下;哪种金属的塑性高;哪种金属的塑性低;或者对于同一种金属;在那种变形条件下塑性高;而在哪种变形条件下塑性低..16.举例说明杂质元素和合金元素对钢的塑性的影响..P41-44①碳:固溶于铁时形成铁素体和奥氏体;具有良好的塑性..多余的碳与铁形成渗碳体Fe 3C;大大降低塑性;②磷:一般来说;磷是钢中的有害杂质;它在铁中有相当大的溶解度;使钢的强度、硬度提高;而塑性、韧性降低;在冷变形时影响更为严重;此称为冷脆性..③硫:形成共晶体时熔点降得很低例如 FeS的熔点为 1190℃;而 Fe-FeS 的熔点为 985℃..这些硫化物和共晶体;通常分布在晶界上;会引起热脆性..④氮:当其质量分数较小0.002%~0.015%时;对钢的塑性无明显的影响;但随着氮化物的质量分数的增加;钢的塑性降降低;导致钢变脆..如氮在α铁中的溶解度在高温和低温时相差很大;当含氮量较高的钢从高温快速冷却到低温时;α铁被过饱和;随后在室温或稍高温度下;氮逐渐以 Fe 4N形式析出;使钢的塑性、韧性大为降低;这种现象称为时效脆性..若在 300℃左右加工时;则会出现所谓“兰脆”现象..⑤氢:氢脆和白点..⑥氧:形成氧化物;还会和其他夹杂物如 FeS易熔共晶体FeS-FeO;熔点为910℃分布于晶界处;造成钢的热脆性..合金元素的影响:①形成固溶体;②形成硬而脆的碳化物;……17.试分析单相与多相组织、细晶与粗晶组织、锻造组织与铸造组织对金属塑性的影响..①相组成的影响:单相组织纯金属或固溶体比多相组织塑性好..多相组织由于各相性能不同;变形难易程度不同;导致变形和内应力的不均匀分布;因而塑性降低..如碳钢在高温时为奥氏体单相组织;故塑性好;而在800℃左右时;转变为奥氏体和铁素体两相组织;塑性就明显下降..另外多相组织中的脆性相也会使其塑性大为降低..②晶粒度的影响:晶粒越细小;金属的塑性也越好..因为在一定的体积内;细晶粒金属的晶粒数目比粗晶粒金属的多;因而塑性变形时位向有利的晶粒也较多;变形能较均匀地分散到各个晶粒上;又从每个晶粒的应力分布来看;细晶粒时晶界的影响局域相对加大;使得晶粒心部的应变与晶界处的应变差异减小..由于细晶粒金属的变形不均匀性较小;由此引起的应力集中必然也较小;内应力分布较均匀;因而金属在断裂前可承受的塑性变形量就越大..③锻造组织要比铸造组织的塑性好..铸造组织由于具有粗大的柱状晶和偏析、夹杂、气泡、疏松等缺陷;故使金属塑性降低..而通过适当的锻造后;会打碎粗大的柱状晶粒获得细晶组织;使得金属的塑性提高..18.变形温度对金属塑性的影响的基本规律是什么就大多数金属而言;其总体趋势是:随着温度的升高;塑性增加;但是这种增加并不是简单的线性上升;在加热过程中的某些温度区间;往往由于相态或晶粒边界状态的变化而出现脆性区;使金属的塑性降低..在一般情况下;温度由绝对零度上升到熔点时;可能出现几个脆性区;包括低温的、中温的和高温的脆性区..下图是以碳钢为例:区域Ⅰ;塑性极低—可能是由与原子热振动能力极低所致;也可能与晶界组成物脆化有关;区域Ⅱ;称为蓝脆区断口呈蓝色;一般认为是氮化物、氧化物以沉淀形式在晶界、滑移面上析出所致;类似于时效硬化..区域Ⅲ;这和珠光体转变为奥氏体;形成铁素体和奥氏体两相共存有关;也可能还与晶界上出现FeS-FeO低熔共晶有关;为热脆区..19.什么是温度效应冷变形和热变形时变形速度对塑性的影响有何不同温度效应:由于塑性变形过程中产生的热量使变形体温度升高的现象..热效应:塑性变形时金属所吸收的能量;绝大部分都转化成热能的现象一般来说;冷变形时;随着应变速率的增加;开始时塑性略有下降;以后由于温度效应的增强;塑性会有较大的回升;而热变形时;随着应变速率的增加;开始时塑性通常会有较显着的降低;以后由于温度效应的增强;而使塑性有所回升;但若此时温度效应过大;已知实际变形温度有塑性区进入高温脆区;则金属的塑性又急速下降..第三章2.叙述下列术语的定义或含义:①张量:由若干个当坐标系改变时满足转换关系的分量所组成的集合称为张量;②应力张量:表示点应力状态的九个分量构成一个二阶张量;称为应力张量; .ζηη.x xy xz③应力张量不变量:已知一点的应力状态④主应力:在某一斜微分面上的全应力S和正应力ζ重合;而切应力η=0;这种切应力为零的微分面称为主平面;主平面上的正应力叫做主应力;⑤主切应力:切应力达到极值的平面称为主切应力平面;其面上作用的切应力称为主切应力⑥最大切应力:三个主切应力中绝对值最大的一个;也就是一点所有方位切面上切应力最大的;叫做最大切应力ηmax⑦主应力简图:只用主应力的个数及符号来描述一点应力状态的简图称为主应力图:⑧八面体应力:在主轴坐标系空间八个象限中的等倾微分面构成一个正八面体;正八面体的每个平面称为八面体平面;八面体平面上的应力称为八面体应力;⑨等效应力:取八面体切应力绝对值的3倍所得之参量称为等效应力⑩平面应力状态:变形体内与某方向垂直的平面上无应力存在;并所有应力分量与该方向轴无关;则这种应力状态即为平面应力状..实例:薄壁扭转、薄壁容器承受内压、板料成型的一些工序等;由于厚度方向应力相对很小而可以忽略;一般作平面应力状态来处理11平面应变状态:如果物体内所有质点在同一坐标平面内发生变形;而在该平面的法线方向没有变形;这种变形称为平面变形;对应的应力状态为平面应变状态..实例:轧制板、带材;平面变形挤压和拉拔等..12轴对称应力状态:当旋转体承受的外力为对称于旋转轴的分布力而且没有轴向力时;则物体内的质点就处于轴对称应力状态..实例:圆柱体平砧均匀镦粗、锥孔模均匀挤压和拉拔有径向正应力等于周向正应力..3.张量有哪些基本性质①存在张量不变量②张量可以叠加和分解③张量可分对称张量和非对称张量④二阶对称张量存在三个主轴和三个主值4.试说明应力偏张量和应力球张量的物理意义..应力偏张量只能产生形状变化;而不能使物体产生体积变化;材料的塑性变形是由应力偏张量引起的;应力球张量不能使物体产生形状变化塑性变形;而只能使物体产生体积变化..12.叙述下列术语的定义或含义1位移:变形体内任一点变形前后的直线距离称为位移;2位移分量:位移是一个矢量;在坐标系中;一点的位移矢量在三个坐标轴上的投影称为改点的位移分量;一般用 u、v、w或角标符号ui 来表示;3相对线应变:单位长度上的线变形;只考虑最终变形;4工程切应变:将单位长度上的偏移量或两棱边所夹直角的变化量称为相对切应变;也称工程切应变;即δrt = tanθxy =θxy =αyx +αxy 直角∠CPA减小时;θxy取正号;增大时取负号;5切应变:定义γ yx =γ xy= 1θyx 为切应变; 26对数应变:塑性变形过程中;在应变主轴方向保持不变的情况下应变增量的总和;记为它反映了物体变形的实际情况;故称为自然应变或对数应变;7主应变:过变形体内一点存在有三个相互垂直的应变方向称为应变主轴;该方向上线元没有切应变;只有线应变;称为主应变;用ε1、ε2、ε3 表示..对于各向同性材料;可以认为小应变主方向与应力方向重合;8主切应变:在与应变主方向成± 45°角的方向上存在三对各自相互垂直的线元;它们的切应变有极值;称为主切应变;9最大切应变:三对主切应变中;绝对值最大的成为最大切应变;10应变张量不变量:11主应变简图:用主应变的个数和符号来表示应变状态的简图;12八面体应变:如以三个应变主轴为坐标系的主应变空间中;同样可作出正八面体;八面体平面的法线方向线元的应变称为八面体应变13应变增量:产生位移增量后;变形体内质点就有相应无限小的应变增量;用dεij 来表示;14应变速率:单位时间内的应变称为应变速率;俗称变形速度;用ε& 表示;其单位为 s -1;15位移速度:14.试说明应变偏张量和应变球张量的物理意义..应变偏张量εij / ----表示变形单元体形状的变化;应变球张量δijεm ----表示变单元体体积的变化;塑性变形时;根据体积不变假设;即εm = 0;故此时应变偏张量即为应变张量15.塑性变形时应变张量和应变偏张量有何关系其原因何在塑性变形时应变偏张量就是应变张量;这是根据体积不变假设得到的;即εm = 0;应变球张量不存在了..16.用主应变简图表示塑性变形的类型有哪些三个主应变中绝对值最大的主应变;反映了该工序变形的特征;称为特征应变..如用主应变简图来表示应变状态;根据体积不变条件和特征应变;则塑性变形只能有三种变形类型①压缩类变形;特征应变为负应变即ε1<0 另两个应变为正应变;ε2 +ε3 = .ε1 ;②剪切类变形平面变形;一个应变为零;其他两个应变大小相等;方向相反;ε2 =0;ε1= .ε3 ;③伸长类变形;特征应变为正应变;另两个应变为负应变;ε1 = .ε2 .ε3 ..17.对数应变有何特点它与相对线应变有何关系对数应变能真实地反映变形的积累过程;所以也称真实应变;简称真应变..它具有如下特点:①对数应变有可加性;而相对应变为不可加应变;②对数应变为可比应变;相对应变为不可比应变;③相对应变不能表示变形的实际情况;而且变形程度愈大;误差也愈大..对数应变可以看做是由相对线应变取对数得到的..21.叙述下列术语的定义或含义:Ⅰ屈服准则:在一定的变形条件变形温度、变形速度等下;只有当各应力分量之间符合一定关系时;质点才开始进入塑性状态;这种关系称为屈服准则;也称塑性条件;它是描述受力物体中不同应力状态下的质点进入塑性状态并使塑性变形继续进行所必须遵守的力学条件;Ⅱ屈服表面:屈服准则的数学表达式在主应力空间中的几何图形是一个封闭的空间曲面称为屈服表面..假如描述应力状态的点在屈表面上;此点开始屈服..对各向同性的理想塑性材料;则屈服表面是连续的;屈服表面不随塑性流动而变化..Ⅲ屈服轨迹:两向应力状态下屈服准则的表达式在主应力坐标平面上的集合图形是封闭的曲线;称为屈服轨迹;也即屈服表面与主应力坐标平面的交线..22.常用的屈服准则有哪两个如何表述分别写出其数学表达式..常用的两个屈服准则是 Tresca屈服准则和 Mises屈服准则;数学表达式分别为max minTresca屈服准则:ηmax =ζ .ζ = C2 式中;ζmax 、ζ min ----带数值最大、最小的主应力; C----与变形条件下的材料性质有关而与应力状态无关的常数;它可通过单向均匀拉伸试验求的..Tresca屈服准则可以表述为:在一定的变形条件下;当受力体内的一点的最大切应力ηmax 达到某一值时;该点就进入塑性状体..Mises屈服准则:ζ= 1 ζ1 .ζ 2 2 + ζ 2 .ζ3 2 + ζ3 .ζ12 =ζs2 = 1ζ 2s2zx2yz2xy2xz2zy2yx6ζηηηζζζζζ=+++.+.+.所以 Mises屈服准则可以表述为:在一定的变形条件下;当受力体内一点的等效应力ζ达到某一定值时;该点就进入塑性状态..23.两个屈服准则有何差别在什么状态下两个屈服准则相同什么状态下差别最大Ⅰ共同点:①屈服准则的表达式都和坐标的选择无关;等式左边都是不变量的函数;②三个主应力可以任意置换而不影响屈服;同时;认为拉应力和压应力的作用是一样的;③各表达式都和应力球张量无关..不同点:①Tresca屈服准则没有考虑中间应力的影响;三个主应力的大小顺序不知道时;使用不方便;而 Mises屈服准则则考虑了中间应力的影响;使用方便..Ⅱ两个屈服准则相同的情况在屈服轨迹上两个屈服准则相交的点表示此。
金属塑性成形原理课后答案
金属塑性成形原理课后答案金属塑性成形是指金属在一定条件下,通过外力作用,使其形状发生改变而不破坏其内部结构的一种加工方法。
金属材料在塑性变形过程中,其晶粒会发生滑移、再结晶等变化,从而使金属材料产生塑性变形。
金属塑性成形原理是金属材料在外力作用下的变形规律,了解金属塑性成形原理对于加工工程师来说是非常重要的。
首先,金属塑性成形的原理是基于金属材料的晶体结构和变形机理。
金属材料的晶体结构决定了其塑性变形的特性,比如晶粒的大小、形状、排列方式等。
而金属材料的变形机理则是指金属材料在外力作用下,晶粒发生滑移、再结晶等变化的规律。
通过了解金属材料的晶体结构和变形机理,我们可以更好地掌握金属塑性成形的原理。
其次,金属塑性成形的原理还与金属材料的力学性能密切相关。
金属材料的力学性能包括强度、硬度、韧性、塑性等指标,这些指标决定了金属材料在外力作用下的变形能力。
不同的金属材料具有不同的力学性能,因此在进行金属塑性成形时,需要根据金属材料的力学性能选择合适的加工方法和工艺参数。
另外,金属塑性成形的原理还与加工工艺和设备密切相关。
不同的金属材料和不同的零件形状需要采用不同的加工工艺和设备来实现塑性成形。
比如锻造、拉伸、压铸、滚压等加工工艺都是金属塑性成形的常见方法,而锻造机、拉伸机、压铸机、滚压机等设备则是实现金属塑性成形的工具。
最后,金属塑性成形的原理还与加工工程师的经验和技能密切相关。
加工工程师需要具备丰富的金属材料知识、加工工艺知识和设备操作技能,才能够准确地把握金属塑性成形的原理,并且根据实际情况进行加工操作。
总之,金属塑性成形原理是一个复杂而又深刻的学科,它涉及到金属材料的晶体结构、力学性能、加工工艺和设备以及加工工程师的经验和技能等多个方面。
只有深入理解金属塑性成形的原理,才能够在实际生产中取得良好的加工效果。
希望通过学习金属塑性成形原理,大家能够对金属加工有更深入的了解,提高加工技术水平,为相关行业的发展做出更大的贡献。
《轧制理论与工艺》习题集
《轧制理论与⼯艺》习题集《轧制理论与⼯艺》习题集绪论⼀.概念题1)轧制2)轧制分类3)平辊轧制4)型辊轧制5)纵轧6)横轧7)斜轧⼆.填空题三.问答题1)轧制有哪些分类⽅法,如何分类?2)轧制在国民经济中的作⽤如何?3)现代轧制⼯艺技术的特点和发展趋势如何?四.计算题第⼀篇轧制理论第1章轧制过程基本概念⼀.概念题1)轧制过程2)简单轧制过程3)轧制变形区(07成型正考)4)⼏何变形区5)咬⼊⾓6)接触弧长度(09成型正考)7)变形区长度8)轧辊弹性压扁(08成型正考)9)轧件弹性压扁10)绝对变形量11)相对变形量12)变形系数13)均匀变形理论14)刚端理论15)不均匀变形理论16)变形区形状系数⼆.填空题三.问答题1)简述不均匀变性理论的主要内容。
2)简述沿轧件断⾯⾼度⽅向上速度的分布特点。
3)简述沿轧件断⾯⾼度⽅向上变形的分布特点。
4)简述变形区形状系数对轧件断⾯⾼度⽅向上速度与变形的影响。
5)简述沿轧件宽度⽅向上的⾦属的流动规律。
四.计算题1)咬⼊⾓计算2)接触弧长度计算3)在?650mm轧机上轧制钢坯尺⼨为100mm×100mm×200mm,第1道次轧制道次的压下量为35mm,轧件通过变形区的平均速度为3.0m/s时,试求:(12分) (07成型正考) (08成型正考)(1) 第1道次轧后的轧件尺⼨(忽略宽展);(2) 第1道次的总轧制时间;(3) 轧件在变形区的停留时间;(4) 变形区的各基本参数。
4)在?750mm轧机上轧制钢坯尺⼨为120mm×120mm×250mm,第1道次轧制道次的压下量为35mm,轧件通过变形区的平均速度为3.5m/s时,试求:(12分) (09成型正考)(1) 第1道次轧后的轧件尺⼨(忽略宽展);(2) 第1道次的总轧制时间;(3) 轧件在变形区的停留时间;(4) 变形区的各基本参数。
第2章实现轧制过程的条件⼀.概念题1)咬⼊2)⾃然咬⼊3)⾃然咬⼊条件(07成型正考)4)极限咬⼊条件(09成型正考)5)稳定轧制6)合⼒作⽤点系数7)稳定轧制条件(08成型正考)8)极限稳定轧制条件⼆.填空题三.问答题1)简述改善咬⼊条件的途径。
- 1、下载文档前请自行甄别文档内容的完整性,平台不提供额外的编辑、内容补充、找答案等附加服务。
- 2、"仅部分预览"的文档,不可在线预览部分如存在完整性等问题,可反馈申请退款(可完整预览的文档不适用该条件!)。
- 3、如文档侵犯您的权益,请联系客服反馈,我们会尽快为您处理(人工客服工作时间:9:00-18:30)。
轧制理论部分思考题1.简单轧制过程的条件,变形区及主要参数有哪些?答:简单轧制过程:轧制过程上下辊直径相等,转速相同,且均为主动辊、轧制过程对两个轧辊完全对称、轧辊为刚性、轧件除受轧辊作用外,不受其他任何外力作用、轧件在入辊处和出辊处速度均匀、轧件本身的力学性质均匀。
变形区:(1)几何变形区:入口和出口截面之间的区域;(2)物理变形区:发生塑性变形的区域。
变形区参数:(1)咬入弧:轧件与轧辊相接触的圆弧。
(2)咬入角α:咬入弧所对应的圆心角称为咬入角。
(3)变形区长:咬入弧的水平投影。
(4)轧辊半径R。
(5)轧件轧前、后的厚度H、h。
(6)平均厚度。
(7)轧件轧前、后宽度B、b。
(8)平均宽度。
(9)压下量。
2.改善咬入条件的途径。
答:由α≤β应使α↓,β↑:1.减小α方法:由α=arccos(1-△h/D) :1)减小压下量; 2)增大D;生产中常用方法:3)采用开始小压下或采用带有楔形端的钢坯进行轧制的方法。
2.提高β的方法:轧制中摩擦系数主要与轧辊和轧件的表面状态、轧制时轧件对轧辊的变形抗力以及轧辊线速度的大小有关:1)改变表面状态,如清除氧化皮;2)合理调节轧制速度,随轧制速度提高摩擦系数降低,采取低速咬入;3)改变润滑情况等。
3.宽展的组成及分类。
答:组成:滑动宽展△B1、翻平宽展△B2、鼓形宽展△B3;分类:自由宽展、限制宽展、强制宽展。
4.前后滑区、中性角的定义。
答:(1)前滑区:摩擦力方向与带钢运行方向相反,在变形区出口处,金属速度大于轧辊圆周速度,相对轧辊向前运动。
(2)后滑区:摩擦力方向与带钢运行方向相同,在变形区入口处,金属速度小于轧辊圆周速度,相对轧辊向后运动。
(3)中性角:前滑区与后滑区的分界面对应的圆心角叫中性角,金属速度与轧辊圆周速度相等,相对轧辊没有运动。
5.确定平均单位压力的方法,说明。
答:(1)理论计算法:它是建立在理论分析基础上,用计算公式确定单位压力。
通常,都要首先确定变形区内单位压力分布形式及大小,然后再计算平均单位压力。
(2)实测法:即在轧钢机上放置专门设计的压力传感器,将压力信号转换成电信号,通过放大或直接送往测量仪表将其记录下来,获得实测的轧制压力资料。
用实测的轧制压力除以接触面积,便求出平均单位压力。
(3)经验公式和图表法:根据大量的实测统计资料,进行一定的数学处理,抓住一些主要影响因素,建立经验公式或图表。
6.卡尔曼微分方程:条件、作图、推到建立,M.D斯通公式轧制力、轧制力矩计算。
(P50)7.轧材按断面形状特征的分类及主要用途。
答:根据轧材的断面形状的特征,分为型材、线材、板材、带材、管材和特殊类型等。
根据加工方式,轧制产品分为热轧材和冷轧材两大类。
(1)型材中的工字钢、槽钢、角钢广泛应用于工业建筑和金属结构,扁钢主要用作桥梁、房架、栅栏、输电、船舶、车辆等。
圆钢、方钢用作各种机械零件、农机配件、工具等。
(2)线材主要用作钢筋混凝土的配筋和焊接结构件或再加工(如拔丝,制钉等)原料。
(3)板材通常做成标准大小的扁平矩形建筑材料板,作墙壁、天花板或地板的构件。
(4)带材可以看做是宽度小于板材的钢材,其用途与板材基本相同。
(5)管材就是用于做管件的材料。
常用的有给水管、排水管、煤气管、暖气管、电线导管、雨水管等。
8.轧材产品标准包括那几个方面?答:轧材的产品标准一般包括有品种(规格)标准、技术条件、试验标准及交货标准等方面内容。
9.制定工艺过程总的目的是什么?轧钢工序的任务?轧材的基本工序?答:总目标:优质、高产、低成本地生产出合乎技术要求的轧材;两大任务:精确成型、改善组织和性能;基本工序:原料的清理准备——加热——轧制——冷却——精整——质量检查。
10.金属压力加工的五大加工方法有哪几种?11. 变速轧制(初轧)的速度制定计算。
12.板带材主要技术要求。
答:(1)尺寸精度要求高:主要是厚度精度,因为它不仅影响到使用性能及连续自动冲压后步工序,而且在生产中难度最大。
(2)板型要好:板型要平坦,无浪形瓢曲。
(3)表面质量要好:板带钢是单位面积最大的一种钢材,又多用作外围构件,故必须保证表面的质量。
(4)性能要好:主要包括机械性能、工艺性能和某些钢板的特殊物理或化学性能。
13.板带材轧制技术发展的主要矛盾是什么?解决途径有哪些?答:(1)轧件变形难,轧件变形及其影响大。
(2)使轧制易于变形的途径:①降低板带钢本身的变形抗力(内阻)。
措施:加热,在轧制过程中保温、抢温使轧件具有较高且均匀的轧制温度。
②设法改变轧件变形时的应力状态,减少外摩擦对金属变形的阻力(外阻)。
措施:带张力轧制、润滑、减小工作辊直径。
控制轧机变形措施:①增强和控制机架和辊身的刚性。
②控制和利用轧辊变形。
14. 从结构来分中厚板轧机可分几类,名称是什么?答:按机架机构分类,可分为二辊可逆式、三辊劳特式、四辊可逆式、复合式和万能式几种。
按机架布置分类,可分为单机架、并列式和顺列式等几种。
15.中厚板轧制方法主要有哪几种?答:(1)全纵轧法:钢板延伸方向和原料的纵轴方向重合。
(2)横轧—纵轧法(综合轧法):适合连铸坯。
横轧:钢板的延伸方向和原料的纵轴方向垂直。
横—纵轧法是先横轧将板坯展宽到所要求的宽度,再转90°纵轧。
(3)全横轧法:用连铸坯为原料是,全横轧与纵轧法一样,产生各向性能异性。
(4)角轧—纵轧法:轧件的轴线与轧辊的轴线成一定角度,送入角δ一般为15°—45°,每对角线轧一、二道后换成另一对角线轧制。
角轧要注意使轧件能迅速宽展到所要求的宽度,而形状又不发生歪斜。
(5)平面形状控制轧法:首先纵轧1—2道次,以整板形,称整形轧制,然后90°横轧宽展,再转90°纵轧成材。
16.在连轧机前要切头尾,其目的是什么?原因何在?答:切头的目的是为了出去温度过低的头部以免损伤辊面,并防止“舌头”、“鱼尾”卡在机架间的导卫装置或辊道缝隙中。
切尾以防后端的“鱼尾”或“舌头”给卷取及其后的精整工序带来困难。
17.热连轧中为保持终扎温度一定,最重要最活跃最有效的手段是什么?具体数值如何?18. 在热连轧中,输出辊道速度如何调节?19.活套支持器的作用是什么及基本工艺要求?答:其作用,一是缓冲金属流量的变化,给控制调整以时间,并防止成叠进钢,造成事故;二是调节各架的轧制速度以保持连轧常数,当各种工艺参数产生波动时发出信号和命令,以便快速进行调整;三是带钢能在一定范围内保持恒定的小张力,防止因张力过大引起带钢拉缩,造成宽度不均甚至拉断。
最后几个精轧机架间的活套支持器,还可以调节张力,以控制带钢厚度。
基本要求:动作反应要快,而且自动进行控制,并能在活套变化时始终保持恒张力。
20.为什么冷轧中采用工艺润滑和张力轧制?答:冷轧采用工艺润滑主要作用是减小金属的变形抗力,这不但有利于保证在已有的设备能力条件下实现更大的压下,而且还可以使轧机能够经济可行地生产厚度更小的产品。
此外,采用有效的工艺润滑也直接对冷轧过程的发热率以及轧辊的温升起到良好影响。
在轧制某些品种时,采用工艺润滑还可以起到防止金属粘辊的作用。
轧制带材时在张力作用下,若轧件出现不均匀延伸,则沿轧件宽向上的张力分布将会发生相应的变化,而延伸较小的一侧则张力增大,结果便自动地起到纠正跑偏的作用。
有利于轧制更精确的产品,并可简化操作。
张力轧制的作用有:1)防止带材在轧制过程中跑偏;2)使所轧带材保持平直和良好多的板形;3)降低金属变形抗力,便于轧制更薄的产品;4)可以适当调整轧机主电机负荷的作用。
21. 冷轧中张力的作用主要有哪几个?其内容是什么?答:张力的主要作用包括:(1)防止带钢在冷轧过程中跑偏.(2)使带钢保持良好板形,横向延伸均匀.(3)降低金属变形抗力.内容:22. 冷轧板带钢中三大典型产品是什么?答:金属镀层薄板(包括镀锡板与镀锌板等)、深冲钢板(以汽车板为典型)、电工用硅钢板与不锈钢板等23. 冷轧中平整工序的作用是什么?答:(1)供冲压用的板带钢事先经过小压下率的平整,就可以在冲压时不出现“滑移线”,以一定的压下率进行平整后,钢的应力-应变曲线即可不出现“屈服台阶”,而理论与实验研究证明,吕德斯线的出现正是与此屈服台阶有关。
(2)冷轧板、带材在退火后再经平整,可以使板材的平直度与板面的光洁度有所改善。
(3)改变平整的压下率,可以使钢板的力学性能在一定的幅度内变化,这可以适应不同用途的镀锡板对硬度和塑性所提出的不同要求。
除此之外,经过双机平整或三机平整还可以实现较大的冷轧压下率,以便生产超薄的镀锡板。
24.什么叫最小可轧厚度?怎样使轧机轧出更薄的产品?答:(1)在同一轧机上轧制板带材时,随着轧件变薄,变形抗力在增大,使压下越来越困难,当厚度薄到某一限度时,不管如何加大压力和反复轧制多少次,也不可能使产品轧薄,这一极限厚度称为轧机最小可轧厚度。
(2)大力减小工作辊直径,采用多辊轧机;采用大的张力轧制;采用高效率的工艺润滑剂以降低摩擦系数;适当对带材进行退火软化处理,减小金属变形抗力;增加轧辊的刚性;采用高刚度的轧机。
25.什么是轧机弹跳方程?答:P278 (2)h=S0’+P/K26.用简化的P.H图,推倒预控AGC模型,推倒辊缝传递函数。
推倒P.A的计算公式。
27.板型是指什么?答:(3)板形是指板带材的平直度,即是指浪形,瓢曲或旁弯的有无及程度而言。
28.一个完整的板带轧制制度应包括哪些内容,它们的关系如何?答:主要制度包括:压下、速度、温度、张力及辊型制度等。
29.热连轧机制定压下规程时,分配各架压下量的原则是什么?习惯上如何分配?30.设计冷轧板带钢轧制规程常用的设计方法是什么?31.热连轧粗轧机布置形式及特点?答:(1)£半连续式:粗轧机组由2架可逆式轧机组成特点:粗轧阶段道次可灵活调整,扎线短,设备和投资较少,适于产品要求不太高,品种范围又广的情况,生产能力强,产量高。
(2)£全连续式:粗轧机组由6架轧机组成,每架轧制一道,全部为不可逆式,后两架可(也可不)实现连轧特点:适合大批量单一品种的生产,操作简单,维护方便,设备多,投资大,轧制流程线或厂房长。
但可采用便宜的交流电动机。
(3)£3/4连续式:粗轧机组由一架可逆式轧机和三架不可逆式轧机所组成,最后两个机架用近距离布置使轧件形成连轧。
特点:设备较全连续式少,投资省;厂房短,生产灵活性大,能适应多品种和不同规格产品的生产;粗轧机组轧出带坯的头尾温差较全连续式和半连续式小,;但轧辊寿命短;操作和维护较复杂,耗电量也较大。
32.变形的表示方法有哪些?33.轧制过程的传动力矩的组成。
答:Mz—轧制力矩,用于使轧件塑性变形所需之力矩。
Mm—克服轧制时发生在轧辊轴承,传动机构等的附加摩擦力矩MK—空转力矩,即克服空转时的摩擦力矩。