铸造多晶硅杂质和缺陷处理工艺研究进展
铸造多晶硅中原生杂质及缺陷的研究
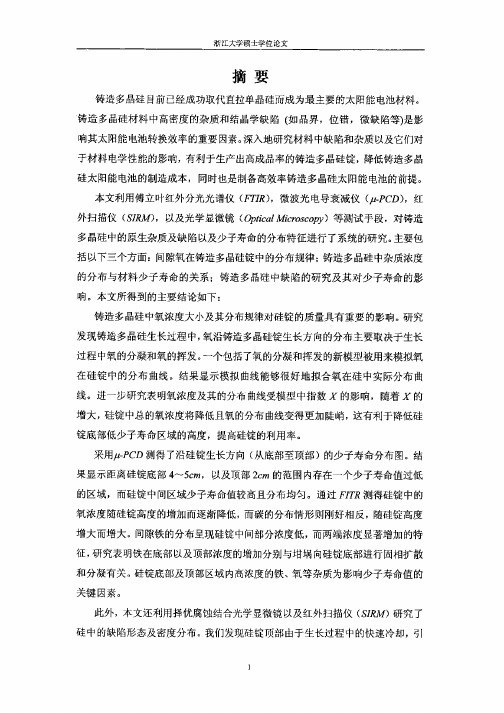
浙江大学硕士学位论文
Ab ta t sr c
C rny a ui sl si n r l d or tl si n h csm l r tle o hs ae m nc sl e o at u t, e r l t ty ai i c n l c a e c o y ai i p n l s c e m ipo vlim tisHg dni o ipri , a ye, o ad a ht oa arl i esy m u tss h o gnc bn n o tc ea . h t f ie u s x c a r n
浙江大学硕士学位论文
起 较大的 应力从而 致了 位错的 热 导 大量 产生 (X m 位错密度大 7 cz 1 0 ) 6 。 体上呈 现
从硅锭底部向硅锭顶部逐渐增加的趋势。 IM 观察到了硅中体缺陷的形态以 S R 及
尺寸大小和密度分布情况。硅锭底部,中部以及顶部处体缺陷平均密度分别为
2 x0 M , x0 m 和1 x0 m . 18 3 8 16 3 . 18 3 8 C . c 5 6 c 左右。
go t d et n G o ar m n bten s u t n epr et dto rwh co . d e et e t i li ad em n l n i i o ge r e w h m ao n x i a a e a oye dsi tn e e alhd T e ye poi w u b a et xgn tb i h b n bi e. o gn fe l e c d ir uo a e s s s t h x r l o d f e
征, 研究表明铁在底部以 及顶部浓度的增加分别与柑祸向硅锭底部进行固相扩散
铸造多晶硅铝吸杂的EBIC研究

值得注意的是,大量位锗呈现明衬度,部分晶界也呈现出明衬度,这是以前文献没有报导过的。
根据EBIC缺陷衬度c的定义:c;生量(式2)Io此处,I。
为背景电流,Id为缺陷处电流。
由此可以推论,这一类缺陷附近区域的扩散长度僮应该很小,存在着一些强复合中心,相比之下,缺陷本身的复合能力比较弱,以致呈现明衬度。
图3是II号样品前表面的EBIC衬度图像。
与图2相似的是,部分位错也呈现明衬度。
我们认为这一现象可能与此类缺陷本身的结构有关,如不同取向的晶界的电学性能是不同的【lO】。
另外在吸杂过程中可能会出现一个现象,由于在某一阶段附集在位错上的金属沉淀溶解,并扩散,单个杂质原子的数目增多,相对于沉淀,均匀分布的杂质原子具有更高的复合能力,反而会使少子扩散长度下降。
也有可能在热处理过程中,由于氧杂质形成的相关缺陷,如位错环,层错,以及点缺陷等,往往会减少少子的复台寿命[111。
在图3黑色指针所示区域,如图3右图所示,分别在T=300K和T=80K对这一区域进行扩散长度的测量。
测量结果见表1。
根据M.Kittler等人的理论[12],说明复合是由浅中心所决定的。
表11I号样品T=300K和T;80K的扩散长度『L(pm)}300K80K12.4,am3.4um图4是I号样品在300K和80K下背表面的EBlC图像。
同样,在大部分位错区域呈现明衬度,但在位错密度很高的区域,位错呈现踣衬度,特别在低温EBIC图像中,高位错密度区域睹衬度十分显著。
图2室温下11号样品背表面的EBIC图像,20keV(左:全貌,右:明衬度区域)Fig2EBICimagesfromre”sideofsampleII“roomtemperature.20keY(1en—overview,right—regionappearedwithbri曲tcontrast)2713图3CP4腐蚀去除Au后II号样品前表面的室温EBlC图像(左:全貌,右:扩散长度测量区域)Fig3EBICimagesfromfrontsideofsamplelfafterremovalofAubyCP6etcNng图4I号样品背表面的EBiC图像,左:300K,右:80KFig4EBICimagesfromrearsideofsamp|eIleft-300It,right-¥0K.4结论通过对铸造多晶硅材料高温铝扩散的EBlC分析,由于在多晶硅中存在许多结晶缺陷,单独铝扩散热处理没有明显吸杂效果。
第七章 铸造多晶硅中的杂质和缺陷
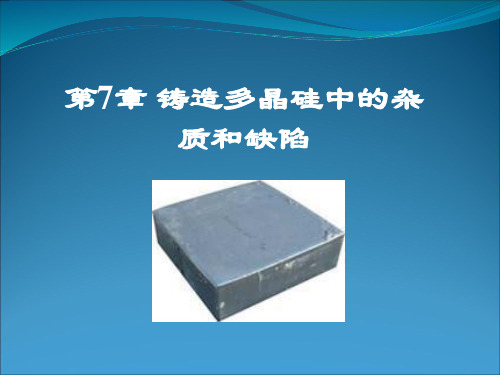
过饱和的间隙氧容易在后续的热处理 工艺中形成复合体与沉淀等。 原生铸造多晶硅中很容易生成氧施主 与氧沉淀,而硅锭底部氧浓度最高, 热处理时间最长,氧施主与氧沉淀的 问题应该是硅锭各部分中最严重的。
铸造多晶硅中原生氧沉淀 的透射电镜照片
第7章 铸造多晶硅中的杂 质和缺陷
铸造多晶硅中的晶界
晶界出现大量的悬桂键,形成界面态,严重影响太阳电 池的光电转换效率。
无金属污染的铸造多晶硅晶界的SEM图像 (a)和EBIC图像(b)
铸造多晶硅中的位错
根据晶体生长方式和过程的不同,铸造多晶硅中的位错 密度约在103~109cm-2左右。
含有高密度位错的铸造多晶硅的光学显微镜照片
a.
p-n结中的金属杂质降低结的反向击穿电压;
b.
金属杂质形成深能级带隙极大地增加p-n结的漏导损耗,
甚至直接导致p-n结变窄;
c.
金属杂质降低氧化诱导生成层错和位错的形成势垒
铸造多晶硅中的金属杂质
金属Cu、Fe、Co在铸造多晶 硅中,自晶体上部(0)到 晶体底部(1)的浓度分布
(直线是根据分凝系数计算的浓 度分布,B的优先分凝系数采用 0.65,Fe的有效分凝系数采用 0.05)
促进其随后氧沉淀生成量。
铸造多晶硅中氧沉淀规律
结果讨论:
铸造多晶硅区别于直拉单晶硅在于,铸造多晶硅中存在较
高密度的位错和晶界等缺陷。而位错和晶界一般可以吸收硅中
过饱和的自间隙硅原子,这降低了铸造多晶硅中氧沉淀的临界 形核半径。另外一方面,由于位错或晶界一般不会影响间隙氧 在硅中的扩散速度,所以,铸造多晶硅中的位错和晶界主要是 通过降低氧沉淀的临界形核半径而促进氧沉淀的生成 。至于原 始氧浓度对氧沉淀的影响,则主要是由于高的原始氧浓度导致 小的氧沉淀临界形核半径,所以高氧样品中氧沉淀生成量较大。
多晶硅的生产工艺及研究
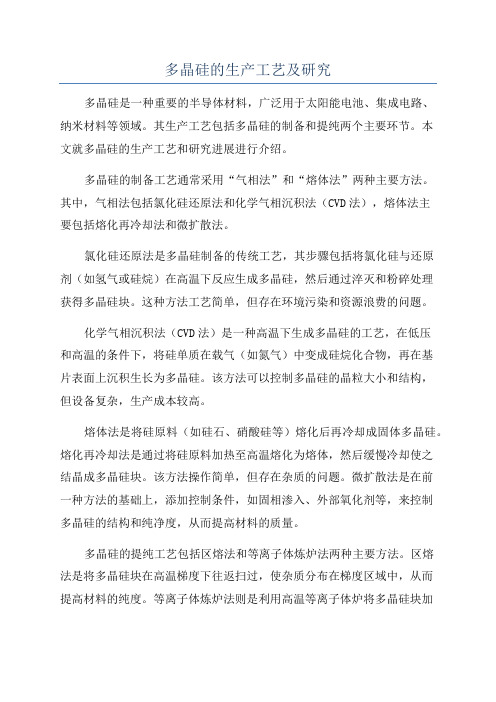
多晶硅的生产工艺及研究多晶硅是一种重要的半导体材料,广泛用于太阳能电池、集成电路、纳米材料等领域。
其生产工艺包括多晶硅的制备和提纯两个主要环节。
本文就多晶硅的生产工艺和研究进展进行介绍。
多晶硅的制备工艺通常采用“气相法”和“熔体法”两种主要方法。
其中,气相法包括氯化硅还原法和化学气相沉积法(CVD法),熔体法主要包括熔化再冷却法和微扩散法。
氯化硅还原法是多晶硅制备的传统工艺,其步骤包括将氯化硅与还原剂(如氢气或硅烷)在高温下反应生成多晶硅,然后通过淬灭和粉碎处理获得多晶硅块。
这种方法工艺简单,但存在环境污染和资源浪费的问题。
化学气相沉积法(CVD法)是一种高温下生成多晶硅的工艺,在低压和高温的条件下,将硅单质在载气(如氮气)中变成硅烷化合物,再在基片表面上沉积生长为多晶硅。
该方法可以控制多晶硅的晶粒大小和结构,但设备复杂,生产成本较高。
熔体法是将硅原料(如硅石、硝酸硅等)熔化后再冷却成固体多晶硅。
熔化再冷却法是通过将硅原料加热至高温熔化为熔体,然后缓慢冷却使之结晶成多晶硅块。
该方法操作简单,但存在杂质的问题。
微扩散法是在前一种方法的基础上,添加控制条件,如固相渗入、外部氧化剂等,来控制多晶硅的结构和纯净度,从而提高材料的质量。
多晶硅的提纯工艺包括区熔法和等离子体炼炉法两种主要方法。
区熔法是将多晶硅块在高温梯度下往返扫过,使杂质分布在梯度区域中,从而提高材料的纯度。
等离子体炼炉法则是利用高温等离子体炉将多晶硅块加热至高温,利用等离子体液体交互作用力使杂质从多晶硅中析出,从而提高材料的纯度。
多晶硅的研究主要集中在杂质控制、晶粒控制和能效提高等方面。
杂质控制是多晶硅研究的重点之一,因为杂质对多晶硅电子性能的影响十分显著。
目前的研究主要集中在减少杂质含量、改善杂质分布和控制杂质降解等方面。
晶粒控制是另一个重要的研究方向,因为晶粒尺寸对多晶硅的导电性能和光学性能有着重要的影响。
研究目标主要是通过改变制备工艺和添加控制条件来控制晶粒尺寸。
冶金法多晶硅中的缺陷及磷吸杂实验研究
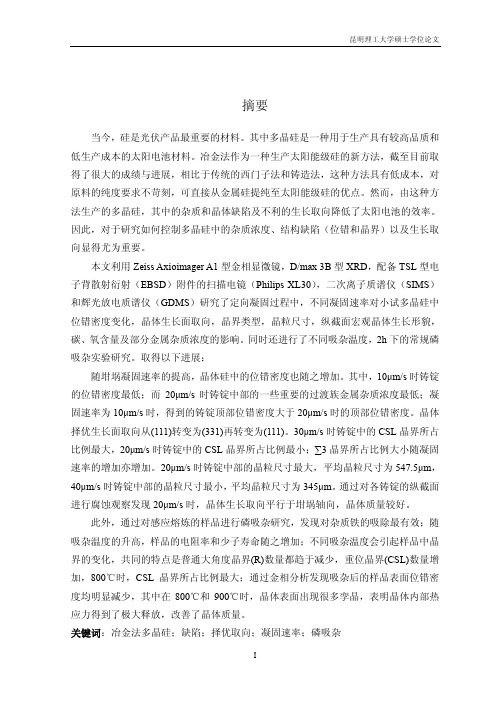
昆明理工大学硕士学位论文摘要当今,硅是光伏产品最重要的材料。
其中多晶硅是一种用于生产具有较高品质和低生产成本的太阳电池材料。
冶金法作为一种生产太阳能级硅的新方法,截至目前取得了很大的成绩与进展,相比于传统的西门子法和铸造法,这种方法具有低成本,对原料的纯度要求不苛刻,可直接从金属硅提纯至太阳能级硅的优点。
然而,由这种方法生产的多晶硅,其中的杂质和晶体缺陷及不利的生长取向降低了太阳电池的效率。
因此,对于研究如何控制多晶硅中的杂质浓度、结构缺陷(位错和晶界)以及生长取向显得尤为重要。
本文利用Zeiss Axioimager A1型金相显微镜,D/max 3B型XRD,配备TSL型电子背散射衍射(EBSD)附件的扫描电镜(Philips XL30),二次离子质谱仪(SIMS)和辉光放电质谱仪(GDMS)研究了定向凝固过程中,不同凝固速率对小试多晶硅中位错密度变化,晶体生长面取向,晶界类型,晶粒尺寸,纵截面宏观晶体生长形貌,碳、氧含量及部分金属杂质浓度的影响。
同时还进行了不同吸杂温度,2h下的常规磷吸杂实验研究。
取得以下进展:随坩埚凝固速率的提高,晶体硅中的位错密度也随之增加。
其中,10μm/s时铸锭的位错密度最低;而20μm/s时铸锭中部的一些重要的过渡族金属杂质浓度最低;凝固速率为10μm/s时,得到的铸锭顶部位错密度大于20μm/s时的顶部位错密度。
晶体择优生长面取向从(111)转变为(331)再转变为(111)。
30μm/s时铸锭中的CSL晶界所占比例最大,20μm/s时铸锭中的CSL晶界所占比例最小;∑3晶界所占比例大小随凝固速率的增加亦增加。
20μm/s时铸锭中部的晶粒尺寸最大,平均晶粒尺寸为547.5μm,40μm/s时铸锭中部的晶粒尺寸最小,平均晶粒尺寸为345μm。
通过对各铸锭的纵截面进行腐蚀观察发现20μm/s时,晶体生长取向平行于坩埚轴向,晶体质量较好。
此外,通过对感应熔炼的样品进行磷吸杂研究,发现对杂质铁的吸除最有效;随吸杂温度的升高,样品的电阻率和少子寿命随之增加;不同吸杂温度会引起样品中晶界的变化,共同的特点是普通大角度晶界(R)数量都趋于减少,重位晶界(CSL)数量增加,800℃时,CSL晶界所占比例最大;通过金相分析发现吸杂后的样品表面位错密度均明显减少,其中在800℃和900℃时,晶体表面出现很多孪晶,表明晶体内部热应力得到了极大释放,改善了晶体质量。
铸造多晶硅制备技术的研究进展

(1 Department of Solar Energy Science and Engineering,Xinyu college,Xinyu 338000,
2 Department of Mechnial and Power Engineering!Nanchang Institute of Technology,Nanchang 330099)
tion and the electromagnetic continuous pulling In addition,the purification technique for phosphorus and boron in
metallurgical grade silicon is explained in details,formation and control of grain boundary and dislocation of multicrys—
为了降低坩埚对硅锭的污染。研究者提出了一种改进方 法。在坩埚内壁涂上si。N4膜层,以降低来自坩埚杂质的玷 污。同时.&。N.涂层还能起到一定的润滑脱模作用,因为硅 熔体在高温时与石墨发生反应,加之硅凝固过程中的体膨胀 作用,易造成硅锭与石墨模具的粘连,冷却后难以脱模,使用 si。N|涂层后硅熔体和坩埚内壁不粘结,这样既可以降低凝固 时产生的大量应力又能多次使用坩埚,从而降低了生产成 本。但最近美国的研究者Buonassisi等[2I]通过分析比较了 口-Si3N.涂层与铸造多晶硅中杂质的种类、相对浓度、含有杂 质颗粒的化学态和杂质分布状况及其形成机理后,认为在铸 造多晶体生长时,si。N。涂层中的金属与非金属杂质可能会 污染铸造多晶硅,并提出了相应解决措施:(1)减少mSi。N中 杂质含量;(2)改善口-Si3N的结构质量,使得在晶体生长时口- 鼠N中的分解物降到最低;(3)降低坩埚的表面面积与体积 的比率(如增大坩埚尺寸大小)。 1.2定向凝固法
铸造多晶硅晶体生长速率对杂质分布的影响研究

铸造多晶硅晶体生长速率对杂质分布的影响研究摘要目前,铸造多晶硅是最主要的光伏材料,其结晶组织、缺陷、和杂质含量显著影响着太阳能电池的转换效率。
杂质的浓度和分布是影响光电转换效率的重要因素。
由于多晶硅锭的质量好坏主要决定于长晶过程中的固液界面形状及晶体生长速率大小,固液界面形状及晶体生长速率大小对定向凝固的排杂效果起决定作用,一般认为微凸的固液界面更有利于多晶硅杂质和位错的排除。
因此深入研究多晶硅生长速率对杂质分布的影响,分析它对多晶硅锭结晶学及电学性能的影响,不仅有利于生长出高成品率的铸造多晶硅锭,而且可以降低铸造多晶硅硅片的制造成本。
本工作利用微波光电导衰减仪(μ-PCD)、二次离子质谱仪(SIMS),四探针测试仪以及红外扫描仪(IR)等方法对铸造多晶硅的杂质以及少子寿命的分布进行了系统的研究。
实验发现,硅锭中的氧浓度随硅锭高度的增加而逐渐降低,而碳的分布情况正好相反。
研究发现,在低速凝固条件下所有金属杂质均有很好提纯效果,硅锭中红区较短,少子寿命较高,但铸锭周期较长。
而高速凝固杂质的排除效果不佳,硅锭中红区较长,少子寿命较低。
实验发现多晶硅锭生长速率为 1.5cm/h为工业生产中较优长晶速率。
关键词:铸造多晶硅,杂质,少子寿命,长晶速率The Investigation on the crystal growth rate of Casting polycrystalline silicon influencing on the distributionof impurityABSTRACTAt present,casting polycrystalline silicon is the main PV materil.Its affect the conversion efficiency of solar battery.Impurity concentratio And distribution is the important factor of photoelectric conversion efficiency.because of quality of pool ycrystalline silicon ingots is determined by the position of the solid/liquid inter face and growth rate of crystal. The shape of solid/liquid interface and growth rate determined the quality of rejecting of impurity.Generally think that small protruding liquid-solid interface is more advantageous to the reject of dislocation and impuritry. So further research about polysilicon growth rate influence on the distribution of the impurity of polycrystalline silicon ingots is necessary. By anal ysis electrical behaviour of the ingot, not only help us improve the yield of the ingots,but also can reduce the cost of casting pol ycrystalline silicon.In this thesis, we use Microwavephoto Conductive Deca y(μ-PCD, ScanningInfrared Microscopy(IR), Scanning Infrared Microscopy(SIR M) and Four-point Probe Tester to Investigate the distribution of impurity and Minority carrier lifetime of the ingots.In the experim -ents we find that osygen content increases in vetical direction, While carbon distribution is exactly thepposite.We find that low-speed solidification conditions is good to the reject of all the reject of all the metal inpurity,minority carrier lifetime is higher, but the casting cycle is longer. Whle High-speed solidification to the disadvantage of the reject of impurity.and its minority carrier lifetime is lower Experimen ts have found that poly ingot growth rate for 1.5 cm/h forindustrial production is a better choice.KEY WORDS:casting polycrystalline silicon,impurity, minority carrier lifetime,growth rate of the crysta l目录第一章绪论 ..................................................................... V I §1.1 引言 ................................................................... V I §1.2铸造多晶硅的研究进展 ....................................... V I §1.2.1 浇铸法 . (VII)§1.2.2定向凝固法 (VII)§1.2.3电磁感应加热连续铸造( EMCP) (VIII)§1.3 多晶硅定向凝固原理及相关工艺参数 (X)§1.3.1 多晶硅定向凝固原理 (X)§1.3.2 温度梯度 (X)§1.3.3 长晶速率................................................... X I §1.4 铸造多晶硅中的主要杂质及影响. (XII)§1.4.1 硅中的氧 (XII)§1.4.2 硅中的碳 (XIII)§1.4.3 硅中的过渡金属 (XIII)§1.5铸造多晶硅中的杂质效应 (XIV)§1.5.1 扩散效应 (XIV)§1.5.2蒸发效应 (XIV)§1.5.3分凝效应 (XV)§1.6 铸造多晶硅锭的主要参数及检测方法 (XVI)§1.6.1 少子寿命 (XVI)§1.6.2电阻率 (XVII)§1.6.3 IR阴影测试 (XVII)§1.6.4杂质浓度测试 ....................................... X VIII §1.7本文研究的主要目的及内容 ........................... X VIII 第二章实验过程 (XX)§2.1样品制备 (XX)§2.1.1检料 (XX)§2.1.2 多晶铸锭过程 (XX)§2.1.3剖方取样 (XXV)§2.2 样品检测....................................................... X XVI §2.2.1 少子寿命检测....................................... X XVI§2.2.2 IR阴影检测 (XXVII)第三章实验结果及分析 (XXVIII)§3.1 实验结果 (XXVIII)§3.1.1 少子寿命检测结果 (XXVIII)§3.1.2 IR阴影检测结果................................... X XIX §3.2 结果分析....................................................... X XIX §3.2.1 碳的浓度分布....................................... X XIX§3.2.2 氧的浓度分布....................................... X XIX 结论 (XXX)参考文献 (XXX)致谢 (XXXIII)第一章绪论§1.1 引言3E,即能源(Energy)、经济(Economy)和环境(Environment),被称为人类文明可持续发展所面临的三大课题。
太阳电池用铸造多晶硅结构缺陷和杂质的
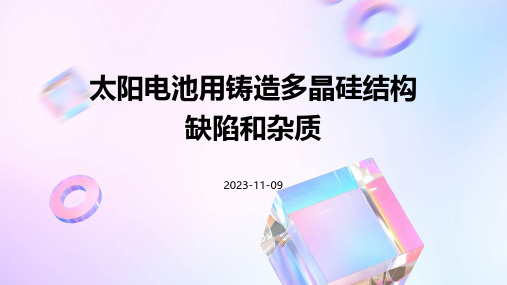
缺陷和杂质2023-11-09•铸造多晶硅太阳电池概述•铸造多晶硅的结构缺陷•铸造多晶硅中的杂质目录•铸造多晶硅结构缺陷和杂质的表征与检测方法•铸造多晶硅结构缺陷和杂质的控制与优化•展望与未来发展趋势01铸造多晶硅太阳电池概述铸造多晶硅太阳电池的制造工艺已经非常成熟,可以实现大规模生产。
制造工艺成熟转换效率较高制造成本较低铸造多晶硅太阳电池的转换效率较高,可以满足大部分应用需求。
铸造多晶硅太阳电池的制造成本较低,具有较好的经济性。
030201吸光层由多晶硅材料构成,能够吸收太阳光并将其转化为电能。
吸光层导电层由掺杂的多晶硅材料构成,能够将吸光层产生的电流导出并传输到外部电路中。
导电层背反射器用于将太阳光反射回吸光层,以增加光吸收效果。
背反射器导电层制备将掺杂的多晶硅材料通过热处理和加工等工艺制成导电层。
铸造多晶硅太阳电池的制造过程原材料准备制造铸造多晶硅太阳电池需要准备多晶硅材料、掺杂剂、反射器等原材料。
吸光层制备将多晶硅材料通过热处理和掺杂等工艺制成吸光层。
背反射器制备将反射器材料通过加工等工艺制成背反射器。
组装将吸光层、导电层和背反射器组装在一起,形成完整的铸造多晶硅太阳电池。
02铸造多晶硅的结构缺陷在铸造多晶硅中,晶界是常见的结构缺陷。
晶界是指不同晶粒之间的交界,通常会对材料的性能产生负面影响。
在太阳电池中,晶界会降低载流子的迁移率,导致光电转换效率下降。
晶界位错是指晶体结构中的原子排列错位。
在铸造多晶硅中,位错会破坏晶体结构的周期性,导致能带结构发生变化。
位错还会影响载流子的散射和复合,进一步降低太阳电池的性能。
位错铸造多晶硅中的晶界与位错杂质陷阱在铸造多晶硅中,杂质原子通常会聚集在晶界或位错等缺陷处。
这些杂质原子会捕获电子或空穴,形成杂质能级,从而影响载流子的迁移和复合过程。
杂质陷阱对太阳电池的光电转换效率产生负面影响。
热处理与杂质陷阱通过热处理可以部分消除杂质陷阱的影响。
在高温下,杂质原子有机会从缺陷处扩散出去,从而减少杂质陷阱的数量。
- 1、下载文档前请自行甄别文档内容的完整性,平台不提供额外的编辑、内容补充、找答案等附加服务。
- 2、"仅部分预览"的文档,不可在线预览部分如存在完整性等问题,可反馈申请退款(可完整预览的文档不适用该条件!)。
- 3、如文档侵犯您的权益,请联系客服反馈,我们会尽快为您处理(人工客服工作时间:9:00-18:30)。
铸造多晶硅杂质和缺陷处理工艺研究进展摘要:近年来,低成本和高效率的多晶硅已经成为最主要光伏材料之一。
本文从太阳能电池制备工艺角度出发,综述了国内外近年来关于对铸造多晶硅杂质和缺陷处理方面的工艺研究进展。
分析比较了各种处理工艺,包括磷吸杂、铝吸杂、磷铝共吸杂和多孔硅吸杂对杂质吸除效果、少子寿命的影响。
也分析了钝化和热处理工艺对多晶硅材料性能的影响。
综合考虑成本要求和除杂效果,高温P-AI联合吸杂以及多孔硅吸杂是较好的选择,它们可能在未来的铸造多晶硅除杂工艺领域中占据重要地位。
一、引言随着国际原油的价格突破100美元/桶,能源问题变得愈来愈严峻。
与此同时,环境问题也要求新能源能够替代化石能源。
自1954年贝尔实验室研制出第一块太阳电池以来,光伏材料为基础所制得的太阳电池直接将太阳能转化为电能,这被公认为解决能源和环境问题最有效的途径之一。
在过去的五年中,光伏产业的年增长率超过了40%,成为目前发展最快的产业。
2006年,全球太阳能电池产能达到了2520MWp,创造了一个价值120亿欧元的产业。
据商业分析,2010年的太阳能产值将达到400亿欧元。
多晶硅作为太阳能电池的主要原料之一,以其相对低廉的成本,成为最重要的原材料,目前已经占据市场50%以上的份额,并且市场份额还有继续扩大的趋势。
但是,由于太阳能用多晶硅原材料很多都来源于微电子工业的头尾料,从而导致太阳能用铸造多晶硅中存在大量的微缺陷和氧、氮、碳等非金属杂质,以及较多的铁、铜、镍、锰、钛等金属杂质。
多晶硅中位错、晶界等这些扩展缺陷存在的悬挂键和金属杂质是少数载流子的复合中心,这些金属杂质和微缺陷在硅禁带中引人了深能级,成为光生少数载流子的复合中心,从而减少了少数载流子的寿命,严重影响了太阳电池的光电转换效率。
如何消除这些因素对多晶硅电池的影响就成为当前研究的主要课题之一。
本文从太阳能电池制备工艺角度出发,综述了国内外近年来关于对铸造多晶硅杂质和缺陷的处理方法的报道,分析比较了各种处理工艺对杂质吸除效果、少子寿命的影响,并对未来的技术和工艺发展的趋势做出了展望。
二、吸杂工艺吸杂可分为外吸杂和内吸杂,内吸杂是利用硅中氧沉积所产生的缺陷作为“陷阱”,以此捕获硅体内的杂质,从而在表面形成一层“洁净”区域用于制备器件,一般用于IC(Integrated Circuit)行业。
外吸杂是采用外部吸收的方式,使金属杂质从活跃区域移动到不产生负面效果的区域,一般是采用磷、铝的单独吸杂或两者的共同吸杂。
太阳电池作为体器件,其吸杂只能使用外吸杂。
一般而言,吸杂的主要过程是:(1)杂质的释放。
金属杂质在多晶硅体内的存在方式有间隙位、替位态、沉淀或和其它杂质形成复合体,而这些形态中只有间隙态的才是可移动的,所以只有把以其它形态的金属变位间隙形态才可以被快速吸杂。
(2)杂质的快速扩散。
这些已变为间隙太的金属杂质快速扩散,到达吸杂点。
(3)杂质在预定的吸杂位置被捕获。
这些预定的吸杂位置可以是缺陷、空位或固溶度增强的区域,而且这些吸杂区域要对杂质原子具有更牢固的束缚能,以使这些被吸杂的杂质不致于被再次释放。
1、磷吸杂磷吸杂是利用浓磷扩散形成重扩散层,它的吸杂原理包括驰豫吸杂和分凝吸杂,分凝吸杂部分是由于费米能级效应和离子成对效应而形成的在重扩散层的增强溶解;驰豫吸杂部分是由重扩散形成的位错网络,同时由于硅扩散时形成过量的自间隙原子而导致金属杂质从替位位置移动到间隙位置,导致了扩散速度的增加,从而加速磷吸杂的完成。
从原则上讲,可以将晶体硅内的金属杂质浓度降到很低。
硅太阳电池通常是利用p型材料,然后进行磷扩散,在硅片表明形成一层高磷浓度的n型半导体层,构成p-n结。
而磷吸杂则是利用同样的技术,在制备p-n结之前,在850-900℃作用热处理1-2h,利用三氯氧磷(POCI3)液态源,在硅片两面扩散高浓度的磷原子,产生磷硅玻璃(PSG),它含有大量的微缺陷,成为金属杂质的吸杂点;在磷扩散的同时,金属原子也扩散并沉积在磷硅玻璃层中;然后通过HPO3、HNO3和HF等化学试剂,去除磷硅玻璃层,将其中的金属杂质一并去除,然后在制备p-n结,达到金属吸杂的目的。
磷吸杂的工艺过程如下图:在吸杂的过程中杂质的释放和扩散要求吸杂温度不能过低,如果温度过低则不利于杂质的溶解和扩散;而吸杂的驱动力—杂质的分凝又要求吸杂温度不能过高,如果温度过高则不利于杂质分凝到吸杂区域,这两方面的因素共同作用导致吸杂有一个最佳的吸杂温度。
在恒温吸杂基础上发展起来的变温吸杂(如图3所示)是在吸杂的过程中通过改变吸杂的温度和时间来达到最佳的吸杂效果。
具体要求是先高温吸杂一段时间,然后再缓慢冷却到较低的温度再吸杂一段时间。
结果表明变温磷吸杂的效果明显优于恒温磷吸杂,特别是在原生多晶硅中的高质量区域。
进一步而言,变温磷吸杂工艺吸杂效果好,且和通常的太阳电池制造工艺兼容,可以在不增加成本的情况下,有效地提高铸造多晶硅太阳电池的光电转换效率。
但是磷吸杂也有其缺陷。
对于替位态杂质,如As、Sb、Sn和Zn等,磷吸杂对它们没有影响,主要原因是替位态的杂质在扩散时,采用“踢出”机制,扩散速度低,因此很难扩散到磷吸杂层而被去除。
铸造多晶硅磷吸杂的效果还受到其它因素如温度、时间等的制约。
法国的Perichaud就温度和时间对磷吸杂的影响做了相关实验,如图2所示为铸造多晶硅中少数载流子扩散长度随磷吸杂时间的变化。
从图中可以看出,随着吸杂处理时间的延长,少数载流子扩散长度越来越大;而在2h内,850℃和900℃吸杂后的扩散长度相同,但是随着时间的延长,900℃磷吸杂的扩散长度明显要大,说明高温有利于金属吸杂。
但是,温度对磷吸杂效果的影响并非如此简单。
如果磷吸杂温度不高会使部分金属沉淀难以被溶解,然而吸杂的驱动力—杂质的分凝又要求吸杂温度不能过高,如果温度过高则不利于杂质分凝到吸杂区域,这两方面的因素共同作用导致吸杂有一个最佳的吸杂温度。
2、铝吸杂除磷吸杂外,铝吸杂也是铸造多晶硅太阳能电池工艺的常用吸杂技术。
铝吸杂是利用金属杂质在铝中的固溶度远大于在硅中固溶度的原理进行吸杂的。
在700-900℃时,许多重金属杂质在铝中的固容度比在硅中的固溶度高4-10个数量级。
铝薄膜的沉积可以作为太阳电池的背电极,也可以起到铝背场作用。
并且,金属杂质在硅中的扩散速度远大于磷、硼等替位式元素。
实验方面,也有大量关于铝吸杂的报道,在铝合金的化或后续的热处理中,硅中的金属杂质会扩散到AISi合金层或高铝浓度掺杂层沉淀,从而导致体内的金属浓度大幅度减小。
然后,将硅片在化学溶液中去除AISi层、高铝浓度掺杂层,达到去除金属杂质的目的。
石湘波等系统研究了不同的铝吸杂温度和方式及对硅片少子寿命、电性能和量子效率的影响,发现在CTP(conventional thermal processing)吸杂时600,700℃的低温铝吸杂所得到的少子寿命较高;而在RTP 吸杂时830℃能得到高达93.8s的少子寿命。
同时发现对于RTP铝吸杂,双面镀铝少子寿命提高明显,对于CTP单面镀铝少子寿命高明显,同时发现高温会使硅片的少子寿命退化。
试验表明在830℃时提供了最适合的杂质吸附条件。
但是进一部研究表明,对于质量好、少数载流子寿命高的铸造多晶硅和直拉单晶,铝吸杂的效果并不明显。
磷吸杂比铝吸杂快,但铝吸杂的吸杂能力和稳定性高于磷吸杂。
所以在实际铸造多晶硅太阳电池工艺中,常常将铝吸杂和磷吸杂结合使用,以提高金属吸杂的能力。
3、磷-铝共吸杂磷吸杂要比铝吸杂快,而铝吸杂的吸杂稳定性又高于磷吸杂。
磷-铝共吸杂兼顾了两者的优点,同时磷-铝的互扩散还加强了对重金属杂质的吸收作用,更有利于产生较深的发射结。
磷铝共吸杂是在一侧为磷源另一侧为铝源的条件下进行吸杂的。
在磷-铝共吸杂下,少数载流子扩散长度增加,提高了少子寿命。
图4是在不同材料多晶硅中,在经过同样的传统热处理工艺之后,进行磷吸杂、铝吸杂、磷-铝共吸杂这种吸杂工艺时的吸杂效果图。
结果表明磷-铝共吸杂的吸杂效果最好。
采用磷-铝共吸杂,多晶硅的最佳退火温度为875℃。
以及考虑在有氧和碳的存在下对其吸杂效率的影响。
图5是在不同的温度范围里,经过快速热处理之后的少数载流子的扩散长度。
结果表明采用磷-铝共吸杂时,多晶硅的最佳快速退火温度是875℃,应尽量避免或缩短多晶硅的高温热处理。
国内赵慧等人研究了浓磷扩散吸杂、铝吸杂以及磷-铝联合吸杂双面蒸铝对于多晶硅的影响,并在此基础上制备多晶硅太阳电池。
测量吸杂前后硅片的有效少数载流子寿命的变化趋势,采用吸杂后的多晶硅片制备1cm*1cm的太阳电池,与未吸杂的多晶硅太阳电池比较,研究多晶硅太阳电池的电学特性变化。
结果表明:(1)磷-铝联合吸杂对于硅片少子寿命的提高最大,达30us以上,其次是磷吸杂,铝吸杂再次之。
(2)采用吸杂后的多晶硅片制备了1cm*1cm的太阳电池,与相同条件下未经吸杂制备的电池相比,发现三种吸杂方式都能提高电池的各项电学特性,其中磷-铝联合吸杂对电池效率提高最大,达40%以上,最差为铝吸杂,只提高15%左右,这与吸杂后所测得的少子寿命的变化趋势一致。
(3)三种吸杂方式在不同程度上促进了硅片界面晶格应力对重金属杂质的吸附作用,减少了载流子的复合中心,从而提高了有效少数载流子的寿命,而有效少数载流子的寿命直接影响到电池的效率。
石湘波等人研究了不同温度下磷吸杂、铝吸杂和磷-铝共吸杂对少子寿命、太阳电池电性能影响。
结果表明,磷铝共吸杂少子寿命的增加比仅用磷、铝单独吸杂都明显,但3种吸杂方式对太阳电池电性能都没太大影响。
高温会造成多晶硅的退化,采用磷铝共吸杂,应尽量避免或缩短多晶硅的高温热处理。
在磷吸杂、铝吸杂、磷铝共吸杂3种吸杂方式中,磷铝共吸杂结合了磷吸杂和铝吸杂的优点,吸杂效果最好。
吸杂能有效地提高硅片的少子寿命,但对多晶硅电性能的改善却不明显。
4、多孔硅吸杂除了传统的利用P或AI或B进行吸杂外,目前利用多空硅进行吸杂也是研究的热点之一。
多孔硅是一个由小孔组成的网状结构,小孔的尺寸在10-1000nm,由于其具有纳米尺寸的小孔结构,试验表明,在多晶硅上经化学沉积多孔硅层,不仅能够有效的充当太阳电池的减反射层,而且由于这种结构在多晶硅表面形成了一层损伤层,它成为杂质和缺陷的有效吸杂中心;通过试验发现,在多晶硅上制备多孔硅,氮气气氛下高温退火后,多晶硅的少子寿命有了明显的提高。
从表和图可以看出,高的退火温度和和适当退火时间将有效提高多孔硅的吸杂能力。
如果多孔硅吸杂和磷吸杂结合起来,将会产生良好的效果(见表2)。
此外,多孔硅有希望将表面织构化、钝化和制备表面减反射层一步完成而且工艺简单,将有效地降低成本。
而且少子寿命能由原来的1.4提高到25.6s。