铸造多晶硅中热施主形成规律
铸造多晶硅中原生杂质及缺陷的研究
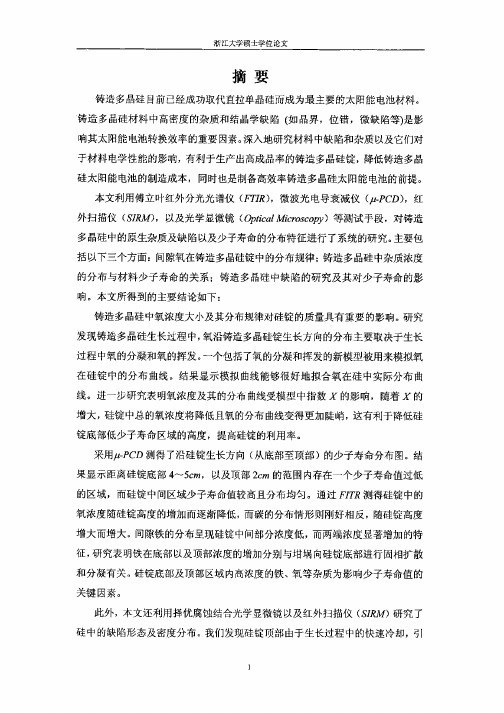
浙江大学硕士学位论文
Ab ta t sr c
C rny a ui sl si n r l d or tl si n h csm l r tle o hs ae m nc sl e o at u t, e r l t ty ai i c n l c a e c o y ai i p n l s c e m ipo vlim tisHg dni o ipri , a ye, o ad a ht oa arl i esy m u tss h o gnc bn n o tc ea . h t f ie u s x c a r n
浙江大学硕士学位论文
起 较大的 应力从而 致了 位错的 热 导 大量 产生 (X m 位错密度大 7 cz 1 0 ) 6 。 体上呈 现
从硅锭底部向硅锭顶部逐渐增加的趋势。 IM 观察到了硅中体缺陷的形态以 S R 及
尺寸大小和密度分布情况。硅锭底部,中部以及顶部处体缺陷平均密度分别为
2 x0 M , x0 m 和1 x0 m . 18 3 8 16 3 . 18 3 8 C . c 5 6 c 左右。
go t d et n G o ar m n bten s u t n epr et dto rwh co . d e et e t i li ad em n l n i i o ge r e w h m ao n x i a a e a oye dsi tn e e alhd T e ye poi w u b a et xgn tb i h b n bi e. o gn fe l e c d ir uo a e s s s t h x r l o d f e
征, 研究表明铁在底部以 及顶部浓度的增加分别与柑祸向硅锭底部进行固相扩散
第七章 铸造多晶硅中的杂质和缺陷
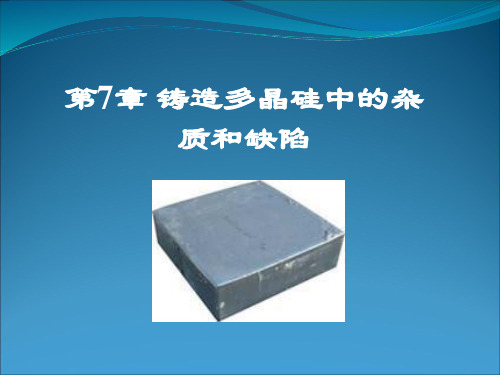
过饱和的间隙氧容易在后续的热处理 工艺中形成复合体与沉淀等。 原生铸造多晶硅中很容易生成氧施主 与氧沉淀,而硅锭底部氧浓度最高, 热处理时间最长,氧施主与氧沉淀的 问题应该是硅锭各部分中最严重的。
铸造多晶硅中原生氧沉淀 的透射电镜照片
第7章 铸造多晶硅中的杂 质和缺陷
铸造多晶硅中的晶界
晶界出现大量的悬桂键,形成界面态,严重影响太阳电 池的光电转换效率。
无金属污染的铸造多晶硅晶界的SEM图像 (a)和EBIC图像(b)
铸造多晶硅中的位错
根据晶体生长方式和过程的不同,铸造多晶硅中的位错 密度约在103~109cm-2左右。
含有高密度位错的铸造多晶硅的光学显微镜照片
a.
p-n结中的金属杂质降低结的反向击穿电压;
b.
金属杂质形成深能级带隙极大地增加p-n结的漏导损耗,
甚至直接导致p-n结变窄;
c.
金属杂质降低氧化诱导生成层错和位错的形成势垒
铸造多晶硅中的金属杂质
金属Cu、Fe、Co在铸造多晶 硅中,自晶体上部(0)到 晶体底部(1)的浓度分布
(直线是根据分凝系数计算的浓 度分布,B的优先分凝系数采用 0.65,Fe的有效分凝系数采用 0.05)
促进其随后氧沉淀生成量。
铸造多晶硅中氧沉淀规律
结果讨论:
铸造多晶硅区别于直拉单晶硅在于,铸造多晶硅中存在较
高密度的位错和晶界等缺陷。而位错和晶界一般可以吸收硅中
过饱和的自间隙硅原子,这降低了铸造多晶硅中氧沉淀的临界 形核半径。另外一方面,由于位错或晶界一般不会影响间隙氧 在硅中的扩散速度,所以,铸造多晶硅中的位错和晶界主要是 通过降低氧沉淀的临界形核半径而促进氧沉淀的生成 。至于原 始氧浓度对氧沉淀的影响,则主要是由于高的原始氧浓度导致 小的氧沉淀临界形核半径,所以高氧样品中氧沉淀生成量较大。
多晶硅铸锭炉的工作原理

多晶硅铸锭炉的工作原理首先,硅料熔融是多晶硅铸锭炉的第一步。
在炉中加入高纯度的硅料,通常是硅块或硅片,然后通过电阻加热或感应加热的方式将硅料加热到熔融温度。
在炉内,硅料中的硅原子由于热能的作用开始振动,并逐渐失去其原子间的结合力。
当硅料的温度达到熔点时,硅原子之间的键强度完全消失,形成了液态硅。
其次,铸锭凝固是多晶硅铸锭炉的第二步。
当硅料熔融后,开始降低温度使其凝固。
凝固过程中,硅原子重新排列并形成了晶体的结构。
在这个过程中,硅原子重新组合并排列成晶格结构,形成了多晶硅。
凝固速度的控制对于提高多晶硅的晶粒度和降低杂质含量非常重要。
通常情况下,在凝固过程中还会控制硅料的搅拌,以避免结晶过程中的杂质团聚。
首先,多晶硅铸锭炉的炉体结构非常重要。
炉体通常由石墨材料制成,可以耐受高温和化学反应。
石墨材料的热传导性能较好,可以加热和散热硅料,确保温度均匀且稳定。
其次,温度控制是多晶硅铸锭炉的关键。
在炉内加热过程中,需要对温度进行精确的控制,以确保硅料能够均匀熔融。
在铸锭凝固过程中,温度的准确控制对于晶体的形成和生长非常重要。
通常通过在炉体中设置多个温度传感器,并通过反馈控制系统来实现温度控制。
最后,搅拌和保护气氛是多晶硅铸锭炉中的重要步骤。
通过搅拌硅料可以改善熔融过程中的均匀性,避免杂质团聚。
此外,为了保护熔融硅料不受氧化的影响,炉内通常需要保持特定的气氛,如氢气或氩气。
总结起来,多晶硅铸锭炉的工作原理包括硅料熔融和铸锭凝固两个主要步骤。
硅料经过加热熔化后,凝固过程中重新排列并形成晶体结构。
在实际操作中,需要考虑炉体结构、温度控制、搅拌和保护气氛等因素的影响。
第十章讲义铸造多晶硅
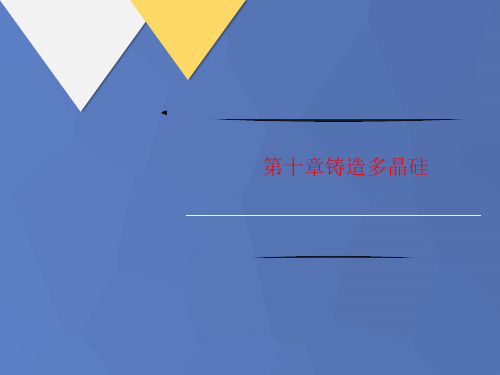
不断挤占单晶硅的市场,成为最有竞争
力的太阳电池材料。21世纪初已占50% 以上,成为最主要的太阳电池材料。
直拉单晶硅为圆片状,而硅片制备 的圆形太阳电池不能有效地利用太阳电 池组件的有效空间,相对增加了太阳电 池组件的成本。如果将直拉单晶硅圆柱 切成方块,制备太阳电池,其材料浪费 就增加,同样也增加了太阳电池组件的 成本。
晶硅,从而降低了太阳电池的光电转换 效率。
铸造多晶硅和直拉单晶硅的比较见表 10.1
自从铸造多晶硅发明以后,技术不 断改进,质量不断提高,应用也不断广 泛。在材料制备方面,平面固液相技术 和氮化硅涂层技术等技术的应用、材料 尺寸的不断加大。
在电池方面,SiN减反射层技 术、氢钝化技术、吸杂技术的开发 和应用,使得铸造多晶硅材料的电 学性能有了明显改善,其太阳电池 的光电转换率也得到了迅速提高。
铸造多晶硅的优缺点
缺
铸造多晶硅具有晶界、高密度的位
错、微缺陷和相对较高的杂质浓度,从 而降低了太阳电池的光电转换效率。
10.1 概述 10.2 铸造多晶硅的制备工艺 10.3 铸造多晶硅的晶体生长
10.1 概述
利用铸造技术制备多晶硅,称为铸 造多晶硅(multicrystalline silicon, mc-Si)。
直熔法
由图可知,硅原材料首先在坩埚中熔 化,坩埚周围的加热器保持坩埚上部温度 的同时,自坩埚的底部开始逐渐降温,从 而使坩埚底部的熔体首先结晶。同样的, 通过保持固液界面在同一水平面并逐渐上 升。使得整个熔体结晶为晶锭。在这种制 备方法中,硅原材料的熔化和结晶都在同 一个坩埚中进行。
直熔法
图10.4 直熔法制备铸造多晶硅用 晶体生长炉的结构
直熔法的冷却方式
铸造多晶硅制备技术的研究进展

(1 Department of Solar Energy Science and Engineering,Xinyu college,Xinyu 338000,
2 Department of Mechnial and Power Engineering!Nanchang Institute of Technology,Nanchang 330099)
tion and the electromagnetic continuous pulling In addition,the purification technique for phosphorus and boron in
metallurgical grade silicon is explained in details,formation and control of grain boundary and dislocation of multicrys—
为了降低坩埚对硅锭的污染。研究者提出了一种改进方 法。在坩埚内壁涂上si。N4膜层,以降低来自坩埚杂质的玷 污。同时.&。N.涂层还能起到一定的润滑脱模作用,因为硅 熔体在高温时与石墨发生反应,加之硅凝固过程中的体膨胀 作用,易造成硅锭与石墨模具的粘连,冷却后难以脱模,使用 si。N|涂层后硅熔体和坩埚内壁不粘结,这样既可以降低凝固 时产生的大量应力又能多次使用坩埚,从而降低了生产成 本。但最近美国的研究者Buonassisi等[2I]通过分析比较了 口-Si3N.涂层与铸造多晶硅中杂质的种类、相对浓度、含有杂 质颗粒的化学态和杂质分布状况及其形成机理后,认为在铸 造多晶体生长时,si。N。涂层中的金属与非金属杂质可能会 污染铸造多晶硅,并提出了相应解决措施:(1)减少mSi。N中 杂质含量;(2)改善口-Si3N的结构质量,使得在晶体生长时口- 鼠N中的分解物降到最低;(3)降低坩埚的表面面积与体积 的比率(如增大坩埚尺寸大小)。 1.2定向凝固法
多晶硅铸锭的晶体生长过程

多晶硅铸锭的晶体生长过程多晶硅铸锭的晶体生长过程在真空熔炼过后,还要经过一个降温稳定,就进入定向凝固阶段。
这个过程既是多晶硅的晶体生长过程,也能够对回收料和冶金法多晶硅料中含有的杂质进行进一步的提纯。
(一)定向凝固与分凝现象硅液中的杂质在硅液从底部开始凝固的时候,杂质趋向于向液体中运动,而不会停留在固体中。
这个现象叫做分凝现象。
在固液界面稳定的时候,杂质在固体中的数量与在液体中的数量的比值,叫做分凝系数。
分凝系数小于1的杂质,在进行定向凝固的时候,都会趋向于向顶部富集。
富集的数量和程度,取决于分凝系数的多少。
一般来说,金属杂质的分凝系数都在10-3以下(铝大约是0.08),所以,定向凝固方式除杂,对于金属杂质比较有效;而硼和磷的分凝系数分别为0.8和0.36,因此,硼和磷的分凝现象就不是太明显。
在定向凝固提纯的同时,考虑硅的长晶工艺,使得定向凝固后的硅能够成为多晶硅锭而直接进行切片,这就是将提纯与铸锭统一在一个工艺流程中完成了。
这也是普罗的提纯铸锭炉的重要提纯手段。
由于含有杂质的硅料和高纯料的结晶和熔液的性质都不太一样,因此,提纯铸锭炉所采用的热场与纯粹铸锭炉的热场是有区别的。
普罗新能源公司目前采用自己研制的提纯铸锭一体化的专利设计,比较成功地解决了这个问题,使得真空熔炼与铸锭是在一次工艺里完成的,既较好地解决了提纯的问题,也圆满地完成了铸锭的要求。
(二)晶体生长过程定向凝固分为以下四个阶段,包括:晶胚形成、多晶生长、顶部收顶、退火冷却。
晶胚形成在熔炼过后,要把硅溶液的温度降低到1440℃左右,并保持一段时间,然后,使坩埚底部开始冷却,冷却到熔点以下6-10℃左右,即1404-1408℃左右。
RDS4.0型的炉体降低底部温度的方法是降低底部功率,和逐渐打开底部热开关的方式。
与常规铸锭炉的提升保温体和加热体方式相比,由于不存在四周先开始冷却然后才逐步到中央的过程,因此,底部温度要均匀得多。
铸锭时,底部红外测温的数据不完全是硅液底部的温度,因为,该测点与坩埚底部的硅液还隔了至少一层坩埚,因此,红外温度仅能参考,还是要根据每台炉子各自的经验数据。
生产多晶硅的工作原理

生产多晶硅的工作原理
多晶硅生产的工作原理主要包括以下几个步骤:
1. 原料准备:首先,将高纯度的硅石通过破碎、磨粉等方式进行预处理,得到符合要求的硅粉。
2. 载体制备:将硅粉与少量添加剂混合,在高温条件下,通过化学反应将硅粉烧结成块状结晶硅,形成多晶硅的基础材料。
3. 铸锭制备:将块状结晶硅通过熔炼、浇铸等方法,将其熔化并倒入特制的铸锭模具中。
在凝固过程中,通过控制温度和冷却速率等参数,使熔态的硅逐渐结晶成为不规则形状的多晶硅铸锭。
4. 晶棒修整:将多晶硅铸锭进行切割,得到多个晶棒。
然后,对晶棒进行粗修整、中修整和精修整等工艺处理,使其尺寸和形状更加精确。
5. 晶棒切片:将修整后的晶棒进行切片,即将晶棒垂直切割成薄片,每片厚度通常为0.2-0.3毫米。
这些薄片即为多晶硅太阳能电池的主要材料。
6. 太阳能电池制造:利用多晶硅薄片制造太阳能电池。
首先,在薄片上形成p-n 结构;然后,通过在片上涂覆导电膜、铝等材料,形成电池电极;最后,进行电池的封装和测试,制成成品太阳能电池。
需要注意的是,多晶硅的生产过程是一个复杂的工序,不同的生产厂家和工艺流程可能会有所不同。
以上仅为一般多晶硅生产的工作原理的简化描述。
定向凝固制备铸造多晶硅的原理及应用综述
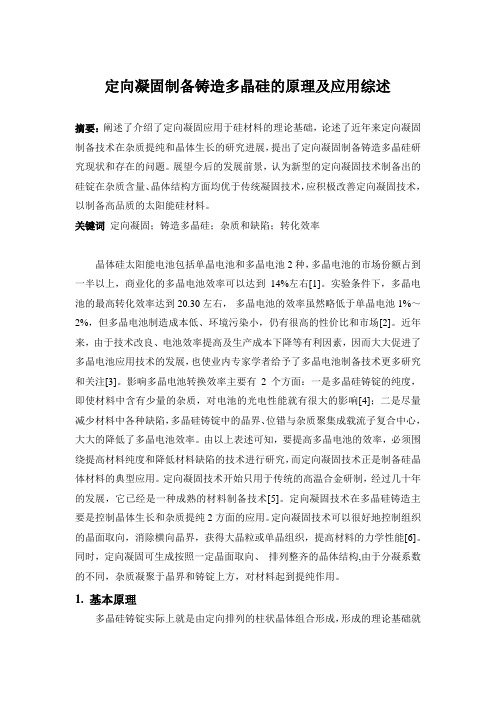
定向凝固制备铸造多晶硅的原理及应用综述摘要:阐述了介绍了定向凝固应用于硅材料的理论基础,论述了近年来定向凝固制备技术在杂质提纯和晶体生长的研究进展,提出了定向凝固制备铸造多晶硅研究现状和存在的问题。
展望今后的发展前景,认为新型的定向凝固技术制备出的硅锭在杂质含量、晶体结构方面均优于传统凝固技术,应积极改善定向凝固技术,以制备高品质的太阳能硅材料。
关键词定向凝固;铸造多晶硅;杂质和缺陷;转化效率晶体硅太阳能电池包括单晶电池和多晶电池2种,多晶电池的市场份额占到一半以上,商业化的多晶电池效率可以达到14%左右[1]。
实验条件下,多晶电池的最高转化效率达到20.30左右,多晶电池的效率虽然略低于单晶电池1%~2%,但多晶电池制造成本低、环境污染小,仍有很高的性价比和市场[2]。
近年来,由于技术改良、电池效率提高及生产成本下降等有利因素,因而大大促进了多晶电池应用技术的发展,也使业内专家学者给予了多晶电池制备技术更多研究和关注[3]。
影响多晶电池转换效率主要有2个方面:一是多晶硅铸锭的纯度,即使材料中含有少量的杂质,对电池的光电性能就有很大的影响[4];二是尽量减少材料中各种缺陷,多晶硅铸锭中的晶界、位错与杂质聚集成载流子复合中心,大大的降低了多晶电池效率。
由以上表述可知,要提高多晶电池的效率,必须围绕提高材料纯度和降低材料缺陷的技术进行研究,而定向凝固技术正是制备硅晶体材料的典型应用。
定向凝固技术开始只用于传统的高温合金研制,经过几十年的发展,它已经是一种成熟的材料制备技术[5]。
定向凝固技术在多晶硅铸造主要是控制晶体生长和杂质提纯2方面的应用。
定向凝固技术可以很好地控制组织的晶面取向,消除横向晶界,获得大晶粒或单晶组织,提高材料的力学性能[6]。
同时,定向凝固可生成按照一定晶面取向、排列整齐的晶体结构,由于分凝系数的不同,杂质凝聚于晶界和铸锭上方,对材料起到提纯作用。
1. 基本原理多晶硅铸锭实际上就是由定向排列的柱状晶体组合形成,形成的理论基础就是定向凝固原理。
- 1、下载文档前请自行甄别文档内容的完整性,平台不提供额外的编辑、内容补充、找答案等附加服务。
- 2、"仅部分预览"的文档,不可在线预览部分如存在完整性等问题,可反馈申请退款(可完整预览的文档不适用该条件!)。
- 3、如文档侵犯您的权益,请联系客服反馈,我们会尽快为您处理(人工客服工作时间:9:00-18:30)。
1 实验过程
选取了一批德国拜耳公司所生产的 P 型铸造多 晶硅底部样品( C S 和其他厂家所生长的 P M 一i ) 型单 晶硅样品(Z, C)使用四探针测试样品的原始电阻率, 使用 M R 测试样品的原始氧浓度和碳浓度。原始 数据如表 1 所示:
表 1 实验所用硅片中原始氧, 碳浓度和电阻率大小
样 品类型和编号
取 拉 硅, 代直 单晶 成为最主 太阳 池材料〔1 要的 电 10 , 2
但是与直拉单晶硅太阳电池相比, 铸造多晶硅太阳 电池的转换效率较低。目前, 产业界中直拉单晶硅 太阳电池的转换效率一般在 1一 6 5 1%左右, 而铸造
多晶 硅太阳电池的 转换效率大约在 1一4 究其 3 1%。
…
,. .
, __ 中 令 / ‘宁 : _一 幸 ,
创卜沪甲 . 创巨尹甲
声,
.
.. -一
立立宜立盆。自。 二一二一一一
2 4 0 0
0
6 8 1 0 1 0 10 1 0 0 0 0 2 4 6
的 形成[, 1 7如表 所示。虽然目 1 前对于热施主的形
成机理尚未清楚, 从而提出了很多种热施主模型, 但 是其中一点是大家所肯定的, 那就是硅中间隙氧的
e P to imti , r st a olkR . r holc e l ht , s u o【 ] . vt ars i y t n t o a a s o a d o u
热处理时间/ h
图 1 各种原生晶体硅样品中热施主浓度
随热处理时间的变化曲线
F . u e ot m l o o ettn r s hradnrc cnao i 1 v f g C e o s ri n
v. an t it i r t l e h d e ns p s san lg n f e a e n i i e m e m
C- ( zi S 位错)F, (, F) Z
0
取其中一批样品(, , D. F) A, G, E+ 在 B , , , ,
60 5℃下退火 05, . 以消除原生热施主。然后, h 将这
万方数据
太
阳
能
学
报
2卷 6
些样品和没有经预处理的样品(2 B, D, 预处理和未经过此预处理的各种样品中热施主浓度 A , C, E, 2 2 z 2 我们可以 瓦) 同时进行40 5℃下的退火处理, 保护气氛为氮气。 随热处理时间的变化曲线。从这两个图, 每隔 1 取样测试样品的电阻率, 0 h 记录电阻率的变 发现原生热施主的存在不影响随后热施主形成规 律。所有样品中热施主的浓度都是先随着热处理的 化, 热施主浓度由热处理前后电阻率变化所对应载 时间而增加, 热处理 1 h 3 左右时到达最大值, 0 尔后 流子浓度的差值。 随着热处理的继续进行而迅速降低。但是对于不同 2 结果和讨论 种类的样品, 其中氧沉淀最大生成量显著不同, 在含 碳量低, 无位错和晶界的单晶硅 B 和B 样品中, 1 2 经 由于晶体生长过程中会生成热施主, 而这些热 1h 3 热处理所形成的热施主浓度最大, 0 大约为 11 . 施主可以在 60 5℃下热处理 3mn 0 i消除。表 2 显示 x c-。与此相对比的是相似单晶硅样品 C 16 3 0 m 1 l 所使用硅片中原始热施主的浓度。从该表中可以发 2 其热施主的生成量则最小, 仅为 6 x 现, 在铸造多晶硅底部的样品中存在着高达 1 x 和 C 样品中, . 4 0 c- 1 m 。这两种样品(lB)C,2由于含有不 B,2(lC) 15 ’ 原生热施主, 0 c- 'm 的 这不仅与高浓度的自 间隙 14 3 同的原始氧浓度, 而所生成热施主量的显著不同, 这 氧有关, 还与铸造多晶硅长达 4h 0 左右的晶体生长
原因, 主要在于铸造多晶硅中存在着高密度的缺陷
和高 浓度的 质, 界、 错、 碳等等[。 杂 如晶 位 氧、 3 虽然 ]
清洁的位错或晶界对材料的电学Байду номын сангаас能没有很大的影
响闭, 但是一旦缺陷和杂质相互作用就会显著影响
材料的电学性能, 所以研究铸造多晶硅中缺陷和杂 质的相互作用显得十分必要。 氧和碳是铸造多晶硅中两种非常重要的杂质元 素。关于这两种杂质在直拉单晶硅中性质的研究已 经有几十年的历史, 对它们及其复合体或沉淀相有 了比较深人地理解, 如热施主、 新施主、 氧沉淀、 碳氧
万方数据
4 期
俞征峰等: 铸造多晶硅中热施主形成规律
列样品, 虽然初始氧浓度与 E F , 系列样品中氧浓度 相近, 但是所形成的热施主较低。这表明, 碳会显著
抑制。
的形成规律, 得出以下结论: 1原始氧浓度对热施主形成的影响最大; )
综上所述, 可以发现, 原始氧浓度对热施主形成 规律的影响最大, 其次是碳和位错, 而晶界则几乎没 有影响, 而且氧和位错是促进热施主的形成, 碳则是 抑制作用, 其抑制作用甚至强于位错的促进作用。 当硅片在 0 一 0℃热处理时, 30 50 过饱和的间隙 氧会相互聚集形成热施主以降低化学势。铸造多晶 硅硅锭长时间的生长过程, 同样也是硅锭的热处理 过程。对于铸造多晶硅底部, 一般会经历长达 2 多 0 个热处理退火, 这样就导致较高浓度的原生热施主
B1 C1
D
‘. 1
二M / I
0 0 4 0 2 0 6
,, ,幸
一・ 杏 众 杏二
1 0 4 1 0 2 1 0 6
,1 八」
1 1
6 1 〕 0 川
热处理时间/ h
E
F 1 3
图 2 经 60 5℃热处理 3mn 0 i后各种晶体硅样品 中热施主的浓度随热处理时间的变化
50
无 该 处 理 , 日
F . Crs e ad o o eri l rc c ttn i2 v otr o s na g ue f hm n n o
v. e n t e h d e n s l i r t p s s ana g i t fe a e n l i n i m e m
第2卷 第4 6 期
20 年 8 05 月
阳 能 学 报
E E G A S L R S N C N R I E A I S I A O I
V l 6 N . o. o4 2 , A g 05 ,20 u.
文章编号: 24 0 20 05- %( 5 0 0
铸造多晶硅中热施主形成规律
俞征峰,席珍强, 杨德仁,阀端麟
影响最大。实验还发现, 60 05 退火处理可以消除部分原生热施主,原生热施主对于随后的热施主的形 在 59 . 0 h
成规律没有明显影响。
关健词: 铸造多晶硅;氧; 热施主
中图分类号 T 54 K1 文献标识码 :A
0 引 言
最近, 铸造多晶硅以其较高的性价比已经成功
的变化, 从而揭示热施主的生成规律。
图1 和图 2 分别是在 40 5 ℃下经过 60C mn 5' 3 i 0
其次, 对比样品( lB ) A , , B , 和( lA )虽然在这 2 2 两种晶体硅中含有非常相近的原始氧浓度 , 但是在 铸造多晶硅中所形成热施主最大浓度低于直拉单晶 硅中热施主的最大生成量, 如图 1 和图2 。这表明: 位错, 晶界或碳都可能会抑制热施主的形成。但究 竟是位错, 晶界还是碳主要抑制了热施主的生成? 我们又分别采用了4 种不同的样品研究了其中的热 施主形成规律。样品(lE ) F, 中, E , 和(lF) 虽然 F 2 2 系列的原始样品中含有晶界, 但是其中热施主生成 规律与 E系列样品中热施主形成规律相似, 如图 1 和 2这表明晶界对热施主的形成规律没有明显的 , 影响。同时, 在这两种样品中所形成的热施主浓度 都明显高于 C系列样品中热施主的最大形成浓度, 这表明位错会促进热施主的形成。另外, 对于 D系
M 一 i 凡, C S 人, ) (
[ix 0 sx1 ol 1 [ ] 0 电阻率 17 C "
/ - c 3 / - m c 3 m
1 0 0.
1 0 0.
‘. 1 0
0
/ ,"m a c
, 1
:
0
7
…
4
C- ( zi S 无位错)B, z (, B) C- ( zi S 无位错)C, (GQ) C- ( zi S 位错)D ,l (, ) D C- ( zi S 位错, 晶界)E, (,
F) 2
9 1. 1
4
山. 1
 ̄、
:
甘
复 合体等[。虽然, 5 1 对铸造多晶硅中氧沉淀的形成 规律 一 做了 些研究[1 很少 6, , 但是 人研究 7 铸造多晶 硅
中热施主的形成规律, 特别是晶界、 位错和碳对热施 本实验采用对比方法, 用四探针仪和傅立叶红 外仪(M ) F 研究铸造多晶硅中电阻率和氧、 碳浓度
20
wh p - n m a6 0 0mn 9 f 30 i i t r a e g 5 o t h e n d t r e
.一
・竺
0 1\ 侧 径 州 樱 藕
30 60 90
。
_ _ .. .
.滚
尹 .
样品编号
已
表明原生氧浓度对热施主形成规律的影响最大。
10 5
.. x扩C预 处 理
M 2 10
一.一 A1
・竺 0 1\ 侧 说
一.一 :1 3
目
原生热施主浓度/ ' m 3 / 4 1 c- 0
州 樱 臻
}且 0
60 3a
_ .,. . 声 - .一
, .
_ 声
A1 1 4
时间有关。
表2 各种硅片中原生热施主的浓度
Tb 2 oc ttn s r n ml o nao oa g w t radnr al Cne ri f o h e - e o s it d e n s p s n i r t l h fe a e e m