物料衡算
物料衡算

物料衡算物料衡算的准则就是质量守恒定律,即“进入一个系统的全部物料必等于离开这个系统的全部物料,再加上过程损失量和在系统中积累量”。
依据质量守恒定律,对研究系统作物料衡算,可由下式表示[13]:∑G进=∑G出+∑G损+∑G积其中式中:∑G进——输入物料量总和;∑G出——输出物料量总和;∑G损——总的物料损失量;∑G积——系统中的积累量。
根据设计任务,苯酐生产能力为80000吨/年,产品纯度达到99.9wt%按照8000小时开工计算,每小时的生产能力:80000×1000×99.9%/8000= 9990kg/h3.1 反应器中氧化反应的物料衡算3.1.1 氧化反应过程的衡算基准本次设计以每小时生产9990kg为基准,进料量9400kg/h,转化率99.8%;生成苯酐的选择性约为0.8;空气与邻二甲苯进料比为9.5:1;主要副产品为苯酞、顺酐、苯甲酸、柠槺酐、二氧化碳、一氧化碳等。
3.1.2 氧化反应过程的物料衡算图画出衡算方框图,标出有关计算目标,然后进行计算:图3-1 反应过程物料衡算图3.1.3 氧化反应过程的物料衡算:邻二甲苯与空气催化氧化的主反应式:106 32 148 18x 3y 9990 z所以主反应中:(1)邻二甲苯消耗量:9990148106=x x = 7155 kg/h 氧气消耗量:9990148y 332=⨯ y =6480 kg/h 水的生成量: 9990148z 318=⨯ z = 3645 kg/h (2) 邻二甲苯转化率为99.8%,且邻二甲苯的进气量为9400kg/h ,所以: 邻二甲苯生产苯酐的选择性为:7155/9400/99.8%=77.27%。
(3)设计进料空邻比为9.5:1,所以空气进料量计算:5.91w 9400=w 空 =89300 kg/h 空气中 O 2所占的比例为21%,所以工艺空气中氧气的进料量:w 氧 = 89300×21%= 18753kg/h 。
第三章-物料衡算

第三章物料衡算3.1 概述1.概念:根据质量守恒定律,以生产过程或生产单元设备为研究对象,对其进出口处进行定量计算,称为物料衡算。
2.意义:通过物料衡算可以计算原料与产品间的定量转变关系,并计算各种原料的消耗量,各种中间产品、副产品的产量、损耗量及组成。
物料衡算是所有工艺计算的基础,通过物料衡算可确定设备容积、台数、主要尺寸,同时可进行热量衡算、管路尺寸计算等。
3.2 物料衡算的基础物料衡算的基础是物质的守恒定律,即进入一个系统的全部物料量必等于离开系统的全部物料量,再加上过程中的损失量和在系统中的积累量。
亦即:∑m1=∑m2+∑m3+∑m4式中∑m1—输入物料量总和,kg;∑m2—输出物料总量和,kg;∑m3—物料损失量总和,kg;∑m4—物料积累量总和,kg;当系统内物料积累量为零时,上式可写成:∑m1=∑m2+∑m33.3 物料衡算的基准1. 间歇式操作过程:常采用一批原料为基准进行计算2. 连续式操作过程:可采用单位时间产品数量或原料量为基准进行计算。
3. 本设计的生产方式为间歇式生产。
4. 包装形式:纸板桶,25kg/桶。
3.4 物料衡算的过程3.4.1 生产规程本次设计内容为化学原料药多功能生产车间工程项目,该车间拟生产阿齐沙坦〔产品年产量为25t/a〕。
该工厂每年根据节假日、设备维护与工艺验证时间,全年生产时间为250天。
生产组织根据车间工艺要求可采用以下倒班方式:倒班方式一:3 班制/天,每天生产时间24 h〔0:00-24:00〕,每周工作5 天;倒班方式二:2 班制/天,每天工作16 h〔7:00-23:00〕,每周工作7 天;注:倒班方式任选其中1 种或2 种组合;结晶釜日常连续运行不纳入倒班时间。
3.4.2 原辅料衡算过程1. 阿齐沙坦原辅料衡算过程每批产生硫辛酸4 桶,包装规格25kg /桶,一批的产量为:4×25=100kg生产一批阿齐沙坦需要AZ-5量为:100÷÷÷÷÷÷÷×0.99=270.29kg杂质含量:273.02-270.29=2.73kg (1) 环合工序物料衡算投料量:×0.5=136.51kg×0.80=218.42kg×0.2=54.60kg×0.20=54.60kgAZ-6(2) 加成工序物料衡算投料量:×0.91=248.4 5kg÷0.8=310.56kg×0.2=62.11kg环合工序物料衡算结果(2) 加成工序物料衡算投料量:×0.91=248.4 5kg×1.02=253.42kg盐酸羟胺×1.20=298.14kg×4.80=1192.56kg×3.66=909.33kg乙醇:248.4 5×加成工序物料衡算结果(3) 缩合工序物料衡算投料量:××0.2=37.28kg×0.28= 52.17kg×4.12=767.71kg×缩合工序物料衡算结果(4) 环合工序物料衡算投料量:××3.20=488.95kg×÷×环合工序物料衡算结果(5) 水解工序物料衡算投料量:××6.6=816.87kg×0.25=30.94kg×0.15=18.57kg水解工序物料衡算结果(6) 精制工序物料衡算①投料量:××4.00=435.66kg×0.10=10.89kg(7) 粉碎包装按要求粉碎、总混、内包、外包、入库。
物料衡算

4.2.2
衡算基准
1、时间基准 对连续稳定流动体系,以单位时间作基准。该基准 可与生产规模直接联系 对间歇过程,以处理一批物料的生产周期作基准。 2、质量基准 对于液、固系统 ,因其多为复杂混合物选择一定 质量的原料或产品作为计算基准 。 若原料产品为单一化合物或组成已知,取物质量 (mol)作基准更方便。
要注意: (1)对多个设备过程,并非每个体系写出的所有 方程式都是独立的; (2)对各个体系独立物料衡算式数目之和>对总过 程独立的物料衡算式数目。 过程独立方程式数目最多=组分数×设备数 过程由M个设备组成,有C个组分时则最多可能列 出的独立物料衡算式的数目 = MC个。
对全塔进行总物料衡算得
D+W=200 (a)
对苯进行物料衡算得
DxD +0.01W =2000.4 (b)
由塔顶馏出液中苯的回收率得
DxD =2000.4 0.985 (c)
联解式(a)、(b)和(c)得
D=80kmolh-1,W=120 kmolh-1,xD=0.985
3、体积基准
对气体选用体积作基准。通常取标况下体积
Nm3(Hm3)
在进行物料衡算或热量衡算时,均须选择相
应的衡算基准。合理地选择衡算基准,不仅
可以简化计算过程,而且可以缩小计算误差
基准选取中几点说明:
(1)上面几种基准具体选哪种(有时几种共用) 视具体条件而定,难以硬性规定。
(2)通常选择已知变量数最多的物料流股作 基准 较方便。 (3)取一定物料量作基准,相当于增加了一个已 知条件(当产物和原料的量均未知时,使隐条件明 朗化)。 (4)选取相对量较大的物流作基准,可减少计算 误差。
化工中物料衡算和热量衡算公式
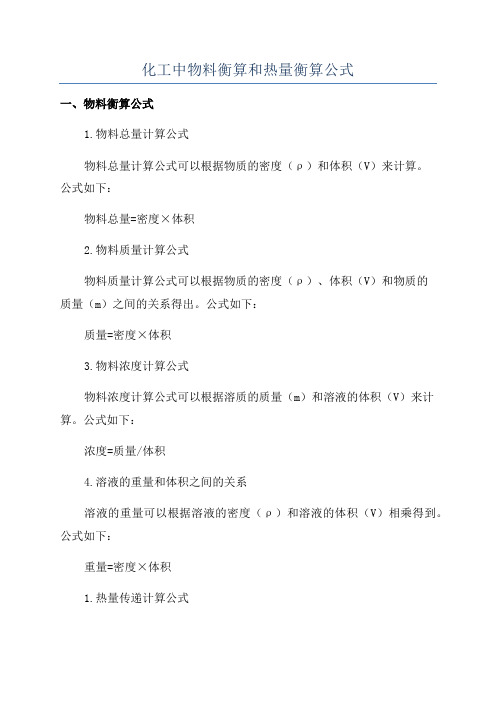
化工中物料衡算和热量衡算公式一、物料衡算公式1.物料总量计算公式物料总量计算公式可以根据物质的密度(ρ)和体积(V)来计算。
公式如下:物料总量=密度×体积2.物料质量计算公式物料质量计算公式可以根据物质的密度(ρ)、体积(V)和物质的质量(m)之间的关系得出。
公式如下:质量=密度×体积3.物料浓度计算公式物料浓度计算公式可以根据溶质的质量(m)和溶液的体积(V)来计算。
公式如下:浓度=质量/体积4.溶液的重量和体积之间的关系溶液的重量可以根据溶液的密度(ρ)和溶液的体积(V)相乘得到。
公式如下:重量=密度×体积1.热量传递计算公式热量传递计算公式可以用于计算传热功率(Q)和传热面积(A)之间的关系。
公式如下:Q=h×A×ΔT其中,h为传热系数,ΔT为温差。
2.物料的热量计算公式物料的热量计算公式可以根据物料的质量(m)、比热容(Cp)和温度变化(ΔT)来计算。
公式如下:热量=质量×比热容×温度变化3.水的蒸发热计算公式水的蒸发热计算公式可以根据水的质量(m)和蒸发热(ΔHvap)来计算。
热量=质量×蒸发热三、补充说明1. 密度(ρ)是物质单位体积的质量,常用的单位有千克/立方米(kg/m^3)或克/立方厘米(g/cm^3)。
2. 比热容(Cp)是物质单位质量的热容量,表示单位质量物质温度升高1℃所需的热量,常用的单位是千焦/千克·℃(kJ/kg·°C)或焦/克·℃(J/g·°C)。
3.传热系数(h)是衡量热传导性能的参数,表示单位面积上的热量流入或流出的速率,常用的单位是瓦特/平方米·℃(W/m^2·°C)。
4.温度变化(ΔT)是物质的温度差,常用的单位是摄氏度(℃)或开尔文(K)。
5. 蒸发热(ΔHvap)是物质从液态转变为气态所需的热量,常用的单位是焦耳/克(J/g)或千焦/千克(kJ/kg)。
物料衡算计算公式

物料衡算计算公式物料衡算是指根据产品的设计要求和生产工艺流程,计算出生产所需的物料数量和成本的过程。
其目的是为了保证生产的顺利进行,避免物料的浪费和成本的过度支出。
物料衡算的计算公式主要包括以下几个方面:1.总物料需求量计算公式总物料需求量=产品数量×单位产品所需物料数量这个公式用于计算生产特定数量产品所需的物料数量。
其中,产品数量是指计划生产的产品数量,单位产品所需物料数量是指生产一个产品所需的各种物料的用量。
2.物料补给计算公式物料补给=总物料需求量-物料库存量物料补给是指为满足生产需求而需要从供应商处采购的物料数量。
物料库存量是指当前仓库中已有的物料数量。
3.物料成本计算公式物料成本=物料单价×物料补给量物料成本是指为满足生产需求而采购物料所需支付的费用。
物料单价是指单个物料单位的价格,物料补给量是指需要从供应商处采购的物料数量。
4.物料利用率计算公式物料利用率=(总物料需求量-物料浪费量)/总物料需求量物料利用率是指生产过程中物料的有效利用程度。
物料浪费量是指因为工艺操作不当、设备故障等原因导致物料的损失量。
5.物料损耗计算公式物料损耗=总物料需求量-实际使用量物料损耗是指在生产过程中由于各种原因而导致的物料的损失量。
实际使用量是指实际上被用于生产的物料数量。
6.物料价格调整计算公式调整后物料价格=原物料价格×调整系数物料价格调整是指根据市场行情或其他因素调整物料价格的过程。
调整系数是一个根据实际情况确定的数值,用于对原物料价格进行调整。
总之,物料衡算的计算公式主要包括总物料需求量计算、物料补给计算、物料成本计算、物料利用率计算、物料损耗计算和物料价格调整计算等。
通过合理地运用这些公式,可以对物料需求和成本进行科学的计算和控制,从而提高生产效率和降低成本。
工厂设计-物料衡算
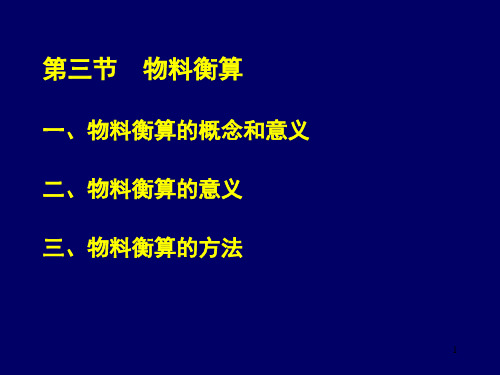
➢ 物料衡算是化工计算的主要内容之一。 ➢ 化工计算包括工艺设计中的物料衡算、能量
衡算、设备选型及计算三部分内容。
➢ 物料衡算是工艺计算的基础,在整个工艺计 算工作中开始的最早,并且是最先完成的项 目。
➢ 当生产方法确定并完成了工艺流程示意图设 计后,即可进行物料衡算。
➢ 由此设计工作由定性分析转入定量计算。
4.2.3 食品机械结构特征代号是表示食品机械的主要工作部件 动作的形式(如冲、印、滚、压等),用汉语拼音第一个大写 字母表示。
4.2.4 食品机械生产能力代号是表示食品机械在单位时间内, 所加工出的产品的实际能力,用阿拉伯数字表示。应以kg/h、 L/h、m/h、m3/h、瓶/h、只/h等为计量单位。
18
■ 物料衡算是设备选型的根据,而设备选型则 要符合工艺的要求。设备选型是保证产品质量 的关键和体现生产水平的标准,又是工艺布置 的基础,并且为动力配电,水、汽用量计算提 供依据。
■设备选型应根据每一个品种单位时间(小时 或分)产量的物料平衡情况和设备生产能力采 确定所需设备的台数。若有几种产品都需要共 同的设备,在不同时间使用时,应按处理量最 大的品种所需要的台数来确定。对生产中的关 键设备,除按实际生产能力所需的台数配备外, 还应考虑有备用设备。后道工序设备的生产能 力要略大于前道工序,以防物料积压。
豆制品 加工机
械
冷饮加 工机械
肉类蛋 品加工
机械
G
糕点(饼干)成型加工机械及包馅、油炸、蒸制等 加工机械和包装机械
T
糖果制品成型加工机械和设备及熬糖、包糖等机械
D
豆类、淀粉类加工机械及其除杂、清洗、破碎等机 械
L
小型汽车水饮料加工设备及冷冻食品等加工机械
物料衡算
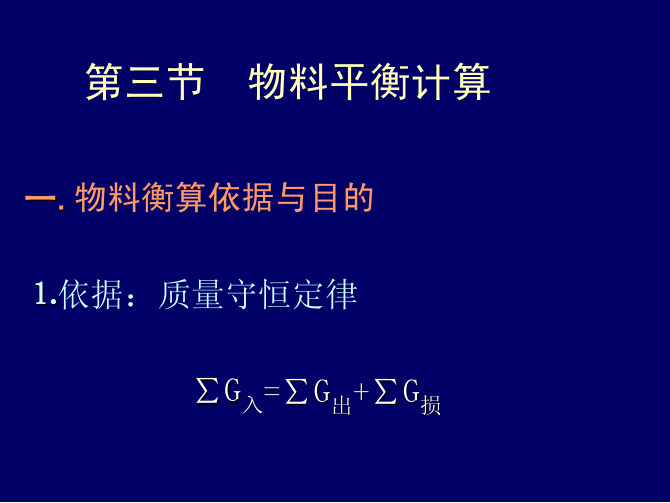
面 粉 875kg 水 315kg 面 粉 350kg
酵 母 25kgkg 接种面团 1372.5kg
水 472.5kg 盐 25kg 油 50kg 切块损 失 52.2kg
可通过工厂实际数 据或实验得来。 注:部分原料工艺 损耗率及原料折用 率见书
糖 62.5kg
二次调粉后面团 2175kg 拌干粉 量 25kg 搓圆后面团 2127.8kg 湿面包坯 2147.8g 成品 1933.02k
损失 214.78k g
P48
三.物料衡算 实例
⒈年产3000T碳酸饮料厂物料衡算
⑴原料成分、产品标准及产品方案 原料成分 产品标准: 产品方案:
序 号 1 2 3 产品名 称 桔汁汽 水 可乐汽 水 小香槟 汽水 年产 量(T) 1400 800 800 一 月 二 月 三 月 四 月 五 月 六 月 七 月 八 月 九 月 十 月 十 一 月 十 二 月
(其中30%—假设稀奶油中F含量)
3)假定脱脂乳中脂肪含量0.05% 4)每吨原料乳可得30%脂肪含量的稀奶油量
1000×3.5%=(1000-X)×0.05%+30%X
X=1000×(3.5-0.05)/(30-0.05)=115kg 5)每吨原料乳可得脱脂乳量
1000×(3.5-0.05)/(30-0.05)=885kg 或1000-115=885kg
3.班产12.5T原汁猪肉罐头工厂
猪肉原料要求 成品标准要求及规格 物料计算过程: (1) 原汁猪肉成品规格397g。 (2) 班成品产量12.5T。 (3) 成品罐数 (4) (5) (6) (7) 需每箱罐数48罐 需纸箱数
=31486.15/48=656(个)
→确定罐型
名词解释物料衡算法

名词解释物料衡算法
物料衡算法(Material Balance Method)是一种基于质量守恒定律的物料管理方法,它用于计算和监控生产过程中的物料流动和消耗。
物料衡算法的核心原则是,进入系统的物料总量必须等于系统中物料的变化量加上离开系统的物料总量。
这种方法可以用来分析生产过程中的物料效率,识别物料的损失和浪费,以及优化物料的使用。
物料衡算法的关键步骤包括:
1. 定义系统边界:确定物料衡算的起始点和结束点,即物料的流入和流出点。
2. 物料流量测量:测量进入和离开系统的物料的数量和质量。
3. 物料平衡计算:计算物料的流入量、流出量和系统内的变化量,确保它们之间符合质量守恒定律。
4. 数据分析:分析物料平衡数据,识别物料的损失、效率低下或不符合预期的流动路径。
5. 优化建议:基于物料平衡分析的结果,提出改进物料管理的建议,如减少浪费、提高物料利用率等。
物料衡算法在化工、冶金、食品和饮料等行业中广泛应用,有助于企业提高资源利用效率,降低成本,并实现可持续发展。
1。
- 1、下载文档前请自行甄别文档内容的完整性,平台不提供额外的编辑、内容补充、找答案等附加服务。
- 2、"仅部分预览"的文档,不可在线预览部分如存在完整性等问题,可反馈申请退款(可完整预览的文档不适用该条件!)。
- 3、如文档侵犯您的权益,请联系客服反馈,我们会尽快为您处理(人工客服工作时间:9:00-18:30)。
3.物料衡算生产过程的总物料衡算3.1.1生产能力年生产商品味精(99%)50000t,折算为100%味精为49500t/a。
日生产商品味精(99%):50000/320=(t/d),折算为100%味精为155t/d。
3.1.2计算指标(以淀粉质为原料)计算指标[10]见表。
表计算指标项目指标淀粉糖化转化率%发酵产酸率(浓度)11%发酵对糖转化率60%培养菌种耗糖为发酵耗糖的%谷氨酸提取收率96%精制收率95%商品淀粉中淀粉含量86%发酵周期(含辅助时间)40h全年工作日320d3.1.3物料衡算(1)1000kg纯淀粉理论上产100%MSG量1000××%×=1153.5kg式中%——谷氨酸对糖的理论转化率——纯味精相对分子质量纯谷氨酸相对分子质量=184147=(2)1000kg纯淀粉实际产100%MSG量1000××%×60%×(100%-%)×96%×95%×=749.6kg (3)1000kg商品淀粉(含量86%的玉米淀粉)产100% MSG量×86%=644.7 kg(4)淀粉单耗①1t100%MSG消耗纯淀粉量1000749.6=t ②1t100%MSG实耗商品淀粉量1000644.7= t/t ③1t100%MSG理论上消耗纯淀粉量10001153.5= t/t④1t100%MSG理论上消耗商品淀粉量0.866986%= t/t (5)总收率可按以下两种方法计算①)749.6)1153.5100%100%64.98% kgkg⨯⨯实际产量(理论产量(==②98.5%60%98.5%96%95%100%64.98%81.7%⨯⨯⨯⨯⨯=(6)淀粉利用率1.008100%65%1.5511⨯=(7)生产过程总损失100%-65%=35%(8)原料及中间品计算①品淀粉或淀粉乳用量:日产100%味精155t,单耗商品淀粉,日耗商品淀粉量155×=d相当日耗100%淀粉:×86%= t/d如使用°Bé,含淀粉30.113g/dL的淀粉乳,日耗量为30%=d(30.113g/dL≈30%)②糖化液量:日产纯糖量×86%××%= t/d只算为30%或34g/dL的糖液30%=; 34= m3③发酵液量:发酵液中纯谷氨酸量×60%×(100%-%)=d折算为谷氨酸11g/dL 的发酵液量11=d×=d 为发酵液相对密度)④提取谷氨酸量:产纯谷氨酸×96%=d折算为90%湿谷氨酸量90%= t/d3.1.4总物料衡算结果总物料衡算结果汇总见表。
表 总物料衡算结果(年产2万t 味精)原料规格玉米淀粉原料生产1t100%MSG日(耗)产量(t/d )玉米淀粉/t 86% 糖液/t 30% 谷氨酸/t 90%味精/t100%155制糖工序的物料衡算(1)淀粉浆量及加水量 淀粉加水比例为1:,1000kg 工业淀粉产淀粉浆1000×(1+)=2800kg加水量为1800kg 。
(2)粉浆干物质浓度100086%100%30.7%2800⨯⨯=(3)液化酶量 使用耐高温α-淀粉酶(液体,20000U/mL ),加酶量10 U/g 干淀粉。
1000kg 干淀粉加酶量1000100010500mL 0.5L 2000⨯⨯==0.5L 液化酶质量约为0.6kg 。
(4)CaCl 2量 一般加量为干淀粉的%,即1000kg 干淀粉加CaCl 21000×%=1.5kg(5)糖化酶量 一般加糖化酶量为120 U/g 干淀粉,如液体糖化酶为100000 U/mL ,则每1000kg 干淀粉加糖化酶量100010001201200mL 1.2L 100000⨯⨯==1.2L 糖化酶质量约为1.5kg 。
(6)糖液产量100086% 1.1198.5%3134kg 30%⨯⨯⨯=30%的糖液相对密度,相当于×30%=34g/dL3134/=2768L(7)过滤糖渣量 湿渣(含水70%)10kg ,折干渣量10×(1-70%)=3kg(8)生产过程进入的蒸汽冷凝水及洗水量3134+10--2800=340.4kg(9)衡算结果(年产5万吨味精) 根据总物料衡算,按日投入商品淀粉,物料衡算汇总见表。
表 制糖车间物料衡算汇总表项目 物料比例/kg日投料量/t项目 物料比例/kg日产料量/t商品淀粉 1000 30%糖液 3134 配料水 1800 滤渣 10 液化酶 CaCl 2 糖化酶蒸汽冷凝水及洗水量累计31443144发酵工序的物料衡算(1)发酵培养基和用糖量 1000kg 商品淀粉,可产100%糖量1000×86%××%=940kg其中初始发酵定容用糖占53%,即940×53%=498kg (100%糖);流加补量用糖占47%,即940×47%=442kg (100%糖)。
初糖用30%的糖液配料:4981660kg 30%=,即4981465L 34g/dL=初糖配13g/dL,初定V=498kg3831L13g/dL=,13g/dL糖液相对密度,则3831×=4023kg流加补糖用60 g/dL浓糖浆(相对密度),则442737L60g/dL=,737×=901kg(2)发酵配料每吨商品淀粉产100%糖940kg,发酵配料用各种营养物比例见表。
表发酵配料用各种营养物比例成分数量(t)数量(kg)玉米浆(CSL)糖蜜MgSO4·7H2OKClNa2HPO4·12H2O其他(生物素等)总计22(3)配料用水初始配料时培养基含糖量不低于20%,向30%的糖液中加水量为30% 166020%1830kg(-)=(4)接种量发酵初定容3831L,种量为10%,即383L。
种子液相对密度,则383×=391kg在391kg种液中含有100%糖14kg(用30%糖液46.7kg)、玉米浆5.2kg、甘蔗糖蜜3.4kg、K2HPO40.68kg、蒸汽及水335.02kg。
(5)连续灭菌过程进入的蒸汽及补水量4023-1660-22-830-391=1120kg(6)发酵过程中加入99%液氨量 1t商品淀粉产100%糖940kg,产100%谷氨酸940×60%×%×96%=533.3kg式中 96%——谷氨酸提取收率一般发酵耗氨量为谷氨酸量的,即:×=160kg99%液氨在35℃相对密度为,160/=272L(7)加消泡剂量 一般1t 谷氨酸加消泡剂5kg ,则533.3×5 2.7kg 1000= 消泡剂相对密度为,=3.4L(8)发酵生化反应过程所产生的水分 1t 商品淀粉在发酵液中所产生的100%谷氨酸量940×60%×%=555.5kg生成1mol 谷氨酸产3molH 2O ;生成1mol 菌体产7 molH 2O 。
根据发酵反应式,发酵产生的水分为318555.5204kg 147⨯⨯=长菌过程产生水分,1g 菌体产酸11g ,应产生水分为555.5718×43.3kg 11147⨯= 以上合计产生水247.3kg 。
(9)发酵过程从排风带走的水分 进风25℃,相对湿度70%,水蒸气分压18mmHg (1 mmHg=);排风32℃,相对湿度100%,水蒸气分压27 mmHg 。
进罐空气的压力为大气压(表压)(1大气压=×105Pa ),排风大气压(表压),出进空气的湿含量差27100%1870%X 0.6220.6220.0150.00420.011kg /kg 1.576027100%2.57601870%X ⨯⨯⨯⨯⨯⨯⨯⨯出进-=-=水干空气---=通风比1:,发酵液数量5000L ,带走水分量5000××60×32×××=37kg式中 60——60min 32——发酵时间,h ——32℃时干空气密度,kg/m 3(10)发酵过程化验取样、放罐残留及其他损失 约13kg 。
(11)发酵终止时的数量 1t 商品淀粉,发酵终止时1660+901+22+830+1120+391++160++-37-13=5403.6kg(30%糖)+(补浓糖)+(营养物)+(配料水)+(灭菌水)+(种子)+(反应水)+(液氨)+(消泡剂)+(空消蒸汽)-(尾气带水)-(损失)=(终止数量) 式中 ——空消时耗用的蒸汽量发酵液相对密度,=5050L ,每日产发酵液,即=2350m 3/d 。
(12)衡算结果汇总 年产2万吨味精,日投商品淀粉(86%),配料、连续灭菌和发酵工序的物料衡算汇总见表。
表 配料、连续灭菌和发酵工序物料衡算汇总表项目1t 工业淀粉之匹配物料/kg每天进入系统的物料/(t/d )项目1t 工业淀粉之匹配物料/kg每天离开系统的物料/(t/d )30%糖液 1660 发酵液 60g/L 浓糖浆 901 尾气带水 37 玉米浆 损失 13 糖蜜 无机盐等 配料水 830灭菌进入蒸汽及补水 1120种液 391 反应水 液氨160消泡剂空消蒸汽累计谷氨酸提取车间物料衡算采用等电-离交回收工艺(按1000kg商品淀粉相对应量计算)。
3.4.1中和等电工序(1)发酵液数量 5404kg;5050L。
(2)高流量为发酵液的45%,即2432kg。
(3)%硫酸用量为纯谷氨酸用量的90%,即×90%=480kg。
(4)等电液数量5404+2432=7836kg(5)谷氨酸产量①分离前Glu量100%Glu量:5050×11(W/V)=555.5kg②分离后Glu量100%Glu量:×96%=533.3kg90% Glu量:90%=592.6kg(6)加水量 479kg。
(7)洗水量为90% Glu量的%,即×%≈86kg。
(8)母液(上清液)数量7836+479-+86=7808kg(9)物料衡算汇总根据以上计算,再乘以(日投商品淀粉数量),即得出每日的物料量,汇总见表。
表谷氨酸等电工序物料衡算汇总表项目1t商品淀粉及相应物料/kg 每天进入系统的物料/(t/d)项目1t商品淀粉及相应物料/kg每天离开系统的物料/(t/d)发酵液540490% Glu57高流2432母液7808水565累计840184013.4.2离交工序(1)母液调pH 用硫酸量 1t 商品淀粉相应用%硫酸480kg ,其总调pH 用酸量占66%,即480×66%=317kg(2)母液数量 7808kg 。