永钢大圆坯连铸工艺装备特点及实践
连铸专业实习报告

实习报告一、实习背景及目的随着连铸技术的不断发展,连铸专业人才的需求日益增加。
为了更好地了解连铸工艺流程,提高自己的实践能力,我选择了连铸专业实习。
本次实习旨在深入了解连铸生产过程,掌握连铸设备的使用和维护方法,以及提高自己在实际工作中的协调和组织能力。
二、实习内容1. 连铸工艺流程学习在实习期间,我认真学习了连铸工艺流程,包括钢水准备、浇注、结晶器操作、拉矫、切割等环节。
通过学习,我了解到连铸是将熔融钢水通过结晶器冷却成固态钢坯的过程,具有生产效率高、成本低、质量好等优点。
2. 连铸设备操作与维护在实习过程中,我参与了连铸设备的操作和维护工作。
学习了结晶器、拉矫机、切割机等设备的使用方法,并熟悉了各种设备的维护保养知识。
通过实践操作,我掌握了连铸设备的工作原理和操作技巧。
3. 实习期间遇到的难题及解决方法在实习过程中,我遇到了一些难题,如结晶器操作不当导致钢坯质量问题,拉矫机故障等。
针对这些问题,我积极与同事和导师沟通交流,学习了解决问题的方法。
在导师的指导下,我不仅解决了问题,还提高了自己的 troubleshooting 能力。
4. 实习期间的团队协作与组织能力培养实习期间,我积极参与团队工作,与同事们共同完成生产任务。
在团队合作中,我学会了如何与他人沟通、协调,提高工作效率。
同时,我还参与了实习基地的日常管理,提高了自己的组织能力和责任心。
三、实习收获通过本次实习,我对连铸工艺流程有了更深入的了解,掌握了连铸设备的使用和维护方法,提高了自己的实践能力。
同时,我在团队协作中培养了良好的沟通和组织能力,为今后从事连铸工作打下了坚实的基础。
四、实习总结本次连铸专业实习让我受益匪浅,不仅提高了自己的专业技能,还培养了良好的团队合作精神。
在今后的学习和工作中,我将继续努力,充分发挥自己在连铸领域的优势,为我国连铸事业的发展贡献自己的力量。
什么是连铸坯?它有什么优点?

什么是连铸坯?它有什么优点?
连铸坯是由钢水经连续铸钢机直接铸成的钢坯。
连续铸钢工艺大大简化了从钢水到钢坯的生产过程,省去了初轧生产过程,因此它有金属收得率高、产品成本低、基建投资和生产费用少、劳动定员少、劳动条件较好等一系列优点。
连铸坯已成为轧钢生产的重要原料,并获得了日益迅速的发展寸某厂用连铸钢坯与用钢锭生产钢材的技术经济指标(见表4-3)证明了连铸坯的优越性。
表4-3 用连铸坯与用钢锭生产钢材的技术经济指标比较
指标名称单
位用150×280mm
连铸坯
用10英寸(相当于254mm)
钢锭
炼钢钢铁料消
耗
锭、坯合
格率
炼钢成本
生产工人
数
kg/t
%
元/t
%
1209.3
99.33
255.30
68
1250.9
98.2
270.90
100
轧钢锭、坯消
耗
钢材合格
率
kg/t
%
%
元/t
1350
99.2
74.10
276.40
1400
99.6
71.40
307.60
元/t 418.70 447.50 成材率
薄板坯成
本
薄板成本。
永钢连铸坯热送热装生产实践

编号:AQ-JS-01453( 安全技术)单位:_____________________审批:_____________________日期:_____________________WORD文档/ A4打印/ 可编辑永钢连铸坯热送热装生产实践Production practice of hot delivery and hot charging of continuous casting billet in Yonggang永钢连铸坯热送热装生产实践使用备注:技术安全主要是通过对技术和安全本质性的再认识以提高对技术和安全的理解,进而形成更加科学的技术安全观,并在新技术安全观指引下改进安全技术和安全措施,最终达到提高安全性的目的。
介绍了2012年以来永钢热送热装工作开展情况和做好热装生产的经验,节能降耗效果十分显著,并对制约热装生产的不利因素和未来热装效益增长潜力进行了初步分析。
连铸坯热送热装是钢铁行业重点推广的节能技术之一,具有节约能源,提高加热炉生产能力,减少连铸坯烧损和钢坯内外温差,提高产品成材率,加快物流流动和减少钢坯多次倒运等优点。
轧钢加热炉是钢铁生产中的重要设备,也是主要的耗能设备之一,在轧钢工序耗中约占65%~70%。
因此,实施连铸坯热送热装技术,降低轧钢加热炉的能源消耗是提高钢材产品竞争力的重要因素。
尤其是2012年永钢开始对产品进行提档升级,开发冷镦、中碳钢等工业用材,线材产品以优特钢为主,产品结构更加复杂,使连铸坯热装率逐步下降。
近年来,连铸坯的热送热装主要集中在品种相对较少、生产批量相对较大的炼钢一厂3#连铸机和与之对应的线材二厂。
同时3#连铸机出坯辊道与线材二厂加热炉车间距离不足50米,为连铸坯热送热装提供了有利条件。
主要存在的问题及原因(1)线材二厂与炼钢一厂地理位置最近,但连铸坯仍采用传统的物流运输模式。
(2)炼钢一厂3#连铸机至线材二厂原有的热装热送装置中提升机对连铸坯的直线度要求高,当连铸坯稍有弯曲时,提升机无法提升连铸坯至上料辊道,被迫中断连铸坯热装热送。
圆坯连铸

圆坯连铸圆坯连铸(round continuous casting) 一种主要生产无缝钢管用管坯的连续铸钢技术。
它具有铸坯精度高、质量好、能耗低和金属综合收得率高的优点。
圆坯连铸技术的发展,加速了无缝管轧制与连铸直接连接的进程。
圆坯连铸除了结晶器是圆形及引锭杆的引锭头为圆头以外,其总体设备结构与方坯连铸没有本质区别。
但由于其产品为无缝钢管坯,其浇注工艺要求严格,其设备也有一定特点。
工艺要求可归纳为4点:(1)严格控制的钢水成分和温度。
钢水必须经过炉外精炼处理,通过钢水调温、合金化和脱气等操作,达到连铸操作所要求的钢水成分和温度及良好的钢水洁净度,为确保铸坯质量提供先决条件。
(2)无氧化浇注。
采取全面的钢水无氧化保护浇注措施,防止盛钢桶至中间罐和中间罐至结晶器的钢流二次氧化。
选择和控制适宜和稳定的中间罐液面深度,保持结晶器液面稳定,根据钢种和断面及拉速配制适宜的结晶器保护渣,达到促进夹杂物上浮,减少夹杂物生成的目的。
(3)合理的浇注参数。
根据钢种、铸坯断面尺寸、冶炼周期和浇注周期,确定合理的浇注参数,特别是冷却制度和浇注温度是直接影响铸坯内部和表面质量。
(4)具备较高的自动化仪表和计算机控制水平,确保浇注参数的稳定。
采用铸坯质量在线计算机控制管理系统,提供生产无缺陷铸坯的保证条件。
设备特点圆坯连铸设备有如下特点: (1)管式圆坯结晶器。
采用单锥度或双锥度的弧形管式圆坯结晶器,带有可精确对中的槽型足辊。
(2)弓f锭杆。
引锭杆和过渡段与圆坯断面相适应,具有与铸坯快速脱离的结构特点。
引锭杆本体可采用矩形断面,并不一定与圆坯断面相适应。
(3)输送辊道。
采用槽型辊道,确保圆坯在输送过程中的严格导向。
(4)引锭杆跟踪系统。
采用特殊的跟踪系统,克服槽型辊道与引锭杆接触面积小,易造成铸坯打滑的缺点,以免影响引锭头的准确定位和切头的位置。
(5)多点矫直系统。
采用多点矫直,减少铸坯的外部和内部的变形率,确保铸坯表面质量和内部质量。
连铸成型的特点、轧制成型的特点
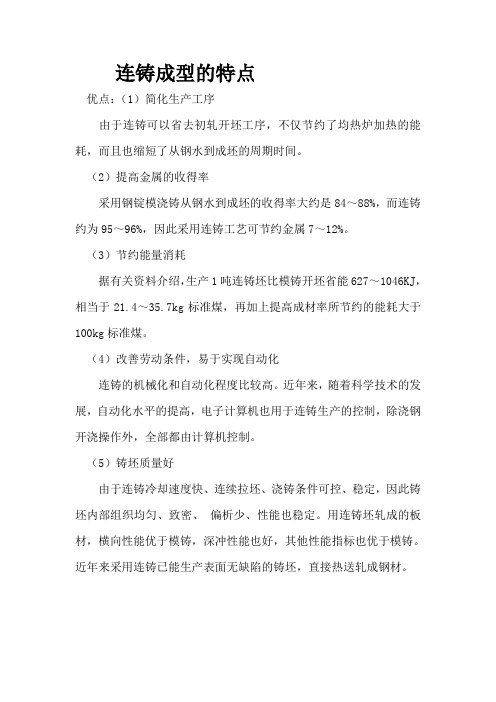
连铸成型的特点优点:(1)简化生产工序由于连铸可以省去初轧开坯工序,不仅节约了均热炉加热的能耗,而且也缩短了从钢水到成坯的周期时间。
(2)提高金属的收得率采用钢锭模浇铸从钢水到成坯的收得率大约是84~88%,而连铸约为95~96%,因此采用连铸工艺可节约金属7~12%。
(3)节约能量消耗据有关资料介绍,生产1吨连铸坯比模铸开坯省能627~1046KJ,相当于21.4~35.7kg标准煤,再加上提高成材率所节约的能耗大于100kg标准煤。
(4)改善劳动条件,易于实现自动化连铸的机械化和自动化程度比较高。
近年来,随着科学技术的发展,自动化水平的提高,电子计算机也用于连铸生产的控制,除浇钢开浇操作外,全部都由计算机控制。
(5)铸坯质量好由于连铸冷却速度快、连续拉坯、浇铸条件可控、稳定,因此铸坯内部组织均匀、致密、偏析少、性能也稳定。
用连铸坯轧成的板材,横向性能优于模铸,深冲性能也好,其他性能指标也优于模铸。
近年来采用连铸已能生产表面无缺陷的铸坯,直接热送轧成钢材。
缺点:(1)夹杂杂质如果液态金属事先不除尽杂质,在铸造过程中会出现问题。
氧化是液态金属杂质的主要来源,气体、矿渣或不溶合金也可能卷入液态金属。
为防止氧化,金属尽量与大气隔离。
在中间包,任何夹杂物包括气泡,其他矿渣或氧化物,或不溶合金也可能被夹杂在渣层。
(2)连铸坯的断裂如果凝固的金属外壳过薄,有可能导致钢坯在拉出一定长度后下方的金属将上方正在凝结的金属拉断,导致钢水泄露,进而破坏其他机器而发生事故。
通常情况下,断裂是由于过高的拉出速度,使凝固的外壳没有足够时间来产生所要求的厚度;也有可能是拉出的金属温度仍然过高,这意味着最终凝固时间大大低于矫直辊和地方链断裂整顿期间,由于应用的压力。
阿突破,也可能发生,如造成撕裂。
如果传入的金属过热,可以通过减慢拉出速度来防止断裂。
(3)可能出现碳化物钢铁与溶解氧反应也可能产生碳化物。
由于金属是液态,这种碳化反应是非常的快,同时产生大量高温气体,如果是在中间包或者结晶器中发生碳化反应,氧元素还会反应生成氧化硅或氧化铝,如果产生过多的氧化硅或氧化铝将有可能堵塞中间包与结晶器中间的连接管,进而导致破坏生产。
连铸实习报告

实习报告一、实习背景及目的随着我国钢铁工业的快速发展,连铸技术在生产中的应用日益广泛。
为了更好地了解连铸工艺流程,提高自己的实践能力,我于某年某月某日至某年某月某日,在某钢铁公司连铸车间进行了为期一个月的实习。
本次实习的主要目的是了解连铸工艺的基本原理、设备组成、操作流程及质量控制等方面知识。
二、实习内容与过程1. 实习前的培训实习开始前,车间主任对我们进行了实习培训,介绍了连铸车间的基本情况、安全注意事项和实习要求。
我们学习了连铸工艺的基本原理、设备组成、操作流程及质量控制等方面的理论知识。
2. 实习过程中的学习与实践在实习过程中,我深入了解了连铸车间的生产现场,参观了连铸机、中间包、结晶器等主要设备,并跟随操作人员学习了连铸操作流程。
此外,我还参与了车间内的安全巡查、设备维护和质量控制等工作。
(1)连铸工艺流程连铸工艺流程主要包括以下几个环节:1)配料:根据钢种和生产要求,合理搭配铁水、废钢等原料。
2)熔炼:在炼钢炉中进行,通过调节炉温和加入合金等材料,使钢水达到所需成分和温度。
3)精炼:通过吹氩、加合金等方法,进一步调整钢水的成分和温度。
4)浇注:将经过精炼的钢水倒入中间包,然后通过连铸机进行浇注。
5)结晶:钢水在结晶器中快速冷却,形成具有一定形状和尺寸的铸坯。
6)拉矫:通过拉矫机对铸坯进行拉伸和矫直,使其达到所需的形状和尺寸。
7)切割:将拉矫后的铸坯切割成一定长度和厚度的板坯或棒材。
(2)设备组成连铸车间的主要设备包括连铸机、中间包、结晶器、拉矫机、切割机等。
连铸机是连铸工艺的核心设备,主要由铸机本体、传动系统、控制系统等部分组成。
(3)操作流程连铸操作流程主要包括以下几个步骤:1)准备:检查设备是否正常,确认生产参数(如拉速、浇注温度等)。
2)浇注:倒入钢水,启动连铸机进行浇注。
3)观察:观察铸坯表面质量,及时调整生产参数。
4)拉矫:启动拉矫机,对铸坯进行拉伸和矫直。
5)切割:启动切割机,将拉矫后的铸坯切割成所需长度和厚度。
淮钢特殊钢大型圆坯连铸工艺装备特点及实践

淮钢特殊钢大型圆坯连铸工艺装备特点及实践淮钢特殊钢大型圆坯连铸工艺装备特点及实践淮钢特殊钢大型圆坯连铸工艺装备是一种高效、节能、环保的钢铁生产工艺,其特点在于采用了先进的连铸技术和设备,能够生产出高质量、高精度的特殊钢圆坯,满足了市场对高品质钢材的需求。
下面将从工艺装备的特点和实践两个方面进行介绍。
一、工艺装备特点1.高效节能淮钢特殊钢大型圆坯连铸工艺装备采用了先进的连铸技术,能够实现高效、连续、自动化的生产过程,大大提高了生产效率和生产能力。
同时,该工艺装备还采用了节能环保的设计理念,通过优化能源结构和节约能源消耗,实现了能源的高效利用和环保生产。
2.高精度淮钢特殊钢大型圆坯连铸工艺装备采用了先进的数控技术和自动化控制系统,能够实现高精度的生产过程。
通过对生产过程中的各个环节进行精细化控制,保证了生产出的特殊钢圆坯的尺寸精度和表面质量的稳定性。
3.高品质淮钢特殊钢大型圆坯连铸工艺装备采用了高品质的原材料和先进的生产工艺,能够生产出高品质的特殊钢圆坯。
同时,该工艺装备还采用了严格的质量控制体系和检测手段,保证了生产出的特殊钢圆坯的质量稳定性和可靠性。
二、实践淮钢特殊钢大型圆坯连铸工艺装备已经在淮钢集团的生产实践中得到了广泛应用。
通过对该工艺装备的实践应用,取得了以下成果:1.提高了生产效率和生产能力淮钢特殊钢大型圆坯连铸工艺装备的应用,使得淮钢集团的生产效率和生产能力得到了显著提高。
通过优化生产过程和提高生产效率,淮钢集团的特殊钢圆坯产量得到了大幅提升,同时还能够满足市场对高品质特殊钢圆坯的需求。
2.提高了产品质量和稳定性淮钢特殊钢大型圆坯连铸工艺装备的应用,使得淮钢集团的产品质量和稳定性得到了显著提高。
通过优化生产工艺和加强质量控制,淮钢集团的特殊钢圆坯的尺寸精度和表面质量得到了大幅提升,同时还能够保证产品质量的稳定性和可靠性。
3.提高了环保效益淮钢特殊钢大型圆坯连铸工艺装备的应用,使得淮钢集团的环保效益得到了显著提高。
炼钢连铸炼铁实习报告

一、实习背景为了更好地了解我国钢铁工业的生产流程和工艺技术,提高自己的实践能力和综合素质,我于2023年XX月至XX月在XX钢铁有限公司进行了为期一个月的实习。
本次实习主要涉及炼钢、连铸和炼铁三个环节,通过实地参观、操作实践和理论学习,使我受益匪浅。
二、实习内容1. 炼铁环节(1)原料准备:炼铁过程中,首先要准备铁矿石、焦炭、石灰石等原料。
铁矿石是炼铁的主要原料,焦炭作为还原剂,石灰石用于去除杂质。
(2)高炉冶炼:将原料送入高炉,在高温下进行还原反应,生成铁水。
高炉冶炼是炼铁的核心环节,对生产效率和产品质量至关重要。
(3)铁水处理:将铁水送入铁水罐,进行脱硫、脱磷等处理,以提高铁水的纯净度。
2. 炼钢环节(1)炉前准备:将铁水送入转炉,进行脱碳处理。
转炉炼钢是炼钢的主要方法,具有生产效率高、成本低等优点。
(2)炉后处理:将钢水送入精炼炉,进行脱氧、脱硫、脱磷等处理,以提高钢水的纯净度和性能。
(3)连铸:将精炼后的钢水浇注到结晶器中,冷却凝固成铸坯。
连铸是炼钢的重要环节,具有生产效率高、质量稳定等优点。
3. 连铸环节(1)铸坯制备:将钢水浇注到结晶器中,通过冷却和凝固形成铸坯。
(2)铸坯加热:将铸坯送入加热炉,进行加热处理,提高铸坯的塑性和韧性。
(3)铸坯切割:将加热后的铸坯切割成所需规格的钢坯。
三、实习体会1. 生产流程严谨:钢铁生产流程复杂,各个环节紧密相连,任何一个环节出现问题都可能影响整个生产过程。
因此,在生产过程中,必须严格按照操作规程进行,确保生产安全和产品质量。
2. 技术创新至关重要:随着科技的不断发展,钢铁生产工艺也在不断改进。
通过引入新技术、新设备,可以提高生产效率、降低生产成本、提高产品质量。
3. 安全生产意识:钢铁生产过程中存在高温、高压、易燃易爆等危险因素,因此,必须加强安全生产意识,严格执行安全操作规程,确保生产安全。
4. 团队协作精神:钢铁生产是一个系统工程,需要各个岗位的密切配合。
- 1、下载文档前请自行甄别文档内容的完整性,平台不提供额外的编辑、内容补充、找答案等附加服务。
- 2、"仅部分预览"的文档,不可在线预览部分如存在完整性等问题,可反馈申请退款(可完整预览的文档不适用该条件!)。
- 3、如文档侵犯您的权益,请联系客服反馈,我们会尽快为您处理(人工客服工作时间:9:00-18:30)。
永钢大圆坯连铸工艺装备特点及实践卢洪星1陆剑锋 2 李占春 2 陆健2(1江苏沙钢集团淮钢特钢股份有限公司,223002;2江苏永钢集团联峰能源装备有限公司215628)摘要介绍了江苏永钢集团联峰能源装备有限公司电炉大圆坯连铸装备特点,调试与生产情况,对连铸设备与工艺技术、产品质量进行分析,提出相关改进措施。
关键词圆坯连铸工艺装备特点实践Practice and Process Equipment Charateristic of Continuous Cast Machinefor Big Bloom in Yonggang SteelLuhongxing1Lujianfeng2Lizhanchun2Lujian2(1.Jiangsu Shasteel Group Huaigang Special Steel Co.,Ltd,HuaiAn 223002;2.Jiangsu Yongsteel Group Energy Equipment Co.,Ltd,YongGang 215628)Abstract Process equipment charateristics,debugging and production situation of continuous cast machine for big round bloom by EAF process in Yonggang Steel CO.,Ltd are introduced,The continuous cast equipment,technique and quality of billet steel are analysed,and adopting related improving and assuring measures。
Key Words Continuous Cast for Round Bloom Process Equipment Charateristic Practice江苏永钢集团能源装备有限公司电炉特殊钢大圆坯连铸机是中冶京城设计、制造,于2013年06月投产,主要生产钢种为优质碳素结构钢、合金结构钢、及低合金高强度钢等,生产初期存在的主要缺陷为铸坯芯部裂纹、外部纵裂、外形尺寸偏差。
为提高和改进大圆坯的质量,对连铸设备、生产工艺进行研究,并采取针对性的改进措施,使大圆坯的内部、外部质量缺陷得到有效控制和改善。
1 工艺流程和设备参数该炼钢厂工艺流程为110tEAF冶炼→110tLF精炼→110tVD→喂线进行夹杂变性→大圆坯连铸。
大圆坯连铸机主要技术参数如表1。
表1 大圆坯连铸机主要技术参数Table 1 main technical parameter of CCM机型弧形圆坯连铸机连铸机流数4流弧半径R=17m铸坯断面φ380mm、φ500mm、φ600mm、φ800mm流间距2600mm中间包容量/液位高度40t/900mm结晶器型式弧型管式铜管长度/锥度780mm/弧形多锥度结晶器液面控制电磁涡流保护渣加渣方式手动振动装置内外弧双液压单元仿弧型液压振动装置振动行程/振动频率0~15mm/30~350opm二次冷却喷水+气雾冷却电磁搅拌M-EMS+F-EMS拉速范围0.2~1m/min设计能力90万t2 主要工艺装备与技术特点该连铸机由中冶京诚公司负责工艺设计和关键设备的详细设计,振动液压缸为进口件。
主要设备有:钢包回转台旋转驱动装置、电动机械塞棒自动控制系统、结晶器、结晶器液位检测系统、中间包车、结晶器电磁搅拌器、二冷喷淋与气-水控制调节系统、末端电磁搅拌器、液压振动装置、拉矫机驱动装置与液压缸、火焰切割系统、打号系统等。
2.1 钢包回转台钢包回转台形状为H蝶形,在两个相互独立的钢包回转台臂上有钢包提升、下降装置,钢包提升行程为600mm。
安装可提升臂的优点方便于钢包与中包之间的长水口保护浇注操作,控制、调节长水口插入中包钢水液面的深度;大包水口不能自动打开时,便于大包工烧氧引流。
2.2 中间包采用优化设计的T型中间罐内形有最佳的流场分布,同时也便于档渣墙、堰的砌筑;中间罐内钢液有足够深度保证钢水内夹杂物有充分的上浮时间;也保证在更换钢包时中间罐钢水液面的稳定。
在中包钢水注入点设置溢流口,其高度为930mm,便于放渣、换渣操作,稳定和控制中间包的冶金效果;控制中间包的渣层厚度,减少中间包钢水被污染的程度,提高连铸坯的洁净度。
2.3 电动机械塞棒系统结晶器液面检测及中间包塞棒控制是保证连铸坯表面质量的重要手段,在稳定拉速下,可以有效地减少连铸坯表面夹杂等缺陷,充分发挥末端电磁搅拌均质的作用。
采用电磁涡流液面自动监测和塞棒控制机构的监测—控制回路可以在稳定拉速的条件下保持液面波动在很小的范围内,同时也可改善操作人员的工作条件,消除人员人为干扰而产生的漏钢等生产事故。
2.4 结晶器和足辊结晶器为管式结晶器,在设计上考虑避免铜管因高温作用而产生永久性变形。
否则,结晶器铜管变形后会造成其寿命大大缩短,并会在大圆坯表面产生深深的振痕等表面缺陷。
为防止铜管高温下的横向变形,铜管被严格限制在只能沿其纵轴上自由膨胀。
铜管与水套间隙保持在3.5mm,通过水缝内的高速水流来降低铜管温度,避免水缝内的水沸腾。
同时,在足够水压作用下,可防止铜管壁温度过高会造成严重结垢,影响铜管的传热效果。
结晶器的自对中设计,在任何条件下都可以保证水缝绝对恒定。
同时,水套安装在橡胶环上,可以在铜管上自由地进行自对中运动。
结晶器底部设有两排足辊,可以偏心调节,足辊的作用是引导引锭杆进出结晶器,可以避免引锭杆划伤铜管,减少铜管磨损和降低浇注条件变化对铸坯质量造成的影响。
同时,可提高铜管拉钢量,提高铸机作业率。
2.5 液压振动台振动台安装在冷却室外的铸机弧型半径的外侧,便于维修人员日常点检、维护和检修。
振动通过液压缸完成,液压缸配有位置传感器,用以控制振动行程,其行程和波形在浇注期间可根据所浇钢种的技术参数而自动地改变。
振动单元(内外弧各1个)是由带有活动段支撑的振动底座进行支承,它确保结晶器和活动段的良好对中。
带有活动段支撑的振动底座用螺栓固定在锚固底板上。
中冶京诚液压振动技术可以在浇注过程中修改振动频率、振动行程和振动模式以获得最佳的表面质量。
实际振动曲线与理想曲线重叠,误差很小,高频、小振幅的振动参数,以保证凝固壳的充分润滑,减少振痕深度和裂纹的产生,获得稳定、良好的铸坯表面质量。
2.6 结晶器电磁搅拌系统结晶器电磁搅拌设置在结晶器铜管下部,利用电磁力把在结晶器内向下流动的钢水搅动起来,使得钢水中的夹渣及气泡上浮,同时使钢水温度均匀。
减少连铸坯表面夹渣、气孔、微裂纹,提高连铸坯的质量。
使用结晶器M-EMS改善铸坯表面质量的作用主要在于:(1)钢水旋转产生的向心力可以除去凝固前沿的夹杂物。
夹杂物上浮到弯月面中心可以防止进入凝固壳内,减少表面和次表面的夹杂物数量并且其沿钢坯中心断面分布更加均匀。
(2)由于结晶器壁上的钢渣漂到弯月面中心并被收集起来,因此可防止钢渣粘接。
(3)由于钢水运动除去凝固前沿的气泡,使次表面区域的气泡、针孔、气孔大大减少。
2.7 末端电磁搅拌系统及流电磁搅拌末端电磁搅拌安装在距结晶器液面约16m的固定段Ⅱ区域,其安装位置可以根据大圆坯实际液芯位置进行调整。
末端电磁搅拌线圈为3相、旋转连续/交替式,根据生产断面的不同采用二组不同线圈,其中:Ø380,Ø500共用一套线圈,Ø600,Ø800共用一套线圈。
供电电源为逆变式变频器,提供了极好的搅拌器无功功率补偿,额定电流650-800A,低频2-10Hz。
在一流上采用流电磁搅拌,在其余3流上预留铸流搅拌的空间和能源介质用量,额定电流650-800A,低频2-10Hz。
2.8 二冷气雾冷却采用气水雾化冷却方式二冷水调节范围和浇注钢种覆盖面大,同时二次冷却采用分区的控制,通过控制模型使在浇注过程中铸坯冷却均匀,温度回升小从而降低裂纹的产生。
本系统二次冷却系统分流、分区,分回路分别控制,每流共分为三个回路:第一回路:结晶器足辊段区域喷水冷却;第二回路:活动段上部区域气水冷却;第三回路:活动段下部区域气水冷却。
二冷水的自动控制,根据浇注不同钢种设定不同比水量,在浇注过程中各段二冷水量按照一定比例、根据拉速的变化分区段自动控制,保证铸坯在冷却区内均匀冷却和控制回温。
每个区域由二级自动化系统单独控制,根据所浇注的圆坯的规格、拉速和钢种的不同,使用不同的冷却区域。
表2 大圆坯连铸机各冷却区采用的喷嘴型号及数量Table 2 nozzle model and quantity of CCM cooling zone冷却区型号冷却方式数量二冷1区Φ380:HB1/4VV9506 水冷/扁平8 Φ500/Φ600:HB1/4VV9506 水冷/扁平16 Φ800:HB1/4VV11006 水冷/扁平16二冷2区Φ380:40206-04900-90480 气雾/锥形12 Φ500/Φ600/Φ800:40206-04900-90480气雾/锥形18二冷3区Φ380:40206-04900-90440 气雾/锥形162.9 中间罐连续测温系统中间罐温度是连铸生产过程中重要的参数。
也是工艺操作人员必须掌握的一个重要工艺参数,对中间罐钢水温度连续监测是生产出高质量产品的一个有效的保障,同时能够使连铸机生产稳定。
3 生产、质量情况与改进3.1 生产钢种目前生产钢种主要有优质碳素结构钢,代表钢号为45、20、20G、35;合金结构钢,代表钢号为40Cr、、42CrMo、42CrMo4V、4130X;低合金高强度结构钢,代表钢号为16Mn、Q345E、S355NL等。
连铸圆坯主要用于生产无缝钢管、环锻件和锻造齿轮坯、轴类件、法兰件及其它机械零件等。
3.2 铸坯质量按YB/T4149-2006和中冶京城的保证值对φ500mm的圆坯进行检验,结果分别如下。
3.2.1铸坯内部质量情况表3 铸坯内部质量情况Table3 Internal quality of round bloom缺陷类别中心疏松缩孔中心裂纹中间裂纹皮下裂纹皮下气泡判定备注YB/T4149-2006 ≤2.0 ≤2.0 ≤2.0 ≤2.0 ≤2.0 ≤2.0 - -检验结果1.5 1.0 0 0 0 0 合格第一流1.0 0.5 0 1.0 0 0 合格第四流3.2.2 铸坯表面质量情况铸坯表面质量总体情况比较好,主要存在与保护渣和冷却相关的渣沟、开裂问题。
3.2.3 铸坯外形尺寸情况表4 铸坯不圆度情况T able4 Ovality of round bloomYB/T4149-2006不圆度判定备注不避开扁平区(mm) 避开扁平区(mm)3.5%(17.5mm) 2%(10mm)实测值39 9 不合格第一流12 1 合格第二流11 4 合格第三流12 5 合格第四流表5 铸坯弯曲度情况Table 5 Camber of round bloomYB/T4149-2006弯曲度判定备注每米弯曲度(mm) 全长弯曲度(mm)≤6mm ≤全长的6mm实测值1 3 合格第一流1 3 合格第二流2 3 合格第三流1 3 合格第四流3.3 存在问题分析与改进3.3.1 保护渣改进在生产Q345E等高锰钢时出现了渣沟等表面缺陷,渣沟沿拉坯方向延伸,时断时续。