设备利用率计算表(依据产能)
生产效率计算方法
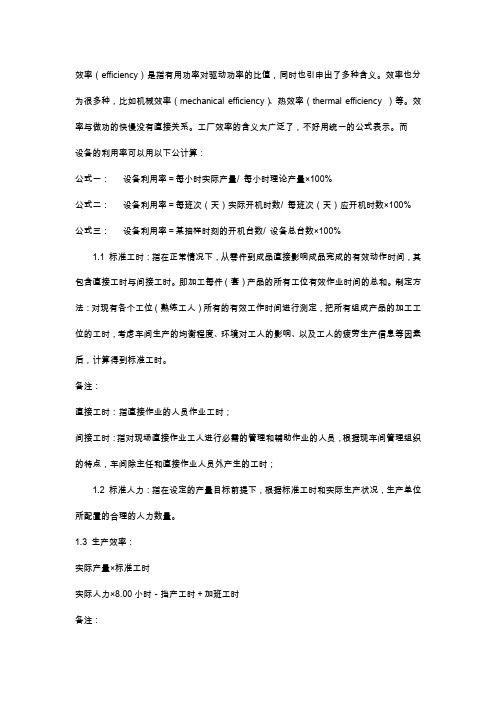
效率(efficiency)是指有用功率对驱动功率的比值,同时也引申出了多种含义。
效率也分为很多种,比如机械效率(mechanical efficiency)、热效率(thermal efficiency )等。
效率与做功的快慢没有直接关系。
工厂效率的含义太广泛了,不好用统一的公式表示。
而设备的利用率可以用以下公计算:公式一:设备利用率=每小时实际产量/ 每小时理论产量×100%公式二:设备利用率=每班次(天)实际开机时数/ 每班次(天)应开机时数×100% 公式三:设备利用率=某抽样时刻的开机台数/ 设备总台数×100%1.1 标准工时:指在正常情况下,从零件到成品直接影响成品完成的有效动作时间,其包含直接工时与间接工时。
即加工每件(套)产品的所有工位有效作业时间的总和。
制定方法:对现有各个工位(熟练工人)所有的有效工作时间进行测定,把所有组成产品的加工工位的工时,考虑车间生产的均衡程度、环境对工人的影响、以及工人的疲劳生产信息等因素后,计算得到标准工时。
备注:直接工时:指直接作业的人员作业工时;间接工时:指对现场直接作业工人进行必需的管理和辅助作业的人员,根据现车间管理组织的特点,车间除主任和直接作业人员外产生的工时;1.2 标准人力:指在设定的产量目标前提下,根据标准工时和实际生产状况,生产单位所配置的合理的人力数量。
1.3 生产效率:实际产量×标准工时实际人力×8.00小时-挡产工时+加班工时备注:实际产量:生产部、财务计算生产效率/生产力时以实际入库量计算;挡产工时:因外部门或受客观条件影响造成停线或返工工时;加班工时:为增加产量而延长的工作时间;生产效率=(实际产量×标准工时)/(实际人力×8.00小时-挡产工时+加班工时)生产效率讲的是快慢,是速度,它是实际产出与标准产出的比率;生产力讲的是效益,它讲的是产出与投入之比。
生产能力利用率计算公式

生产能力利用率计算公式
生产能力利用率,有时也叫设备利用率,是工业总产出对生产设备的比率,简单的理解,就是实际生产能力到底有多少在运转发挥生产作用。
指工业产品全年实际生产量,与工业产品全年平均生产能力的比率。
该指标越接近百分之百,说明生产能力利用越充分,实际产出与潜在产出之差越小,经济发展质量越高;反之,说明有部分生产能力被闲置,实际经济发展速度小于潜在经济发展速度,经济发展质量有待提高。
生产能力利用率是衡量经济发展质量的重要指标。
要正确评价经济发展质量,必须完善该指标的统计和考核办法。
计算如下:实际产能/设计产能*100%
由于没有产能利用的直接统计数据,所以产能利用状态必须依靠间接的度量方法才能实现。
生产能力的度量方法大致上可以分为峰值分析法、随机参数生产前沿面方法(SPF)、非参数生产前沿面(DEA)的数据包络分析方法以及在第三种方法为基础发展起来的要素拥挤度方法四大类,这四类方法的共同原理都是以实际生产状态和最好或者有效生产状态的比较作为过剩状态的度量。
OEE设备综合利用率详解第一讲-单台设备的OEE计算
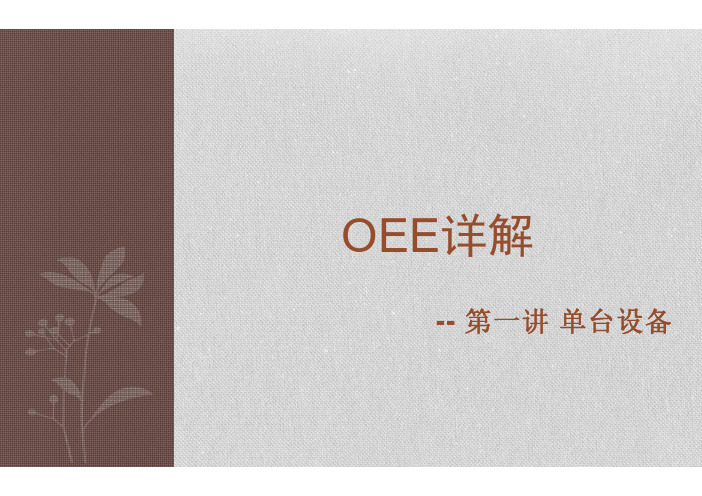
OEE详解--第一讲单台设备OEE是一个独立的测量工具,它用来表现实际的生产能力相对于理论产能的比率。
国际上对OEE的定义为:OEE是Overall Equipment Effectiveness(设备综合效率)的缩写。
它由利用率,表现性以及质量指数三个关键要素组成,即:OEE =利用率X表现性X 质量指数利用率=实际操作时间/ 计划工作时间它是用来考虑停工所带来的损失,包括引起计划改变并生产发生停顿的任何事件,例如设备故障,原料短缺以及生产方法的改变等。
表现性=实际总产量/ (实际操作时间/理想节拍时间)表现性考虑生产速度上的损失。
包括任何导致生产不能以最大速度运行的因素,例如设备的磨损,材料的不合格以及操作人员的失误等。
质量指数=良品数量/ 实际总产量质量指数考虑质量的损失,它用来反映没有满足质量要求的产品(包括返工的产品)。
--笔者基于百度百科的定义进行了修改OEE 三大要素中部分名词解析OEE=利用率X表现性X质量指数利用率=实际操作时间/计划工作时间表现性=实际总产量/(实际操作时间/理想节拍时间)质量指数=良品数量/实际总产量机器设备实际使用的时间占比在机器设备性能完好的情况下可供使用的时间占比利用率可用率V.S.* 生产过程中短暂的停顿是否定义成为停机要根据各个工厂自己的定义。
** 此处所有时间均为预先计划好的,任何临时发生的情况即使是上面描述的内容,也不能算计划停机,只能算损失,即表现性下降。
计划工作时间总时间扣除所有的计划停机时间**计划停机时间包括但不仅限于休息,吃饭,换班,维护保养实际操作时间计划停机时间扣除所有非计划停机时间非计划停机时间包括但不仅限于紧急换型,计划外维护,等料,等人,各种小停机*OEE 三大要素中部分名词解析OEE=利用率X表现性X质量指数利用率=实际操作时间/计划工作时间表现性=实际总产量/(实际操作时间/理想节拍时间)质量指数=良品数量/实际总产量加工时间(PT)节拍时间(CT)V.S.连续生产的情况下两件成品之间的间隔时间*一件产品从进入到设备开始到成为成品离开设备的时间* 如果该设备为多穴同时加工,则CT=两模之间的间隔时间÷穴数** 实际生产节拍通常由工程师现场测量(或设备自动记录)多组数据后求平均值得到理想节拍时间工艺设计时规划的理论节拍时间此时间不考虑任何影响因素设备PT 实际节拍时间**实际生产中两件产品之间的间隔时间设备不能按照理论设计节拍工作,原因包含但不仅限于,机器老化,来料不良,人员影响等单台设备OEE 计算例题--题目摘自百度百科,笔者略作修改并订了正错误OEE=利用率X表现性X质量指数利用率=实际操作时间/计划工作时间表现性=实际总产量/(实际操作时间/理想节拍时间)质量指数=良品数量/实际总产量设某设备某天工作时间为8h, 班前计划停机15min, 故障停机30min,设备调整25min, 产品的理论加工节拍为0.6min/件, 这天一共加工产品450件, 其中有20件废品, 求这台设备的OEE。
自动化生产流水线节拍、设备利用率计算
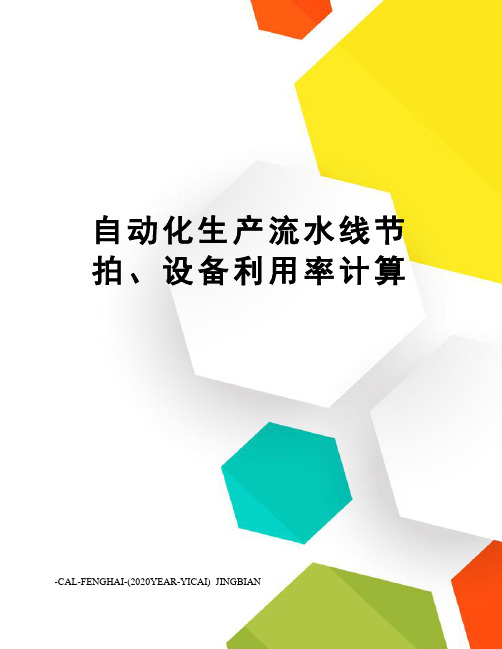
自动化生产流水线节拍、设备利用率计算-CAL-FENGHAI-(2020YEAR-YICAI)_JINGBIAN自动化生产流水线节拍流水线的负荷系数又称编程效率,其值越大,表明流水线的生产效率越高。
流水线上总负荷系数可按下列公式计算:η=T/(N×Pt)其中η为负荷系数Pt为生产节拍=计划期有效工作时间/计划期产品产量=标准总加工时间/作业员人数=有限机种的标准总加工时间/有限机种台数N为工位数T为所有工位完成一个节拍所用时间之合一般以工作地(机器)作计算单元的,流水线的负荷系数不应低于;以操作工人作计算单位的,其流水线的负荷系数应在-以上。
举个例子某一新开设的丁恤衫制衣厂,生产目标为每日1000件T恤杉、每日工作8h。
生产工序和每个工序的日产量如表所示工序名称 8H产量1装袋 3202缝肩 10003缝领 5004缝袖 9505上袖 4006上领 4807车边 10508开门 9009钉纽 950①计算这条生产线的生产节拍PtPt=H/Q=8×60/1000=/件②计算每个工序所需的标准作业时间,结果如表5-8③计算每个工位所需的工位数,结果列于表5-8例如,第一个工序的作业时间第一个工序理论上所需的工位数= 15/=个工序名称作业之间计算工位数实际工位1 32 1 13 2 24 15 36 27 18 19 1合计 15④计算出理论上该生产线所需的最小工作位数,即Nmin=[T/Pt]+1=[]+1=15个⑤计算该生产线平衡后的平均负荷率η=T/(N×Pt)×100%=(15× ×100%=&依照工序流程安排生产线,首先要按照每个工序的难易程度,计算出各工序所需的工作位数目,务必使各工序每小时的总产量大致相同,才能得到一条子衡的生产线,例1中该生产线平衡后实际的节拍应为(瓶颈工作地节拍),平衡后的工序负荷率为%。
流程的“节拍”(Cycle time)是指连续完成相同的两个产品(或两次服务,或两批产品)之间的间隔时间。
设备综合利用率统计表

可利用时间(H)
实际运行时间(H)
0
0
0
0
0
换线程序导入及修正时间(H)
换线更换刀具时间(H)
换线更换夹具时间(H)
日常点检时间(H)
机床预热及5S时间(H)
计划保养时间(H)
计划待料时间(H)
QC首件确认时间(H)
计划停机时间(H)
0
0
0
0
0
更换刀具(H)
11 程序修正(H) 夹具修正(H)
机床维修(H)
换线更换刀具时间(H)
换线更换夹具时间(H)
日常点检时间(H)
机床预热及5S时间(H)
计划保养时间(H)
计划待料时间(H)
QC首件确认时间(H)
计划停机时间(H)
0
0
0
0
0
更换刀具(H)
6 程序修正(H) 夹具修正(H)
机床维修(H)
异常待料时间(H)
异常停机时间(H)
0
0
0
0
0
利用水准(AL)
#DIV/0! #DIV/0! #DIV/0! #DIV/0! #DIV/0!
异常待料时间(H)
异常停机时间(H)
0
0
0
0
0
利用水准(AL)
#DIV/0! #DIV/0! #DIV/0! #DIV/0! #DIV/0!
标准产量(PCS/H)
标准产出(PCS)
0.00
0.00
0.00
0.00
0.00
实际产出(PCS)
运行水准(OL)
#DIV/0! #DIV/0! #DIV/0! #DIV/0! #DIV/0!
换线更换刀具时间(H)
设备利用率OEE计算

设备利用率O E E计算 Prepared on 24 November 2020如何计算工厂的整体设备效能日本工厂设备维修保养协会的Seiichi Nakajima曾表示,对于分散式生产的制造商来说,工厂整体设备效能(以下简称OEE)如果能达到85%,就可以被公认为世界一流的。
然而实际上目前并没有一个通用的工厂整体设备效能的计算方法。
在进行车间的OEE的数据处理计算时,应考虑多种因素。
下面介绍的方法包含了一种计算生产线或生产流程的OEE,它也可推广用于计算整个工厂的OEE。
计算生产线或生产流程上的OEE如果所有的机器相对于生产率和生产能力来说其贡献是相同的,那么计算生产线的OEE就简单了。
但是完全均衡的生产线几乎没有,并且它也不能代表大多数工厂的真实情况。
另外,大多数工厂并非都是一条笔直的生产线,其生产的产品部件能从一台机器非常和谐的传到另一台机器而且设备之间也非常谐调。
实际上,一个生产流程往往是非常复杂的,生产线上的机器有些是串联关系,有些是并行工作,而且它们常常还有旁路流程。
因此直接计算生产线或生产流程的OEE而不计算各单个机器的OEE是不可能的。
生产线或生产流程的OEE计算,在理论上认为整个生产线或生产流程是一个单独的机器,它理论上的生产周期等于生产流程中瓶颈机器的生产周期。
例如,如果一条生产线上有三个机器,它们的生产周期分别为:3秒,2秒和4秒,则总的生产流程周期为4秒,即为瓶颈机器的生产周期。
生产线作为一个整体,在4秒钟之内它只能生产一个产品。
一个生产流程的关键是它要在瓶颈机器这一环节上保持一个高的可用度、生产率和优质率。
在典型的生产流程中各台机器的加工生产之间都有一定的时间冗余,如果这个时间冗余能够控制或允许一些机器短暂时间的停机,而不影响整个的生产流程,则它并不影响整个生产线或生产流程上的生产率。
如果这个时间冗余不能弥补其它机器的短暂停机时间,瓶颈机器就会由于没有原料而停机或阻塞下面的流程,而不能生产出额外的资料。
设备利用率计算表(依据产能)

8:00-9:009:00-10:0010:00-11:0011:00-12:0012:00-13:0013:00-14:0014:00-15:0015:00-16:0016:00-17:0017:00-18:0050048048048048049048048048050046048196.20%40038038039038039038028039038038037393.25%60058058061048050048048048050046051585.83%50048048048048049048048048050046048196.20%49048048048048049048048048050046048198.16%50048048048048049048048048050046048196.20%80078078048068079078048069070076069286.50%70068068068058069068058066067062065293.14%车间设备编号设备名称理论时产日均每小时实际产量生产管理工具——生产计划与控制管理设备利用率计算表说明:设备利用率是指某时间阶段设备实际使用时间占计划用时的百分比,是指设备的使用效率,是反映设备工作状态及生产效率的技术经济指标。
由于设备投资常常在企业总投资中占较大的比例,设备能否被充分利用,直接关系到投资效益。
本表格可以帮助生产管理者有效监控设备利用率,并通过数据比较分析,不断改进、提高设备的利用率。
计算公式:公式一:设备利用率=每小时实际产量/ 每小时理论产量×100%。
编制部门/车间: 编制人: 编制日期:实际时产记录核准:审核:制表:设备利用率备注。
设备利用率统计分析图表(年度)
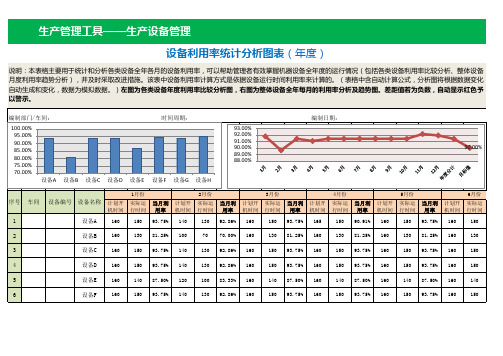
130 81.25% 160
130 81.25% 160
130 81.25% 1860
1500
93.75% 160
150 93.75% 160
150 93.75% 160
150 93.75% 160
150 93.75% 160
150 93.75% 160
150 93.75% 1900
1780
93.75% 160
设备名称
计划开 机时间
1月份
实际运 行时间
当月利 用率
计划开 机时间
2月份
实际运 行时间
当月利 用率
计划开 机时间
3月份
实际运 行时间
当月利 用率
计划开 机时间
4月份
实际运 行时间
当月利 用率
计划开 机时间
5月份
实际运 行时间
当月利 用率
计划开 机时间
6月份
实际运 行时间
设备A
160
150 93.75% 140
100 83.33% 160
140 87.50% 160
140 87.50% 160
140 87.50% 10 93.75% 140
130 92.86% 160
150 93.75% 160
150 93.75% 160
150 93.75% 160
150
7
设备G
8
设备H
设备总体利用率合计
生产管理工具——生产设备管理
设备利用率统计分析图表(年度)
说明:本表格主要用于统计和分析各类设备全年各月的设备利用率,可以帮助管理者有效掌握机器设备全年度的运行情况(包括各类设备利用率比较分析、整体设备 月度利用率趋势分析),并及时采取改进措施。该表中设备利用率计算方式是依据设备运行时间利用率来计算的。(表格中含自动计算公式,分析图将根据数据变化 自动生成和变化,数据为模拟数据。)左图为各类设备年度利用率比较分析图,右图为整体设备全年每月的利用率分析及趋势图。差距值若为负数,自动显示红色予 以警示。
- 1、下载文档前请自行甄别文档内容的完整性,平台不提供额外的编辑、内容补充、找答案等附加服务。
- 2、"仅部分预览"的文档,不可在线预览部分如存在完整性等问题,可反馈申请退款(可完整预览的文档不适用该条件!)。
- 3、如文档侵犯您的权益,请联系客服反馈,我们会尽快为您处理(人工客服工作时间:9:00-18:30)。
生产管理工具——生产设备管理
设备利用率计算表
说明:设备利用率是指某时间阶段设备实际使用时间占计划用时的百分比,是指设备的使用效率,是反映设备工作状态及生产效率的技术经济指标。
由于设备投资常常在企业总投资中占较大的比例,设备能否被充分利用,直接关系到投资效益。
本表格可以帮助生产管理者有效监控设备利用率,并通过数据比较分析,不断改进、提高设备的利用率。
计算公式:公式一:设备利用率=每小时实际产量/ 每小时理论产量×100%。
版权所有:
北京未名潮管理顾问有限公司。