公司仓库进料作业流程
进料检验控制程序

进料检验程序1.目的规范外购、外协材料的检验作业, 确保物料入库合格, 防止不合格品的非预期使用。
2.范围适用于外购、外协生产物料的检验(包括测试)。
3.职责3.1仓库: 负责进料的点收、保管, 不合格品的隔离及记账等工作。
3.2采购: 负责与供应商联络、处理来料异常事项。
3.3检验:负责进料的品质检验/试验, 并做好相应的检验状态标志;负责启动进料不合格品处理作业流程。
4.作业程序4.1供应商交货到厂后, 仓管员将供应商的送货单与实际数量进行核对, 无误后将物料放入收货待检区。
4.2仓管员在规定时间内完成物料数量验收, 并在物料包装明显位置上贴好物料标示卡。
4.3仓管员以《送检单》书面方式通知原材料检验员, 并指明物料所在位置。
若为紧急来料, 仓管员可先电话通知原材料检验员先检而后补《送检单》报检。
4.4原材料检验在收到仓库报检的《送检单》后10分钟内须向仓管员回复检验时间。
若来料为生产急需料或为原材料检验可在30分钟内鉴定的物料, 原材料检验员须在接到《送检单》后10分钟内进行现场检验。
4.5原材料检验员按物料检验标准确定待检物料的检验方案, 准备好相关的图纸资料、样品、检验用具。
如果是客户提供物料或客户指定的特殊来料, 由销售部提供客户物料具体规格及客户品质明确要求, 以便原材料检验员进行检验。
4.6原材料检验员按进料检验规范、全检物料清单、批量产品抽样方案对物料进行抽样或全检, 并对照图纸、样板、BOM等进行检验工作, 并将检验结果记录在原材料检验报告上(要求原材料检验报告必须填写完整、正确、规范)。
4.7送检物料检验合格后不需进行性能测试的, 由原材料检验员在物料包装明显位置贴上绿色合格标签, 填写完整的检验内容(包括物料名称、规格/型号、检验员、日期等内容)。
4.8送检物料若需进行性能测试的, 由原材料检验员按测试标准进行性能测试, 将测试结果记录在检验报告上, 要求当天的测试工作于一个工作日内完成。
物料出入库作业流程
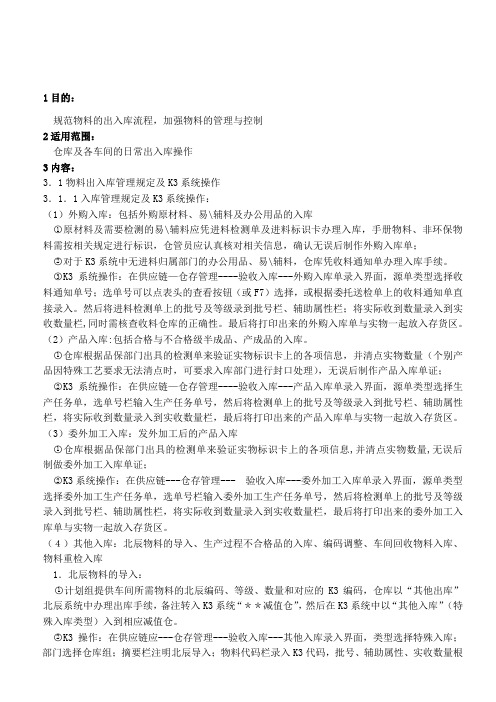
1目的:规范物料的出入库流程,加强物料的管理与控制2适用范围:仓库及各车间的日常出入库操作3内容:3.1物料出入库管理规定及K3系统操作3.1.1入库管理规定及K3系统操作:(1)外购入库:包括外购原材料、易\辅料及办公用品的入库○1原材料及需要检测的易\辅料应凭进料检测单及进料标识卡办理入库,手册物料、非环保物料需按相关规定进行标识,仓管员应认真核对相关信息,确认无误后制作外购入库单;○2对于K3系统中无进料归属部门的办公用品、易\辅料,仓库凭收料通知单办理入库手续。
○3K3系统操作:在供应链—仓存管理----验收入库---外购入库单录入界面,源单类型选择收料通知单号;选单号可以点表头的查看按钮(或F7)选择,或根据委托送检单上的收料通知单直接录入。
然后将进料检测单上的批号及等级录到批号栏、辅助属性栏;将实际收到数量录入到实收数量栏,同时需核查收料仓库的正确性。
最后将打印出来的外购入库单与实物一起放入存货区。
(2)产品入库:包括合格与不合格级半成品、产成品的入库。
○1仓库根据品保部门出具的检测单来验证实物标识卡上的各项信息,并清点实物数量(个别产品因特殊工艺要求无法清点时,可要求入库部门进行封口处理),无误后制作产品入库单证;○2K3系统操作:在供应链—仓存管理----验收入库---产品入库单录入界面,源单类型选择生产任务单,选单号栏输入生产任务单号,然后将检测单上的批号及等级录入到批号栏、辅助属性栏,将实际收到数量录入到实收数量栏,最后将打印出来的产品入库单与实物一起放入存货区。
(3)委外加工入库:发外加工后的产品入库○1仓库根据品保部门出具的检测单来验证实物标识卡上的各项信息,并清点实物数量,无误后制做委外加工入库单证;○2K3系统操作:在供应链---仓存管理--- 验收入库---委外加工入库单录入界面,源单类型选择委外加工生产任务单,选单号栏输入委外加工生产任务单号,然后将检测单上的批号及等级录入到批号栏、辅助属性栏,将实际收到数量录入到实收数量栏,最后将打印出来的委外加工入库单与实物一起放入存货区。
仓库进销存工作管理制度(精选7篇)

仓库进销存工作管理制度(精选7篇)仓库进销存工作管理制度篇11、收货流程1.1.正常产品收货1.1.1根据供应商到货通知在货物到达后,收货人员根据司机的随货箱单清点收货。
1.1.2收货人员应与司机共同掐铅封,打开车门检查货品状况,如货物有严重受损状况,需马上通知主管和物流经理等候处理,如货物状况完好,开始卸货工作。
1.1.3卸货时,收货人员必须严格监督货物的装卸状况(小心装卸),确认产品的数量,包装及保质期与箱单严格相符。
任何破损,短缺必须在收货单上严格注明,并保留一份由司机签字确认的文件,如事故记录单,运输质量跟踪表,送货单等。
破损,短缺的情况须及时上报主管及生管,以便及时通知客户。
1.1.4卸货时如遇到恶劣天气(下雨,大风,冰雹等),必须采取各种办法确保产品不会受损。
卸货人员须监督产品在码放到托盘上时全部向上,不可倒置,每堆码放的数量严格按照产品码放示意图。
1.1.5收货人员签收送货箱单,并填写相关所需单据,将有关的收货资料产品名称、数量、生产日期(保质期或批号)、货物状态等交主管。
1.1.6接单后必须在当天完成将相关资料通知记入台帐。
1.1.7破损产品须与正常产品分开单独存放,等候处理办法。
并存入相关记录。
1.2.退货或换残产品收货1.2.1各种退货及换残产品入库都须有相应单据,如运输公司或司机不能提供相应单据,仓库人员有权拒收货物。
1.2.2退货产品有良品及不良品的区别,如良品退货,货物必须保持完好状态,否则仓库拒绝收货;不良品收货则必须与相应单据相符,并且有完好的包装。
1.2.3换残产品则须与通知单上的型号、编号相符,否则仓库拒绝收货。
1.2.4收货人员依据单据验收货物后,将不同状态的货物分开单独存放,将退货或换残单据及收货入库单,记录产品名称、数量、状态等交。
1.2.5依据单据记入台账。
2、发货流程2.1.1所有的出库必须有公司授权的单据(授权签字,印章)作为发货依据。
2.1.2接到公司出库通知时,仓管进行单据审核(检查单据的正确性,是否有充足的库存),审核完毕后,通知运输部门安排车辆。
仓储程序文件

2.3 数量无误后,收货员在送货单上签名确认,开立“采购收货送检单”送 品管IQC,如需外发加工则开立“外发加工报检单”送品管课。
2.4 IQC依《进料检验控制程序》检验后,将检验结果及处理方法填在相对应 的送检单上,并由IQC作出合格与不合格标示,仓管员依此标示将合格品入 库,入完后仓管员在<采购收货送检单>上填写数量并签名;不合格依<不合 格品控制程序>理。
7.2 因制程报废物料需补料时,应开立“超领单”经品管课IPQC确 认,部门主管审核,生管课长、生管部长核准后方可补料,补 料后还应据此登记在相应的台帐上更改。
物料保存期限一览表
类别 塑胶件 五金件 化学品类 触点类
保存期限
类别
保存期限
12个月
漆包线
6个月
6个月
纸箱类
12个月
3个月
塑管、塑盒
6个月
3个月
6、原材料的出库:
6.1 生管凭“制造命令单”开立“发料单”交仓库文员过账,然后仓库 安排发料。
6.2 仓管员根据发料单进行发料
6.3 发料遵循“先进先出”的原则,仓管员备完料后,送料到生产车间门口.
6.8 对低值易耗品、辅助材料的领用,由领用部门开立“出仓单”,部门主管审核后,发料员 方可发料;文具等办公用品由领用部门根据自已预算及实际购入量开立“出仓单”;
6.9 捺印钢板、网板,由制造课开具“出仓单”经制造课长核准后,发料员审核后,仓管员方 可发料;
6.10 确保出仓物料上名称、料号、型号、规格相符、实发数准确无误,如出仓单、规格不完整 或所发物料有变动,应立即在单上注明或更改;发料单有类似问题则及时提报生管处理.
公司面里料进仓至成品入库管理分序流程

公司面里料进仓至成品入库管理分序流程
1. 面里料进仓管理流程
1.1 仓库接收面里料
•面里料由供应商送至公司仓库,仓库人员核对送货单和实际物品是否一致。
•若无异常,仓库人员记录面里料的基本信息,如数量、批次等。
1.2 面里料质检
•质检人员对面里料进行外观检查、抽样检测、化验等。
•合格的面里料通过质检,不合格的面里料退回供应商或做进一步处理。
2. 面里料生产加工管理流程
2.1 面里料调配
•生产计划员根据生产订单和产品配方,合理安排面里料的调配和使用顺序。
•仓库人员按照生产计划,将需要的面里料准备到生产线边。
2.2 面里料加工生产
•生产人员按照产品生产工艺要求,对面里料进行加工操作,生产出半成品或成品。
2.3 半成品入库管理
•生产完成的半成品经过质检合格后,由仓库人员记录并入库,为后续生产提供支持。
3. 成品入库管理流程
3.1 成品质检
•从生产线上出来的成品进行终检,确保产品质量符合标准。
•合格的成品进入下一流程,不合格的产品退回重工或报废处理。
3.2 成品入库记录
•仓库人员按照产品批次和数量记录成品入库情况,做好相关档案归档工作。
•入库记录需及时更新到系统中,以便后续查看和管理。
以上是公司面里料进仓至成品入库管理的分序流程,每个环节都需要严格执行,确保公司产品质量和生产效率。
仓库操作收货检验入库产品处理流程图
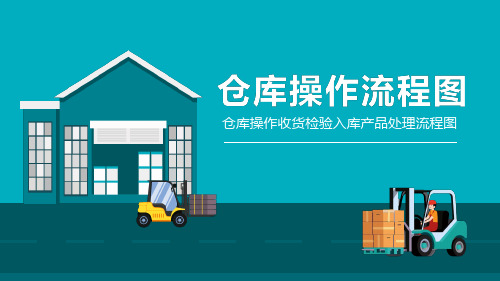
在金蝶系统中录入其他出库单
仓库操作流程图
盘点作业流程
每月最后一个工作日仓管人员从金蝶系统中打印盘点报告 仓管根据仓位顺序对仓库物料依次进行清点
仓管确认点数无误后将盘点信息登记在盘点报告上交财务复核 财务复核
仓管人员及财务人员在盘点报告上签字确认盘点结果 将盘点结果报送经理审批如有差异,在金蝶系统中进行账务调整
仓库操作流程图
生产任务单物料领用流程
备料时应在STOCK OUT LIST上将有IQC编号的物料 记录下来备查。格式为IQC编号_数量X
如有766516领用需通知质量部门IQC编号
生产部门开STOCK OUT LIST
仓管人员根据STOCK OUT LIST按照先进先 出原则将物料从货架中取出
相同产品、不同的WO编号的领 料单备料时应分开摆放
仓库操作收货检验入库产品处理流程图
仓库操作
仓库操作畅通、安全、有序,降低库存积压,提高库存周转 率,促使销售、生产、采购相协调,加速资金流通。采购物 资到厂后,供应商将送货单交仓管员,由仓管员引导供方将 物资存放在待检区。供应商《送货单》必须注明公司物料订 购单单号及订购数量、送货数量等信息。
仓库操作流程图
质量部门在入库单备注栏填写物料编码及可用数量 填写格式为:641931_10x for re-stock in
将可用物料拿回仓库上架并在金蝶系统录入其它入库单
仓库操作流程图
其他入库流程
在生产环节报废的物料重新检验后入库
检验完毕,质量部门开出OTHER STOCK IN给仓库
供应商赠送物料
是否需 要检验
N 与检验部门负责人再次确认
将合格物料上架
将不良品放入退货库
供应商开发票 将发票退回供应商
仓库进料管理规范
4.1.2供应商送货到仓库后,仓管员核对《送货单》与《采购订单》或《发外加工单》或《物料请购单》各项内容是否相符。并在《每日进料明细登记表》上作好相应的记录,以备追溯与查核;若为供应商原因错误,要求供应商纠正,并要求供应商送货人员在纠正处签名确认,若为我方原因错误,则通知相应的采购员确认原因,直至清楚后方可收货。
4.4.2仓管员将物料进到相应仓位后,于10分钟内详细填写物料《物料存卡》;并将《材料进货单》签回并入库。
4.5表单处理
4.5.1所以供应商的《送货单》在仓管员核对点收后2分钟内登记在《每日进料明细表》。
4.5.2账务员在收到仓管员交的《送货单》在2分钟内输入系统,入完后将《送货单》同《每
日进料明细表》交IQC,IQC并在《每日进料明细表》中对应的单号签收栏签名。
6.5《进料入库单》
在物料外包装进料标签上盖红色“IQC REJ”章,同时在外包装上贴红色退货标签,并
注明不良原因,IQC在《送货单》中注明“退货”后交仓库办理退货,具体按《进料不合格品处理作业流程》进行作业。
4.4入库与进帐
4.4.1账务员在收到品管员的《检验报告》、《送货单》后,在5分钟内在系统里查核《材料进货单》验收数量,并打印《材料进货单》,通知入库员将合格物料入库。
4.1.3若对单无误,则由仓管员通知供应商送货人员,将需检验的物料卸在指定的收料待检区。4.1.4供应商按规包装、标识、堆叠、摆放:
A:包装要求:
1.电子、五金、塑胶、小件包材等物料必须用专用纸箱或胶箱包装,不能用水果类箱、饮料类箱、酒类箱等包装交货。
2.而却每一批送货包装规格要一致。
仓储中心作业流程
仓储中心各环节作业流程描述为适应公司的快速发展,提升仓储中心的管理水平,规范员工的作业程序,提高工作质量和工作效率。
现对仓储各岗位的操作流程描述如下。
概述:A、物料备件收发流程B、卷板收发流程A、物料备件收发流程(一)、流程图:(二)流程描述:外购外协单核对流程、物料备件验收作业流程、物料备件发货作业流程、物料备件退仓退货流程、日常管理和盘点管理1外购外协单核对流程库存名称及数据查询一仓库确认返单1.1库存名称及数据查询1.11各领料部门将计划采购的外购外协单明细交仓库进行物料名称及库存数的确认。
1.12仓管员在ERP系统上查询名称是否已在系统上存有记录以及库存数量情况,仓管员对必须于外购外协单上的物料名称进行纠正及规范,规范原则是以系统名称为准。
1.2仓库确认返单1.21仓库将上述内容复核后签名确认后交给领料部门。
2物料备件验收作业流程核对单据及实物一办理进仓手续2.1核对单据及实物2.11仓管员收到《申请物料采购计划单》”必须先检查单据的填写手续是否完整,不符合要求的退回,《申请物料采购计划单》仓库用于在供应商或采购人员送货时作进仓的依据。
2.12供应商或采购人员送货到仓库时,仓管员首先要根据其送货单上注明的《申请物料采购计划单》编号查找核对是否有有效的《申请物料采购计划单》方能办理后续的收货手续,对于某些临时紧急需要申购的备件,若相关部门直接通知采购部购买的,必须在物资到货后24小时内补办已审批的“《申请物料采购计划单》”。
2.13当值仓管员接收“紧急申购”的物料备件时,必须立刻向相关申购部门部长或授权人汇报,等确认及验收物资后再办理进仓手续,同时,仓管员必须做好《申请物料采购计划单》”补办的跟踪工作,需要交接班的,也必须交接。
2.14在规定时间内没有补办手续的,仓管员将以书面报告形式向相关部门部长或授权人汇报,并建议其部门作出处理(报告一式两份,一份备件仓留,另一份由物料组长交给相关部门部长或授权人)。
工厂仓储收发存作业流程,生产企业货物管理具体操作步骤
浙江大中能源有限公司工厂仓储收发存作业流程全文目录1. 目的 (1)2. 范围 (1)3. 定义 (1)4. 职责 (2)4.1 非生产部门 (2)4.2 生产部门 (2)4.3 采购部 (2)4.4 品质部 (2)4.5 成品检测部 (3)4.6 计划部 (3)4.7 仓储物流部 (3)4.8 商务部 (4)4.9 财务部 (4)5. 作业内容(具体操作流程步骤) (4)采购入库流程 (4)5.2 生产订单物料领用流程 (6)非生产订单物料领用流程 (7)产成品入库单流程 (8)销售出库流程 (10)销售退货 (11)物资存放管理 (11)5.8 报表管理规定 (12)1. 目的为加强成本核算,提高公司的基础管理工作水平,进一步规范存货流通、保管和控制程序,维护公司资产的安全完整,加速资金周转,特制订本办法。
2. 范围凡公司存货收、发、存作业均适用本办法。
3. 定义3. 1采购入库流程3. 2生产物料领用流程:3. 3 非生产物料领用流程;3. 4产成品入库流程;3. 5 销售出库流程3. 6销售退货流程4. 职责4.1 非生产部门4.1.1 ERP系统中领料单及时开立与审批流及时完成(平时物料领用);4.1.2 ERP系统中请购单及时开立与审批流及时完成(月度预算内请购时,汇总请购计划于上月28日于ERP系统中操作完成;预算外请购时,ERP系统请购单当日开立、审批完成);根据领料单确认实物后,在仓库账务员开立的出库单上签字确认;4.1.4 实物退回仓库后,在仓库账务员开立的红字出库单上签字确认;4.1.5 报废品入库与仓库确认签收;4.1.6 无领料单不得领料;4.2 生产部门4.2.1 由生产主管以上级人员与仓库、计划部对接,处理物料领、退的账务确认与实物接收工作;4.2.2 溢领流程需在溢领实物当日ERP账务处理完成;4.2.3 非在制订单用料及时办理退库;及时办理废品入库;生产订单关闭前按计划部通知及时清理订单领、退物料(每月底盘点前一日处理完成);4.2.4 生产订单物料与仓库物料员每日在出库单上确认签收;非生产订单物料开立领料单至仓库领用,并在出库单上确认签收;4.2.5 无生产订单与领料单不得领料;4.3 采购部4.3.1 非请购不得下达采购(无ERP请购单不得下达采购订单);4.3.2 已完成采购订单及时关闭(每月处理一次);4.3.3 供应商送货单必须备注采购订单号,以方便仓库对应入库;4. 采购订单下达及时性,避免实物到库,仓库无法办理入库与出库;4. 供应商来料不良物料及时办理退货;4.安全库存的掌控;4.4 品质部4. 供应商来料检验及时性(品管接到到货通知最迟24H检验完毕,以不同材料类别区分检验时间);4.4.2 紧急需求物料到货时检验及时性(为生产必须,配合采购到货检验);4.4.3 检验单据及时处理(报检单、检验单ERP开立及审批提交),以方便仓库入仓管理;.4 硅片试投报告及时提供(投产12H);4.4.5 确认入库物料和出库产品的质量情况,对入库物料和发出产品的质量负责;根据检验销售退回的实物,确认退回原因及处理方式;4.4.6 生产制程中采购来料不良物料提报(确认原因并提报采购部处理:退货或扣款)4.5 成品检测部4.根据产线中生产完工打包的数量,填制ERP产成品入库单;产成品实物入库及时性,单据开立的正确性;4. 对需提醒仓库分开管理的产成品特别标识与区分,并及时通知仓库相关负责人;4. 每日与仓库物料员做好成品入库实物清点工作,与仓库账务员做好账务对接,保证成品及时入账;4.6 计划部4. BOM物料请购单开立及时性(按采购进料周期提前下达ERP物料请购);4. 生产订单下达及时性;4. 督促临时撤换订单时生产部门物料的退库并及时关闭此类订单;4. 以生产订单管控产线生产与物料,不得计划外生产;4. 产线在制物料管控及返工片最小留存量管控;4. 生产订单关闭及时性(以生产订单量等于入库量为基准);4. 仓库呆滞物料的消耗;4.7 仓储物流部4.7.1 仓库管理员:a)、根据入库单、红字出库单接收实物;根据生产订单、材料出库单、发放实物;根据销售出库单配货出库;首要原则“见单收发料”;b)、与物料员确认清点每次实物交接是否相符,与账务员确认每日账实是否相符;c)、严禁已收、发实物跨月处理账务;4.7.2 仓库账务员:a)、根据来料检验单、采购订单开立采购入库单;根据领料单开立材料出库单;根据仓管员与各部门签字确认的退料明细开立红字材料出库单;根据品质部与仓管员签字确认的客户退货明细,开立红字销售出库单;根据商务部发货单开立销售出库单;b)、与成品检测部确认每日ERP入库账务;与各领料部门确认每日ERP出库账务;c)、与仓库管理员确认每日账实是否相符;并随时对仓库实物进行抽查盘核;d)、当月ERP单据必须在公司盘点前一日账务处理完成;4.7.3 仓库配送员:a)、与仓库管理员清点确认物料,配送物料至生产部门,并与生产部门在出库单上确认签收;b)、与成品检测部清点确认入库成品,并与仓库管理员在实物入库前在成品入库单上确认签收;4.7.4 仓库班长:a)、审核仓库各项单据签核流程的完整性,数量的准确性,在ERP系统中确认仓库收发业务单据,以保证仓库账务处理及时性;b)、当日ERP单据确认工作,最迟不得超过次日10:00时;所有当月单据确认工作不得跨月,必须于月底盘点前一日处理完成;c)、确认仓库物料账实相符,并督促仓库管理员与仓库账务员的相互监督机制有效实施;d)、月底公司盘点前,必须对仓库进行全面初盘;e)、仓库各项流程的梳理、实施及资产的保全工作;4.8 商务部a)、销售发货单开立;b)、销售出库单的确认与签收;c)、客户退货、补货等异常处理跟踪;d)、销售退回产品需报废时,流程提报;4.9 财务部a)、抽查单据开立的正确性与审核的及时性,保证账物一致;b)、每月底存货盘点工作组织与实施;5. 作业内容(具体操作流程步骤)5.1采购入库流程5.1.1 时间节点:5.1.2 各部主要人员职责::a)、仓库账务员:a1)、无需检验的物料(根据到货单直接做入库):以仓库管理员点收完实物数量及各种有效票据,根据到货单开具入库单;a2)、需要检验的物料(根据采购到货单,品保来料报检验单、检验单做入库):以仓库管理员点收完实物数量及各种有效票据,根据检验部门的检验单,开具入库单;a3)、账务员应与仓库管理员工作交相稽核(账实相符核查);b)、仓库管理员:b1)、根据送货单及到货单将未开立入库单物料存放到待检区;b2)、无需检验的物料:点收完实物数量,通知账务员办理入库,以入库单点收实物入库;b3)、需要检验的物料:通知、督促相关检验部门及时检验完毕,点收完实物数量,通知账务员办理入库,以入库单点收实物入库;b4)、以ERP系统中入库单为基准收料,不得出现实物已入库而无ERP单据的情况发生。
仓库原材料出入库管理作业流程,仓库物料出入库操作指南
物料出入库治理规定1、总则1.1、制定目的:规范入库流程,使之有章可循。
1.2、适用范围:本公司使用的原材料、辅助材料、板材、工具悉依本规定办理。
2、原材料入库规定2.1、暂收作业流程①、采购人员与供给商于送交物料到公司时,仓库人员必须填写《入库单》一式三联,具体填写订购单号码、日期、品名、料号、数量并送到点收处,并将《入库单》立即交于IQC人员。
②、仓库人员将《入库单》与本公司《订购单》核对;IQC人员接到《入库单》后,立即开立《进料检验单》并对来料进行检验,确认无误在入库单上签字。
③、仓库人员将《入库单》与本公司《订购单》核对;点收人员对进入供给商所送之物料进行点收,核对物料质量与《入库单》无误后,再核对订单数量与所交数量是否相符入库,是否有超交现象。
④、超交之物料以退回为原则,但可以考虑让厂商寄存,而不作进料验收之处理。
⑤、点收人员核对无误后,在《入库单》上签章,并将其内容转记于《原材料暂收日报表》。
⑥、点收人员若在核对送交物料时,发现数量不符,或混有其他物料,以及其它非凡情况时,必须要求供给商之送货人员立即修改《送货单》或予以拒收。
2.2、验收检查①、原材料的验收检查,由品质部进料检验依《进料检验规定》,实施检验。
②、进料检验结果有三种,即合格(或允收)、不合格(或拒收)与特采(或让步接受)。
③、判定合格时,须将良品总数填入《进料检验单》合格栏内并签字,经部门主管/经理核准后,第一至三联转交仓库人员,以利办理入库手续。
④、判定不合格时,须于《进料检验单》上注明,并签字,同时填写《不合格处理单》一式两联,经部门主管/经理审核后,留存《进料检验单》第三联及《不合格处理单》第二联,将《进料检验单》第一、二联转仓管人员,将《不合格处理单》第一联转采购人员,以利办理退货手续。
⑤、判定不合格而暂收之物料应予以办理退货,但因实际需要,须对暂收中的物料的一部分或全部进行特采使用时,依《来料作业指导书》中有关特采的流程办理特采。
- 1、下载文档前请自行甄别文档内容的完整性,平台不提供额外的编辑、内容补充、找答案等附加服务。
- 2、"仅部分预览"的文档,不可在线预览部分如存在完整性等问题,可反馈申请退款(可完整预览的文档不适用该条件!)。
- 3、如文档侵犯您的权益,请联系客服反馈,我们会尽快为您处理(人工客服工作时间:9:00-18:30)。
公司仓库进料作业流程
1.0 目的
为了进一步规范和完善仓库进料作业程序,确保进料得到合理、及时的处理,控制进料数量,以满足生产需要。
2.0 范围
适用于本公司对外采购的所有原材料、辅助材料,发外加工的物料、半成品。
3.0 职责
3.1 物控部(仓库):负责物料的接收,清点与入库、记帐工作。
3.2 物控部(采购):负责来料过程中的供应商异常情况的协调与处理工作。
3.3 品管部:负责物料的品质检验工作。
4.0作业程序
4.1供应商送货
4.1.1采购员要求供应商按照公司要求填写规范、完整、准确的《送货单》,若为生产急料,采购员须于供应商送货到厂前1个小时通知仓库作好收货准备工作,若为供应商晚上送货厂的当天下次前通知仓管员加班收货。
4.1.2供应商送货到仓库后,仓管员核对《送货单》与《采购订单》或《发外加工单》或《物料请购单》各项内容是否相符。
并在《采购订单》上作好相应的记录,以备追溯与查核;若为供应商原因错误,要求供应商纠正,并要求供应商送货人员在纠正处签名确认,若为我方原因错误,则通知相应的采购员确认何种原因出错,直至清楚后方可收货。
4.1.3若对单无误,则由仓管员通知供应商送货人员或公司搬运人员,将需检验的物料卸在指定的收料待检区,将不需要检验的物料直接卸在物料暂存区。
若是生产急料,仓管员可将料收到生产备料区。
4.2进料数量验收
4.2.1货卸至指定区域后,仓管员将大件箱数与《送货单》核对后,再按照20% -50%的比例抽查单位包装,单位包装内若出现包装不足的现象,应与供应商送货员一起确认,再加大比例抽样(最高100%清点),同时,通知采购员前来确认。
4.2.2加大比例抽样比例后,计算出包装不足的平均数量,然后计算出总的包装不足数量,由供应商送货员更改《送货单》并签名,之后,仓管员方可盖“收货章“,并在《送货单》上注明实收数量。
4.2.3对于来料数量无法清点或难以清点的物料,仓管员应在《送货单》上注明“细数未点”字样,表示具体数量待检验或计量后确认。
4.2.4仓管员在核对、点收实物过程中,若发现供应商物料不符合本厂产品防护及有关采购要求(包括包装破烂,来料凌乱,无物料标识或标识不清等),即通知采购员,由采购员与供应商进行沟通、处理。
4.2.5若来料为生产急料或为品质可在30分钟内鉴定的物料,由仓管员在接到《送货单》后5分钟内通知品管员进行现场检验。
4.2.6仓管员清点完物料数量后10分钟内,将《送货单》(若无《送货单》,则开具《内部联络单》交品质部进料检验员,并说明物料所在位置,以便品管员对物料进行品质检验。
免检物料不需要品管人员检验,直接办理入库。
若是外发缝制的半成品,则要求供应商提供该批次产品的《半成品/成品检验报告单》,直接办理入库,若不能提供则通知后整QC组长进行检验。
非生产用物料(办公用品、设备及其配件除外)由品管员同用料部门进行现场品质验收。
4.2.7数量验收处理时间:仓管员处理一般性非急用料的时间为30分钟,处理急料的时间为10分钟内。
4.3进料品质验收
4.3.1品质部进料品管员收到《送货单》后10分钟内须向仓管员回复检验时间。
检验过程具体按《进料检验作业流程》及相关检验标准进行,必要时,须对物料进行相关的测试与检验,检验完毕后贴上相应检验标签,检验标签上注明物料名称、检验员、检验日期等内容;
4.3.2经检验判定合格的,品管员须在物料外包装明显位置贴上“合格”标签,并做好检验记录,在检验结果判定后30分钟内出具检验报告并转交个物控部、仓库,仓管员及时将物料搬运到指定的储存位置摆放。
4.3.3经品质判定不合格的,品管员需在10分钟内报告品质经理,具体按《进料不合格品处理作业流程》进行作业。
4.4入库与进帐
4.4.1仓管员在收到品管员的《检验报告》、《送货单》后,应对进仓物料详细填写《物料标识卡》,尾数贴上《尾数标签》
4.4.2仓管员将物料进到相应仓位后,于10分钟内详细填写物料《物料存卡》;
4.4.3仓管员按实际进仓数量及单据管理要求于物料进仓后2小时内开具《材料/半成品进仓单》;
4.4.4仓管员在开具《材料/半成品进仓单》的当天内入好帐目,要求良品入良品帐,不良品入不良品帐;
4.5表单处理
4.5.1仓管员根据《材料/半成品进仓单》制作《每日收货汇总表》,并于当天下午下班前将《材料/半成品进仓单》、《每日收货汇总表》交仓库主管审核,仓库
主管审核后于次日上午9:00前由仓管员将《材料/半成品进仓单》报送财务部、物控部采购处,仓库主管将《每日收货汇总表》报送物控部物控处。
4.5.2仓管员将当天产生的单据分类,归档保管。
5.0处罚规定
5.1采购员未提前通知仓库作好收货前准备工作的,处罚责任采购员5元/次;
5.2仓管员未核对《送货单》与《采购订单》,并在《采购订单》上签署收货记录的罚款5元/次,若因此造成超收或错收物料的,按公司《赔偿管理制度》进行赔偿。
5.3未经制造中心总监批准仓管员超《采购订单》数量收货的,按公司《赔偿管理制度》进行赔偿。
5.4仓管员将需检验而未经品管员检验的物料入仓的,罚款10元/单;
5.5品管员未在检验完成后30分钟内出具《检验报告》并分送到相关部门的,罚
款5元/单。
5.6物料进仓时,仓管员未依《仓库管理制度》进行摆放的,罚款5元/次;
5.7物料进仓归位后,仓管员未在规定的时间内登记卡帐或台帐的,罚款5元/次。
5.8仓管员收料进仓不作计量,在抽查时发现物料不足的,对仓管员出发10元/次,并视情况按《赔偿管理制度》进行处理;
5.9仓库未在规定时间内报送相关表单的,处罚责任人5元/次。
6.0相关表单
6.1《送货单》
6.2《采购订单》
6.3《物料请购单》
6.4《每日收货汇总表》
6.5《检验报告》
6.6《检验标签》
6.7《物料标识卡》
6.8《尾数标签》
6.9《物料存卡》
6.10《材料/半成品入库单》。