脱硫技术简介
脱硫技术简介
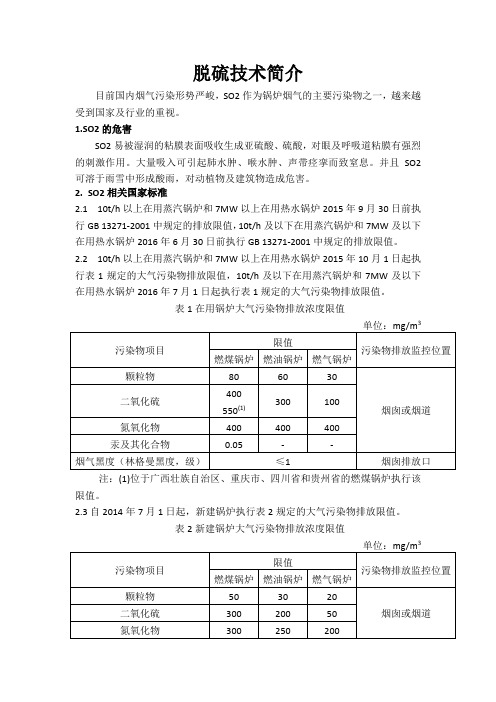
脱硫技术简介目前国内烟气污染形势严峻,SO2作为锅炉烟气的主要污染物之一,越来越受到国家及行业的重视。
1.SO2的危害SO2易被湿润的粘膜表面吸收生成亚硫酸、硫酸,对眼及呼吸道粘膜有强烈的刺激作用。
大量吸入可引起肺水肿、喉水肿、声带痉挛而致窒息。
并且SO2可溶于雨雪中形成酸雨,对动植物及建筑物造成危害。
2.SO2相关国家标准2.1 10t/h以上在用蒸汽锅炉和7MW以上在用热水锅炉2015年9月30日前执行GB 13271-2001中规定的排放限值,10t/h及以下在用蒸汽锅炉和7MW及以下在用热水锅炉2016年6月30日前执行GB 13271-2001中规定的排放限值。
2.2 10t/h以上在用蒸汽锅炉和7MW以上在用热水锅炉2015年10月1日起执行表1规定的大气污染物排放限值,10t/h及以下在用蒸汽锅炉和7MW及以下在用热水锅炉2016年7月1日起执行表1规定的大气污染物排放限值。
表1在用锅炉大气污染物排放浓度限值3注:(1)位于广西壮族自治区、重庆市、四川省和贵州省的燃煤锅炉执行该限值。
2.3自2014年7月1日起,新建锅炉执行表2规定的大气污染物排放限值。
表2新建锅炉大气污染物排放浓度限值单位:mg/m32.4重点地区锅炉执行表3规定的大气污染物特别排放限值。
执行大气污染物特别排放限值的地域范围、时间,由国务院环境保护主管部门或省级人民政府规定。
表3大气污染物特别排放限值单位:mg/m33.脱硫技术脱硫方法可划分为燃烧前脱硫、燃烧中脱硫和烟气脱硫(FGD)3类。
燃烧前脱硫:分物理脱硫和化学脱硫两种。
其优点是能同时除去灰分,减轻运输量,减轻窑炉的沾污和磨损,减少灰渣处理量,还可回收部分硫资源。
但煤的燃烧前的脱硫技术还存在着种种问题,得不到广泛应用。
炉内脱硫:是在燃烧过程中,向炉内加入固硫剂如CaCO3等,使煤中硫分转化成硫酸盐,随炉渣排除。
应用较多的就是循环硫化床锅炉。
缺点:脱硫效率低,对锅炉受热面磨损大。
热电厂脱硫的详细介绍

热电厂多是以燃烧煤作为发电的能源,煤中含有硫,燃烧出二氧化硫,会污染空气产生酸雨,所以常用的脱硫方法是石灰石—石膏湿法脱硫。
石灰石被磨碎,制成石灰石浆液,石灰石浆液与烟气中的二氧化硫反应生成石膏,这个过程就脱除了二氧化硫,接下来就为大家详细的讲解一下,希望对大家有所帮助。
1、脱硫原理。
石灰石—石膏湿法脱硫技术是将石灰石粉加水制成浆液作为吸收剂泵入吸收塔与烟气充分接触混合,烟气中的二氧化硫与浆液中的碳酸钙以及从塔下部鼓入的空气进行氧化反应生成硫酸钙,硫酸钙达到一定饱和度后,结晶形成二水石膏。
经吸收塔排出的石膏浆液经浓缩、脱水,使其含水量减小,然后用输送机送至石膏贮仓堆放,脱硫后的烟气经过除雾器除去雾滴,再经过换热器加热升温后,由烟囱排入大气。
由于吸收塔内吸收剂浆液通过循环泵反复循环与烟气接触,吸收剂利用率很高,钙硫比较低,脱硫效率高。
2、技术和经济性。
石灰石—石膏法脱硫工艺流程简单、技术先进又可靠,脱硫效率高以上,是
目前国内外烟气脱硫应用广泛的脱硫工艺。
但是系统复杂、设备庞大、耗水量大、一次性投资高,一般适用于大型电厂。
3、适用范围。
单塔处理脱硫量大,适用于任何含硫量的煤种的烟气脱硫,对锅炉的适应性强,一般在大型电厂或大功率锅炉使用。
正如上文所介绍的,使用石灰石—石膏湿法脱硫技术更加适合大型电厂等废弃排放量大的惬意,而且脱硫原料石灰石的价格也很便宜。
浙江钙科机械设备有限公司,于2014年三月注册成立,注册资金4500万元。
本公司与合肥水泥设计院合作,致力于石灰生产工艺研究,以改革目前我国石灰生产工艺为研究目标,为配套企业提供石灰原料。
密相干塔法脱硫
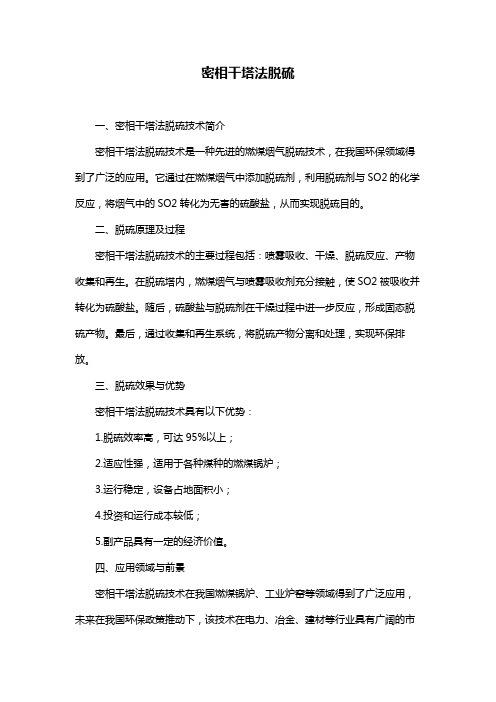
密相干塔法脱硫
一、密相干塔法脱硫技术简介
密相干塔法脱硫技术是一种先进的燃煤烟气脱硫技术,在我国环保领域得到了广泛的应用。
它通过在燃煤烟气中添加脱硫剂,利用脱硫剂与SO2的化学反应,将烟气中的SO2转化为无害的硫酸盐,从而实现脱硫目的。
二、脱硫原理及过程
密相干塔法脱硫技术的主要过程包括:喷雾吸收、干燥、脱硫反应、产物收集和再生。
在脱硫塔内,燃煤烟气与喷雾吸收剂充分接触,使SO2被吸收并转化为硫酸盐。
随后,硫酸盐与脱硫剂在干燥过程中进一步反应,形成固态脱硫产物。
最后,通过收集和再生系统,将脱硫产物分离和处理,实现环保排放。
三、脱硫效果与优势
密相干塔法脱硫技术具有以下优势:
1.脱硫效率高,可达95%以上;
2.适应性强,适用于各种煤种的燃煤锅炉;
3.运行稳定,设备占地面积小;
4.投资和运行成本较低;
5.副产品具有一定的经济价值。
四、应用领域与前景
密相干塔法脱硫技术在我国燃煤锅炉、工业炉窑等领域得到了广泛应用,未来在我国环保政策推动下,该技术在电力、冶金、建材等行业具有广阔的市
场前景。
烟气脱硫技术简介

国内烟气脱硫技术我国目前的经济条件和技术条件还不允许象发术达国家那样投入大量的人力和财力,并且在对二氧化硫的治理方面起步很晚,至今还处于摸索阶段,国内一些电厂的烟气脱硫装置大部分欧洲、美国、日本引进的技术,或者是试验性的,且设备处理的烟气量很小,还不成熟。
不过由于近几年国家环保要求的严格,脱硫工程是所有新建电厂必须的建设的。
因此我国开始逐步以国外的技术为基础研制适合自己国家的脱硫技术。
以下是国内在用的脱硫技术中较为成熟的一些,由于资料有限只能列举其中的一些供读者阅读。
石灰石——石膏法烟气脱硫工艺石灰石——石膏法脱硫工艺是世界上应用最广泛的一种脱硫技术,日本、德国、美国的火力发电厂采用的烟气脱硫装置约90%采用此工艺。
它的工作原理是:将石灰石粉加水制成浆液作为吸收剂泵入吸收塔与烟气充分接触混合,烟气中的二氧化硫与浆液中的碳酸钙以及从塔下部鼓入的空气进行氧化反应生成硫酸钙,硫酸钙达到一定饱和度后,结晶形成二水石膏。
经吸收塔排出的石膏浆液经浓缩、脱水,使其含水量小于10%,然后用输送机送至石膏贮仓堆放,脱硫后的烟气经过除雾器除去雾滴,再经过换热器加热升温后,由烟囱排入大气。
由于吸收塔内吸收剂浆液通过循环泵反复循环与烟气接触,吸收剂利用率很高,钙硫比较低,脱硫效率可大于95% 。
注意:锅炉出来的烟气经过除尘之后温度还是很高,而进入脱硫系统,温度是不能太高,温度过高,则吸收塔内的石膏结晶受到很大影响,而且设备的腐蚀和磨蚀会非常严重。
一般在原烟气和净烟气之间加设GGH(气气换热器),一方面对原烟气进行降温,以利于后面处理。
一方面对净烟气进行升温,有利于排烟的抬升,减少烟囱雨的形成,也在直观上减少烟囱排烟的量。
而且如果净烟气不升温的话,SO3会形成酸露,对烟囱的腐蚀非常严重。
脱硫过程的温度一般控制在40-60之间,不是需要太高的温度进行的。
旋转喷雾干燥烟气脱硫工艺喷雾干燥法脱硫工艺以石灰为脱硫吸收剂,石灰经消化并加水制成消石灰乳,消石灰乳由泵打入位于吸收塔内的雾化装置,在吸收塔内,被雾化成细小液滴的吸收剂与烟气混合接触,与烟气中的SO2发生化学反应生成CaSO3,烟气中的SO2被脱除。
脱硫的常见方式
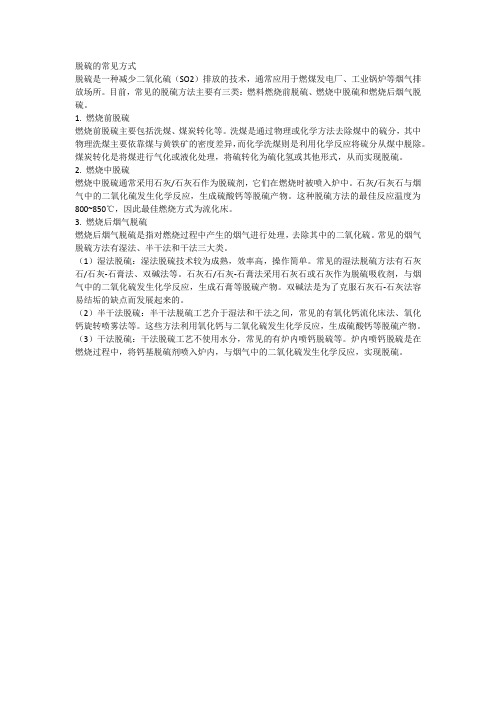
脱硫的常见方式脱硫是一种减少二氧化硫(SO2)排放的技术,通常应用于燃煤发电厂、工业锅炉等烟气排放场所。
目前,常见的脱硫方法主要有三类:燃料燃烧前脱硫、燃烧中脱硫和燃烧后烟气脱硫。
1. 燃烧前脱硫燃烧前脱硫主要包括洗煤、煤炭转化等。
洗煤是通过物理或化学方法去除煤中的硫分,其中物理洗煤主要依靠煤与黄铁矿的密度差异,而化学洗煤则是利用化学反应将硫分从煤中脱除。
煤炭转化是将煤进行气化或液化处理,将硫转化为硫化氢或其他形式,从而实现脱硫。
2. 燃烧中脱硫燃烧中脱硫通常采用石灰/石灰石作为脱硫剂,它们在燃烧时被喷入炉中。
石灰/石灰石与烟气中的二氧化硫发生化学反应,生成硫酸钙等脱硫产物。
这种脱硫方法的最佳反应温度为800~850℃,因此最佳燃烧方式为流化床。
3. 燃烧后烟气脱硫燃烧后烟气脱硫是指对燃烧过程中产生的烟气进行处理,去除其中的二氧化硫。
常见的烟气脱硫方法有湿法、半干法和干法三大类。
(1)湿法脱硫:湿法脱硫技术较为成熟,效率高,操作简单。
常见的湿法脱硫方法有石灰石/石灰-石膏法、双碱法等。
石灰石/石灰-石膏法采用石灰石或石灰作为脱硫吸收剂,与烟气中的二氧化硫发生化学反应,生成石膏等脱硫产物。
双碱法是为了克服石灰石-石灰法容易结垢的缺点而发展起来的。
(2)半干法脱硫:半干法脱硫工艺介于湿法和干法之间,常见的有氧化钙流化床法、氧化钙旋转喷雾法等。
这些方法利用氧化钙与二氧化硫发生化学反应,生成硫酸钙等脱硫产物。
(3)干法脱硫:干法脱硫工艺不使用水分,常见的有炉内喷钙脱硫等。
炉内喷钙脱硫是在燃烧过程中,将钙基脱硫剂喷入炉内,与烟气中的二氧化硫发生化学反应,实现脱硫。
脱硫技术

喷淋吸收塔示意图
38
石灰石/石 膏法的烟气 脱硫系统图
1—锅炉;2—电除尘器;6—吸收塔;9—氧化用空气;10—工艺过程用水;11—粉状石 灰石,13—粉状石灰石贮仓;14—石灰石中和剂贮箱;15—水力旋流分离器;16—皮带 39 过滤机;17—中间贮箱;18—溢流贮箱;20—石膏贮仓;21—溢流废水,22—石膏
三、海水烟气脱硫
• 海水因具有—定的天然碱度和特定 的水化学特性被用于烟气脱硫 • 海水烟气脱硫工艺适用于燃煤含硫 量不高并以海水为循环冷却水的海
边电厂
40
海水烟气脱硫工艺的主要特点
1. 工艺简单,无需脱硫剂的制备,系统可靠, 可用率高 2. 系统脱硫效率高,—般可达90% 3. 不需添加脱硫剂,也无废水废料处理问题 4. 与其它湿法脱硫工艺相比,投资省,运行费 用低 不足之处: 1. 其应用有局限性,只能用于海边电厂,适用 于燃煤含硫量不大于1.5%的中低硫煤 2. 重金属和多环芳烃的浓度不能超过规定的排 放标准
34
石灰石/石膏法
• 石灰石/石膏法和石灰石/石灰法最主 要的区别就是,向吸收塔的浆液中鼓入 空气,以强制使100%的CaSO3均氧化成 CaSO4(石膏)。这样,脱硫以后的固体副 产品不再是废物而需抛弃,而是有用的 石膏产品
35
石灰石/石膏法的优点
1. 吸收塔将洗涤循环、石灰石溶解、强制空气氧化 及石膏结晶结合为—体; 2. 洗涤循环底槽内有机械搅拌和氧化空气分配系统; 3. 石灰石粉与水混合制浆后定量加入吸收塔内; 4. 引风机位于吸收塔烟气入口,没有腐蚀和结垢的 问题,吸收塔正压运行; 5. 采用回转式气/气烟气再热器,利用原烟气自身 热能加热洗涤脱硫后的冷湿烟; 6. 石膏浆液经水力旋流分离器和真空皮带过滤器脱 水及热烟气干燥处理,最终副产品为粉状或块状 石膏; 7. 在燃煤含硫量为 0.7%~2.5% 时, Ca/S = 1.0~1.5 , 可以达到 90%~99.2%的脱硫效率。对于含硫量高 于3%的煤种,其运行经验较少 36
脱硫工艺流程
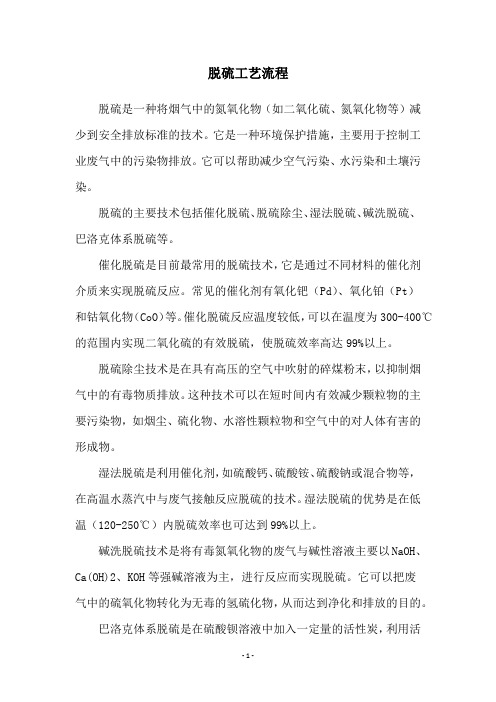
脱硫工艺流程脱硫是一种将烟气中的氮氧化物(如二氧化硫、氮氧化物等)减少到安全排放标准的技术。
它是一种环境保护措施,主要用于控制工业废气中的污染物排放。
它可以帮助减少空气污染、水污染和土壤污染。
脱硫的主要技术包括催化脱硫、脱硫除尘、湿法脱硫、碱洗脱硫、巴洛克体系脱硫等。
催化脱硫是目前最常用的脱硫技术,它是通过不同材料的催化剂介质来实现脱硫反应。
常见的催化剂有氧化钯(Pd)、氧化铂(Pt)和钴氧化物(CoO)等。
催化脱硫反应温度较低,可以在温度为300-400℃的范围内实现二氧化硫的有效脱硫,使脱硫效率高达99%以上。
脱硫除尘技术是在具有高压的空气中吹射的碎煤粉末,以抑制烟气中的有毒物质排放。
这种技术可以在短时间内有效减少颗粒物的主要污染物,如烟尘、硫化物、水溶性颗粒物和空气中的对人体有害的形成物。
湿法脱硫是利用催化剂,如硫酸钙、硫酸铵、硫酸钠或混合物等,在高温水蒸汽中与废气接触反应脱硫的技术。
湿法脱硫的优势是在低温(120-250℃)内脱硫效率也可达到99%以上。
碱洗脱硫技术是将有毒氮氧化物的废气与碱性溶液主要以NaOH、Ca(OH)2、KOH等强碱溶液为主,进行反应而实现脱硫。
它可以把废气中的硫氧化物转化为无毒的氢硫化物,从而达到净化和排放的目的。
巴洛克体系脱硫是在硫酸钡溶液中加入一定量的活性炭,利用活性炭的吸附作用,将烟气中硫氧化物等有毒物质吸附在活性炭表面,实现对环境的污染物的有效净化。
综上所述,脱硫工艺的主要技术有催化脱硫、脱硫除尘、湿法脱硫、碱洗脱硫以及巴洛克体系脱硫等。
这些技术都有自己的优势,在应用时可以根据实际情况选择最佳的技术方案,以减少环境污染,提高环境质量。
脱硫方法及其比较

脱硫方法及其比较脱硫是指从含硫燃料中去除硫化物的过程。
硫化物在燃烧过程中会产生有害的硫酸和硫酸盐,对环境和人体健康造成危害。
因此,脱硫技术在能源和环保领域中具有重要意义。
下面将介绍几种常用的脱硫方法及其比较。
1.石灰吸收法石灰吸收法是一种传统的脱硫方法,适用于高含硫煤和高温燃烧设备。
该方法利用石灰将燃烧产物中的硫捕获并形成硫化钙。
硫化钙可以作为建筑材料或化肥利用。
然而,石灰吸收法存在一些问题,如石灰需求量大、产生大量的废水与废渣等。
2.湿法石膏脱硫法湿法石膏脱硫法是一种湿法脱硫方法,通过将石膏和含硫燃料混合反应,形成硫酸钙脱除硫化物。
湿法石膏脱硫法具有较高的脱硫效率和较低的投资成本,在电力行业中广泛应用。
但是,湿法石膏脱硫法也存在一些问题,如处理大量的废水和废渣,处理过程中需添加大量的草酸等。
3.干法喷射碱脱硫法干法喷射碱脱硫法是一种常见的干法脱硫方法。
该方法通过将碱性吸收剂喷射到燃烧设备中,与硫酸盐反应生成硫化物,然后通过过滤装置进行分离。
干法喷射碱脱硫法适用于低温燃烧设备,并且可以降低废水和废渣的排放,减少环境污染。
然而,干法喷射碱脱硫法对吸收剂的选择和处理技术要求较高,操作复杂,投资成本较高。
4.生物脱硫法生物脱硫法是近年来发展起来的绿色脱硫技术,利用特定的硫酸盐还原菌将硫酸盐还原为硫化物,并最终生成硫和硫酸。
该方法具有脱硫效率高、能耗低、无二次污染等优点。
然而,生物脱硫法在应用中还面临着技术成熟度、处理量、原料适应性等问题。
综上所述,不同的脱硫方法各有利弊,并适用于不同的场景和需求。
在选择脱硫方法时,需要考虑燃料特性、设备条件、投资成本、环境要求等多个因素,并进行综合比较。
未来,随着环保意识的提高和技术的发展,更加高效和环保的脱硫方法将被广泛应用。
- 1、下载文档前请自行甄别文档内容的完整性,平台不提供额外的编辑、内容补充、找答案等附加服务。
- 2、"仅部分预览"的文档,不可在线预览部分如存在完整性等问题,可反馈申请退款(可完整预览的文档不适用该条件!)。
- 3、如文档侵犯您的权益,请联系客服反馈,我们会尽快为您处理(人工客服工作时间:9:00-18:30)。
2021/3/15
• 风机选型(四)
• 可靠性
• 动调和静调轴流风机的可靠性指标均为99%,但 由于动、静调各自的结构特点,在高温含尘烟气 的工作条件下,动调叶片磨损的潜在风险较静调 高。
2021/3/15
• 蓄热式气-气热交换器(GGH)(二) 当烟气中二氧化硫浓度很高或要求的脱硫率
非常高时,需要使用无泄漏的再热器。这 种气-气热交换器是吸热器和再热器的组 合,由电除尘器来的烟气被多管吸热器从 130℃冷却到97℃,FGD净化后的烟气被再 热器从48℃加热到80℃以上。无泄漏的气 -气热交换器的投资明显高于旋转式的投 资。不过可以由泄漏率的降低和占空间更 小的设备布置(对旋转式,烟道必须平行 布置),来补偿。
点,为了增加烟囱排放烟气的能力,减少可见烟团的出现 ,许多国家规定了烟囱出口的最低排烟温度,如德国。不 同的火电厂有不同的方法再热处理烟气。最简单的方法是 使用燃烧天然气或是低硫油的后燃器。与旋转式气-气热 交换器和多管气-气热交换器相比,这种方法要消耗大量 的能量,此外燃料燃烧又是另外一个污染源。另一种是采 用蒸汽-烟气再热器,使用工艺蒸汽或锅炉产生的热量。 蒸汽-烟气再热器的基本投资比蓄热式气-气热交换器低 ,但运行费用高。此外还必须注意高温蒸汽在管道烟气侧 结垢。安装蒸汽-烟气再热器主要是空间限制造成的。
2021/3/15
• 风机选型(二) 随着机组容量的大型化,风机的介质流量较大, 离心风机体积大、占地大,检修起吊困难的弊端 ,使其较少被采用,轴流风机则得到广泛的使用 。
• 一次性投资 静叶可调轴流风机比较便宜,大概是动调价格的 70~80%左右,并且由于其转速低,设备基础的 费用也略低。
• 维修费用 • 风机的维修费用主要考虑的是叶片的更换。动调
• 动叶可调式轴流风机 动叶可调轴流风机具有调节性能高的优点,
能很好的适应变工况负荷运行,它主要的 缺点一是耐磨性差,在烟气系统中,叶片 的磨损甚至剃光头的事,在国内时有发生 ;二是液压调节系统较复杂,给维修及运 行费用上造成一定困难。
2021/3/15
• 静叶可调式轴流风机
静叶可调轴流风机的优缺点均介于动调和离心之间 ,它的变负荷调节性能比离心机好,但比动调稍 差。与动调相比,静调在BMCR和ECR工况点的 效率差别在1%左右,在半负荷工况下差别约为 5~6%;但由于其空气动力性能的优越,使其耐磨 性能较好。另外,它的调节系统采用简单的电动 执行机构调节,可靠性较高,系统简单,维修也 方便。早期的静调风机主要是在拆缺转子时,要 连带拆下中空轴,比较麻烦,现在在二者之间采 用短轴连接,使转子能简便拆卸。随着检修条件 和性能的改善,静调轴流风机日益普遍用于大型 电站锅炉,同时,在FGD系统中亦被广泛采用。
风机的叶片是靠堆焊和喷涂耐磨材料来提高磨损 寿命,其寿命较静调短,但叶片更换费用高;另 外,其液压系统结构虽精密,但也易出现漏油、 卡涩,现场维修量也大。
2021/3/15
• 风机选型(三)
静调风机主要是靠改善风机的气体流动特性设计 叶型和轮毂,使含尘气体避免冲刷叶片根部而冲 刷叶尖部和后导叶,另外,同样要求下,静调的 转速比动调低一至二档。同时在叶片和后导叶上 喷涂耐磨材料,寿命相对长一些,叶片更换费用 也较低。
• 结论
• 从运行经济性分析,虽然动调的运行效率略高于 静调,但考虑维护、检修费用、一次性投资,静 调的经济性要略强于动调;
• 从安全可靠性、安装维护方面,静调为优。
• 综合指标:在烟气系统中,静叶可调轴流风机优 于动叶可调轴流风机 。
2021/3/15
二、烟气再热系统
• 烟气再热系统 烟气经过湿法FGD系统洗涤后,温度降到50-60℃,低于露
风机、动调轴流风机和静调轴流风机均占有较大 比例。用于烟气系统,离心风机由于叶片型式多 样,有前弯型、后弯型、板式等,使得其抗磨损 性能好;另外,离心风机在设计工况点的效率最 高。但离心风机的最大缺点一是叶片直径大,占 地和检修都不易解决,二是变负荷调节性能差, 随着风机参数的变化,效率下降很快。
2021/3/15
2021/3/15
• 蓄热式气-气热交换器(GGH)(一) 烟气再热器有蓄热式和非蓄热式两种。蓄热式工艺
利用未脱硫的热烟气加热冷烟气,简称GGH。蓄 热式又分回转式换热器、介质循环换热器和管式 换热器,均通过载热体或载热介质将烟气的热量 传递给冷烟气。旋转式换热器与电厂用的旋转式 空气预热器的工作原理相同,是通过平滑的或带 波纹的金属薄片或载热体将烟气的热量传递给净 化后的冷烟气。旋转式在150℃运行中遇到的问 题是热烟气会泄漏到冷烟气中,占总流量的3%- 5%。
风机位置 A
B
烟气温度/℃ 100-150 70-110
磨损
少
少
腐蚀
无
有
沾污
少
少
漏风率/% 3.0
0.3
能耗
100
90
C 45-55 无 有 有 0.3 82
D 70-100 无 少 无 3.0 95
2021/3/15
一、脱硫风机
• 升压风机的选择(一) 在目前国内200MW~600MW机组大型锅炉上,离心
脱硫技术简介
典型的工艺流程
2021/3/15
系统构成
• 石灰石制备系统:由石灰石粉料仓、石灰 石磨机及测量站构成。
• 吸收塔:由洗涤循环系统÷除雾器和氧化 工序组成的吸收塔。
• 烟气系统(脱硫风机、烟气再热系统) • 石膏脱水装置:由水力旋流分离器、真空
皮带过滤机和储存系统组成。 • 工艺水及废水处理系统 • 自动控制系统等
2021/3/15
系统构成(一)烟气系统
• 烟气系统:指锅炉烟气排出之后直到最后 经过烟囱排放到大气中的全行程控制系统 。
• 由除尘系统、脱硫系统、气/气换热器系统 、烟道烟囱及各种闸板门、旁道装置等组 成。
• 脱硫风机
装设烟气脱硫装置后,整个脱硫系统的烟气 阻力约为2940Pa,单靠原有锅炉引风机( IDF)需设助推风机,或称脱硫风机( 202B1/3U/15 F),脱硫风机有四种布置方案,四种布置