167_聂祚兴_车身接附点动刚度仿真及试验对标分析
车身关键接附点动刚度分析与改进
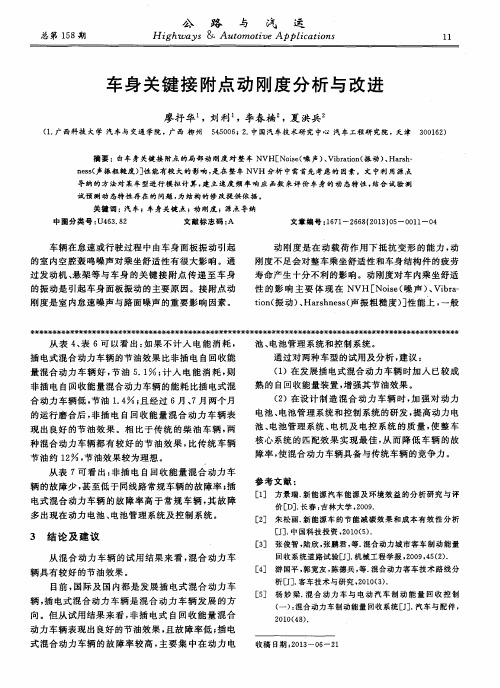
( 一) : 混合动力车制动能量 回收系统 [ J ] . 汽车与配件 ,
从表 4 、 表 6可 以看 出 : 如果不计入电能消耗 , 插 电式 混 合动 力车 辆 的节 油 效果 比非 插 电 自回收 能
池、 电池 管理 系统 和控 制系统 。 通 过对两 种 车型 的试用 及分析 , 建议 :
量 混合 动 力 车辆 好 , 节油 5 . 1 ; 计入 电能消耗 , 则 非 插 电 自回收能量 混合 动力 车辆 的能 耗 比插 电式 混 合 动力 车 辆低 , 节油 1 . 4 ; 且经 过 6月 、 7月两 个 月
车辆 在怠 速或 行驶 过程 中 由车身 面板振 动 引起 的室 内空 腔轰 鸣噪声 对乘 坐舒 适性 有很 大影 响 。通 过 发动 机 、 悬 架 等 与 车身 的关 键 接 附点 传 递 至 车身 的振 动是 引起 车身 面板 振动 的主要 原 因 。接 附点动
动 刚 度是 在 动 载荷 作 用下 抵 抗 变形 的能 力 , 动 刚度 不足 会对 整车 乘坐 舒适性 和车 身结 构件 的疲 劳
( 1 )在 发展 插 电式混合 动力 车 辆 时加 入 已较 成
熟 的 自回收能量装 置 , 增强 其节 油效果 。 ( 2 )在 设计 制 造 混 合 动 力 车 辆 时 , 加 强 对 动 力
的运行 磨合 后 , 非 插 电 自回收 能 量 混合 动力 车辆 表
现 出 良好 的节 油效 果 。相 比于传 统 的柴 油 车 辆 , 两 种 混合 动 力车 辆都 有 较 好 的节 油效 果 , 比传 统 车辆
摘要 :白车身关键接 附点 的局部动 刚度 对整 车 NVH[ N o i s e ( 噪 声) 、 Vi b r a t i o n ( 振动) 、 Ha r s h —
车身动力总成悬置安装点动刚度分析与优化

3,700
转速『 r.m- Ⅱ一
问题与发动机转速有关 ,与变速器档位无关 ,初步 怀疑 为发 动机 振 动直接 通 过悬 置系 统 、排气 系 统
图 1 地 板 振 动加 速 度 曲线
等传递至车身或与进气系统、排气系统 、车身系统
结构 频率 耦合 共振 产 生 ,对 以上系 统部 件进 行 整
车道路 测试 。 lz-s.‘lI 器曩
l i i
D 0 0
6 4 2 1 8 6 4
从源 、路径 、响应考虑查找 问题原因 ,分别在
发动机悬置支架、排气管吊挂支架 、及车身地板布
置三向加速度传感器 ,运用 LMS公司 Test.Lab测
试 软件 ,采 用 Signature Testing—Advanced测 试模
现 ,当发 动 机转 速达 到 3800 r/min时 ,车 内地 板存 在明显振动峰值(图 1),样车为直列 4缸 4冲程发 动机 ,发动机 2阶能量对地板振动贡献较大 ,频率 为 130Hz。从悬置支架的振动加速度与车内地板 振动数 据 中可 以看 出(图 2),发 动机前 悬置 被动侧 支架 振 动 与 地板 振 动 峰 值相 对 应 的频率 相 近 ,且 能量较大。车型开发前期 ,已对悬置支架模态进行
I 动力总成系统 l动力 蓥接盘
考 一
一 /
厂
仿真分析 ,频率在 500Hz以上 ,但悬置支架安装在 前副车架横梁上 ,对此安装位置 、结构进行实车分
l 车身局部 l
析 ,结构较弱 ,将前悬置支架与安装横梁断开后 ,
图 3 动 力总 成一悬 置 系统 一车 身模 型
主min以上前地板振动大受发动机悬 置支架 安装 点影响 ,动力总成振动主要从前悬置位置传递到 车 身 ,引起 车 内地板振 动 。
车体结构振动模态仿真与试验一致性分析

JOURNAL
大 连 交 通 大 学 学 报 OF DALIAN JIAOTONG UNIVERSITY
Vol. 32 No. 6 Dec. 2011
文章编号:1673 -9590 ( 2011 ) 06 -0026 -04
mm刚度系数钢结构状态弹性优化整备状态弹性优化54611889811205125338整备状态车体模态的对比分析图通过上述弹簧刚度系数的参数优化提高了车体在约束条件下得出的车体三阶模态与试验数据相关度当然这个约束条件与实际会有所差异其差异在于计算中的约束条件不仅包括线路试验中的约束刚度还包括车体的阻尼和质量分布不确定等因素在内
· ·
成的特点, 建模时需按偏安全原则, 尽可能细致离 因此车体 散车体. 由于模态分析时加载均被忽略, 各附加部件的质量和配重采用质量单元的方式进 质量较大的车下吊挂按实际位置相加. 为 行施加, 了更好地掌握车体的动态特性, 对车体钢结构及在 整备状态下的车体分别计算其固有频率及振型.
M x + Kx = 0
车体结构振动模态仿真与试验一致性分析
赵红伟, 田爱琴, 王万静, 丁叁叁
( 中国南车集团 青岛四方机车车辆股份有限公司 技术中心 过对比分析车体钢结构和整备两种车体状态中的仿真和试验数据 , 利用试验数据, 采用尺寸
调整弹性支撑刚度系数来修改车体的边界约束条件 , 使得仿真数据与试验数据达到很好的 优化的方式, 相关度, 为以后的车体模态计算分析提供强有力的支持 . 关键词:车体结构; 动态特性; 尺寸优化; 边界条件 文献标识码:A
27
2. 1
车体约束方式
车型
表2
分类 计算 1 中间车 计算 2 试验
车身连接点动刚度分析与NVH性能改进研究

车身连接点动刚度分析与NVH性能改进研究车身连接点动刚度分析与NVH性能改进研究汽车结构的主要部分是车身结构,而车身结构的动刚度是评估汽车NVH性能的重要指标之一。
车身连接点的动刚度对汽车的NVH性能有重要影响。
因此,本文将研究车身连接点动刚度分析与NVH性能改进。
1、车身连接点动刚度分析车身连接点动刚度是指在汽车行驶时,由于悬挂系统抵消车身上的不良振动所产生的剧烈影响。
此外,它还包括车体和底盘的构造和设计,以最大程度地减少噪声、振动和硬度的传递。
在设计车身连接点时,需要考虑到连接点的材料、形状、尺寸等。
合理的材料选择和结构设计能够有效地改善车身连接点的动刚度,从而降低噪声、震动和硬度的传递。
汽车的车身连接点主要包括悬挂连接点、发动机安装点、传动系连接点等。
对悬挂系统的连接点的动刚度进行分析和优化,能够有效降低路面颠簸所带来的体验。
对发动机安装点和传动系连接点的动刚度进行分析和优化,能够有效降低发动机运行时带来的振动和噪音。
2、NVH性能改进NVH性能与车身连接点的动刚度密切相关。
在降低车身连接点的动刚度的同时,可以进一步改善汽车的NVH性能。
要改进汽车的NVH性能,需要采取一系列措施。
首先,优化车身结构设计,包括悬挂系统、车架、车门等,在减少振动、噪音和硬度传递的同时,还需保持车身结构的强度和刚度。
其次,采用高性能的材料,如复合材料、高韧性钢材等,以提高车身结构的动刚度。
这可以显著减少车身振动和噪声,提高汽车的行驶舒适性和NVH性能。
最后,可以采用主动或被动隔音措施,如隔音材料和减震器等,来进一步改善汽车的NVH性能。
这些措施可以有效降低车内噪音和振动,提高乘坐舒适性。
总之,车身连接点动刚度分析与NVH性能改进是提高汽车运行安全性、舒适性、节能性和环保性的关键环节。
对车身连接点的动刚度进行合理的分析和优化,可以显著提高汽车的NVH性能,使其更加符合用户需求和市场需求。
3、车身连接点动刚度分析方法在车身连接点动刚度分析方面,可以采用有限元方法进行计算。
某轻客接附点局部动刚度分析(精)

IPI(源点导纳分析)是指在一定的频率范围内,通过在加载点施加单位力作为输入激励,同时将该点作为响应点,测得该点在该频率范围内的加速度作为输出响应,用于考察该点的局部动刚度。
源点加速度导纳公式为[2]:
- 1 -
2(1)其中:Ka=F/x为接附点动刚度;a =ωx为加速度;圆频率ω=2πf
假设通过IPI响应曲线如图1所示,计算得到该曲线所包围的面积,则有:
Abstract: To achieve the BIW IPI analysis and optimization of light bus, the CAE model of the BIW is operated by HyperWorks. By comparing the results of simulation and testing, the correctness of the model and the analytical method was verified.
应用求解器计算,计算结果通过HyperView读取,得到各接附点的动刚度响应曲线,与目标值对比后发现,只有前减震器安装点主方向的动刚度不满足目标值要求。利用HyperMesh软件对前减震器支架进行结构优化,增加支架处加强筋。如图5、6所示为优化前后的支架结构对比。
汽车减震器橡胶连接件静刚度有限元分析_胡振娴

收稿日期:2009-03-25 修回日期:2009-04-28第27卷 第6期计 算 机 仿 真2010年6月文章编号:1006-9348(2010)06-0309-05汽车减震器橡胶连接件静刚度有限元分析胡振娴,顾 亮(北京理工大学,北京100081)摘要:在汽车悬架设计中,汽车减震器与车体的连接多采用橡胶-钢零件作为弹性万向节,由于橡胶本身的超弹性以及零件模型的几何非线性,在较大变形的有限元计算中造成网格扭曲与畸形,为了改善车辆的乘适性,在动态冲击下达到减震降噪作用。
重新划分网格进行计算是解决问题的一种途径。
根据Abaqus 非线性有限元分析软件中的CAE 和Python 模块,给出了网格充分计算基本流程。
采用上述方法对汽车减震器的橡胶连接件的垂向和偏转静刚度进行了有限元计算,并与实验对比,有限元计算的误差不超过5%。
关键词:橡胶;减震器;有限元;网格划分中图分类号:TP391 文献标识码:BFEA Techni que on Static Stiffness for ShockerM ountHU Zhen-x ian ,GU L iang(B eiji ng Institute of T echno l ogy ,Be ijing 100081)AB STRACT :There are rubber-steel parts used asm ounts bet ween s hocke r and chassis .Because rubber i s hypere lastic and geo m e try of t he part i s non li near ,the e le m en ts are distorted when stra i ns become too l a rge in l oad i ng procedure ,itm akes the job aborted .R em eshi ng m akes t he job con tinued .In t h i s paper ,process o fR em es h i ng is prov i ded by us i ng CAE and P ython modu l es of A baqus .T he m et hod is used for si m ulati ng the stati c stiffness o f rubber m ount and comparing to the exper i m ent .FEA error i s not ex ceed 5%.K EY W ORDS :R ubbe r ;Sho cker ;FEA;M ap so l u tion1 引言在汽车悬架的设计中,为了改善车辆的乘适性,各部件之间的连接多采用橡胶连接。
车身薄壁梁结构刚度特性的仿真研究

车身薄壁梁结构刚度特性的仿真研究随着汽车行业的快速发展,车身结构设计成为自动化工程领域的热门话题之一。
车身结构对汽车的轻量化、环保、节能、安全等方面有着非常重要的作用。
其中,车身薄壁梁结构是目前较为流行的一种结构形式,经过多年的技术积累和工艺改进,其性能不断得到优化和提升。
车身薄壁梁结构的特点是通过大量的细长梁件将车身封闭起来,从而达到大幅度减少车身重量的效果。
然而,在降低车身重量的同时,车身的刚度也会相应地下降。
因此,对于这种车身结构,刚度特性的仿真研究显得尤为重要。
对于车身薄壁梁结构的刚度研究,可以采用有限元分析方法进行仿真计算。
通过数值模拟,可以对车身结构的刚度特性进行精确的分析和预测,从而实现结构的优化设计。
具体步骤如下:1. 建立分析模型首先,需要建立车身薄壁梁结构的有限元分析模型。
这个模型应该包含车身的全部细节,如车身框架、车身板材、梁件以及连接结构等。
然后,需要对模型进行网格划分,使得模型能够进行数值计算。
2. 确定边界条件为了计算车身的刚度特性,需要设定合适的约束和荷载条件。
常见的边界条件有固定支撑和滚动支撑。
而荷载条件则可以包括静载和动载,其中动载往往是更为复杂的情况。
3. 进行数值计算在确定边界条件以后,便可以进行数值计算了。
通过求解有限元方程组,可以得到车身在不同状态下的形变和应力分布。
这些分析结果能够反映车身结构的刚度特性,从而帮助设计师评估结构的性能。
4. 评估分析结果基于仿真分析结果,可以对车身结构进行刚度特性的评估。
评估结果可以用于指导设计师进行结构优化,包括模型的拓扑结构、材料选择和加强结构设计。
总之,车身薄壁梁结构的刚度特性对于汽车的轻量化和安全性有着非常重要的作用。
通过有限元分析方法进行仿真计算,能够精确地预测车身结构的刚度特性,为车身设计提供重要的指导。
因此,这种方法在汽车工程领域的应用前景非常广泛。
除了刚度特性,车身薄壁梁结构的设计还需要考虑其在碰撞等工况下的安全性能。
车载作用下公路桥梁耦合振动精细化建模及验证分析

车载作用下公路桥梁耦合振动精细化建模及验证分析作者:殷新锋晏万里任厚乾刘扬来源:《湖南大学学报·自然科学版》2021年第09期摘要:現有车-桥耦合振动分析中车辆模型不能精确考虑车辆动力特性和柔性轮胎对车桥耦合振动响应的影响.为了进一步研究充气轮胎胎压对车-桥耦合振动的影响,基于LS-DYNA 程序,采用线弹性橡胶材料模拟轮胎并定义轮胎内气压,结合常用重载三轴汽车的结构参数,运用弹簧阻尼单元及梁、壳单元模拟车辆悬架系统的动力特性,建立可分析车轮气压的三维车辆模型;并基于实桥试验结果及响应面法得到高精度有限元桥梁模型;通过显式求解程序LS-DYNA内置的接触算法,将车辆子系统和桥梁子系统联立耦合起来,形成显式的车-桥耦合振动分析模型.计算结果与实测结果对比分析验证了该方法的正确性,并分析了轮胎胎压对桥梁振动的影响.关键词:响应面法;有限元模型修正;连续刚构桥;LS-DYNA;动力响应中图分类号:U441.2 文献标志码:AFine Modeling of Coupled Vibration of Highway Bridge underVehicle Loading and Verification AnalysisYIN Xinfeng1,YAN Wanli1,REN Houqian1,LIU Yang1,2(1. College of Civil Engineering,Changsha University of Science & Technology,Changsha 410114,China;2. College of Civil Engineering,Hunan University of Technology,Zhuzhou 412007,China)Abstract:In the existing coupling vibration analysis of vehicle bridge,the influence of vehicle dynamic characteristics and flexible tire on the vehicle bridge coupling vibration response can not be accurately considered. In order to further study the influence of pneumatic tire pressure on vehicle bridge coupling vibration,the linear elastic rubber material is used to simulate the tire and define the air pressure in the tire based on LS-DYNA program. Combined with the structural parameters of the commonly used heavy-duty three-axle vehicle,the dynamic characteristics of the vehicle suspension system are simulated by using the spring damping element,beam and shell element,and a three-dimensional vehicle model is established. Based on the test results of the real bridge and the response surface method,a high-precision finite element bridge model is obtained. The vehicle subsystem and the bridge subsystem are coupled together to form the explicit vehicle bridge coupling vibration analysis model through the contact algorithm built in the explicit solution program LS-DYNA. The correctness of the method is verified by comparing the calculation results with the measured results,and the influence of tire pressure on bridge vibration is analyzed.Key words:response surface method;finite element model updating;continuous rigid-frame bridge;LS-DYNA;dynamic response车辆在桥梁上行驶时产生的激励导致车辆和桥梁产生相互振动,该振动称为车桥耦合振动[1]. 国内外学者对车桥耦合振动问题进行了大量研究,并取得非凡成果.夏禾[2]将车辆简化为悬挂振动模型,研究了车-桥-墩相互作用的动力响应. Cai等[3-4]采用两轴车辆模型,基于功率谱密度函数生成随机桥面不平整度,分析了车辆荷载作用下桥梁振动响应. Huang等[5]采用三轴车辆有限元模型研究了简支梁的车桥随机振动. 韩万水等[6]结合实测数据对桥梁模型进行修正以得到桥梁基准模型,并采用梁格法对车桥振动进行分析. 李奇等[7]考虑车体柔性的影响,分析了高速列车和简支梁桥相互作用的影响. 邓露等[8]运用动态称重技术(BWIM)实时监测车辆总重和轴重,进行中小型跨径混凝土梁桥的振动研究.赵越等[9]基于等参映射与改进折半法在传统车桥耦合分析的基础上进一步提升其分析精度及计算效率,从而进行公路车桥耦合分析.但关于充气轮胎胎压对车-桥耦合振动影响的研究较少.主要原因为现有车-桥耦合振动分析中车辆模型多为简化的质量-弹簧-阻尼多自由度振动模型[10-13],该模型常将车轮简化为点或者等效线面接触,故不能精确考虑车辆动力特性和柔性轮胎对车桥耦合振动响应的影响.因此,建立精确车辆模型和桥梁模型是至关重要的,这样才能提高数值模拟精度,为桥梁结构的健康运营提供有利建议.本文以一座连续刚构箱梁桥为工程背景.首先,基于LS-DYNA程序以车辆实际构造及动力特性为基准,建立车辆精细三维有限元模型;然后,结合响应面法并依据实桥试验结果对桥梁模型进行修正,以得高精度的桥梁有限元模型;最后,通过LS-DYNA程序将桥梁模型和车辆模型进行耦合,求解车桥的振动响应,并通过改变车轮气压,分析该参数对桥梁振动响应的影响.1 车辆模型的建立及校验1.1 车辆模型的建立在车桥耦合振动模型中,影响桥梁振动响应的主要因素为车辆模型的动力特性和荷载分布. 车辆模型需着重模拟悬架系统、车轮和轴重. 本文参照东风牌三轴载重自卸货车,建立车辆有限元模型,其相关参数如表1所示.前中轴距为3.5 m,中后轴距为1.4 m,后轮距为1.8 m. 基于CAD软件SolidWorks分别建立各部位的几何模型并进行网格划分,最后使用梁、壳、实体单元及离散单元等赋予不同部位网格不同的属性,从而构建车辆模型,如图1所示.车轮由轮胎、轮盘和轮毂组成.轮胎采用线弹性橡胶材料,轮盘和轮毂采用线弹性钢材材料,车轮模型中各部位连接均为刚性连接,边界为刚性固态约束,有限元模型如图2所示. 根据轮胎内实际气压,使用LS-DYNA程序关键字*AIRBAG_SIMPLE_AIRBAG_MODEL定义由轮胎、轮毂组成的封闭体内的气压,其气体压力值为0.6 MPa.由于车辆悬架系统结构复杂,本文采用壳单元、刚体、弹簧阻尼单元和多点约束来模拟悬架系统.前后悬架的弹簧和阻尼器的参数参考文献[14],前悬架的弹簧刚度取800 N/mm,阻尼系数取20 Ns/mm;后悬架的弹簧刚度取1 200 N/mm,阻尼系数取25 Ns/mm. 前后悬架实体构造及有限元模型如图3所示.为了使车轮正常转动,在轮盘与车轴之间设置旋转铰,再通过定义*INITIAL_VELOCTIY_GENERATION关键字设置车轮的转动和平动速度,实现车轮滚动向前的状态,如图4所示.1.2 车辆模型的校验在车辆模型的3个轴上选择6个节点,约束竖向位移. 然后对车辆施加重力荷载使车辆产生瞬时振动,再通过定义关键字*DAMPING_GLOBAL对车辆模型施加全局阻尼,使其快速达到稳定状态,计算出约束反力,并与实测车辆轴重进行比较,最终得到车辆模型的轴载曲线如图5所示.由表2知,车体总重偏差为0.87%,说明实测车辆轴重分布特性能体现于建立的车辆模型.通过对比车辆模型和实测车辆的自振频率,验证车辆模型动力特性的有效性. 如图6所示,该车实测自振频率为1.635 Hz,车辆有限元模型的自振频率为1.647 Hz,显然,两者基频相差很小.2 桥梁模型2.1 桥梁概况该桥主桥为三跨变截面预应力混凝土连续刚构结构,跨径布置为(65+120+65) m,其立面及断面示意图分别如图7和图8所示.2.2 实桥试验利用有限元软件ANSYS建立初始有限元模型如图9所示. 主梁和墩身都用实体单元模拟,墩底采用固结连接. 混凝土密度取为2 500 kg/m3,主梁和墩的混凝土弹性模量分别为34.5 GPa和32.5 GPa.现场对桥梁进行静力试验,测试中加载车辆总数为6辆,每辆总重为35 t,车辆前轴重7 t,中轴和后轴各重14 t,车辆照片如图10所示.在正式试验前先进行预加载,以消除非弹性变形,确保试验及设备处于良好工作状态. 正式试验中将加载车分3級加载,每一级加载持荷2 ~ 3 min,待实测应变及挠度数据稳定后进行数据的采集工作,再进行下一级的加载工作. 限于篇幅,仅就其中一个工况做详要概述. 为了使加载截面承受最大正弯矩,在中跨跨中截面中心加载,相应的荷载效率系数为0.967.挠度测点布置如图11所示.实桥试验的挠度采用水准仪进行测量,现场测试照片如图12所示.脉动试验采用多通道数据采集分析系统NI公司的PXI系统进行试验,采用8330B3型超低频加速度传感器进行数据采集,最低采样频率从0 Hz开始,采集主梁横向和竖向振动数据,再经信号分析得到全桥的各阶固有振动特性,现场采集照片如图13所示.2.3 基于响应面法的有限元模型更新基于响应面法的有限元模型修正是用响应面函数来模拟实际结构的响应函数,将试验设计与数理统计相结合,通过样本选取、方差分析参数选取、响应面的拟合及采用优化算法寻求响应面模型中的最优解来进行有限元模型修正.据文献[15-16]知,影响有限元模型与实测桥梁结构差别的主要因素为结构混凝土密度、主梁和墩混凝土弹性模量,因此取这三个因素作为变量. 为获得响应与所选定的三参数之间的联系,首先需要参数设计. 根据参数取值的变化规律,假设三参数的单位长度值为10%,则可得该三参数值的变化范围见表3.以桥梁模态和静力变形为目标来更新桥梁模型,选取桥梁结构的第一阶自振频率(R1)、测点5挠度值(R2)和测点6挠度值(R3)作为目标函数.这3个目标函数充分利用了现场的实桥试验条件,且包含了桥梁静、动力性能指标,可较为全面、准确地反映桥梁的力学性能.根据上述试验设计,应用回归分析技术对样本数据进行响应面拟合,并用R2准则和R2adj准则进行响应面拟合精度的检验,其表达式见方程(1)(2).式中:SST = SSE + SSR表示模型的总方差;dT表示模型的总自由度.如果R2和R2adj的值都接近1且两者差值很小,则表示响应面方程拟合得很好.本文以一座连续刚构箱梁桥为工程背景.首先,基于LS-DYNA程序以车辆实际构造及动力特性为基准,建立车辆精细三维有限元模型;然后,结合响应面法并依据实桥试验结果对桥梁模型进行修正,以得高精度的桥梁有限元模型;最后,通过LS-DYNA程序将桥梁模型和车辆模型进行耦合,求解车桥的振动响应,并通过改变车轮气压,分析该参数对桥梁振动响应的影响.1 车辆模型的建立及校验1.1 车辆模型的建立在车桥耦合振动模型中,影响桥梁振动响应的主要因素为车辆模型的动力特性和荷载分布. 车辆模型需着重模拟悬架系统、车轮和轴重. 本文参照东风牌三轴载重自卸货车,建立车辆有限元模型,其相关参数如表1所示.前中轴距为3.5 m,中后轴距为1.4 m,后轮距为1.8 m. 基于CAD软件SolidWorks分别建立各部位的几何模型并进行网格划分,最后使用梁、壳、实体单元及离散单元等赋予不同部位网格不同的属性,从而构建车辆模型,如图1所示.车轮由轮胎、轮盘和轮毂组成.轮胎采用线弹性橡胶材料,轮盘和轮毂采用线弹性钢材材料,车轮模型中各部位连接均为刚性连接,边界为刚性固态约束,有限元模型如图2所示. 根据轮胎内实际气压,使用LS-DYNA程序关键字*AIRBAG_SIMPLE_AIRBAG_MODEL定义由轮胎、轮毂组成的封闭体内的气压,其气体压力值为0.6 MPa.由于车辆悬架系统结构复杂,本文采用壳单元、刚体、弹簧阻尼单元和多点约束来模拟悬架系统.前后悬架的弹簧和阻尼器的参数参考文献[14],前悬架的弹簧刚度取800 N/mm,阻尼系数取20 Ns/mm;后悬架的弹簧刚度取1 200 N/mm,阻尼系数取25 Ns/mm. 前后悬架实体构造及有限元模型如图3所示.为了使车轮正常转动,在轮盘与车轴之间设置旋转铰,再通过定义*INITIAL_VELOCTIY_GENERATION关键字设置车轮的转动和平动速度,实现车轮滚动向前的状态,如图4所示.1.2 车辆模型的校验在车辆模型的3个轴上选择6个节点,约束竖向位移. 然后对车辆施加重力荷载使车辆产生瞬时振动,再通过定义关键字*DAMPING_GLOBAL对车辆模型施加全局阻尼,使其快速达到稳定状态,计算出约束反力,并与实测车辆轴重进行比较,最终得到车辆模型的轴载曲线如图5所示.由表2知,车体总重偏差为0.87%,说明实测车辆轴重分布特性能体现于建立的车辆模型.通过对比车辆模型和实测车辆的自振频率,验证车辆模型动力特性的有效性. 如图6所示,该车实测自振频率为1.635 Hz,车辆有限元模型的自振频率为1.647 Hz,显然,两者基频相差很小.2 桥梁模型2.1 橋梁概况该桥主桥为三跨变截面预应力混凝土连续刚构结构,跨径布置为(65+120+65) m,其立面及断面示意图分别如图7和图8所示.2.2 实桥试验利用有限元软件ANSYS建立初始有限元模型如图9所示. 主梁和墩身都用实体单元模拟,墩底采用固结连接. 混凝土密度取为2 500 kg/m3,主梁和墩的混凝土弹性模量分别为34.5 GPa和32.5 GPa.现场对桥梁进行静力试验,测试中加载车辆总数为6辆,每辆总重为35 t,车辆前轴重7 t,中轴和后轴各重14 t,车辆照片如图10所示.在正式试验前先进行预加载,以消除非弹性变形,确保试验及设备处于良好工作状态. 正式试验中将加载车分3级加载,每一级加载持荷2 ~ 3 min,待实测应变及挠度数据稳定后进行数据的采集工作,再进行下一级的加载工作. 限于篇幅,仅就其中一个工况做详要概述. 为了使加载截面承受最大正弯矩,在中跨跨中截面中心加载,相应的荷载效率系数为0.967.挠度测点布置如图11所示.实桥试验的挠度采用水准仪进行测量,现场测试照片如图12所示.脉动试验采用多通道数据采集分析系统NI公司的PXI系统进行试验,采用8330B3型超低频加速度传感器进行数据采集,最低采样频率从0 Hz开始,采集主梁横向和竖向振动数据,再经信号分析得到全桥的各阶固有振动特性,现场采集照片如图13所示.2.3 基于响应面法的有限元模型更新基于响应面法的有限元模型修正是用响应面函数来模拟实际结构的响应函数,将试验设计与数理统计相结合,通过样本选取、方差分析参数选取、响应面的拟合及采用优化算法寻求响应面模型中的最优解来进行有限元模型修正.据文献[15-16]知,影响有限元模型与实测桥梁结构差别的主要因素为结构混凝土密度、主梁和墩混凝土弹性模量,因此取这三个因素作为变量. 为获得响应与所选定的三参数之间的联系,首先需要参数设计. 根据参数取值的变化规律,假设三参数的单位长度值为10%,则可得该三参数值的变化范围见表3.以桥梁模态和静力变形为目标来更新桥梁模型,选取桥梁结构的第一阶自振频率(R1)、测点5挠度值(R2)和测点6挠度值(R3)作为目标函数.这3个目标函数充分利用了现场的实桥试验条件,且包含了桥梁静、动力性能指标,可较为全面、准确地反映桥梁的力学性能.根据上述试验设计,应用回归分析技术对样本数据进行响应面拟合,并用R2准则和R2adj准则进行响应面拟合精度的检验,其表达式见方程(1)(2).式中:SST = SSE + SSR表示模型的总方差;dT表示模型的总自由度.如果R2和R2adj的值都接近1且两者差值很小,则表示响应面方程拟合得很好.本文以一座连续刚构箱梁桥为工程背景.首先,基于LS-DYNA程序以車辆实际构造及动力特性为基准,建立车辆精细三维有限元模型;然后,结合响应面法并依据实桥试验结果对桥梁模型进行修正,以得高精度的桥梁有限元模型;最后,通过LS-DYNA程序将桥梁模型和车辆模型进行耦合,求解车桥的振动响应,并通过改变车轮气压,分析该参数对桥梁振动响应的影响.1 车辆模型的建立及校验1.1 车辆模型的建立在车桥耦合振动模型中,影响桥梁振动响应的主要因素为车辆模型的动力特性和荷载分布. 车辆模型需着重模拟悬架系统、车轮和轴重. 本文参照东风牌三轴载重自卸货车,建立车辆有限元模型,其相关参数如表1所示.前中轴距为3.5 m,中后轴距为1.4 m,后轮距为1.8 m.基于CAD软件SolidWorks分别建立各部位的几何模型并进行网格划分,最后使用梁、壳、实体单元及离散单元等赋予不同部位网格不同的属性,从而构建车辆模型,如图1所示.车轮由轮胎、轮盘和轮毂组成.轮胎采用线弹性橡胶材料,轮盘和轮毂采用线弹性钢材材料,车轮模型中各部位连接均为刚性连接,边界为刚性固态约束,有限元模型如图2所示. 根据轮胎内实际气压,使用LS-DYNA程序关键字*AIRBAG_SIMPLE_AIRBAG_MODEL定义由轮胎、轮毂组成的封闭体内的气压,其气体压力值为0.6 MPa.由于车辆悬架系统结构复杂,本文采用壳单元、刚体、弹簧阻尼单元和多点约束来模拟悬架系统.前后悬架的弹簧和阻尼器的参数参考文献[14],前悬架的弹簧刚度取800 N/mm,阻尼系数取20 Ns/mm;后悬架的弹簧刚度取1 200 N/mm,阻尼系数取25 Ns/mm. 前后悬架实体构造及有限元模型如图3所示.为了使车轮正常转动,在轮盘与车轴之间设置旋转铰,再通过定义*INITIAL_VELOCTIY_GENERATION关键字设置车轮的转动和平动速度,实现车轮滚动向前的状态,如图4所示.1.2 车辆模型的校验在车辆模型的3个轴上选择6个节点,约束竖向位移. 然后对车辆施加重力荷载使车辆产生瞬时振动,再通过定义关键字*DAMPING_GLOBAL对车辆模型施加全局阻尼,使其快速达到稳定状态,计算出约束反力,并与实测车辆轴重进行比较,最终得到车辆模型的轴载曲线如图5所示.由表2知,车体总重偏差为0.87%,说明实测车辆轴重分布特性能体现于建立的车辆模型.通过对比车辆模型和实测车辆的自振频率,验证车辆模型动力特性的有效性. 如图6所示,该车实测自振频率为1.635 Hz,车辆有限元模型的自振频率为1.647 Hz,显然,两者基频相差很小.2 桥梁模型2.1 桥梁概况该桥主桥为三跨变截面预应力混凝土连续刚构结构,跨径布置为(65+120+65) m,其立面及断面示意图分别如图7和图8所示.2.2 实桥试验利用有限元软件ANSYS建立初始有限元模型如图9所示. 主梁和墩身都用实体单元模拟,墩底采用固结连接. 混凝土密度取为2 500 kg/m3,主梁和墩的混凝土弹性模量分别为34.5 GPa和32.5 GPa.现场对桥梁进行静力试验,测试中加载车辆总数为6辆,每辆总重为35 t,车辆前轴重7 t,中轴和后轴各重14 t,车辆照片如图10所示.在正式试验前先进行预加载,以消除非弹性变形,确保试验及设备处于良好工作状态. 正式试验中将加载车分3级加载,每一级加载持荷2 ~ 3 min,待实测应变及挠度数据稳定后进行数据的采集工作,再进行下一级的加载工作. 限于篇幅,仅就其中一个工况做详要概述. 为了使加载截面承受最大正弯矩,在中跨跨中截面中心加载,相应的荷载效率系数为0.967.挠度测点布置如图11所示.实桥试验的挠度采用水准仪进行测量,现场测试照片如图12所示.脉动试验采用多通道数据采集分析系统NI公司的PXI系统进行试验,采用8330B3型超低频加速度传感器进行数据采集,最低采样频率从0 Hz开始,采集主梁横向和竖向振动数据,再经信号分析得到全桥的各阶固有振动特性,现场采集照片如图13所示.2.3 基于响应面法的有限元模型更新基于响应面法的有限元模型修正是用响应面函数来模拟实际结构的响应函数,将试验设计与数理统计相结合,通过样本选取、方差分析参数选取、响应面的拟合及采用优化算法寻求响应面模型中的最优解来进行有限元模型修正.据文献[15-16]知,影响有限元模型与实测桥梁结构差别的主要因素为结构混凝土密度、主梁和墩混凝土弹性模量,因此取这三个因素作为变量. 为获得响应与所选定的三参数之间的联系,首先需要参数设计. 根据参数取值的变化规律,假设三参数的单位长度值为10%,则可得该三参数值的变化范围见表3.以桥梁模态和静力变形为目标来更新桥梁模型,选取桥梁结构的第一阶自振频率(R1)、测点5挠度值(R2)和测点6挠度值(R3)作为目标函数.这3个目标函数充分利用了现场的实桥试验条件,且包含了桥梁静、动力性能指标,可较为全面、准确地反映桥梁的力学性能.根据上述试验设计,应用回归分析技术对样本数据进行响应面拟合,并用R2准则和R2adj准则进行响应面拟合精度的检验,其表达式见方程(1)(2).式中:SST = SSE + SSR表示模型的总方差;dT表示模型的总自由度.如果R2和R2adj的值都接近1且两者差值很小,则表示响应面方程拟合得很好.本文以一座连续刚构箱梁桥为工程背景.首先,基于LS-DYNA程序以车辆实际构造及动力特性为基准,建立车辆精细三维有限元模型;然后,结合响应面法并依据实桥试验结果对桥梁模型进行修正,以得高精度的桥梁有限元模型;最后,通过LS-DYNA程序将桥梁模型和车辆模型进行耦合,求解车桥的振动响应,并通过改变车轮气压,分析该参数对桥梁振动响应的影响.1 车辆模型的建立及校验1.1 车辆模型的建立在车桥耦合振动模型中,影响桥梁振动响应的主要因素为车辆模型的动力特性和荷载分布. 车辆模型需着重模拟悬架系统、车轮和轴重. 本文参照东风牌三轴载重自卸货车,建立车辆有限元模型,其相关参数如表1所示.前中轴距为3.5 m,中后轴距为1.4 m,后轮距为1.8 m. 基于CAD软件SolidWorks分别建立各部位的几何模型并进行网格划分,最后使用梁、壳、实体单元及离散单元等赋予不同部位网格不同的属性,从而构建车辆模型,如图1所示.车轮由轮胎、轮盘和轮毂组成.轮胎采用线弹性橡胶材料,轮盘和轮毂采用线弹性钢材材料,车轮模型中各部位连接均为刚性连接,边界为刚性固态约束,有限元模型如图2所示. 根据轮胎内实际气压,使用LS-DYNA程序关键字*AIRBAG_SIMPLE_AIRBAG_MODEL定义由轮胎、轮毂组成的封闭体内的气压,其气体压力值为0.6 MPa.由于车辆悬架系统结构复杂,本文采用壳单元、刚体、弹簧阻尼单元和多点约束来模拟悬架系统.前后悬架的弹簧和阻尼器的参数参考文献[14],前悬架的弹簧刚度取800 N/mm,阻尼系数取20 Ns/mm;后悬架的弹簧刚度取1 200 N/mm,阻尼系数取25 Ns/mm. 前后悬架实体构造及有限元模型如图3所示.为了使车轮正常转动,在轮盘与车轴之间设置旋转铰,再通过定义*INITIAL_VELOCTIY_GENERATION关键字设置车轮的转动和平动速度,实现车轮滚动向前的状态,如图4所示.1.2 车辆模型的校验在车辆模型的3个轴上选择6个节点,约束竖向位移. 然后对车辆施加重力荷载使车辆产生瞬时振动,再通过定义关键字*DAMPING_GLOBAL对车辆模型施加全局阻尼,使其快速达到稳定状态,计算出约束反力,并与实测车辆轴重进行比较,最终得到车辆模型的轴载曲线如图5所示.由表2知,车体总重偏差为0.87%,说明实测车辆轴重分布特性能体现于建立的车辆模型.通过对比车辆模型和实测车辆的自振频率,验证车辆模型动力特性的有效性. 如图6所示,该车实测自振频率为1.635 Hz,车辆有限元模型的自振频率为1.647 Hz,显然,两者基频相差很小.2 桥梁模型2.1 桥梁概况该桥主桥为三跨变截面预应力混凝土连续刚构结构,跨径布置为(65+120+65) m,其立面及断面示意图分别如图7和图8所示.2.2 实桥试验利用有限元软件ANSYS建立初始有限元模型如图9所示. 主梁和墩身都用实体单元模拟,墩底采用固结连接. 混凝土密度取为2 500 kg/m3,主梁和墩的混凝土弹性模量分别为34.5 GPa和32.5 GPa.现場对桥梁进行静力试验,测试中加载车辆总数为6辆,每辆总重为35 t,车辆前轴重7 t,中轴和后轴各重14 t,车辆照片如图10所示.在正式试验前先进行预加载,以消除非弹性变形,确保试验及设备处于良好工作状态. 正式试验中将加载车分3级加载,每一级加载持荷2 ~ 3 min,待实测应变及挠度数据稳定后进行数据的采集工作,再进行下一级的加载工作. 限于篇幅,仅就其中一个工况做详要概述. 为了使加载截面承受最大正弯矩,在中跨跨中截面中心加载,相应的荷载效率系数为0.967.挠度测点布置如图11所示.实桥试验的挠度采用水准仪进行测量,现场测试照片如图12所示.脉动试验采用多通道数据采集分析系统NI公司的PXI系统进行试验,采用8330B3型超低频加速度传感器进行数据采集,最低采样频率从0 Hz开始,采集主梁横向和竖向振动数据,再经信号分析得到全桥的各阶固有振动特性,现场采集照片如图13所示.2.3 基于响应面法的有限元模型更新基于响应面法的有限元模型修正是用响应面函数来模拟实际结构的响应函数,将试验设计与数理统计相结合,通过样本选取、方差分析参数选取、响应面的拟合及采用优化算法寻求响应面模型中的最优解来进行有限元模型修正.。
- 1、下载文档前请自行甄别文档内容的完整性,平台不提供额外的编辑、内容补充、找答案等附加服务。
- 2、"仅部分预览"的文档,不可在线预览部分如存在完整性等问题,可反馈申请退款(可完整预览的文档不适用该条件!)。
- 3、如文档侵犯您的权益,请联系客服反馈,我们会尽快为您处理(人工客服工作时间:9:00-18:30)。
关键词:动刚度 接附点 仿真 试验 HyperWorks Abstract: As the body's interface attachment points dynamic stiffness reflecting the transmit
level between the main excitations and internal response, optimizing the IPI(Input Points Inertance) of the attachment points could improve the vehicle's NVH performance significantly. In this paper, a sedan's IPI simulation, test and benchmark analysis of the left shock absorber MNT points in front suspension and the right spring MNT points in rear suspension were carried out by HyperWorks, and the accuracy and efficiency of the analysis were verified by the results. The application has validated the important guiding significance to the continuous optimization and improvement in engineering. Key words: Dynamic Stiffness, Interface Attachment Points, Simulation, Test, HyperWorks
5 参考文献
[1] 顾 宇 庆 , 李 俊 鹏 , 粱 新 华 等 . 轿 车 副 车 架 连 接 点 动 刚 度 试 验 分 析 [J]. 杌 械 研 究 与 应 用,2012,122(6):71-73. [2] 王 志 亮 , 刘 波 , 桑 建 兵 等 . 动 刚 度 分 析 在 汽 车 车 身 结 构 设 计 中 的 应 用 [J]. 机 械 设 计 与 制 造,2008,2:30-31. [3]张守元,张义民,戴云等.车身连接点动刚度分析与 NVH 性能改进研究[J].汽车技术,2010,10:26-29. [4] 朱 茂 桃 , 范 俊 , 何 志 刚 等 . 微 型 轿 车 白 车 身 模 态 试 验 与 分 析 [J]. 重 庆 交 通 大 学 学 报 ( 自 然 科 学 版),2010,29(4):659-662. [5]李建康,郑立辉,宋向荣.汽车发动机悬置系统动刚度模态分析[J].汽车工程,2009,31(5):457-461.
Altair 2013 技术大会论文集
车身接附点动刚度仿真及试验对标分析 Dynamic Stiffness Simulation and Benchmark Analysis for Body's Interface Attachment Points
聂祚兴 周建文 (中国汽车工程研究院股份有限公司,重庆,40039)
(1)
Ms
N
2
K jG X (s) F (s)
(2)
采用复模态分析法,即可得到结构的动刚度(位移阻抗):
H s ( )
r 1
1
T
K
r
2 M r jr K r
(3)
其中, 为结构阻尼系数, g / k 。 加速度导纳是指单位激振力所产生的加速度响应,它与动刚度存在倒数的关系,加速度响应越 大,表明结构的动刚度越小。工程中,一般都是通过频率响应分析,得到原点的加速度响应,然后 经过积分、倒数等运算得到结构的动刚度特性[2]。由式(3),可得到加速度频响函数(加速度导纳函数) 为:
3.4 车身接附点动刚度对标分析
将前悬架左侧减震器 MNT 点所采用的夹具有限元离散化之后导入仿真模型中; 修改仿真分析中 后悬架右侧弹簧 MNT 点的加速度拾取位置,使其与动刚度试验保持一致[5]。其中,后悬架右侧弹簧 对标模型如下图 11 所示。
图 11 后悬架右侧弹簧对标模型 将对标分析的仿真模型再次进行模态频率响应求解,并将其结果与试验曲线对比,结果如下图 12-17 所示。
-2-
Altair 2013 技术大会论文集
3.2 车身接附点动刚度试验
测试车身结构的固有振动特性时,要求车身结构在支撑件上的固有频率与车身结构所关注的固 有频率之比小于 1/3。为满足上述要求,采用橡皮绳将车身水平悬挂于桁架上,悬吊频率为 1Hz,远 小于车身的一阶固有频率的 1/3。
图 2 接附点动刚度试验悬挂方式 为了使车身接附点本身能够作为一个整体来考虑其刚度大小,保证试验与实车使用状态尽可能 一致, 同时兼顾到可行性, 需要采用特定的夹具或在试验过程中选取易操作的拾取点。 本次试验中, 前悬架减震器 MNT 点所采用的辅助夹具如下图 3 所示,后悬架右侧弹簧 MNT 点的加速度响应拾取 位置如下图 4 所示[3]。
图 16 后悬架右侧弹簧 MNT 点 Y 向动刚度对标分析曲线 图 17 后悬架右侧弹簧 MNT 点 Z 向动刚度对标分析曲线
从图 12-17 的对比可以看出:对标曲线和试验曲线在 20-500Hz 频率区间内具有较为一致的趋 势,而且幅值也基本相当。对比结果表明,以某型轿车为例的车身接附点动刚度试验方法合适,仿 真模型准确,两者具有较好和一致性和精确度,所建立有限元模型可以运用到后续的仿真及优化分 析中。
图 12 前悬架左侧减震器 MNT 点 X 向动刚度对标分 析曲线
图 13 前悬架左侧减震器 MNT 点 Y 向动刚度对 标分析曲线
图 14 前悬架左侧减震器 MNT 点 Z 向动刚度对标分 析曲线 -5-
图 15 后悬架右侧弹簧 MNT 点 X 向动刚度对标分析 曲线
Altair 2013 技术大会论文集
图 3 前悬架左侧减震器 MNT 点
图 4 后悬架右侧弹簧 MNT 点
-3-
Altair 2013 技术大会论文集
采用声振测试分析系统进行接附点动刚度测试,采样频率 1024Hz,力锤激励信号施加力窗函 数,响应信号施加指数窗函数,以减少泄漏误差。比较同一工况下的 3 组数据,每两组之间加速度 有效值的差别不能过大,相干系数应达到 90%,否则数据无效,需要重新测量,直到 3 组数据之间 每两组数据之间加速度有效值之间非常接近,从而得到各接附点的动刚度曲线[4]。
-1-
Altair 2013 技术大会论文集
2 动刚度分析基本理论
动刚度是指引起单位位移量所需要的动态力,反应的是结构抵抗预定动态激扰能力的能力。结 构的振动微分方程[1]可以表达为:
mx k x j g x f (t )
其中, g 为结构损耗因子。 对等式两边进行拉普拉斯变换,有:
摘 要:车身接附点动刚度反映汽车主要激励与车身间的传递特性,对接附点动刚度的分析及优化
能够显著提高整车的 NVH 性能。以某型轿车为例,采用有限元分析软件 Altair HyperWorks 对其前 悬架左侧减震器 MNT 点、后悬架右侧弹簧 MNT 点动刚度进行了仿真、试验及对标分析,结果表明 所采用仿真及试验方法准确可靠,对后续优化和改进具有重要工程指导意义。
-6-
( j )2 T H a ( ) 2 r 1 K r M r jr K r
N
(4)
3 应用实例
3.1 车身接附点动刚度有限元分析
本文以某型轿车为例进行车身接附点动刚度有限元分析。采用有限元软件 网格单元主要以四边形壳单元为主,单元总数约 64.5 万,节点总数约 66.9 万。
3.3 车身接附点动刚度结果对比
将试验所得到的动刚度曲线与仿真结果相对比,如下图所示 5-10 所示:
图 5 前悬架左侧减震器 MNT 点 X 向动刚度对比曲线
图 6 前悬架左侧减震器 MNT 点 Y 向动刚度对比曲线
图 7 前悬架左侧减震器 MNT 点 Z 向动刚度对比曲线
图 8 后悬架右侧弹簧 MNT 点 X 向动刚度对比曲线
图 9 后悬架右侧弹簧 MNT 点 Y 向动刚度对比曲线
图 10 后悬架右侧弹簧 MNT 点 Z 向动刚度对比曲线
-4-
Altair 2013 技术大会论文集
从图 5-10 的结果对比中可以看出,前悬架左侧减震器 MNT 点、后悬架右侧弹簧 MNT 点的试验和 仿真动刚度曲线在幅值与峰值频率上都存在较大差别。 考虑到仿真分析工况在试验中的不可实现性, 两者边界条件和拾取位置的不一致可能是造成差别的主要原因。
1 引言
随着人们对驾驶及乘坐舒适性要求的不断提高,汽车 NVH 性能也逐渐成为消费者考虑的主要 因素之一。 车身接附点动刚度反映了汽车主要激励与车身间的传递特性,对驾驶室振动和噪声控制有着重 要影响。车身接附点动刚度能够在车身设计阶段通过频率响应分析准确预估,从而尽早发现和修正 潜在的设计问题,提高产品的性能及设计周期。这一指标也越来越受到汽车设计工程师的重视。 为了使车身接附点能够作为一个整体反应其动态性能,同时兼顾到可行和易操作性,需要在接 附点安装特定的夹具。仿真分析与试验间存在相互检验、互相验证的作用,考虑到标准动刚度分析 工况在试验时的不可实现和差异性,试验与仿真的对标分析就具有重要的意义。 轿车车身接附点主要包括发动机悬置安装点、 减震器安装点、 拖曳臂安装点, 副车架安装点等, 这些安装点反应了汽车车身所承受的最主要的激励位置。本文以某型轿车为例,对车身前悬架左侧 减震器 MNT 点、后悬架右侧弹簧 MNT 点进行了动刚度的仿真、试验及对标分析,结果表明所采用 仿真及试验方法准确可靠,对提高整车 NVH 性能具有重要工程指导意义。