气分装置
气分装置操作规程

10×104气体分馏装置1.5×104MTBE装置操作规程二00七年七月二十二日山东万通石油化工集团有限公司10×104气体分馏装置1.5×104MTBE装置操作规程编写:赵建桥边树源审定:王建锋陈大章二00七年七月二十二日山东万通石油化工集团有限公司1 装置简介 (3)1.1 装置概述 (3)1.2 工艺原理 (3)1.3 工艺流程说明 (4)1.4 主要操作参数控制指标 (5)1.5 原料及产品性质(设计数据) (6)1.6 物料平衡(设计数据) (9)1.7 消耗指标及能耗 (9)2 装置开工规程 (12)2.1 装置开工必备条件 (12)2.2 开工前的准备工作 (12)2.3 设备吹扫和试压 (13)2.4 置换空气 (18)2.5 引瓦斯置换 (18)2.6 拆加盲板 (20)2.7 装置开工 (20)3 岗位操作法 (23)3.1 工作范围 (23)3.2 岗位职责 (23)3.3 操作员须知 (24)3.4 正常操作法 (24)3.5 非正常操作法 (28)4 装置停工规程 (32)4.1 停工前的准备工作 (32)4.2 正常停工步骤 (33)4.3 装置的紧急停工 (34)5 专用设备操作法 (35)5.1 司泵岗位指责及操作法 (35)5.2 屏蔽电泵的操作 (40)6 安全生产规定 (41)6.1 安全生长要点 (41)6.2 装置开、停工安全规定 (41)6.3 装置检修安全规定 (43)6.4 防毒 (44)6.5 防火防爆安全规定 (47)6.6 防冻防凝安全规定 (50)7 事故预案 (51)7.1 停水、电、汽、风事故预案 (51)7.2 分馏事故预想方案 (52)8 环境保护和职业安全卫生 (53)8.1 环境保护 (53)8.2 火灾、爆炸危险 (53)9 附录 (55)附录一:扫线流程 (55)附录二:塔器一览表 (57)附录三:容器一览表 (58)附录四:机泵一览表 (59)附录五:冷换设备一览表 (60)附录六:安全阀 (61)1 装置简介1.1 装置概述本装置为新建项目,设计规模为年加工原料液化汽10万吨配套1.5万吨MTBE联合装置,年开工8000小时。
气体分馏装置的能耗分析与节能措施研讨
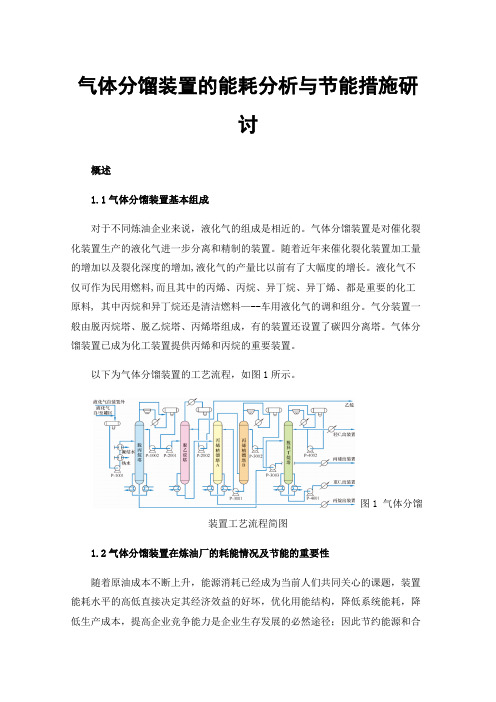
气体分馏装置的能耗分析与节能措施研讨概述1.1气体分馏装置基本组成对于不同炼油企业来说,液化气的组成是相近的。
气体分馏装置是对催化裂化装置生产的液化气进一步分离和精制的装置。
随着近年来催化裂化装置加工量的增加以及裂化深度的增加,液化气的产量比以前有了大幅度的增长。
液化气不仅可作为民用燃料,而且其中的丙烯、丙烷、异丁烷、异丁烯、都是重要的化工原料, 其中丙烷和异丁烷还是清洁燃料—--车用液化气的调和组分。
气分装置一般由脱丙烷塔、脱乙烷塔、丙烯塔组成,有的装置还设置了碳四分离塔。
气体分馏装置已成为化工装置提供丙烯和丙烷的重要装置。
以下为气体分馏装置的工艺流程,如图1所示。
图1 气体分馏装置工艺流程简图1.2气体分馏装置在炼油厂的耗能情况及节能的重要性随着原油成本不断上升,能源消耗已经成为当前人们共同关心的课题,装置能耗水平的高低直接决定其经济效益的好坏,优化用能结构,降低系统能耗,降低生产成本,提高企业竞争能力是企业生存发展的必然途径;因此节约能源和合理利用能源为大势所趋,势在必行。
气分装置总能耗一般占全厂总能耗的15-17%,其用能水平直接关系到整个炼厂的经济效益,因此气分装置的节能降耗工作意义重大。
1.3气体分馏装置的能耗组成及用能分析1.3.1气体分馏装置的用能形式;目前国内气体分馏装置用能有4种形式,分别为;1)采用蒸汽作为气分再沸器热源气体分馏塔塔底再沸器多用0.45 MPa蒸汽作热源。
该形式流程简单,但能耗高,适宜小型装置或复杂系数较低的炼厂。
2)采用其它装置工艺物流的低温余热催化裂化装置与气体分馏装置就近联合布置,同步开停工,实现装置间的热联合是节能降耗的有效途径。
催化裂化分馏塔顶循环回流的低温热足以作为气体分馏装置的低温热源。
其利用方式有2种。
①直接采用顶循油气作为气体分馏塔热源;②利用软化水与顶循换热,热水作为气体分馏塔热源,可大大减少蒸汽的消耗。
后者相比操作可靠,安全性好;直接换热可减少换热器投资,但对设备的性能要求较高,存在一定的运行风险。
气分装置简介

气分装置概况
二、气分装置工艺流程简介
1、装置简介: 中石油哈石化第一套气体分馏装置于1999年9月10日建成投产,南临 油品在线调和区域,北临一套催化装置,东临聚丙烯装置,西临油品罐 区。装置原设计处理量为15万吨/年,生产纯度为99.40%(V)丙烯,纯度 99%的丙烷及MTBE装置原料(混和碳四)三种产品。2004年9月气分装置 进行改造,改造后处理能力为30万吨/年,2010年4月气分装置又进行了 处理能力35×104T/a扩容改造 。装置由脱丙烷塔、脱乙烷塔、丙烯塔三
2014-5-17
5
气分装置概况
二、气分装置工艺流程简介
2、装置变动、改造情况: 公司节能技改:气分脱乙烷塔、丙烯塔与三催低温位热联合(更换 E-404)。 车间小型技改:E-408/2碳四出口加温控:泵房扫线蒸汽与消防蒸汽 加跨线;E-411/1、2与E-405/1、2加泄压线;装置框架-1、装置框架-2加 氮气及低压管线,二层、三层加放空阀;凝结水系统流程完善。 T-502/B由装丙烯脱水剂改造为下段装丙烯COS水解剂,上层装ZnO 脱硫剂;利用脱乙烷塔低温位热源与丙烯精制汽提塔热联合。
2014-5-17
6
气分装置概况
二、气分装置工艺流程简介
• 2、装置变动、改造情况:
•
2007年6月气分为确保大处理量下丙烯塔的冷却负荷,对丙烯塔空冷能力进行增 容,新增加两组空冷器四台风机EC-402/16~19。 • 2010年4月气分装置又进行了扩能改造,装置处理能力由30万吨/年增加到35万 吨/年,主要改造情况如下: • 冷却器部分:脱丙烷塔后冷器E-412更换高效芯子; • 脱乙烷塔后冷器E-405/1、2并联改串联后与新增E-405/3并联。 • 空冷器部分:拆除2007年增加的两组空冷器四台风机EC-402/16~19,新增加三 组空冷器九台风机EC-402/16~24; • 重沸器部分:脱丙烷塔底重沸器E-402扩容; • 丙烯塔新增重沸器E-413。 • 车间小型技改:消除热联合注汽系统 • E-410加出入口跨线
气分装置节能降耗优化措施

气分装置节能降耗优化措施在全球经济一体化和世界经济的迅速发展的背景下,节约能源,降本增效,是一项长期而紧迫的战略任务,也是未来可持续发展的必然选择。
气体分馏装置的主要作用是将催化裂化装置来的液化烃分离出丙烯、丙烷及混合碳四作为聚丙烯与MTBE装置的原料。
分离过程采用精馏方式,能量使用密集,降低装置能耗。
分析气体分馏装置单位能耗偏高的原因,找出不合理因素,采用优化操作参数、方案及换热流程优化等措施,在保证产品质量与生产效率的同时,降低能耗。
因此,几个重要操作参数进行调整,优化工艺条件,有效提高了丙烯产品的收率和纯度,提升了装置运行平稳率,降低了成本和能耗,增加了经济效益。
标签:气分装置;节能降耗;优化措施气分装置虽然具有以下优势:工艺流程简单,生产运行易于控制,但是,降低气分装置能耗,已成为目前国内同类装置面临的一个共同课题。
能源作为人类社会生存和社会经济发展的重要物质基础,随着全球经济一体化和世界经济的迅速发展,资源已是全人类共同关心的重要问题和面临的严峻挑战。
节约能源,降本增效,是一项长期而紧迫的战略任务,也是未来可持续发展的必然选择。
1 装置简介我们中海油东方石化有限责任公司,气体分馏装置设计加工量60万t/年,采用常规三塔流程,原料液态烃来自上游催化装置,由脱丙烷塔分离成碳二、碳三和碳四馏分。
碳二、碳三馏分经脱乙烷塔脱除碳二后,进入丙烯精馏塔分离出丙烯和丙烷馏分。
丙烷馏分外销,碳四馏分和丙烯作为聚丙烯和MTBE装置原料。
主要能源消耗是塔底热源(蒸汽、低温热)和机泵耗能。
开工投产以来,装置运行平稳,丙烯纯度≥99.6%,主要技术经济指标达到设计要求,装置已通过采用高效浮阀塔盘、应用屏蔽泵、干气密封泵、表面蒸发式空冷等新技术新设备,充分利用装置内部热源给原料液态烃换热、与催化装置进行热联合等措施,有效降低装置能耗。
但受上游装置生产方案及市场影响,投产后相当长时间液态烃加工量仅为设计能力的68%左右,投产当年加工量更仅有设计能力的62%,处于装置加工弹性范围60%~110%的下限。
气分MTBE及品精制装置基本原理概述

产品精制、气体分馆及MTBE装置基本原理概述2010年4月30日第一章第二章第三章第四章第五章总述干气、液化气脱硫轻油、液化气脱硫醇气体分MTBE合成第一章总述1・1双脱装置作用:1)处理来自催化装置的干气,脱除其中的硫化氢,脱硫后的气体去燃料气管网和制氢装置;2)处理来自催化装置的液化气,脱除其中的硫化氢和硫醇,为下游气体分憎装置提供原料;3)处理来自催化装置的汽油,脱除汽油中的硫醇硫,满足汽油质量对硫醇硫的要求。
1.2气分装置作用:来自催化装置并经过脱硫、脱硫醇装置精制后的液化气经过气体分憎装置精憎后,生产丙烯和丙烷产品。
混合碳四作为下游MTBE装置的原料。
1.3MTBE装置作用:来自气分装置的混合碳四与外购甲醇经过MTBE装置处理后主要产品为MTBE产品,MTBE纯度>98% (重)(含C5),该产品辛烷值高,且调合性能优良,可用作高辛烷值无铅车用汽油的添加组分,乂是汽油中所需氧含量的最重要来源。
装置的副产品为未反应C4憎分,用作民用液化气燃料。
第二章干气、液化气脱硫2.1基本原理:吸收与解吸炼油生产过程产生的炼厂气是多种组分的混合物,并可能含有杂质。
只有将它们分离、提纯、精制,才能进人下一道炼制工序或作为化工原料和其他用途。
为实现分离过程,炼油厂广泛采用吸收和解吸的方法。
2.1.1基本概念(1)物系的相在物质体系中,具有相同物理和化学性质的均匀部分,称为相。
其分散度达到分子大小的数量级。
相与相之间有明确的分界面。
如装在压力容器内的液化石油气,上部的气体称为气相,下部的液体称为液相。
由浮在水面上的冰块及水、蒸汽所组成的物系,冰块称为固相,水称为液相,上部蒸汽则称为气相。
这三者虽具有相同的化学性质,但物理性质却不一样,因此是三个相。
由油和水组成的物系,如果分了层,上面油的部分称为油相,下面水的部分称为水相。
虽然都是液体,但属于不同的相。
乂如两种或两种以上的物质组成的溶液,因其任何部分都是均匀的,所以整个溶液就是一个相。
气体分馏装置的基本原理及工艺流程

气体分馏装置的基本原理及工艺流程作者:董兴鑫来源:《中国科技博览》2014年第11期一气体分馏的重要性炼厂气是石油化工过程中,特别是破坏加工过程中产生的各种气体的总称。
包括热裂化气、催化裂化气、催化裂解气、重整气、加氢裂化气等,炼厂气的产率一般占所加工原油的5~10%。
这些气体的组成较为复杂,主要有C1~C4的烷烃和烯烃,其中有少量的二烯烃和C5以上重组分,此外还有少量的非烃类气体,如:CO、H2、CO2、H2S和有机硫(RSH、COS)等。
炼厂气过去大多是用作工业和民用燃料,少部分加工成为高辛烷值汽油和航空汽油的组成,随着石油化学工业的发展,炼厂气已成为宝贵的化工原料。
炼厂气作为化工原料,必须进行分离,分离的方法很多,就其本质来说可以分为两类,一类是物理分离法,即利用烃类的物理性质的差别进行分离。
如:利用烃类的饱和蒸汽压、沸点不同而进行气体分离过程,有些合成过程对气体纯度要求较高时,则需要高效率的气体分离,如吸附、超精馏、抽提精馏、共沸蒸馏等;另一类方法是化学方法,既利用化学反应的方法将它们分离,如化学吸附和分子筛分离。
目前,我国绝大多数炼油厂采用气体分离装置对炼厂气进行分离,以制取丙烷、丁烷、异丁烷,可以说是以炼油厂气为原料的石油化工生产的重要装置。
一、气体分馏的基本原理炼厂液化气中的主要成分是C3、C4的烷烃和烯烃,即丙烷、丙烯、丁烷、丁烯等,这些烃的沸点很低,如丙烷的沸点是—42.07℃,丁烷为—0.5℃,异丁烯为—6.9℃,在常温常压下均为气体,但在一定的压力下(2.0MPa以上)可呈液态。
由于它们的沸点不同,可利用精馏的力法将其进行分离”所以气体分馏是在几个精馏塔中进行的。
由于各个气体烃之间的沸点差别很小,如丙烯的沸点为—47.7℃.比丙烷低4.6℃,所以要将它们单独分出,就必须采用塔板数很多(一般几十、甚至上百)、分馏精确度较高的精馏塔。
二、气体分馏的工艺流程气体分馏装置中的精馏塔一般为三个或四个,少数为五个,实际中可根据生产需要确定精馏塔的个数。
ASPEN_培训教材10-ASPEN_气分

h
气分装置流程模拟计算
一、工艺流程简述
气分装置是炼油厂后续加工加工装置之一。
它的主要作用是把炼厂深加工装置出来的液化气组份,通过常精馏的方法的分离出丙烷、碳四,高纯度的丙烯。
气分装置一般由三个塔系组成,第一个脱除液化气中比碳四重的组份,叫脱丙烷塔,第二个脱除液化气中比碳二轻的组份,叫脱乙烷塔,第三个塔顶出高纯度的丙烯产品,塔底得到碳三液化气,叫丙烯精馏塔,该塔塔板数较多一般分为两个塔,有的气分装置还有碳四分离塔。
气分装置其工流流程如图5-1所示,所涉及主要模块有进料泵(P101),脱丙烷塔(T101)、脱乙烷塔进料泵(P102),脱乙烷塔(T102)、丙烯精馏塔(T103AB)。
h
h
图5-1 气分装置模拟计算流程图
A1液化气进料;1B碳四出料;2T轻组份排放;3T丙烯产品;3B碳三液化气
h
h
二、需要输入的主要参数
1、装置进料数据
2、单元操作参数
3、设计规定
三、软件版本
采用ASPEN PLUS 软件12.1版本,文件名QF24.APW。
欢迎您的下载,资料仅供参考!
h。
气分MTBE装置技术讲座ppt课件

*
五、装置工艺原则流程图
C2.C3 C2 C=3 C2C3C4C5 C3 C4C5 CO3
*
四、气体分馏装置的基本原理
板以下为提馏段,塔内进行精馏过程。原料进入进料板,其汽、液相在进料板的温度、压力下分别与塔内的汽、液相混合后,汽相上升到精馏段,液相下流到提馏段。通过塔板的精馏 作用,沿塔高向上,轻组分浓度递增,温度递减;沿塔高向下,重组分浓度递增,温度递增。塔顶馏出物经塔顶冷凝冷却器冷凝冷却,一部分抽出作为塔顶产品,一部分送回塔顶作塔顶回流。塔底由重沸器提供热量,将塔底物加热,使塔底物中所含部分轻组分蒸发,作为塔内蒸汽。塔底(或重沸器)液相抽出一部分送回塔内,一部分作为产品。
*
2、能量平衡
名 称
单耗 /吨原料
设 计
1996年 (标定)
2000年 (标定)
循环水
t/t
61.19
94.00
108.04
电
Kw.h(度)/t
11.84
9.15
5.276
1.0Mpa蒸汽
t/t
0.23
0.90
0.905
110℃热水
t/t
12.58
凝结水
t/t
*
四、装置的工艺原则流程图
2、产品分离部分采取先共沸蒸馏,分离出MTBE产品,然后用无离子水为萃取剂,萃取脱除C4中的MeOH,这种产品分离流程,可避免因水洗脱除MeOH,再蒸馏分离的C4和MeOH而引起的MTBE产品的部分损失和含水MTBE产品的干燥问题。
*
五、装置工艺原则流程图
2.4
2.4
T201顶回流温度℃
41.8
32
- 1、下载文档前请自行甄别文档内容的完整性,平台不提供额外的编辑、内容补充、找答案等附加服务。
- 2、"仅部分预览"的文档,不可在线预览部分如存在完整性等问题,可反馈申请退款(可完整预览的文档不适用该条件!)。
- 3、如文档侵犯您的权益,请联系客服反馈,我们会尽快为您处理(人工客服工作时间:9:00-18:30)。
气分装置
该装置主要生产纯度较高的丙烯、丙烷、异丁烯馏分和丁烯-2及碳-五等产品。
产品用途:生产的精丙烯作聚丙烯原料,异丁烯用作低分子聚异丁烯原料或烷基化的原料。
丁烯-2馏份作顺酐原料外,其余部分留下自用。
碳-五作车用汽油的调和组份。
丙烷馏份做丙烷脱沥青的溶剂外,其余作民用燃料。
本装置的生产原理是利用物理分离的原理对液态烃中各组份在同一压力下具有不同的挥发度而加以分离,生产较高纯度的丙烯、丙烷、异丁烯、丁烯-2、碳-五产品。
因为装置未设冷冻系统、故蒸馏在较高的压力和温度下进行操作。
流程采用先脱碳三、然后分离碳四、最后脱除碳五。
碳三馏份先脱乙烷、然后进行丙烷、丙烯分离。
但装置设计了液态烃碱洗精制及分馏两个部份。
分馏共六具分馏塔。
工艺流程说明:
原料液态烃经气体精制装置脱硫后送入本装置。
进入本装置的液态烃静静态混合器(M-1)与来自循环碱泵(P-9、P-10/1)或液态烃沉降罐(V-1)底部的碱液混合后进入V-1进行沉降分离,然后再经静态混合器(M-2)与来自循环碱泵(P-10/2、P-10/1)或液态烃沉降罐(V-2)底部的碱液混合后进入V-2进行沉降分离。
V-1、V-2沉降分离后的碱液循环使用到碱液浓度降低到--定程度后,压入废碱罐(D-9002/3)或排入全厂含硫污水管网统--处理,液态烃则由脱丙烷塔进料泵(P-1/1、2)送至进料换热器(E-1/1)与脱丙烷油换热,然后再经进料预热器(E-1/2)用热水加热后进入T-1第24层塔盘。
脱丙烷塔顶混合碳三组分经脱丙烷塔塔顶冷凝器(E-2/1、2)冷凝后进入脱丙烷塔回流罐(V-4),然后--部分经脱丙烷塔回流泵(P-2/1、2)送回T-1顶作回流,--部分经脱乙烷塔进料泵(P-3/1、2)加压经脱乙烷塔进料预热器(E-10)加热后进入脱乙烷塔T-4第28层塔盘。
脱丙烷塔塔底碳四、碳五馏份经E-1/1与T-1进料液态烃换热后进入碳四塔(T-2),脱丙烷塔塔底重沸器(E-3)用蒸汽供热。
碳四塔进料位置--般在第54层塔盘,塔顶异丁烯馏份经塔顶冷凝器(E-4/1、2)冷凝后进入碳四塔回流罐(V-5),然后经碳四塔回流泵(P-4/1、2)部分送入T-2顶作回流,部分经异丁烯冷却器(E-6)冷却后作为产品送出装置,塔底丁烯-2及碳五馏分自压进入碳五塔(T-3)第18层塔盘。
碳四塔塔底重沸器(E-5/1、2)用热水或蒸汽供热。
丁烯-2及碳五进入碳五塔(T-3)后,塔顶丁烯-2组分经碳五塔冷凝器(E-7)冷凝后进入碳五塔回流罐(V-6),然后经碳五塔回流泵(P-5/1、2)部分送入T-3顶作回流,部分经丁烯-2冷却器(E-9)冷却后作为产品送出装置,塔底碳五馏分靠自压或P-14/1、2加压后进入碳五冷却器(E-13)冷却后送出装置。
碳五塔塔底重沸器(E-8)用蒸汽供热。
进入T-3的混合碳三、碳二组分,经分离后塔顶气体经脱乙烷塔冷凝器(E-11)冷凝后进入脱乙烷塔回流罐(V-7),罐顶不凝气返回第三套催化裂化装置或排入管网,冷凝液经脱乙烷塔回流泵(P-6/1、2)送回T-4顶作回流,塔底丙烷、丙烯混合物自压进入丙烯塔-1(T-5)第62层塔盘。
脱乙烷塔塔底重沸器(E-12)用热水或蒸汽供热。
丙烯塔由丙烯塔-1(T-5)与丙烯塔-2(T-6)组成,丙烯由T-6顶经丙烯塔冷凝器(E-15/1-4、E-4/3)冷凝后进入丙烯塔回流罐(V-8),然后经丙烯塔回流泵(P-8/1、2)部分送入T-6顶作回流,部分经丙烯冷却器(E-16)冷却后作为产品送出装置,丙烷由T-5底靠自压经丙烷冷却器(E-17)冷却后作为产品送出装置。
T-6底釜液由丙烯塔-2釜液泵(P-7/1、2)送至T-5顶部。
丙烯塔重沸器(E-14/1、2)用热水或蒸汽作为热源。
主要工艺条件:。