精轧机组设备及功能
热轧带钢精轧机组主要辅助设备

首钢技师学院
热轧带钢精轧机组主要辅助设备
1、飞剪
功能:将进入精轧机的带坯的低温和形状不良的头尾端剪切掉,防止
穿带过程中卡钢和低温头尾在轧辊表面产生辊印。 类型:转鼓式飞剪和曲柄式飞剪两类。
飞剪
转鼓式飞剪
曲柄式飞剪
首钢技师学院
热轧带钢精轧机组主要辅助设备
转鼓式飞剪
结构:上下转鼓各装 1 或 2 个剪刃。
结构:为双曲柄式,上下曲柄各装一个剪刃。
优点:曲柄式飞剪的剪切机构属于四连杆结构,能够保证剪切过程中, 上下剪刃接近做平行运动,同时在剪切区剪切基本上是垂直轧件,剪切端
面的质量较好。
缺点:这种机构的剪股和摆杆做摆动, 动负荷冲击大。
首钢技师学院
热轧带钢精轧机组主要辅助设备
2、边部加热器
功能:将带坯的边部温度加热补偿至与中部温度接近一致。
带坯在轧制过程中,边部温降大于中部温降,温差大约为 100 0C 左右。 边部温降大,在带钢横断面上晶粒组织
不均匀,性能差异大;同时,还将造成
轧制中边部裂纹和对轧辊严重的不均匀 磨损。
带坯俯视
类型:火焰型边部加热器和电磁感应加热型边部加热器。
首钢技师学院
热轧带钢精轧机组主要辅助设备
电磁感应加热型边部加热器 类型:固定型、地面小车移动型和悬挂式移动型。 。 边部加热器加热带坯厚度范围为 20~6O mm,边部加热范围为 80~ 15O mm,一般在距边部 25mm 处增加温度 80 0C 左右。 需边部加热器加热的钢种主要有:冷轧深冲钢、硅钢、不锈钢、合金
钢等。
1-轮子 2-框架 3-轨道 4-电缆入口 5-电缆软管 6-接触式探测器 7-感应器 8-中心挡板 9-边部加热器支架
精轧区功能说明速度活套V2.0解剖

首钢1580热轧带钢精轧区主速度活套控制器功能说明北京北科麦思科自动化工程技术有限公司目录1.1主速度活套控制器功能说明 (3)1.1.1F1E立辊轧机 (3)1.1.1.1F1E立辊轧机的功能 (3)1.1.1.2F1E立辊轧机的技术参数 (3)1.1.1.3F1E立辊轧机的速度控制 (4)1.1.1.4F1E立辊轧机的操作 (5)1.1.1.5F1E立辊轧机的状态显示 (6)1.1.2F1-F7精轧机 (6)1.1.2.1F1-F7精轧机的功能 (7)1.1.2.2F1-F7精轧机的技术参数 (7)1.1.2.3F1-F7精轧机的速度级联 (9)1.1.2.4F1-F7精轧机的速度控制 (12)1.1.2.5F1-F7精轧机的主轴定位控制 (15)1.1.2.6F1-F7精轧机的操作 (15)1.1.2.7F1-F7精轧机的状态显示 (15)1.1.3活套 (16)1.1.3.1活套的功能 (16)1.1.3.2活套高度及张力控制 (16)1.1.3.2.1活套机构的基本方程 (16)1.1.3.2.2活套张力控制方法 (19)1.1.3.2.3活套高度调节原理 (20)1.1.3.3活套的技术参数 (20)1.1.3.4活套的控制 (20)1.1.3.5活套的操作 (21)1.1.3.6活套的状态显示 (22)1.2精轧区模拟轧钢功能 (22)1.2.1区域模轧 (22)1.2.2全线模轧 (23)1.3精轧区主速度通讯 (23)1.3.1精轧区主速度与传动系统通讯 (23)1.3.2精轧区主速度与精轧区压下控制系统通讯 (25)1.3.3精轧区主速度与精轧区板形控制系统通讯 (25)1.3.4精轧区主速度与卷取控制系统通讯 (25)1.1 主速度活套控制器功能说明主速度活套控制器控制F1E立辊轧机,F1-F7精轧机和L1-L6活套。
其中主轧机和活套是精轧区域的最核心设备。
1.1.1 F1E立辊轧机F1E立辊轧机由主传动装置、立辊机架装配、左右侧辊缝调整装置、轧辊轴承、吊具、配管及平台等部件组成。
三、热轧带钢设备及控制07(CS FSB)

2、精轧机组(Finishing Mill)精轧机组位于粗轧机出口辊道或热卷箱后面,是热轧带钢生产的核心部分主要设备:边部加热器(SH)、切头剪(CS)、剪前辊道、剪前侧导板、精轧除鳞机(FSB)、精轧立辊机前辊道(FE)、精轧机,测厚、板形、测宽、测温仪表等。
精轧机组的布置:2.1 边部加热器位置:切头剪前。
作用:补偿中间坯边部温度,使其与中部温度一致。
边部与中部温差100℃,造成组织性能不均,轧辊边部磨损大。
升温:80~26080~260 ℃针对钢种:冷轧深冲钢、硅钢、不锈钢、合金钢分类:火焰型:带保温罩和煤气烧嘴。
电磁感应型:悬挂式移动型边部加热器结构2.2 切头剪位置:粗轧机后精除鳞机前。
作用:将温度低、形状不良的中间坯头部切除,便于轧件顺利通过精轧机、输出辊道进入卷取机,防止对钢和轧辊表面硌痕。
形式:转鼓式:结构简单,可分别安装不同形状的剪刃分别切头/尾。
mm 。
最大剪切厚度6060mm单侧传动式:双侧传动式:异步剪切式:剪切断面质量好,不连刀。
mm,只有一对剪刃。
曲柄式:剪刃垂直剪切,剪切厚度范围大,最大8080mm转鼓式曲柄式转鼓剪2.3 精轧除鳞机(FSB)位置:精轧机入口。
作用:去除中间坯表面的二次氧化铁皮。
为适应中间坯厚度变化,保证最佳除鳞效果,喷嘴喷射高度可调节。
精轧除鳞机结构2.4 精轧前立辊(F1E )位置:位于F1轧机前。
作用:进一步控制带钢宽度,提高宽度精度,改善边部质量。
侧压量:最大2020mm(mm(坯厚6060mm)mm) 轧制力:最大100吨功能;AWC精轧前立辊结构RALRALRAL。
精轧AGC功能说明

精轧AGC系统功能说明一、AGC系统概况由于带钢全长轧制中会遇到各种干扰,为了消除这些干扰的影响,减少带钢厚度公差,需设置精轧机组自动厚度控制系统,简称AGC系统,AGC系统是提高带钢全长厚度精度的主要手段。
AGC功能投入框图:二、AGC系统的功能GM-AG,即轧制力AGC即利用弹跳方程间接测量钢板厚度作为实测厚度进行反馈控制,这是AGC系统中基本的控制功能,根据GM-AG(中采用头部锁定值还是过程计算机设定值作为厚度基准可分为相对AGC( LK-AGC或绝对AGC(AB-AGC,一般以绝对AGC为主。
KFF-AGC即硬度前馈AGC即将上游机架的实测轧制力所获得的硬度变化信息用于后面各机架进行前馈控制。
MN-AGC即监控AGC由于弹跳方程的精度不高,因此需利用未机架后测厚仪信号对厚度的系统偏差进行纠正。
三、AGC算法GM-AGCL制力AGC其基本原理就是弹跳方程,其本质就是轧机产生单位弹跳量所需要的轧制力。
式中,h为轧机实际出口厚度;S。
为辊缝预设值;P为实际轧制力;M为轧机刚度;轧机刚度M在轧机牌坊制作安装完成以后就已经确定,是一个常值,无法修改,但是在实际的控制过程中,人们却希望轧机的刚度可变,比如为了消除轧辊偏心的影响,人们希望轧机的刚度尽可能的小,但为了消除来料厚度及材料温度变化的影响,又希望轧机刚度尽可能的大,因此产生了变刚度的控制方式。
假设预设辊缝值为S o,轧机的刚度系数为M来料厚度为H。
,此时轧制压力为P】,则实际轧出厚度h i应为:当来料厚度或温度因某种原因有变化时,在轧制过程中必然会引起轧制压力和轧出厚度的变化,如果压力由P i变为P2,则轧出厚度h2为:当轧制压力由P】变为P2时,则其轧出厚度的厚度偏差△ h正好等于压力差所引起的弹跳量为:为了消除此厚度偏差,可以通过调节液压缸的位置来补偿轧制力变化所引起的轧机弹跳变化量,此时液压缸所产生的轧辊位置修正量△ x,应与此弹跳变化量呈正比,方向相反,为:式中C为变刚度系数KFF-AGCi机架出口厚度变化量可用下式计算:h| = A Hi H汁 A Ki--K汁 A Si、SA“(X i)C QX 为'P :H i,或 C式中,为i i机架入口厚度变动(从静态角度可认为H i h i-1)「K为1 i机架厚度变动"Si为i机架辊缝调节量主要扰动为温度变动,我们曾对不同成品规格当FTO有20O C变动时各机架轧制温度以及其变形阻力(硬度)的变动作了计算,由计算结果可知,不能用::K K匚相等的法则来表示各机架、水间的关系,而应采用Ki=:匚、K i其中一:为0.95〜1.05 因此可利用上游机架的实测轧制力P*来求出K!设叶R*—? (p为设定值)—CQC Q然后即可求出K i= v'K i各机架前馈控制量(使6^ =0 ),为;卩一、S = J K iC其中B ki=如上一机架有残余出口偏差h i-1,则亦可用于水i田:K i、S j =C Chi的动作时间可以每一机架咬钢后「时刻投入,X为检测机架机架所实测到的突发量发生时间(相对于咬钢时间),由于精轧组秒流量相当,因此i 机架仍可用怡来判断突发量的到达,「为提前量决定于压下系统的响应速度。
三、热轧带钢设备及控制07(CS_FSB)

2、精轧机组(Finishing Mill)精轧机组位于粗轧机出口辊道或热卷箱后面,是热轧带钢生产的核心部分主要设备:边部加热器(SH)、切头剪(CS)、剪前辊道、剪前侧导板、精轧除鳞机(FSB)、精轧立辊机前辊道(FE)、精轧机,测厚、板形、测宽、测温仪表等。
精轧机组的布置:2.1 边部加热器位置:切头剪前。
作用:补偿中间坯边部温度,使其与中部温度一致。
边部与中部温差100℃,造成组织性能不均,轧辊边部磨损大。
升温:80~26080~260 ℃针对钢种:冷轧深冲钢、硅钢、不锈钢、合金钢分类:火焰型:带保温罩和煤气烧嘴。
电磁感应型:悬挂式移动型边部加热器结构2.2 切头剪位置:粗轧机后精除鳞机前。
作用:将温度低、形状不良的中间坯头部切除,便于轧件顺利通过精轧机、输出辊道进入卷取机,防止对钢和轧辊表面硌痕。
形式:转鼓式:结构简单,可分别安装不同形状的剪刃分别切头/尾。
mm 。
最大剪切厚度6060mm单侧传动式:双侧传动式:异步剪切式:剪切断面质量好,不连刀。
mm,只有一对剪刃。
曲柄式:剪刃垂直剪切,剪切厚度范围大,最大8080mm转鼓式曲柄式转鼓剪2.3 精轧除鳞机(FSB)位置:精轧机入口。
作用:去除中间坯表面的二次氧化铁皮。
为适应中间坯厚度变化,保证最佳除鳞效果,喷嘴喷射高度可调节。
精轧除鳞机结构2.4 精轧前立辊(F1E )位置:位于F1轧机前。
作用:进一步控制带钢宽度,提高宽度精度,改善边部质量。
侧压量:最大2020mm(mm(坯厚6060mm)mm) 轧制力:最大100吨功能;AWC精轧前立辊结构RALRALRAL。
精轧机工作原理
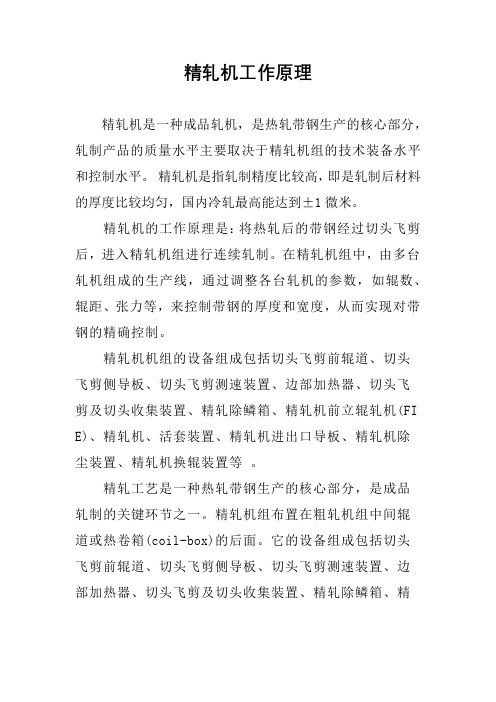
精轧机工作原理
精轧机是一种成品轧机,是热轧带钢生产的核心部分,轧制产品的质量水平主要取决于精轧机组的技术装备水平和控制水平。
精轧机是指轧制精度比较高,即是轧制后材料的厚度比较均匀,国内冷轧最高能达到±1微米。
精轧机的工作原理是:将热轧后的带钢经过切头飞剪后,进入精轧机组进行连续轧制。
在精轧机组中,由多台轧机组成的生产线,通过调整各台轧机的参数,如辊数、辊距、张力等,来控制带钢的厚度和宽度,从而实现对带钢的精确控制。
精轧机机组的设备组成包括切头飞剪前辊道、切头
飞剪侧导板、切头飞剪测速装置、边部加热器、切头飞
剪及切头收集装置、精轧除鳞箱、精轧机前立辊轧机(FI E)、精轧机、活套装置、精轧机进出口导板、精轧机除
尘装置、精轧机换辊装置等。
精轧工艺是一种热轧带钢生产的核心部分,是成品
轧制的关键环节之一。
精轧机组布置在粗轧机组中间辊
道或热卷箱(coil-box)的后面。
它的设备组成包括切头
飞剪前辊道、切头飞剪侧导板、切头飞剪测速装置、边
部加热器、切头飞剪及切头收集装置、精轧除鳞箱、精
轧机前立辊轧机(FIE)、精轧机、活套装置、精轧机进出口导板、精轧机除尘装置、精轧机换辊装置等。
精轧机工作原理
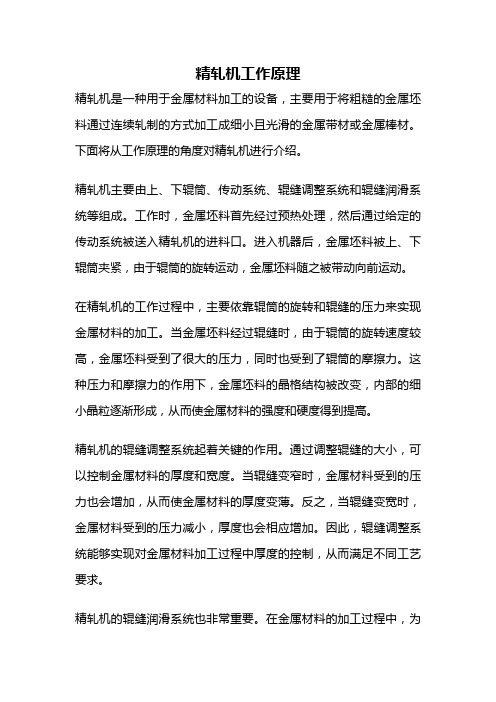
精轧机工作原理精轧机是一种用于金属材料加工的设备,主要用于将粗糙的金属坯料通过连续轧制的方式加工成细小且光滑的金属带材或金属棒材。
下面将从工作原理的角度对精轧机进行介绍。
精轧机主要由上、下辊筒、传动系统、辊缝调整系统和辊缝润滑系统等组成。
工作时,金属坯料首先经过预热处理,然后通过给定的传动系统被送入精轧机的进料口。
进入机器后,金属坯料被上、下辊筒夹紧,由于辊筒的旋转运动,金属坯料随之被带动向前运动。
在精轧机的工作过程中,主要依靠辊筒的旋转和辊缝的压力来实现金属材料的加工。
当金属坯料经过辊缝时,由于辊筒的旋转速度较高,金属坯料受到了很大的压力,同时也受到了辊筒的摩擦力。
这种压力和摩擦力的作用下,金属坯料的晶格结构被改变,内部的细小晶粒逐渐形成,从而使金属材料的强度和硬度得到提高。
精轧机的辊缝调整系统起着关键的作用。
通过调整辊缝的大小,可以控制金属材料的厚度和宽度。
当辊缝变窄时,金属材料受到的压力也会增加,从而使金属材料的厚度变薄。
反之,当辊缝变宽时,金属材料受到的压力减小,厚度也会相应增加。
因此,辊缝调整系统能够实现对金属材料加工过程中厚度的控制,从而满足不同工艺要求。
精轧机的辊缝润滑系统也非常重要。
在金属材料的加工过程中,为了减小辊筒与金属材料之间的摩擦力,增加金属材料的延展性,必须保证辊缝处有足够的润滑剂。
润滑剂能够形成一层薄膜,减小辊筒与金属材料之间的接触面积,从而减小摩擦力。
同时,润滑剂还能起到冷却作用,防止金属材料因为摩擦而过热。
精轧机是一种通过连续轧制来加工金属材料的设备。
它主要依靠辊筒的旋转和辊缝的压力来实现金属材料的加工,通过辊缝调整系统和辊缝润滑系统的配合,能够实现对金属材料厚度和宽度的控制。
精轧机的工作原理简单明了,但在实际应用中,还需要根据具体的金属材料和工艺要求进行参数的调整和控制,以确保加工质量的稳定性和一致性。
精轧机说明书.(DOC)

高速线材精轧机组安装使用说明书制造单位:哈尔滨广旺机电设备制造有限公司设备图号: ZJF90d00使用客户:出厂日期:目录第一章、技术说明 (2)第二章、设备安装调整 (4)第三章、设备的使用维护与更换 (7)第四章、常见故障及排除 (13)第五章、附件 (14)精轧机组是高速线材车间的重要设备,为了保证精轧机组正常运转,用户须了解机组的性能、安装、运行与日常维护等基本常识。
本说明书就以上几个方面作了简单的介绍,用户在安装、使用机组前请先阅读本手册。
本说明书供武安文煜高线专用。
第一章技术说明一、设备用途本精轧机组为摩根五代顶交45°无扭重载高速线材精轧机组,图纸由国内设计转化完成。
本机组通过10机架连续微张力轧制,将上游轧机输送的轧件,轧制成φ5.5-φ20mm的成品线材。
二、设备主要性能参数1. 工艺参数:●来料规格:φ17—φ22mm●来料温度:>900℃●成品规格: φ5.5-φ20mm●主要钢种:碳钢、优质碳素钢、低合金钢、合金钢、焊条钢、冷镦钢等●第10架出口速度:≤95m/s(轧制φ6.5规格时)2. 设备参数:●机组组成:∅230轧机(5架)、∅170轧机(5架)、增速箱、大底座、挡水板与防水槽、缓冲箱、保护罩、联轴器、精轧机组配管等。
●机架数量: 10架(1-5架为∅230轧机,6-10架为∅170轧机同种规格的轧辊箱可以互换)●布置方式:顶交45°,10机架集中传动●辊环尺寸:∅230轧机:∅228.3/∅205×72mm∅170轧机:∅170.66/∅153×57.35/70mm ●传动电机: AC同步变频电机,功率: 5500kW●振动值:≤4.5 mm/s●噪音:≤80dB(距轧机1.5米处)●机组总速比(电机速度/装辊转速)见下表:●机组润滑方式:稀油集中润滑油压: 0.35MPa(点压力)总耗量:1200L/min油品: Mobil 525清洁度:10μ供油温度:38°C -42°C●保护罩液压系统:工作压力:15MPa系统流量:20 l/min●装辊工作压力:高压45 MPa -49.5MPa,低压22 MPa -25 MPa●卸辊工作压力:最大70MPa第二章设备安装调整一、安装调整顺序●将机组底座、增速箱、和主电机初步就位。
- 1、下载文档前请自行甄别文档内容的完整性,平台不提供额外的编辑、内容补充、找答案等附加服务。
- 2、"仅部分预览"的文档,不可在线预览部分如存在完整性等问题,可反馈申请退款(可完整预览的文档不适用该条件!)。
- 3、如文档侵犯您的权益,请联系客服反馈,我们会尽快为您处理(人工客服工作时间:9:00-18:30)。
精轧机组用途:F1-F7精轧机组用于将经过粗轧并切头的中间坯轧制为成品规格,中间坯厚度25~50×700~1350mm,成品规格1.2~20×700~1350mm。
结构:精轧机组由以下部分组成: F1精轧机列、F2精轧机列、F3精轧机列、F4精轧机列、F5精轧机列、F6精轧机列、F7精轧机列、F1-F7传动装置、工作辊换辊装置、支撑辊换辊装置、F1-F7活套和导卫装置、F1-F7机上配管、F1-F7平台围栏和平台配管等。
F1━F7精轧机列是四辊不可逆式水平轧机,由7架轧机组成,呈连续式布置,机架间距离5500,称为F1━F7机架。
轧机由机架装配、工作辊装配、支承辊装配、压下装置、弯辊窜辊装置、平衡装置、移动垫板装置、传动装置、走台、配管、接近开关等组成。
传动装置由主电机、电机联轴器、减速机、中间接轴、齿轮机座和轧辊接轴组成。
其中F5-F7没有减速机。
工作辊换辊装置由横移列车、固定轨道和电动小车等组成。
支撑辊换辊装置由固定滑道和推拉液压缸等组成。
活套和导卫装置由液压活套、工作辊冷却、支撑辊冷却、机架间冷却、入口导卫、出口导卫、导卫梁、交叉喷射等组成。
主要结构见简图。
1.电机2.联轴器3.减速机4.中间接轴5.齿轮机座6.轧辊接轴7.精轧机本体三、主要技术参数四辊精轧机主要技术参数表轧机名称F1 F2 F3 F4 F5 F6 F7最小工作辊直径mm 720 720 720 720 540 540 540最大工作辊直径mm 800 800 800 800 600 600 600工作辊辊身长度mm 1700 1700 1700 1700 1700 1700 1700最小支撑辊直径mm 1250 1250 1250 1250 1250 1250 1250最大支撑辊直径mm 1350 1350 1350 1350 1350 1350 1350支撑辊辊身长度mm 1500 1500 1500 1500 1500 1500 1500最大轧制力t 3500 3500 3500 3500 3000 3000 3000最大轧制力矩t*m 177.6 149.7 100 47.8 36.7 29.8 27.5最大弯辊力/单侧t 150 150 150 150 120 120 120轧机线速度(最大辊径时)基速(m/s) 1.26 1.632 2.4 3.49 4.71 6.28 8.01最高速(m/s) 3.15 4.236 6.336 9.22 12.44 15.39 18.54轧机线速度(最小辊径时)基速(m/s) 1.134 1.476 2.16 3.14 4.24 5.652 7.21 最高速(m/s) 2.835 3.804 5.7 8.29 11.2 13.85 16.68推荐减速机速比 4.65 3.92 2.62 1.8主电机DC/AC AC AC AC AC AC AC AC功率kW 6000 6000 6000 6000 6000 6000 6000基速r/min 125 150 150 150 150 200 255最高速r/min 350 400 400 400 400 490 5901、设备结构及功能上部支撑辊平衡装置位置和作用:上支撑辊的平衡装置安装在牌坊连接梁的顶部。
液压缸的活塞杆通过轨梁与两个导轨连接,他们分别分布在轧机机架的入口和出口侧,上支撑辊轴承座用挂钩连接在轨道上。
垫块缩回装置位置和作用:安装在各个机架顶部和液压压下缸之间。
它用来补偿上工作辊磨削后的偏差,将压下缸的行程保持在特定的范围内,垫块有液压缸拖动。
液压辊缝设定系统位置和作用:液压辊缝设定缸安装在上支撑辊轴承座和上部机架连接架之间。
液压辊缝设定系统用来调整预期的辊缝,并用作最终的自动厚度控制元件和过载保护。
轧机机架上的提升轨道位置和作用:安装在机架窗口的入口和出口侧,出口侧的延伸段用螺栓固定在轧机机架上,滑动导轨用螺栓拧紧在提升轨道上,轨道在液压缸的推动下在牌坊窗口中安全的进行升降动作。
提升导轨在液压推动下做垂直调整,用来将工作辊提升到轧辊换辊位置。
带有传动轴夹持的工作辊弯辊和窜辊位置和作用:固定式的弯辊缸安装在机架窗口内的两侧表面,弯辊缸座用于安装弯辊缸,工作侧有工作辊锁紧装置,传动侧有主轴夹持装置。
其作用是轴向移动工作辊,对工作辊进行正弯辊,控制带钢的板形。
支撑辊轴承座和部件位置和作用:支撑辊轴承座将由辊缝设定系统施加的力传送到支撑辊上,支撑辊装在支撑辊轴承座上的油膜轴承中。
支撑轴承座位于传动和操作侧的机架窗口内。
操作侧的轧辊轴承座在液压推动的固定板来进行轴向定位。
上下支撑辊轴承座在操作侧有一个推力轴承。
油膜轴承位置和作用:油膜轴承用于安装支撑辊。
油膜轴承是最合适的承受产生在机架间的高轧制力的轴承。
锥套安装在轧辊颈部,衬套安装在轧辊轴承座上。
轴承面对辊身一侧带有特殊的密封系统。
支撑辊位置和作用:支撑辊安装在两侧的轴承箱内的油膜轴承中。
支撑辊支撑着工作辊并且传递轧制力。
轧机的轧制线调整和支撑辊更换台架位置和作用:用于下工作辊和支撑辊的磨损补偿和通过精轧机架的轧制线调整,对于精轧机,在下支撑辊轴承座下面安装一个液压设定的阶梯垫装置,这就使轧制线可以有小增量的调整,例如在工作辊换辊之后的调整,这样在更换支撑辊时,下支撑辊完全被液压缸顶起,为安装在轧机机架上阶梯垫设定系统留出空间,依据轧辊直径进行设定。
入口导卫位置和作用:在机架前引导轧件,F1—F7上、下全部采用气缸驱动式摆动机构,摆入时擦辊器贴靠在工作辊上,摆出时让出换辊辊道。
入口侧工作辊冷却水管固定在其上,工作辊冷却水装有调节阀,可以按工艺要求调节或开闭工作辊冷却水。
F1—F7入口侧还设有工艺润滑,下入口导位上还设有侧导板喷水孔道。
出口导卫位置和作用:在机后从上下方向引导轧件防止轧件上翘和钻钢,F—F7相同,它们都支撑在一个导位架上,上导位用气缸拉起擦辊器贴靠在上工作辊上,下导卫板自重使擦辊器贴靠在下工作辊上,出口侧工作辊冷却水管固定在其上,工作辊冷却水装有调节阀,可以按工艺要求调节或开闭工作辊冷却水。
入口侧导板位置和作用:导板安装在机架入口侧的轧制线上下部位,用于将进来的带钢导入辊缝中。
出口侧导板位置和作用:导板安装在每个机架的出口侧,用来将轧出的带钢送出机架。
工作辊冷却位置和作用:冷却水通过喷射头喷在精轧机工作辊上,用于过钢时轧辊的冷却和润滑。
冷却的最主要目的是保持轧辊在轧钢过程中的温度基本保持不变,在停机时水量减少,停机时水量的参考值越为最大流量的20℅,这一数值调试时设定好并在试运转中来设定。
因此操作模式可以分为如下三个阶段:—不供应水(轧机因更换轧辊而停止)—越为最大水量的20℅来供水(轧制间隙时)—选择最大量供水(轧钢状态)机架间冷却位置和作用:在轧机之间装有一个循环水集管,并且用来防止在薄板的表面形成氧化铁皮。
此外,在轧制过程中用来冷却机架间的带钢。
因此带钢的温度可以得到控制。
每个冷却区域装有一个气动控制阀,从而使在整个工作过程中可以不断地对水量进行调节。
机架间底步对头部进行导向的横梁采用内部水冷却。
活套辊也采用内部水冷却。
这两个采用同一个水冷系统,每个机架有一个阀来控制水的开关。
交叉喷射位置及作用:交叉喷射集管固定在F2—F7机架的前部,用以喷射抑制氧化铁皮和其它扬尘用水。
出口吹扫位置和作用:出口吹扫包括设在F7后的蒸气侧喷和吹风装置,用以吹净水蒸气和粉尘,保证F7后测厚仪、测温仪、凸度仪和板形仪的正常工作。
工作辊的换辊装置安装位置和功能:在精轧机操作侧安装换辊装置,此装置带有侧移平台和换辊缸;侧移平台是对每架轧机两套工作辊来设计的,当更换支撑辊时,侧移平台可以用横车移开。
工作辊可通过轧辊更换缸来抽出或推入轧机。
支撑辊换辊装置安装位置和功能:支撑辊更换装置安装在操作侧,且位于工作辊换辊装置下面。
当工作辊侧移平台吊开后,就可看到支撑辊换辊用的更换架,更换架装在导轨上作为支撑辊更换的拖架,上支撑辊是通过一板凳压在下支撑辊轴承座上。
支撑辊从机架上抽出和推入都是通过液压缸动作来实现的,该液压缸是安装在工作辊换滚缸基础之下,固定再支撑辊换辊拖架上。
活套装置位置和作用:安装在每两个机架之间,用于支撑带钢,形成调节轧机动态速度变化的套量,维持机架间带钢的张力,参与精轧机组的调速控制。
4.位移传感器1) 用于移动垫板换位(共7台)位移传感器置于液压缸尾部,用于控制阶梯垫板的位置。
每机架都装配有移动垫板装置,其安装于机架窗口与辊缝调节液压缸(AGC缸)之间。
由一个液压缸驱动,操作侧和传动侧机械组合。
驱动移动垫板的液压缸装配有位置测量系统,其安装在液压缸里,目的是为确保移动垫板达到准确位置。
因为辊缝调节液压缸有一限定的行程,使用移动垫板的目的是较小的调节液压缸行程而获得较大的辊缝范围,其调节范围是10——65mm。
这样就能补偿各种不同的工作辊辊径带来的影响。
换辊时,须根据新的辊径由计算机对移动垫板装置进行必要的计算;当移动垫板运行到各种不同的位置时,必须进行校准。
校准以后才能将新的垫板推进,当调整同样的垫板时,则不需要校准,同样适应工作辊检测时的拉出与推进,垫板块的位置改变。
其位置精确度为±2mm。
为能将垫板块拉出或推进一个新位置,支撑辊平衡系统在此之前必须下降约15——20mm,在换辊时,垫板块的转换由一个自动程序来完成。
新的位置选定后,使用按钮或键盘开始自动程序,在地面操作点操作面板上,使用点动或手动模式也可对垫板块的位置进行调整。
每架轧机1个,阶梯垫板有4个工作位置,每2个位置之间的距离为210mm,前3个位置垫板厚度分别90 mm \45 mm \0 mm,第4个位置为换辊位置。
参考型号: RHN0700MP071S1G4100数量: 1个/每架,共7个.2)用于液压压下AGC缸(共14台)位移传感器置于液压缸底部,用于控制AGC缸活塞的位置,进行轧机辊缝设定及压下量调整。
每架轧机2个。
轧辊最大开口度60 mm,AGC缸行程115 mm。
参考型号: RHN0150MP071S1G6100数量: 2个/每架,共14个.3)用于上支撑辊平衡装置(共7台)平衡支撑辊的液压缸安装于上横梁的中间,由液压缸活塞杆上的滑动轴承支撑,横梁,连接杆和平衡杆形成了上支撑辊的悬吊结构。
支撑辊平衡系统用来平衡支撑辊,对辊缝无作用力,上支撑辊装置,辊缝调节液压缸,移动垫板装置和支撑辊的平衡系统须紧靠轧机机架轭。
平衡力应比静平衡装置重量高20——30﹪,平衡液压缸是单杆液压缸,通过活塞杆侧的液压箱供给流体,然后通过活塞杆侧的孔流进活塞。
因为这样在活塞底部区域的工作压力大。
闭和回路的控制信息由一个位置传感器和一个压力传感器来完成。