高线无扭线材精轧机组(BGV)精密维修实践
高速无扭轧机产线材(盘条)的品质管理与持续改进实践

高速无扭轧机产线材(盘条)的品质管理与持续改进实践随着工业化进程的不断发展,钢铁行业作为基础产业之一扮演着重要的角色。
高速无扭轧机产线材(盘条)作为钢铁行业的重要产品之一,在生产中的品质管理与持续改进显得尤为重要。
本文将探讨高速无扭轧机产线材(盘条)在品质管理与持续改进方面的实践经验。
首先,品质管理是高速无扭轧机产线材(盘条)生产过程中的核心环节。
品质管理的目标是保证产品的质量符合市场需求和技术标准,并且持续提升产品的品质水平。
在品质管理方面,高速无扭轧机产线材(盘条)需要注意以下几个方面:1. 完善的生产工艺控制系统:高速无扭轧机产线材(盘条)生产过程多层次、多环节,需要建立完善的生产工艺控制系统。
这个系统包括对原材料的选择和质量控制、生产过程中各个环节的监控和控制、产品质量检测和分析等方面。
只有建立完善的生产工艺控制系统,才能从根本上保证产品的品质。
2. 严格的品质检测标准:高速无扭轧机产线材(盘条)需要建立一套严格的品质检测标准。
这个标准应该基于市场需求和技术标准,并且要具备可操作性和可实施性。
只有在严格的品质检测标准的指导下,才能保证产品的品质。
3. 持续的质量改进活动:高速无扭轧机产线材(盘条)的生产过程中,质量问题是难以避免的。
因此,持续的质量改进活动是必不可少的。
这包括对产品质量问题的分析和改进、对生产工艺的改进以及对人员技术能力的提升等方面。
只有通过持续的质量改进活动,才能不断提升产品的品质水平。
其次,持续改进是高速无扭轧机产线材(盘条)品质管理的关键。
持续改进是一个不断追求优化和进步的过程,能使企业在竞争激烈的市场中保持竞争力。
高速无扭轧机产线材(盘条)在持续改进方面需要注意以下几个方面:1. 建立改进机制:高速无扭轧机产线材(盘条)需要建立一个持续改进的机制。
这个机制应该包括信息收集和反馈、问题分析和解决、改进方案的制定和实施等环节。
只有建立了良好的改进机制,才能推动企业持续改进。
高速无扭轧机产线材(盘条)的质量控制与检测技术

高速无扭轧机产线材(盘条)的质量控制与检测技术近年来,随着工业化的发展,钢铁产业成为了国民经济的支柱级产业之一。
而作为钢铁产业中的重要环节,无扭轧机产线材的质量控制和检测技术尤为关键。
本文将介绍高速无扭轧机产线材的质量控制与检测技术,以提高产品质量和生产效率。
一、质量控制1. 原材料选择和预处理:把优质的原材料作为生产的基础是确保产品质量的先决条件。
原材料的来源和成分要符合相关标准和要求。
在预处理阶段,需要对原材料进行过筛、预热和预切等处理,以提高材料的可加工性和减少生产过程中的缺陷。
2. 控制生产工艺参数:高速无扭轧机产线材的生产是一个精密的过程,需要在合适的温度、压力、速度和润滑条件下进行。
生产过程中需要对各项参数进行严格控制,包括轧辊压力、顶辊位置、轧辊间隙等,以确保产品尺寸、形状、表面质量等的稳定性。
3. 实施质量检测及时反馈:在生产过程中,需要建立及时的质量检测机制,对产品尺寸、形状、表面质量等进行在线监测和检测。
一旦发现异常,立即停机进行调整和修复,避免不合格产品的堆积。
二、检测技术1. 尺寸测量技术:高速无扭轧机产线材的尺寸测量是质量控制的重要环节之一。
常用的测量技术包括钢尺测量、激光测量和光学传感器测量等。
这些测量技术可以实时监测产品尺寸的变化,并与预设的标准进行比对,及时发现并纠正尺寸偏差。
2. 表面质量检测技术:无扭轧机产线材的表面质量直接影响到产品的使用性能和外观。
表面质量的检测技术包括模具观察、高速摄像仪、涡流检测等。
通过这些技术,可以实时观察和检测产品表面的缺陷,如气泡、坑洞、裂纹等,并及时采取措施进行修复或调整。
3. 成分分析技术:高速无扭轧机产线材的成分分析对于产品的质量控制具有重要意义。
通过光谱、导电度和化学分析等技术手段,可以对产品的成分进行快速和准确的分析。
这有助于及时发现成分异常和变化,制定调整生产参数的措施,以确保产品的化学成分符合要求。
4. 紧急故障检测技术:为了提高产线的稳定性和可靠性,需要实施紧急故障检测技术。
高速无扭轧机产线材(盘条)的设备维护与故障诊断技术

高速无扭轧机产线材(盘条)的设备维护与故障诊断技术引言:随着工业的快速发展,高速无扭轧机产线已成为钢铁和金属制造行业中不可或缺的关键设备。
在生产线上,高速无扭轧机产线负责将金属料材进行加工,使其变成符合不同行业需求的线材或盘条。
然而,由于长时间高强度的运转,设备的维护和故障诊断成为保证生产顺畅的重要任务。
本文将探讨高速无扭轧机产线材(盘条)的设备维护与故障诊断技术,以提高设备的可靠性和生产效率。
一、设备维护技术1. 定期检查和保养定期检查和保养是保证高速无扭轧机设备正常运行的基础。
操作人员应制定详细的设备维护计划,包括定期检查设备的关键部件,如轴承、油封、润滑系统等,确保其在良好的工作状态。
此外,还应定期对设备进行清洁和润滑,以防止积尘和摩擦损耗。
2. 轴承和传动系统维护高速无扭轧机的轴承和传动系统是经常磨损和故障的部件。
为了保障设备的正常运行,应定期检查轴承的润滑情况,并及时添加润滑油进行维护。
同时,检查传动系统的皮带或链条的张力,确保其工作正常,避免因传动系统故障导致设备停机。
3. 温度控制和冷却系统检查高速无扭轧机设备在运行过程中会产生大量的热量,为了保证设备的正常工作,必须对温度进行有效的控制和冷却。
操作人员应定期检查和清洁冷却系统,确保冷却剂的供给畅通,并根据设备的工作状态调整冷却系统的参数,以确保设备的正常运行温度范围。
二、故障诊断技术1. 数据监测和分析高速无扭轧机产线材的故障诊断可以通过数据监测和分析实现。
通过安装传感器和数据采集设备,可以实时监测设备的运行状态和各种参数,如温度、振动、电流等。
通过对这些数据进行分析,可以判断设备的工作状态是否正常,及时发现故障隐患。
2. 故障分析和排除当设备出现故障时,操作人员应根据故障现象和相关参数分析故障原因,并采取相应的排除措施。
在进行故障分析时,可以借助专业的故障诊断软件和设备维护手册,结合经验和知识,快速准确地识别和解决问题。
3. 预防性维护措施除了及时排除故障,还需要采取预防性维护措施,避免设备出现故障。
高速线材精轧机常见故障分析与故障诊断方法研究本科毕业论文

学号:1006060113Xingtai Polytechnic College毕业论文GRADUATE DESIGN论文题目:高速线材精轧机常见故障分析与故障诊断方法研究学生姓名:专业班级:材料成型与控制技术院系:资源与环境工程系指导教师:目录摘要 (2)ABSTRACT (2)引言 (4)1 高速线材轧机的发展 (5)1.1线材轧机的发展与高速线材轧机的诞生 (5)1.2高速线材轧机的发展概况 (5)1.2.1高速线材轧机机型 (5)1.2.2高速线材轧机的发展与成熟 (6)1.2.3高速线材精轧轧机的典型结构 (7)2 高速线材精轧机的故障机理和故障特征 (8)2.1精轧机轴承的故障机理和故障特征 (8)2.1.1滚动轴承常见故障形式 (9)2.1.2滚动轴承的震动信号特征 (10)2.2精轧机齿轮的故障机理和故障特征 (11)2.2.1齿轮常见的故障形式 (11)2.2.2齿轮的震动信号号特征 (12)3 高速线材精轧机故障诊断方法研究 (13)3.1精轧机振动信号的时域波形分析 (14)3.2精轧机振动信号的幅值域分析 (15)结论 (15)致谢 (16)参考文献 (18)摘要精轧机组是线材厂的关键设备,对精轧机组进行在线监测,可以提前预知设备的工作状态以及故障的发展趋势,对保证企业的安全生产有重大意义。
锥齿轮箱是精轧机的重要零部件,因此研究锥齿轮箱的诊断技术对于降低设备维修费用,提高产品质量和市场竞争力具有重要的工程应用价值。
论文针对高速线材精轧机故障开展研究,利用便携式仪器,对关键设备进行点检,按照一定周期采集设备的振动数据进行统计并分析。
以曲线形式反映在系统工作站,成功捕捉到精轧机的各种故障,避免了恶性事故的发生,取得了显著的经济效益。
关键词: 高速线材轧机;齿轮箱;在线监测;故障研究ABSTRACTThe finishing mill is the key part of high speed rolling mill. The working condition andfault trends can be predicted by the on-line monitoring and fault diagnosis system, whichis very important to ensure the safety in production. Bevel gear box is an important component of finishing mill, therefore to study the diagnosis technology of bevel gear box to reduce equipment maintenance costs, improve product quality and market competitiveness has important engineering application value. Paper for high speed wire rod finishing mill failure to carry out the research, the use of portable instruments, the key equipment to check, according to certain cycle vibration dataacquisition equipment for statistics and analysis. Workstation in curve form reflected in the system, successfully capture the finishing mill all kinds of fault, to avoid the malignant accident, has obtained the remarkable economic benefits.Keywords: High-speed wire mills; Gear Box; On-Line Monitoring; Fault diagnosis;引言企业的发展动力来源于员工的较高素质,员工的专业知识与技能的熟练握是企业高效率生产及操作技能水平。
高速无扭线材精轧机组维修实践
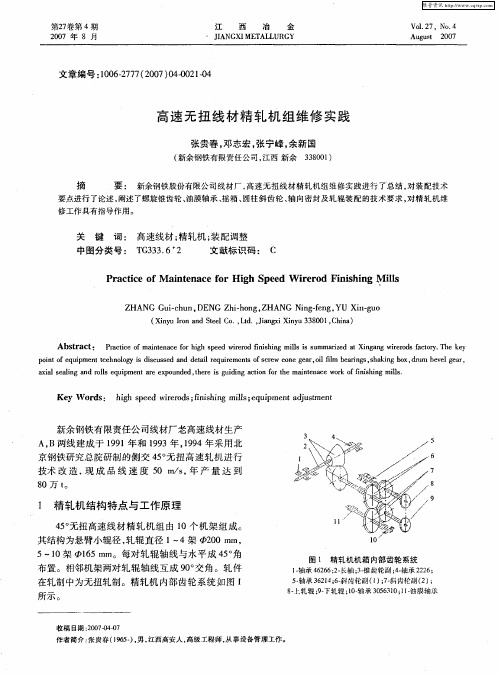
高速 无扭 线 材精 轧 机 组维 修 实践
张贵 舂 , 邓志 宏 , 宁峰 , 新 国 张 余
( 新余钢铁有限责任公司 , 西 新余 3 80 ) 江 30 1
摘
要 : 新余钢铁股份有限公司线材厂, 高速无扭线材精轧机组维修实践进行了总结, 对装配技术
要点进行 了论 述 , 阐述了螺旋锥齿轮 、 油膜轴 承 、 摇箱 、 圆柱斜 齿轮 、 向密封及 轧辊装配 的技术要 求 , 轴 对精轧 机维 修工作 具有指 导作用 。
关
键
词 : 高 速线 材 ; 精轧 机 ; 配调整 装
文 献标 识码 : C
中图分 类号 : T 3 3 6 2 G 3 .
P a t eo an e a ef r Hih S e d W ie o i i i g M is r ci fM i tn c o g p e r r d F ns n l c h l
收 稿 日期 :0 70 -7 20 - 0 4
作者简 介: 张贵春 (9 5 )男 , 】6 一, 江西商安人 , 高级工程师 , 从事设备管理工作。
维普资讯
・
2
20 07年 8月
由2台联轴的直流电机通过全数控直流调速系 统拖动 , 经增速箱分别带动精轧机上下两长轴 , 长轴
Ab ta t sr c :
P at eo e a efrhg p e rrd f ihn l ss mmai d a n a gwi rd a tr. ek y rci fmmn n c o ih se d wi o ns ig mi si u c t e i l r e tXig n r o sfcoy Th e z e
5 0架 q15m 。每对轧辊轴线与水平 成 4 。 ~l 06 m 5角
高速无扭精轧机组设备故障诊断分析

高速无扭精轧机组设备故障诊断分析高速无扭精轧机组是现代化轧钢设备的一种,广泛应用于钢铁、有色等行业。
在机组的使用过程中,难免会出现各种故障,需要及时进行诊断和排除。
本文将对高速无扭精轧机组的设备故障进行分析和诊断。
一、轧辊故障(1) 轧辊磨损严重高速无扭精轧机组的轧辊经常在高强度的作用下运转,长时间使用后轧辊表面会出现磨损现象。
磨损严重会导致轧辊几何形状发生变化,影响轧钢工艺和质量。
解决这个问题的方法是定期更换轧辊或在保养时进行轧辊磨平操作。
(2) 轧辊表面开裂在轧制过程中,由于轧辊表面有较强的压力和摩擦,轧辊表面容易出现裂纹。
轧辊表面开裂会影响轧制工艺和轧钢质量,严重时可能会导致轧辊断裂。
处理轧辊表面开裂问题的方法是定期进行轧辊表面检查,在发现裂纹时及时更换轧辊或进行焊接修复。
(3) 轧辊间隙不均匀高速无扭精轧机组的轧辊间隙对轧制质量具有重要影响。
轧辊间隙过大会导致轧钢成品尺寸变差,轧辊间隙过小则会加大动力负荷,影响机组稳定性。
轧辊间隙不均匀的原因可能是轧辊尺寸不一致、轧辊安装不当等多种因素,需要在日常运维中进行调整和检查。
二、冷却系统故障高速无扭精轧机组在轧制过程中需要进行冷却,以控制轧辊表面温度,避免轧辊表面损伤。
冷却系统故障可能会导致轧辊过热,影响轧制质量,严重时可能会导致轧辊损坏。
(1) 冷却液温度过高冷却液温度过高会导致冷却效果不佳,轧辊表面温度难以控制。
处理方法是检查冷却系统的管道和散热装置,保证冷却液循环畅通,并定期更换冷却液。
(2) 冷却液压力不足冷却液压力不足会导致液流不畅,冷却效果不佳。
处理方法是检查液压系统,保证液压系统工作正常。
高速无扭精轧机组的传动系统是机组的核心部分,直接决定了机组的运行效率和稳定性。
传动系统故障可能会导致机组出现振动、噪声、载荷不稳定等问题,甚至会影响机组的安全运行。
(1) 传动带松动传动带松动会导致机组动力传递不稳定,工作效率降低。
处理方法是及时检查传动带的张力,保持合适的张力。
高速无扭轧机产线材(盘条)的抗腐蚀性能与防腐技术研究
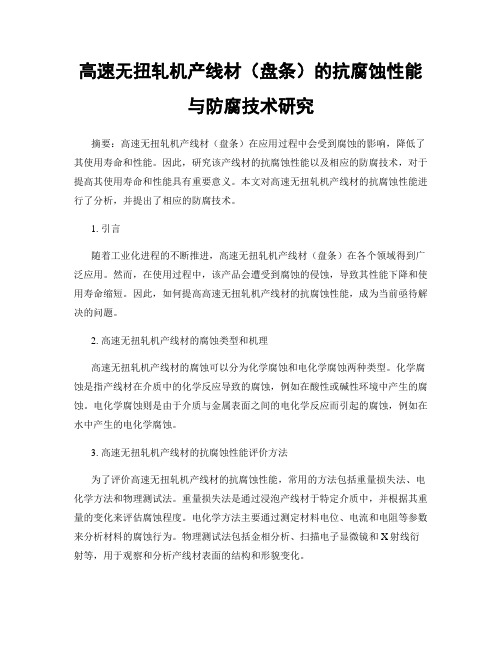
高速无扭轧机产线材(盘条)的抗腐蚀性能与防腐技术研究摘要:高速无扭轧机产线材(盘条)在应用过程中会受到腐蚀的影响,降低了其使用寿命和性能。
因此,研究该产线材的抗腐蚀性能以及相应的防腐技术,对于提高其使用寿命和性能具有重要意义。
本文对高速无扭轧机产线材的抗腐蚀性能进行了分析,并提出了相应的防腐技术。
1. 引言随着工业化进程的不断推进,高速无扭轧机产线材(盘条)在各个领域得到广泛应用。
然而,在使用过程中,该产品会遭受到腐蚀的侵蚀,导致其性能下降和使用寿命缩短。
因此,如何提高高速无扭轧机产线材的抗腐蚀性能,成为当前亟待解决的问题。
2. 高速无扭轧机产线材的腐蚀类型和机理高速无扭轧机产线材的腐蚀可以分为化学腐蚀和电化学腐蚀两种类型。
化学腐蚀是指产线材在介质中的化学反应导致的腐蚀,例如在酸性或碱性环境中产生的腐蚀。
电化学腐蚀则是由于介质与金属表面之间的电化学反应而引起的腐蚀,例如在水中产生的电化学腐蚀。
3. 高速无扭轧机产线材的抗腐蚀性能评价方法为了评价高速无扭轧机产线材的抗腐蚀性能,常用的方法包括重量损失法、电化学方法和物理测试法。
重量损失法是通过浸泡产线材于特定介质中,并根据其重量的变化来评估腐蚀程度。
电化学方法主要通过测定材料电位、电流和电阻等参数来分析材料的腐蚀行为。
物理测试法包括金相分析、扫描电子显微镜和X射线衍射等,用于观察和分析产线材表面的结构和形貌变化。
4. 高速无扭轧机产线材的常见腐蚀防护技术4.1 表面涂层技术表面涂层技术是目前应用最广泛的防腐技术之一。
常用的涂层材料包括有机涂层和无机涂层。
有机涂层主要通过形成一层保护膜来阻止氧、水和化学物质对产线材的侵蚀。
无机涂层则是通过沉积一层氧化物或者磷酸盐等化合物在产线材表面,形成一层保护层来提高抗腐蚀性能。
4.2 阳极保护技术阳极保护技术主要利用自然电位差或外加电流,将产线材的表面变成阳极,形成一层保护层,从而减少腐蚀情况。
同时可以通过选择合适的阳极材料,提高产线材的抗腐蚀性能。
国产高速线材精轧机组综合改进
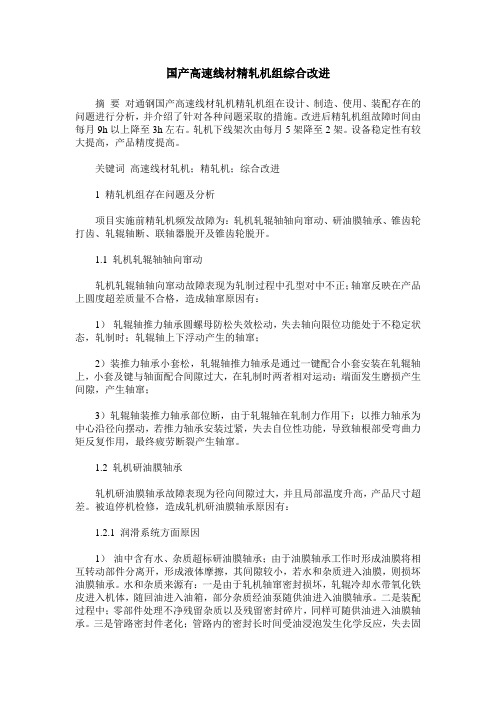
国产高速线材精轧机组综合改进摘要对通钢国产高速线材轧机精轧机组在设计、制造、使用、装配存在的问题进行分析,并介绍了针对各种问题采取的措施。
改进后精轧机组故障时间由每月9h以上降至3h左右。
轧机下线架次由每月5架降至2架。
设备稳定性有较大提高,产品精度提高。
关键词高速线材轧机;精轧机;综合改进1 精轧机组存在问题及分析项目实施前精轧机频发故障为:轧机轧辊轴轴向窜动、研油膜轴承、锥齿轮打齿、轧辊轴断、联轴器脱开及锥齿轮脱开。
1.1 轧机轧辊轴轴向窜动轧机轧辊轴轴向窜动故障表现为轧制过程中孔型对中不正;轴窜反映在产品上圆度超差质量不合格,造成轴窜原因有:1)轧辊轴推力轴承圆螺母防松失效松动,失去轴向限位功能处于不稳定状态,轧制时;轧辊轴上下浮动产生的轴窜;2)装推力轴承小套松,轧辊轴推力轴承是通过一键配合小套安装在轧辊轴上,小套及键与轴面配合间隙过大,在轧制时两者相对运动;端面发生磨损产生间隙,产生轴窜;3)轧辊轴装推力轴承部位断,由于轧辊轴在轧制力作用下;以推力轴承为中心沿径向摆动,若推力轴承安装过紧,失去自位性功能,导致轴根部受弯曲力矩反复作用,最终疲劳断裂产生轴窜。
1.2 轧机研油膜轴承轧机研油膜轴承故障表现为径向间隙过大,并且局部温度升高,产品尺寸超差。
被迫停机检修,造成轧机研油膜轴承原因有:1.2.1 润滑系统方面原因1)油中含有水、杂质超标研油膜轴承;由于油膜轴承工作时形成油膜将相互转动部件分离开,形成液体摩擦,其间隙较小,若水和杂质进入油膜,则损坏油膜轴承。
水和杂质来源有:一是由于轧机轴窜密封损坏,轧辊冷却水带氧化铁皮进入机体,随回油进入油箱,部分杂质经油泵随供油进入油膜轴承。
二是装配过程中;零部件处理不净残留杂质以及残留密封碎片,同样可随供油进入油膜轴承。
三是管路密封件老化;管路内的密封长时间受油浸泡发生化学反应,失去固有特性变质脱落,脱落密封杂质进入油膜轴承或阻塞油路。
杂质、水分、空气没有时间排除,使之随润滑油被送到润滑点造成损害。
- 1、下载文档前请自行甄别文档内容的完整性,平台不提供额外的编辑、内容补充、找答案等附加服务。
- 2、"仅部分预览"的文档,不可在线预览部分如存在完整性等问题,可反馈申请退款(可完整预览的文档不适用该条件!)。
- 3、如文档侵犯您的权益,请联系客服反馈,我们会尽快为您处理(人工客服工作时间:9:00-18:30)。
高线无扭线材精轧机组(BGV)精密维修实践
摘要宝钢集团八钢股份有限责任公司棒线轧钢厂高线机组,高速无扭线材精轧机组维修实践进行了总结,对装配技术要点进行了论述,阐述了螺旋锥齿轮、油膜轴承、锥箱、辊箱、圆柱斜齿轮、轴向密封及轧辊装配的技术要求,对精轧机维修工作具有指导作用。
关键词高速线材;精轧机;装配调整
中图分类号TG335 文献标识码 A 文章编号1673-9671-(2012)071-0158-01
1 概述
宝钢集团八钢股份有限责任公司棒线轧钢厂高线机组建成于2000年,设计产量40万吨,2003年顺利达产,现年产量达到72万t。
其主线设备采用意大利达涅利公司研制的侧交45°无扭高速轧机(BGV)及减定径机(TMB)8+4机组,现成品线速度为115 m/s。
2 精轧机结构特点与工作原理
45°无扭高速线材精轧机组由8个机架组成。
其结构为悬臂小辊径,轧辊直径1~4架Φ200mm,5~8架Φ165 mm。
每对轧辊轴线与水平成45°角布置。
相邻机架两对轧辊轴线互成90°交角,轧件在轧制中为无扭轧制。
3 锥齿轮的装配调整
纵轴锥齿轮靠增减两端轴承端盖的垫片来调节它的位置,使螺旋锥齿轮副的齿侧间隙满足以保证齿侧间隙0.12 mm~0.22 mm,
齿接触面积高度方向和长度方向均不少于70%。
这里要注意在装配时,一般通过研磨图一中7222轴承间的隔圈,让装有纵轴锥齿轮的纵轴朝锥齿轮小头方向(与轧制方向相同)留有
0.108 mm~0.132 mm的间隙量,以减缓轧制咬钢时的瞬时冲击力。
4 油膜轴承及滚动轴承的安装
4.1 油膜轴承安装
①转轴和轧辊齿轮轴主要的径向力在动压油膜轴承上,其轴向力由滚动轴承支承。
在压力作用下,油膜轴承可能发生折皱现象,还可能在轴承外表面和偏心套内孔之间发生粘连,为了减少这种现象的发生,在装配前可通过加热偏心套、冷冻油膜轴承来减少过盈量。
安装油膜轴承时应用特殊的安装工具将偏心套加热120℃,同时将轴瓦置于干冰或液态氮中冷却至-80℃。
将偏心套放置在装配台上,将两半轴瓦按油膜轴承装配图图示位置放好,注意应确保油孔对准,两半轴瓦分隔线与偏心套的刻线对正。
②油膜轴承油楔应在负荷区处侧,油楔位置依靠一螺钉固定定位,螺栓的螺纹应涂抹螺栓紧固胶保证螺栓不出现松动。
同时,注意固定螺钉的端部不能压紧油膜轴承,保证油膜轴承仍有约±7度转角。
③每架轧机设有两条给油管,一条润滑油送到轧机的油膜轴承中去,另一条润滑油送到轧机的齿轮啮合点,轧机内各输油管应保证固定良好,以防止轧机振动等原因使油嘴偏离轴承或齿轮润滑点。
进油膜轴承的滤油精度应小于10 μm,到达轧辊箱油膜轴承的润滑油压力应为0.13 MPa~0.14 MPa,过低的油压,容易出现油膜轴承烧坏事故。
4.2 锥齿轮箱滚动轴承安装
精轧机锥齿轮箱均采用瑞典SKF公司的高速轴承。
滚动轴承与轴装配采用
温差法。
装配后其间隙值应满足下列要求:纵轴:圆柱滚子轴承的径向间隙:0.076 mm-0.114 mm角接触球轴承的轴向间隙:0.050 mm-0.089 mm锥齿轮轴:靠近锥齿轮端圆柱滚子轴承的径向间隙:0.038 mm-0.089 mm,靠近轧辊端圆柱滚子轴承的径向间隙:0.025 mm-0.076 mm,角接触球轴承的轴向间隙:
0.025 mm-0.063 mm圆螺母的松动和脱落,会造成轴承损坏事故,装配时,防松压板两端的固定螺钉应串铁丝,以防松。
5 辊箱的安装及斜齿轮传动
5.1 辊箱的安装
在装配时先将辊箱箱体安装在专业翻转底座上,再将偏心套垂直插入精轧机箱座安装。
辊箱立轴一端定位在箱座内的铜锥套内,另一端定位在中间板上的铜锥套内。
两根轧辊绕两根立轴分别转动,可调节轧辊辊缝。
由于辊箱立轴靠两端锥形铜套定位,锥形结合面处的松紧程度就显得很重要。
太紧,立轴转不动,无法调整轧辊辊缝,太松,辊箱立轴与机箱支座端面的垂直度及两根立轴的平行度就难以保证要求,使斜齿轮齿面接触不良。
辊箱就位后,合上中间板并紧固,这时就可以用百分表检测立轴的轴向间隙,这个轴向间隙一般在0.108 mm~0.115 mm。
5.2 斜齿轮传动
圆柱斜齿轮啮合情况不符合要求,传动冲击振动大,容易折齿,斜齿轮传动啮合情况的检测标准:齿侧隙在0.121 mm-0.216 mm之间,齿接触面积高度方向不小于60%,长度方向不小于70%。
齿侧隙用压铅丝法检测,齿接触面积用涂红丹粉法进行检测。
①检查斜齿轮轴等零件的加工质量,零备件的尺寸公差和形位公差是否符合图纸的技术要求。
②立轴两端定位铜套处结合的松紧度再调整,微调,直至斜齿轮啮合情况理想为止。
6 轴向密封,辊环安装及辊缝调整
6.1 轴向密封
精轧机辊箱轧辊轴端密封的工况条件比辊箱的安装较为苛刻:轴端密封的安装侧必须保证封水,防止冷却水和杂物进入锥箱污染润滑油;另一侧封油,防止锥箱的润滑油泄漏,造成润滑油的浪费。
密封面与轧机轴端最大摆动Smax为±0.13 mm,密封工作面线速度最高Vmax为9 6m/s,要保证轴向密封一定的使用寿命,密封件选用的材料和合理的结构是密封效果关键。
6.2 辊环的安装
轧辊辊环安装前用干净白布或专用清洁纸彻底擦干净配合处的轴颈,锥套内外表面和辊环内表面。
辊环9与辊轴7采用中间锥套8的无键联接。
为避免错辊轧制,上下辊环的孔形应对正。
在装配辊箱的过程中,如图2所示,研磨好调整垫3的厚度,保证(图3)锥箱传动纵轴中心与辊环内侧面的距离为981.15±011 mm(Φ200机架),893±011 mm(Φ165机架)这是确保上下轧辊端面对正的关键。
发生轻微错辊,也可以在外挡环3与辊环9之间垫薄铜皮进行校正。
6.3 辊缝调整
辊缝调整是通过丝杆机构调整,转动调整杆会改变两个辊轴偏心套之间的偏心量。
每转90°两轧辊张开或靠拢0.02 mm,辊缝调整丝杆在中间轴承座位置设计尺寸较小,是薄弱点,特别是在使用小辊径时常会断裂(辊径越小丝杠所承受冲击力矩越大)。
我们在总结经验后将丝杠此处尺寸放大,两端定位压板柱销放大,避免了重复故障的发生。
综上所述:精轧机的装配维修是一项劳动强度大、技术要求高的工作,它要
求员工具有高度的工作责任心和熟练的业务技术。
充分挖掘设备潜能,提高线材生产作业率,实现高效化生产,搞好精轧机管理是关键。
参考文献
[1]精轧机维护使用说明书[M].哈飞工业机电设备制造公司,2009,01.
[2]刘秀芹.高线精轧机油膜轴承安装使用探讨[J].润滑与密封,2005,05.。