车架横梁法计算
12m客车车架结构设计及分析
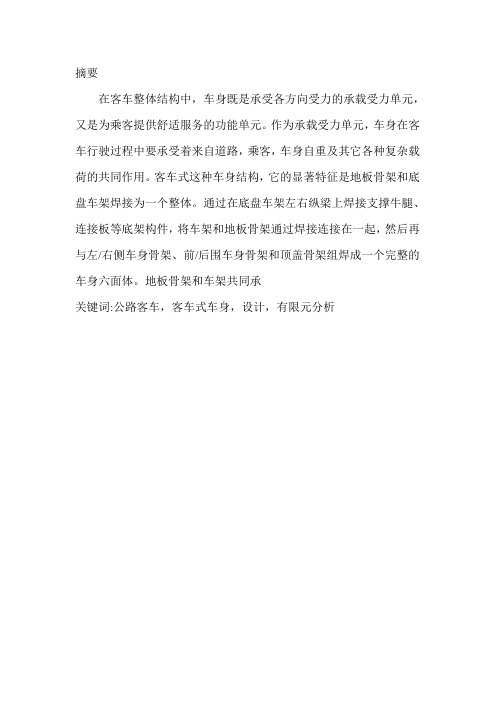
摘要在客车整体结构中,车身既是承受各方向受力的承载受力单元,又是为乘客提供舒适服务的功能单元。
作为承载受力单元,车身在客车行驶过程中要承受着来自道路,乘客,车身自重及其它各种复杂载荷的共同作用。
客车式这种车身结构,它的显著特征是地板骨架和底盘车架焊接为一个整体。
通过在底盘车架左右纵梁上焊接支撑牛腿、连接板等底架构件,将车架和地板骨架通过焊接连接在一起,然后再与左/右侧车身骨架、前/后围车身骨架和顶盖骨架组焊成一个完整的车身六面体。
地板骨架和车架共同承关键词:公路客车,客车式车身,设计,有限元分析AbstractIn the bus structure, the body is bearing unit and functional unit. As bearingunit, body in the passenger car driving to pressure from roads and other variouscomplex load role. Car many important assembly components are body for thecarrier, so the body in the whole bus system occupies very important position, thestrength and stiffness of the direct influence on the bus service life and security.As a functional unit, the body should provide the driver with convenient workingenvironment, for the crew to provide comfortable riding environment, protectthem from bus when exercising vibration, noise, exhaust gas invasion and outside harsh climate; in the traffic accident, reliable body structure and occupant protection system helps to reduce the crew and pedestrian injuries caused by. Inrecent years, with the development of society and the improvement of economicKey Words:analysis Coach bus, Semi-integral body, Design, Finite element目录第1章绪论 (4)1.1研究背景 (4)1.2研究意义 (5)1.3 UG技术的发展概况 (5)1.4客车车身技术的研究现状 (6)1.5本论文的研究内容及目标 (7)第2章车身的总体设计 (8)2.1车身的总体设计方案 (8)2.2车辆布置形式 (9)2.3车身主要尺寸的确定 (9)2.4车辆质量参数的确定 (10)第3章客车车身UG建模 (12)3.1客车式长途客车车身底架建模 (13)3.2左侧骨架总成建模 (18)第四章车身结构有限元分析 (19)4.1车身模型的简化 (19)4.2车辆载荷工况分析 (19)4.2.1水平弯曲工况分析 (19)4.2.2紧急制动工况分析 (22)4.2.3极限扭转工况(右前轮悬空)分析 (24)4.2.4极限扭转工况(左前轮悬空)分析 (25)第5章 (27)论文总结 (27)第1章绪论1.1研究背景中国客车行业从上世纪70年代中期开始起步,经过40年的不断发展和国家汽车产业重点改造,通过引进国外先进技术和合资汽车企业,目前拥有自主研发新车型的能力。
车架受力分析基础

车架受力分析基础一、对车架整车的受力要求二、车架的受力情况具体分析三、车架的结构分析1.车架的基本结构形式2.车架宽度的确定3.纵梁的形式、主参数的选择4.车架的横梁及结构形式5.车架的连接方式及特点6.载货车辆采用铆接车架的优点四、车架的计算1.简单强度计算分析2.简单刚度计算分析3.CAE综合分析五、附表2000年7月1日一、整车对车架的要求车架是整车各总成的安装基体,对它有以下要求:1.有足够的强度。
要求受复杂的各种载荷而不破坏。
要有足够的疲劳强度,在大修里程内不发生疲劳破坏。
2.要有足够的弯曲刚度。
保证整车在复杂的受力条件下,固定在车架上的各总成不会因车架的变形而早期损坏或失去正常工作能力。
3.要有足够的扭转刚度。
当汽车行使在不平的路面上时,为了保证汽车对路面不平度的适应性,提高汽车的平顺性和通过能力,要求车架具有合适的扭转刚度。
对载货汽车,具体要求如下:3.1车架前端到驾驶室后围这一段车架的扭转刚度较高,因为这一段装有前悬架和方向机,如刚度弱而使车架产生扭转变形,势必会影响转向几何特性而导致操纵稳定性变坏。
对独立悬架的车型这一点很重要。
3.2包括后悬架在内的车架后部一段的扭转刚度也应较高,防止由于车架产生变形而影响轴转向,侧倾稳定性等。
3.3驾驶室后围到驾驶室前吊耳以前部分车架的刚度应低一些,前后的刚度较高,而大部分的变形都集中在车架中部,还可防止因应力集中而造成局部损坏现象。
4.尽量减轻质量,按等强度要求设计。
二、车架的受力情况分析1.垂直静载荷:车身、车架的自重、装在车架上个总成的载重和有效载荷(乘员和货物),该载荷使车架产生弯曲变形。
2.对称垂直动载荷:车辆在水平道路上高速行使时产生,其值取决于垂直静载荷和加速度,使车架产生弯曲变形。
3.斜对称动载荷在不平道路上行使时产生的。
前后车轮不在同一平面上,车架和车身一起歪斜,使车架发生扭转变形。
其大小与道路情况,车身、车架及车架的刚度有关。
钢结构设计吊车梁计算
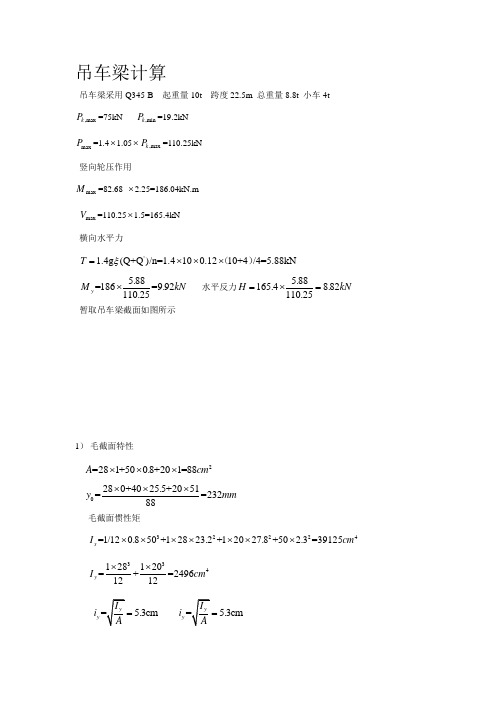
吊车梁计算吊车梁采用Q345-B 起重量10t 跨度22.5m 总重量8.8t 小车4t ,max k P =75kN ,min k P =19.2kNmax P =1.4⨯1.05⨯,max k P =110.25kN竖向轮压作用max M =82.68 ⨯2.25=186.04kN.mmax V =110.25⨯1.5=165.4kN横向水平力'1.4g (Q+Q )/n=1.4100.1210+4/4=5.88kN T ξ=⨯⨯⨯()5.88=186=9.92110.25y M kN ⨯ 水平反力 5.88165.48.82110.25H kN =⨯= 暂取吊车梁截面如图所示1) 毛截面特性2=281+500.8+201=88A cm ⨯⨯⨯0280+4025.5+2051==23288y mm ⨯⨯⨯ 毛截面惯性矩32224=1/120.850+12823.2+12027.8+50 2.3=39125x I cm ⨯⨯⨯⨯⨯⨯⨯334128120=+=24961212y I cm ⨯⨯5.3cm y i = 5.3cm y i =净截面特性2=(28-22)1+500.8+201=84n A cm ⨯⨯⨯⨯形心位置 1=y (40⨯25.5+20⨯51)/84=243mm净截面惯性矩32224=1/120.850+40 1.2+12424.3+2026.7=36820nx I cm ⨯⨯⨯⨯⨯⨯3==148524.8nx nx I W cm 上 3==135427.2nx nx I W cm 下 3x S =28124.3+23.80.823.8/2=907cm ⨯⨯⨯⨯对上翼缘 324128=-1272=163312ny I cm ⨯⨯⨯⨯ =ny W 3=116.7cm 14ny I 毛截面 33128/12==130.714y W cm ⨯ 2)强度验算①上翼缘最大正应力6622max 33ny n 186109.9210=+=+=210.26N/mm <310N/mm 148510116.710y x M M W W σ⨯⨯⨯⨯上 下翼缘正应力 max n =x M W σ下=6318610=137135410⨯⨯.422N/mm <310N/mm ②剪应力 33max 4165.41090710===50.936820810x w V S I t τ⨯⨯⨯⨯⨯22N/mm <180N/mm ③腹板局部压应力=+5+250+510+2130360mm z y R l a h h =⨯⨯=31.0110.2510=38.38360c w z P t l ψσ⨯⨯==⨯22N/mm <310N/mm3)整体稳定验算1116000100.412280520l t b h ξ⨯===<⨯ 取0.730.180.80b βξ=+= 6000113.253y mm λ== h=520mm1121633/24690.65b I I I α===+ 0.8(21)0.248b b ηα=-= 2345/y f N mm =222234320235=+]43208800520235 =0.8+0248]0.770.6113.2148510345b b b y X yAh y W f ϕβλ⨯⨯⨯=>⨯ ' 1.070.282/0.70b b ϕϕ=-=66'33186.0109.9210 5.6560.7165110130.7101000yXb y M M l mm W σϕ⨯⨯=+=+=<=⨯⨯⨯ 4)刚度验算 挠度 2622kx 54186.04 1.05 1.4106000=236.8310/mm 1010 2.06103912510X M l N EI υ÷÷⨯⨯==<⨯⨯⨯⨯ 满足要求 吊车为A1~A5 疲劳可不进行验算5)加劲肋0wh t 可按构造配量0.50h 02a h ≤≤ 求间距 a =1.20h =600mm界面尺寸外伸长度 0/30+40=57s b h mm ≥ 厚度s t ≥/15s b =3.8m 采用80⨯8mm支座反力 R=165.4KN计算截面面积A=18⨯1.2+15⨯0.8=33.62cm绕腹板中线的截面惯性矩 3341.218 1.50.8+583.81212I cm ⨯⨯==4.17cm i = 50=12.04.17λ= 查表ϕ=0.989 322165.41049.8310/0.9893360N N mm f N mm A ϕ⨯==<=⨯ 6) 焊缝计算上翼缘与腹板连接焊缝=1.8f h mm= 取f h =6mm下翼缘与腹板连接焊缝3max 1.2 1.2165.410 1.771.4 1.4500160f w w t R h mml f ⨯⨯===⨯⨯ 同样取f h =6mm 吊车梁计算结束。
轻型货车车架设计讲解

汽车车身结构与设计课程设计题目轻型货车车架设计班级M11车辆工程姓名刘符利学号 **********指导教师智淑亚2014年12摘要本设计课题是关于轻型载货汽车的车架设计。
所设计的车架结构形式是前后等宽的边梁式车架,其中纵梁和横梁的截面形状都采用槽型,纵梁与横梁通过焊接连接。
本说明书涉及了现阶段载货汽车技术的发展趋势,以及国内外载货汽车车架的发展状。
关键词:轻型货车、车架、设计1 绪论1.1概述汽车车架是整个汽车的基体,是将汽车的主要总成和部件连接成汽车整体的金属构架,对于这种金属构架式车架,生产厂家在生产设计时应考虑结构合理,生产工艺规范,要采取一切切实可行的措施消除工艺缺陷,保证它在各种复杂的受力情况下不至于被破坏。
车架作为汽车的承载基体,为货车、中型及以下的客车、中高级和高级轿车所采用,支撑着发动机离合器、变速器、转向器、非承载式车身和货箱等所有簧上质量的有关机件,承受着传给它的各种力和力矩。
为此,车架应有足够的弯曲刚度,以使装在其上的有关机构之间的相对位置在汽车行驶过程中保持不变并使车身的变形最小;车架也应有足够的强度,以保证其有足够的可靠性与寿命,纵梁等主要零件在使用期内不应有严重变形和开裂。
车架刚度不足会引起振动和噪声,也使汽车的乘坐舒适性、操纵稳定性及某些机件的可靠性下降。
本说明书只是叙述非承载式车身结构形式中单独的车架系统。
承载式汽车,前、后悬架装置,发动机及变速器等传动系部件施加的作用力均由车架承受,所以,车架总成的刚性、强度及振动特性等几乎完全决定了车辆整体的强度、刚度和振动特性。
设计时在确保车架总成性能的同时,还应对车架性能和匹配性进行认真的研究。
车架结构很多都是用电弧焊焊接而成,容易产生焊接变形。
在设计方面对精度有要求的部位不得出现集中焊接,或者从部件结构方面下工夫,尽量确保各个总成的精度。
另外,与其他焊接方法相对比,采用电弧焊的话,后端部容易出现比较大的缺口,出现应力集中现象。
梁格法 汽车荷载
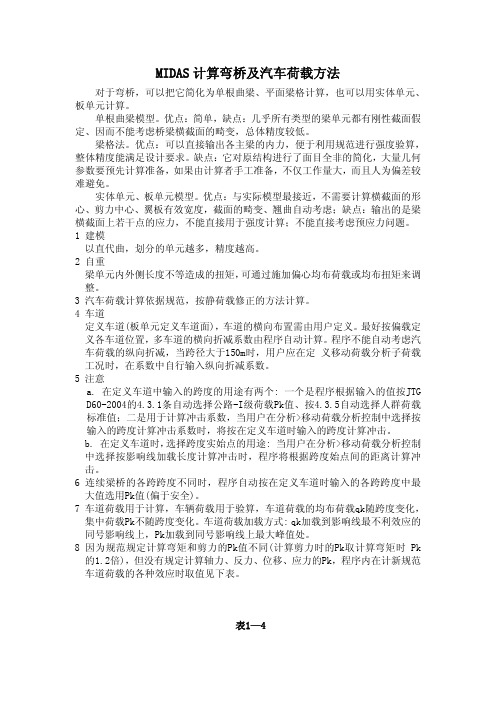
Pk
Pk
-
Pk
扭转
-
Pk
-
-
Pk
应力
法向
组合
-
Pk
Pk
-
Pk
应力
主应Pkຫໍສະໝຸດ PkPkPk
Pk
力
其他
Pk
Pk
Pk
Pk
Pk
9 汽车制动力 程序目前不提供自动计算功能。 建议: a. 可按下列步骤加载: 首先进行一般的移动荷载分析,在后处理利用 移 动 荷 载 追 踪 器 功 能 获 得 某 项 结 果 的 最 不 利 加 载 位 置 , 然 后 通 过 按 JTG D60-2004的4.3.6条计算制动力,用梁单元荷载中集中荷载方式(局部坐标系) 加载到最不利加载位置。 b. 注意制动力不考虑冲击的影响。
实体单元、板单元模型。优点:与实际模型最接近,不需要计算横截面的形 心、剪力中心、翼板有效宽度,截面的畸变、翘曲自动考虑;缺点:输出的是梁 横截面上若干点的应力,不能直接用于强度计算;不能直接考虑预应力问题。 1 建模
以直代曲,划分的单元越多,精度越高。 2 自重
梁单元内外侧长度不等造成的扭矩,可通过施加偏心均布荷载或均布扭矩来调 整。 3 汽车荷载计算依据规范,按静荷载修正的方法计算。 4 车道 定义车道(板单元定义车道面),车道的横向布置需由用户定义。最好按偏载定 义各车道位置,多车道的横向折减系数由程序自动计算。程序不能自动考虑汽 车荷载的纵向折减,当跨径大于150m时,用户应在定 义移动荷载分析子荷载 工况时,在系数中自行输入纵向折减系数。 5 注意 a. 在定义车道中输入的跨度的用途有两个: 一个是程序根据输入的值按JTG D60-2004的4.3.1条自动选择公路-I级荷载Pk值、按4.3.5自动选择人群荷载 标准值;二是用于计算冲击系数,当用户在分析>移动荷载分析控制中选择按 输入的跨度计算冲击系数时,将按在定义车道时输入的跨度计算冲击。 b. 在定义车道时,选择跨度实始点的用途: 当用户在分析>移动荷载分析控制 中选择按影响线加载长度计算冲击时,程序将根据跨度始点间的距离计算冲 击。 6 连续梁桥的各跨跨度不同时,程序自动按在定义车道时输入的各跨跨度中最 大值选用Pk值(偏于安全)。 7 车道荷载用于计算,车辆荷载用于验算,车道荷载的均布荷载qk随跨度变化, 集中荷载Pk不随跨度变化。车道荷载加载方式: qk加载到影响线最不利效应的 同号影响线上,Pk加载到同号影响线上最大峰值处。 8 因为规范规定计算弯矩和剪力的Pk值不同(计算剪力时的Pk取计算弯矩时 Pk 的1.2倍),但没有规定计算轴力、反力、位移、应力的Pk,程序内在计新规范 车道荷载的各种效应时取值见下表。
最新汽车吊机支腿反力计算及梁板受力分析资料
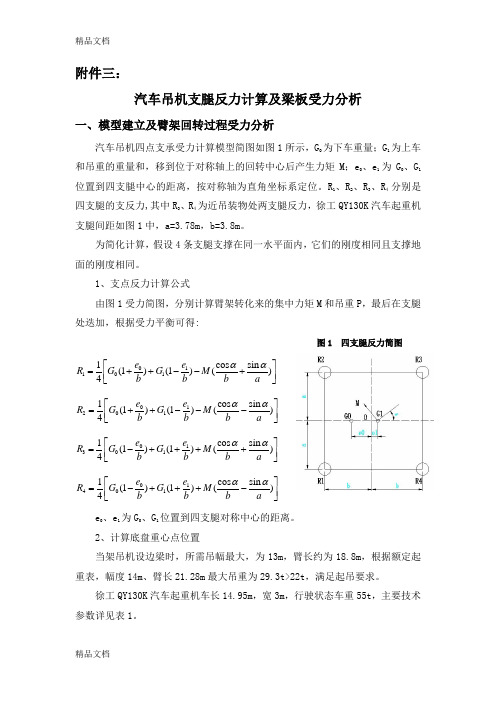
附件三:汽车吊机支腿反力计算及梁板受力分析一、模型建立及臂架回转过程受力分析汽车吊机四点支承受力计算模型简图如图1所示,G 0为下车重量;G 1为上车和吊重的重量和,移到位于对称轴上的回转中心后产生力矩M ;e 0、e 1为G 0、G 1位置到四支腿中心的距离,按对称轴为直角坐标系定位。
R 1、R 2、R 3、R 4分别是四支腿的支反力,其中R 3、R 4为近吊装物处两支腿反力,徐工QY130K 汽车起重机支腿间距如图1中,a=3.78m ,b=3.8m 。
为简化计算,假设4条支腿支撑在同一水平面内,它们的刚度相同且支撑地面的刚度相同。
1、支点反力计算公式由图1受力简图,分别计算臂架转化来的集中力矩M 和吊重P ,最后在支腿处迭加,根据受力平衡可得:图1 四支腿反力简图011011cos sin (1)(1)()4e e R G G M b b b a αα⎡⎤=++--+⎢⎥⎣⎦012011cos sin (1)(1)()4e e R G G M b b b a αα⎡⎤=++---⎢⎥⎣⎦ 013011cos sin (1)(1)()4e e R G G M b b b a αα⎡⎤=-++++⎢⎥⎣⎦ 014011cos sin (1)(1)()4e e R G G M b b b a αα⎡⎤=-+++-⎢⎥⎣⎦e 0、e 1为G 0、G 1位置到四支腿对称中心的距离。
2、计算底盘重心点位置当架吊机设边梁时,所需吊幅最大,为13m ,臂长约为18.8m ,根据额定起重表,幅度14m 、臂长21.28m 最大吊重为29.3t>22t ,满足起吊要求。
徐工QY130K 汽车起重机车长14.95m ,宽3m ,行驶状态车重55t ,主要技术参数详见表1。
表1 徐工QY130K汽车起重机主要参数类别项目单位参数尺寸参数整机全长mm 14950 整机全宽mm 3000 整机全高mm 3950轴距第一、二mm1420第二、三mm2420第三、四mm1875第四、五第五、六mm1400重量参数行驶状态整机自重55000kg 9100/9100 三/四轴kg五/六轴12700/9700支腿距离纵向m 7.56横向m 7.6 转台尾部回转半径(平衡重)mm 4600吊机支腿纵向距离7.56m,横向距离7.6m,支腿箱体位于2桥和3桥之间以及车架后端,工作时配重38000kg。
中华人民共和国国家标准汽车车架修理技术条件
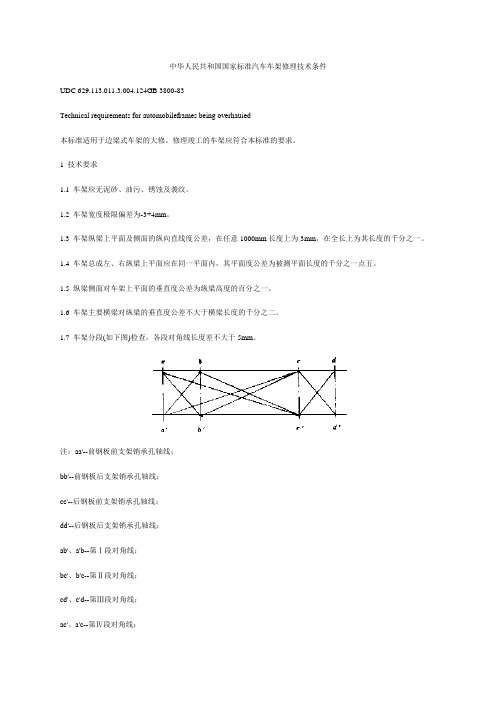
中华人民共和国国家标准汽车车架修理技术条件UDC 629.113.011.3.004.124GB 3800-83Technical requirements for automobileframes being overhauied本标准适用于边梁式车架的大修。
修理竣工的车架应符合本标准的要求。
1 技术要求1.1 车架应无泥砂、油污、锈蚀及袭纹。
1.2 车架宽度极限偏差为-3+4mm。
1.3 车架纵梁上平面及侧面的纵向直线度公差,在任意1000mm长度上为3mm,在全长上为其长度的千分之一。
1.4 车架总成左、右纵梁上平面应在同一平面内,其平面度公差为被测平面长度的千分之一点五。
1.5 纵梁侧面对车架上平面的垂直度公差为纵梁高度的百分之一。
1.6 车架主要横梁对纵梁的垂直度公差不大于横梁长度的千分之二。
1.7 车架分段(如下图)检查,各段对角线长度差不大于5mm。
注:aa'--前钢板前支架销承孔轴线;bb'--前钢板后支架销承孔轴线;cc'--后钢板前支架销承孔轴线;dd'--后钢板后支架销承孔轴线;ab'、a'b--第Ⅰ段对角线;bc'、b'c--第Ⅱ段对角线;cd'、c'd--第Ⅲ段对角线;ac'、a'c--第Ⅳ段对角线;1.8 左右钢板弹簧固定支架销孔应同轴,其同轴度公差为φ2.0mm(按GB 1958-80《形状和位置公差检测规定》检测方法5-1进行检测)。
前后固定支架销孔轴线间的距离左、右相差:轴距在4000mm及其以下的应不大于2mm,轴距在4000mm以上的应不大于3mm。
1.9 车架的焊接应符合焊接规范。
焊缝应平整、光滑、无焊瘤、弧坑,咬边深度不大于0.5mm,咬边长度不大于焊缝长度的百分之十五,并不得有气孔、夹渣等缺陷。
1.10 车架挖补或截修的焊缝方向,除特殊车架外,不允许与棱线垂直、重叠;焊缝及其周围基体金属上,不应有裂纹。
桥式起重机大小车设计计算

起重机小车设计计算1.小车横梁设计计算P1 P2P3P41╒ 2╒ 3╒ 4╒1╘ 2╘ 3╘ 4╘图1 小车横梁尺寸图额定起重量:Q=500 000N小车横梁截面惯性矩:I1=I4=3。
96×108mm4I 2=I3=7。
32×108mm4小车横梁截面中性轴以上截面静矩:S1=S4=1。
26×106mm3S 2=S3=1。
73×106mm3材料弹性模量:E=2。
1×105N/mm2y 2=y3=329mm 滑轮组倍率:m=5P=P1=P2=P3=P4=)1(m205.1-mQ=2.1×105NM 2=M3=Pa=1。
89×108N.mmσmax =σ2=σ3=y2M=84.95MPa≤[σ1]=140MPaτ1=τ4=tISP.2.11=20。
9MPa≤[τI]=3][1σ=80MPaτ2=τ3=t.2.12ISP=15。
47MPa≤[τI]=3][1σ=80MPa发生应力集中的截面应力:σb2=σb3=12.2t dp=13.2t dP=54.69MPa≤[σS/4]=[235/4]=58.75MPa刚度符合要求。
2.小车端梁设计计算图2 小车端梁尺寸图G X =20 000N GX─小车自重的1/2(t)小车端梁截面惯性矩:I1=2.1×107mm4; I2=2。
1×108mm4; I3=3.32×108mm4; I5=2。
09×108mm4; I6=9。
07×106mm4y 2=174mm; y3=222mm; y5=174mm小车端梁截面静矩:S1=1.88×105mm3; S2=8。
27×105mm3; S3=1.24×106mm3; S5=8。
27×105mm3; S6=1.1×105mm3R 3=mQ205.1=52500NR 5=mQm2)1(05.1⨯-⨯=210 000NR 1=2XG+babR-3+bcabR--5=104 028NR 6=2XG+baR3+bcaR+5=104 972NM 2=21bR—)(23aR b-=34 699 000N.mmM3=R。