自卸侧翻计算分析
后倾式自卸半挂车侧翻原因的探讨
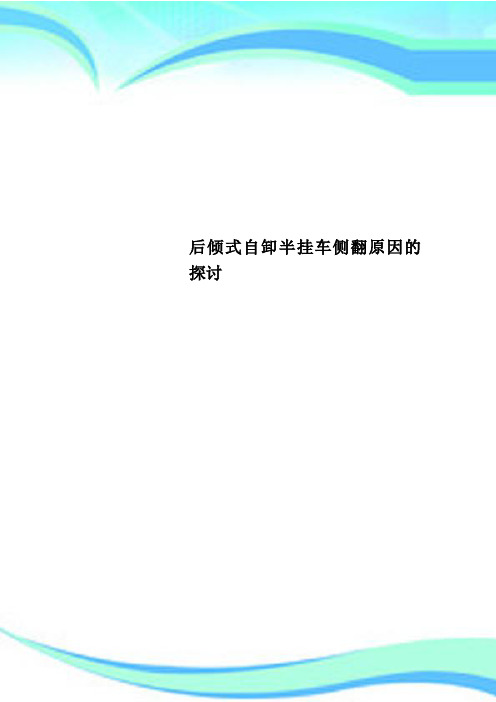
后倾式自卸半挂车侧翻原因的探讨————————————————————————————————作者:————————————————————————————————日期:后倾式自卸半挂车侧翻原因的探讨-汽车后倾式自卸半挂车侧翻原因的探讨国家工程机械质量监督检验中心张晓惠高晶摘要:简要介绍了后倾式自卸半挂车的结构,分析出后倾式自卸半挂车发生侧翻的原因,通过实际案例,提出防止后倾式自卸半挂车发生倾翻的措施。
随着我国经济的快速发展,自卸汽车行业朝着中大吨位发展,特别是近几年来自卸半挂车的自身优势,销量逐渐上升。
其中,自卸半挂车又分侧卸和后卸两种卸货方式。
因后倾式自卸半挂车近年来在卸货时倾翻事故时有发生,因此为了避免类似事故的发生,现就后倾式自卸半挂车卸货时侧翻的原因进行探讨,便于制造厂家在使用说明书上对用户铭示,以避免类似的事故发生,造成不必要的损失。
后倾式自卸半挂车的构成后倾式自卸半挂车主要由牵引车和半挂车组成,由鞍座把主车(牵引车)和半挂车联接在一起,一般是前置复合油缸(倒置,见图1)。
发生侧翻的原因后倾式自卸半挂车卸货侧向倾翻时,一般都发生在半挂车卸货时,且车辆停在不坚实路面或不平整路面上,随着车厢后倾角的增大,货物质心不断提高。
以下几种可能性,使得车辆发生倾翻的可能性加大(见图2,G为半挂车整备质量;a为地面倾角;L为半挂车随动桥轮距;h为质心高度)。
a.用户超载作业;b.装载左右两侧不均匀,特别是载荷质心偏向轮胎较低侧;c.车厢后门锁止机构未能打开;d.轮胎和钢板弹簧变形;e.装有含水量较大的砂料。
当半挂车的质心高度与倾翻线I-I重合时,此时半挂车到达临界点,沿I-I 直线(一级倾翻线)马上产生一级倾翻。
由于惯性,即刻沿II-II直线(二级倾翻线)产生二级倾翻,即牵引车随半挂车一起倾翻(见图3)。
后倾自卸半挂车发生的案例2005年冬季,国家质量监督检验总局顾客投诉中心组织了对青岛某企业生产的×××9400×型自卸半挂车质量鉴定工作,按照中国质量检验和鉴定申请人唐山市路北区人民法院签订的(2005)中检协鉴字第××号《质量鉴定委托书》要求,于2005年12月对该自卸半挂车进行了质量鉴定。
某自卸车型侧翻分析报告

X型自卸车型侧翻分析报告张敏北汽福田汽车股份有限公司长沙汽车厂技术中心CAE分析室长沙410129近年来,自卸车的侧翻己经成为一个重要的安全问题,据统计,自卸车侧翻事故己成为仅次于汽车正面碰撞的严重车辆事故,侧翻稳定性研究引起了人们的重视。
而自卸车由于自身结构因素决定了其整车的质心高度较一般载货车要高,其失稳的危险性也较一般载货车要高。
自卸车特殊的、危害最大的失效形式是卸载时作业失稳自卸汽车按货厢倾卸方向分为后倾卸式和三面倾卸式两种。
倾卸机构是自卸汽车的关键装置,它直接关系到自卸汽车的使用性能及整体布置。
倾卸机构要有很好的动力性,卸料过程平衡、协调,满足结构紧凑、安全可靠的要求由于自卸汽车通常采用的是车架和车厢相分离的结构以及开式车厢,致使自卸汽车车厢在卸货时的刚度较弱,再加上运载货物的物理和化学性质、气候、道路、工作场地的影响,有时在卸载时会出现侧翻现象,发生严重的事故。
根据事故的分析统计,影响汽车侧翻的因素很多,也很复杂。
其中导致事故发生的两个关键因素有:(1)驾驶员对汽车的操纵或者货物装载不良。
(2)道路条件不良。
(3)车辆设计问题。
(4)高速转向因此,自卸汽车的倾翻稳定性是自卸汽车设计及使用过程中的重要研究热点问题。
有必要对侧翻的情况进行分析,计算和试验,以提高自卸车抗侧翻的能力但是,由于自卸车的应用领域限制了其设计研究的范围和规模。
而传统设计大都采用类比法或经验取值法,也限制了产品性能的进一步提高,往往自卸车的作业稳定性试验并不够,己不能适应社会高速发展和对产品安全高性能的要求。
下面就将某自卸车型作为研究对象进行分析,利用CAD,CAE等手段。
1、 某整车参数。
表1 某车型参数2、 静止状态整车为刚性时的侧翻计算2.1 理论分析在不考虑悬架及轮胎弹性变形的情况下,即将整车视为“刚性汽车”的模型。
假设重型汽车在侧翻时尚未发生侧滑,当发生侧翻时其中一个轮胎不受力,轮胎与地面的相对距离迅速增加。
自卸侧翻计算分析ppt课件
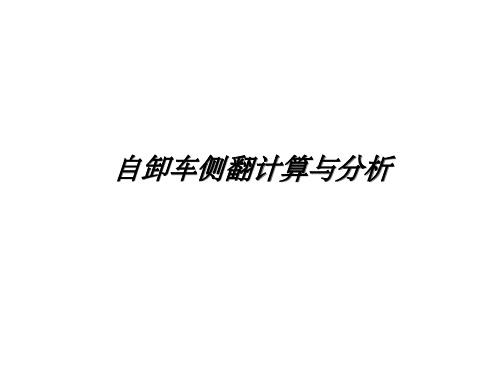
2.1 静止状态整车为刚性时的侧翻计算 (见图2)
在不考虑悬架及轮胎 弹性变形的情况下,即 将整车视为“刚性汽车” 的模型。根据有关资料 可知,一般重型汽车在 侧翻时尚未发生侧滑, 此时的侧翻计算较为简 单,将有关参数代入相 关公式即可算出整 车重心。
图2
H H 1W 1 H 2W 2 W 1W 2
下面结合某具体车型(结构简图见图1,主要参数见表)进行计算分析。
图1
表1
底盘整备质量W 1
上装及货物质量WWW122
底盘质心高度 H1 上装质心高度 H2 整车质心高度 H
车距 B
外轮中心距 B1
板簧中心距 b
板簧刚度 K
7450Kg 40000Kg 800mm 2385mm 2136mm 1820mm 2146mm 1006mm 200Kg/mm
800 7450 3048 28560 7450 28560
2136 ( mm )
tg
B1 2 H
2146 2 2136
26 . 6
式中, 为横向斜坡角度。
2.2 静止状态考虑悬架因素时的侧翻计算(见图3)
当整车停在横向角度为的斜坡上时,由于重力分力的作用,使得左、右悬架受力不
自卸车一般在举升卸货时发生侧翻事
故较多,下面就以举升20 时 ,由于货箱重
心的抬高.计算发生侧翻的坡度 ,如图4
所示.按照一般沙、石、土的自然堆积角
为 45 ,举升 20 时,货箱及货物重心高度
为3048mm。此时整车的重心高度为:
图4
H ' H ' W 2 H 2 ' W 2 ' 8 7 0 4 0 35 0 2 0 4 8 2 8 5 ( 5 m 6 )8 0 m 2
后倾式自卸半挂车侧翻原因的探讨

后倾式自卸半挂车侧翻原因的探讨后倾式自卸半挂车侧翻是指自卸半挂车在运输过程中因其中一种原因而突然倾翻的现象。
这种事故不仅造成物质损失,还可能导致人员伤亡,对交通安全和道路环境造成严重影响。
因此,了解后倾式自卸半挂车侧翻的原因,对于预防和减少此类事故的发生具有重要意义。
在探讨后倾式自卸半挂车侧翻原因之前,首先要了解自卸半挂车的结构。
自卸半挂车主要由车头、拖挂板和汽车底盘组成。
拖挂板由车体、自卸机构和液压卸料系统等组成。
自卸车主要通过液压卸料系统将车体提升至一定角度,然后自动卸料。
一、车辆设计和制造的原因1.结构设计不合理:自卸半挂车的结构设计不合理,例如重心过高、重量分配不均匀等。
2.制造技术不过关:自卸半挂车在制造过程中可能存在材料质量不合格、焊接缺陷等问题,导致在运输过程中发生故障引起侧翻。
二、驾驶员操作不规范和错误1.过速行驶:驾驶员在下坡或转弯时过于快速行驶,导致车辆重心不稳,产生侧翻风险。
2.超载行驶:车辆超载会使车辆的重心加大,稳定性降低,增加侧翻的风险。
3.过度转动卸料:驾驶员在卸料时过度转动车体,使车辆倾斜过大而发生侧翻。
三、道路和环境原因1.道路条件不良:如路面凹凸不平、弯道急转等。
2.环境因素:如强风、路面湿滑等,会增加后倾式自卸半挂车侧翻的风险。
四、维护保养不到位1.制动系统故障:制动系统故障可能导致车辆无法及时停车或制动力不足,增加侧翻的风险。
2.轮胎磨损:轮胎磨损后抓地力降低,减少了车辆的稳定性。
综上所述,后倾式自卸半挂车侧翻的原因涉及到车辆设计和制造的问题、驾驶员操作不规范和错误、道路和环境原因以及维护保养不到位等多个方面。
1.加强车辆结构设计和制造过程的质量管理,保证车辆的稳定性和安全性。
2.加强驾驶员的培训和安全意识教育,确保驾驶员按照规范操作车辆。
3.定期检查和维护车辆,保障车辆的正常运行和安全性能。
4.加强道路维护工作,改善道路条件,提高道路的安全性。
5.建立健全的安全管理制度,加强对自卸半挂车运输的监管和管理。
汽车侧翻加速度计算公式

汽车侧翻加速度计算公式汽车侧翻是指汽车在行驶过程中由于某种原因失去平衡,发生侧翻的现象。
汽车侧翻不仅会造成车辆损坏,还可能导致乘客受伤甚至死亡。
因此,对于汽车侧翻的研究和预防显得尤为重要。
在研究汽车侧翻的过程中,加速度是一个非常重要的参数。
本文将介绍汽车侧翻加速度的计算公式,并探讨其在汽车侧翻研究中的应用。
汽车侧翻加速度的计算公式如下:a = (v^2) / r。
其中,a表示汽车侧翻的加速度,v表示汽车的速度,r表示汽车的半径。
这个公式告诉我们,汽车的侧翻加速度与车速的平方成正比,与车辆的半径成反比。
这意味着,当汽车的速度增加时,汽车侧翻的危险性也会随之增加;而当汽车的半径增加时,汽车侧翻的危险性则会减小。
在实际的汽车侧翻研究中,我们可以利用这个公式来评估不同车辆在不同速度下的侧翻危险性。
通过测量车辆的速度和半径,我们可以计算出汽车侧翻的加速度,从而评估汽车在不同情况下的侧翻风险。
这有助于我们在设计和制造汽车时,更好地考虑汽车侧翻的安全性能,从而减少汽车侧翻事故的发生。
除了在汽车设计和制造中的应用外,汽车侧翻加速度的计算公式还可以在汽车驾驶和行驶过程中的安全评估中发挥作用。
通过测量车辆的速度和半径,驾驶员可以及时了解车辆的侧翻风险,从而采取相应的措施来减少侧翻的可能性。
比如,在高速行驶时,驾驶员可以适当减速或者选择更宽阔的道路来降低侧翻的风险;在转弯时,驾驶员可以选择更大的转弯半径来减小侧翻的危险性。
总的来说,汽车侧翻加速度的计算公式为我们提供了一个重要的工具,可以帮助我们评估汽车在不同情况下的侧翻风险,从而在汽车设计、制造和驾驶过程中更好地预防和减少汽车侧翻事故的发生。
通过进一步的研究和应用,我们可以更好地保障汽车驾驶和乘坐的安全,为汽车行业的发展和社会的进步做出贡献。
工程车侧翻设计方案

工程车侧翻设计方案一、引言现代工程车在建筑、道路施工等行业中扮演着重要的角色。
然而,工程车在运输过程中存在一定的侧翻风险,一旦发生侧翻事故,不仅会造成车辆和货物的损失,还可能导致人员伤亡。
因此,如何有效地预防工程车侧翻事故,保障运输安全,显得尤为重要。
本文将针对工程车侧翻问题,提出相应的设计方案,以期减少侧翻风险,提高运输安全性。
二、侧翻原因分析工程车侧翻是指工程车在运输过程中因侧向力作用而导致车辆倾倒或翻滚。
造成工程车侧翻的原因有多种,主要包括以下几点:1. 载荷失稳:工程车在运输过程中,如果货物的重心位置不稳,或者货物分布不均匀,就会增加车辆侧翻的风险。
2. 高速转弯:在高速转弯时,工程车的侧翻风险会明显增加,尤其是在道路条件较差的情况下。
3. 风力和外部影响:强风或者外部影响,也会对工程车的侧翻安全造成威胁。
4. 车辆设计缺陷:一些工程车本身的设计缺陷,如悬挂系统不稳定、底盘结构强度不足等,也会增加侧翻风险。
综上所述,工程车侧翻风险存在于多个方面,需要综合考虑设计方案。
三、预防措施及设计方案1. 载荷稳定为了预防工程车侧翻事故,首先需要确保货物的重心位置稳定。
可以通过以下设计方案来实现:(1)优化货物布局:在设计货物载荷时,应该合理安排货物的位置,确保货物重心处于车辆的稳定位置。
(2)增加固定设施:在工程车的箱体内部,可以设置一些固定设施,如固定托盘、固定带等,以确保货物在运输过程中不会产生移动。
2. 提升悬挂系统稳定性一些工程车的悬挂系统缺乏稳定性,容易受到外部因素的影响而发生侧翻事故。
因此,在设计方案中,应该考虑如何提升悬挂系统的稳定性。
以下是一些可能的方案:(1)优化悬挂结构:通过对悬挂结构进行优化设计,增加悬挂系统的稳定性。
(2)采用智能控制系统:可以通过智能控制系统来监测车辆悬挂系统的状态,及时调整悬挂系统的工作参数,以确保悬挂系统的稳定性。
3. 预警系统在工程车上安装预警系统,可以提前感知到侧翻风险,采取相应的预防措施。
自卸车设计计算书-3
中设计计算书自卸汽车设计计算书一、整车要求1、用户要求:内控尺寸:6000*2300*1100;总质量:25000Kg;2、技术要求:(1)纵梁:180*70*8/Q345压制件;底板5/Q235,边板3/Q235(2)两纵梁底架,单后开门;3、技术条件;(1)、取钢的弹性模量E=206GPa;(2)、材料的力学性能:见下表(3)、安全系数的选择根据《机械设计手册》(化学工业出版社2002年第四版)第1篇第1-115页表1-1-92,选择安全系数。
S=S1*S2*S3式中:S—安全系数;S1—可靠性参数,为第一参数;S2—重要程度参数,为第二参数;S3—计算精确性参数,为第三参数,统一选为1.25;二、整车计算1、整车侧翻稳定性计算车辆在倾斜行驶时,需要验证它的安全角度。
如右图所示,车辆的重心垂直作用线不能超过轮胎外沿。
否则车辆定要向侧面倾翻。
计算车辆满载的重心:车厢高度1100毫米;副车架高度170毫米;底架高度180毫米底盘高度1150毫米;则:自卸车的承高为1150+170+180=1500;整车满载重心为1500+1100/2=2050所以:满载重心高度2050。
车辆横向度的一半为1250,两线成直角组合,并连接另一端点,构成三角形ABC当线AB垂直于地面(即线BD)时,车辆处于监界状态。
此时,车辆与地面的角度就是倾翻角度。
如右图所示。
角CBA和角A的大小应该一样。
计算可得知:角A最大为为42度,所以,角CBA的最大值为42度。
即车辆的满载倾翻角度为31度;车辆空载的重心高度:1150+170+180=1500即车辆空载的倾翻角度为:40度;2、前后轴荷计算整车总重量G为25000Kg。
自卸车的前后悬1500/1870,轴距4125+1350;经过计算简化,数量如下:上图中,L1为自卸车前悬,1500毫米L2为前后悬间距,4800毫米L3为自卸车后悬,2545毫米列方程式得:FA+FB=G;MA(F)=0;G*(L/2-L1)=FB*L2; G*(L/2-L3)=FA*L2联立解得: FB=15220KgFA=9780Kg前后桥承载比例分别为:前桥:9780/25000=39.12%符合前桥承载30~40%的比例;后桥: 15220/25000=60.88%符合后桥承载60~70%的比例;三、部件的计算1、纵梁计算1)、纵梁安全系数S由于纵梁为卷板成型的焊接件,材料的可靠性较低,选第一参数为1.5:纵梁属于重要件,选第二参数为1.5;由于计算准确度不高,统一选1.25;则纵梁的安全系数S=1.5*1.5*1.25=2.8;2)纵梁的强度计算纵梁180*70*8/Q345,则纵梁的许用应力[σ]= σS /S=345/2.8=123MPa 整车载重量为25000Kg,可以认为上述载荷均布,如下图所示:上图中,L1为自卸车前悬, 1500毫米L2为前后悬间距, 4800毫米L3为自卸车后悬, 2545毫米取重力加速度g=10m/s2则均布载荷 q=25000/2*10/8845=14.13N/mm ;求支反力,如前所得:前桥承载=97800N 后桥承载=152200N 则FA=48900N FB=76100Nb)绘剪力图,如左图所示c)绘弯矩图,如左图所示,并求得最大弯矩在第一个零点以前,x=1500时,弯矩最大,有M1=-1/2*q*L1^2=-15896250 N*mm;在两个零点之间,当剪力=0时,此时的弯矩最大,计算出此时,x=3460,有:M2=FAL2-1/2*q*(L1^2+L2^2+L3^2)=234720000-224434031=10285969 N*mm在后一个零点之后,x=6300时,M3=-1/2*q*L3^2=-45760181 N*mm;由以上可知,当在后一个零点处的弯矩最大,为危险断面,即Mmax=45760181 N*mmd)危险截面计算抗弯截面系数W=(140*450^3-134*430^3)/(6*450) =779097则,危险断面的应力为σ=Mmax/W=4576018/779097=58.73MPa因为 [σ]=123MPa,上述三个断面的应力均小于[σ],所以纵梁在弯曲变形方面是安全的;2)、纵梁稳定性计算自卸车在行驶过程中,免不了要过一些沟沟坎坎,车辆就要上下跳动。
集装箱侧翻自重计算公式
集装箱侧翻自重计算公式在集装箱运输行业中,集装箱侧翻是一个非常严重的安全问题。
侧翻不仅会造成货物损失,还可能导致人员伤亡和环境污染。
因此,对集装箱侧翻的自重进行准确的计算和评估是非常重要的。
本文将介绍集装箱侧翻自重的计算公式,并探讨其在实际运输中的应用。
集装箱侧翻自重计算公式通常包括以下几个方面的因素,集装箱的重量、货物的重量、集装箱的尺寸和结构、集装箱的装载方式、集装箱的悬挂设备等。
下面我们将分别介绍这些因素,并给出相应的计算公式。
首先是集装箱的重量。
集装箱的重量包括集装箱本身的重量和货物的重量。
集装箱本身的重量可以通过集装箱的型号和制造厂家提供的数据来获取。
货物的重量则需要根据实际情况进行测量或估算。
集装箱的重量对侧翻的影响非常大,因此在计算侧翻自重时必须准确考虑这一因素。
其次是集装箱的尺寸和结构。
集装箱的尺寸和结构对其侧翻自重有着直接的影响。
一般来说,集装箱的高度、宽度和长度越大,其侧翻自重就越大。
此外,集装箱的结构也会影响其侧翻自重,比如采用加固结构的集装箱其侧翻自重会相对较小。
再者是集装箱的装载方式。
集装箱的装载方式包括堆叠式装载和侧向装载两种。
堆叠式装载是指将集装箱按照一定的方式堆叠在一起,而侧向装载则是指将货物从集装箱的侧面装载进去。
这两种装载方式对集装箱的侧翻自重有着不同的影响,因此在计算侧翻自重时需要对其进行考虑。
最后是集装箱的悬挂设备。
集装箱的悬挂设备包括吊装钩、吊装索等。
这些设备对集装箱的侧翻自重也有着一定的影响。
一般来说,采用更加牢固和稳定的悬挂设备可以减小集装箱的侧翻自重。
综合考虑以上因素,集装箱侧翻自重的计算公式可以表示为:侧翻自重 = 集装箱本身重量 + 货物重量 + 集装箱尺寸和结构影响 + 装载方式影响 + 悬挂设备影响。
其中,集装箱本身重量、货物重量和悬挂设备影响可以通过实际测量或厂家提供的数据来获取。
集装箱尺寸和结构影响以及装载方式影响则需要根据实际情况进行分析和计算。
汽车侧翻及稳定性分析
以不考虑纵向运动的影响;忽略了空气作用力的影 响;忽略非簧载质量影响,即不考虑轮胎质量以及垂 直变形;忽略前后轴不同特性对侧翻的影响;悬架简 化为理想带阻尼的扭转弹簧;同时假设横向速度以 及横摆角速度相对车速很小,可进行线性化处理。
收稿日期:2006一04—14 作者简介:金智林(1978一).男(汉),江西,博士研究生,jd_nu雅@hot眦iI.com
2平衡态稳定性分析把方程x0处按泰勒公式进行一阶展开得到1235614a21a22a23a14a24a34a44a11kfcoskrakfcosbkrkfcoskrmhmhghcixakfcosbkrkfcosakfcosbkriza41kfcoskrakfcosbkrkfcoskra0a0kfkrcosakfcosbkrkfcoskrkfcoskfkrcosmuakfcosbkrkfkrcosmizkfkrcosmuakfcoscosbkkfcos2ixizkfcoskrkfcos根据劳斯赫尔维茨稳定判据可以得到系统平衡状态稳定性条件为muakfcosbkr2kfkrlcosmhg13根据式11平衡态约束条件以及式13平衡状态稳定性条件定义一个汽车侧翻准动态稳定因子qdsf2kfcosgllw则汽车侧翻系统能达到稳定的平衡状态条件为qdsf且随着qdsf值减小汽车稳定性降低
”丧
咖o=O 式中:£=口+6为前后轴距。
由于汽车转弯时轮胎的垂直载荷会发生转移, 即内侧载荷减小,外侧载荷增加。当内侧载荷减小 为零时,内侧轮胎离地,汽车系统将无法达到平衡状 态。根据绕外侧轮胎与地面接触点的力矩平衡关系 可得平衡状态约束方程
FinZ。+m^。。口,一7,lg(Z。/2一^咖)=0 (9) 即汽车能保持平衡态要求
汽车起重机侧翻事故案例分析
you're uinique, nothing can replace you.悉心整理助您一臂之力(页眉可删)汽车起重机侧翻事故案例分析1.事故过程简述2004年,一台LTMl170型汽车式起重机在装卸货物时,由于支腿销子未固定且水平支腿只伸出一半,司机从正后方吊起货物,向侧向回转时,起重机侧翻,造成起重臂严重损伤。
2.事故原因分析经现场勘察和测量得知:起重机所吊重物并未超过该工况下的额定起重量。
但当时由于施工现场的条件限制,操作人员在打支腿时只打了半腿且未固定销子。
在支腿没有完全伸开的情况下使用了起重机的原性能表,在吊重从正后方回转到侧向时,由于实际起重力矩超过起重机的额定起重力矩(在支腿没有完全伸开的情况下,实际的额定起重力矩小于原性能表中的额定起重力矩)造成起重机侧翻、起重臂受损。
3.事故应汲取的教训这是一起在支腿未完全伸开情况下按原起重性能表进行吊重操作引发的汽车起重机超载倾翻事故。
从事故中应汲取以下教训:(1)汽车式起重机的性能曲线是在支腿全伸状态下的额定起重能力。
在支腿未完全伸开的情况下,其起重能力小于性能曲线上标示的数值。
因此,在进行起重作业时,必须将支腿全部伸开, 支座盘应牢靠地连接在支腿上,支腿应可靠地支承起重机。
(2)起重机的操作人员应该严格按照操作规程操作。
在工作场所达不到规定的条件时,应该本着安全第一的原则,协调、改善和创造条件,使起重机能够在规程允许的工作条件下运行, 而不能凭主观、凭经验或长官意志,想当然地变更操作要领,违章操作。
4.违反何种标准、规定、规程的有关条款本事故是由于违反如下条款而造成:(1)《中华人民共和国国家标准起重机械安全规程》(GB6067-85)之5.1.2.2司机操作时,应遵守下述要求:h.流动式起重机,工作前应按说明书的要求平整停机场地, 牢固可靠地打好支腿。
(2)《特种设备安全检查条例》(国务院令第373号)之第四十条特种设备使用单位应当对特种设备作业人员进行特种设备安全教育和培训,保证特种作业人员具备必要的特种设备安全作业知识。
- 1、下载文档前请自行甄别文档内容的完整性,平台不提供额外的编辑、内容补充、找答案等附加服务。
- 2、"仅部分预览"的文档,不可在线预览部分如存在完整性等问题,可反馈申请退款(可完整预览的文档不适用该条件!)。
- 3、如文档侵犯您的权益,请联系客服反馈,我们会尽快为您处理(人工客服工作时间:9:00-18:30)。
此时的整车力矩平衡近似方程为 :
W • cos • (B1/ 2 • h) sin •W • H
(1)
上装围绕侧倾中心O1 的旋转,是由于在上装重力分力的作用下,围绕 O1点产生一
个转矩M,从而使得一侧的板簧受压,另一侧的板簧受拉,因此,钢板弹簧刚度的大小
对整车的侧翻角度是有影响的.转矩M与的近似方程为:
二.分析计算
底盘车架的高度、副车架、车厢副纵梁、中间垫块、货厢等尺寸参数决定 了自卸车的重心高度,其中副车架、车厢副纵梁、中问垫块的累加高度一般 为480~550mm,再加上高栏板货箱内高一般为1400~1800mm,这样整车 的重心高度一般在2000~2200mm之间。自卸车的重心较一般载货车要高。
W1 W 2'
7450 28560
将有关参数带入方程(1),(2)得,
2582•tg 10731962•
由方程(3),(4)得 11.6 , 15.7
1.3703• sin
(3) (4)
三.结论
整车在严重趋载情况下,侧向稳定角大大减小:本车在超载100%时,侧向 稳定角仅为14.6. 而举升 20时.稳定角仅为11.6,若再考虑轮胎的弹性变形的 影响,侧向稳定角实际要小于11.6, 主要是由于超载后,钢板弹簧的受力已经 超出设计要求.此时若将整车停止在侧向角度为 的斜坡上时,会导致左右悬 架的挠度变形不一样.其中内侧悬架挠度变形要大于外侧悬架的挠度变形.从 而使得侧稳定角减小。
自卸车侧翻计算与分析
一.引言
影响汽车侧翻的因素很多,也很复杂,如驾驶员对汽车的操纵、道路条 件、 悬架形式及重心高度等。目前,由于超载现象严重,自卸车倾卸货物时翻车事 故屡有发生。本文就自卸车的静态侧翻进行计算,分析翻车的原因,找出解决 的办法。
静态侧翻,无规律,除 零部件质量因素外,较 难找到有效的根本措施? 如何解决?
故较多,下面就以举升20时 ,由于货箱重
心的抬高.计算发生侧翻的坡度 ,如图4 所示.按照一般沙、石、土的自然堆积角
此时整车的重心高度为:
图4
H ' H 'W 2 H 2'W 2' 800 7450 3048 28560 2582(mm)
下面结合某具体车型(结构简图见图1,主要参数见表)进行计算分析。
图1
表1
底盘整备质量W1
上装及货物质量WWW122
底盘质心高度 H1 上装质心高度 H 2
整车质心高度 H
车距 B
外轮中心距 B1
板簧中心距 b 板簧刚度 K
7450Kg 40000Kg 800mm 2385mm 2136mm 1820mm 2146mm 1006mm 200Kg/mm
800 7450 3048 28560 7450 28560
2136(mm)
tg
B1 2 H
2146 2 2136
26.6
式中, 为横向斜坡角度。
2.2 静止状态考虑悬架因素时的侧翻计算(见图3)
当整车停在横向角度为 的斜坡上时,由于重力分力的作用,使得左、右悬架受力不
均,产生的弹性变形也不一样,从而使得上装围绕上装的侧倾中心O1偏转一个角度 ,
M
b/2 b •
(2)
K
2
将数据代入方程(1),(2)得 14.6 19
其中 M sin •W 2 • h1
由此可以看出,若考虑悬架的影响,上装及货物为40t时,在14.6 的斜坡上就 可导致侧翻。
图3
2.3 静止状态举升 20 时考虑悬架因素时的侧翻计算(见图4 )
自卸车一般在举升卸货时发生侧翻事
2.1 静止状态整车为刚性时的侧翻计算 (见图2)
在不考虑悬架及轮胎 弹性变形的情况下,即 将整车视为“刚性汽车” 的模型。根据有关资料 可知,一般重型汽车在 侧翻时尚未发生侧滑, 此时的侧翻计算较为简 单,将有关参数代入相 关公式即可算出整 车重心。
图2
H H1W1 H 2W 2 W1W 2
解决的办法:①减小钢板弹簧限位块的空间,这样在超载时,限位块及时 起到作用,以减缓钢板弹簧的变形,起到稳定作用;②增加板簧中心距,板
簧中心距b的增加可以减小上装的侧倾角 ,从而增加侧稳定性;③适当增
加板簧刚度 ,以减小由于超载而引起的严重的板簧变形。