橡胶模具结构
硫化模设计橡胶加工工艺

橡胶硫化模设计基础知识1对橡胶硫化模的要求1.1切实有效:设计的橡胶硫化模必须保证压制出的橡胶制品在尺寸、形状、表面外观质量等方面符合图纸要求。
1.2方便操作:包括以下几个方面●装料方便●取零件方便●装卸模具方便●搬动模具方便●模具轻便1.3制造简便:模具结构的机械加工工艺性要好。
1.4经久耐用1.5造价低廉2橡胶硫化模主要构成2.1成型结构:包括上模、中模、下模、型芯、哈夫块等。
2.2定位结构:包括定位销定位、本体定位等。
2.3排气结构:包括硫胶槽等。
2.4启模结构:包括启模槽、卸模架等。
2.5测温结构:包括测温孔。
2.6标识结构:包括对模倒角、防错销、防错孔、文字标识等。
2.7加料结构:包括加料室、注压缸、浇注孔等。
3分模面选择与胶料收缩率确定分模面选择应以方便制件取出和不影响制件外观为原则,一般选在最大外园处并且是棱角部位。
橡胶制件是在高温下成型的,由于橡胶的热膨胀系数比模具材料(钢)大的多,所以橡胶制件冷却后尺寸要比型腔尺寸小。
型腔尺寸与橡胶制件冷却后尺寸之比叫胶料收缩率,丁腈橡胶收缩率为1.5%,硅橡胶为2.5%,氟橡胶为3%。
4常用模具结构●上下模中心定位●上下模本体定位●上下模双销定位●上中下中心定位●上中下本体定位●上中下双销定位●上下模型芯定位●上中下型芯定位●普通复合模结构●合页式复合模结构橡胶模压工艺1.模压工艺综述1.1 模压工艺流程图1.2 模压工艺各工步操作要点1.2.1 下料:将胶料制成与橡胶制品的形状与大小相适应的毛坯,根据不同制品的要求,可采取不同的下料方法,如冲切下料、挤出下料和手工下料。
毛坯的好坏直接影响橡胶制品质量,主要影响因素有毛坯的重量、形状和尺寸。
1.2.2 装料:将毛坯装入模具中,装料位置要准确。
对于金属橡胶件,要注意金属件的安装方向和位置。
1.2.3 合模:合模时要注意:①方向不要搞错②定位销要确实进入定位孔内③不要碰伤模具④多套模具压制时模具之间的零件不要搞混。
阀圈橡胶模具设计2
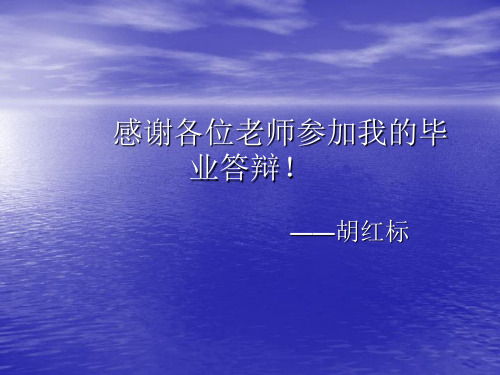
模具,简称橡胶注压模。此种成形工艺,是利用注压 机的压力,将已塑化好的胶料由螺杆或柱塞经喷嘴直 接注入模腔,完成成形并进行硫化的一种生产方法。 注压成形的特点,是把成形和硫化过程合为一体,成 形周期短,废边料少,劳动强度低,生产效率高,产 品质量好。目前,广泛用于橡胶密封圈、橡胶复合制 品、减振制品及胶鞋等橡胶制品生产。
计算应力状态
➢ 设计任务 设计参数:
设计要求
橡胶件的成型工艺性能分析
• 产品名称:船用中心型船用蝶阀阀圈(150
型)
• 产品材料: 丁腈橡胶 • 产品数量:中批量(<10万模) • 胶件尺寸:图中所示 塑件质量:160g • 胶件颜色:黑色 • 胶件要求:胶件外侧表面较光滑,产品的主
要工作面为内径部分圆弧面因此该处不能出 现流痕、气泡,塑件收缩率为1.4%,零件表 面按HG6-409-79三条(3)项要求,一般尺 寸公差按HB5522-80三级精度。
橡胶传递模:用于橡胶制品传递成形工艺方法的一类
模具,简称橡胶传递模。传递成形就是将混炼过的、 限量的胶条对压料柱塞施压,迫使胶料流经模具的浇 注系统注满模腔,经硫化定型后便可获得外观质量较 好和尺寸精度较高的橡胶制品。
橡胶传递模结构,虽然较压模复杂,但特适于薄壁、 细长、易弯曲以及形状较复杂的橡胶制品成形。采用 此类模具生产的橡胶制品,致密性好,质量也较高。
橡胶挤出模:用于挤出成形各种橡胶型材的一 类模具,简称橡胶挤出模。挤出成形工艺是生 产橡胶产品的主要方法之一。它是利用挤出机 使胶料在螺杆推动下,连续不断地向前运动, 然后借助于挤出口模,挤压出各种所需截面形 状的半成品,以完成不用造型或其他作业过程。 它具有连续、高效、甚至不用金属模具,就能 成形与制造多种不同截面形状的空心或实心半 成品,以达到初步造型的目的。而后进过冷却 定型,输入到硫化罐内进行硫化或作为压制法 所需的预成形半成品胶料。该模具在橡胶工业 中,亦占有及其重要的位置。
橡胶模具构造及保养培训资料

不同清洗方法能力对比
○:好 △:一般 ×:差
洗模方法一览表
洗模种类
喷砂 (树脂)
洗模 原理
物理性
洗模液
化学性
洗模橡胶 化学性
干冰
物理性
清洗能力 污垢状态 模腔状态
工作
用途
基本
使用 模具类型 价格 比例
堆积 物
表面 薄膜
平面
细小 部位
深沟 部位
防锈 性能
工作 时间
操作 升温 废弃 性 时间 成型
平压 模
特点:
优点:没有压料槽、操作方便模具、结构简单,模具廉价。
缺点:⑴毛边厚度方向尺寸精度难调整出来。
⑵产品容易产生材料不足的不良品。
型腔゙
导柱(位置定位用) 导套(位置定位用)
二.模具的基本认识
A.模具由钢材制造,其中模腔部采用优质模具钢。
B.橡胶模具一般由两板或三板模板组成,接触面为分模面(P.L 面).板与板之间是由导柱和导套进行对准定位。
②生产效率高、质量稳定
③水口废料产生少。
缺点:①毛边厚度方向尺寸精度难调整出来。
②对于壁厚产品容易产生材料不足的不良品。
定位环 热流道
隔热板
流道套 型腔
⑵.真空注入模具
真空注入模具:它是将搅炼过的、形状简单的、限量一定的橡胶料或胶
块半成品放入注入模压料槽中,通过压料板的压力挤压
橡胶料,并使橡胶料通过浇注系统进入模具型腔中硫化
C.模具型腔决定产品的形状.规格.尺寸.外观光洁度。
D.模板表面有表面处理:1.无电镀
2.电镀硬铬
橡胶模具设计教程.

5.排气槽设计
一般排气槽宽为1.5~2mm,深0.05~0.5mm。
6.启模槽设计
启模槽的设计,应使启模容易、省力、迅速,不损坏模板。
启模槽深为4~6mm,则宽15~20mm。
7.模具的定位机构
(1)圆柱面定位
(2)圆锥面定位
(3)导柱、导套定位
四.橡胶模典型结构
总结
本章主要讲述橡胶的分类、成型工艺特点和橡胶制品的结 构工艺性;橡胶模的分类及基本结构,橡胶模成型尺寸的确定 和设计要点。要重点掌握橡胶模的典型结构、橡胶模分型面的 确定、浇注系统的设计和橡胶模的结构设计。
第二节 橡胶模设计
一.橡胶模分类及基本结构
(一)橡胶模分类
根据橡胶模制品的类型、模具的使用条件和操作方法的不同,橡胶模主 要可分为填压模、压注模和注射模。 1.填压模 将定量胶料或预成形半成品直接填入模具型腔中,然后合模,通过电热 式平板硫化机进行加压、加热、硫化等工艺得到橡胶模制品的模具。 2.压注模 将混炼过的胶料或半成品装入模具料室中,通过压机将胶料由模具的浇 注系统挤入模具的型腔内。 3.注射模 利用专用的注胶设备,将预热塑化状态的胶料强行挤压射入模具的型腔, 然后硫化、起模得到制品。
(三)橡胶模结构设计
1.浇注系统的设计
(1)主浇道的设计 主浇道可以直接设置在模板上,也可以设计成嵌套式的。 主浇道为圆锥孔,上小下大,锥度一般为1:12、1:10等;大头 出口处设计成圆角,圆角半径0.5~2.5mm左右;尽量短些,降 低胶料的消耗及压力和热能的损失。
(2)分浇道的设计 分浇道是胶料进入主浇道后和进入进料口充满型腔前,流
型面处由于留有缝隙,会在制品的工作面留有胶边和痕迹,经
修边整理,也很难达到较好的质量。
橡胶模具

差 位 位置度
跳 圆跳动
动 全跳动
2020/7/18
曲轴
第三节 模具结构设计
一、压模结构设计及设计原则 (一)结构类型及分型面的选择 1.分型面的概念 将模具型腔分割成两个及两个以上可分离
部分的分割面称为分型面。
图13-6 O形密封圈模的两种分型面
2020/7/18
第三节 模具结构设计
2.分型面的选择原则 (1)保证制品易取出
1、孔与轴的概念
1)孔 2)轴
孔
+0
基本尺寸
上偏差
2020/7/18
es=0 基准轴h
基准孔H EI=0
基本偏差代号 a、b、c d、e、f cd、ef、fg g j 、 js j~n p~zc
使用要求 大间隙和热动配合
用于旋转运动 用于尺寸较小的旋转运动件
用于滑动或定位配合 用于与轴承相配合的轴
图13-l 橡胶矩形圈模 1—下模板;2—上模板;3—启模口;4—制品; 5—排气孔; 6—余料槽;7—定位销
2020/7/18
第一节 概 述
(二)分类 橡胶模具按模制方式可分为压模,压
铸模和注射模三种。
2020/7/18
第一节 概 述
1.压模 压模是将一定形状的胶料,加入
敞开的型腔内,用压机闭模加压,在 平板硫化机或立式硫化罐中硫化成型 的一种模具,它结构简单、造价低廉 、应用广泛。根据成型型腔的闭合形 式有开放式、封闭式和半封闭式之分 。
2020/7/18
2020/7/18
2020/7/18
2020/7/18
2020/7/18
2020/7/18
2020/7/18
2020/7/18
橡胶类模具设计规范 (节选)

xxxx纯橡胶产品模具设计技术规范1目的为规范xxxx纯橡胶产品设计(以下简称公司产品)轴套类产品模具设计,特编制本标准。
2 使用范围本规范适用于本公司轴套类产品模具设计。
3 引用标准无4 轴套类模具的组成4.1 轴套类模具由上模板、中模板、下模板、型芯、定位销、定位套、导向销、导向套、抬耳等主要部分组成。
5 流道设计要求5.1 排布流道时,应避免流道分支处与上一级流道交汇处出现尖角,应圆弧过渡。
5.2 流道排布应平衡,避免出现不对称,影响注射效果,流道壁面粗糙度小于Ra 018μm。
5.3 流道末端处,应设有冷料穴,伸出长度一般为10mm。
6 轴套类产品特点6.1按轴套组成形式,设计模具前应了解轴套类产品结构、材质、产品材料性能6.1.1 A类轴套:由内管、外管加橡胶体构成。
A类轴套(带铁骨架)一般情况下设计成上、中、下三模板结构。
例如A类轴套还包括铝骨架、尼龙骨架。
由于铝骨架、尼龙骨架刚度较小在注射时由于注射压力变形量较大,在设计时中板应设计成哈夫块结构,以避免由于骨架膨胀造成卸件困难。
6.1.2 B类轴套:内管加橡胶体构成。
B类轴套模具为方便卸件一般情况下设计为哈夫块结构。
6.1.3外管为翻边的骨架,在设计时应注意上板能将翻边压住,避免外管上下移动造成产品尺寸不合格。
例如6.2安装部位精度要求安装部位包括定位销与模板销孔定位,装配为过盈配合以保证装配性能,一般定位销尺寸比销孔尺寸大0.05mm为宜。
6.3.4模具材料及热处理一般情况下模板需经热处理调质,考虑到模具成本原因。
模板多用45#钢,硬度要求为HRC28-32度;模芯材质为P20,硬度要求为HRC33-38;开发初期单腔模具一般采用未调质的45#钢。
7 分型面的选择7.1 分型面的数目应少且为平面。
7.2不影响产品的外观质量。
在分型面处不可避免地出现飞边,因此应避免在外观光滑面上设计分型面。
7.3分型面一般不取在装饰外表面或带圆弧的转角处。
橡胶成型工艺及模具设计

橡胶塑炼的实质
降低分子量是生胶获得可塑性的最有效 方法。只有这样才能使粘度下降,可塑性增 加。 降低分子量,实质上就是使分子链断链。 低温塑炼:机械降解为主 塑 炼 的 方 法
机械塑炼法 高温塑炼:自动氧化降解 为主机械力强化橡胶与氧 的接触
化学塑解法
混炼
指在炼胶机上将各种配合剂加入到 橡胶中制成混炼胶的工艺过程
橡胶成型工艺及模具设计
第1章 橡胶概述
橡胶是高弹性的高分子材料,由于橡胶具有 其他材料所没有的高弹性,因而也称作弹性体。 天然橡胶 通用橡胶 用途 特种橡胶 合成橡胶 来源 再生橡胶 功能橡胶
粉末橡胶 液体橡胶 热塑性橡胶 板块固态橡胶
形态
橡 胶
生物胶 物化状态 熟橡胶 硬橡胶 混炼橡胶
天然橡胶(NR)
★一般工作温度:-10~150℃ ★基本特性:良好的耐高温,较好的耐油(包括含 硫的油)、耐磨性,耐寒性差。 ★主要用途:耐油、耐热、密封、板、囊、护套制 品。
★参考价格:10.0~12.0万元/吨
橡胶的基本特性
1.高弹性:弹性模量低,伸长变形大,有可恢复 的变形,并能在很宽的温度(-50~150℃)范围内 保持弹性。 2.粘弹性:橡胶材料在产生形变和恢复形变时受 温度和时间的影响,表现有明显的应力松弛 和蠕 变 现象,在震动或交变应力作用下,产生滞后损 失。
压型
压型是将胶料压制成一定断面形状的半成品或 表面有花纹的胶片。
压型工艺要求规格准确,花纹清晰,胶料密致, 故要求胶料收缩变形率小及配方中含胶率不宜过高。
压型工艺方法
纺织物挂胶(贴胶、擦胶)
纺织物挂胶是使纺织物通过压延机辊筒间隙,使 其表面挂上一层薄胶,制成挂胶帘布或挂胶帆布, 作为橡胶制品的骨架层。 贴胶
橡胶模具设计举例(word版)

1.序言毕业设计是大学学习的最后一个教学环节,是本专科人才培养计划的重要组成部分。
通过毕业设计既可以巩固学生在学校学过的理论知识,培养学生运用所学知识分析和解决工程实际问题的综合能力,又可以使学生初步掌握科学研究的基本方法和撰写符合规范要求的专业技术文件的能力。
搞好毕业设计工作,对培养学生的实践能力、创新能力和创业能力,全面提高教学质量和促进学生顺利就业具有重要意义。
.大学四年的本科学习和生活就要结束了,毕业设计是其中最后一个学习和锻炼的重要环节,是对以前我们所学过的理论知识及所掌握的设计创新思维在实际中的综合运用和检验。
随着我国经济的迅速发展,特别是十一五规划完成以来,采用模具的生产技术得到愈来愈广泛的应用。
随着中国制造的崛起,我国模具产业发展迅速,模具已成为当代制造业的主流装备。
目前我国正处于工业化中期,即从解决短缺为主的开放逐步向建设经济强国转变,家电、汽车、钢铁、房地产、建材、机械、电子、化工等一批基础工业高速增长行业发展势头强劲,构成了对模具市场的巨大需求。
据国际模具及五金塑胶产业供应商协会秘书长罗百辉介绍,中国已成为世界第一大模具市场,预计2015年模具产值将达到2500亿元,其中中高档模具、经济型模具的比例会大幅增加。
在这大学四年的课程学习中,我基本上掌握了机械制图、机械设计、机械原理等专业基础课和专业课方面的知识,在生产和参观实习中思考运用所学知识,再加上我一个月来在单位实践学习,对机械制造、加工的工艺有了一个系统、全面的理解,达到了学习的目的。
对于橡胶模具设计这个实践性非常强的设计课题,我在单位进行了大量的实践考察和学习。
经过在宝鸡真空股份有限公司的参观实习,尤其是在咸阳时代密封科技有限公司设计部近一个月的生产工作实习,我对于模具特别是橡胶模具的设计步骤有了一个全新的认识,丰富了各种模具的结构和动作过程方面的知识,而对于模具的制造工艺更是实现了零的突破。
在指导老师的协助下和在工厂师傅的讲解下,同时在现场查阅了很多相关资料并亲手拆装了一些典型的橡胶模具实体,明确了橡胶模具的一般工作原理、制造、加工工艺,并在图书馆借阅了许多相关模具设计手册和书籍资料,在设计中,我将充分利用和查阅各种资料,并与同学、老师和工人师傅进行充分讨论,尽最大努力搞好本次毕业设计。
- 1、下载文档前请自行甄别文档内容的完整性,平台不提供额外的编辑、内容补充、找答案等附加服务。
- 2、"仅部分预览"的文档,不可在线预览部分如存在完整性等问题,可反馈申请退款(可完整预览的文档不适用该条件!)。
- 3、如文档侵犯您的权益,请联系客服反馈,我们会尽快为您处理(人工客服工作时间:9:00-18:30)。
1.橡胶模具的概念:是指利用特定形状的型腔,成型具有一定形状和尺寸精度橡胶制品的工具。
2.压制成型模具概念:是指将具有一定可塑性的胶料,经预制成简单的形状后填入模具型腔,
经加压,加热硫化后,即可获得所需形状制品的一种模具
3.压制成型模具的结构种类及主要用途
开放式:适用于形状简单,胶料硬度较低,并具有较好流动性的胶料橡胶制品
封闭式:适于夹布,夹其他织物的制品以及硬度较高,流动性差的制品
半封闭式:适于上下模带有型腔,制品同轴度要求较高的单腔模具,也适于内夹织物的制品零件的模压生
4.分型面的概念及种类:根据模压制品的几何图案和质量要求,在模具结构上确定一个或几个
分合面和机械加工面的分离面,成为分型面。
常见的分型面:水平分型面,垂直分型面,阶梯分型面,斜分斜面以及复合分斜面等
5.分型面选取的原则:
1、保证制品顺利取出与脱模,有利于Fig2-16型腔中气体的排出
2、模具的分型面应尽量避开制品的工作面
3、同一类型制品不同分型面的选择
4、分型面应选择制品的边角和圆弧突出点的面上,有利于飞边的修除
5、夹布,夹织物制品的分型面选择
6、橡胶制品中各类套管,防尘罩,橡胶轴承分型面的选择
7、保证制品精度,对同轴度要求高的制品的外形或内孔,应尽可能设在同一块模板上,否则
由于模板间配合精度不够,定位偏差将影响制品的同轴度。
6.模具的定位方式:圆柱面的定位,圆锥面与斜面定位,分型面定位,导柱导套定位,镶块与
挡板定位,哈夫定位机定位,螺钉定位。
7.胶料收缩率的概念,产生原因影响因素
概念:胶料收缩是指制品硫化后,从型腔内取出冷却至室温的尺寸与制品对应型腔尺寸之差同制品实际尺寸的百分比
产生原因:
1、温度变化引起的收缩
2、化学反应引起的收缩
3、分子链取向引起的收缩
影响因素:
1、含胶率和胶种
2、胶料硬度
3、硫化温度
4、半成品胶料重量
5、胶料加工工艺
6、制品形状大小
8.胶料收缩率的一般规律
1、胶料压延方向和在模具中流动方向的收缩率大于垂直方向的收缩率,流动距离越长,收缩率越大。
2、模具型腔中装入半成品胶料越多,制品致密度越高,其收缩率就越小。
3、多孔模腔的模具,中间模腔压出的制品收缩率比边沿模腔压出的制品收缩率要小。
4、注射法成型的制品收缩率比一般模压法压制的制品收缩率略小。
5、薄形制品的收缩率比厚制品收缩率大0.2%-0.6%。
6、一般橡胶制品的收缩率随制品的内外径和截面的增大而减小。
7、棉布经涂胶与橡胶分层贴合的夹布制品的收缩率,一般在0-0.14%,夹布层越多,收缩率越小,织物为涤纶线的制品的硫化收缩率为0.4%-1.5%,含锦纶丝,尼龙布类织物的制品的硫化收缩率一般在0.8%-1.8%
8、含有金属等硬嵌件的橡胶制品零件硫化收缩率较小,且向嵌件的几何中心收缩,收缩率一般在0-0.4%。
9、硬质橡胶含胶量在20%左右时,制品零件的硫化收缩率大约为1.5%左右
10、橡塑并用制品的收缩率一般为1.1%-1.6%,约比同类橡胶制品小0.1%-0.3%
9.飞边的概念,以及修除飞边的方法:减少或消除橡胶模压制品飞边的主要措施是合理设计模
具结构和骨架封模尺寸,保证模具的制作精度,规范装模和启模操作
11.压铸成型基本原理:在普通模压法生产的橡胶制品模具上,增加压铸塞,加料室两个元件。
其压铸料腔起装填胶料的作用,在压铸料腔底部与相连接的模板或模腔部位开置一定数量的压铸料流道口。
压铸时,在平板硫化机的压力作用下,将力传递至压铸塞,再通过压铸塞传递给
胶料促使其压缩,受热,受压的胶料快速挤入料道,充满模具型腔,通过硫化,定型,从而得到模压制品
12.压铸料腔中进胶流道的结构形式:
1、有底压铸料腔。
2、无底或带有台阶的压铸料腔。
3、带腔型的压铸料腔结构。
4、有底加强压铸料腔结构。
13.何谓工艺间隙:考虑到成型工艺简单和加料方便,半成品加料与加料室应保留一定间隙,称为工艺间隙
14.排气孔位置选择的原则:
1、排气孔开设在远离浇口的流动末端,即气体最终聚集的地方。
2、靠近嵌件或壁厚最薄处。
3、多数排气槽开设在模具分型面上。
4、模具中的活动型芯,镶块,动配合面,其他配合间隙都可以用来排气,一般不必开设排气槽。
5、对型腔死角,斜面定位配合面余料逃气槽。
15.注射成型工艺特点:缩短硫化时间,减少生产工序,减轻劳动强度,提高了生产效率,产品质量高,机械化和自动化程度高
16.注射硫化工艺对胶料的要求:胶料必须有较好的抗焦烧性,并且有一定的流动性能
17.橡胶注射流道的特点:由于注射成型具有方向性强,成型快,高温硫化等特点,所以浇口开设得位置正确与否直接影响到制品的成型与性能。
胶料注射时,在模具中的流动非常复杂,
而且胶料在闭模的状态下注入,因而在浇道和模内分流道的形状、截面及长度对胶料的生热影响很大。
18.浇注系统的组成:主流道,分流道,内浇口冷料穴四部分组成
19.冷料穴的作用:作用是使浇注系统通过截面起过渡作用和转向作用,使胶料平稳转换,分
流道截面大小,决定于满足良好的压力传递和合理的填充时间等。
20.橡胶挤出成型的基本原理:是在压出机中对胶料加热和塑化,通过螺杆的转动,使胶料在
螺杆和机筒桶壁之间受到强大的挤压力,不断的向前传递,然后在一定的压力作用下,通过橡胶压出成型模(口型模)而制的一定形状断面、连续的型材(半成品)
21.压出工艺对机头与口型的要求:
1)机头内腔呈流线型。
2)有足够的压缩比。
22.橡胶挤出胀大的规律:
1)硬度较低(邵A50-60度)的胶料,挤出时膨胀变形大,挤出尺寸不稳定。
硬度较高(邵A70度以上)的胶料,压出后膨胀变形小,压出尺寸较稳定。
2)可塑性较好的胶料,压出后膨胀变形较小,压出尺寸较稳定。
3)硅橡胶与其他胶料不同,一般压出制品尺寸形状不膨胀,而稍有收缩。
4)压出的型材膨胀与制品尺寸大小有关。
在型材断面形状相同、材料相同并在通一工艺下压
出时,它的膨胀率与型材尺寸大小成正比。
5)压出的型材膨胀与制品断面形状有关。
一般圆断面的制品压出后因膨胀直径增大或减小,
断面形状不变:而其它形状断面的制品,压出后因膨胀而变形
23.挤出胀大的影响因素:
1)在一定剪切速率下,胶料挤出膨胀率B随口型(毛细管)长径比增大而减小。
2)在恒定的口型长径比条件下,家里挤出膨胀率B随温度升高而降低。
3)降低挤出速度,可以减少挤出膨胀率。
4)胶料含胶率对B有较大的影响,增大填充剂用量能降低挤出膨胀率,病史挤出物表面光滑。
5)软化剂(增塑剂)可以减小分子间作用力,缩短橡胶大分子松弛时间
24.制造模具用钢的基本性能要求;
1)加工性能良好,热处理后变形小。
2)抛光性好。
3)耐磨性好。
4)较好的淬透性。
5)耐腐蚀性好
25.常用模具钢种类:碳素钢(碳素钢分碳素结构和碳素工具钢),合金钢(合金钢分合金工具和合金结构钢)
26.模具材料的热处理:模具材料的热处理时保证模具性能的重要工艺过程,对模具的性能有如下直接影响:模具的制造精度,模具的强度,模具的工作寿命,模具的制造成本等。
27.模具的表面处理:模具的表面处理技术,是通过表面涂覆、表面改性或符合处理技术,改变模具表面形态,化学成分、组织结构和应力状态,以获得所需表面性能的系统工程
28.模具常见的加工方法:通过机床加工,数控机床加工,特种加工,模具外工作型面的加工,模具内工作型腔的加工。