高透气性湿型砂铸件表面粘砂控制
防止铸件粘砂的方法

防止铸件粘砂的方法
铸件粘砂是铸造过程中经常遇到的问题,以下是防止铸件粘砂的方法:
1. 合理选择造型材料和烘干时间,将确保砂型和砂芯具有足够的强度,能够承受铸造过程中的压力和温度变化。
2. 在砂型和砂芯表面涂布一层合适的脱模剂,能够防止粘附和易于除去砂芯。
3. 提高砂箱准确度和翻转速度,不仅有助于砂型的平整度和强度,还可以减少砂芯残留,并有助于铸件的散热。
4. 对于难以烘干或大量含水的砂型和砂芯,可以采用气流干燥的方法,以保证其表面干燥。
5. 提高清理砂型和砂芯的效率,避免残留和二次污染,防止因此导致铸件表面不光滑及砂芯残留。
以上是几个常用的防止铸件粘砂的方法,通过这些措施可以有效降低铸件的次品率,提高铸件的质量和生产效益。
彻底弄清铸件粘砂根源,9个防治措施真正解决粘砂难题

彻底弄清铸件粘砂根源,9个防治措施真正解决粘砂难题铸件粘砂不仅影响铸件的外观质量,甚至引起报废。
因此,对铸件的粘砂必须引起足够的重视,以提高产品出品率。
那应该如何防止铸件粘砂呢?“治病”当然要找到根源,首先我们先来看一下铸件粘砂的原因1、足够的压力使金属液渗人砂粒之间较高的金属液静压力头。
即由铸件浇注高度和浇注系统形成的压力。
如该压力超过砂粒间隙之间毛细现象形成的抵抗压力。
即尸毛=QcosO/r,式中P毛为毛细压力;为金属液表面张力;e为金属液毛细管的润湿角;r为毛细管半径。
就会形成机械粘砂。
静压力头超过500 mm,铸造用砂又较粗,多数会产生机械粘砂,除非上涂料。
上式亦说明:越大,即砂粒粒度越粗,尸毛越小,即较易产生机械粘砂。
2、金属液在铸型内流动形成的动压力。
3、铸型“爆”或“呛”。
即铸型浇注时释放的可燃气体与空气混合并被炽热金属液点燃所形成的动压力。
4、机械粘砂一经开始,即便压力减小,金属液渗透还会继续进行,直到渗透金属液前沿凝固。
即金属液温度低于固相线温度,渗透方可停止。
5、化学粘砂最通常的原因是湿型和制芯用原材料耐火度、烧结点低;石英砂不纯;煤粉或代用品加人不足;没有使用涂料或使用不当;浇注温度过高;浇注不当致使渣子进人铸型等因素造成。
容易造成粘砂的原因找到了,接下来我们就来说一下如何防止!1、预防机械粘砂可采用如下措施1)避免较高的金属液静压力头;在满足铸件补缩条件下冒口高度不要过高;避免浇包处于高位直接浇到直浇道内,必要时可利用盆形浇口杯缓冲一下金属流,并形成恒高静压力头。
2)尽量使用粒度较细、的铸造用砂。
3)砂型应紧实良好。
’机器造型不可超载,供给造型机的压缩空气应保持规定压力,避免使用过湿或存放期过长的型砂,因难以紧实,芯盒通气孔(塞)不得堵塞;采用树脂砂造型和制芯不能仅靠型砂的良好流动性,要保证紧实,必要时辅以震动。
4)防止铸型“爆”或“呛”。
型砂不可加人过量煤粉和水分。
尽量为型和芯开好出气孔、通气孔,增加铸型透气性。
最新(1)湿型砂的性能要求
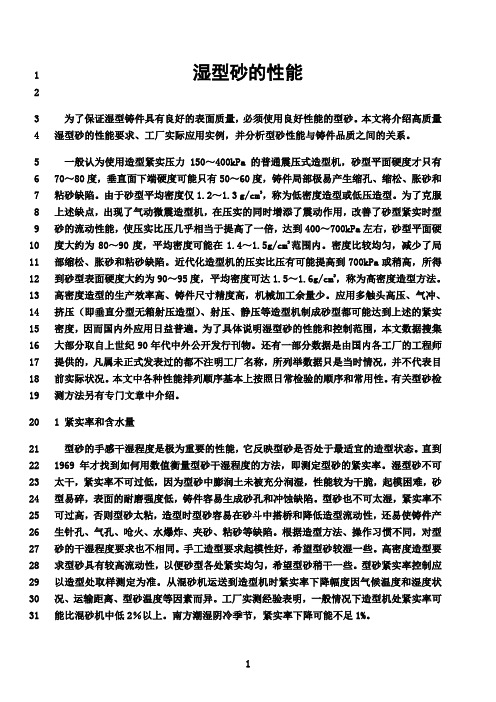
湿型砂的性能123为了保证湿型铸件具有良好的表面质量,必须使用良好性能的型砂。
本文将介绍高质量4湿型砂的性能要求、工厂实际应用实例,并分析型砂性能与铸件品质之间的关系。
5一般认为使用造型紧实压力150~400kPa的普通震压式造型机,砂型平面硬度才只有670~80度,垂直面下端硬度可能只有50~60度,铸件局部极易产生缩孔、缩松、胀砂和7粘砂缺陷。
由于砂型平均密度仅1.2~1.3 g/cm3,称为低密度造型或低压造型。
为了克服8上述缺点,出现了气动微震造型机,在压实的同时增添了震动作用,改善了砂型紧实时型9砂的流动性能,使压实比压几乎相当于提高了一倍,达到400~700kPa左右,砂型平面硬10度大约为80~90度,平均密度可能在1.4~1.5g/cm3范围内。
密度比较均匀,减少了局部缩松、胀砂和粘砂缺陷。
近代化造型机的压实比压有可能提高到700kPa或稍高,所得1112到砂型表面硬度大约为90~95度,平均密度可达1.5~1.6g/cm3,称为高密度造型方法。
高密度造型的生产效率高、铸件尺寸精度高,机械加工余量少。
应用多触头高压、气冲、1314挤压(即垂直分型无箱射压造型)、射压、静压等造型机制成砂型都可能达到上述的紧实15密度,因而国内外应用日益普遍。
为了具体说明湿型砂的性能和控制范围,本文数据搜集16大部分取自上世纪90年代中外公开发行刊物。
还有一部分数据是由国内各工厂的工程师17提供的,凡属未正式发表过的都不注明工厂名称,所列举数据只是当时情况,并不代表目18前实际状况。
本文中各种性能排列顺序基本上按照日常检验的顺序和常用性。
有关型砂检测方法另有专门文章中介绍。
19201 紧实率和含水量21型砂的手感干湿程度是极为重要的性能,它反映型砂是否处于最适宜的造型状态。
直到221969年才找到如何用数值衡量型砂干湿程度的方法,即测定型砂的紧实率。
湿型砂不可23太干,紧实率不可过低,因为型砂中膨润土未被充分润湿,性能较为干脆,起模困难,砂24型易碎,表面的耐磨强度低,铸件容易生成砂孔和冲蚀缺陷。
铸件粘砂的原因及处理
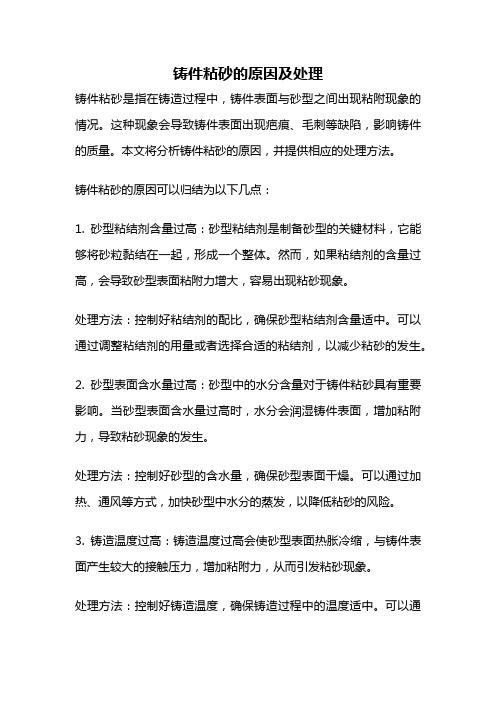
铸件粘砂的原因及处理铸件粘砂是指在铸造过程中,铸件表面与砂型之间出现粘附现象的情况。
这种现象会导致铸件表面出现疤痕、毛刺等缺陷,影响铸件的质量。
本文将分析铸件粘砂的原因,并提供相应的处理方法。
铸件粘砂的原因可以归结为以下几点:1. 砂型粘结剂含量过高:砂型粘结剂是制备砂型的关键材料,它能够将砂粒黏结在一起,形成一个整体。
然而,如果粘结剂的含量过高,会导致砂型表面粘附力增大,容易出现粘砂现象。
处理方法:控制好粘结剂的配比,确保砂型粘结剂含量适中。
可以通过调整粘结剂的用量或者选择合适的粘结剂,以减少粘砂的发生。
2. 砂型表面含水量过高:砂型中的水分含量对于铸件粘砂具有重要影响。
当砂型表面含水量过高时,水分会润湿铸件表面,增加粘附力,导致粘砂现象的发生。
处理方法:控制好砂型的含水量,确保砂型表面干燥。
可以通过加热、通风等方式,加快砂型中水分的蒸发,以降低粘砂的风险。
3. 铸造温度过高:铸造温度过高会使砂型表面热胀冷缩,与铸件表面产生较大的接触压力,增加粘附力,从而引发粘砂现象。
处理方法:控制好铸造温度,确保铸造过程中的温度适中。
可以通过调整熔炼温度、浇注速度等方式,控制铸造温度在合适的范围内,以减少粘砂的发生。
4. 铸造速度过快:当铸造速度过快时,砂型表面与铸件表面的接触时间较短,难以形成良好的粘结力,容易导致粘砂问题。
处理方法:控制好铸造速度,确保铸造过程中的速度适中。
可以通过调整浇注速度、铸型的设计等方式,使铸造速度与砂型的接触时间相匹配,以减少粘砂的发生。
5. 金属表面未做处理:金属表面的处理对于粘砂问题也有一定影响。
未经过适当处理的金属表面可能存在氧化物、污垢等,会增加砂型与铸件表面的粘附力,导致粘砂问题。
处理方法:对金属表面进行适当处理,去除氧化物、污垢等杂质。
可以通过酸洗、喷丸等方式,使金属表面保持清洁,并增加其粗糙度,以减少粘砂的发生。
铸件粘砂是由多种原因造成的,包括砂型粘结剂含量过高、砂型表面含水量过高、铸造温度过高、铸造速度过快以及金属表面未做处理等。
湿型铸造铸件缺陷产生的原因与控制
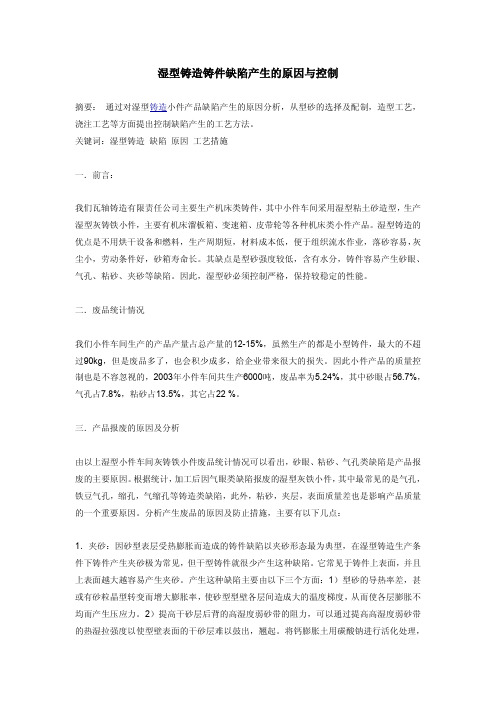
湿型铸造铸件缺陷产生的原因与控制变成钠膨润土,可以增加高湿度弱砂带的热湿拉强度,要使用优质粘土,还应增加型砂中粘土含量,以保证有高热湿拉强度。
可以在湿型型砂中添加淀粉来增加型砂的热湿拉强度。
在手工造型时,造型完毕,常在上箱型腔顶面插入钉子,并使钉子头与型腔表面齐平,钉子的作用是浇注时,将型壁表层的干砂层牢牢地钉住在后背的砂层中,使干砂层不能突出,翘起,防止夹砂产生。
3)砂型紧实均匀,有利于减少夹砂缺陷。
另外在造型操作中砂型扎出通气孔对防止夹砂缺陷是有效的。
防止夹砂有以下三方面对策:(1)减少砂型(芯)的宏观膨胀量。
(2)增加干砂层与砂型本体之间的水份凝聚区的热湿拉强度(3)增加干砂层的热变形量,使热变形量值超过它的受热膨胀值。
2.砂眼生成原因主要来自于造型材料,型砂和芯砂灰分高,强度低或水分及发气物质过多,则浇注时由于砂型或砂芯的强度不足或甚至金属液发生沸腾而使型砂掉落。
造型时紧实不匀,修型不当,以及在下芯,合箱时因不注意而发生碰撞都会造成砂粒的掉落,从而造成砂眼。
防止砂眼除了要注意造型和合箱操作以及尽量减少金属液对砂型的过分冲刷外,主要应合理控制型砂水份,提高型砂的韧性和强度。
3.气孔:金属液在凝固过程中,陷入金属中的气泡在铸件中形成的孔洞,称之为气孔,气孔属于孔壁光滑的孔洞类铸件缺陷。
与缩松,缩孔,砂眼,夹渣是不一样的,其形成原因也非常复杂。
或是因为砂型中的水分含量过高,或是型腔的排气不好,砂芯之间通气不畅,或炉料没有烘干等都易造成气孔缺陷。
跟据气孔形成的机理分为侵入气孔,裹携气孔,析出气孔,内生式反应气孔,外生式反应气孔,侵入气孔是从浇注到铸件表面凝固成固体壳的期间内,外部气体源(砂型,砂芯等)发生的气体侵入型腔内的金属液中,形成气泡而产生的气孔。
防止侵入气孔生成的对策:(1)降低砂粒间毛细管中气体压力主要是增大砂型型壁或砂芯的通气能力,减少和控制砂型或砂芯等气体源真实发气量以降低砂粒间毛细管中的气体压力,避免外部气体侵入金属液中,首先要控制型砂湿透气性和湿型表面硬度,人工增强砂型型壁和砂芯-砂型排气系统的通气能力,除了依靠型砂和芯砂的透气性来保证通气能力外,生产中主要采取人工增强通气能力的措施来防止和消除侵入气孔。
铸造粘土湿型砂的特性及其控制要点

铸造粘土湿型砂的特性及其控制要点发表时间:2018-12-25T11:33:27.080Z 来源:《基层建设》2018年第33期作者:赵艳锋1 李晶1 张小荣2 [导读] 摘要:针对铸造湿型砂的特性,组成,回收混配,覆膜砂对型砂的性能影响等方面控制,从而提高铸件的质量。
1.河南省西峡汽车水泵股份有限公司河南西峡 4745002.河南省西峡县天马有限责任公司河南西峡 474500摘要:针对铸造湿型砂的特性,组成,回收混配,覆膜砂对型砂的性能影响等方面控制,从而提高铸件的质量。
关键词:型砂;粘土;覆膜砂前言:铸造技术历史悠久,从人类进入青铜时代起,就用手工铸造生产了精美绝伦的产品。
铸造的三大基础是:炉子、模子、型砂。
型砂的主要原料是:原纱(烘干砂),粘土,旧砂,芯砂;型砂对铸件的质量起着决定性的影响。
1 粘土混型砂的特性通常都说粘土是湿型砂的粘结剂,实际上这种说法是不贴切的,粘土湿型砂中的粘结剂是粘土和水按一定比例混配组成的,水是粘结剂中的重要组成部分,但是水必须是自来水或蒸馏水,否则会影响型砂的湿压强度。
1.1 土水比采用高压造型工艺时,大部分土水比都在3: 1左右。
在这种条件下,型砂的可紧实性也最适合高压造型的要求(约在35~ 45之间)。
水与粘土混合后产生粘土膏,但水分再增多,其粘度随之降低,强度也相应下降。
采用震压式造型机造型时,型砂的强度就应该低一些。
因为型砂的强度越高,其抵抗变形的能力越强, 韧性就差,为适合这种工艺要求,型砂中的土-水比例就应该适当高一些,一般以控制在3: 2左右。
1.2 粘土混型砂的砂粒结构砂粒之间的粘结,是靠粘土来实现的。
理想的情况是:水和粘土混合充分,成为均匀的粘土膏,粘土膏又均匀地分布在每一砂粒的表面,砂粒之间由其表面的粘土膏彼此相连而形成的粘结桥粘结起来,其间的空隙可使型砂具有必要的透气性。
1.3 粘土湿型砂的混砂效率粘土湿型砂的混砂效率是指:型砂中实际上起粘结作用的膨润土量与其中的活性膨润土含量之比就是混砂效率,混砂效率= 有效膨润土量/活性澎润土含量 X 100 %,由于粘土膏属于半固态性质,粘度很高,难以混配均匀,用于混制粘土湿型砂的混砂机,所需的功率比供砂能力相同的树脂砂混砂机大得多,混砂所需要的时间也更长。
怎样调整与控制湿型砂湿态强度与黏度?

怎样调整与控制湿型砂湿态强度与黏度?如果型砂湿态强度不足,在起模、搬运砂型、下芯、合型等过程中,砂型有可能破损和塌落;浇注时砂型可能承受不住金属液的冲刷和冲击,而造成砂孔缺陷甚至跑火(漏铁水);浇注铁水后石墨析出会造成型壁移动而导致铸件出现疏松和胀砂缺陷。
生产较大铸件的高密度砂型所用砂箱没有箱带,高强度型砂可以避免塌箱、胀箱和漏箱。
无箱造型的砂型在造型后缺少砂箱支撑也需要具有一定的强度。
挤压造型时顶出的砂型要推动其它造好砂型向前移动,更对型砂的强度提出了较高要求。
但是,强度也不宜过高。
因为高强度的型砂需要加入更多的膨润土,不但影响型砂的水分和透气性能,还会使铸件生产成本增加,而且给混砂、紧实和落砂等工序带来困难。
以下文章中各种型砂强度的单位均为kPa,不再逐个标明。
1 湿压强度一般而言,欧洲铸造行业对铸铁用高密度造型型砂的的湿压强度值要求较高。
欧洲造型机供应商推荐的湿压强度值范围在130~250之间,集中于180~220。
有些日本铸造工厂对型砂湿压强度的要求偏低。
除丰田上乡和三菱川崎强度较高以外,很多工厂只有80~180。
北美铸造行业的型砂强度似乎介于欧洲于日本之间。
例如福特汽车厂Cleveland铸造厂排气管高压造型型砂为172,万国收割机公司Loisville铸造厂生产拖拉机缸体高压型砂为134~156。
有人认为欧洲铸造工厂的型砂湿压强度比美、日两国工厂高的原因之一是由于欧洲铸铁用原砂含SiO2较高,型砂中必须加入大量膨润土才能避免铸件产生夹砂结疤缺陷。
我国工厂高密度造型的型砂湿压强度比较接近美洲和日本工厂,对于铸铁件而言,除个别铸造厂以外,高密度造型的湿压强度大多在120~200范围内,比较集中在140~180。
湿压强度控制值较低的优点之一是即使所使用的振动落砂机破碎效果不好,也不致有大砂块随铸件跑掉。
而且很多铸造工厂所选用膨润土的品质较差,宁愿型砂的湿压强度稍低些,就无需加入大量膨润土,型砂含水量也可低些。
铸钢用湿型砂的性能分析及控制

26 含 泥 量 .
型砂 必 须具 备一定 的强 度 ,以承受各 种
外 力 的作用 。如 果强 度不 足 , 在起模 、 运砂 搬
型、 下芯 、 箱 等 过 程 中 , 型 有 可能 造 成 破 合 铸
损 塌 落 ;浇 注 时也可 能承受 不住 金属 液 的冲 刷 和 冲击 , 型被 冲 坏造 成 铸件 砂 孔 、 肉 、 砂 多
型铸造得 到 广泛应用 。 我 车间正 是基 于湿 型 的诸多 优点 .采 用 了石 英砂 湿 型铸造 方法 , 经过 不断 摸 索 、 研究 和改进 , 已能生 产 出结 构较 为复 杂 、 现 重量 达
由于湿 型本 身存在 以上 缺陷 。这就 要求
在生产 中加 强湿 型砂各 种性 能 的控制 。使之 达 到较 好 的使用效 果 , 同时 , 造型设 备必 须使 砂 型 紧实 、 匀 , 模 平 稳 , 型腔 具 有较 高 均 起 使
维普资讯
《 重庆重 汽 科技》
20 0 7年 第 1 期
铸钢用湿型砂 的性 能分析及控制
冯小涛
【 摘要 】 本文说明了湿型铸造 的特点 , 对铸钢用湿型砂 的主要性能进行 了分析 , 而根据铸钢 进
生 产 的特 点 提 出 了对 型 砂 各 主要 性 能 的控 制措 施 . 以得 到 质 量较 好 的 铸钢 件 。
关键 词
湿型
湿型砂
性能
水分
湿 压 强度
湿 透气性
紧 实率
流 动性
前 言
遇 时 , 分 蒸 发 , 积骤 胀 , 使 铸钢 件产 生 水 体 易 气孔 缺陷 。
在 砂 型铸造 中 .根据 砂型 在合 箱和 浇注 时的状 态 不 同可 以分 为湿 型 、干型 和表 面干 型三类 。 它们 的区别 主要在 于 : 型在造好 型 湿 后 不必 烘干 . 可直 接浇 入高 温金属 液 体 ; 型 干 在合箱 和浇 注前 要将 整个 砂型送 入 窑炉 中烘 干 :表 面干 型只 需将砂 型 型腔表 面烘 干到 一 定深 度 即可 , 必全部烘 干 。 不
- 1、下载文档前请自行甄别文档内容的完整性,平台不提供额外的编辑、内容补充、找答案等附加服务。
- 2、"仅部分预览"的文档,不可在线预览部分如存在完整性等问题,可反馈申请退款(可完整预览的文档不适用该条件!)。
- 3、如文档侵犯您的权益,请联系客服反馈,我们会尽快为您处理(人工客服工作时间:9:00-18:30)。
粒度 ,取每天做完含泥量的旧砂做为旧砂粒度 ,
高透气 性湿型砂铸件表面粘砂控 制
杜 文科
( 广西玉柴机器股份有限公 司铸 造厂 , 广西 玉林 570 ) 3 0 5
摘要 : 介绍 了生产 H 2 0 T 5 气缸 盖铸件 的型砂 系统构成 , 对铸件 表面粘砂 缺陷进行分析认为是机械粘砂 , 采取提高铸型硬
度, 控制含泥量在工艺上限 , 原砂 SO 量相对偏低时 , i 加入一定 比例 的细新砂等措施 , 有效解决 了问题 。
s r c e e t o h a t g w s a a y e n tw sc n i d t a h e e t smea e e r t n B n r a i g t e mod u f e d f c s f e c si a n l z d a d i a o f me h t e d f c tl n tai . y i ce sn h l a t n r t wa p o
1.%~ 30 A) 1.~ 35 B) 25 1 . %( 和 30 1 . %( 两个 区域 , 进
行 连 续 大批 量生 产 对 比。从 生产 结 果来 看 , B区
域透气性的平均值 比 A区域透气性 的平均值下
降约 1 0个单位。对 比开箱后铸件表面的粘砂情 况可见 , B区域优于 A区域 。
砂 。按其 形 成 原 理 , 砂 分 为 机 械粘 砂 、 学 粘 粘 化
砂、 热粘砂等 。 用湿型砂生产铸铁件 , 由于铁液 中 含有大量的碳 ,不会产生大量 F2 e 等金属氧化 0
物 , 型 中含 有 足够 的煤 粉 , 注 时产 生 的还 原 砂 浇
性 气氛 也可 防止金 属 氧化 物 的产 生 , 以一 般 只 所 会 产生 机械 粘 砂 。 因此 , 对产 生机 械 粘砂 的主要 因素进 行分 析 如下 。
的牌号 为 H 2 0的柴 油机 气缸盖铸件为例 , T5 对 高透气性湿型砂铸件表面粘砂问题进行 了探讨。
1 生 产 情 况
11 生产设 备 .
采用 国产气冲造型线混线生产平浇 A缸盖 和侧浇 B缸盖两种机型的铸件 , 两种缸盖产量所
占比例约为 4 6 :。两种铸件均为实体芯射芯 , 其
关键词 : 粘砂 ; 铸型硬度 ; 含泥量 ; 粒度分布
中图分类号 :G 5 T 21 文献标识号 : B 文章编号 :0 3 8 4 (0 3 O 一 o 7 0 10 — 3 5 2 1 )l 0 6 — 4
D :0 9 9 .s.0 3 8 4 .0 3 1 0 OI 1. 6  ̄i n10 — 3 5 1. . 1 3 s 2 0 0 1 Su f c t l e e rt n De e tCo to fCa t g o u e t g e me bly Gr e r e Me a n ta i f c n r l si s Pr d c d wi Hih P r a it e n a P o o n h i Molig S n dn a d
械 粘砂 。
2 试 验 结 果 与 分析
铸件 表面出现牢 固粘附砂粒 的现象称为粘
从控制机械粘砂 的 目的来选择合适 的含 泥 量, 则需要依据各生产线实际能力而定。以本生
6 现 铸 2l/ 8 l 代 铁 o31
产线为例 , 铸件表 面粘砂 的主要原因在于型砂透
气性 过 高 , 论分 析 需要 偏 高 的含 泥量 。为验 证 理
得顶面大平面 的铸型硬度最高 ,硬度值在 9 左 2 右; 铸件前 、 后端面( 砂箱宽向两侧 ) 次之 , 硬度值 在 8 左右 ; 5 铸件排气面( 砂箱长向两端 ) 最差 , 硬
度值在 8 右。 0左
由于型砂质量 、 型机性 能等 的波动 , 造 每箱 机处的紧实率为 3~ 0 透气性大于 10 湿压强 04 、 2、
的铸件混线进行生产 , 这种生产模式导致芯砂大 量混入造型线砂处理系统 ,造成型砂透气性高 , 甚至高达 10以上 ,导致铸件表面粘砂严重 , 5 难 以控制。面对这一问题 , 笔者以缸盖生产线生产
砂处理线配备滚筒筛、 圆盘机、 沸腾冷却床等 相关设备 , 2台双转子混砂机 , 混砂量为 1 辊。 .t 1/ 熔炼设备为 7 冲天炉和工频炉。 t
盖 , 他各物料和控制参数不变 , 其 各连续大批量
生 产一 个 月 以上 , 析型 砂 系统各 关 键参数 的变 分 动情 况 ,两 种 芯砂 的透 气 性对 比如 图 2所 示 , 图 中 2 1— 0 1 前采 用 A种 砂 , 后采 用 B种 0 1 1— 8之 之
砂。
这一假 设 , 据实 际情 况 , 型砂 含泥量 分 为 依 将
表 面 光洁 。
作者简 介 : 杜文科 (9 0 ) 男 , 1 8 一 , 甘肃 泾川人 , 业于华 中科技 大 毕
学材料成 型及控 制工程专业 , 工程 师, 主要 从事现场 生产及质 量
管理等工作。
() 1型砂性能 : 含泥量为 1. 1. 造型 2 %~ 3 %、 5 5
21/ 代 铁17 03 1现 铸 6
和砂 型 透气 性 两方 面 。含 泥量 过 高 , 在相 同 紧实
砂混入了旧砂系统。 结合该生产线生产铸件 的产 量 以及型 、 芯砂 比例分析 , 混入的芯砂 主要以 5/ 0
10目的冷芯 硅砂 为主 。 0
度的条件下型砂水分升 高 , 流动性变差 , 造型时 边角或结构复杂部位铸型硬度差 , 铸件表面很容 易产生粘砂缺 陷; 含泥量过低 , 使型砂透气性升 高, 铁液更容易渗入砂粒之间 的孑 隙 中, L 产生机
随着科学技术的不断发展 , 人们对铸件质量
的要求不 断提高 , 而且对于铸件质 量 , 人们如今 关注的已不仅仅是废 品率 、 尺寸精 度 、 材料性能 等常规项 目,铸件外观质量也越来越受到重视 。 提升铸件外观质量 , 不仅仅要在铸 件清理 、 表面 处理方面开展工作 , 更重要的是要在制芯 、 造型 、 熔炼等方面进行有效控制 。 对于流水线作业的铸 造车间来说 , 如果生产工序对铸件外观质量不能
45 1 型 、 .: , 芯砂 比约 1 : 。 0 1
批量生产 的铸件表面质量情况 , 发现铸型硬度提
高后 的铸件表面粘砂率大大降低 。
22 型砂 含 泥量 .
侧 浇 B缸盖 采用 全砂 芯组 芯造 型 , 铸件 所有 内腔 、 形 均 由实体 砂 芯形 成 。砂铁 比约 25 1 外 .:,
b i g r lt e y lw r a d S n, e d f c a e n ef ci ey e i n t d e n ea i l o e , n O o t e e t sb e f t l l v h h e v mi a e .
Ke rs: tl e ert n mod h r n s ;lyc ne tgandsr uin y wod mea n tai ; l ad e s ca o tn ;ri i i t p o tb o
有效控制 , 仅靠后期 的清理工序来保证 , 则会造 成待清理的铸件积压 。
目前 , 国内很 多生 产线 都将 多 种不 同砂铁 比
中平浇 A缸盖采用全套热芯盒覆膜砂射芯工艺 ,
利用 Z 6 0 84 C热芯盒射芯机制芯 ; 侧浇 B缸盖为
全 套 冷芯 盒射 芯工 艺 , 用 L 6 芯机 制芯 。 利 B 5冷
度 为 01~ . a .101 MP 。 4 ( ) 型 紧实 度 : 2铸 用湿 型砂 硬 度计 检 测 , 型腔 底 面大平 面不低 于 9 , 腔侧 面不低 于 7 。 0型 5 ( ) 注 工艺 : 注 温度 为 130 14 0℃ , 3浇 浇 8 ~ 2
浇 注时 间为 1 ~ 0s 2 2 。 13 型砂 、 砂 比例 . 芯
2 1 砂型 硬度 .
从 开 箱后 的铸 件 表 面粘 砂情 况 看 , 砂 主要 粘
集 中在铸件前 、 后端面Байду номын сангаас排 气面 , 铸件顶面大平
面较 好 。造 型后 砂 型各 部位 的硬 度 有差 异 , 造 而
型机的能力对砂型各处的硬 度均匀性起决定作
用 。 以笔 者 公 司 现有 的气 冲 造 型线 生 产 的 A种 缸 盖 为例 ,利 用 湿型 硬度 计对 砂 型进 行 检测 , 测
12 生产 工 艺及 参数 .
采用冲天炉+ 工频炉双联熔炼 ,对铸件表面
收稿 日期 :0 2 0 — 4 2 1— 7 1 修定 日期 :0 2 1— 5 2 1 — 2 2
的质量 的要求是 : 经开箱 、 粗清 、 退火后 , 表面无 大面积连续粘砂( 如图 l 所示 )抛丸处理后铸件 ,
DU W e — e n k
( a giYu h i c ieyCo。t.Yui 5 7 0 C ia Gu n x c a hn r . d , l Ma L n 3 0 5, hn )
Ab t c : h ligsn y tm s dfrpo u t n o 2 0 ga ega rnc l d rh a at g a nrd c d T e sr tT emodn a ds s a e u e o r d ci fHT 5 rd ryio yi e e dc s n sw sito u e . h o n i
由此得 到 初 步结论 , 于高 透气 性 的砂处 理 对 系统 , 含泥 量控 制 取工 艺上 限利 于机 械粘 砂 的控
制。 23 芯砂粒 度及 SO, . i 含量
由图 2 可见 ,两种砂的型砂透气性有差别 , 其 中砂 B的透气性 比砂 A的透气性低 2 个 单 0 位左 右 。