铸件常见缺陷(图文并貌)
铸件缺陷分析PPT课件

铸件在凝固末期或刚凝固 后不久产生的裂纹。
03
铸件缺陷形成原因及机理分析
原材料因素
原材料质量
使用不合格或质量差的原材料, 如废钢、生铁等,其中含有的杂 质元素和气体可能导致铸件缺陷 。
原材料配比
原材料配比不合理,如碳、硅等 元素含量过高或过低,会影响铸 件的凝固过程和机械性能。
熔炼工艺因素
熔炼温度
介绍了常用的铸件缺陷检测与评估方法,如目视检查、无损检测、 金相分析等,以及各种方法的优缺点和适用范围。
缺陷预防与控制措施
重点讲解了铸件缺陷的预防和控制措施,包括优化铸造工艺、提高原 材料质量、加强过程监控等方面。
学员心得体会分享
知识收获
学员们表示通过本次课程,对铸件缺陷的类型、成因、检 测与评估方法有了更深入的了解,对铸件质量控制的重要 性有了更深刻的认识。
其他可能影响因素
生产环境
生产环境中的温度、湿度和清洁度等因素对铸件质量也有一 定影响。例如,湿度过高可能导致型砂粘结力下降,温度过 高则可能导致铁液冷却速度过快。
操作技能
操作工人的技能水平和经验对铸件质量也有重要影响。例如 ,合箱时定位不准确、浇注时铁液温度控制不当等都可能导 致铸件缺陷。
04
铸件缺陷预防措施与改进方法
控制熔炼温度
根据原材料成分和熔炼设备特点, 合理设置熔炼温度,避免过高或 过低的熔炼温度对铸件质量产生 不良影响。
调整化学成分
通过添加合金元素和调整废钢、生 铁等原材料的配比,控制铁水的化 学成分,提高铸件的力学性能和耐 蚀性。
减少熔炼杂质
采取过滤、除渣等措施,减少熔炼 过程中产生的氧化物、硫化物等杂 质,提高铁水的纯净度。
夹渣和夹杂物
01属夹杂物,夹杂 物则是金属或非金属杂质。
铸件外观缺陷图

铸件常见缺陷常见缺陷缺陷的分类:铸件常见缺陷分为孔眼、裂纹、表面缺陷、残缺类缺陷、形状及尺寸和重量不合格、成份及组织和性能不合格六大类。
1孔眼类缺陷孔眼类缺陷包括气孔、缩孔、缩松、渣眼、砂眼、等。
1.1.1气孔:别名气眼,气泡、由气体原因造成的孔洞。
铸件气孔的特征是:其表面一般比较光滑,主要呈梨形\圆形和椭圆形.一般在铸件表面露出,大孔常孤立存在,小孔则成群出现。
(如图)产生的原因是:来源于气体,炉料潮湿或绣蚀、表面不干净、炉气中水蒸气等气体、炉体及浇包等修后未烘干、型腔内的气体、浇注系统不当,浇铸时卷入气体、铸型等。
1.1.2缩孔缩孔别名缩眼,由收缩造成的孔洞。
缩孔的特征是:形状不规则,孔壁粗糙并带有技状晶,常出现在铸件最后凝固的部位,广义的缩孔包括缩松。
(如图)产生的原因是:金属在液体及凝固期间由于补缩不良而产生的孔洞,主要有以下几点:铸件结构设计不合理,浇铸系统不适当,冷铁的大小、数量、位置不符实际、铁水化学成份不符合要求,如含磷过高等。
浇注温度过高浇注速度过快等。
1.1.3缩松缩松别名疏松、针孔蜂窝、由收缩耐造成的小而多的孔洞。
缩松的特征是:铸件断面上出现的分散而细小的缩孔.助高倍放大镜才能发现的缩松称为显微缩松,铸件有缩松的部位,在气密性实验时易渗漏。
(如图)产生的原因同以上缩孔。
1.1.4渣眼渣眼别名夹渣、包渣、脏眼、铁水温度不高、浇注挡渣不当造成。
渣眼的特征是:铸件浇注位置上表面的非金属夹杂物。
通常在加工后发现与气孔并存,孔径大小不一,成群集结。
(如图)产生的原因是:铁水纯净度差、除渣不净、浇注时挡渣不好,浇注系统挡渣作用差、浇注时浇口未充满或断流。
1.1.5砂眼砂眼是夹着砂子的砂眼。
砂眼的特征是:铸件内部或表面带有砂粒的孔洞(如图)。
产生的原因是:型砂损坏脱落,型腔内的散砂或砂块未清除干净、型砂紧实度差、浇注时冲坏型芯、浇注系统设计不当、型芯表面涂料不好等。
1.1.6铁豆铁豆是夹着铁珠的孔眼、别名铁珠、豆眼、铁豆砂眼等。
铸造缺陷及其对策.pptx

4、防止方法:
1、优化铸件结构设计,壁厚均匀,过渡平滑,肋板 厚度和分布的合理化; 2、优化浇注系统,控制浇温、浇速使铸件各部位冷 却速度趋于一致; 3、降低有害元素,合理控制合金元素添加量; 4、合理设定开箱时间。
5、补救措施:
1、开止裂孔后焊补; 2、采用工业修补剂; 3、如在重要面,报废重铸。
第16页/共28页
4、防止方法: 1、优化工艺设计,合理设置浇注系统; 2、考虑使用保温冒口、发热冒口; 3、优化铸件结构设计; 4、模拟分析(CAE); 5、调整成份; 6、控制炉料.
第17页/共28页
5、补救措施: 1、轻者焊补或采用工业修补剂; 2、重者报废重铸.
第18页/共28页
2.夹砂
的不同大小、形状的 孔洞缺陷的总称
缩孔 缩松
形状不规则,孔壁粗糙,常伴有粗大 树枝晶.夹杂物.裂纹等缺陷;
是细小的分散缩孔,断口呈海绵状;
疏松(显微缩松) 不作严格区分;
第3页/共28页
气 孔
第4页/共28页
针孔
2、裂纹、冷隔类缺陷
定义
缺陷名 称
特征
宏观(肉眼、PT、R T、MT、UT)或微 观(显微镜)判断发现 有开裂状纹络
1、铸件内部裂纹可采用超声波探伤(UT)、 磁粉探伤(MT)或射线探伤法(RT)进行检验; 2、铸件表面的裂纹可采用染色探伤法(PT)来 帮助确定,大部份是肉眼可直接发现的。
第24页/共28页
3、形成原因:
1、铸件结构或浇注系统设计不合理壁厚相差悬殊, 过渡圆角小; 2、铸造合金中有害元素(P、S等)超标,珠光体 元素过量; 3、铸件开箱过早,冷却过快; 4、合金收缩率大; 5、肋板设计不合理。
铸件常见缺陷(图文并貌)
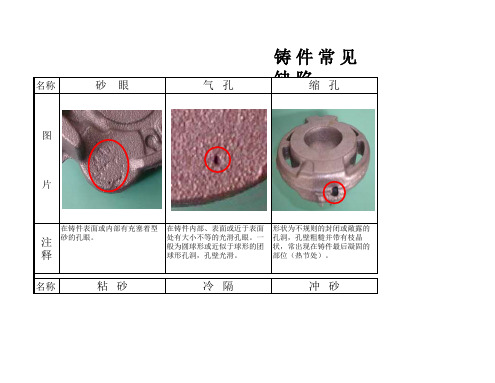
铸件常见缺陷
名称砂眼气孔缩孔披缝图
片
注释在铸件表面或内部有充塞着型
砂的孔眼。
在铸件内部、表面或近于表面
处有大小不等的光滑孔眼。
一
般为圆球形或近似于球形的团
球形孔洞,孔壁光滑。
形状为不规则的封闭或敞露的
孔洞,孔壁粗糙并带有枝晶
状,常出现在铸件最后凝固的
部位(热节处)。
披缝是铸件表面上厚薄不均匀
的片状金属突起物,常出现在
铸件分型面和芯头部位。
名称粘砂冷隔冲砂掉砂
图片
注释在铸件表面上、全部或部分覆
盖着金属与砂的混合物,或一
层烧结的型砂,致使铸件表面
粗糙。
冷隔是铸件上未完全融合的缝
隙或洼坑,其交接边缘呈圆
角,多出现在远离浇口的铸件
宽大上表面和薄壁处、金属流
股汇合处或激冷部位。
铸件表面上有粗糙不规则的金
属瘤状物,常位于浇口附近。
在铸件其它部位则往往出现砂
眼。
铸件表面的块状金属突起物,
其外形与掉落的砂块很相似。
在铸件其它部位则往往出现砂
眼或残缺。
毛 刺浇 不 足
毛刺是铸件表面上刺状金属突起物,常出现在型和芯的裂缝处,形状极不规则。
由于金属液未完全充满型腔而产生的铸件缺肉。
缺 损变 形渣 眼
在铸件清理或搬运时,损坏了铸件的完整性。
由于收缩应力或型壁变形、开
裂引起的铸件外形和尺寸与图
纸不符。
在铸件内部或表面形状不规
则的孔眼。
孔眼不光滑,里
面全部或部分充塞着渣。
(推荐)铸件外观缺陷图

铸件常见缺陷常见缺陷缺陷的分类:铸件常见缺陷分为孔眼、裂纹、表面缺陷、残缺类缺陷、形状及尺寸和重量不合格、成份及组织和性能不合格六大类。
1孔眼类缺陷孔眼类缺陷包括气孔、缩孔、缩松、渣眼、砂眼、等。
1.1.1气孔:别名气眼,气泡、由气体原因造成的孔洞。
铸件气孔的特征是:其表面一般比较光滑,主要呈梨形\圆形和椭圆形.一般在铸件表面露出,大孔常孤立存在,小孔则成群出现。
(如图)产生的原因是:来源于气体,炉料潮湿或绣蚀、表面不干净、炉气中水蒸气等气体、炉体及浇包等修后未烘干、型腔内的气体、浇注系统不当,浇铸时卷入气体、铸型等。
1.1.2缩孔缩孔别名缩眼,由收缩造成的孔洞。
缩孔的特征是:形状不规则,孔壁粗糙并带有技状晶,常出现在铸件最后凝固的部位,广义的缩孔包括缩松。
(如图)产生的原因是:金属在液体及凝固期间由于补缩不良而产生的孔洞,主要有以下几点:铸件结构设计不合理,浇铸系统不适当,冷铁的大小、数量、位置不符实际、铁水化学成份不符合要求,如含磷过高等。
浇注温度过高浇注速度过快等。
1.1.3缩松缩松别名疏松、针孔蜂窝、由收缩耐造成的小而多的孔洞。
缩松的特征是:铸件断面上出现的分散而细小的缩孔.助高倍放大镜才能发现的缩松称为显微缩松,铸件有缩松的部位,在气密性实验时易渗漏。
(如图)产生的原因同以上缩孔。
1.1.4渣眼渣眼别名夹渣、包渣、脏眼、铁水温度不高、浇注挡渣不当造成。
渣眼的特征是:铸件浇注位置上表面的非金属夹杂物。
通常在加工后发现与气孔并存,孔径大小不一,成群集结。
(如图)产生的原因是:铁水纯净度差、除渣不净、浇注时挡渣不好,浇注系统挡渣作用差、浇注时浇口未充满或断流。
1.1.5砂眼砂眼是夹着砂子的砂眼。
砂眼的特征是:铸件内部或表面带有砂粒的孔洞(如图)。
产生的原因是:型砂损坏脱落,型腔内的散砂或砂块未清除干净、型砂紧实度差、浇注时冲坏型芯、浇注系统设计不当、型芯表面涂料不好等。
1.1.6铁豆铁豆是夹着铁珠的孔眼、别名铁珠、豆眼、铁豆砂眼等。
常见压铸件缺陷及解决方法

常见压铸件缺陷及解决方法(总10页)--本页仅作为文档封面,使用时请直接删除即可----内页可以根据需求调整合适字体及大小--常见压铸件缺陷及解决方法一、流痕其他名称:条纹。
特征:铸件表面上呈现与金属液流动方向相一致的,用手感觉得出的局部下陷光滑纹路。
此缺陷无发展方向,用抛光法能去处。
产生原因:1、两股金属流不同步充满型腔而留下的痕迹。
2、模具温度低,如锌合金模温低于150℃,铝合金模温低于180℃,都易产生这类缺陷。
3、填充速度太高。
4、涂料用量过多。
排除措施:1、调整内浇口截面积或位置。
2、调整模具温度,增大溢流槽。
3、适当调整填充速度以改变金属液填充型腔的流态。
4、涂料使用薄而均匀。
二、冷隔,水纹其他名称:冷接(对接),水纹。
特征:温度较低的金属流互相对接但未熔合而出现的缝隙,呈不规则的线形,有穿透的和不穿透的两种,在外力的作用下有发展的趋势。
产生原因:1、金属液浇注温度低或模具温度低。
2、合金成分不符合标准,流动性差。
3、金属液分股填充,熔合不良。
4、浇口不合理,流程太长。
5、填充速度低或排气不良。
6、比压偏低。
排除措施:1、适当提高浇注温度和模具温度。
2、改变合金成分,提高流动性。
3、改进浇注系统,加大内浇口速度,改善填充条件。
4、改善排溢条件,增大溢流量。
5、提高压射速度,改善排气条件。
6、提高比压三、擦伤其他名称:拉力、拉痕、粘模伤痕。
特征:顺着脱模方向,由于金属粘附,模具制造斜度太小而造成铸件表面的拉伤痕迹,严重时成为拉伤面。
产生原因:1、型芯、型壁的铸造斜度太小或出现倒斜度。
2、型芯、型壁有压伤痕。
3、合金粘附模具。
4、铸件顶出偏斜,或型芯轴线偏斜。
5、型壁表面粗糙。
6、涂料常喷涂不到。
7、铝合金中含铁量低于%。
排除措施:1、修正模具,保证制造斜度。
2、打光压痕。
3、合理设计浇注系统,避免金属流对冲型芯、型壁,适当降低填充速度。
4、修正模具结构。
5、打光表面。
6、涂料用量薄而均匀,不能漏喷涂料。
压铸件常见缺陷

压铸件常见缺陷一、流痕A其他名称:条纹。
B特征:铸件表面上呈现与金属液流动方向相一致的,用手感觉得出的局部下陷光滑纹路。
此缺陷无发展方向,用抛光法能去处。
C产生原因:1、两股金属流不同步充满型腔而留下的痕迹。
2、模具温度低,如锌合金模温低于150℃,铝合金模温低于180℃,都易产生这类缺陷。
3、填充速度太高。
4、涂料用量过多。
D排除措施:1、调整内浇口截面积或位置。
2、调整模具温度,增大溢流槽。
3、适当调整填充速度以改变金属液填充型腔的流态。
4、涂料使用薄而均匀。
二、冷隔A其他名称:冷接(对接)。
B特征:温度较低的金属流互相对接但未熔合而出现的缝隙,呈不规则的线形,有穿透的和不穿透的两种,在外力的作用下有发展的趋势。
C产生原因:1、金属液浇注温度低或模具温度低。
2、合金成分不符合标准,流动性差。
3、金属液分股填充,熔合不良。
4、浇口不合理,流程太长。
5、填充速度低或排气不良。
6、比压偏低。
D排除措施:1、适当提高浇注温度和模具温度。
2、改变合金成分,提高流动性。
3、改进浇注系统,改善填充条件。
4、改善排溢条件,增大溢流量。
5、提高压射速度,改善排气条件。
6、提高比压。
三、擦伤A其他名称:拉力、拉痕、粘模伤痕。
B特征:顺着脱模方向,由于金属粘附,模具制造斜度太小而造成铸件表面的拉伤痕迹,严重时成为拉伤面。
C产生原因:1、型芯、型壁的铸造斜度太小或出现倒斜度。
2、型芯、型壁有压伤痕。
3、合金粘附模具。
4、铸件顶出偏斜,或型芯轴线偏斜。
5、型壁表面粗糙。
6、涂料常喷涂不到。
7、铝合金中含铁量低于0.6%。
D排除措施:1、修正模具,保证制造斜度。
2、打光压痕。
3、合理设计浇注系统,避免金属流对冲型芯、型壁,适当降低填充速度。
4、修正模具结构。
5、打光表面。
6、涂料用量薄而均匀,不能漏喷涂料。
7、适当增加含铁量至0.6~0.8%。
四、凹陷A其他名称:缩凹、缩陷、憋气、塌边。
B特征:铸件平滑表面上出现的凹瘪的部分,其表面呈自然冷却状态。
铸件常见缺陷(图文并貌)

压铸日常缺陷及分析压铸件抛丸后产品表面变色, 主要是使用的抛丸有问题。
若是使用不锈钢丸,在里面加少量铝丸,抛后产品表面白亮。
压铸件表面经常有霉点,严重影响铸件的外观质量,主要是脱模剂造成。
目前,市面上大大小小生产脱模剂的厂家有一大批,其中不少厂质量存在各种问题,最主要的就是对压铸件会产生腐蚀作用。
一般压铸件厂不太注意,压铸件时间放得长一些,表面就会有白斑(霜状、去掉后呈黑色)出现,实际上已产生腐蚀。
主要是脱模剂中有会产生腐蚀作用的成分。
所以选择脱模剂一定不要只压铸件在抛丸后经常出现表面起皮现象,般由如下一些原因造成:1.模具或压射室(熔杯)未清理干净;2.压射压力不够,(还需注意压射时动模有否退让现象);3.浇注系统开设有点问题,合金液进入型腔有紊流现象;4.模温问题等5.压射时金属液飞溅严重。
脱模剂一般不会渗透到压铸件里面。
但劣质脱模剂会对压铸件表面产生腐蚀作用,而且会向内部渗透;另外,脱模剂发气量大的话,会卷入压铸件里面形成气孔。
如果使用脱模膏之类的涂料不当时,会产生夹渣等缺陷。
丝焊接7005压铸件,在焊接处出现油污和气泡,焊接方式为氩弧焊。
一般存在如下问题:1.焊丝与压铸件表面有油污,未清洗干净; 2.氩气不纯净,市售氩气有的里面杂质多,甚至含有水气,应选优质气。
合金压铸如果出模角度控制不好,经常出现粘模现角,如何来计算这个角度?压铸模出模斜度根据合金和铸件高度不同,有所不同。
一般铝合金压铸件拔模高度从3mm~250 mm:内壁出模斜度按5º30´~0º30´,外壁出模斜度取其一半;圆型芯的出模斜度,按4º~0º30´。
文字符号的出模斜度按10º~15º具体如何细分挡次和各挡次斜度值的选取,请参阅模具设计手册或压铸件标准等资料不进行T6处理. 2.若进行T6处理,表面会变色(灰暗3.变形与否,取决于压铸件本身的形状和在加热炉里放置是否得当.只要注意,一般不会变形. 4.把刚出模的压铸件放进水里,起不到T6的效果.锌合金电镀起泡。
- 1、下载文档前请自行甄别文档内容的完整性,平台不提供额外的编辑、内容补充、找答案等附加服务。
- 2、"仅部分预览"的文档,不可在线预览部分如存在完整性等问题,可反馈申请退款(可完整预览的文档不适用该条件!)。
- 3、如文档侵犯您的权益,请联系客服反馈,我们会尽快为您处理(人工客服工作时间:9:00-18:30)。
在铸件清理或搬运时,损坏了 铸件的完整性。
由于收缩应力或型壁变形、开 裂引起的铸件外形和尺寸与图 纸不符。
渣眼
在铸件内部或表面形状不规 则的孔眼。孔眼不光滑,里 面全部或部分充塞着渣。
股汇合处或激冷部位。
披缝
毛刺
浇不足
பைடு நூலகம்
披缝是铸件表面上厚薄不均匀 毛刺是铸件表面上刺状金属突 由于金属液未完全充满型腔而
的片状金属突起物,常出现在 起物,常出现在型和芯的裂缝 产生的铸件缺肉。
铸件分型面和芯头部位。
处,形状极不规则。
掉砂
缺损
变形
铸件表面的块状金属突起物, 其外形与掉落的砂块很相似。 在铸件其它部位则往往出现砂 眼或残缺。
名称
砂眼
气孔
铸件常见 缺 陷缩 孔
图
片
在铸件表面或内部有充塞着型 在铸件内部、表面或近于表面 形状为不规则的封闭或敞露的
注 砂的孔眼。 释
处有大小不等的光滑孔眼。一 孔洞,孔壁粗糙并带有枝晶
般为圆球形或近似于球形的团 状,常出现在铸件最后凝固的
球形孔洞,孔壁光滑。
部位(热节处)。
名称
粘砂
冷隔
冲砂
图
片
在铸件表面上、全部或部分覆 冷隔是铸件上未完全融合的缝 铸件表面上有粗糙不规则的金
注
盖着金属与砂的混合物,或一 隙 或 洼 坑 , 其 交 接 边 缘 呈 圆 属瘤状物,常位于浇口附近。 层烧结的型砂,致使铸件表面 角,多出现在远离浇口的铸件 在铸件其它部位则往往出现砂
释 粗糙。
宽大上表面和薄壁处、金属流 眼。