铸件粘砂现象及粘沙
高透气性湿型砂铸件表面粘砂控制

粒度 ,取每天做完含泥量的旧砂做为旧砂粒度 ,
高透气 性湿型砂铸件表面粘砂控 制
杜 文科
( 广西玉柴机器股份有限公 司铸 造厂 , 广西 玉林 570 ) 3 0 5
摘要 : 介绍 了生产 H 2 0 T 5 气缸 盖铸件 的型砂 系统构成 , 对铸件 表面粘砂 缺陷进行分析认为是机械粘砂 , 采取提高铸型硬
度, 控制含泥量在工艺上限 , 原砂 SO 量相对偏低时 , i 加入一定 比例 的细新砂等措施 , 有效解决 了问题 。
s r c e e t o h a t g w s a a y e n tw sc n i d t a h e e t smea e e r t n B n r a i g t e mod u f e d f c s f e c si a n l z d a d i a o f me h t e d f c tl n tai . y i ce sn h l a t n r t wa p o
1.%~ 30 A) 1.~ 35 B) 25 1 . %( 和 30 1 . %( 两个 区域 , 进
行 连 续 大批 量生 产 对 比。从 生产 结 果来 看 , B区
域透气性的平均值 比 A区域透气性 的平均值下
降约 1 0个单位。对 比开箱后铸件表面的粘砂情 况可见 , B区域优于 A区域 。
砂 。按其 形 成 原 理 , 砂 分 为 机 械粘 砂 、 学 粘 粘 化
砂、 热粘砂等 。 用湿型砂生产铸铁件 , 由于铁液 中 含有大量的碳 ,不会产生大量 F2 e 等金属氧化 0
物 , 型 中含 有 足够 的煤 粉 , 注 时产 生 的还 原 砂 浇
球墨铸铁管件砂眼现象及粘砂原因分析

球墨铸铁管件砂眼现象及粘砂原因分析球墨铸铁管是以镁或稀土镁结合金球化剂在浇注前加入铁水中,使石墨球化,应力集中降低,使管材具有强度大、延伸率高、耐冲击、耐腐蚀、密封性好等优点;内壁采用水泥砂浆衬里,改善了管道输水环境、提高了供水能力、降低了能耗;管口采用柔性接口,且管材本身具有较大的延伸率,使管道的柔性较好,在埋地管道中能与管道周围的土体共同工作,改善管道的受力状态,从而提高了管网运行的可靠性。
因此,目前我国供水行业通常采用球墨管作为主管材。
一般人们使用的采用涂刷涂料会有铸件出现夹砂,砂眼的情况。
一是因为浇口涂刷涂料比较辛苦和困难。
二就是在浇注过程中浇注温度高,冲刷大,涂料在冲刷和高温浸泡下很容易脱落。
造成夹砂砂眼。
一直以来很多铸件厂不很重视浇道。
忽视了浇注过程中对浇道壁的冲刷。
因此导致了球墨铸铁管铸件夹砂砂眼。
所以为了提高铸件成品率,提高铸件质量,降低铸件总成本。
采用铸造浇口陶管,此产品使用方便,具有流通光滑,耐铁水,钢水冲刷,不吸收钢水,可锯性佳等特点,可以简化造型工艺,省去浇口内侧上涂料的困难工作,并对改善浇注系统的布置,避免铸件冲砂,砂眼,加砂缺陷。
这可以说就是最好的办法了,大家可以来采用一下。
球墨铸铁管件由于它的使用环境,出现腐蚀现象也是不可避免的,因此,就需要我们了解如何应对球墨管砂眼现象。
球墨铸管件粘砂的原因分析1。
足够的压力使金属液渗人砂粒之间较高的金属液静压力头。
即由铸件浇注高度和浇注系统形成的压力。
如该压力超过砂粒间隙之间毛细现象形成的抵挡压力。
即尸毛=QcosO/r,式中P毛为毛细压力;。
球墨铸管件为金属液表面张力;e为金属液毛细管的润湿角;r为毛细管半径。
就会形成机械粘砂。
静压力头超过500mm,锻造用砂又较粗,多数会产气愤但愿械粘砂,除非上涂料。
上式亦说明:越大,即砂粒粒度越粗,尸毛越小,即较易产气愤但愿械粘砂。
2。
金属液在铸型内流动形成的动压力。
3。
铸型“爆”或“呛”。
谈砂型铸造表面缺陷

漫谈湿砂型铸件表面缺陷与其它铸造方法相比,湿型铸件是较容易产生粘砂、砂孔、夹砂、气孔等缺陷的。
如果铸造工厂注意控制湿型砂的品质,这些缺陷本来是有可能减少或避免。
以下用实例说明型砂性能与铸件表面缺陷的关系。
一.粘砂研究工作表明,一般湿砂型铸件,不论铸钢还是铸铁,粘砂缺陷都是属于机械粘砂,而不是化学粘砂。
机械粘砂的产生原因有多种,最多见的如下的实例:1.砂粒太粗和透气性过高,金属液容易钻入砂粒间孔隙,使铸件表面粗糙,或将砂粒包裹固定在表面上。
江苏某外资工厂的铸铁旧砂中不断混入大量30/50目粗粒芯砂,以致型砂透气性达到220以上,铸件表面极为粗糙。
内蒙某工厂铸钢车间的气动微震造型机生产中、小铸件。
使用主要集中在40目的40/70粗粒石英砂混制型砂,铸件表面产生严重粘砂。
平时不检测型砂透气性,认为已经符合工艺规程规定的≥80。
为了找到粘砂原因而专门检测一次,发现透气性居然高达1070左右,表明这就是产生粘砂的原因。
因此型砂透气性必须有上限,型砂粒度粗细和透气性应当处于适宜范围内。
一般震压机器造型单一砂最适宜的型砂粒度大多为70/140目,透气性大致为70~100,高密度造型的型砂粒度最好是50/140或100/50,透气性为80~140。
有些生产发动机的铸造厂大量使用50/100目粗原砂制造砂芯,落砂时不断混入旧砂中,使型砂透气性可能达到180以上,就应加入100/140目细砂,或将旋流分离器中的细颗粒部分返回到旧砂中,以便纠正型砂粒度。
2.铸铁型砂中煤粉含量不足或煤粉品质不良。
北京某铸造厂生产高速列车刹车盘,铸件材质符合要求,而表面有严重粘砂,需整体打磨后才能交货。
型砂中所用煤粉来自郊区一家关系密切的私营小供应商。
粘砂的产生原因可能是煤粉品质太差,还可能是型砂中有效煤粉量也不足够。
安徽某阀门总厂使用的“煤粉”是生产焦炭洗选下来的废料,灰分高达76%。
使用后整个型砂性能遭破坏,铸件废品超过一半。
铸造工厂应该对购入的煤粉品质加强检验。
铸件粘砂的原因及处理
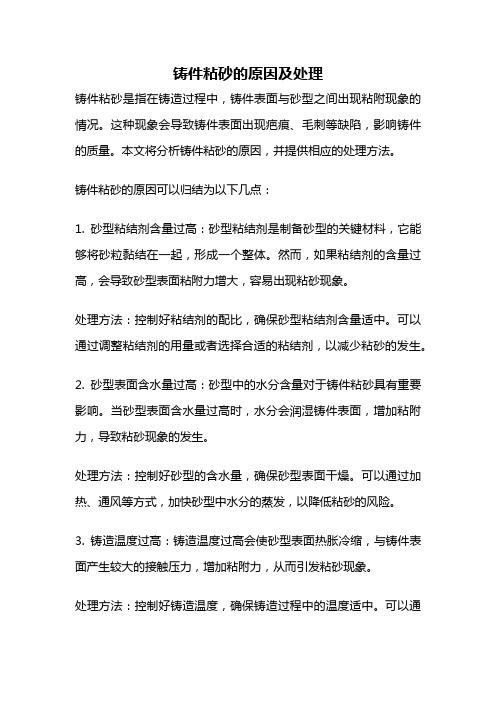
铸件粘砂的原因及处理铸件粘砂是指在铸造过程中,铸件表面与砂型之间出现粘附现象的情况。
这种现象会导致铸件表面出现疤痕、毛刺等缺陷,影响铸件的质量。
本文将分析铸件粘砂的原因,并提供相应的处理方法。
铸件粘砂的原因可以归结为以下几点:1. 砂型粘结剂含量过高:砂型粘结剂是制备砂型的关键材料,它能够将砂粒黏结在一起,形成一个整体。
然而,如果粘结剂的含量过高,会导致砂型表面粘附力增大,容易出现粘砂现象。
处理方法:控制好粘结剂的配比,确保砂型粘结剂含量适中。
可以通过调整粘结剂的用量或者选择合适的粘结剂,以减少粘砂的发生。
2. 砂型表面含水量过高:砂型中的水分含量对于铸件粘砂具有重要影响。
当砂型表面含水量过高时,水分会润湿铸件表面,增加粘附力,导致粘砂现象的发生。
处理方法:控制好砂型的含水量,确保砂型表面干燥。
可以通过加热、通风等方式,加快砂型中水分的蒸发,以降低粘砂的风险。
3. 铸造温度过高:铸造温度过高会使砂型表面热胀冷缩,与铸件表面产生较大的接触压力,增加粘附力,从而引发粘砂现象。
处理方法:控制好铸造温度,确保铸造过程中的温度适中。
可以通过调整熔炼温度、浇注速度等方式,控制铸造温度在合适的范围内,以减少粘砂的发生。
4. 铸造速度过快:当铸造速度过快时,砂型表面与铸件表面的接触时间较短,难以形成良好的粘结力,容易导致粘砂问题。
处理方法:控制好铸造速度,确保铸造过程中的速度适中。
可以通过调整浇注速度、铸型的设计等方式,使铸造速度与砂型的接触时间相匹配,以减少粘砂的发生。
5. 金属表面未做处理:金属表面的处理对于粘砂问题也有一定影响。
未经过适当处理的金属表面可能存在氧化物、污垢等,会增加砂型与铸件表面的粘附力,导致粘砂问题。
处理方法:对金属表面进行适当处理,去除氧化物、污垢等杂质。
可以通过酸洗、喷丸等方式,使金属表面保持清洁,并增加其粗糙度,以减少粘砂的发生。
铸件粘砂是由多种原因造成的,包括砂型粘结剂含量过高、砂型表面含水量过高、铸造温度过高、铸造速度过快以及金属表面未做处理等。
铸件表面粘砂的原因和解决方法

铸件表面粘砂的原因和解决方法哎呀,说起铸件表面粘砂这事儿,我可是深有体会。
记得有一回,我在工厂实习的时候,就遇到了这么一个头疼的问题。
那会儿,我们正在做一批汽车发动机的铸件,结果出炉的时候,发现铸件表面粘满了砂子,那画面,简直了,就像刚从沙滩上挖出来的土豆一样。
首先,咱们得搞清楚,为啥铸件会粘砂。
其实,原因挺多,但最常见的就是砂型太干,或者是涂料没涂好。
你想啊,砂型要是太干,砂子就容易脱落,然后粘在铸件上。
涂料没涂好,那就更别提了,砂子就像找到了新家一样,牢牢地粘在上面。
那会儿,我们师傅一看这情况,眉头一皱,就知道事情不妙。
他先检查了砂型,发现砂型确实有点干,然后又看了看涂料,发现涂得也不均匀。
师傅说,这事儿得一步步来解决。
首先,他调整了砂型的湿度,让砂子保持在一个合适的湿度范围内。
这就好比是做菜,水多了不行,水少了也不行,得刚刚好。
然后,他又重新调配了涂料,确保涂料的粘度和流动性都合适。
这涂料啊,就像是给铸件穿上了一层保护衣,既能保护铸件不粘砂,又能让它表面光滑。
接下来,师傅还调整了浇注的速度和温度。
这浇注速度啊,就像倒水一样,太快了,水花四溅,太慢了,水又倒不出来。
温度呢,太高了,铸件容易变形,太低了,砂子又容易粘在上面。
所以,这速度和温度都得控制得刚刚好。
经过师傅这么一调整,再出炉的铸件,那叫一个光滑,就跟镜子一样,一点砂子都没有。
我们这些实习生看了,都忍不住啧啧称赞。
所以啊,解决铸件粘砂的问题,其实就跟做饭一样,得讲究火候和配料。
砂型、涂料、浇注速度和温度,这些因素都要考虑进去。
只要把这些细节都处理好了,那铸件表面粘砂的问题,自然就迎刃而解了。
最后,我想说的是,虽然这只是一个小小的生产问题,但它教会了我一个道理:不管做什么事情,细节真的很重要。
就像我们写文章一样,细节描写得越丰富,文章就越生动,越能打动人心。
所以,不管是铸件,还是写作,都得多注意细节,这样才能做出好作品。
铸件粘砂的原因及处理

铸件粘砂的原因及处理
铸件粘砂是铸造过程中常见的一种问题,它会影响到铸件的质量和生
产效率。
以下是铸件粘砂的原因及处理方法。
一、原因
1. 粘合剂不当:粘合剂含量过高或过低、粘合剂与沙子混合不均匀等
都会导致铸件粘砂。
2. 沙子质量差:沙子中含有杂质、水分过高等都会导致铸件粘砂。
3. 烘干温度不当:沙子在烘干时温度过高或过低都会导致铸件粘砂。
4. 铸造温度不当:铸造温度过高或过低都会导致铸件粘砂。
5. 铸造压力不足:如果压力不足,就无法使沙子紧密地填充模具,从
而导致铸件粘砂。
二、处理方法
1. 调整粘合剂配比:根据实际情况调整粘合剂的配比,确保混合均匀,
并控制好含量,以避免出现问题。
2. 选择优质沙子:选择品质良好的沙子,减少沙子中的杂质,降低水分含量,以避免铸件粘砂。
3. 控制烘干温度:控制好烘干温度,确保沙子干燥透彻,以避免铸件粘砂。
4. 控制铸造温度:根据实际情况控制好铸造温度,确保合适的温度范围内进行铸造,以避免出现问题。
5. 增加铸造压力:增加铸造压力可以使沙子更加紧密地填充模具,从而减少铸件粘砂的发生。
6. 做好清理工作:及时清理模具中残留的沙子和杂质等物质,以保证下一次使用时不会出现问题。
总之,在进行铸造过程中要注意各个环节的控制和调整,并及时处理出现的问题。
只有这样才能保证生产效率和产品质量。
粘土砂铸造工艺

粘土砂铸造工艺LG GROUP system office room 【LGA16H-LGYY-LGUA8Q8-LGA162】粘土砂铸造工艺一.概述粘土砂是以粘土(陶土)作粘结剂的型(芯)砂。
粘土砂造型由于其成本低廉,适合于批量大规模生产,所以目前仍然作为铸件生产的最主要方式。
粘土砂旧沙由于在循环使用过程中各组份的热分解,发生物理性能的变化,如未经再生就加以使用,将使型砂质量不稳定。
据统计铸件废品率中30~40%为型砂质量引起,因此型砂质量的控制在粘土砂造型中起十分重要的作用。
随着目前对铸件要求的提高,对型砂质量的要求也越来越高。
二.粘土砂造型中几种与型砂质量有关的常见缺陷。
1.气孔、浇不到、冷隔粘土砂型砂的组成绝大部分为旧砂(85~95%),由于旧砂循环使用过程中经过反复热冲击,一些组分会出现热分解,发生物理性能的变化:a. 粘土在砂型温度高于500度的区域,膨润土晶体结构受到完全破坏,就变成没有湿态粘结力的无效粘土以粉尘状态存在与旧砂中,成为旧砂泥份中的一种;b. 煤粉炭化成为枯化物;c. 不稳定的砂粒(包含杂质)会粉化。
这些衍生物共同成为旧砂的微粉。
微粉含量超过一定的限度,微粉堵塞砂砾空隙就会造成型砂透气性差。
而且无效粘土吸水能力比有效粘土强,从有效粘土中夺取有效水分,因此当无效粘土含量较多时,达到调匀所需的加水量就得增加。
加大了型砂加水量,在某种程度上也就加大了型砂的发气量。
由于发气量增加而透气性减少,浇铸时液体所收的阻力增大,必然导致侵入性气孔、浇不到、冷隔等缺陷的形成。
2.表面光洁度差(包括砂眼、毛刺、夹砂结疤等)大量的无效粘土造成型砂的抗拉强度差、韧性低、透气性差。
增大型砂的脆性,使型砂易塌箱、掉砂,在浇铸时砂粒容易掉落形成砂眼、毛刺、夹渣结疤等缺陷,进而影响铸件质量。
3.粘砂无效粘土(死黏土)部分约占整个砂型重的2~5%,无效粘土的一部分在高温作用下包裹在砂粒表面上,烧结形成一层牢固的膜,不能用水洗掉,成为砂粒的一部分,这层膜又称为惰性膜。
铸件机械粘砂的产生原因及其防止措施【建筑工程类独家文档首发】
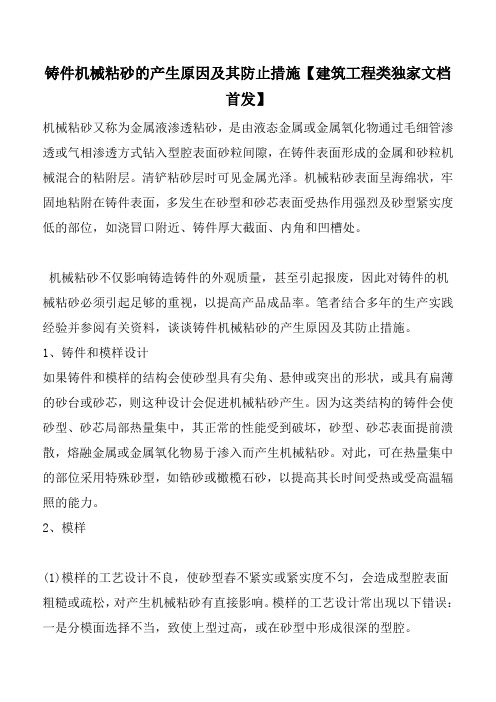
铸件机械粘砂的产生原因及其防止措施【建筑工程类独家文档首发】机械粘砂又称为金属液渗透粘砂,是由液态金属或金属氧化物通过毛细管渗透或气相渗透方式钻入型腔表面砂粒间隙,在铸件表面形成的金属和砂粒机械混合的粘附层。
清铲粘砂层时可见金属光泽。
机械粘砂表面呈海绵状,牢固地粘附在铸件表面,多发生在砂型和砂芯表面受热作用强烈及砂型紧实度低的部位,如浇冒口附近、铸件厚大截面、内角和凹槽处。
机械粘砂不仅影响铸造铸件的外观质量,甚至引起报废,因此对铸件的机械粘砂必须引起足够的重视,以提高产品成品率。
笔者结合多年的生产实践经验并参阅有关资料,谈谈铸件机械粘砂的产生原因及其防止措施。
1、铸件和模样设计如果铸件和模样的结构会使砂型具有尖角、悬伸或突出的形状,或具有扁薄的砂台或砂芯,则这种设计会促进机械粘砂产生。
因为这类结构的铸件会使砂型、砂芯局部热量集中,其正常的性能受到破坏,砂型、砂芯表面提前溃散,熔融金属或金属氧化物易于渗入而产生机械粘砂。
对此,可在热量集中的部位采用特殊砂型,如锆砂或橄榄石砂,以提高其长时间受热或受高温辐照的能力。
2、模样(1)模样的工艺设计不良,使砂型舂不紧实或紧实度不匀,会造成型腔表面粗糙或疏松,对产生机械粘砂有直接影响。
模样的工艺设计常出现以下错误:一是分模面选择不当,致使上型过高,或在砂型中形成很深的型腔。
二是模样在模底板上的位置布置不当,使凹陷处难于舂实,这可能是由于模样距箱壁太近,或模样排列过密所致。
由于模样排列过于拥挤,会引起铸件产生胀砂,即使没有明显的胀砂,也会发生机械粘砂。
由于产生缺陷的根源相同,机械粘砂和胀砂会出现在同一个铸件上。
三是直浇道、冒口和横浇道的位置布置不当,会出现不易舂实的凹陷部位,这与浇冒口系统的布局有关。
四是起模斜度<1.5°时,即使整个砂型的紧实度合适,也会使砂型表面撕裂,易于使金属或金属氧化物渗入。
(2)模样的工艺结构不良,导致金属液静压力过高。
- 1、下载文档前请自行甄别文档内容的完整性,平台不提供额外的编辑、内容补充、找答案等附加服务。
- 2、"仅部分预览"的文档,不可在线预览部分如存在完整性等问题,可反馈申请退款(可完整预览的文档不适用该条件!)。
- 3、如文档侵犯您的权益,请联系客服反馈,我们会尽快为您处理(人工客服工作时间:9:00-18:30)。
铸件粘砂现象及粘沙原因
铸件粘砂不仅影响铸件的外观质量,甚至引起报废。
因此,必须对铸件的粘砂引起足够的重视。
一、粘砂现象
1.机械粘砂系金属液渗人砂型或砂芯砂粒间隙中,与砂烧结并粘附在铸件表面。
它可以是薄薄的一层,也可能是数毫米的厚层。
金属液有时会渗透到砂芯的整个截面,致使内腔阻塞,这种粘砂往往是不可能清除的,铸件不得不报废。
2.化学粘砂系金属液化学反应生成的金属氧化物与造型材料作用形成的粘着力很强的
硅酸铁浮渣。
它多产生在铸件内浇口或厚壁处,尤其当砂型或砂芯较薄而铸件较厚时较易产生。
3.化学粘砂与机械粘砂的简易鉴别,在于前者粘砂层中往往不含有金属铁。
二、粘砂原因
1.足够的压力使金属液渗人砂粒之间较高的金属液静压力头。
即由铸件浇注高度和浇注系统形成的压力。
如该压力超过砂粒间隙之间毛细现象形成的抵抗压力。
即尸毛=QcosO/r,式中P毛为毛细压力;。
为金属液表面张力;e为金属液毛细管的润湿角;r为毛细管半径。
就会形成机械粘砂。
静压力头超过500 mm,铸造用砂又较粗,多数会产生机械粘砂,除非上涂料。
上式亦说明:越大,即砂粒粒度越粗,尸毛越小,即较易产生机械粘砂。
2.金属液在铸型内流动形成的动压力。
3.铸型“爆”或“呛”。
即铸型浇注时释放的可燃气体与空气混合并被炽热金属液点燃所形成的动压力。
4.机械粘砂一经开始,即便压力减小,金属液渗透还会继续进行,直到渗透金属液前沿凝固。
即金属液温度低于固相线温度,渗透方可停止。
5.化学粘砂最通常的原因是湿型和制芯用原材料耐火度、烧结点低;石英砂不纯;煤粉或代用品加人不足;没有使用涂料或使用不当;浇注温度过高;浇注不当致使渣子进人铸型等因
素造成。