Citisteel 4060mm宽厚板轧机板形问题的分析和改进措施_宽厚板_2000tr
轧制缺陷图谱、形成原因分析以及预防措施

缺陷名称纵裂Longitudinal Crack照片缺陷形貌及特征:缺陷形貌及特征纵裂纹是距钢板边部有一定距离的沿轧制方向裂开的小裂口或有一定宽度的线状裂纹。
板厚大于20mm的钢板出现纵裂纹的机率较大。
缺陷成因:1. 板坯凝固过程中坯壳断裂,出结晶器后进一步扩展形成板坯纵向裂纹,在轧制过程中沿轧制方向扩展并开裂;2. 板坯存在横裂,在横向轧制过程中扩展和开裂形成。
预防:防止纵列纹产生的有效措施是使板坯坯壳厚度均匀,稳定冶炼,连铸工艺是减少纵裂纹产生的关键推荐处理措施:1. 深度较浅的纵裂可采用修磨去除。
2. 修磨后剩余厚度不满足合同要求的钢板可采用火切切除、改规的方法,由于纵裂有一定长度,一般不采用焊补的方法挽救;3. 纵裂面积较大时钢板可直接判次或判废可能混淆的缺陷1. 边部折叠2. 边部线状缺陷缺陷名称横裂Transverse Crack缺陷形貌及特征:缺陷形貌及特征:裂纹与钢板轧制方向呈30°~90°夹角,呈不规则的条状或线状等形态,有可能呈M或Z型,横向裂纹通常有一定的深度。
缺陷成因:板坯在凝固过程中,局部产生超出材料迁都极限的拉伸应力导致板坯横裂,在轧制过程中扩展和开裂形成。
有可能是板坯振痕过深,造成钢坯横向微裂纹;钢坯中铝,氮含量较高,促使AIN沿奥氏体晶界析出,也可能诱发横裂纹;二次冷却强度过高也会造成板坯上的横裂预防:1. 减少板坯振痕;2. 控制板坯表面温度均匀并尽量减少板坯表面和边部的温度差;3. 根据钢中不同合力选用保护渣;4. 合理控制钢中的铝、氮含量。
推荐处理措施:1. 深度较浅的横裂可用修磨的方法去除;2. 修磨后剩余厚度不满足合同要求的钢板可采用厚度改规或切除缺陷后改尺的方法;3. 缺陷面积较大时钢板可直接判次或判废;可能混淆的缺陷1. 夹渣2. 折叠3. 星型裂纹缺陷名称边裂Edge Crack缺陷形貌及特征:边部裂纹是钢板边部表面开口的月牙型,半圆型裂口,通常位于钢板单侧或两侧100mm 范围内,一般沿钢板边部密集分布。
影响宽厚板成材率的因素及改进措施
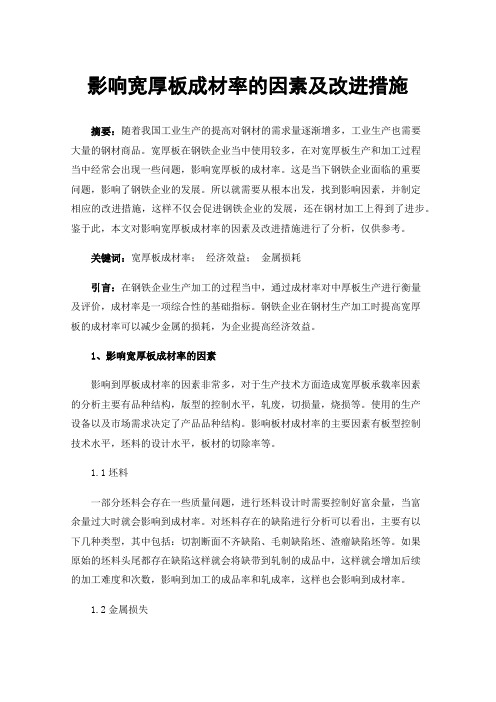
影响宽厚板成材率的因素及改进措施摘要:随着我国工业生产的提高对钢材的需求量逐渐增多,工业生产也需要大量的钢材商品。
宽厚板在钢铁企业当中使用较多,在对宽厚板生产和加工过程当中经常会出现一些问题,影响宽厚板的成材率。
这是当下钢铁企业面临的重要问题,影响了钢铁企业的发展。
所以就需要从根本出发,找到影响因素,并制定相应的改进措施,这样不仅会促进钢铁企业的发展,还在钢材加工上得到了进步。
鉴于此,本文对影响宽厚板成材率的因素及改进措施进行了分析,仅供参考。
关键词:宽厚板成材率;经济效益;金属损耗引言:在钢铁企业生产加工的过程当中,通过成材率对中厚板生产进行衡量及评价,成材率是一项综合性的基础指标。
钢铁企业在钢材生产加工时提高宽厚板的成材率可以减少金属的损耗,为企业提高经济效益。
1、影响宽厚板成材率的因素影响到厚板成材率的因素非常多,对于生产技术方面造成宽厚板承载率因素的分析主要有品种结构,版型的控制水平,轧废,切损量,烧损等。
使用的生产设备以及市场需求决定了产品品种结构。
影响板材成材率的主要因素有板型控制技术水平,坯料的设计水平,板材的切除率等。
1.1坯料一部分坯料会存在一些质量问题,进行坯料设计时需要控制好富余量,当富余量过大时就会影响到成材率。
对坯料存在的缺陷进行分析可以看出,主要有以下几种类型,其中包括:切割断面不齐缺陷、毛刺缺陷坯、渣瘤缺陷坯等。
如果原始的坯料头尾都存在缺陷这样就会将缺带到轧制的成品中,这样就会增加后续的加工难度和次数,影响到加工的成品率和轧成率,这样也会影响到成材率。
1.2金属损失金属损失是影响中厚板成材率的重要因素,在中厚板生产过程中会造成多种金属损失。
在中厚板生产过程当中,出现金属损失十分普遍,也是重要的消耗。
在一般情况下,金属损失大于产品成本一半以上。
只有通过恰当的方式控制金属损失,才可以起到节约金属的效果,中厚板加工的成材率也会随时提升。
中厚板生产进行分析可以看出金属损失可以分为两种,一种是物理损耗,需要对中厚板进行切头、切尾、切边等处理,这样就会产生很多的废料,出现浪费的情况。
02-宽厚板连铸坯的主要缺陷及防止措施.

宽厚板连铸坯的主要缺陷及防止措施程士富孙中强东北大学沈阳110004沈阳东北大学冶金技术研究所有限公司沈阳110004摘要:根据工厂全年生产统计结果,确定宽厚板连铸坯(以船板钢为主)主要缺陷为连铸坯纵横裂纹及轧材的冷弯和拉伸合格率低。
对产生原因结合生产实际进行分析,提出改进措施,使铸坯和轧材质量得到明显改善。
关键词:宽厚板;纵裂纹;横裂纹;冷弯性能;拉伸性能1前言宽厚板中的管线钢、船板钢、低温容器钢等,对钢材性能和质量要求极为严格,既要求高强度又要求高韧性,对焊接性能、疲劳性、耐腐蚀性、抗氢致裂纹、抗层状撕裂性等多方面均有较高或极为严格要求。
为保证钢材性能,要求钢材极低的有害元素、气体和夹杂物含量,其中P≤0.010%,S≤0.0010%,N≤0.0050%,H≤0.00025%,TO≤0.0020%;夹杂物形态应为分散细小,应消除大颗粒夹杂物,变条形MS为细小球状,又要求钢材具有良好表n面质量和内部质量。
宽厚板为保证强度和韧性的匹配,成品设计采用低碳高锰的原则,并加入微量元素Nb、V、Ti等,钢的等效含碳量多为包晶钢,所以铸坯易产生表面缺陷;宽厚板由于轧材厚度大,使轧材压缩比小,不易消除铸坯中心缺陷,轧材难以保证内部质量。
连铸坯质量控制:就是如何同时改善铸坯表面和中心质量,以达到保证轧材的表面质量和内部质量。
2宽厚板主要缺陷根据国内F厂2007年主要缺陷种类如表1表12007年炼钢缺陷统计表缺陷或性能种类块数重量(T)发裂94290.870分层3391.933夹杂67224.658夹渣618.001结疤5792244.545裂纹330313794.8530气泡4272091.963气泡、结疤18.860结疤、裂纹741.853小计451718807.520冷弯32577983.556延伸6032524.251屈服、冷弯1 3.140延伸、冷弯95310.021抗拉、延伸618.991抗拉、冷弯617.405延伸、冲击37.536冲击、延伸、冷弯1128.376冲击、抗拉、冷弯37.580抗拉、延伸、冷弯722.351冷弯、冲击3354.217化学成分不合38.761小计402810986.195合计854529793.7152007年炼钢合格率:97.84%从全年炼钢废品统计看,铸坯缺陷主要是裂纹,性能不合的主要是冷弯和延伸,因此必须查清原因,采取相应措施,提高炼钢合格率。
轧制缺陷及质量控制
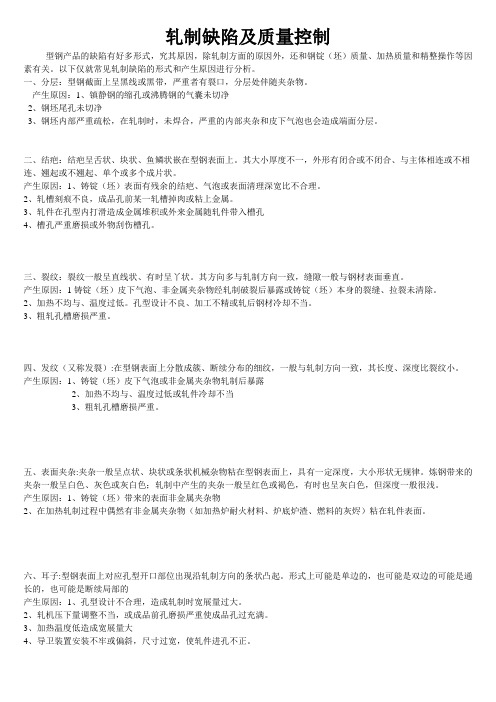
轧制缺陷及质量控制型钢产品的缺陷有好多形式,究其原因,除轧制方面的原因外,还和钢锭(坯)质量、加热质量和精整操作等因素有关。
以下仅就常见轧制缺陷的形式和产生原因进行分析。
一、分层:型钢截面上呈黑线或黑带,严重者有裂口,分层处伴随夹杂物。
产生原因:1、镇静钢的缩孔或沸腾钢的气囊未切净2、钢坯尾孔未切净3、钢坯内部严重疏松,在轧制时,未焊合,严重的内部夹杂和皮下气泡也会造成端面分层。
二、结疤:结疤呈舌状、块状、鱼鳞状嵌在型钢表面上。
其大小厚度不一,外形有闭合或不闭合、与主体相连或不相连、翘起或不翘起、单个或多个成片状。
产生原因:1、铸锭(坯)表面有残余的结疤、气泡或表面清理深宽比不合理。
2、轧槽刻痕不良,成品孔前某一轧槽掉肉或粘上金属。
3、轧件在孔型内打滑造成金属堆积或外来金属随轧件带入槽孔4、槽孔严重磨损或外物刮伤槽孔。
三、裂纹:裂纹一般呈直线状、有时呈丫状。
其方向多与轧制方向一致,缝隙一般与钢材表面垂直。
产生原因:1铸锭(坯)皮下气泡、非金属夹杂物经轧制破裂后暴露或铸锭(坯)本身的裂缝、拉裂未清除。
2、加热不均与、温度过低。
孔型设计不良、加工不精或轧后钢材冷却不当。
3、粗轧孔槽磨损严重。
四、发纹(又称发裂):在型钢表面上分散成簇、断续分布的细纹,一般与轧制方向一致,其长度、深度比裂纹小。
产生原因:1、铸锭(坯)皮下气泡或非金属夹杂物轧制后暴露2、加热不均与、温度过低或轧件冷却不当3、粗轧孔槽磨损严重。
五、表面夹杂:夹杂一般呈点状、块状或条状机械杂物粘在型钢表面上,具有一定深度,大小形状无规律。
炼钢带来的夹杂一般呈白色、灰色或灰白色;轧制中产生的夹杂一般呈红色或褐色,有时也呈灰白色,但深度一般很浅。
产生原因:1、铸锭(坯)带来的表面非金属夹杂物2、在加热轧制过程中偶然有非金属夹杂物(如加热炉耐火材料、炉底炉渣、燃料的灰烬)粘在轧件表面。
六、耳子:型钢表面上对应孔型开口部位出现沿轧制方向的条状凸起。
钢管轧制存在质量问题的原因及改进措施

一穿轧制存在的质量问题1、毛管外径偏大或偏小原因:①辊距偏大或偏小②导板板距偏大或偏小③顶头位置向前或靠后④顶头直径偏大或偏小⑤轧辊径向串动量太大⑥上导板座没有固定,上下跳动量大改进措施:根据轧制表的参数选择合适的辊距,导板距,顶头伸入量及顶头直径,加强轧辊和导板的固定,正常轧制时,辊距和导板距保证相对稳定,不能轻易调整,若钢管偏厚或偏薄,可采取进、退顶杆的方法。
2、壁厚严重不均原因:①一穿三个轧辊的外径大小不一②三个轧辊偏离轧制线③三个轧辊调整后不成等边三角形,轧辊前后距轧机牌坊距离不一致;④定心辊未抱住顶杆甩动严重⑤定心孔不对中⑥穿孔机受料槽、一穿轧机、定心机架、顶杆小车的机械中心线不对⑦轧辊轧制过程中跳动太大;⑧顶杆位置过后;⑨轧辊直径过小,轧制大规格钢管时产生滑动现象;改进措施:①安装轧辊时先要测量三个轧辊的辊径,保持三个轧辊的辊径一致;②调整轧制中心线,俣证轧制中心线与穿孔中心线重合,然后可使轧制中心线略低于穿孔中心线0-5mm;③将三个轧辊调整后成等边三角形,保证三个轧辊在轧制过程中受力一致,轧辊前后距牌坊距离一致;④调整定心辊,保证在空载时能抱住顶杆,并使顶杆的水平线与穿孔中心线重合;⑤保证定心孔对中;⑥要求设备测试中心线,保证穿孔机受料槽、一穿轧机、定心机架、顶杆小车的机械中心线在一条水平直线上;⑦临时用铁片调整间隙,保证跳动值不超标。
⑧调整到合适的顶杆位置;⑨更换轧辊,选择合适辊径的轧辊,当辊径小于一定值,予以报废。
3、头尾外径不一致(头大尾小)原因:①坯料加热温度不均匀,头部温度偏低;②穿孔过程中轧辊在辊箱中抖动③穿孔中误动作侧压进装置④管坯开始变形时顶头的轴向阻力加大,轴向延伸受阻,延伸变形减小,横向变形(扩径)加大⑤管坯尾部顶透时轴向阻力减小,使延伸变形容易,同时横向辗轧减小,因而尾部直径变小改进措施:按加热制度加热,保证钢温一致;采取措施固定轧辊,使轧辊在辊箱中不串动;提高操作水平,减少误动作,加强调整,保证轴向变形与横向变形同步。
【轧机修复】轧机机架与衬板结合面磨损快速解决
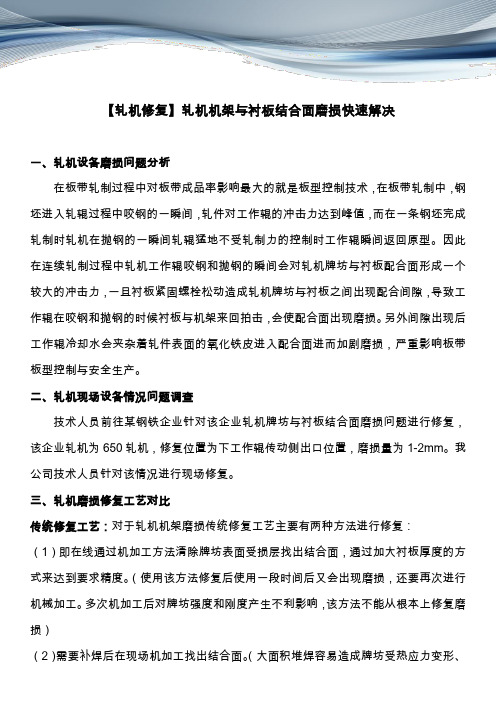
【轧机修复】轧机机架与衬板结合面磨损快速解决一、轧机设备磨损问题分析在板带轧制过程中对板带成品率影响最大的就是板型控制技术,在板带轧制中,钢坯进入轧辊过程中咬钢的一瞬间,轧件对工作辊的冲击力达到峰值,而在一条钢坯完成轧制时轧机在抛钢的一瞬间轧辊猛地不受轧制力的控制时工作辊瞬间返回原型。
因此在连续轧制过程中轧机工作辊咬钢和抛钢的瞬间会对轧机牌坊与衬板配合面形成一个较大的冲击力,一旦衬板紧固螺栓松动造成轧机牌坊与衬板之间出现配合间隙,导致工作辊在咬钢和抛钢的时候衬板与机架来回拍击,会使配合面出现磨损。
另外间隙出现后工作辊冷却水会夹杂着轧件表面的氧化铁皮进入配合面进而加剧磨损,严重影响板带板型控制与安全生产。
二、轧机现场设备情况问题调查技术人员前往某钢铁企业针对该企业轧机牌坊与衬板结合面磨损问题进行修复,该企业轧机为650轧机,修复位置为下工作辊传动侧出口位置,磨损量为1-2mm。
我公司技术人员针对该情况进行现场修复。
三、轧机磨损修复工艺对比传统修复工艺:对于轧机机架磨损传统修复工艺主要有两种方法进行修复:(1)即在线通过机加工方法清除牌坊表面受损层找出结合面,通过加大衬板厚度的方式来达到要求精度。
(使用该方法修复后使用一段时间后又会出现磨损,还要再次进行机械加工。
多次机加工后对牌坊强度和刚度产生不利影响,该方法不能从根本上修复磨损)(2)需要补焊后在现场机加工找出结合面。
(大面积堆焊容易造成牌坊受热应力变形、弯曲。
且修复好之后在生产中配合面和固定座长期配合受冲击、腐蚀又会出现磨损。
也不能根本上解决磨损,且工期长。
消耗了企业大量人力、物力、财力。
福世蓝修复工艺:使用复合材料技术产品现场修复时间短,效果好。
其产品自身具有极高的抗压强度,即使在高达1900吨的轧制力作用下,材料也不会损坏;独特的高分子结构赋予材料良好的抗冲击性能,可以吸收固定座对牌坊的冲击,避免了磨损的产生;同时产品具有良好的耐腐蚀性能,可使配合面表面免受冷却水的侵蚀。
宽厚板剪切质量改进措施
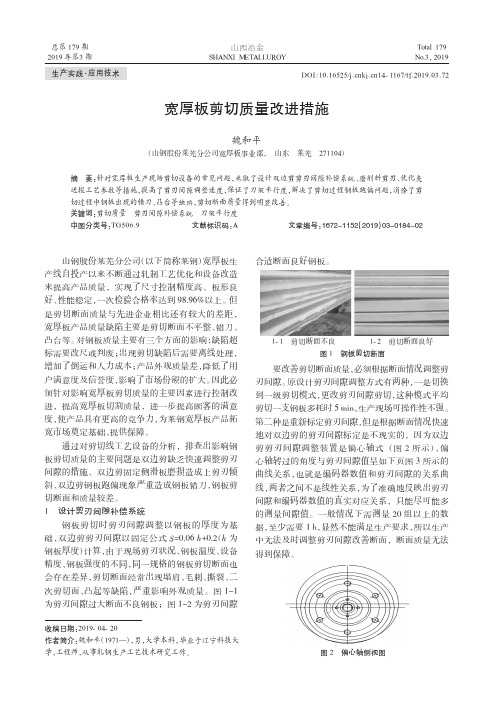
生产实践·应用技术山西冶金SHANXI M ETALLURGYTotal179No.3,2019DOI:10.16525/14-1167/tf.2019.03.72总第179期2019年第3期宽厚板剪切质量改进措施魏和平(山钢股份莱芜分公司宽厚板事业部,山东莱芜271104)摘要:针对宽厚板生产现场剪切设备的常见问题,采取了设计双边剪剪刃间隙补偿系统、磨削斜剪刃、优化夹送辊工艺参数等措施,提高了剪刃间隙调整速度,保证了刀架平行度,解决了剪切过程钢板跑偏问题,消除了剪切过程中钢板出现的错刀、凸台等缺陷,剪切断面质量得到明显改善。
关键词:剪切质量剪刃间隙补偿系统刀架平行度中图分类号:TG506.9文献标识码:A文章编号:1672-1152(2019)03-0184-02收稿日期:2019-04-20作者简介:魏和平(1971—),男,大学本科,毕业于辽宁科技大学,工程师,从事轧钢生产工艺技术研究工作。
1-1剪切断面不良1-2剪切断面良好图1钢板剪切断面图2偏心轴侧视图山钢股份莱芜分公司(以下简称莱钢)宽厚板生产线自投产以来不断通过轧制工艺优化和设备改造来提高产品质量,实现了尺寸控制精度高、板形良好、性能稳定,一次检验合格率达到98.96%以上。
但是剪切断面质量与先进企业相比还有较大的差距,宽厚板产品质量缺陷主要是剪切断面不平整、错刀、凸台等。
对钢板质量主要有三个方面的影响:缺陷超标需要改尺或判废;出现剪切缺陷后需要离线处理,增加了倒运和人力成本;产品外观质量差,降低了用户满意度及信誉度,影响了市场份额的扩大。
因此必须针对影响宽厚板剪切质量的主要因素进行控制改进,提高宽厚板切割质量,进一步提高顾客的满意度,使产品具有更高的竞争力,为莱钢宽厚板产品拓宽市场奠定基础、提供保障。
通过对剪切线工艺设备的分析,排查出影响钢板剪切质量的主要问题是双边剪缺乏快速调整剪刃间隙的措施、双边剪固定侧滑板磨损造成上剪刃倾斜、双边剪钢板跑偏现象严重造成钢板错刀,钢板剪切断面和质量较差。
板形缺陷及预防措施
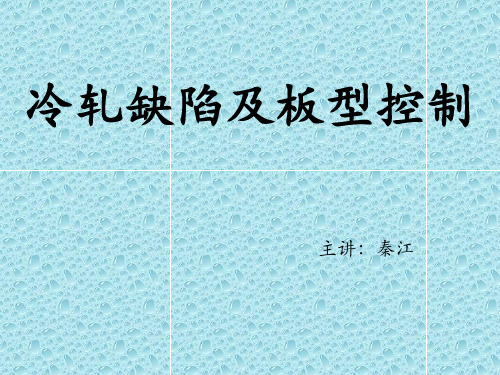
原因:带卷头部卷取张力过小,轧制规格薄。
措施:提高头部卷取张力,一般应大于设定张力20~30%, 适当增大带头厚度,必要时更换小直径卷筒。
4.抽心 卸卷时,卷取机卷筒将卷心部分带出,或是热处理吊车在 掉卷时,将卷心部分吊起,无法将钢卷吊走
特征:钢卷内径局部溢出
原因:带钢头部板形不好,卷心卷取张力过小,卷取机卷 筒位移或钢卷小车上塑料垫磨损不均,造成钢卷中心与卷 筒中心不一致
3.金属碎末压入
带钢表面粘附着金属碎末,无规则,有大有小,有块状、 也有条状,压入深度亦有深浅之别。
产生原因:轧辊表面不干净或金属碎末(如铁屑、钢丝等) 落于带钢表面轧入,金属碎末轧入一般也只存在表面,有 时可用小刀清除掉,甚至将带钢轻轻弯曲就可掉落。
4.辊印
带钢表面呈凸起或凹陷的印痕, 但没有明显的凸凹感觉,印痕部 位较亮。
产生原因:轧机的导卫装置安装不正确,或导板等粗糙不 平,有凸起的锐边。另外,在轧制、卷取中,带钢与异物 摩擦也可引起划痕。
措施:1、定期检查辅助传动辊是否转动灵活及表面状况 2、固定辅助设备与带钢应保持一定间隔 3、及时检查、清除生产线设备中的异物 4、发现带钢表面有划伤,应从后向前逐个检查,
查出事故原因后,根据情况采取办法给予处理。
复合浪是在板中部和边部同时出现浪形缺陷。
复合浪形成的主要原因: 1.轧制吨位过大,磨损不均匀 ; 2.没有预热轧辊,轧辊局部冷却不好。
(二)控制板型缺陷的主要措施
1.选择合适的轧辊凸度值
带钢在轧后其横断面上的厚度形状是由轧 辊实际辊缝的形状所决定的。如果轧辊是平辊, 在轧制力作用下,轧辊产生弹性变形,使轧件 通过轧辊时的实际辊缝呈现中间开口度大,而 两边开口度小的辊型,这种辊缝轧出的带钢, 横断面必是中间厚,两边薄。为克服此种缺陷, 轧辊原始辊型应具有一定的凸度。