染色织物色光偏差原因和解决办法之色光回修
【纺织印染整技术】染色后的织物经后整理,为什么色光会发生变化?该如何应对?

【纺织印染整技术】染色后的织物经后整理,为什么色光会发生变化?该如何应对?染色后的织物经后整理,为什么色光会发生变化?该如何应对?1产生原因织物染色后,经后整理,其色光会发生一定程度的变化。
这是染色普遍存在的现象。
经分析,以下因素与色光波动密切相关。
①许多染料染色后,在纤维上并非是稳定态,而是亚稳态(还原染料最为突出)。
经后道的湿、热处理,有可能发生以下变化:a.纤维中处于高度分散状态的染料分子,进一步聚集,会使染料的结晶状态发生一定的改变。
b.纤维中的染料分子,会从纤维分子链的平行状态,变为垂直状态,使染料的存在取向发生改变。
c.具有分子异构化(顺式一反式)倾向的染料,会发生构型变化。
染着在纤维中的染料,一旦发生结晶、取向、构型等改变,必然会导致染料的吸光性能产生变化,从而引起色光波动。
②常用的后整理剂(柔软剂、防水剂、抗菌剂、抗紫外线剂等),在湿、热处理的过程中,会产生以下问题:a.阳离子性助剂与阳离子性染料之间,会产生一些复杂的化学反应。
b.纤维上的助剂膜,会发生一定程度的“泛黄”。
C:后整理液的酸碱度(主要是酸度),会导致染料的色光发生异变。
d.后整理剂会促使分散染料在高温条件下,产生不同程度的“热迁移”与“热升华”。
后整理剂与染料之间的这种复杂关系,必然会给染色色光造成影响。
③经过后整理的染色布,在放置过程中,其色光还有可能发生变化,主要影响因素有以下三点:a.常用染料普遍存在着不同的“三敏”(湿敏、热敏、光敏)现象。
即其染色色光会随着纤维含湿量的多少、温度的高低、光照的强弱不同而不同。
因此,织物的含湿、温度、光照一旦变化,其色光就会不同。
b.织物上残留的矿物质与重金属化合物(主要来自水和后整理剂),在色布放置过程中,会与染料缓慢地发生复杂性的化学作用,从而引起色光的变化。
c.色布在放置过程中,周围环境的酸、碱性气体或氧化性、还原性气体,也会导致染料的稳定性下降,进而发生色光异变。
2应对措施如下①染色后一定要进行充分净洗(皂洗)。
纺织品染色常见问题及防治

纺织品染色常见问题及防治
纺织品染色是指将染料涂覆在纺织品表面,以增强其色彩、外观和质感,成为消费者可接受的产品的过程。
纺织品染色的过程中,可能会遇到一些问题,从而影响产品的整体质量,如染料没有完全染透、颜色差异大等。
第一,染料不能完全染透的问题。
这种问题主要是由纤维结构引起的,当纤维结构较紧密时,染料难以完全渗透;当纤维结构较松散时,染料容易渗透,但是染料渗透深度不一致,产生不一致的色彩差异。
为了解决这个问题,必须严格控制纤维结构的紧密度,以保证染料的完全渗透。
此外,应使用多层染料涂装,以增强染料的渗透性。
第二,染色颜色差异大的问题。
染料染色过程中,染料可能不均匀地渗透到纺织品中,产生不同程度的色彩差异。
这种问题一般是由于染料和纤维之间的反应不够均匀导致的。
为了解决这个问题,应采用筛选染料和预处理纤维的方法。
筛选染料可以解决染料弱反应的问题,而预处理纤维可以增强染料和纤维之间的相互作用,从而达到着色均匀的效果。
第三,染料褪色的问题。
染料可能会受到长期的太阳和气候光照,使其褪色或失去原有的色调。
为了解决这个问题,可以在染料涂覆前使用紫外线吸收剂或防晒剂,以提高染料的耐光性,并使纺织品具有良好的抗褪色性能。
此外,还可以通过改变染料结构,使染料更耐光,从而达到改善
染料耐久性的目的。
总之,纺织品染色中会遇到一些问题,其防治理论主要体现在:严格控制纤维结构、采用多层染料涂装、挑选合适染料、预处理纤维等;使用防晒剂或紫外线吸收剂;改变染料结构以增强其耐光性。
以上措施有助于提高纺织品染色的质量,确保产品的着色和耐久性。
锦纶染色产生疵点的原因及防止措施
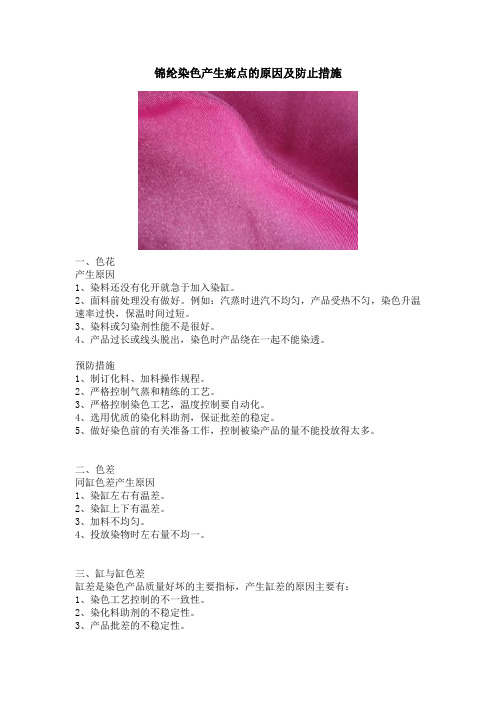
锦纶染色产生疵点的原因及防止措施一、色花产生原因1、染料还没有化开就急于加入染缸。
2、面料前处理没有做好。
例如:汽蒸时进汽不均匀,产品受热不匀,染色升温速率过快,保温时间过短。
3、染料或匀染剂性能不是很好。
4、产品过长或线头脱出,染色时产品绕在一起不能染透。
预防措施1、制订化料、加料操作规程。
2、严格控制气蒸和精练的工艺。
3、严格控制染色工艺,温度控制要自动化。
4、选用优质的染化料助剂,保证批差的稳定。
5、做好染色前的有关准备工作,控制被染产品的量不能投放得太多。
二、色差同缸色差产生原因1、染缸左右有温差。
2、染缸上下有温差。
3、加料不均匀。
4、投放染物时左右量不均一。
三、缸与缸色差缸差是染色产品质量好坏的主要指标,产生缸差的原因主要有:1、染色工艺控制的不一致性。
2、染化料助剂的不稳定性。
3、产品批差的不稳定性。
4、染色技术员和操作工的敬业性和责任性。
预防措施1、改善染色设备。
例如:改用外置加热或底部加循环泵,保证左右升温均匀。
2、加快桨叶的运转速度,使上下传热加快。
3、产品投缸时要保证左右中间量的均匀性。
4、加料能改成自动加料系统。
5、严格控制染色工艺,确保缸次间工艺的一致性。
6、优选染化料助剂,做好染料和助剂换批的检测工作,保证染色处方准确性。
7、加强产品白坯的管理,保证配缸重量的准确性,不混淆产品的批次,不乱混产品货号。
8、加强员工的素质教育,提高员工素养和敬业精神。
四、色点和色斑产生原因1、纱线不纯,有杂质或者色纱混入其中,染色后无法消除。
2、在织造生产过程中混入有颜色飞毛。
3、白坯堆放时间过长产生霉斑和黄斑。
4、染色过程染料飞沾到产品上成色点。
5、产品部分地方在前处理或染色时碰到了某种助剂原液,影响了染料的上染,从而在此产生白点或浅色斑。
6、与某些溶解度特别小的染料拼色时,没有充分化料就加入染缸,没有完全溶解的染料沾到产品上产生色点。
预防措施1、加强进原料时的质量检验和控制,防止不纯纱线的进入。
筒子染色时内外色差原因及预防措施
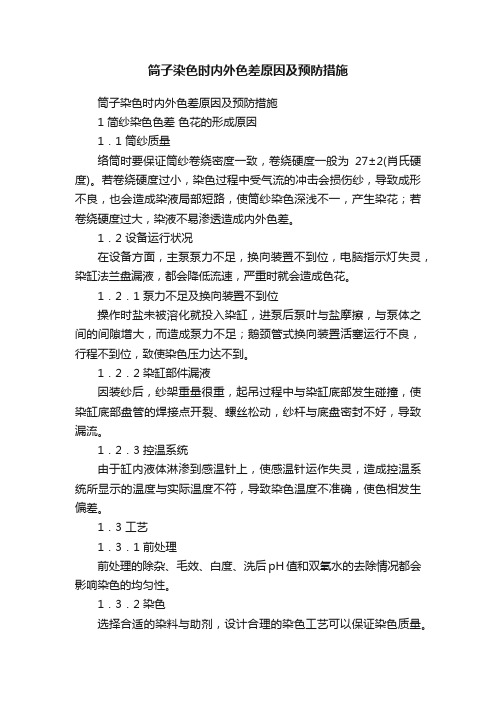
筒子染色时内外色差原因及预防措施筒子染色时内外色差原因及预防措施1 简纱染色色差色花的形成原因1.1 筒纱质量络筒时要保证筒纱卷绕密度一致,卷绕硬度一般为27±2(肖氏硬度)。
若卷绕硬度过小,染色过程中受气流的冲击会损伤纱,导致成形不良,也会造成染液局部短路,使筒纱染色深浅不一,产生染花;若卷绕硬度过大,染液不易渗透造成内外色差。
1.2 设备运行状况在设备方面,主泵泵力不足,换向装置不到位,电脑指示灯失灵,染缸法兰盘漏液,都会降低流速,严重时就会造成色花。
1.2.1 泵力不足及换向装置不到位操作时盐未被溶化就投入染缸,进泵后泵叶与盐摩擦,与泵体之间的间隙增大,而造成泵力不足;鹅颈管式换向装置活塞运行不良,行程不到位,致使染色压力达不到。
1.2.2 染缸部件漏液因装纱后,纱架重量很重,起吊过程中与染缸底部发生碰撞,使染缸底部盘管的焊接点开裂、螺丝松动,纱杆与底盘密封不好,导致漏流。
1.2.3 控温系统由于缸内液体淋渗到感温针上,使感温针运作失灵,造成控温系统所显示的温度与实际温度不符,导致染色温度不准确,使色相发生偏差。
1.3 工艺1.3.1 前处理前处理的除杂、毛效、白度、洗后pH值和双氧水的去除情况都会影响染色的均匀性。
1.3.2 染色选择合适的染料与助剂,设计合理的染色工艺可以保证染色质量。
工艺设计不好,选择三原色的配伍性差,也会造成色花。
2 防止色差色花的措施2.1 筒纱质量筒纱成形要严格把关,杜绝哑铃纱、喇叭纱、重叠纱、漏眼纱及硬边纱,卷绕密度要控制在要求范围之内,过硬过松的`要挑出,筒纱大小一致。
2.2 设备维修为保证设备正常运行,对上述所存在的问题要定期检查,这样才能保证设备运转良好和染色质量稳定。
定期对水、汽阀门进行检查,看有无开启不灵活和关闭不严现象,加强设备维护。
2.3 前处理工艺选择前处理工艺要煮透、煮匀,以便于染色。
为缩短时间,采用煮练漂白同浴法。
工艺处方(g/L)3O%氢氧化钠 4精练剂 2渗透剂 2双氧水 6稳定剂 3前处理工艺曲线(见图1)。
面料色差的应对方法

色差的应对方法在服装面料中深颜色的印染过程中,经常会因种种原因出现边中色差、前后色差等现象,极大地影响了服装印花生产的产品质量和生产效率。
在服装面料印染过程中,半成品的性能对色布的色差、色光的一致性,以及面料色泽的稳定影响极大。
半成品条件稍有变化,印染时在色泽上就能反映出来,就会引起前后面料的色差现象。
在生产中有的货单批量大,即使同一品种,也可能由于采购坯布产地不同,上浆品种和上浆率存在差异,棉花品质、配棉以及生产工艺上的差别,使半成品品质两样。
;’应对方法:因此在印染生产中,要严格把好每道工序的关口,及时观察测定各工序的情况,保证工艺技术一致,颜料配方一致,印染用料一致。
在大批量生产时要用标准样经常对比生产,发现差距要及时调整处方,避免产生前后色差的现象。
为减少由于半成品对染色上染率的影响,漂炼应制定合理的工艺,对于同一品种布,尤其要注意返单,定机台,成熟工艺生产,提高原单处方的重演性。
避免生产中出现色差的印染差现象。
加入合适的助剂,可以有效改善因坯布、设备等原因造成的色差现象。
但有时加入某种助剂后,只能解决一方面的问题,并不能同时解决色差和条花等多种问题,此时,重新选用染化料基础上使用效果较好的助剂才能生产出满足客户的产品,例如,在生产中加入防泳移剂,它能改善由于风房、烘干温度不匀造成的染料泳移,有利于色差的调整,但它不能有效的改善布面织疵,棉杂,棉结,死棉,织条等疵点,布面看上去非常不匀,不饱满,因此在坯布质量较差时,使用匀染剂,效果就比较好。
但使用匀染剂又会出现新的问题,即色差不好调整,比使用防泳移剂,在同样条件下边中色差较重,如在生产涤棉灰色时,加入防泳移剂,色差较好,但布面不好,而使用匀染剂后,布面好了,但色差有时却调整不好。
应对方法:可根据灰色不同可以选择分散黑,或分散灰两种处方,使色差控制达到4.5级通过大量生产实践,利用合理的生产工艺,助剂,解决以上难点可以有效提高产品质量,和节能降耗。
服装染色工艺中色差控制与调整的智能化方法研究
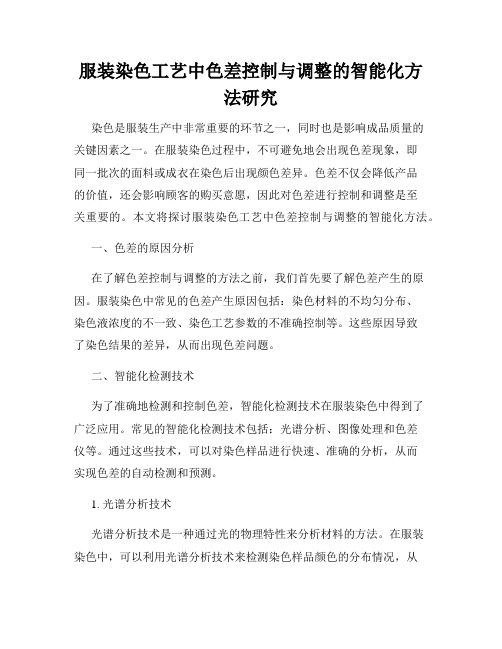
服装染色工艺中色差控制与调整的智能化方法研究染色是服装生产中非常重要的环节之一,同时也是影响成品质量的关键因素之一。
在服装染色过程中,不可避免地会出现色差现象,即同一批次的面料或成衣在染色后出现颜色差异。
色差不仅会降低产品的价值,还会影响顾客的购买意愿,因此对色差进行控制和调整是至关重要的。
本文将探讨服装染色工艺中色差控制与调整的智能化方法。
一、色差的原因分析在了解色差控制与调整的方法之前,我们首先要了解色差产生的原因。
服装染色中常见的色差产生原因包括:染色材料的不均匀分布、染色液浓度的不一致、染色工艺参数的不准确控制等。
这些原因导致了染色结果的差异,从而出现色差问题。
二、智能化检测技术为了准确地检测和控制色差,智能化检测技术在服装染色中得到了广泛应用。
常见的智能化检测技术包括:光谱分析、图像处理和色差仪等。
通过这些技术,可以对染色样品进行快速、准确的分析,从而实现色差的自动检测和预测。
1. 光谱分析技术光谱分析技术是一种通过光的物理特性来分析材料的方法。
在服装染色中,可以利用光谱分析技术来检测染色样品颜色的分布情况,从而判断是否存在色差。
通过这种方法,可以实时监测染色过程中的颜色变化,并进行相应的调整。
2. 图像处理技术图像处理技术可以将染色样品的图像输入计算机进行处理和分析。
通过图像处理技术,可以提取出染色样品的颜色信息,并进行比对和分析,从而得出色差的程度和分布情况。
这种方法可以辅助人工判断染色样品是否合格,并进行调整。
3. 色差仪色差仪是一种专门用于测量和分析色差的仪器。
它可以通过测量染色样品与标准颜色之间的差异,来评估色差的程度和种类。
色差仪具有测量精确、操作简便等特点,因此在服装染色中得到了广泛的应用。
三、智能化调整方法在检测到染色样品存在色差后,智能化调整方法可以自动进行调整,以降低色差的程度。
1. 自动控制染色液浓度染色液浓度的不一致是导致色差的重要原因之一。
智能化调整方法可以通过检测染色液浓度,调整染色液的配比和控制染色液的加入量,从而保证染料的均匀分布,减小色差的发生。
染色过程中色差的成因与预防

染色过程中色差,色条,色花的预防与控制赵利强靳建彬王素霞 (石家庄第二印染厂050091)摘要:染色过程中(中深颜色)易出现边中色差及前后色差,色条,及条花,这是提高色布产品质量及生产效率的难点,通过大量生产实践,利用合理的生产工艺,助剂,解决以上难点可以有效提高产品质量,和节能降耗。
关键词:染色,边中色差,匹匹色差,条花,生产工艺,助剂一、前言:随着中国服装面料出口大幅提高,商业竞争加剧,如今客户对外销服装面料的色光,色差,色泽,牢度的要求非常严格,因此提高染色布的色光准确性和稳定性,生产出布面丰满,均匀,色泽一致,尺寸稳定性一致的优质产品是满足客户要求的重要因素,也是赢得客户立足市场不败之地的关键,因此我想通过大量的生产实践,就如何防止染色过程中,色差色条色花的问题谈一下经验。
二、半成品的影响,在生产染色布的过程中,半成品的性能对色布的色光一致性,色泽稳定性及色差的调整至关重要,半成品要求匀透,白度和毛效概念模糊,且质量不易察觉,半成品条件稍有变化,染色时在色泽上就能反映出来。
在生产中有的货单批量大,即使同一品种,也可能由于采购坯布产地不同,上浆品种和上浆率不同,棉花品质不同,配棉不同,和生产工艺不同,使半成品品质不同,因此在生产中,要道道工序把关,及时测定漂炼各工序,工艺一致,大批量的要带样生产,差距大的要及时调整处方,避免生产中前后色头变化大,造成回修和消耗增加,为减少由于半成品对染色上染率的影响,漂炼应制定合理的工艺。
对同一品种布,尤其返单,定机台,成熟工艺生产,提高原单处方的重演性。
三、染色过程的影响1.染料,助剂的选用对色差的影响a.选用士林染料染色时,由于个别染料在料槽中上染速率慢,而沉积,造成前后色差,而使色光,逐渐向上染速率慢的染料色光上变,而造成前后色差,如生产橄榄绿时使用士林黄,为了稳定色光,我们采取士林橄榄绿或草绿替代黄,另外为了防止黄料沉积,还可以在染料中加入分散剂,使料缸,料槽中的染液更均匀,不发生聚积,可以有效改善色差,并降低成本。
色差研究-最全面的色差产生原理及一般解决办法
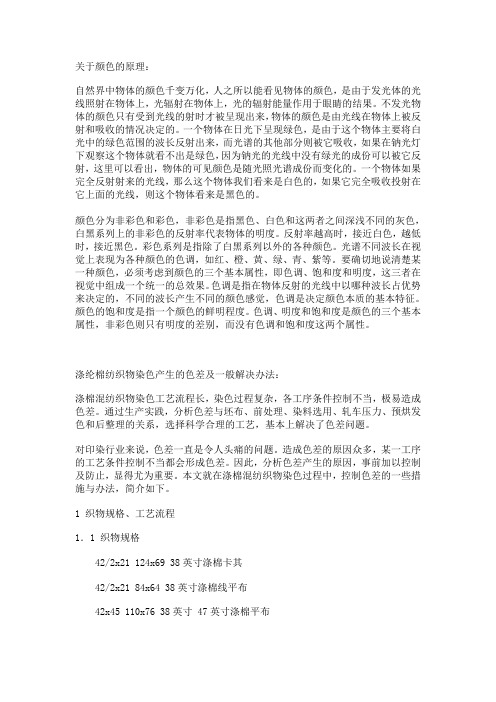
关于颜色的原理:自然界中物体的颜色千变万化,人之所以能看见物体的颜色,是由于发光体的光线照射在物体上,光辐射在物体上,光的辐射能量作用于眼睛的结果。
不发光物体的颜色只有受到光线的射时才被呈现出来,物体的颜色是由光线在物体上被反射和吸收的情况决定的。
一个物体在日光下呈现绿色,是由于这个物体主要将白光中的绿色范围的波长反射出来,而光谱的其他部分则被它吸收,如果在钠光灯下观察这个物体就看不出是绿色,因为钠光的光线中没有绿光的成份可以被它反射,这里可以看出,物体的可见颜色是随光照光谱成份而变化的。
一个物体如果完全反射射来的光线,那么这个物体我们看来是白色的,如果它完全吸收投射在它上面的光线,则这个物体看来是黑色的。
颜色分为非彩色和彩色,非彩色是指黑色、白色和这两者之间深浅不同的灰色,白黑系列上的非彩色的反射率代表物体的明度。
反射率越高时,接近白色,越低时,接近黑色。
彩色系列是指除了白黑系列以外的各种颜色。
光谱不同波长在视觉上表现为各种颜色的色调,如红、橙、黄、绿、青、紫等。
要确切地说清楚某一种颜色,必须考虑到颜色的三个基本属性,即色调、饱和度和明度,这三者在视觉中组成一个统一的总效果。
色调是指在物体反射的光线中以哪种波长占优势来决定的,不同的波长产生不同的颜色感觉,色调是决定颜色本质的基本特征。
颜色的饱和度是指一个颜色的鲜明程度。
色调、明度和饱和度是颜色的三个基本属性,非彩色则只有明度的差别,而没有色调和饱和度这两个属性。
涤纶棉纺织物染色产生的色差及一般解决办法:涤棉混纺织物染色工艺流程长,染色过程复杂,各工序条件控制不当,极易造成色差。
通过生产实践,分析色差与坯布、前处理、染料选用、轧车压力、预烘发色和后整理的关系,选择科学合理的工艺,基本上解决了色差问题。
对印染行业来说,色差一直是令人头痛的问题。
造成色差的原因众多,某一工序的工艺条件控制不当都会形成色差。
因此,分析色差产生的原因,事前加以控制及防止,显得尤为重要。
- 1、下载文档前请自行甄别文档内容的完整性,平台不提供额外的编辑、内容补充、找答案等附加服务。
- 2、"仅部分预览"的文档,不可在线预览部分如存在完整性等问题,可反馈申请退款(可完整预览的文档不适用该条件!)。
- 3、如文档侵犯您的权益,请联系客服反馈,我们会尽快为您处理(人工客服工作时间:9:00-18:30)。
染色织物色光偏差原因和解决办法之色光回修
一、产生色光偏差的缘由
1.不一样批次的前处置半制品布,因为其纤维功能白度、毛效程度等存在区别,而致使染色布色光差错。
2.不一样厂家或同一厂家不一样批次的染化料之间存在区别,而致使色差。
3.拼色染料选用不妥,没有遵从同拼色、近拼色、少拼色的准则,上染同步性较差,使色泽重演性下降,形成染色色光差错。
1.染色技术条件操控不妥是色光差错的首要缘由。
①染色温度是影响色光的关键因素,例如:活性染料、分散染料、酸性染料等对染色温度非常灵敏,如染色温度偏高时,X—GN、X—BR的平衡上染百分率比其它染料相对添加,X—3B、X—2B则相对削减,从而使色光发作差错。
②染浴PH值动摇首要影响活性染料的固色率,一些含酯基、酰胺基、氰基等的分散染料在高温染色时的色光。
③浸染中浴比的动摇,色光的重演性受到影响。
活性染料染色较为显着,通常的浴比越小,得色量相对较高。
④染色后处置的影响:织物染色后过酸氧化、皂煮、加白、树脂收拾等进程,对此染色织物的色光有影响。
此外,染化料、助剂储存时刻过长或受空气中水汽、酸碱性以及氧化、复原性气体的影响,值得附致使染色色差;称量差错、染色用具、管道清洗欠好等等,也会致使必定的色差。
二、色光回修窍门和办法
当染色织物色光不契合需求时,需求色光回修,以进步产品质量、下降生产成本。
色光回修的办法首要有两大类,非染料进行色光回修及染料套印回染回修。
1.非染料进行色光回修:此类办法操作简洁,成本低,质量好。
①水洗。
这种办法适用于染色布色光略深,浮色较多和水、皂洗牢度不太好的染色布修色,是回修中最简略的办法。
经过水洗可将浮色除掉,到达看似浅淡的批改色光的意图。
能否适用此法,通常应在修色前检查物理测验中皂洗牢度与皂煮后的色光改动是不是契合修色方向,若契合即可选用此法。
别的把握单个染料在水洗、皂煮进程中色变的特色,可运用于修色中。
例如:活性黄、蓝染料拼绿染料时,关于活性翠蓝KNG、活性翠蓝KGL水洗皂煮易落色的特色,对绿色染后嫌色光差错可经过水洗,进步染色制品布的黄光,可到达修色的意图。
②碱水洗。
本法适用于对碱灵敏的染料用以色光的回修,较多的活性染料均可运用,例如用活性黑KN—B拼色的染色布如色光偏蓝,则可经过轧适当烧碱平洗的办法,到达修去蓝光改浅的意图。
并不是一切染色都可用此类办法回修。
关于那些色泽深、色光萎暗或改浅后仍不契合标样等染色布,只能选用套染、剥色重染、改染深色等办法回修。
2.染料套印回染回修
运用此类办法回修时,应尽量选操作简洁、成本低、质量好的技术。
①染色布样色光浅得较多,但色相根本共同时,可选用原处方,按色浅成数断定处方的用量。
并用原技术进行套印。
②色光浅的较少,可选用直接染料技术进行套印。
③色光深度挨近,而色相不对时,选用缺什么套什么的准则。
④色光较深,但在可修色范围内,则应先剥色然后再套染回修。
常剥色技术及技术举例如下:
硫化染料染色织物经过次氯酸钠法即可到达满足作用,活性染料染色织物可选用稳妥数值法或氯酸钠法剥色,但稳妥粉法对酞氰布局染料如翠蓝KN—G剥色不太满足,如先后运用两种办法,则可到达满足作用,两种办法别离如下:①稳妥粉法:稳妥粉5g/L、烧碱(360Cbe’)15Ml/L、浴比1:20~30、温度T=40~900C、时刻入=40min。
②次氯酸钠法:有效氯5g/L、PH值11、浴比1:20~30、温度T =室温、时刻入=30min,然后二次水洗——酸洗(醋酸)脱氯。
③关于色光深,且不行回修时,则只能改染深色。
三、色光回修的注意事项1.用直接染料回修时,其用量应通常把握在1g/L以下,避免影响回修后制品布的染色牢度。
2.色光回修时,不能只思考色泽契合标样,还要注意回修后织物的强力、幅宽、色光艳丽度及染色牢度等均要契合规范。
度及染色牢度等均要符合标准。
出处:广州庄杰染整助剂官网。