某电厂3号燃气轮机压气机叶片故障的原因分析
燃气轮机运行故障分析及排除措施分析

0引言燃气轮机具有结构紧凑、启动速度快、运行状态平稳等优点,但是燃气几轮发生故障的频率也比较高,对设备的正常运行造成了严重的干扰。
1燃机启动过程中热挂问题及处理燃气机轮启动时排气温度升高,但是按照控制规范,燃油流量会继续增加,而燃机运转速度维持不变,会导致转速下降,处于“热挂”状态,随后燃机的转速下降会导致燃机启动失败。
出现启动热挂问题与燃机性能恶化有关,具体影响因素包括:燃油流量分配器卡涩、进气滤网堵塞、燃油母管压力释放阀泄露、燃机的控制系统发生故障、燃油雾化不良、透平出力不足。
处理热挂问题的要点有三个方面:一是需要定期清洗压气机,将流道内的油污、污垢等清除干净,保证运行状态正常;二是需要及时清洗透平热通道,清除通道内的灰尘,保证透平出力充足,在燃气启动时确保燃机的运转速度;三是在出现热挂问题时,可以减少燃油流量,让运行点下移,再增加燃油流量。
2压气机喘振及处理压气机喘振通常发生在燃机启动和停机过程中,主要有两种类型,一是突变失速所导致的喘振,二是渐变叶片排失速引起的喘振。
处理这个问题主要有四种方法,从压气机的中间级放气,也可以末级放气;选用可调进口导流叶片和静叶片;在压气机中应用多转子技术;应用机匣处理技术。
另外对于高压比压气机可以采取双转子结构防止喘振。
3燃机大轴弯曲及处理发生燃机大轴弯曲问题通常有三方面原因:一是在燃机运行时汽温汽压值超过了紧急停机值,但是并没有进行停机操作;二是管理人员并没有很好的落实防范措施和管理制度;三是没有充分重视停机过程中发生的一些异常状况,未能深入分析这些异常状态出现的原因。
处理这个故障问题的具体措施包括:设备管理者需要依据燃机的制造标准以及运行的具体特性制定不同状态下的燃机运行曲线,包括启动时曲线和停机时曲线,将典型曲线编入运行规程;针对滑参数停机的情况,需要专业技术人员制定滑参数停机方案以及对应的防范措施,加强对技术人员的培训和管理,确保其严格按照专业人员制定的方案完成各项操作;定期检查机组监测仪表的状态,保证仪表完好,运行状态准确,尤其需要加强对大轴弯曲表、振动表、气缸金属温度表的校验和检查;在遇到特殊情况且汽温汽压值达到了停机标准时,一定要立即进行停机操作,比如主、再热蒸汽温度在10min内突然下降50摄氏度、高压外缸上和下缸温差超过50摄氏度、高压内缸上和下缸温差超过35摄氏度等。
燃气轮机常见的故障与故障诊断技术分析

燃气轮机常见的故障与故障诊断技术分析2杭州汽轮动力集团股份有限公司浙江杭州市 310022摘要:燃气轮机是一个非线性系统,且其结构的设计和部件具有一定的复杂性。
在燃气轮机具体运行的过程中,各个部件的质量对于燃气轮机的稳定运行都具有非常重要的作用。
只有确保各个部件的设计都符合燃气轮机运行的需要,才能保证燃气汽轮机的稳定运行。
但是燃气轮在长期运转的过程中,出现一定的故障问题是不可避免的。
为了确保对燃气轮机故障的快速、准确处理,需要对燃气轮常见的故障进行总结和分析。
本文从燃气轮机常见的故障与故障诊断技术展开分析,尝试为燃气轮机的维护提供更多的参考建议。
关键词:燃气轮机;常见故障;故障诊断技术引言:燃气轮机在运行的过程中,针对燃气轮机早期故障问题的出现,制定了使用门控循环单元构建基础模型的参数趋势分析方法,能够达到对燃气轮机故障进行准确定位的作用。
但是机组的故障在发生时,会促使机组的性能发生变化,进而导致运行的参数也随之出现改变。
为了有效应对此类问题的出现,相关研究人员提出了以神经网络为基准建立模型和运行的实际参数值的偏差值作为检测的对象,通过设置偏差阈值的方法,在燃气轮机出现故障的状况下发出警报提醒燃气轮机的监测人员。
以便采取适当的措施进行控制燃气轮机,预防燃气轮机因为故障的因素造成严重的损坏。
因此,为了降低燃气轮机故障出现对设备造成的严重损坏,需要相关管理人员不断对常见故障的发生、故障诊断技术的科学应用展开详细的分析工作。
一、燃气轮机常见故障(一)机械故障在燃气轮机具体运行的过程中,燃气轮机出现部件的侵蚀、机身腐蚀、零件缝隙增大、叶片厚度增加的问题的出现,属于燃气轮机的机械故障问题。
造成燃气轮机机械故障发生的原因是多方面的,需要根据具体的状况展开科学的分析工作,才能制定出符合机械故障检测的方法。
比如,燃气轮机零部件出现侵蚀的现象,主要的原因是在燃气轮机工作的环境中,空气中的颗粒物质会与燃气轮机产生摩擦的现象。
燃气轮机压气机首级动叶弯曲原因及检修工艺介绍

对 油性积垢 的清除效 果没有 干洗理 想 。
气 因为 缸壁 的导热 系数较 大 ,其 温度远 高于周 围环境 温
冬季清洗压气机 ,如果清洗后盘 不允分 ,残余的 度 (厂房 内气温 ),所 以缸 擘不断 向环境 散热 而降温 当压
水 、汽将 降温结 冰 从 图 l的气缸壁结 构 可以看 出 .压气 气机内部的湿空气温度降到该压力下的饱和温度时,空
提高 。
结冰的现象。这种改进初投资少 ,运行成本低 ,而收效却
③修 复 弯曲 的首级动 叶后 ,叶顶 部位 不再有 涡流存 t‘分 显著 ●
机进气缸呈喇叭口形,前缸旱网锥形,中缸及排气缸前 气中的水蒸气会 断地 向缸壁释放 汽化潜热而凝结 成
部呈圆柱形 粘附在转子及缸体 部的水在重力作用 F 水 ,并 沿缸壁 向衄低点 流 动 ,当环 境温 度降 至零 下 ,缸壁
流到 底 部 ,其 中排 气缸 内积水 流 至 C处 的防 喘放 气孔 会 迅速散热而降温至零下。积存于进 口导叶轴套或酋
道 变窄 ,降低了压气机 的工作效率利整机 的热效率;再 次加热后难 以将叶片修复到位,一般校正一片弯曲叶片
次 ,弯 曲的叶 片使 转子 动平衡受 到一 定程度的 影响
需 对叶 片加 热两 次 ,而加热 次数 过多则 容 易 导致 叶片 内
(1)压 气机 喘振
部金属结构的变化 这种修复方案的优点是简单 易行,
工况时 ,这种气体脱离现象 导n十的开度增大而变得更 因此 建议 慎用此 方案
为严莺,极 易造成机组喘振
(2)打磨掉 叶片 弯 曲部分
发生喘振时,压气机的流量和压力大幅度 、低频率的 这种方案就是将动叶卷边部分去除,并且对叶片前
燃气轮机控制系统的故障原因与对策分析_1
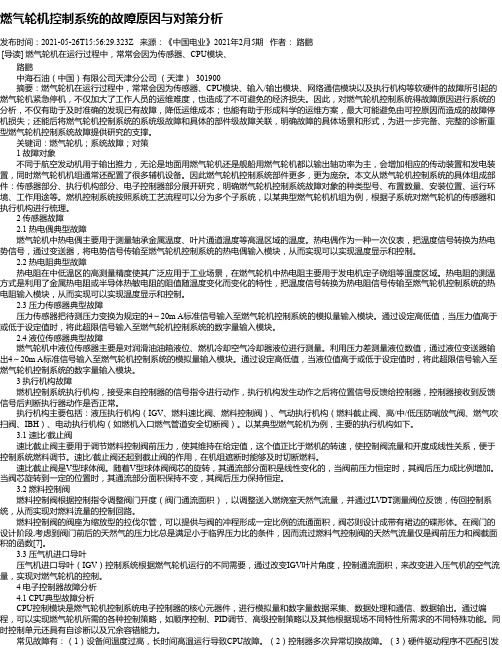
燃气轮机控制系统的故障原因与对策分析发布时间:2021-05-26T15:56:29.323Z 来源:《中国电业》2021年2月5期作者:路鹏[导读] 燃气轮机在运行过程中,常常会因为传感器、CPU模块、路鹏中海石油(中国)有限公司天津分公司(天津) 301900摘要:燃气轮机在运行过程中,常常会因为传感器、CPU模块、输入/输出模块、网络通信模块以及执行机构等软硬件的故障所引起的燃气轮机紧急停机,不仅加大了工作人员的运维难度,也造成了不可避免的经济损失。
因此,对燃气轮机控制系统得故障原因进行系统的分析,不仅有助于及时准确的发现已有故障,降低运维成本;也能有助于形成科学的运维方案,最大可能避免由可控原因而造成的故障停机损失;还能后将燃气轮机控制系统的系统级故障和具体的部件级故障关联,明确故障的具体场景和形式,为进一步完备、完整的诊断重型燃气轮机控制系统故障提供研究的支撑。
关键词:燃气轮机;系统故障;对策1 故障对象不同于航空发动机用于输出推力,无论是地面用燃气轮机还是舰船用燃气轮机都以输出轴功率为主,会增加相应的传动装置和发电装置,同时燃气轮机机组通常还配置了很多辅机设备。
因此燃气轮机控制系统部件更多,更为庞杂。
本文从燃气轮机控制系统的具体组成部件:传感器部分、执行机构部分、电子控制器部分展开研究,明确燃气轮机控制系统故障对象的种类型号、布置数量、安装位置、运行环境、工作用途等。
燃机控制系统按照系统工艺流程可以分为多个子系统,以某典型燃气轮机机组为例,根据子系统对燃气轮机的传感器和执行机构进行梳理。
2 传感器故障2.1 热电偶典型故障燃气轮机中热电偶主要用于测量轴承金属温度、叶片通道温度等高温区域的温度。
热电偶作为一种一次仪表,把温度信号转换为热电势信号,通过变送器,将电势信号传输至燃气轮机控制系统的热电偶输入模块,从而实现可以实现温度显示和控制。
2.2 热电阻典型故障热电阻在中低温区的高测量精度使其广泛应用于工业场景,在燃气轮机中热电阻主要用于发电机定子绕组等温度区域。
燃气轮机压气机首级动叶弯曲原因及检修工艺

燃气轮机发电技术第4卷则,假如对称叶片修磨误差为1/10,即:07克(实际远远小于此),则每对对称叶片的重心变化对整个转子的影响使转子的重心偏移约:5×10~111。
考虑到修磨后的偏差不可能偏到一侧,因此整个转子的重心偏移应在108rii数量级上,转子重心变化产生的附加离心力约为150千克力左右。
这个力对转子的动平衡影响甚微,因此转子的平衡较动叶修磨前状态大为改善。
但这个方案同时也存在着缺点,即叶片修磨后,首级压气机压比因叶片叶身面积变小而降低,进而影响其后各级压比,最终整机压比下降,使整个机组的效率有所下降。
但较叶片不修整状态而言,其效率要高很多。
3.3打磨叶片检修工艺在分析了各种修复方案优缺点后.我厂决定采用第二种方案。
对压气机首级全部32片叶片的弯曲部位进行打磨处理。
该方案虽然以牺牲一定效率为前提,但消除了机组的安全隐患,提高了机组安全运行的可靠性。
具体的检修工艺如下:(1)做模板,如图2图2叶片弯位打磨模板1叶片弯曲部分2一模板其中BC、CD、AE三边紧紧靠在叶片边缘。
AB为一圆弧线,在A点应使AB弧线与Bc线即动叶前额线圆滑过渡,而不能有较大折转角。
3一叶片4一动叶背弧侧5一动叶修磨部位(2)对称打密根据动叶卷曲的大小制作多个不同模板。
模板露出的部分,即AB弧线外侧部分应能覆盖住叶片弯曲部分。
打磨时应采取对称修磨,即以转子中心为对称点,每两片动叶打磨掉的面积理论上应绝对相等。
即必须采用同一模板靠在对称叶片上,用笔划好边线,即AB弧线。
采用颗粒较细的手砂轮将AB弧线以外的弯曲叶片刨去。
注意,不要一次修正到AB弧线处,应留出1mm余量以便精细修磨。
叶片打磨时,应紧握砂轮,以免高速旋转的砂轮片伤及其它叶片。
(3)精细修磨精细修磨的过程即采用油石粘上滑油一点点修整余下的叶片。
注意修磨的时候应修整叶片的叶背,不允许修整叶片内弧侧。
叶片修整后应保证叶片各部圆整平滑,过渡部分应自然,不允许有折角。
燃气轮机叶片失效分析及检验探讨

燃气轮机叶片失效分析及检验探讨摘要:燃气轮机叶片是燃气轮机的重要部件,可以说是燃气轮机的“心脏”,在燃气轮机的正常工作系统中发挥了不可或缺的作用。
因为燃气轮机工作是靠燃料在燃烧室中产生的高温气体去吹动涡轮,类似风车,所以如果燃气轮机叶片出现故障无法正常运转,肯定会造成一些安全问题。
因此,对于能够造成燃气轮机叶片失效的原因进行分析,同时对其相关的制造工艺及安装的检验也是非常必要的,这样才能更好的保障燃气轮机叶片的有效性,以及燃气轮机的正常运行,从而减少安全隐患。
所以文中将重点阐述分析燃气轮机叶片失效的原因,以及相关的检验方法,希望为将来有关方面带来一定的帮助。
关键词:燃气轮机叶片;失效分析;检验技术燃气轮机是一种先进而复杂的成套动力机械装备,具有效率高、功率大、体积小投资省、运行成本低和寿命周期较长等优点。
主要用于发电、交通和工业力。
例如用于飞机,轮船,坦克,汽车,发电,大型驱动装置,比如前段时间说的日本排水系统的水泵驱动,还有天然气输送站的升压装置等多个领域。
然而燃气轮机的主要部位是燃气轮机叶片,所以对于叶片失效的分析及检验就起到了至关重要的作用。
但是目前由于多方面的原因,我国燃气轮机同国际先进水平相比仍存在很大差距,其技术仅被世界上少数几个发达国家所控制,先进的燃气轮机在西方国家仍然限制对华出口。
因此,研究燃气轮机叶片失效的分析以及检验就很有必要。
1燃气轮机叶片的重要作用及工作环境1.1燃气轮机叶片的重要作用从燃气轮机的组成来看,在由压气机、燃烧室和涡轮三大部件组成的燃气涡轮发动机当中,压气机和涡轮都是由转子和静子构成,然而静子又是由内、外机匣和导向(整流)叶片构成;转子则是由叶片盘、轴及轴承构成,其中叶片数量最多。
所以说光从组成上来看的话,叶片在其结构组成上占有很大一部分的比例,也起到了不可或缺的作用。
那从工作原理上来看,发动机就是依靠这众多的叶片完成对气体的压缩和膨胀以及以最高的效率产生强大的动力来推动飞机前进的工作。
燃气轮机气路故障诊断技术

燃气轮机气路故障诊断技术摘要:燃气轮机具有体积小、开启速度快、运行稳定性强及效率高等显著优点,同时其运行过程还不会对社会大众的居住环境产生太大影响,因此,在我国的工业、交通运输业、船舶动力和天然气等领域和行业中都得到了广泛应用。
然而,燃气轮机在运行过程中还是会受到很多外界因素的干扰,并且设备又长期处于高压和高温的环境中,一点点的风险隐患和因素都可能导致气路故障问题的出现,并直接影响设备的整体运行效率,那么相关人员就必须及时且有效地检查燃气轮机的汽路故障,尽早发现并采取有针对性的预防和诊断技术,将故障问题快速解决,保证燃气轮机的稳定、高效运行。
关键词:燃气轮机;气路故障;诊断;预防1、燃气轮机的常见气路故障1.1 压气机叶片积垢在燃气轮机的实际运行过程中,其最容易出现的一类气路故障便是叶片积垢问题,通过对燃气轮机的具体运行原理进行分析可知,每千瓦燃气轮机如果要保证24 h稳定运行就必须吸入大概0.5 t左右的空气,并会有一些微粒杂质随着空气进入燃气轮机中,即使企业会针对这种情况采取相应的处理措施,也无法将微粒杂质完全隔离出去,微粒杂质进入燃气轮机的内部后通常都会附着在叶片的表面,当这些微粒杂质积聚一段时间后便会在叶片表面形成较大面积的沉积物,如果没有及时清理这些沉积物便会出现积垢,随着燃气轮机的持续运行,积垢会不断增多,并直接影响燃气轮机的实际运行性能。
1.2 压气机叶片磨损和腐蚀当燃气轮机运行时,如果有固体颗粒或是盐分存在于空气中,那么这些物质就可能磨损甚至是腐蚀燃气轮机叶片的表面,不但会在叶片表面形成划痕,还会进一步增加叶片表面的粗糙程度。
如果没有及时处理这一问题,会对叶片表面的整体气动性能产生不利影响,加大其阻力系数,一旦压气机叶片出现了磨损和腐蚀等问题后,通流的面积和流量都会越来越大。
1.3 压气机叶片机械损伤和喷嘴腐蚀随着燃气轮机的不断运行,其流道内表面一定会受到燃气轮机自身出现脱落现象的部件或是液体燃料中存在的颗粒等物体的不断撞击,其中如果是燃气轮机内部有部件出现了脱落并撞击了叶片,这属于自身物件损伤,而如果是液体燃料中的颗粒撞击了流道内表面,这便是外来物损伤,会直接影响燃气轮机的实际运行情况。
压气机叶轮叶片的失稳分析

压气机叶轮叶片的失稳分析近年来,压气机叶轮叶片的失稳问题引起了广泛的关注。
压气机作为燃气轮机的核心部件,其稳定运行对于燃气轮机的性能和寿命至关重要。
然而,在实际运行中,叶轮叶片的失稳现象常常会导致燃气轮机的性能下降、噪声和振动增大、甚至发生严重的事故。
因此,深入研究压气机叶轮叶片的失稳问题有着重要的意义。
首先,我们需要了解压气机叶轮叶片失稳的原因。
一种常见的原因是叶片本身的结构问题。
由于叶轮叶片是高速旋转的,其受到的离心力和气动力的作用很大,因此叶片的强度和刚度是关键因素。
如果叶片的强度不够或者刚度不均匀,就容易发生失稳。
此外,叶片的材料和工艺也会对失稳性能产生影响。
例如,叶片的塑性变形和疲劳破坏会导致叶片的形状产生变化,从而引发失稳现象。
另一个导致压气机叶轮叶片失稳的原因是流体动力学问题。
在压气机内部,气体流动会导致叶轮叶片的受力情况不均匀,从而引发叶片的振动。
特别是在大负荷运行和转子共振区域,由于气体的非线性和不稳定性,叶片的失稳现象更加明显。
此外,还存在着气体边界层的分离和抖动、各种流动涡流的相互作用等问题,这些也会对叶片的失稳性能产生重要影响。
针对压气机叶轮叶片的失稳问题,研究人员们提出了不同的分析方法和解决方案。
一种常用的方法是通过数值模拟来研究叶片的振动和失稳特性。
利用计算流体力学(CFD)方法,可以模拟叶轮叶片在不同工况下的气动受力情况,从而分析叶片的振动和失稳现象。
此外,还可以利用有限元分析方法研究叶片的结构应力和振动响应,进一步分析叶片的失稳性能。
通过这些分析方法,可以准确评估压气机叶轮叶片的稳定性,并根据分析结果提出相应的改进和优化措施。
除了数值模拟方法,实验方法也是研究压气机叶轮叶片失稳问题的重要手段。
实验可以直观地观察到叶片的振动和失稳现象,提供直接的实验数据,对于验证数值模拟结果和分析结果的准确性具有重要意义。
目前,研究人员们常常利用激光测振技术、压电传感器和加速度计等仪器设备来对叶片的振动进行测量。
- 1、下载文档前请自行甄别文档内容的完整性,平台不提供额外的编辑、内容补充、找答案等附加服务。
- 2、"仅部分预览"的文档,不可在线预览部分如存在完整性等问题,可反馈申请退款(可完整预览的文档不适用该条件!)。
- 3、如文档侵犯您的权益,请联系客服反馈,我们会尽快为您处理(人工客服工作时间:9:00-18:30)。
第36卷 第1期热力透平Vol136No11 2007年3月THER M A L T UR BI NE Mar12007某电厂3号燃气轮机压气机叶片故障的原因分析朱宝田,肖俊锋,祁文玉(西安热工研究院,西安,710032)摘 要: 对某电厂3号燃气轮机压气机叶片的故障原因进行分析,调查了故障发生经过、运行记录、控制系统记录、机组分解现场、零部件损坏情况,对叶片材质和断口进行了理化检验分析,得出故障原因,对机组的修复和今后的安全运行具有重要的意义。
故障与运行操作无直接关系。
故障原因分析的结论成为电厂向制造商索赔的技术依据。
关键词: 发电厂;燃气轮机;压气机;叶片;故障;原因分析中图分类号:T K47418 文献标识码:A 文章编号:1672-5549(2007)01-0067-04Analysis on Compressor Blade Failure of No13G as Turbine in a Certain PlantZ H U B ao2ti an,X I A O J un2f eng,QI W en2y u(Thermal Power Research Institute,Xi’an710032,China)Abstract: An analysis on the compressor blade failure of No13gas turbine in a certain plant was analyzed1 The failure occurring,operating record,control system record,unit decomposition site and components damage status were investigated1The physical and chemical inspection analysis for blade material and blade fracture were done to obtain the failure causes,which has a great significance to the rehabilitation of unit and later safe operation1The failure had no direct relation to operation.The conclusion of failure analysis could be considered as technical material used for the plant,who claimed for damages f rom manufacturer1K ey w ords: power plant;gas turbine;compressor;blade;failure;analysis1 机组情况某电厂3号燃气轮机为GE2AL STOM公司制造的P G65812B型燃气轮机,额定功率42100kW(天然气燃料),额定转速5163r/min。
2004年9月24日简单循环投运,2005年9月4日,联合循环投运。
3号燃气轮机累计点火运行1004314小时;累计启动80次,事故跳闸9次(因燃气轮机引起的跳闸仅本次事故);系统周波4919~5012Hz。
机组正常运行负荷在30~40MW之间,平均负荷33MW,冬季环境温度低时最高负荷48MW,调峰时最低负荷25MW。
2 故障情况故障前,3号燃气轮机负荷37MW。
2005年12月6日凌晨5点左右,1号轴承两个振动监测值由原来的0189mm/s、0197mm/s分别增至1182mm/s、119mm/s。
9时许,1号轴承振动监测值增至316mm/s、3156mm/s,2号轴承两个振动监测值由113mm/ s、1144mm/s增至3139mm/s、3109mm/s;由于上述振动监测值与GE公司规定的报警值1217mm/s尚有距离,机组继续运行。
11:52分,控制系统出现“燃机排气温度高”报警,机组跳闸。
跳闸前报警信息如下:时间 报警信息2005/12/06 11:52:231343燃机排气温度高2005/12/06 11:52:231343排气超温跳闸2005/12/06 11:52:241718发电机短路器跳闸2005/12/06 11:52:451343高振动跳闸或停机机组跳闸前后燃机有短促异常声响。
跳闸后机组惰走时间11分20秒,与正常停机6走时间收稿日期:2006-09-27作者简介:朱宝田(1948-),男,西安热工研究院首席研究员,享受国务院政府特殊津贴的专家,从事发电厂设备和系统的研究。
本文为2006年中国动力工程学会透平专委会论文研讨会宣读论文,获优秀论文奖。
一致,6走结束后正常盘车。
12月6日下午19时,打开5号燃烧室下部启动失败排放管线,发现一些块状金属物。
12月7日上午,打开并拆除5、6、8号燃烧室火嘴,在燃烧室及火焰筒内均发现叶片残块。
3 设备损坏情况311 压气机目视检查,压气机第1级—第15级动、静叶片基本完好,但第1~16级动叶顶部及各级动叶对应的气缸内壁有明显的磨擦痕迹。
压气机第16级动、静叶片不同程度碰撞受损。
压气机缸体内第17级静叶片全部损毁。
压气机下缸体内第17级段散落有叶片残骸。
压气机第17级动叶共56片,全部损毁。
现场对压气机第17级动叶进行编号,其中:第3、4、7、8、11、12、20、26、27、30、32~41、43~48、50、52、54、55号共30片动叶断裂脱落;第1、2、5、6、9、10、13~19、21~25、28、29、31、42、49、51、53、56号共26片动叶不同程度受损。
在30片断裂脱落叶片中,其中有26片叶片断口位于叶型根部截面,叶片断口呈明显的疲劳断口特征(见图1~2)。
在每个断口上均可用肉眼可分辩出疲劳裂纹萌生区(疲劳源点)、疲劳裂纹扩展(贝壳样或沙滩样)区和失稳断裂区三个区域,疲劳源点位于叶片型线根部的背弧中部;疲劳扩展区的疲劳纹由背弧向内弧侧扩展,疲劳扩展区占断口面积约3/4~1/4(多数断口的疲劳扩展区较大),疲劳扩展区断口颜色有差别,终断区呈粗糙金属样。
一些叶片断口有多疲劳源,疲劳扩展区表面较粗糙。
叶片断口的位置及疲劳源点、疲劳扩展区、终断区的分布表明,叶片的振动为一阶切向(垂直于最小惯性轴)的弯曲振动。
在第17级受损伤但未断裂脱落的动叶片中,其型线根部背弧中部(对应断裂脱落疲劳断口的疲劳源点位位置)几乎都有肉眼可见裂纹。
312 透平透平第1、2、3级静叶背弧表面粗糙,有明显固体撞击痕迹。
透平第1级全部动叶片在叶顶进气边部位存在约30mm ×20mm 撞击缺口。
透平第2、3级动叶片表面粗糙,有明显固体颗粒撞击痕迹。
4 压气机第一级叶片材质和断口理化检验分析411 化学成份化学成份分析见表1,化学成份符合G B1221292中1Cr13牌号的技术要求。
表1 叶片化学成份分析结果%CSSiMnPCr Ni 实测值0115010010126015901011121650149G B1221292标准≤0115≤01030≤1100≤1100≤010351115~13150≤0160412 硬度和室温拉伸试验按G B/T2311122002方法测定硬度,HB =278(d =3164)。
叶片硬度符合G B1221292中1Cr13牌号的技术要求。
按G B22822002方法进行室温拉伸试验,见表2。
表2 室温拉伸试验结果抗拉强度MPa 屈服强度MPa延伸率%断面收缩率%905800181565413 金相组织分析抛光态按G B10561289进行夹杂物评定,其D 类夹杂为1级,A 、B 、C 类夹杂物<1级。
腐蚀态按G B639422002评定晶粒度为5级。
金相组织为具有马氏体位向的回火索氏体,属正常的显微组织。
断裂源区未见点蚀坑等腐蚀特征。
414 断口分析(1)断口的宏观特征叶片断口均呈紫红色。
各片叶片裂纹的起始部位及宏观特征基本相同。
叶片断裂均起源于背弧中部,裂纹向内弧,向进、排气边扩展(图3)。
源区(图4)为多源,台阶状源区,裂纹起始于不同平面,源区均未见材料及86某电厂3号燃气轮机压气机叶片故障的原因分析冶金缺陷,亦未见到腐蚀特征。
扩展区较大,说明疲劳扩展比较充分,扩展区均可见到明显的疲劳弧线(图5、图6),有明显的多次载荷重大波动形成的休止线(图7)。
第一休止线以前,即源区台阶区,不同平面起裂形成的扩展棱线明显。
这些特征表明裂纹的起始应力较大。
瞬断区位于内弧一侧,比较小。
图7 断口休止线形貌 断口宏观特征相同表明各叶片的受力状况相同,均为交变应力较大的疲劳断裂。
(2)断口的微观特征叶片断口的微观特征亦相同,源区和扩展区均可见到明显的疲劳扩展特征、穿晶裂纹和二次裂纹;扩展区表面粗糙,在休止线处二次裂纹尤为明显,有的可见到韧窝特征。
(3)叶片源区能谱分析成份叶片源区能谱成份分析结果(图8)表明叶片的工作环境无明显的腐蚀气氛。
图8 断口源区能谱成份分析415 材质和断口理化检验综合分析3号叶片的化学成份、硬度符合G B1221292中1Cr13的有关技术要求。
金相组织正常,为具有马氏体位向的回火索氏体。
叶片的断裂与材质及加工无关。
叶片断口宏观特征相同,裂纹源部位相同,各叶片疲劳裂纹的萌生、扩展几乎相同,叶片断口均为交变应力较大的疲劳断口。
表明各叶片受力状况相同,断裂性质相同。
5 故障原因分析511 振动损坏燃气轮机压气机叶片损坏原因较多,其中振动为主要原因,称为振动损坏或疲劳损坏。
叶片振动损坏或疲劳损坏包括常规强迫振动损坏与颤振损坏。
(1)强迫振动的特怔激振力:气流激振力具备周期性质,只有当激振力的频率等于叶片的自振频率时,叶片才会共振。
频率:由于级内叶片频率分散度的原因,在激振力的作用下,一个激振频率仅能与级内叶片中一个叶片或几个叶片的固有频率相吻合,强迫振动是叶片以激振频率振动。
振型:一级叶片中只有一个叶片或几个叶片的强迫振动较大,不会出现同相位、同振幅的强迫振动;叶片共振疲劳故障经常在少数叶片上出现。
振幅:能量来源于激振力,在多数情况下,激振力的力幅是一定的,因此叶片振幅便保持一定值,成为恒定振幅的共振。
在一般情况下,强迫振动不会出现过大的振幅,使叶片在短时间内破坏。
96第1期 热力透平疲劳特征:为高周疲劳损伤,叶片断口的疲劳条带窄、沿晶或穿晶裂纹、疲劳扩展区表面较细。
(2)颤振的特怔激振力:气流激振力不需要脉动性质,气流仅在特定的气动条件下,才对叶片形成颤振的激励能源。
频率:以叶片某种振形的固有频率振动。