复合材料模压工艺
复合材料模压成型的工艺特性和影响因素分析

复合材料模压成型的工艺特性和影响因素分析摘要:本文简述了聚合物基复合材料模压成型工艺特性,对模压成型的设备、预浸料、工装模具、工作环境条件等提出相应要求,着重对成型工艺过程中模压成型温度、压力、保温时间等工艺参数对复合材料制品性能影响做了分析,且简要介绍了复合材料模压制品可能出现的质量问题、产生原因、预防措施等内容。
关键词:复合材料;模压成型;工艺特性;影响因素现今社会复合材料越来越受到重视,并不断朝着更高比刚度、耐更苛刻工作环境等超高性能方向发展。
因此复合材料在材料科学中占据着重要地位,它的发展大大丰富了材料科学的内容。
复合材料成型工艺方法主要有手糊、注射、缠绕、真空导流、模压、热压罐、软模、树脂传递模塑等。
复合材料成型工艺是其重要环节,通常包括两个阶段,首先是使原材料在一定温度和压力下产生变形或流动,获取所需的形状,然后设法保持其形状。
本文着重对复合材料模压成型工艺特性、成型过程、影响制品质量因素及制品缺陷的产生原因及预防措施等内容作了简单叙述。
一、模压成型工艺特性模压成型工艺是将一定量预浸料放入到金属模具的对模腔中,利用带热源的压机产生一定的温度和压力,合模后在一定的温度和压力作用下使预浸料在模腔内受热软化、受压流动、充满流动、充满模腔成型和固化,从而获得复合材料制品的一种工艺方法。
模压成型工艺的特点是在成型过程中需要加热,加热的目的是使预浸料中树脂软化流动,充满模腔,并加速树脂基体材料的固化反应。
预浸料充满模腔过程中,不仅树脂基体流动,增强材料也随之流动,树脂基体和增强纤维同时填满模腔的各个部位。
只有树脂基体粘度很大、粘结力很强才能与增强纤维一起流动,因此模压工艺所需的成型压力较大,这就要求金属模具具有高强度、高精度和耐腐蚀,并要求用专用的热压机来控制固化成型的温度、压力、保温时间等工艺参数。
模压成型方法生产效率较高,制品尺寸准确,表面光洁,尤其对结构复杂的复合材料制品一般可一次成型,不会损坏复合材料制品性能。
复合材料模压成型工艺与应用技术

复合材料模压成型工艺与应用技术【摘要】随着复合材料生产水平和成型效率的提高,在各行各业已经取得了广泛的应用。
通过分析SMC、WCM、PCM三种模压成型工艺的工艺特点和关键技术,对三种高效率成型工艺的应用场景进行了对比。
总结而言,通过结构统型扩大单件产量需求,采用高效率模压成型工艺实现自动化生产,将进一步降低复合材料部件的制造成本。
【关键词】复合材料;高效率;低成本;模压成型1.引言以碳纤维、玻璃纤维、芳纶纤维等为代表的纤维增强复合材料,具备高比强度、高比模量、高耐候的优异特性,是目前最理想、应用最广泛的轻量化材料之一。
随着国内复合材料生产水平的提高以及成型效率的提升,复合材料越来越广泛地被各行各业接受。
在很多应用场景下,复合材料结构全生命周期的应用成本或低于金属结构。
面对汽车、风电、轨道交通等大批量应用场景,生产效率对成本的影响尤为关键。
复合材料的成型工艺为重要环节,高效低成本成型工艺的应用将直接降低部件的生产制造成本。
复合材料模压成型工艺是典型的高效成型工艺之一,具备以下优势:1.生产效率高,便于实现专业化和自动化生产;2.产品尺寸精度高,可重复性好;3.制品的内应力很低,且翘曲变形也很小,机械性能较稳定;4.表面光洁度高,无需二次加工;5.可在一给定的模板上放置模腔数量较多的模具,生产率高;6.原材料的损失小,不会造成过多的损失(通常为制品质量的2%-5%);7.能一次成型结构复杂的制品;8.模腔的磨损很小,模具的维护费用较低。
同时模压成型也存在一定的不足:1.不适用于存在凹陷、侧面倾斜等的复杂制品;2.在制作过程中,完全充模存在一定的难度;3.模具制造较为复杂,投资较大;4.产品尺寸受压机限制,一般只适合制造中小型复合材料制品。
复合材料模压成型工艺类型很多,本文主要对三种高效率复合材料模压成型工艺技术及其应用场景进行分析。
1.复合材料高效率模压成型工艺复合材料模压成型工艺在各种成型方法中占有十分重要的地位,其优势在于成型异形制品的高效率、高可重复性制造。
复合材料模压工艺

复合材料模压工艺(总7页)--本页仅作为文档封面,使用时请直接删除即可----内页可以根据需求调整合适字体及大小--复合材料模压工艺复合材料由于其众所周知的优异性能及各种工艺的日益成熟、原材料来源丰富、成本下降、可靠性提高,使其受到用户与生产者双方的青睐,越来越多地取代传统金属材料,我们的时代已进入了复合材料时代。
据美国塑料工业协会复合材料所(Society of the Plastics Industry's Instit ute)1997年元月27日发表的年度统计报告表明:1996年美国复合材料的销售量为161万吨,比1995年的万吨增长约%,是复合材料的销售量连续第五年增长。
据预测,1997年以及以后五年内复合材料销售量仍会连续增长。
聚合物基复合材料模压成形工艺在各种成形工艺方法中占有重要地位,主要用于异型制品的成形,因而所用的成形压力高于其它工艺方法。
由于模压成形工艺所需设备简单,又能对纤维料、碎布、毡料、层压制品、缠绕制品、编织物进行模压成形,因而被各种规模的复合材料生产企业所普遍采用,复合材料模压工艺也几乎为各生产单位家喻户晓。
因此,本文并不打算对模压复合材料制品工艺进行系统介绍,仅就影响复合材料制品质量的一些重要环节谈谈体会,因为就复合材料复杂结构异型件而言,保证质量、提高合格率比一般制件更为重要,难度也更大。
一、对复合材料模压制品质量产生影响的因素模压成形工艺的基本过程是将一定量的经过一定预处理的模压料放入预热的压模内,施加较高的压力使模压料充满模腔。
在预定的温度条件下,模压料在模腔内逐渐固化,然后将制品从压模内取出,再进行必要的辅助加工即得到最终制品。
从上述过程看,完成最终制品涉及的因素有模压料本身、压模模具、加压加温的热压机等;最重要的当是压制工艺,本文将单列一节予以重点讲述;还有工作环境和辅助加工等。
1.模压料任何形式的模压料(碎布料、毡料、长、短纤维),在装模前均应使其按预定比例与树脂均匀浸渍。
smc模压成型工艺流程

SMC模压成型工艺流程SMC模压成型是一种常见的复合材料成型工艺,被广泛应用于汽车、航天、建筑等领域。
SMC(Sheet Molding Compound)是一种预浸有树脂的增强复合材料,主要由玻璃纤维、石墨、填料和热固性树脂等组成。
在SMC模压成型过程中,首先将预制好的SMC 预浸料加热软化,然后通过模具形成所需的零部件形状,最终在加热和压力的作用下固化成型,达到产品设计要求。
以下是SMC模压成型的工艺流程。
SMC模压成型工艺流程1. 准备工作在SMC模压成型之前,需要准备好所需的模具、预浸SMC料、加热设备以及压力设备等。
确保所有设备运行正常,符合操作规范。
2. 加热预浸料将预制的SMC料放入加热设备中,经过加热软化,使树脂充分熔化,增强纤维得到活化,便于后续成型。
3. 模具装配将加热后的SMC料放入模具中。
模具需要根据所需产品的设计图纸来选择,并确保模具表面干净平整,涂抹模具脱模剂以防粘连。
4. 模压成型开始进行模压成型工艺,将已经装配好的SMC料模具置于压力设备中,通过加压使SMC料充分填充模具腔体,并且确保均匀分布。
5. 施加压力在模具内加入适当的压力,使SMC料在热固化过程中得到充分压实,以确保产品密度和强度。
6. 加热固化通过加热设备对模具中的SMC料施加恒定的温度,使树脂充分固化,增强纤维和填料得到固定,从而形成产品的稳定结构。
7. 冷却脱模待SMC料在模具中充分固化后,关闭加热设备,待产品冷却至室温。
然后打开模具,取出成型产品,进行后续的修整和表面处理。
8. 检验和包装对成型的产品进行外观检验、尺寸检测以及性能测试,确保产品符合设计要求。
最后对产品进行包装,以防止在运输和储存过程中受到损坏。
以上就是SMC模压成型的工艺流程,通过严谨的操作和控制,可以生产出高质量的复合材料制品,满足各行业对材料性能和外观要求的不断提升。
复合材料模压成型工艺过程
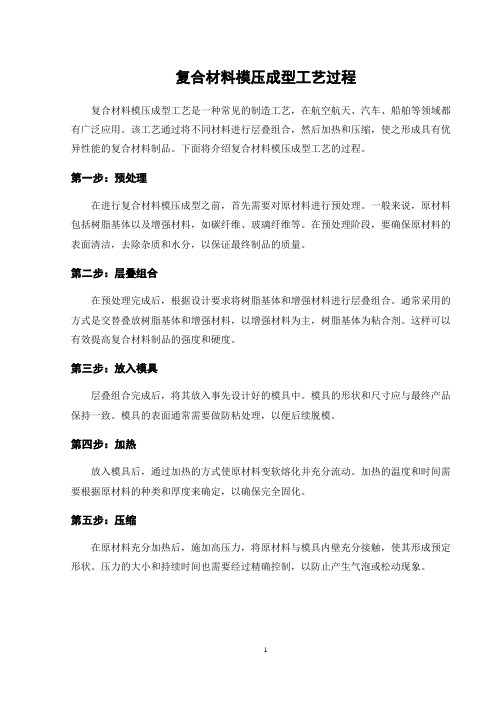
复合材料模压成型工艺过程复合材料模压成型工艺是一种常见的制造工艺,在航空航天、汽车、船舶等领域都有广泛应用。
该工艺通过将不同材料进行层叠组合,然后加热和压缩,使之形成具有优异性能的复合材料制品。
下面将介绍复合材料模压成型工艺的过程。
第一步:预处理在进行复合材料模压成型之前,首先需要对原材料进行预处理。
一般来说,原材料包括树脂基体以及增强材料,如碳纤维、玻璃纤维等。
在预处理阶段,要确保原材料的表面清洁,去除杂质和水分,以保证最终制品的质量。
第二步:层叠组合在预处理完成后,根据设计要求将树脂基体和增强材料进行层叠组合。
通常采用的方式是交替叠放树脂基体和增强材料,以增强材料为主,树脂基体为粘合剂。
这样可以有效提高复合材料制品的强度和硬度。
第三步:放入模具层叠组合完成后,将其放入事先设计好的模具中。
模具的形状和尺寸应与最终产品保持一致。
模具的表面通常需要做防粘处理,以便后续脱模。
第四步:加热放入模具后,通过加热的方式使原材料变软熔化并充分流动。
加热的温度和时间需要根据原材料的种类和厚度来确定,以确保完全固化。
第五步:压缩在原材料充分加热后,施加高压力,将原材料与模具内壁充分接触,使其形成预定形状。
压力的大小和持续时间也需要经过精确控制,以防止产生气泡或松动现象。
第六步:冷却经过加热和压缩后,复合材料开始冷却固化。
在这个过程中,保持模具的压力不变,直至完全固化为止。
冷却时间的长短取决于原材料的性质和厚度。
第七步:脱模当复合材料完全固化后,打开模具,将制成的复合材料制品取出。
在脱模的过程中,需要小心操作,以避免损坏制品表面或内部结构。
通过以上步骤,复合材料模压成型工艺完成。
这种工艺具有制作周期短、成本低、制品质量高等优点,因此在工业生产中得到广泛应用。
复合材料制品具有重量轻、强度高、耐腐蚀等特点,在现代制造业中发挥着重要作用,也在未来的发展中将有更广阔的应用前景。
LFT-D复合材料模压成型工艺研究

—133—《装备维修技术》2021年第13期LFT-D 复合材料模压成型工艺研究梁绍吉(珠海格力电器股份有限公司,广东 珠海 519070)摘 要:针对LFT-D 复合材料模压成型,介绍生产线构成、生产工艺流程,结合超大型LFT-D 客车空调底盘的开发研究,分析相关因素的影响,验证确定工艺参数。
关键词:LFT -D 复合材料;模压成型;生产线设备;空调底盘引言玻璃纤维增强塑料俗称玻璃钢,它以价格低廉,固化后综合性能好,尤其在小批量生产中可降低成本和缩短生产周期,因此玻璃钢在客车行业应用广泛。
我司客车空调底盘用玻璃钢制作,随着产量增大,玻璃钢的缺点也日益呈现,如产品成型一致性差,漏水问题严重,绝缘性能差,生产不环保,材料不可回收利用,因此需要研究质量稳定、环保的产品制作工艺。
LFT-D 是以热塑性树脂为基体(PP 、PA 、PET 等),以长玻纤为增强材料的复合材料直接模压成型工艺。
目前在欧美、日本等发达国家,轻质、高强度,可回收的LFT -D 技术正广泛应用于汽车零部件生产,尤其是在机械强度要求较高的零部件如前端框架、吸能防撞保险杠、座椅骨架等。
本文主要讲述LFT-D 复合材料模压成型工艺及其应用于客车空调底盘的研究,用PP 和玻璃纤维作为主要材料来制作。
1 LFT -D 模压成型生产线构成LFT -D 模压成型生产线主要由三个部分构成,挤出、输送、成型。
挤出部分装置由真空上料机、连续称重计量混合装置、双螺杆挤出机构成,输送部分装置由玻纤切割计量装置、立式双刃双向加热切断机组、不锈钢保温输送机组构成,成型装置是液压压力机。
2 LFT -D 模压成型生产工艺流程模压成型主要工艺流程为在第一段螺杆中加入PP 并加热熔融,PP 和玻璃纤维加入到第二段螺杆中加热熔融并混合,再通过挤出机挤出,然后根据成型产品所需的质量定额将熔体切断,再将熔体保温输送到模具中进行模压成型,最后冷却定型和后处理。
3 产品分析根据空调系统和结构设计,底盘尺寸确定为3297mm*1803mm*238mm ,产品和模具是目前模压成型中最大的,没有现成的经验可以参考,如何制造出合格的产品,需要不断摸索和试验,并保证强度足够,能长期抵抗客车运行振动。
复合材料的预浸料模压成型工艺
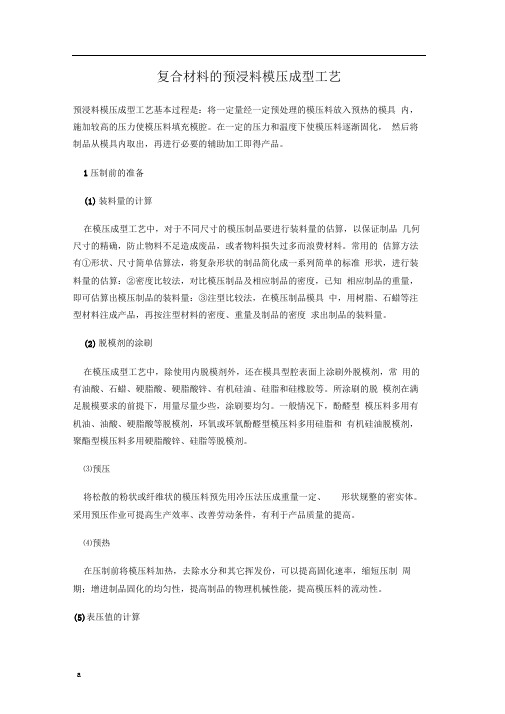
复合材料的预浸料模压成型工艺预浸料模压成型工艺基本过程是:将一定量经一定预处理的模压料放入预热的模具内,施加较高的压力使模压料填充模腔。
在一定的压力和温度下使模压料逐渐固化,然后将制品从模具内取出,再进行必要的辅助加工即得产品。
1压制前的准备(1)装料量的计算在模压成型工艺中,对于不同尺寸的模压制品要进行装料量的估算,以保证制品几何尺寸的精确,防止物料不足造成废品,或者物料损失过多而浪费材料。
常用的估算方法有①形状、尺寸简单估算法,将复杂形状的制品简化成一系列简单的标准形状,进行装料量的估算:②密度比较法,对比模压制品及相应制品的密度,已知相应制品的重量,即可估算出模压制品的装料量:③注型比较法,在模压制品模具中,用树脂、石蜡等注型材料注成产品,再按注型材料的密度、重量及制品的密度求出制品的装料量。
(2)脱模剂的涂刷在模压成型工艺中,除使用内脱模剂外,还在模具型腔表面上涂刷外脱模剂,常用的有油酸、石蜡、硬脂酸、硬脂酸锌、有机硅油、硅脂和硅橡胶等。
所涂刷的脱模剂在满足脱模要求的前提下,用量尽量少些,涂刷要均匀。
一般情况下,酚醛型模压料多用有机油、油酸、硬脂酸等脱模剂,环氧或环氧酚醛型模压料多用硅脂和有机硅油脱模剂,聚酯型模压料多用硬脂酸锌、硅脂等脱模剂。
⑶预压将松散的粉状或纤维状的模压料预先用冷压法压成重量一定、形状规整的密实体。
采用预压作业可提高生产效率、改善劳动条件,有利于产品质量的提高。
⑷预热在压制前将模压料加热,去除水分和其它挥发份,可以提高固化速率,缩短压制周期;增进制品固化的均匀性,提高制品的物理机械性能,提高模压料的流动性。
(5)表压值的计算在模压工艺中,首先要根据制品所要求的成型压力,计算出压机的表压值。
成型压力是指制品水平投影面上单位面积所承受的压力。
它和表压值之间存在的函数关系:j成型压力,即表压T MPa;仁——制品婴求的单位压力■念J\—压机额定表压,MPa:5 一制品水平投影面积T CT3;T——压机吨位,g复合材料的预浸料模压成型工艺在模压成型工艺中,成型压力的大小决定于模压料的品种和制品结构的复杂程度,成型压力是选择压机吨位的依据。
[复合材料模压工艺]复合材料模压成型工艺
![[复合材料模压工艺]复合材料模压成型工艺](https://img.taocdn.com/s3/m/929d26f131126edb6e1a105d.png)
[复合材料模压工艺]复合材料模压成型工艺复合材料模压工艺复合材料由于其众所周知的优异性能及各种工艺的日益成熟、原材料来源丰富、成本下降、可靠性提高,使其受到用户与生产者双方的青睐,越来越多地取代传统金属材料,我们的时代已进入了复合材料时代。
据美国塑料工业协会复合材料所(SocietyofthePlasticsIndustry"sInstitute)1997年元月27日发表的年度统计报告表明:1996年美国复合材料的销售量为161万吨,比1995年的158.5万吨增长约1.6%,是复合材料的销售量连续第五年增长。
据预测,1997年以及以后五年内复合材料销售量仍会连续增长。
聚合物基复合材料模压成形工艺在各种成形工艺方法中占有重要地位,主要用于异型制品的成形,因而所用的成形压力高于其它工艺方法。
由于模压成形工艺所需设备简单,又能对纤维料、碎布、毡料、层压制品、缠绕制品、编织物进行模压成形,因而被各种规模的复合材料生产企业所普遍采用,复合材料模压工艺也几乎为各生产单位家喻户晓。
因此,本文并不打算对模压复合材料制品工艺进行系统介绍,仅就影响复合材料制品质量的一些重要环节谈谈体会,因为就复合材料复杂结构异型件而言,保证质量、提高合格率比一般制件更为重要,难度也更大。
一、对复合材料模压制品质量产生影响的因素模压成形工艺的基本过程是将一定量的经过一定预处理的模压料放入预热的压模内,施加较高的压力使模压料充满模腔。
在预定的温度条件下,模压料在模腔内逐渐固化,然后将制品从压模内取出,再进行必要的辅助加工即得到最终制品。
从上述过程看,完成最终制品涉及的因素有模压料本身、压模模具、加压加温的热压机等;最重要的当是压制工艺,本文将单列一节予以重点讲述;还有工作环境和辅助加工等。
1.模压料任何形式的模压料(碎布料、毡料、长、短纤维),在装模前均应使其按预定比例与树脂均匀浸渍。
对经溶剂稀释的树脂溶液,在浸渍纤维后应充分晾置使溶剂挥发。
- 1、下载文档前请自行甄别文档内容的完整性,平台不提供额外的编辑、内容补充、找答案等附加服务。
- 2、"仅部分预览"的文档,不可在线预览部分如存在完整性等问题,可反馈申请退款(可完整预览的文档不适用该条件!)。
- 3、如文档侵犯您的权益,请联系客服反馈,我们会尽快为您处理(人工客服工作时间:9:00-18:30)。
复合材料模压工艺
复合材料由于其众所周知的优异性能及各种工艺的日益成熟、原材料来源丰富、成本下降、可靠性提高, 使其受到用户与生产者双方的青睐, 越来越多地取代传统金属材料,我们的时代已进入了复合材料时代。
据美国塑料工业协会复合材料所(Society of the Plastics Industry's Instit ute)1997 年元月27 日发表的年度统计报告表明:1996 年美国复合材料的销售量为161万吨,比1995年的万吨增长约%,是复合材料的销售量连续第五年增长。
据预测,1997 年以及以后五年内复合材料销售量仍会连续增长。
聚合物基复合材料模压成形工艺在各种成形工艺方法中占有重要地位, 主要用于异型制品的成形,因而所用的成形压力高于其它工艺方法。
由于模压成形工艺所需设备简单, 又能对纤维料、碎布、毡料、层压制品、缠绕制品、编织物进行模压成形, 因而被各种规模的复合材料生产企业所普遍采用, 复合材料模压工艺也几乎为各生产单位家喻户晓。
因此, 本文并不打算对模压复合材料制品工艺进行系统介绍, 仅就影响复合材料制品质量的一些重要环节谈谈体会, 因为就复合材料复杂结构异型件而言, 保证质量、提高合格率比一般制件更为重要, 难度也更大。
、对复合材料模压制品质量产生影响的因素
模压成形工艺的基本过程是将一定量的经过一定预处理的模压料放入预热的压模内, 施加较高的压力使模压料充满模腔。
在预定的温度条件下, 模压料在模腔内逐渐固化, 然后将制品从压模内取出, 再进行必要的辅助加工即得到最终制品。
从上述过程看, 完成最终制品涉及的因素有模压料本身、压模模具、加压加温的热压机等;最重要的当是压制工艺, 本文将单列一节予以重点讲述; 还有工作环境和辅助加工等。
1. 模压料
任何形式的模压料(碎布料、毡料、长、短纤维), 在装模前均应使其按预定比例与树脂均匀浸渍。
对经溶剂稀释的树脂溶液, 在浸渍纤维后应充分晾置使溶剂挥发。
晾置时间与环境温度湿度有关。
2. 压制模具
制品用的模具除应保证在工作压力下的强度、刚度条件以外, 主要应考虑能给制品的各部位、各方向较均匀地加上压力。
一定的拔模斜度既能保证制品顺利出模, 又能起到侧向加压的作用。
模具设计尽量使制品整体成形,既可保证制品的强度、刚度,又可减少辅助加工工序和工装模具数量。
在模具上应开有流胶槽使多余的胶料顺利排出
压模的成型表面应至少进行抛光或镀铬,使光洁度在4 9以上,
以保证顺利脱模。
应在模具靠近型腔部位开设测温孔。
模具本身, 必要时考虑设计一定的附件以保证较方便地实现脱模。
3. 压机压机的尺寸和吨位应能满足制品及所选材料、模具结构的
要求。
压机的温度、压力最好能有手控和自动控制两种模式。
压机的工作台或上下加热板应尽量使工件保持水平以避免树脂
向一侧流聚。
加热板在有效工作范围内温度差控制在士5C左右。
4. 工作场地
工作场地应光线充足、通风良好,温度、湿度满足要求,吊升降叉车、真空泵、压缩机、工作台等配套设备齐全、工作安全可靠。
环境清洁、整齐。
二、复合材料模压制品的压制工艺
复合材料模压制品的压制工艺(以环氧树脂基体复合材料为例)
是指模压料装模后在固化剂存在或加热的条件下在模腔内固化成制品的过程。
它是温度、压力、时间综合作用的结果, 压制工艺条件的选择及可靠控制是决定制品质量的关键。
虽然原则上讲某一种牌号的树脂有一定的固化特性, 但由于同牌号
树脂的分子量、软化点,环氧值等都有一定的变化范围, 因而固化特性也
会有所差异。
为保证复合材料制品的质量, 最好对每一批次树脂的固化
特性进行测定, 以确定最佳的压制工艺。
这一工作我们是通过DDA动态介电分析)和DMA动态力学性能分析)来完成的。
环氧树脂的固化过程从DDA曲线来看可分为软化流动、凝胶、固化、熟化(后固化)四个阶段。
如将后两个阶段合并为固化阶段也可视为三个阶段。
根据制品材料制作的试片所测的DDA曲线,再根据制件的厚度和模具结构情况, 确定在一定的加热速度下每个阶段所需保温时间和加压时机。
在对不同加热速率、不同保温时间和加压时机的试片进行DM/测试后,选择动态力学性能最好的试片的温度、压力与时间关系的固化特性确定压制工艺。
图1、2、3分别为F46+BF・MEA 树脂体系试片的DDA DMA W试曲线及该体系为基体的结构制品的固化曲线。
由于该复合材料制品尺寸大、厚度厚、结构复杂, 为保证接头部位的强度和刚度又采用了难度很大的整体成形工艺, 因而固化压制工序成了特别关键的工序。
考虑产品大而厚的因素及压机中心位置与边缘温度的差异,为保证整个产品均匀固化,我们在80C的软化流动峰前增加了在(45 士5)C时小时的低温保温过程。
另外,在固化后的自然降温阶段, 考虑到钢模与碳复合材料热物理性能的差异, 为避
免钢模收缩造成复合材料制品的翘曲变形, 在工艺文件中规定在产品
温度降至70C左右时松开模具四周的顶模螺钉,使产品自由降至室温
再卸模。
在上述压制工艺条件下压制的制品合格率达到90%以上。
三、聚合物基复合材料模压制品的缺陷、产生的原因及预防措施
影响复合材料制品质量的因素很多, 从原材料的选用到预浸料的制备、贮存, 从生产环境到每道生产工序都会影响最终制品的性能。
对热固性树脂基复合材料而言, 最终产品一旦发现重大质量问题则很难挽救。
特别是整体成形的较大制品, 无论从当前原材料仍然昂贵的价格, 还是从制品的生产周期, 质量问题造成的损失都将是巨大的。
因此, 总结实践经验找出缺陷产生的原因, 制定有效的预防措施都将是很有意义的。
表 1 列出了聚合物基复合材料模压制品的缺陷、产生原因及预防措施, 可供参考。
四、复合材料模压制品工艺新进展
据1997年 4 月23日至25日在法国巴黎召开的第32 届“欧洲复合材料”和“先进材料与加工工程科学”大会报导, 德国凯瑟斯劳腾的复合材料研究所(Institut fur
Verbundwerkstoffe,Kaiserslautern, 简称IVW)从1993 年起研制了
一种双面传送压机, 可以压制聚合物基复合材料连续薄板。
该研究所
用纤维布和热塑性树脂膜作原料, 采用连续等压工艺制出浸渍质量良好的宽度达600mm勺预制板(带)。
压机的主要工作参数为:温度高达410C ,压力可达到。
预制板在加热条件下可在不到一分钟的时间内模压或冲压成最终制品, 形成了预处理、塑化、模压和后加工一条龙生产线。
双面传送压机可用各种纤维增强各种树脂制成预制板, 再压制成各种形状复杂的结构件,比RTM法、热压罐成形法等生产操作简单, 生产周期短, 是一种很有前途的工业复合材料制品模压工艺。
由德国、意大利、西班牙、瑞典几家公司合作, 在欧共体的支持下还完成了用夹层板生产汽车内外结构件的研究工作。
这种夹层材料用13mm勺热塑性发泡材料做骨架,用10层玻璃纤维浸渍聚酰胺树脂,再上压机压成纤维体积含量为50%勺2mm厚的板作为蒙皮。
压制前用计算机模拟三维夹层板模压工艺过程, 以估算其最大许用变形采取防止层压缺陷的措施等。
整个产品的模压至冷却仅用40秒的时间即可完成。
这种汽车结构板抗压能力强, 骨架与蒙皮共固化, 界面粘接良好, 无需辅助粘接工艺。
这种结构材料汽车在发生撞击时可吸收能量,减轻车祸, 增加乘客安全,是一种高强度、高刚度、轻质的结构功能材料。
总之, 近几年来随着复合材料生产自动化和建立在二维与三维织物的先进工艺基础上的复合材料半成品材料工业的发展, 以长或短纤维为增强材料, 以热塑性、热固性树脂为基体材料的各类复合材
料模压制品工艺发展很快,产品性能价格比高,环境污染小,生产率高, 已经或正在不断适应汽车公交业、航空航天业、化工业、桥梁、通讯等领域工业化发展的需要。
参考文献(略)
5. 适时加压,不要过早,过迟1. 纤维,树脂或溶剂中含
杂质
2. 排布机不清洁
3.铺层环境不清洁
夹杂 4.预浸料晾置时未加保护
膜
5.隔离纸质量差、掉毛
6.操作时不慎,带进杂质
或忘记去除预浸料保护膜
1. 铺层时未压实
2. 铺层时预浸料上粘有脱分层模剂或油污
3. 脱模不当
4. 压力不够1. 严格检查原材料,去除杂质
2. 操作前、后清理排布机
3. 工作环境干净整洁,操作人员穿好工作服
4. 预浸料晾置加盖保护膜防止
灰尘
5. 选用合格隔离纸
6. 操作人员经培训考核上岗
1. 铺层时各层间切实压实
2. 严禁将脱模剂或油污粘在预
浸料上,操作人员带手套
3. 正确脱模,不许乱撬、乱铲
4. 适当加大压力
5. 尽量避免胶铆接时的应力集。