第三章-非高炉炼铁重点设备介绍(下)..
(完整版)高炉炼铁工艺流程及主要设备简介
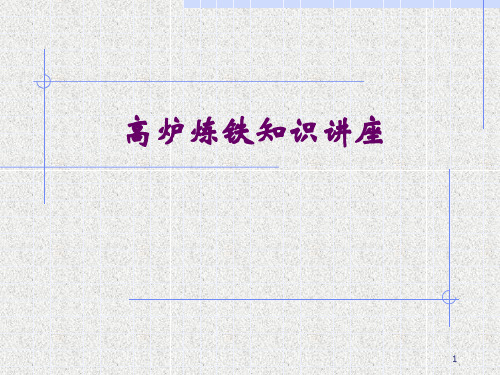
三、高炉冶炼主要设备简介
1、高炉 高炉炉本体较为复杂。 横断面为圆形的炼铁竖炉。用 钢板作炉壳,壳内砌耐火砖内衬。高炉本体自上而下 分为炉喉、炉身、炉腰、炉腹 、炉缸5部分。高炉生 产时从炉顶装入铁矿石、焦炭、造渣用熔剂(石灰 石),从位于炉子下部沿炉周的风口吹入经预热的空 气。在高温下焦炭中的碳同鼓入空气中的氧燃烧生成 的一氧化碳和氢气,在炉内上升过程中除去铁矿石中 的氧,从而还原得到铁。炼出的铁水从铁口放出。铁 矿石中未还原的杂质和石灰石等熔剂结合生成炉渣, 从渣口排出。产生的煤气从炉顶排出,经除尘后,作 为热风炉、加热炉、焦炉、锅炉等的燃料。高炉冶炼 的主要产品是生铁 ,还有副产高炉渣和高炉煤气。
1—高炉;2—重力除尘器;3 — 布袋除尘器; 4—调压阀组
23
三、高炉冶炼主要设备简介 重力除尘
24
三、高炉冶炼主要设备简介
箱体除尘: 由重力除尘后的荒煤气进入箱体进行布 袋过滤,最后成为净煤气。要求净煤气 粉尘量小于10毫克。
25
高炉冶炼主要设备简介
刮板机
26
高炉冶炼主要设备简介
27
高炉冶炼主要设备简介
炉渣和生铁定期通过铁口外排。通过炉前撇渣器进行渣 铁分离,铁水通过铁水罐运到炼钢或铸铁。炉渣经过 水淬后,输送到渣场。
高炉炼铁的主产品是生铁,副产品是高炉煤气、水渣、 炉尘。
5
二、高炉炼铁原理
6
三、高炉冶炼主要设备简介
高护炼铁设备组成有:①高炉本体;②供料设备;③ 送风设备;④喷吹设备;⑤煤气处理设备;⑥渣铁处 理设备。 通常,辅助系统的建设投资是高炉本体的4~5倍。生 产中,各个系统互相配合、互相制约,形成一个连续 的、大规模的高温生产过程。高炉开炉之后,整个系 统必须日以继夜地连续生产,除了计划检修和特殊事 故暂时休风外,一般要到一代寿命终了时才停炉。 高炉炼铁系统(炉体系统、渣处理系统、上料系统、 除尘系统、送风系统)主要设备简要介绍一下。
非高炉炼铁

非高炉炼铁一、非高炉炼铁的发展高炉炼铁是炼铁生产的主题,经过长期的发展,它的技术已经非常成熟。
但它也存在固有的不足,即对冶金焦的强烈依赖。
但随着焦煤资源的日渐贫乏,冶金焦价格越来越高。
因此,使炼铁生产摆脱对冶金焦的依赖是开发非高炉炼铁的原动力。
经过数百年的发展,至今已形成了以直接还原和熔融还原为主的现代化非高炉炼铁工业体系。
现代化钢铁工艺流程主体由四部分构成,焦炉、造块设备(例如烧结机)、高炉和转炉。
高炉使用冶金焦为主题能源,他是由焦煤经炼焦得到。
高炉的产品是液态生铁,它经转炉冶炼成转炉钢。
熔融还原的产品相当于高炉铁水。
高炉使用冶金焦,熔融反应则使用非焦煤。
这样就使炼铁摆脱了对冶金焦的依赖。
直接还原的产品是在熔点以下还原得到固态金属铁,称为直接还原铁(DRI),又称海绵铁。
直接还原的流程可分为煤基直接还原、气基直接还原和电热直接还原三大类。
煤基直接还原以煤为主要能源,主要是使用回转炉为主体设备的流程。
气基直接还原以天然气为主题能源。
包括竖炉、反应罐和流化床流程。
电热直接还原以电力为主要能源,是使用电热竖炉直接还原流程。
熔融还原的主体能源主要分为三种:非焦煤,焦炭和电力。
熔炼设备是熔融还原流程的精华。
还原设备决定了适用原料的性质。
例如流化床可直接处理粉料,竖炉则适用于处理块状炉料。
二、重点设备分析直接还原的核心装置是一个还原单元。
占有重要地位的还原设备有竖炉,反应罐,回转炉和流化床。
熔融还原的核心装置时一个还。
原单元和一个熔炼造气单元。
最受重视的还原设备是竖炉和流化床,最重要的熔炼造气设备是煤炭流化床和铁浴炉。
竖炉是一种成熟的还原设备。
除了产量在海绵铁工业中高居榜首外,熔融还原也将它作为还原单元最实际的选择。
目前唯一的工业化二步法熔融还原流程COREX即使用竖炉还原单元。
作为还原设备,流化床的地位非常微妙。
海绵铁工业中流化床的生产能力并不大。
但他具有一个竖炉无法比拟的优点:可直接使用粉矿。
这个特点使流化床成为熔融还原中最受青睐的还原设备。
高炉炼铁的工艺流程及主要设备

高炉炼铁的工艺流程及主要设备概述高炉炼铁是一种传统的冶炼工艺,用于将铁矿石转化为熔融的生铁。
这个过程涉及多个步骤和大量的设备,其中每个步骤都至关重要。
工艺流程1. 铁矿石的预处理首先,铁矿石需经过预处理,包括破碎、磨粉和矿石的分类。
这些步骤有助于提高矿石的反应性,使其更容易在高炉中被还原。
2. 喂料矿石、焦炭和石灰石等原料被送入炉内,形成“料柱”。
这些原料在高炉炼铁过程中将被逐渐还原,并最终形成生铁。
3. 还原在高炉中,由于焦炭的还原作用,铁矿石中的铁氧化物会逐渐还原为金属铁。
同时,石灰石还能吸收硫等有害元素。
4. 熔化当铁矿石被还原后,熔融的生铁会沿料柱往下移动,并最终流出高炉。
5. 放出渣炼铁过程中产生的渣会上浮到生铁表面并被排出高炉,从而将不需要的非金属物质排除。
6. 铁水处理生铁从高炉中流出后,需要进一步进行处理,去除夹杂物质,以提高铁的品质。
主要设备•高炉:用于炼制铁矿石成为生铁的主要设备。
•炉料制备系统:包括矿石破碎机、输送带等设备,用于将原料处理成适合入炉的状态。
•热风炉系统:用于向高炉提供热风,促进铁矿石的还原。
•煤气净化系统:将高炉产生的煤气进行净化处理,以回收有价值的物质。
•废气处理系统:对高炉排放的废气进行处理,以符合环保要求。
•铁水处理设备:包括转炉、钢包等设备,用于对生铁进行进一步加工处理。
结论高炉炼铁是一项复杂的工艺,涉及多个步骤和设备的协同作用。
通过对每个环节的精细控制和优化,可以提高生铁的质量和产量,同时降低生产成本。
在环保意识日益增强的今天,高炉炼铁企业应致力于提高资源利用效率,减少排放,实现可持续发展。
非高炉炼铁
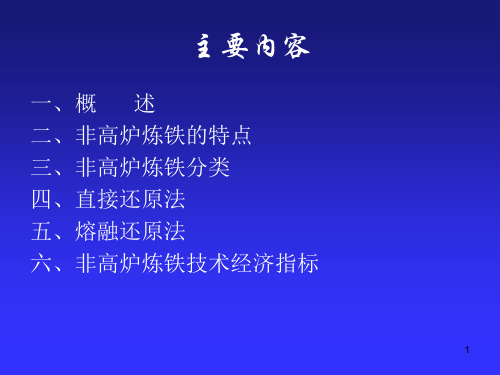
3.二步法-KR法(COREX法)工艺介绍
二步法: 将熔融还原
过程分为固相预还 原及熔态终还原并 分别在两个反应器 中完成; 优点:
改善了能量 利用,降低了渣中 FeO浓度。
12
六、非高炉炼铁技术经济指标
1.单位容积利用系数:
每立方米反应器有效容积每天的产品量,即 η=Q/Vu, t/(m3.d)
8
3.使用气体还原剂举例(Midrex法)
工艺过程: 天 然 气 + 净 化 炉 顶 气 (300-
400℃)→混合室→重整炉 (Ni 催 化 剂 ) →900-950 ℃反应:
CH4+H2O=CO+3H2 CH4+CO2=2CO+2H2 还原气→竖炉(炉料炉顶加入) →停留6h →冷却带N2冷却 至100℃ →炉料排出
主要内容
一、概 述 二、非高炉炼铁的特点 三、非高炉炼铁分类 四、直接还原法 五、熔融还原法 六、非高炉炼铁技术经济指标
1
一、概 述
1.概 念 非高炉炼铁法是高炉法之外,不用焦炭
炼铁的各种工艺方法的统称。
2.发展史 1770 年 第 一 个 直 接 还 原 法 专 利 诞 生
→1857 年 提 出 完 整 的 近 代 直 接 还 原 (Chenot)构思→1873建成第一座非高炉 装置→上世纪20年代电炉(矿热炉)炼铁 →70年代具备一定规模→近期又重新成为 研究热点
高炉流程: 矿石A在高炉内升温、
还原、熔化为铁水B→[C] 已达到饱和→在炼钢过程 脱C→再去除多余氧成为成 品钢液; 非高炉流程:
矿石被升温、还原为 海绵铁→在电炉中熔化还 原未还原部分→得到成品 钢液
4
钢铁生产过程产品中氧量、碳量的变化
高炉炼铁的工艺流程及主要设备
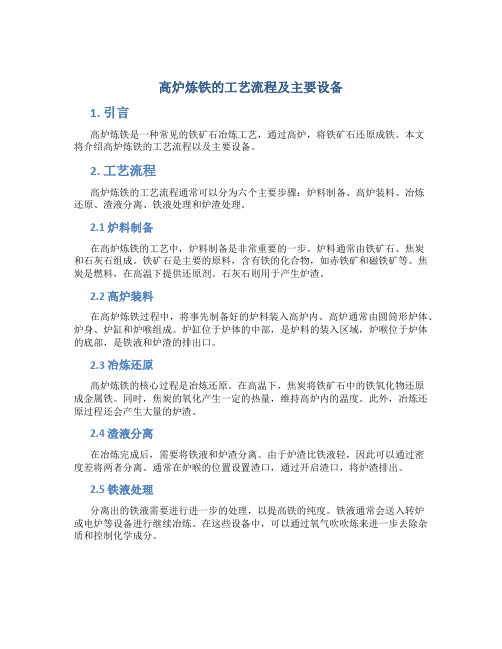
高炉炼铁的工艺流程及主要设备1. 引言高炉炼铁是一种常见的铁矿石冶炼工艺,通过高炉,将铁矿石还原成铁。
本文将介绍高炉炼铁的工艺流程以及主要设备。
2. 工艺流程高炉炼铁的工艺流程通常可以分为六个主要步骤:炉料制备、高炉装料、冶炼还原、渣液分离、铁液处理和炉渣处理。
2.1 炉料制备在高炉炼铁的工艺中,炉料制备是非常重要的一步。
炉料通常由铁矿石、焦炭和石灰石组成。
铁矿石是主要的原料,含有铁的化合物,如赤铁矿和磁铁矿等。
焦炭是燃料,在高温下提供还原剂。
石灰石则用于产生炉渣。
2.2 高炉装料在高炉炼铁过程中,将事先制备好的炉料装入高炉内。
高炉通常由圆筒形炉体、炉身、炉缸和炉喉组成。
炉缸位于炉体的中部,是炉料的装入区域,炉喉位于炉体的底部,是铁液和炉渣的排出口。
2.3 冶炼还原高炉炼铁的核心过程是冶炼还原。
在高温下,焦炭将铁矿石中的铁氧化物还原成金属铁。
同时,焦炭的氧化产生一定的热量,维持高炉内的温度。
此外,冶炼还原过程还会产生大量的炉渣。
2.4 渣液分离在冶炼完成后,需要将铁液和炉渣分离。
由于炉渣比铁液轻,因此可以通过密度差将两者分离。
通常在炉喉的位置设置渣口,通过开启渣口,将炉渣排出。
2.5 铁液处理分离出的铁液需要进行进一步的处理,以提高铁的纯度。
铁液通常会送入转炉或电炉等设备进行继续冶炼。
在这些设备中,可以通过氧气吹吹炼来进一步去除杂质和控制化学成分。
2.6 炉渣处理炉渣是冶炼还原过程中产生的副产品。
炉渣中含有一定的铁和其他金属成分,因此可以经过处理进行回收利用。
常见的炉渣处理方法包括浸出法、粉碎法和重力分离法等。
3. 主要设备在高炉炼铁工艺中,主要的设备包括高炉、转炉(或电炉)、炉缸、炉喉和渣口等。
3.1 高炉高炉是高炉炼铁过程中最重要的设备之一。
高炉通常采用圆筒形炉体,炉体内部由耐火材料构成,能够承受高温和化学腐蚀。
高炉的炉体一般由上部、中部和下部组成,各个部分有不同的功能。
3.2 转炉或电炉转炉或电炉是对分离出的铁液进行进一步处理的设备。
非高炉炼铁--重点设备介绍
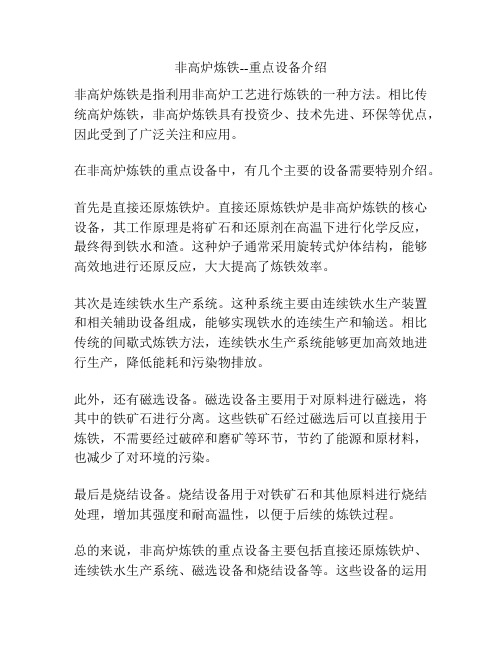
非高炉炼铁--重点设备介绍
非高炉炼铁是指利用非高炉工艺进行炼铁的一种方法。
相比传统高炉炼铁,非高炉炼铁具有投资少、技术先进、环保等优点,因此受到了广泛关注和应用。
在非高炉炼铁的重点设备中,有几个主要的设备需要特别介绍。
首先是直接还原炼铁炉。
直接还原炼铁炉是非高炉炼铁的核心设备,其工作原理是将矿石和还原剂在高温下进行化学反应,最终得到铁水和渣。
这种炉子通常采用旋转式炉体结构,能够高效地进行还原反应,大大提高了炼铁效率。
其次是连续铁水生产系统。
这种系统主要由连续铁水生产装置和相关辅助设备组成,能够实现铁水的连续生产和输送。
相比传统的间歇式炼铁方法,连续铁水生产系统能够更加高效地进行生产,降低能耗和污染物排放。
此外,还有磁选设备。
磁选设备主要用于对原料进行磁选,将其中的铁矿石进行分离。
这些铁矿石经过磁选后可以直接用于炼铁,不需要经过破碎和磨矿等环节,节约了能源和原材料,也减少了对环境的污染。
最后是烧结设备。
烧结设备用于对铁矿石和其他原料进行烧结处理,增加其强度和耐高温性,以便于后续的炼铁过程。
总的来说,非高炉炼铁的重点设备主要包括直接还原炼铁炉、连续铁水生产系统、磁选设备和烧结设备等。
这些设备的运用
使得非高炉炼铁在提高炼铁效率、降低成本、减少环境污染等方面具有显著优势。
随着科技的不断发展,相信非高炉炼铁的设备和工艺会更加完善,为炼铁行业的可持续发展做出更大的贡献。
非高炉炼铁

•非高炉炼铁非高炉炼铁是指除高炉炼铁以外的其它还原铁矿石的方法。
非高炉炼铁可归纳为两大类:直接还原法和熔融还原法,都是炼铁冶金技术中的新工艺。
直接还原法是指在铁矿石熔化温度下把铁矿石还原成海绵铁的炼铁生产过程。
产品叫直接还原铁或海绵铁。
由于低温还原,得到的直接还原铁未能充分渗碳,因而含碳较低(<2%),实际生产中仍需要用电炉精炼成钢。
电炉精炼的主要任务是熔化脱除杂质和调整钢成分•熔融还原法是指一切不用高炉冶炼液态生铁的方法。
它是不用焦炭在一个容器中完成高炉炼铁过程的,基本上不改变目前传统钢铁生产的基本原理。
•非高炉炼铁法发展较快的原因:1 不用焦炭炼铁。
高炉冶炼需要高质量冶金焦,而焦煤从世界储量而言,只占煤总储量的5%,而且日渐短缺,价格越来越高。
非高炉炼铁可以使用非炼焦煤和其它能源作燃料与还原剂。
近几十年来,大量开发了天然气、石油、电和原子能等新能源,为高炉炼铁发展提供了条件。
•2 随着钢铁工业的发展,氧气转炉和电炉炼钢完全取代平炉,废钢消耗量迅速增加,废钢供应量日感紧张,非高炉生产的海绵铁、粒铁等是废钢的极好代用品。
•3 省去了炼焦设备,总的基建费用比高炉炼铁法少。
虽然非高炉炼铁法的生产效率远赶不上高炉,但对缺乏焦煤资源的国家和地区,用于中小型企业生产,前途是光明的。
中国的非高炉炼铁宝钢罗泾熔融还原COREX-30002 COREX炼铁技术概况•熔融还原炼铁技术是近代钢铁工业的前沿技术, 它是以富铁矿或球团矿与煤燃烧后还原成铁水的工艺,俗称无焦炼铁,包括COREX 、DIOS、HIsmelt 和Romelt 等工艺技术。
•COREX法自1989年底正式投产以来,经过15年的工业生产,已积累了大量生产经验,技术成熟,目前COREX 法的总生产能力已超过500 万吨,约占世界生铁产量的1 %,是唯一已用于工业化生产的熔融还原炼铁技术。
COREX炼铁技术概况•COREX 法的主要优点是投资和生产成本低,开停炉容易,特别适合与电炉或转炉短流程钢厂配套。
高炉炼铁工艺流程与主要设备概述
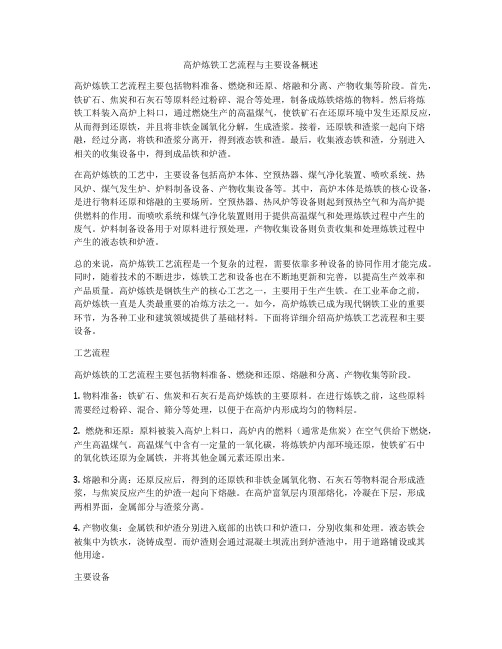
高炉炼铁工艺流程与主要设备概述高炉炼铁工艺流程主要包括物料准备、燃烧和还原、熔融和分离、产物收集等阶段。
首先,铁矿石、焦炭和石灰石等原料经过粉碎、混合等处理,制备成炼铁熔炼的物料。
然后将炼铁工料装入高炉上料口,通过燃烧生产的高温煤气,使铁矿石在还原环境中发生还原反应,从而得到还原铁,并且将非铁金属氧化分解,生成渣浆。
接着,还原铁和渣浆一起向下熔融,经过分离,将铁和渣浆分离开,得到液态铁和渣。
最后,收集液态铁和渣,分别进入相关的收集设备中,得到成品铁和炉渣。
在高炉炼铁的工艺中,主要设备包括高炉本体、空预热器、煤气净化装置、喷吹系统、热风炉、煤气发生炉、炉料制备设备、产物收集设备等。
其中,高炉本体是炼铁的核心设备,是进行物料还原和熔融的主要场所。
空预热器、热风炉等设备则起到预热空气和为高炉提供燃料的作用。
而喷吹系统和煤气净化装置则用于提供高温煤气和处理炼铁过程中产生的废气。
炉料制备设备用于对原料进行预处理,产物收集设备则负责收集和处理炼铁过程中产生的液态铁和炉渣。
总的来说,高炉炼铁工艺流程是一个复杂的过程,需要依靠多种设备的协同作用才能完成。
同时,随着技术的不断进步,炼铁工艺和设备也在不断地更新和完善,以提高生产效率和产品质量。
高炉炼铁是钢铁生产的核心工艺之一,主要用于生产生铁。
在工业革命之前,高炉炼铁一直是人类最重要的冶炼方法之一。
如今,高炉炼铁已成为现代钢铁工业的重要环节,为各种工业和建筑领域提供了基础材料。
下面将详细介绍高炉炼铁工艺流程和主要设备。
工艺流程高炉炼铁的工艺流程主要包括物料准备、燃烧和还原、熔融和分离、产物收集等阶段。
1. 物料准备:铁矿石、焦炭和石灰石是高炉炼铁的主要原料。
在进行炼铁之前,这些原料需要经过粉碎、混合、筛分等处理,以便于在高炉内形成均匀的物料层。
2. 燃烧和还原:原料被装入高炉上料口,高炉内的燃料(通常是焦炭)在空气供给下燃烧,产生高温煤气。
高温煤气中含有一定量的一氧化碳,将炼铁炉内部环境还原,使铁矿石中的氧化铁还原为金属铁,并将其他金属元素还原出来。
- 1、下载文档前请自行甄别文档内容的完整性,平台不提供额外的编辑、内容补充、找答案等附加服务。
- 2、"仅部分预览"的文档,不可在线预览部分如存在完整性等问题,可反馈申请退款(可完整预览的文档不适用该条件!)。
- 3、如文档侵犯您的权益,请联系客服反馈,我们会尽快为您处理(人工客服工作时间:9:00-18:30)。
(4)
计算umf时应使用颗粒的平均直径,u0不能太靠近umf; 而计算ut时则应使用小粒度组分直径,uo同样不能太 靠近ut。 令Du=ut-umf,则Du越大,流化床越稳定。 u0的选择必须保证流化床下部uo>umf,上部u0 <ut。
床层内压力分布与高度大致成直线关系: 在恒温床层内有: 床层极限高度Lmax时,ui=umf,上部u0 =ut,可得:
干基热量为Qd; Q包括造气热(Qg,干基造气热Qgd)和熔炼煤的有效热值(Qe,干基有
效热值Qed); ➢ 造气热Qg :包括煤气物理热、挥发物分解热、溶剂分解热等与熔炼无关
的热消耗,以煤气物理热为主; ➢ 有效热值:真正用于熔炼的热量
熔炼煤主要性质
熔炼煤的干基有效热值可由下式估算:
有效热值(Qe)的影响因素: ➢ 湿度:影响较大。
➢ 煤气出炉温度Tg。
3.4.2 矿石熔炼热
铁矿石化学成分
铁矿石热收入包括铁矿石(海绵铁)物理热和成渣 热;
熔炼热支出包括:冷却热损失、SiO2分解热、FeO 分解热、脱硫热、溶剂分解热、铁水物理热、矿渣 物理热、渗碳热等。
一般矿石的熔炼热(Qs)可由下式估算:
3.4.3 煤耗与产气量
umf的二次方程: 如Rep很低,压降以粘度损失为主,忽略动能损失,
有: 很高,压降以动能损失为主可忽略粘度损失,有:
对很多系统有: 则有:
由上三式可求出临界流化速度,标准误差为±35%。
其中:(2)适用于小Re,即小粒度炉料; (3)适用于大Re,即大粒度炉料; (1)适用Re适中。
终端速度ut有: 式中:Cd为曳力系数,其有:
度。
(4)还原率或金属化率。粘结失流的前提是Rm>0及还原行气氛, 粘结失流总是在粘结失流还原率Rs附近发生。
(5)还原剂种类和铁的析出形态。H2还原时,铁以多孔的或致密 的平面状析出,CO还原时,铁则多以针状析出。
(6)矿粉粒度。大颗粒矿粉可在一定程度上抑制粘结失流现象。
➢ Ts=830℃ ➢ 失流以前矿石还原率f在Ts处不连续。
粘结失流的影响因素 颗粒的粘结失流趋势:
式中:St是粘结失流趋势;Ak是发生碰撞时的颗粒接 触面积;Sp是颗粒表面粘度或活性;mp是颗粒动量。
间接影响因素较多:
(1)还原温度。当还原温度高于粘结失流温度Ts时,粘结失流则 会有规律的发生。
(2)气氛。粘结失流现象仅发生于还原气氛中。 (3)气流流速。较高的流速下, Ts较高,则可使用较高的还原温
(4)使用粘结趋势较低的矿石。
(5)使用高速流化床。高速流下带出的矿粉返回使用,即采用循环流化 床。
3.3.4 还原速度与气体利用率
流化床的反应条件:
(1)矿粉成分接近全混合床。床层上下还原率分布较均 匀,尾气还原需最低与FeO和Fe平衡,还原气利用率 低于竖炉。
(2)气流接近活塞流。温度分布下高上低,总温差较小。 (3)总压降约等于单位截面积上的矿粉质量,压力分布
应的Rm即为Rm0,C记为C0,统称理论最佳配合参数,其由熔炼 煤有效热值和矿石熔炼热决定。
3.4.5 原燃料及配合参数对煤耗的影响
矿石成分。矿石成分→矿石熔炼热→配合参数(Rm0) →煤耗。
式中:Q0——矿石预还原金属化率=0时的熔炼热, 对Q0影响最为显著的参数是TFe、SiO2和CaO。
➢ Rm0随Q0的提高而提高; ➢ 当Q0很低时,Rm0也很低。虽然对应煤耗较低,但过
铁矿石还原用气固两相流。实际中炉料粒度不均匀,所以工业流化床一般不 能以单纯的形式存在。
3.2.2 流化参数
临界流化条件:气流对料层向上的摩擦力等于料层的 质量。由此可得:
整理得:
式中: S——流化床截面积;Lmf——临界流化床高度; εmf——临界流化床孔隙率;ρs——固体颗粒密度。 固定床压将为:
用液体流化介质形成的流化床较为均匀,称为均匀流化床。
(4)鼓泡流化床。使用气体流化介质形成的流化床均匀性、稳定性较均匀床低, 料层中可观察到明显的鼓泡现象和沟流现象,颗粒运动比均匀床活跃,床层 的膨胀率不如均匀床,称为鼓泡流化床或聚式流化床,简称鼓泡床。
(5)腾涌床。如果流化床截面积较小,气泡直径能够长大到流化床直径以上, 床层将被气泡截断,形成腾涌现象。
煤气的改质或重整:将高温煤气通入煤炭床(如 资源条件允许,天然气或其他碳氢化合物也可以 使用),使其中的氧化性气体得到还原,提高煤 气的还原性气氛,降低煤气温度。
预热空气明显不利于有效热值的提高; 煤气含氮量高,质量变差; 随着助燃空气温度提高,Qe有所改善。
重要冶炼参数与二次燃烧率的关系(氧气助燃)
rpc↑,Qe↑,Tg↑。过高会给炉衬维护带来麻烦,煤气 物理热的利用越来越重要。
煤气物理热的利用方法有:通过换热器预热空气作 二次助燃剂;煤气的改质或重整。
低会造成冶炼困难,一般规定Rm不能低于85%; ➢ 当Q0很高时,Rm0也很高。太高生产无法满足,一般
规定,不能高于96%。
熔炼热对配合参数的影响
熔炼煤湿度。湿度→Qe→煤耗。
3.4 熔炼造气煤炭流化床学习重点
熔炼煤的有效热值及影响因素 理论最佳配合配合点,理论最佳配合参数; 矿石成分、熔炼煤湿度及配合参数对煤耗的
两式合并则有:
3.3 还原流化床学习重点
流化床类型及各类流化床△P与u0的关系,Umf和Ut; 粘结失流:定义、影响因素、粘结失流机制及控制
粘结失流的措施;
3.4 熔炼造气煤炭流化床
3.4.1 熔炼煤的有效热值
热收入——煤的燃烧; CH4和H2O比例很低,可忽略H2的热效应; 煤在熔炼过程中放出的全部热量(Q)为碳素燃烧热和煤灰成渣热之和,
二次燃烧:向气相中通入氧气,烧掉部分煤气,同时 保持生成的CO2和H2不被还原。
二次燃烧率:通过二次燃烧氧化掉的CO和H2的比例, 记为rpc。其对熔炼煤有效热值的影响极大。计算可知, 当rpc =0.3左右时二次燃烧热的水平即可与一次燃烧 相当。
3.5.3 二次燃烧率与有效热值
Qcom ←二次燃烧率 Qe←
(6)稀相流化床。流体流速进一步提高,流体与颗粒间摩擦力大于颗粒质量, 颗粒被流体带走,形成夹带现象。使床层上届面消失,颗粒密度降低,这种 床称为稀相流化床。
床层类型可由△P与u0的关系确定:
(1) △P与u0 呈直线关系,固定床。 (2)u0=umf, △P=W/S,临界流化床。 (3) u0>umf, △P恒定,鼓泡床。 (4)u0↑,△P开始波动,并逐渐减小,腾涌床。 (5)u0>ut,△P较小。稀相流化床。
近似直线。
(4)炉料粒度小,扩散条件好。 (5)影响气体利用率因素复杂,主要有还原速
度、热量供应、还原剂供应和流速要求等。 (6)流化床形式有重要影响。主要形式有单级
流化床、多级流化床、鼓泡床和循环流化床。
气体利用率
还原剂扩散量在流化床高度上的分布(即为还原反应 速度在高度上的分布):
单位时间还原剂供应量为M0,η为气体利用率,则有:
第三章-非高炉炼铁重点设备 介绍(下)..
3.3 还原流化床
3.2.1 流态化现象及流化床类型
(1)固定床。流体流速较低,床层颗粒静止,孔隙率不变。 (2)临界流化床。流体流速达临界值umf,流体与颗粒间的摩擦力等于颗粒质
量,此时为固定床与流化床的分界点。 (3)均匀流化床。流速↑,孔隙率↑,高度↑,实际流速恒定,称为流化床。使
0点左边,Mr>Mr‘,金属化率偏低,还原气供过于求。煤耗由Mr 决定,有副产品过剩煤气产出;
0点右边,Mr<Mr‘,金属化率偏高,还原气供应不足;解决办法: ➢ 循环使用煤气。还原尾气清洗,脱除氧化性成分,加压,预热,
返回使用;
➢ 按Mr’确定煤耗。热收入过剩,Tg提高。 0点,Mr=Mr‘,系统最简单,此点称为理论最佳配合点。 0点对
Tg ←二次燃烧热效率ηq和煤气水当量 燃烧热Qcom与二次燃烧率rpc近似成直线关系。
rpc越大, Qe越高。但为了避免金属铁或低价氧化铁 的氧化,不能无限提高。 二次助燃剂可选用氧气、空气和预热空气。使用氧气 时煤气水当量最低,煤气量最低,在同样冶炼强度下 煤气与熔池间热交换时间最长,热效率最高。
➢ 产品类似高炉生铁。
➢ 连续运行。
卧式铁浴炉主要特点是煤气与熔池的接触面积较大, 且在炉内有一个与熔池平行的流动过程,强化了气 液两相之间的热交换。
铁浴炉中的过程主要有三个:继续完成还原单元未完 成的还原过程、将还原出的铁熔炼成生铁和制取还原 气(煤的气化)。
还原反应: 气化反应产物没有二次燃烧的主要产物CO2 和H2O。 熔炼所需热量由碳的燃烧反应提供:
熔炼煤耗随入炉海绵铁金属化率的提高直线下降, 其关系有:
产气量与煤耗的关系近似正比; 总气量Mg有: 还原剂(CO+H2O)气量Mr有:
3.3.4 与还原单元的配合
熔炼单元与还原单元通过还原气和海绵铁的联系称为一 个整体;
还原单元的还原剂需要量由海绵铁金属化率和气体利用 率决定;
海绵铁金属化率同时影响产气量(煤耗)和需气量; 产气量(Mr)随Rm提高而降低; 需气量(Mr‘)随Rm提高而升高。
式中:pu= umf/ut。 可见,pu越高, Lmax则越大。
Lmax还与流体压力有关。当气体出口式得:
则在 当
时, Lmax随pu提高而提高; 时, Lmax与pu无关,其应写为:
Du和Pu是粒度的函数。
➢粒度较小(0.1mm)时, pu较大,ut和umf相对差别很 大,u0的控制和床层的提高 较容易。利于提高产率和还 原气体利用率。但粒度太低, 易粘结失流。
或:
3.5.2 影响熔炼煤有效热值的参数
对于铁浴炉有:
由上式可见,影响Qe的主要因素是煤气温度和熔炼 煤湿度。 铁浴炉煤气出口温度与离开燃烧区时的温度差别不大 较煤炭流化床高。主要是由于熔池上方不存在含碳料 层,不能有效形成垂直方向的温度梯度。 铁浴炉单位煤耗较高。主要是由于熔炼煤在铁浴炉中 的有效热值过低,可通过提高燃烧热来改善。