第三章高炉本体设计3
第3章高炉本体设计

炉腹高度由下式计算 :
h2
D 2
d
• tg
炉腹角一般为79º~83º,过大不利于煤气
分布并破坏稳定的渣皮保护层,过小则增
大对炉料下降的阻力,不利于高炉顺行。
4. 炉身: 炉身呈正截圆锥形。
作用:
(1)适应炉料受热后体积的膨胀,有利于 减小炉料下降的摩擦阻力,避免形成料拱。
(2)适应煤气流冷却后体积的收缩,保证 一定的煤气流速。
D——炉腰直径;
d1——炉喉直径; α——炉腹角;
β——炉身角;
hf hz
d1
β D
α 风口中心线
渣口中心线 d
铁口中心线
图3-1 五段式高炉内型图
h0 h1 h2 h3
h4
h5
Hu
1. 高炉有效容积和有效高度
1)有效高度:
高炉大钟下降位置的下缘到铁口 中心线间的距离称为高炉有效高度 (Hu),对于无钟炉顶为旋转溜槽最 低位置的下缘到铁口中心线之间的距 离。
铁口中心线到炉底砌砖表面之间的 距离称为死铁层厚度。
作用:
(1)残留的铁水可隔绝铁水和煤气对炉底 的冲刷侵蚀,保护炉底; (2)热容量可使炉底温度均匀稳定,消除 热应力的影响; (3)稳定渣铁温度。
死铁层厚度: 新设计高炉的死铁层厚度h0=0.2d。
3.1.3 炉型设计与计算
名词概念:
(1)设计炉型:按照设计尺寸砌筑的炉型; (2)操作炉型:指高炉投产后,工作一段时 间,炉衬被侵蚀,高炉内型发生变化后的炉型;
Vu'
P
V
4035 2018(m3 ) 2.0
(3)炉缸尺寸: ①炉缸直径:
选定冶炼强度:
I
0.9 5
高炉本体及附属设备
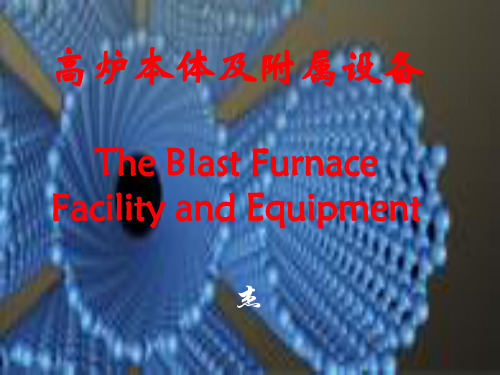
高炉金属结构:
高炉本体的外部结构;
炉壳:
①承受载荷; ②固定冷却设备; ③保证砌体牢固; ④防止煤气逸出; ⑤便于喷水冷却;
高炉结构形式:
高炉本体钢结构
a-炉缸支柱式;b-炉缸、炉身支柱式;c-炉体框架式;d-自立式
一.炉缸支柱式
——曾用于中小型高炉
1. 特点: 炉顶荷载及炉身荷载由炉身外壳通过炉缸支
优点:
➢取消了笨重的大小料钟,而且布料上有很大的 灵活性;
缺点:
➢控制和传动系统较复杂,要求有较高的监测和 自动化水平;
➢对原燃料的粒度上限要求严格,否则容易卡料;
2、高炉附属系统
➢原料供应系统; ➢送风系统; ➢煤气净化除尘系统; ➢渣铁处理系统; ➢高炉喷吹设备;
原料供应系统
是指原料运入高炉车间到装入高炉的一系列 过程,由两部分组成.
(2)无钟炉顶:
随着高炉炉容增大,大钟体积越来越庞大,重量也相 应增大,难以制造、运输、安装和维修,寿命短,而且 大钟直径越大,径向布料越不均匀;
卢森堡保尔乌斯公司在1970年提出的无钟炉顶, 称为PW型炉顶.这种炉顶完全取消了大小料钟,采 用一个旋转溜槽代替大料钟,溜槽可以绕高炉中心 线旋转,也可以在径向上摆动.溜槽正上方有一个控 制溜槽旋转与摆动的气密齿轮箱.溜槽上面有个料 仓,轮换装料与卸料,每个料仓的上下各有一个密 封阀.当料仓的上密封阀开启、下密封闭关闭时, 处在装料状态,反之则为卸料.
炉顶装料装置:
炉顶是炉料的入口也是煤气的出口,又是 高炉的咽喉.炉顶装料设备是把运送到炉 顶的炉料装入炉内,并能得到合理的分布. 现代高炉随着高压操作的广泛应用,炉顶 设备已成为高炉设备中的薄弱环节,其寿 命、结构和制造质量等不但影响高炉的作 业率,也影响高压作业和布料调剂,还决定 着高炉中修甚至大修的期限.
高炉本体设计
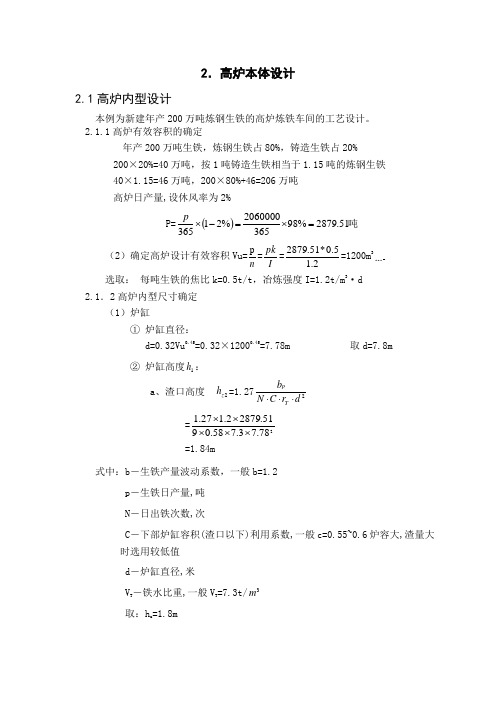
2.高炉本体设计2.1高炉内型设计本例为新建年产200万吨炼钢生铁的高炉炼铁车间的工艺设计。
2.1.1高炉有效容积的确定年产200万吨生铁,炼钢生铁占80%,铸造生铁占20% 200×20%=40万吨,按1吨铸造生铁相当于1.15吨的炼钢生铁 40×1.15=46万吨,200×80%+46=206万吨高炉日产量,设休风率为2% P=()吨51.2879%983652060000%21365=⨯=-⨯p (2)确定高炉设计有效容积Vu=n p =I pk =2.15.0*51.2879=1200m 3选取: 每吨生铁的焦比k=0.5t/t ,冶炼强度I=1.2t/m 3·d2.1.2高炉内型尺寸确定(1)炉缸① 炉缸直径:d=0.32Vu 0.45=0.32×12000.45=7.78m 取d=7.8m ② 炉缸高度1h :a 、渣口高度 2z h =1.272d r C N b T p ⋅⋅⋅ =278.73.758.0951.28792.127.1⨯⨯⨯⨯⨯ =1.84m式中:b -生铁产量波动系数,一般b=1.2p -生铁日产量,吨N -日出铁次数,次C -下部炉缸容积(渣口以下)利用系数,一般c=0.55~0.6炉容大,渣量大时选用较低值d -炉缸直径,米V T -铁水比重,一般V T =7.3t/3m取:h z =1.8mb.风口高度: f h = k hz =1.8/0.55=3.27mK-渣口高度与风口高度之比取h z =3.3m风口数n=2(d+1)=2(7.8+1)=17.6取n=18取风口结构尺寸f==0.37mc.炉缸高度1h =f h +f=3.3+0.37=3.67m 取 3.7m③死铁层高度h 0=0.2*炉喉高度=0.2*h 5=0.2*2.7=0.54m(2)炉腰取 D/d=1.15则 D=1.15×7.8=8.95m取D=8.9m(3)炉腹取'3079︒=α h 2=tan *2d D -α=28.79.8-*tan 3079︒=2.96 取2h =3校核α αd D h -2278.76.932-⨯'2879︒=α(4)炉喉①炉喉直径取d 1/D=0.73d 1=0.73D=0.73*8.9=6.49m取d 1=6.5m②炉喉高度取h 5=2.7m(5)炉身、炉腰高度①炉身角β取β=84.5°②炉身高度h 4h 4=21(D-d 1)tan β=21 *(8.9-6.5)tan84.5°=12.46m 取12.5 校核β tan β=6.6946.12*2-=10.38 β=84.5°炉腰高度h 3H u =2.7*D=3.0*8.9=24.6mh 3 =H u -h 1-h 2-h 4-h 5=24.6-3.7-3-12.5-3=2.4m(6)校核炉容炉缸容积: 1V =41πd 21h =41×3.14×28.7×3.7 =176.73m炉顶容积:2V =( d 2+2D +Dd)122h π =(8.92+8.9*7.8+28.7)123⨯π=164.433m 炉腰容积:3V =41π3D 3h =41×3.14×29.8 *2.4 =149.233m炉身容积:4V =(1212Dd d D ++)124h π =(8.92+ 6.52+ 8.9×6.5) 125.12⨯π =586.493m炉喉容积:5V =41π21d 5h =41×3.14×6.52×3 =99.493mV u =1V +2V +3V +4V +5V =1176.34m3相对误差为:|34.117634 .11761200 |×100%=2%约为2%,设计较为合理.。
《高炉本体设计》课件

高炉本体设计流程
1
高炉结构分析
2
通过结构分析,评估高炉本体的承载能
力和稳定性,并确定设计参数。
3
结构优化和方案选择
4
进一步优化高炉本体设计,选择最合适 的方案以实现高炉的高效运行。
设计流程概述
设计高炉本体的流程包括需求分析、结 构分析、设计和方案选择等多个阶段。
高炉本体结构设计
根据结构分析的结果,设计高炉本体的 具体细节和构造方式。
关键技术及应用
壳体结构材料选择
钢铁高炉壳体由特殊耐火材料构 成,能够抵御高温和化学腐蚀。
高炉内部构件设计
高炉内部构件的设计需要考虑耐 磨、耐高温和保护钢铁质量等因 素。
高炉维护与检修
高炉维护和检修是确保高炉长期 稳定运行的关键,需要定期进行。
总结
1 设计的重要性
高炉本体设计对于钢铁生产具有重要意义, 直接关系到工艺效率和产品质量。
பைடு நூலகம்
2 总结与展望
本课件详细介绍了高炉本体设计的内容和流 程,并展望了未来的发展方向。
参考文献
1. 钢铁行业标准化委员会. 高炉本体设计技术规范[M]. 北京:中国标准出版社, 2018。
2. Smith, John. Blast Furnace Design: Principles and Practice[M]. London: Steel Publishing, 2019.
高炉本体设计案例分享
1 国内案例
中国在高炉本体设计领域取得了丰硕成果,例如某钢铁集团的高炉本体设计。
2 国外案例
国外也有很多优秀的高炉本体设计案例,比如日本的某钢铁公司的高炉。
高炉本体设计高炉冷却设备

,a click to unlimited possibilities
高炉本体设计及高炉冷却设备
CONTENTS
目录
输入目录文本
高炉本体设计
设计优化建议
未来发展趋势
高炉冷却设备
添加章节标题
高炉本体设计
结构特点
炉壳:高炉炉壳由钢板焊接而成,分为炉喉、炉身和炉腰三个部分。
炉衬:高炉炉衬由耐火材料砌筑而成,分为工作层、永久层和填充层。
冷却设备:高炉冷却设备包括冷却壁、风冷管和汽化冷却器等,用于控制炉衬温度和保护炉壳。
风口装置:高炉风口装置包括风口小套、大套和十字测温装置等,用于向炉内鼓入空气和测量炉温。
材质选择
耐火材料:高炉炉衬的主要材料,要求具有高温强度、耐腐蚀性和良好的热稳定性
碳化硅砖:具有高导热率和高电子饱和迁移率,是高炉出铁口用砖的理想材料
新型冷却材料类型:陶瓷、金属基复合材料等
绿色环保理念融入设计
减少能源消耗:采用高效节能技术,降低高炉本体及冷却设备的能源消耗。
降低污染物排放:优化燃烧过程,减少废气、废渣等污染物的排放,提高环保性能。
循环利用资源:对高炉本体及冷却设备产生的废弃物进行回收利用,实现资源循环利用。
智能化控制:采用先进的智能化控制技术,提高设备的运行效率,减少人工干预,降低对环境的影响。
定期对高炉本体和冷却设备进行检查和维修
未来发展趋势
智能化控制技术应用
智能化控制技术概述
高炉冷却设备中的智能化控制技术应用
未来发展趋势及展望
高炉本体设计中的智能化控制技术应用
新型冷却材料研发
研发背景:高炉冷却设备在钢铁生产中的重要性
新型冷却材料特点:高效、耐高温、耐腐蚀等
第三章 高炉炼铁

的碳化硅砖或高导热的炭砖为主,高
炉下部以高导热的石墨质炭砖为主,
图 5.7 炉缸、炉底砌筑结构
6
图 3.7 为炉缸、炉底砌筑结构示意图。 3)冷却设备
冷却设备的作用是降低炉衬温度,提高炉衬材料抗机械、化学和热产生的侵蚀能力, 使炉衬材料处于良好的服役状态。高炉使用的冷却设备主要有冷却壁、冷却板和风口。冷却 壁紧贴着炉衬布置,冷却面积大;而冷却板水平插入炉衬中,对炉衬的冷却深度大,并对炉 衬有一定的支托作用。
(3)鼓风:空气通过高炉鼓风机加压后成为高压空气(鼓风),经过热风炉换热,将温 度提高到 1100~1300℃,再从高炉风口进入炉缸,与焦炭和煤粉燃烧产生热量和煤气。鼓风 带入高炉的物理热占高炉热量总收入的 20%左右。在鼓风中加入氧气可提高鼓风中的氧含 量(称为富氧鼓风)。采用富氧鼓风可提高风口燃烧温度,有利于高炉提高喷煤量和高炉利
4000m3 级高炉日产生铁量达到 10000 t 以
上。
hf
d1
β D
α
风口 中心线
d
铁口 中心线
h1
h2
h3
h4
h5
h6
炉 喉
炉 身
炉 腰 炉 腹 炉 缸 死铁层
Hu H
h0
3.2.3 高炉生产主要技术经济指标
图 5.3 高炉内型
(1)有效容积利用系数(ηu ):每 m3 高炉有效容积每天生产的铁水量( t / m3 ⋅ d ),
KΣ
=
每天装入高炉的焦炭量+ 每天喷入高炉的煤粉量×置换比 高炉每天出铁量
(3.4)
煤粉置换比通常小于 1.0,一般在 0.75~0.90 之间。
(6)冶炼强度( I ):每 m3 高炉有效容积每天消耗的(干)焦炭量( t / m3 ⋅ d )。
3 高炉本体

3、高炉本体高炉本体包括高炉基础、钢结构、炉村、冷却装置,以及高炉炉型设)表示;高炉有效容积和座数计计算等。
高炉的大小以高炉有效容积(V有表明高炉车间的规模,高炉有效容积和炉型是高炉本体设计的基础。
近代高炉有效容积向大型化发展。
目前,世界大型高炉有效容积已达到5000m3/D值已近2.0左右。
级,而炉型设计则向着大型横向发展,H有高炉本体结构的设计以及是否先进合理是实现优质、低耗、高产、长寿的先决条件,也是高炉辅助系统装置的设计和选型的依据。
高炉炉衬用耐火材料,已由单一的陶瓷质耐火材料,普遍地过渡到陶瓷质和碳质耐火材料综合结构,也有采用高纯度Al2O3的刚玉砖和碳化硅砖;高炉冷却设备器件结构亦在不断改进,软水冷却、纯水冷却在逐渐扩大其使用范围。
由于炉体综合设计水平的提高,强化高炉炉龄已可望达到十年或更长。
高炉本体结构及其设计是高炉车间设计首先要解决的关键所在,必须慎重对待。
3.1高炉炉型高炉是竖炉。
高炉内部工作空间剖面的形状称为高炉炉型或称高炉内型。
高炉问世二百多年来,随着人们对产量的要求和原料燃料条件的改善,以及鼓风能力的提高,高炉炉型也在不断地演变和发展;高炉冶炼的实质是上升的煤气流和下降炉料之间所进行的传热传质过程,因此必须提供燃料燃烧所必须的空间,提供高温煤气流与炉料进行传热传质的空间。
炉型要适应原料燃料条件,保证冶炼过程的顺行。
3.1.1炉型的发展过程图3-l所示原始形高炉炉型,由于当时工业不发达,高炉冶炼以人力、蓄力、风力、水力鼓风,鼓风能力很弱,为了保证整个炉缸载面获得高温,炉缸直径很小;冶炼以木炭或无烟煤为燃料,机械强度很低,为了避免在高炉下部压碎而影响料柱透气性,故原始高炉高度很小;为了人力装料方便并能够将炉料装到炉喉中心,炉喉直径也很小,而大的炉腰直径减小了烟气外流速度,延长了烟气在炉内停留时间,起到切住炉内热量的作用。
因此,炉缸和炉喉直径小,炉身下部炉腹直径大,高度小等等,是各国原始高炉炉型的共同特点。
高炉本体.
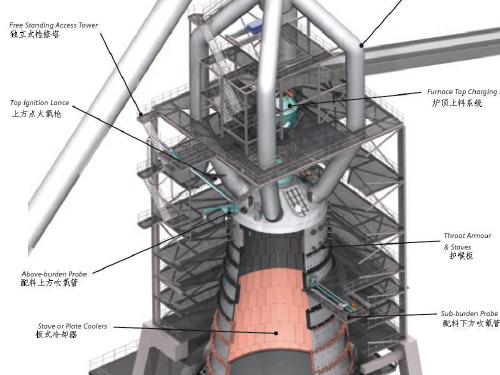
炉身角:
一般取值为81.5º~85.5º之间。大高 炉取小值,中小型高炉取大值。 4000~5000m3高炉β角取值为81.5º左右, 前苏联5580m3高炉β角取值 7942'17' '
炉身高度 :
h4
d 0.23 I •Vu i燃
式中: I——冶炼強度, t/m3·d
i 燃——燃烧強度,t/m2·h
Vu——高炉有效容积,m3 d——高炉炉缸直径,m
计算得到的炉缸直径再用Vu/A进 行校核,不同炉容的Vu/A取值为:
大型高炉:22~28 中型高炉:15~22 小型高炉:11~15
(2)渣口高度: 渣口中心线与铁口中心线间距离。
高炉炉型
概念:高炉内部工作空间剖面的形
状称为高炉炉型或高炉内型。
❖横断面为圆形的炼铁竖炉。用钢板作炉壳, 壳内砌耐火砖内衬。高炉本体自上而下分为 炉喉、炉身、炉腰、炉腹 、炉缸5部分。由 于高炉炼铁技 术经济指标良好,工艺 简单 , 生产量大,劳动生产效率高,能耗低等优点, 故这种方法生产的铁占世界铁总产量的绝大 部分。
大型:2.8~3.6m;小型:1.5~2.5m
作用:
(1)炉腹的形状适应了炉料熔化滴落后体积 的收缩,稳定下料速度。
(2)可使高温煤气流离开炉墙,既不烧坏炉 墙又有利于渣皮的稳定。
(3)燃烧带产生大量高温煤气,气体体积激 烈膨胀,炉腹的存在适应这一变化。
炉腹的结构尺寸是炉腹高度和炉腹角。
炉腹高度由下式计算 :
风口数目也可以根据风口中心线在炉缸圆周上的距离 进行计算:
n d
s
S 取值在1.1~1.6m之间, 风口数目一般为支柱数目的整数倍取偶数。
- 1、下载文档前请自行甄别文档内容的完整性,平台不提供额外的编辑、内容补充、找答案等附加服务。
- 2、"仅部分预览"的文档,不可在线预览部分如存在完整性等问题,可反馈申请退款(可完整预览的文档不适用该条件!)。
- 3、如文档侵犯您的权益,请联系客服反馈,我们会尽快为您处理(人工客服工作时间:9:00-18:30)。
5.
负荷称为冷却强度。
第三章高炉本体设计3
•热负荷:
•式中: Q ——热负荷,kJ/h;
•
M——冷却水消耗量,t/h;
•
c——水的比热容,kJ/(kg•℃);
•
t——冷却水出水温度,℃;
•
t0——冷却水进水温度,℃。
第三章高炉本体设计3
• 通过提高冷却水温度差,可以 降低冷却水消耗量。 •提高冷却水温度差的方法: •①降低流速; •②增加冷却设备串联个数。
六. 炉身冷却模块技术
•1. 结构: • 炉身冷却模块是指将厚壁(14~16mm) 把手型无缝钢管作为冷却元件直接焊接在炉 壳上,在炉壳及钢管间浇注耐热混凝土,混 凝土层高出水管110~130mm,构成大型预 制冷却模块。
• 简单地说就是由炉壳——厚壁钢管— —耐热混凝土构成的大型冷却模块组成。
• 唐钢炉身冷却模块结构示意图:
第三章高炉本体设计3
3.3.6 高炉冷却系统
•高炉冷却系统方式: • 汽化冷却 • 开式工业水循环冷却系统 • 软(纯)水密闭循环冷却系统
第三章高炉本体设计3
•一. 高炉汽化冷却 •1. 概念: • 高炉汽化冷却是把接近饱和温度的 软化水送入冷却设备内,热水在冷却设 备中吸热汽化并排出,从而达到冷却设 备的目的。 • 分为自然循环汽化冷却和强制循环 汽化冷却两种。
第三章高炉本体设计3
•3. 冷却壁的优点: •①冷却壁安装在炉壳内部,密封性好; •②冷却均匀,侵蚀后炉衬内壁光滑。 •4. 缺点: • 消费金属多、笨重、冷却壁损坏后 不能更换。
第三章高炉本体设计3
三. 冷却板(又称扁水箱)
• 冷却板厚度 70~110mm,内部铸有 φ44.5×6mm无缝钢管。 •1. 冷却部位: • 用在炉腰和炉身部位。
•
空气——风冷
•
汽水混合物——汽化冷却
• 2. 对冷却介质的要求:
• (1)有较大的热容量及导热能力;
1. (2)来源广、容易获得、价格低廉;
2. (3)介质本身不会引起冷却设备及
高炉的破坏。
第三章高炉本体设计3
•3. 水的硬度: • 指每m3水中钙、镁离子的摩尔数。
•根据硬度不同,水可分为三类: • 软 水:硬度<3mol/m3 • 硬 水:硬度在3~9mol/m3 • 极硬水:硬度>9mol/m3 •水的软化处理: • 就是将Ca2+、Mg2+ 离子除去,通 常用Na+ 阳离子置换。
第三章高炉本体设计3
•2. 水压和流速 • 确定冷却水压力的重要原则是冷 却水压力大于炉内静压 。 • 降低冷却水流速,可以提高冷却 水温度差,减少冷却水消耗量。但流 速过低会使机械混合物沉淀,而且局 部冷却水可能沸腾。
第三章高炉本体设计3
•3. 冷却水温度差 • 一般要求进水温度低于35℃,不 应超过40℃;出水温度不超过50~ 60℃。 • 实际的进出水温差比允许的进出 水温差适当低些 ,其关系为:
第三章高炉本体设计3
2020/12/8
第三章高炉本体设计3
3.3.1 冷却设备的作用
•(l)保护炉壳。 •(2)对耐火材料的冷却和支承。 •(3)维持合理的操作炉型。 •(4)促成炉衬内表面形成渣皮,代替 炉衬工作,延长炉衬寿命。
第三章高炉本体设计3
3.3.2 冷却介质
1. 冷却介质:
2.
水——水冷
第三章高炉本体设计3
•板壁交错布置结构
第三章高炉本体设计3
五. 新型冷却壁——铜冷却壁 •1. 结构: • 铜冷却壁是在轧制好的壁体上加 工冷却水通道,并且在热面设置耐火砖。 • 铜冷却壁与铸铁冷却壁特性的比 较见表
第三章高炉本体设计3
•2. 铜冷却壁的特点: •(l)铜冷却壁具有导热率高,热损失 低的特点;
第三章高炉本体设计3
冷却水箱 1-支梁式;2-扁水箱(P107)
第三章高炉本体设计3
•2. 安装: •①上下层间距500~900mm,同层间 距150~300mm,呈棋盘式布置,炉腰 部位比炉身部位要密集一些。 •②冷却板前端距炉衬设计工作表面一 砖距离230mm或345mm 。
第三章高炉本体设计3
第三章高炉本体设计3
3.3.4 冷却设备的工作制度
•概念: • 冷却设备的工作制度,即制定和控 制冷却水的流量、流速、水压和进出水 的温度差等。
第三章高炉本体设计3
•一. 水的消耗量
1. 概念:
2. 热负荷:高炉某部位需要由冷却水带 走
3.
的热量称为热负荷。
4. 冷却强度:单位表面积炉衬或炉壳的 热
第三章高炉本体设计3
3.3.3 高炉冷却结构形式
• 两种: • ★外部冷却:向炉壳外部喷水冷却。 • ★内部冷却:将冷却介质通入冷却
设备内部进行冷却。包括冷却壁、 冷却板、板壁结合冷却结构、炉身 冷却模块及炉底冷却等。
第三章高炉本体设计3
一. 外部喷水冷却
• 适用于小型高炉,对于大型高炉, 在炉龄晚期冷却设备烧坏的情况下使用。 • 炉身和炉腹部位装设有环形冷却水 管,距炉壳约100mm,水管上朝炉壳的 斜上方钻有若干φ5~φ8mm小孔,小孔 间距100mm。
第三章高炉本体设计3
•2.自然循环汽化冷却
•(1)工作原理:
• 汽包中的水沿下降管向下流动,经 冷却设备汽化后,汽水混合物沿上升管 向上流动,进入汽包后经水、汽分离, 蒸汽排出做为二次能源利用,并由供水 管补充一定量的新水保证循环的进行。
• 示意图:
第三章高炉本体设计3
• 自然循环汽化冷却示意图 •1-汽包;2-下降管;3-上升管;4-冷却设第三备章高;炉5本-体设供计水3 管
第三章高炉本体设计3
•2516m3高炉水冷炉底结第构三章图高炉本体设计3
• 大型高压高炉多采用炉底封板, 水冷管的位置有两种: •①水冷管设置在封板以上:在炉壳上 开孔将降低炉壳强度和密封性,但冷却 效果好;
•②水冷管设置在封板以下:对炉壳没 有损伤,但冷却效果差。
•宝钢1号高炉采用后一种结构。
•式中: •为后备系数
第三章高炉本体设计3
•高炉不同部位后备系数:
•炉腹、炉身 风口带
•0.4~0.6
0.15~0.3
渣口以下 风口小套 0.08~0.15 0.3~0.4
第三章高炉本体设计3
•4. 冷却设备的清洗 •一般要3个月清洗一次,清洗方法有: •①用20~25%的70~80℃盐酸,加入缓蚀 剂——1%废机油,用耐酸泵送入冷却设 备中,循环清洗10~15分钟,然后再用压 缩空气顶回酸液,再通冷却水冲洗。 •②用0.7~1.0MPa的高压水或蒸气冲洗。
• 循环的动力是靠下降管中的水和上 升管中汽水混合物的重度差所形成的压头, 克服管道系统阻力而流动。
•压头表示为:
•式中:
• △P ——自然循环流动压头,Pa;
• h ——汽包与冷却设备高度差,m;
•
rW——下降管中水的密度,kg/m3;
•
rV——上升管中汽水混合物的密度,kg/m3。
第三章高炉本体设计3
•3. 六室双通道结构铜冷却板 : •(1)结构: • 采用隔板将冷却板腔体分隔成六 个室,即把冷却板断面分成六个流体 区域,并采用两个进、出水通道进行 冷却。 • 示意图:
第三章高炉本体设计3
• 冷却板
第三章高炉本体设计3
•(2)特点: •①适用于高炉高热负荷区的冷却,可以 采用密集式的布置形式。 •②冷却板前端冷却强度大,不易产生局 部沸腾现象; •③当冷却板前端损坏后可继续维持生产; •④双通道的冷却水量可根据高炉生产状 况分别进行调整。
第三章高炉本体设计3
•二. 排水系统 •排水管直径为供水管直径的1.3~2.0倍。 • 供水管直径通过计算确定,供水 管内水流速为0.7~1.0m/s。
第三章高炉本体设计3
高炉给排水系统(P111) 1-滤水器;2-给水主管;3-给水围管;4-环形排水槽;5-配水器;
6-排水箱;7-排水管;8-炉身喷水管;9-炉腹喷水管
•3. 强制循环汽化冷却 • 是在自然循环汽化冷却的下降 管路上装一水泵,作为循环的动力, 推动循环过程的进行,此时汽包装置 的高度可灵活一些。
第三章高炉本体设计3
•4. 汽化冷却的优点: •(1)冷却强度大,节水、节电; •(2)防止冷却设备结垢,延长寿命; •(3)产生大量蒸气,可作为二次能源; •(4)有利于安全生产。
第三章高炉本体设计3
二. 冷却壁
• 冷却壁设置于炉壳与炉衬之间, 有光面冷却壁和镶砖冷却壁两种 。 • 基本结构图:
第三章高炉本体设计3
•冷却壁基本结构 •a-渣铁口区光面冷却壁;b-镶砖冷却壁;c-上部带凸台镶砖冷却壁;d-中间带凸台镶砖冷却壁
第三章高炉本体设计3
•1. 光面冷却壁 •(1)结构: • 在铸铁板内铸有无缝钢管。无缝钢 管为φ34×5mm或φ44.5×6mm,中心距 为100~200mm的蛇形管。 •(2)应用部位: • 炉缸和炉底部位冷却。
•(2)安装:镶砖冷却壁紧靠炉衬。 •(3)结构型式: • 普通型、上部带凸台型和中间带 凸台型。
•(4)凸台冷却壁的优点:
•①凸台部分除起冷却作用外,还起到 支撑上部砌砖的作用 ;
•②延长炉衬寿命。中间带凸台的冷却 壁更优越。
第三章高炉本体设计3
•(5)新日铁第三代和第四代冷却壁: • 结构见图
第三章高炉本体设计3
3.3.5 高炉给排水系统
•一. 对供水系统的要求:
•①水泵站供电系统须有两路电源,并且两路电 源应来自不同的供电点。
•②应设有水塔,塔内要储有30min的用水量。 •③泵房内应有足够的备用泵。 •④由泵房向高炉供水的管路应设置两条。
•⑤串联冷却设备时要由下往上,保证断水时冷 却设备内留有一定水量。